管道失效准则与强度理论的关系
第二讲 四种常见的强度理论

基本假说:最大正应力(拉应力)1是引起材料脆断的因素。 失效准则:最大拉应力1 脆断破坏的条件:1 = b 强度条件:1 [ 无论材料处于什么应力状态,只要微元内的最大拉应力1达 到了单向拉伸的强度极限b,就会发生断裂破坏。
4.2.2 四种常见的强度理论
4、最大畸变能密度理论(第四强度理论) 塑性材料
根据:无论材料处于什么应力状态,只要发生屈服,都是由 于微元的最大畸变能密度达到一个极限值。 基本假说:最大畸变能密度νds是引起材料屈服的因素。
失效准则:最大畸变能密度νds
单向拉伸下,1= s, 2= 3 = 0,材料畸变能密度的极限值
1、最大拉应力理论(第一强度理论) 脆性材料
例如,水管在寒冬低温条件下,由于管内水结冰引起体积膨胀,而 导致水管爆裂。由作用反作用定律可知,水管与冰块所受的压力相 等,试问为什么冰不破裂,而水管发生爆裂? 解答:水管在寒冬低温条件下,管内水结冰引起体积膨胀,水管承 受内压而使管壁处于双向拉伸的应力状态下,且在低温条件下材料 的塑性指标降低,因而易于发生爆裂;而冰处于三向压缩的应力状 态下,不易发生破裂。例如深海海底的石块,虽承受很大的静水压 力,但不易发生破裂。
4.2 四种常见的强度理论
4.2.1 概述
1、四种常见的强度理论 ➢ 第一类强度理论:以脆断作为破坏的标志。 包括:最大拉应力理论 最大伸长线应变理论 ➢ 第二类强度理论:以屈服作为破坏的标志。 包括:最大切应力理论 最大畸变能密度理论
4.2.2 四种常见的强度理论
1、最大拉应力理论(第一强度理论) 脆性材料
基本假说:最大切应力max是引起材料屈服的因素。 失效准则:最大切应力max
压力管道的强度分析
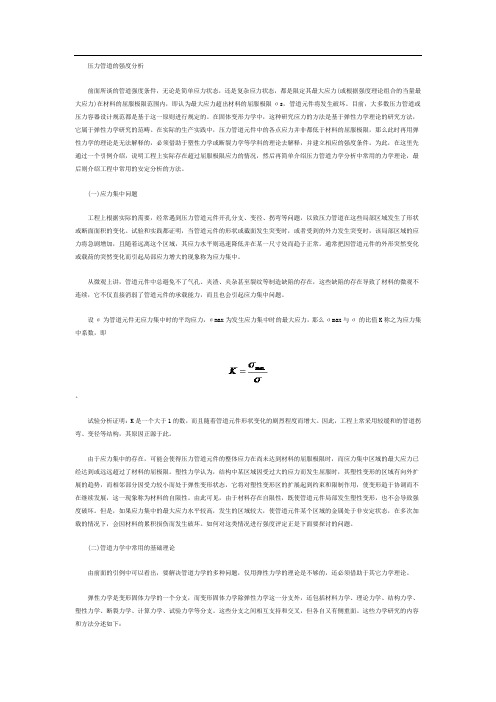
压力管道的强度分析前面所谈的管道强度条件,无论是简单应力状态,还是复杂应力状态,都是限定其最大应力(或根据强度理论组合的当量最大应力)在材料的屈服极限范围内,即认为最大应力超出材料的屈服极限σs,管道元件将发生破坏。
目前,大多数压力管道或压力容器设计规范都是基于这一原则进行规定的。
在固体变形力学中,这种研究应力的方法是基于弹性力学理论的研究方法,它属于弹性力学研究的范畴。
在实际的生产实践中,压力管道元件中的各点应力并非都低于材料的屈服极限,那么此时再用弹性力学的理论是无法解释的,必须借助于塑性力学或断裂力学等学科的理论去解释,并建立相应的强度条件。
为此,在这里先通过一个引例介绍,说明工程上实际存在超过屈服极限应力的情况,然后再简单介绍压力管道力学分析中常用的力学理论,最后则介绍工程中常用的安定分析的方法。
(一)应力集中问题工程上根据实际的需要,经常遇到压力管道元件开孔分支、变径、拐弯等问题,以致压力管道在这些局部区域发生了形状或断面面积的变化。
试验和实践都证明,当管道元件的形状或截面发生突变时,或者受到的外力发生突变时,该局部区域的应力将急剧增加,且随着远离这个区域,其应力水平则迅速降低并在某一尺寸处而趋于正常。
通常把因管道元件的外形突然变化或载荷的突然变化而引起局部应力增大的现象称为应力集中。
从微观上讲,管道元件中总避免不了气孔、夹渣、夹杂甚至裂纹等制造缺陷的存在,这些缺陷的存在导致了材料的微观不连续,它不仅直接消弱了管道元件的承载能力,而且也会引起应力集中问题。
设σ为管道元件无应力集中时的平均应力,σmax为发生应力集中时的最大应力,那么σmax与σ的比值K称之为应力集中系数,即。
试验分析证明:K是一个大于1的数,而且随着管道元件形状变化的剧烈程度而增大。
因此,工程上常采用较缓和的管道拐弯、变径等结构,其原因正源于此。
由于应力集中的存在,可能会使得压力管道元件的整体应力在尚未达到材料的屈服极限时,而应力集中区域的最大应力已经达到或远远超过了材料的屈极限。
容器失效准则强度理论计算法则资料
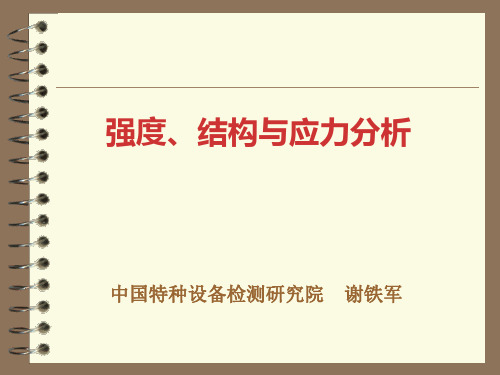
压力容器强度计算概述——设计压力选取
表 设计压力选取 设 计 压 力 1.0~1.10 倍工作压力; 不低于(等于或稍大于)安全阀开启压力(安全 阀开启压力取 1.05~1.10 倍工作压力) ; 取爆破片设计爆破压力加制造范围上限; 取无安全泄放装置时的设计压力,且以 0.1Mpa 外 压进行校核; 设计外压力取 1.25 倍最大内外压力差或 0.1Mpa 两者中的小值; 设计外压力取 0.1Mpa; 设计外压力按无夹套真空容器规定选取 1 设计内压力按内压容器规定选取;
压力容器强度计算概述——术语厚度
3、厚度
(1)计算厚度δ:由计算压力计算(设计压力加静压力)得到,容器受压元件为满足 强度及稳定性要求,按相应公式计算得到的不包括厚度附加量的厚度。 (2)设计厚度δd:计算厚度与腐蚀裕量之和。 (3)名义厚度δn(即图样标注厚度):设计厚度加上钢材厚度负偏差后,向上圆整至 钢材(钢板或钢管)标准规格的厚度。 (4)有效厚度δe:名义厚度减去厚度附加量(腐蚀裕量与钢材厚度负偏差之和)。 (5)最小实测厚度:实际测量的容器壳体厚度的最小值。厚度校核时如果局部减薄 用《检规》的G0校核,如果均匀减薄,则需要考虑腐蚀余量后校核。 (6)厚度附加量:设计容器受压元件时所必须考虑的附加厚度,包括钢板(或钢管) 厚度负偏差C1及腐蚀裕量C2。<制造减薄量C3> 注意:容器壳体加工成型后不包括腐蚀裕量的最小厚度δmin: 对碳素钢、低合金钢,不小于3mm 对高合金钢,不小于2mm
压力容器强度计算概述——术语压力
1、压力(除注明者外,压力均为表压力)
(5)最大允许工作压力[Pw]:指在设计温度下,容器顶部所允许承受的最大表压力。 该压力是根据容器壳体的有效厚度计算所得,且取最小值。 最大允许工作压力可作为确定保护容器的安全泄放装置动作压力(安全阀开启 压力或爆破片设计爆破压力)的依据。 (6)安全阀的开启压力 PZ:安全阀阀瓣开始离开阀座,介质呈连续排出状态时,在 安全阀进口测得的压力。介于容器最大工作压力和设计压力之间。 (7)爆破片的标定爆破压力Pb:爆破片铭牌上标明的爆破压力。1.0-1.1
第十一章 材料失效及强度理论

屈服失效──最大切应力理论、形变应变能理论
第11章 材料失效及强度理论
11-2 关于断裂的强度理论
1)最大拉应力强度理论(第一强度理论)
把材料脆断失效的原因归结为最大拉应力。只要最大拉应力 达到材料单向拉伸脆断时的极限拉应力值(即强度极限) 1u , 材料就发生脆断失效。
第11章 材料失效及强度理论
11-5 许用应力 强度条件
1)相当应力 综上所述,当由强度理论来建立各种应力状态下材料失效判据时, 是将主应力的某一综合值与材料单向拉伸时极限应力相比较。主 应力的这一综合值称为相当应力,用 r 表示。
•第一强度理论 •第二强度理论
r1
1
b
r2
1
2
3
b
•第三强度理论
r3
第11章 材料失效及强度理论
莫尔认为:最大剪应力 是使物体破坏的主要因素, 但滑移面上的摩擦力也不可 忽略(莫尔摩擦定律)。综 合最大剪应力及最大正应力 的因素,莫尔得出了他自己 的强度理论。
阿托?莫尔(O.Mohr),1835~1918
1)两个概念:
第11章 材料失效及强度理论
(1)极限应力圆:材料失效时对应的一
材料屈服失效的原因归结为最大切应力。认为,无论材料
处于何种应力状态,只要最大切应力达到材料单向拉伸屈
服时的极限最大切应力值 u,材料就发生屈服失效。
• 失效原因: max
• 失效判据: max
u
因为
1
2 max
1
3
1 u 2s
所以
1
3
s
第11章 材料失效及强度理论
11-3 关于屈服的强度理论 1)最大切应力强度理论(第三强度理论) 第三强度理论曾被许多塑性材料的试验结果所证实,且 稍偏于安全。这个理论所提供的计算式比较简单,故它在工 程设计中得到了广泛的应用。该理论没有考虑中间主应力σ2 的影响,其带来的最大误差不超过15%,而在大多数情况下 远比此为小。
材料失效及强度理论.
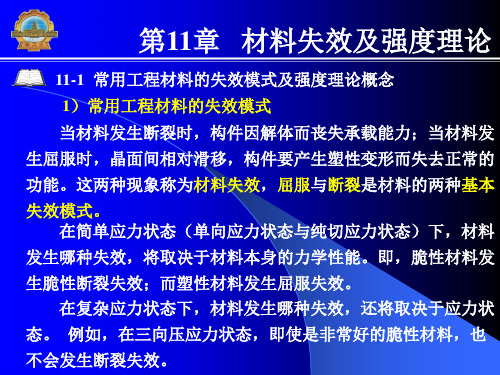
第11章 材料失效及强度理论
1) 0 ; s 2) 0 ; s 3) 0 ; s 4) 0 ; s 5) 0 , 0 ; s 6) 0 , 0 ; s
讨论:
1
2
1 2 2
2
3 2
3 1
s
若为平面应力状态时,假如 、 、 0(三个主应力
没有顺序关系)。这样,上式将变为
2 2 s
第11章 材料失效及强度理论
11-3 关于屈服的强度理论 2)形变应变能强度理论(第四强度理论)
s
第11章 材料失效及强度理论
11-4 许用应力 强度条件
1)许用应力 工程构件的强度达到极限状态(即发生强度失效)的条件 是什么?怎样才能保证构件安全可靠的工作?
以最大切应力理论为例,来回 答这个问题。
现有材料相同的四个构件,其 危险点应力状态如图所示。
由于存在 强度分析的诸 多不确定因素, 那么,B 构件 比D 构建更安 全一些。
第11章 材料失效及强度理论
11-1 常用工程材料的失效模式及强度理论概念 2)强度理论的概念 材料发生什么形式的失效?何时发生失效?失效时的应力, 即极限应力是多大?怎样建立失效判据?要解决这些问题,对于 单向应力状态情况是很容易的。那就是可以模拟实际的单向应力
失效分析与强度准则
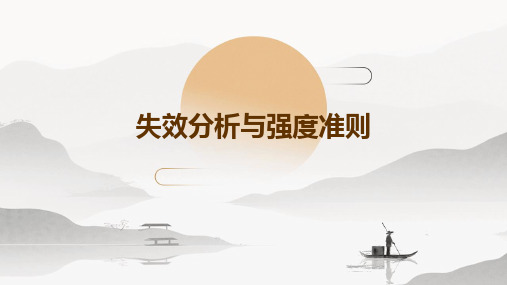
VS
详细描述
汽车零件的磨损失效是汽车故障的主要原 因之一,可能导致车辆性能下降和安全事 故。通过磨损失效分析,可以了解汽车零 件的磨损机理和影响因素,为汽车零件的 设计、制造和使用提供优化方案。
案例五:高分子材料的老化失效分析
总结词
高分子材料的老化失效分析主要研究高分子材料在环境因素作用下的性能退化和老化机理。
详细描述
高分子材料的老化失效是一个普遍存在的现象,受到环境因素如温度、湿度、紫外线等的影响。通过老化失效分 析,可以了解高分子材料的老化机理和影响因素,为高分子材料的设计、制造和使用提供科学依据。
感谢您的观看
THANKS
高分子材料的失效分析
01
高分子材料的失效分析主要关注高分子材料的强度、
硬度、韧性、耐热性、耐腐蚀性等方面的变化。
02
高分子材料的失效通常是由于老化、氧化、水解等因
素引起的。
03
高分子材料的失效分析方法包括红外光谱分析、核磁
共振谱分析、热重分析等。
04
结构失效分析
结构失效的分类与原因
断裂失效
由于材料内部存在缺陷或应力集中区 域,导致结构在低于其承载能力的应 力作用下发生断裂。
最大伸长应变准则
该准则认为当最大伸长应 变达到材料的极限伸长应 变时,材料会发生拉伸失 效。
莫尔-库仑准则
该准则认为当剪切应力与 正应力之比达到某一特定 值时,材料会发生剪切失 效。
强度准则的应用场景与限制
应用场景
强度准则广泛应用于工程结构的设计、分析和优化,特别是在材料和结构的承载能力评 估方面。
05
失效分析案例研究
案例一:金属材料疲劳失效分析
总结词
金属材料疲劳失效分析主要研究金属材料在循环载荷作用下的性能退化和最终 断裂过程。
材料失效准则详解
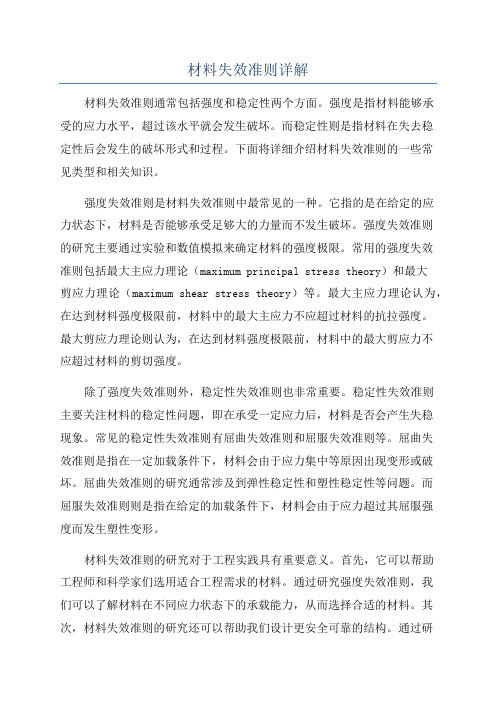
材料失效准则详解材料失效准则通常包括强度和稳定性两个方面。
强度是指材料能够承受的应力水平,超过该水平就会发生破坏。
而稳定性则是指材料在失去稳定性后会发生的破坏形式和过程。
下面将详细介绍材料失效准则的一些常见类型和相关知识。
强度失效准则是材料失效准则中最常见的一种。
它指的是在给定的应力状态下,材料是否能够承受足够大的力量而不发生破坏。
强度失效准则的研究主要通过实验和数值模拟来确定材料的强度极限。
常用的强度失效准则包括最大主应力理论(maximum principal stress theory)和最大剪应力理论(maximum shear stress theory)等。
最大主应力理论认为,在达到材料强度极限前,材料中的最大主应力不应超过材料的抗拉强度。
最大剪应力理论则认为,在达到材料强度极限前,材料中的最大剪应力不应超过材料的剪切强度。
除了强度失效准则外,稳定性失效准则也非常重要。
稳定性失效准则主要关注材料的稳定性问题,即在承受一定应力后,材料是否会产生失稳现象。
常见的稳定性失效准则有屈曲失效准则和屈服失效准则等。
屈曲失效准则是指在一定加载条件下,材料会由于应力集中等原因出现变形或破坏。
屈曲失效准则的研究通常涉及到弹性稳定性和塑性稳定性等问题。
而屈服失效准则则是指在给定的加载条件下,材料会由于应力超过其屈服强度而发生塑性变形。
材料失效准则的研究对于工程实践具有重要意义。
首先,它可以帮助工程师和科学家们选用适合工程需求的材料。
通过研究强度失效准则,我们可以了解材料在不同应力状态下的承载能力,从而选择合适的材料。
其次,材料失效准则的研究还可以帮助我们设计更安全可靠的结构。
通过研究稳定性失效准则,我们可以了解材料在承受一定应力后的变形和破坏形式,从而设计出更稳定的结构。
最后,材料失效准则的研究还有助于我们了解材料破坏的机理和过程。
通过深入研究材料失效准则,我们可以揭示材料在应力或环境作用下破坏的原因和机制,从而为材料科学和工程实践提供更多的依据和指导。
第08章 失效分析与强度准则 课件
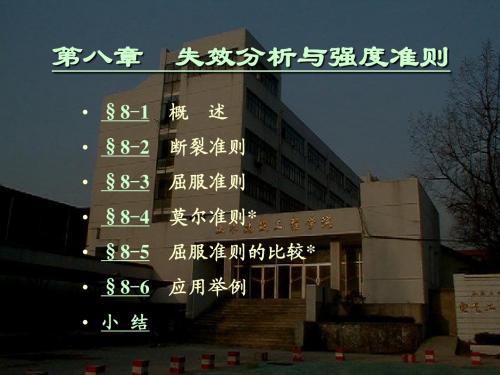
屈服准则
§8-4
一、莫尔准则
莫尔准则*
莫尔准则: 切应力是使材料达到危险状态的主要因
素,但滑移面上所产生的阻碍滑移的内摩擦力却取决 于剪切面上的正应力 的大小。
1.莫尔准则适用于脆性剪断: 脆性剪断: 在某些应力状态下,抗拉、压强度不等的 材料也可能发生剪断,例如铸铁的压缩。 2.材料的剪断破坏发生在(f)值最大的截面上 (f为内摩擦系数) 1)在一定应力状态下,滑移面上为压应力时,滑移阻 力增大;为拉应力时,滑移阻力减小;
§8-1 二、单向拉伸应力状态下的强度失效
1.脆性材料 1)失效形式:断裂 b 由单向拉伸试验建立 2)失效判据:
2.塑性材料 1)失效形式:屈服 s 由单向拉伸试验建立 2)失效判据:
概
述
三、强度准则的提出
1.简单应力状态下强度准则可由试验确定; 2.一般应力状态下,材料失效方式不仅与材料性质有关, 且与应力状态有关,即与各主应力大小及比值有关;
最大拉应力1,与应力状态无关; 1.断裂原因: 2.强度准则: 1 u / nb 1 [ ] 失效判据: 1 u 1 b 3.u由单向拉伸断裂条件确定: u b nb [ ] 4.应用情况: 符合脆性材料的拉断试验,如铸铁单向拉 伸和扭转中的脆断;未考虑其余主应力影响且不能用 于无拉应力的应力状态,如单向、三向压缩等。
§8-1
概
述
1)一般脆性材料脆断,塑性材料屈服; 2)脆性材料在三向等压应力状态下会产生塑性变形, 塑性材料在三向等拉应力状态下会发生脆性断裂; 3.复杂应力状态下的强度准则不能由试验确定(不可能 针对每一种应力状态做无数次试验);
4.强度准则 塑性屈服与脆性断裂; 1)金属材料的失效分为:
- 1、下载文档前请自行甄别文档内容的完整性,平台不提供额外的编辑、内容补充、找答案等附加服务。
- 2、"仅部分预览"的文档,不可在线预览部分如存在完整性等问题,可反馈申请退款(可完整预览的文档不适用该条件!)。
- 3、如文档侵犯您的权益,请联系客服反馈,我们会尽快为您处理(人工客服工作时间:9:00-18:30)。
纯剪应力状态 ������������������������ ≤ ,������������ ������������ ≤ ,������������ ������
������������������������ =
(弯曲)
������������������������ =
(扭转)
������ ������ ������ ������ ,������- = , ������ ������ 为极限应力 , ������ ������ 为极限应力 ������ ������ 用接近这类构件受力情况的试验装置测定极限应力值比较容易实现。 但是复杂应力状态下的应力强度就不能用上面的公式进行校核了。实践证明,强度与 ,σ- = σ、τ均有关,相互影响。 ������������ ������������ ������������ ������������ 长期以来, 随着生产和实践的发展, 大量工程构件强度失效的实例和材料失效的实验结 果表明: 虽然复杂应力状态各式各样, 但是材料在复杂应力状态下的强度失效的形式却是共 同的,而且是有限的。 无论应力状态多么复杂,材料在常温、静载作用下的主要发生两种强度失效形式:一种 是断裂,另一种是屈服。相应地,强度理论也分成两类:一类是解释断裂失效的,其中有最 大拉应力理论和最大伸长线应变理论。 另一类是解释屈服失效的, 其中有最大切应力理论和 畸变能密度理论。下面将以此介绍这几种理论。 最大拉应力理论(第一强度理论) :这一理论认为最大拉应力是引起断裂的主要因素。 即认为无论是什么应力状态,只要最大拉应力������1 达到������������ 就导致断裂。于是得到断裂准则 ������1 = ������������ 将极限应力������������ 除以安全系数得到许用应力,σ-,所以按第一强度理论建立的强度条件是 ������1 ≤ ,σ铸铁等脆性材料在单向拉伸下, 断裂发生于拉应力最大的横截面。 脆性材料的扭转也是 沿拉应力最大的斜面发生断裂。 这些都与最大拉应力理论相符。 这一理论没有考虑其它两个 应力的影响,且对没有拉应力的状态(如单向压缩、三向压缩等)也无法应用。
以上介绍了四种常用的强度理论。铸铁、石料、混凝土、玻璃等脆性材料,通常以断裂 的形式失效,宜采用第一和第二强度理论。碳钢、铜、铝等塑性材料,通常以屈服的形式失 效,宜采用第三和第四强度理论。 应该指出,不同材料固然可以发生不同形式的失效,但即使是同一材料,在不同应力状 态下也可能有不同的失效形式。例如,碳钢在单向拉伸下以屈服的形式失效,但碳钢制成的 螺钉受拉时,螺纹根部因应力集中引起三向拉伸,就会出现断裂。这是因为当三向拉伸的三 个主应力数值接近时,由第三强度准则 ������1 − ������3 = ������������ 和第四强度准则 1 √ ,(������1 − ������2 )2 + (������2 − ������3 )2 + (������3 − ������1 )2 - = ������������ 2 可以看出,屈服将很难出现。又如,铸铁单向受拉时以断裂的形式失效。但如以淬火钢 球压在铸铁板上,接触点附近的材料处于三向受压状态,随着压力的增大,铸铁板会出现明 显的凹坑,这表明已出现屈服现象。以上例子说明材料的失效形式与应力状态有关。无论是 塑性或脆性材料,在三向拉应力相近的情况下,都将以断裂的形式失效,宜采用最大拉应力 理论。在三向压应力相近的情况下,都可引起塑性变形,宜采用第三或第四强度理论。 管道失效准则: 管道的作用是传输介质, 因此保证一个工艺系统的正常运转, 管道的安全起到了至关重 要的作用。 不管是在系统停止运行即所谓的安装态还是在系统正常运行即所谓的操作态, 管 道都不能有失效发生,否则系统将无法工作。无论在管道的安装态亦或是操作态,ASME 规 范都严格的给定了管道受力校核条件。 管道在受到综合载荷的作用,为三向应力状态,轴向������������ ,环向������������ ,径向������������ 以及扭转产生 的剪切应力τ。轴向包括管道受到弯曲、内压、轴向集中力所产生的应力分量。环向主要是
页 1
最大伸长线应变理论(第二强度理论) :这一理论认为最大伸长线应变是引起断裂的主 要因素。即认为无论什么应力状态,只要������1 达到极限值������������ /������ ,材料就发生断裂。故得断裂准 则为 ������1 = ������������ /������ 由广义胡克定律: ������1 = ,������1 − μ(������2 + ������3 )-/E 带入前面一个式子得断裂准则 ������1 − μ(������2 + ������3 ) = ������������ 将������������ 除以安全系数得许用应力,σ-,于是按第二强度理论建立的强度条件是 ������1 − μ(������2 − ������3 ) ≤ ,σ石料或混凝土等脆性材料受轴向压缩时, 如在试验机与试块的接触面上加添润滑剂, 以 减小摩擦力的影响,试块将沿垂直于压力的方向裂开。裂开的方向也就是������1 的方向。铸铁在 拉-压二向应力,且压应力较大的情况下,试验结果也与这一理论接近。 最大切应力理论(第三强度理论) :这一理论认为最大切应力是引起屈服的主要因素。 即认为无论什么应力状态,只要最大切应力������������������������ 达到与材料性质有关的某一极限值,材料 就发生屈服。单向拉伸下,当与轴线成 45°的斜截面上的������������������������ = ������������ /2时(这时,横截面上 的正应力为������������ ) ,出现屈服。可见,������������ /2就是导致屈服的最大切应力的极限值。因为这一极 限值与应力状态无关,任意应力状态下只要������������������������ 达到������������ ,就引起材料屈服。我们知道, ������������������������ = (������1 − ������3 )/2,那么屈服准则为 ������1 − ������3 ������������ = 2 2 或 ������1 − ������3 = ������������ 将������������ 换为许用应力,σ-,得到按第三强度理论建立的强度条件 ������1 − ������3 ≤ ,σ最大切应力理论较为满意地解释了塑性材料的屈服现象。例如,低碳钢拉伸时,沿与轴 线成 45°的方向出现滑移线,是材料内部沿这一方向滑移的痕迹。沿这一方向的斜面上切 应力也恰为最大值。 畸变能密度理论(第四强度理论) :这一理论认为畸变能密度是引起屈服的主要因素。 即认为无论什么引力状态,只要畸变能密度������������ 达到与材料相关的某一极限值,材料就发生 屈服。单向拉伸下,屈服应力为������������ ,相应的畸变能密度公式为 (1 + μ) 2 (2������������ ) 6E 这就是导致屈服的畸变能密度的极限值。任意应力状态下,只要畸变能密度������������ 达到上 述极限值,变引起材料的屈服。故畸变能密度屈服准则为 ������������ = 在任意应力状态下, (1 + μ) ,(������1 − ������2 )2 + (������2 − ������3 )2 + (������3 − ������1 )2 6E 带入前式整理得屈服准则为 ������������ = 1 √ ,(������1 − ������2 )2 + (������2 − ������3 )2 + (������3 − ������1 )2 - = ������������ 2 (1 + μ) 2 (2������������ ) 6E
页 3
内压产生的应力。径向管道内壁为内压,外壁为环境压力。径向的最大应力为这二者之一, 因此径向应力与环向和轴向比起来很小,可以忽略。所以在管道的强度校核过程中,将其视 为二向应力的状态。 我们知道,无论是塑性或脆性材料,在三向拉应力相近的情况下,都将以断裂的形式失 效。由于管道径向应力远远小于其它两个方向的应力,因此管道的失效主要表现为屈服,选 用第三或第四强度理论进行校核是合适的。由于第三强度理论较第四强度理论更趋安全, ASME B31 规范采用了第三强度理论,即最大切应力理论。 最大切应力理论: ������1 − ������3 ≤ ,σ将最大切应力理论应用到管道中: (������������ − ������������ ) (������������ + ������������ ) ������1 = + √*[ ] + ������ 2 + 2 2 (������������ − ������������ ) (������������ + ������������ ) ������3 = − √*[ ] + ������ 2 + 2 2 即, √(������������ − ������������ )2 + 4������ 2 ≤ ,������如果是架空管道,在安装态,为保证其不发生屈服失效,应用第三强度理论得: √(������������ − ������������ )2 + 4������ 2 ≤ ,������ℎ 为保证安全,会进一步留出安全裕量,将上式左边的环向应力������������ 略去;另外,考虑到 安装态下的管道, 受力比较简单, 不考虑系统可能产生的扭转问题, 因此忽略了剪切应力τ。 所以管道在安装态的应力校核公式如下: ������������ ≤ ,������ℎ 我们知道,安装态时,管道受到的外载荷为重力 W、内压 P、轴向集中载荷 F 以及偶然 载荷诸如地震、风、冰雪等的作用。这些载荷在管道轴向产生的应力为: ������ ������������ ������ ������������������������ + + + ������ 4������ ������ ������ 因为偶然载荷不是持续发生的, 只在偶然的时间段作用于管道, 所以应力的校核会区别 于 W、P、F 的作用情况。我们将 W、P、F 在轴向产生的应力总和称为一次应力,将偶然载 荷在轴向产生的应力������������������������ /������称为偶然应力。得到安装态的校核公式: ������������ = ������1 = 和 ������ ������������ ������ ������������������������ + + + ≤ ������,������ℎ ������ 4������ ������ ������ 金属材料的许用应力会随着温度的变化而变化。一般来说,材料的冷态许用应力,������������ -比 热态许用应力,������ℎ -大,因此校核采用与热态许用应力进行比较,这样更安全。 管道在操作态情况时,除了受到 W、P、F 的作用,还会受到温度 T 的作用。此时,管 道轴向的应力加入了温度产生的部分,即二次应力������2 = ������������ ⁄������。考虑到由温度产生的热涨推 力具有自限性的特征,它会随着管道变形的发生而逐渐减小。另外,因为温度会根据工艺要 求发生变化(开停机反复循环) ,因此温度引起管道的失效形式主要为疲劳破坏。为了避免 管道发生疲劳破坏,规范引进了安定性概念,即允许管道在初始几个循环发生一定的屈服, 当这些屈服发生后,管道的应力完全进入弹性范围内变化,用力学条件表示为: