三种特种加工技术的比较
列举五种特种加工方法

1.热处理:热处理是一种特殊的加工方法,它通过改变材料的组织结构,改变材料的性能,以满足特定的要求。
热处理可以改变材料的硬度、
强度、疲劳强度、耐腐蚀性、抗拉强度等性能。
2.激光加工:激光加工是一种特殊的加工方法,它利用激光束的热能,将材料表面的熔融层切割或熔化,以达到加工的目的。
激光加工可以
实现高精度、高速度、高效率的加工,并且可以实现复杂形状的加工。
3.火花机加工:火花机加工是一种特殊的加工方法,它利用火花机的高速旋转刀具,将材料表面的熔融层切割或熔化,以达到加工的目的。
火花机加工可以实现高精度、高速度、高效率的加工,并且可以实现
复杂形状的加工。
4.电火花加工:电火花加工是一种特殊的加工方法,它利用电火花的高速旋转刀具,将材料表面的熔融层切割或熔化,以达到加工的目的。
电火花加工可以实现高精度、高速度、高效率的加工,并且可以实现
复杂形状的加工。
5.气体保护焊接:气体保护焊接是一种特殊的加工方法,它利用气体保护焊接的高速旋转刀具,将材料表面的熔融层切割或熔化,以达到加
工的目的。
气体保护焊接可以实现高精度、高速度、高效率的加工,
并且可以实现复杂形状的加工。
特种加工的种类

特种加工的种类特种加工是指不断发展的新型制造工艺,其中包括利用化学能、电能、流体动能或其他物理形式能量来去除或改变材料的性质,从而满足特定的制造需求。
特种加工的主要种类包括:1.电火花加工(Electrical Discharge Machining, EDM):这种加工方法主要用于加工硬金属和耐热合金等难加工材料。
原理是利用工具电极和工件之间的间隙,在高压电场下产生火花放电,使局部材料被电离并瞬间熔化。
2.激光加工(Laser Beam Machining, LBM):激光加工利用高功率激光束聚焦在材料表面,产生高温高压,使材料瞬间蒸发或熔化。
激光加工可以用于打孔、切割、焊接、热处理等。
3.电子束加工(Electron Beam Machining, EBM):电子束加工利用高能量电子束冲击材料表面,产生热能和化学能来去除或改变材料。
它主要用于加工高精度和高质量的零件。
4.水射流加工(Water Jet Machining, WJM):水射流加工使用高压水流冲击材料表面,以达到切割、打孔、磨削等目的。
这种加工方法具有无热影响区、无残余应力和环境污染小的特点。
5.超声波加工(Ultrasonic Machining, UM):超声波加工利用高频振动产生的能量对材料进行打孔、切割和抛光等。
这种加工方法主要用于脆性材料,如玻璃、陶瓷等。
6.等离子束加工(Plasma Beam Machining, PBM):等离子束加工利用高温高压的等离子流对材料进行切割、打孔、喷涂等操作。
这种加工方法具有高速度、高精度和高效率的特点。
7.化学加工(Chemical Machining, CM):化学加工通过化学反应去除材料,以达到切割、打孔、磨削等目的。
例如,化学腐蚀、电化学腐蚀等。
8.磁力研磨加工(Magnetic Abrasive Finishing, MAF):磁力研磨加工是一种表面精整技术,利用磁场将研磨介质吸附在磁性工作表面,通过不断振动和更换研磨介质来实现对工件表面的研磨。
特种加工技术

特种加工技术1. 引言特种加工技术是指在工业生产过程中,利用先进的加工设备和工艺,对特殊材料或特殊形状的零件进行加工加工的技术方法。
特种加工技术在许多领域中都有广泛的应用,如航空航天、汽车制造、船舶建造等。
本文将介绍几种常见的特种加工技术,包括电火花加工、激光加工以及电化学加工。
2. 电火花加工电火花加工是一种利用电火花放电来进行加工的技术。
该技术主要用于加工高硬度和脆性材料,如硬质合金、陶瓷等。
其工作原理是利用高压脉冲电流在工件表面产生电火花放电,从而烧蚀掉工件表面的材料。
通过控制放电的时间和能量,可以实现对工件的精细加工。
电火花加工具有以下几个优点: - 能够加工高硬度和脆性材料; - 加工过程中不会产生机械应力; - 可以实现复杂形状的加工。
然而,电火花加工也存在一些限制:- 加工效率相对较低;- 加工精度受到局限。
3. 激光加工激光加工是利用高能量密度的激光束对工件进行加工的技术。
激光加工可以通过烧蚀、熔化、汽化等方式来剥离工件表面的材料。
激光加工具有以下几个特点: - 高加工精度和加工质量; - 高加工速度; - 可以实现对不同材料的加工。
激光加工在航空航天、汽车制造等领域有广泛的应用。
例如,在飞机制造中,激光加工可以用于切割、焊接、打孔等工艺操作。
激光加工的应用还面临一些挑战: - 高能量激光设备的成本较高; - 对工件材料的适应性有限。
4. 电化学加工电化学加工是利用电化学反应对工件进行加工的技术。
它通过在电解液中施加电压,使得工件表面发生氧化、溶解等反应,从而实现加工目的。
电化学加工具有以下优点: - 加工精度高; - 加工过程中不会产生机械应力; - 可以加工高硬度和脆性材料;电化学加工主要用于微小零件加工、细微结构加工、薄板加工等领域。
例如,在电子芯片制造中,电化学加工可以用于进行微细线路的蚀刻。
然而,电化学加工也存在一些限制: - 加工速度较慢; - 加工尺寸受到限制。
5. 总结特种加工技术在现代工业中起着重要作用。
特种加工技术的名词解释
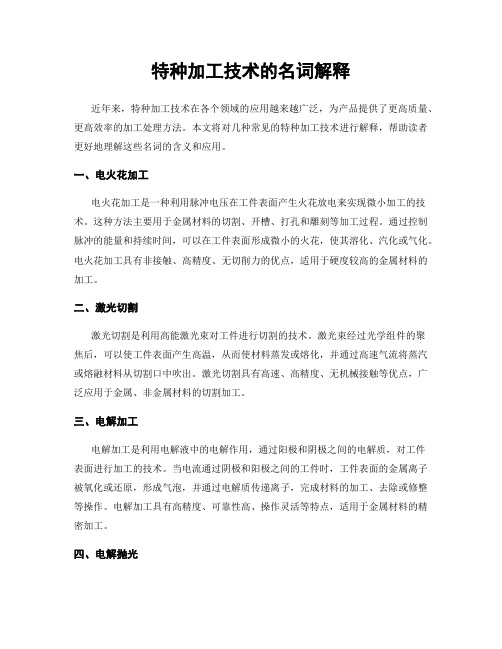
特种加工技术的名词解释近年来,特种加工技术在各个领域的应用越来越广泛,为产品提供了更高质量、更高效率的加工处理方法。
本文将对几种常见的特种加工技术进行解释,帮助读者更好地理解这些名词的含义和应用。
一、电火花加工电火花加工是一种利用脉冲电压在工件表面产生火花放电来实现微小加工的技术。
这种方法主要用于金属材料的切割、开槽、打孔和雕刻等加工过程。
通过控制脉冲的能量和持续时间,可以在工件表面形成微小的火花,使其溶化、汽化或气化。
电火花加工具有非接触、高精度、无切削力的优点,适用于硬度较高的金属材料的加工。
二、激光切割激光切割是利用高能激光束对工件进行切割的技术。
激光束经过光学组件的聚焦后,可以使工件表面产生高温,从而使材料蒸发或熔化,并通过高速气流将蒸汽或熔融材料从切割口中吹出。
激光切割具有高速、高精度、无机械接触等优点,广泛应用于金属、非金属材料的切割加工。
三、电解加工电解加工是利用电解液中的电解作用,通过阳极和阴极之间的电解质,对工件表面进行加工的技术。
当电流通过阴极和阳极之间的工件时,工件表面的金属离子被氧化或还原,形成气泡,并通过电解质传递离子,完成材料的加工、去除或修整等操作。
电解加工具有高精度、可靠性高、操作灵活等特点,适用于金属材料的精密加工。
四、电解抛光电解抛光是利用电解液对工件表面进行表面处理和研磨的技术。
在电解加工的基础上,通过调节电解液的组分和操作条件,使工件表面的金属离子在电流作用下发生氧化、析出或降解反应,从而实现对工件表面的平整化和光洁度的改善。
电解抛光广泛应用于不锈钢等材料的表面处理,可提高材料的光洁度和抗腐蚀性能。
五、真空蒸镀真空蒸镀是利用高真空环境下的热蒸发或电子束蒸发技术,使金属材料蒸发并沉积在工件表面的一种技术。
在真空腔体中,通过加热金属源或电子束轰击金属源,使金属原子蒸发,并在工件表面沉积,形成一层均匀、致密的金属膜。
真空蒸镀广泛应用于镜面、陶瓷、塑料等材料的表面覆盖和装饰,提供了高光洁度、高硬度和防腐蚀等性能。
特种加工其他特种加工方法

化学铣切(化学蚀刻) 光化学腐蚀
用于表面加工的方法主要是:
化学抛光 化学镀膜
化学蚀刻加工原理
化学蚀刻工艺过程
光化学腐蚀
是光学照相制版和光刻(化学腐蚀)相 结合的一种精密微细加工方法。
与化学蚀刻的主要区别: 用照相感光来确定工件表面要蚀除的图
形、线条,而不是靠样板人工刻形、划 线。
二、等离子体加工
又称等离子弧加 工,利用电弧放 电使气体电离成 过热的等离子气 体流束,靠局部 熔化及气化来取 出材料的。
三、挤压珩磨
又称磨料流动加工
(Abrasive Flow Machining,AFM)
四、水射流切割
利用500~900m/s的高速水或带有添加剂 的水冲击工件进行加工,简称“水切 割” ,俗称“水刀”
其他特种加工方法
化学加工 等离子体加工 挤压珩磨 水射流切割 磁性磨料研磨加工和磁性磨料电解研磨加工 快速成型技术 铝合金微弧氧化表面陶瓷化处理技术
一、化学加工
化学加工(ChemicalMachining,CHM)是利用 酸、碱、盐等化学溶液对金属产生化学反应, 使金属溶解,改变工件的尺寸和形状,以及表 面性能。
化学抛光
改善工件表面粗糙度 原理:用硝酸或磷酸等氧化剂溶液,使
工件表面氧化,产生的氧化层又能慢速 溶入溶液,这样微凸处氧化较快,而微 凹处演化较慢,逐步使表面平整。
化学镀膜
原理:在含金属的盐溶液中加入一种还Байду номын сангаас原剂,将镀液中的金属离子还原成原子 沉积在被镀的工件表面。
镀膜主要起装饰、防腐蚀或导电作用。
五、磁性磨料研磨加工和磁性 磨料电解研磨加工
结束
特种加工的种类
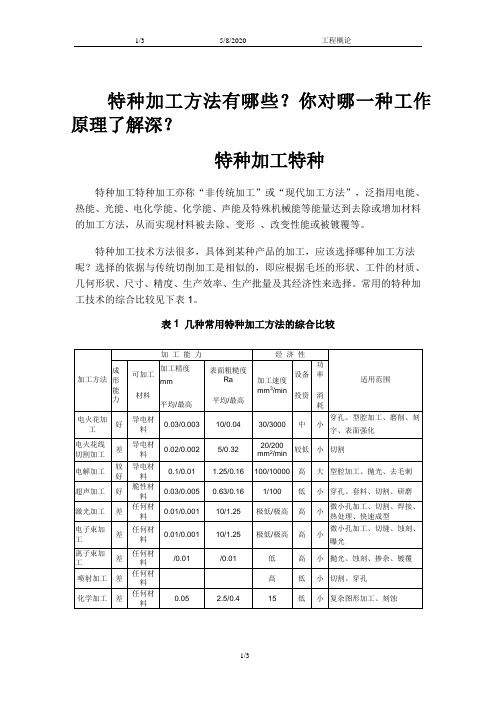
特种加工方法有哪些?你对哪一种工作原理了解深?特种加工特种特种加工特种加工亦称“非传统加工”或“现代加工方法”,泛指用电能、热能、光能、电化学能、化学能、声能及特殊机械能等能量达到去除或增加材料的加工方法,从而实现材料被去除、变形、改变性能或被镀覆等。
特种加工技术方法很多,具体到某种产品的加工,应该选择哪种加工方法呢?选择的依据与传统切削加工是相似的,即应根据毛坯的形状、工件的材质、几何形状、尺寸、精度、生产效率、生产批量及其经济性来选择。
常用的特种加工技术的综合比较见下表1。
表1 几种常用特种加工方法的综合比较加工方法加工能力经济性适用范围成形能力可加工材料加工精度mm平均/最高表面粗糙度Ra平均/最高加工速度mm3/min设备投资功率消耗电火花加工好导电材料0.03/0.00310/0.0430/3000中小穿孔、型腔加工、磨削、刻字、表面强化电火花线切割加工差导电材料0.02/0.0025/0.3220/200mm2/min较低小切割电解加工较好导电材料0.1/0.01 1.25/0.16100/10000高大型腔加工、抛光、去毛刺超声加工好脆性材料0.03/0.0050.63/0.161/100低小穿孔、套料、切割、研磨激光加工差任何材料0.01/0.00110/1.25极低/极高高小微小孔加工、切割、焊接、热处理、快速成型电子束加工差任何材料0.01/0.00110/1.25极低/极高高小微小孔加工、切缝、蚀刻、曝光离子束加工差任何材料/0.01/0.01低高小抛光、蚀刻、掺杂、镀覆喷射加工差任何材料高低小切割、穿孔化学加工差任何材料0.05 2.5/0.415低小复杂图形加工、刻蚀电火花加工电火花加工又称放电加工、电蚀加工(E1ectro-Discharge Machining,简称EDM),是一种利用脉冲放电产生的热能进行加工的方法。
其加工过程为:使工具和工件之间不断产生脉冲性的火花放电,靠放电时局部、瞬时产生的高温把金属熔解、气化而蚀除材料。
特种加工技术总结
特种加工技术总结引言特种加工技术是指利用特殊的加工方法和工艺,对特定材料进行处理、加工和改性的技术手段。
随着科技的发展和工业的进步,特种加工技术得到了广泛的应用和发展。
本文将对几种常见的特种加工技术进行总结和介绍。
1. 表面处理技术表面处理技术是一种通过改变材料表面的特性和性能,来满足特定要求的加工方法。
常见的表面处理技术包括:1.1. 电镀技术电镀是利用电解反应将一层金属沉积在材料表面的一种加工方法。
通过电镀可以提高材料的耐腐蚀性、硬度和光泽度。
常见的电镀技术有镀铬、镀镍、镀金等。
1.2. 涂层技术涂层技术是将一层涂料或薄膜覆盖在材料表面的一种加工方法。
通过涂层可以增加材料的耐磨性、耐腐蚀性和防护性能。
常见的涂层技术有喷涂、浸涂、喷淋等。
1.3. 氮化处理氮化处理是将材料暴露在氮气或含氮气体环境中,利用化学反应使材料表面形成一层氮化物的加工方法。
氮化处理可以提高材料的硬度、耐磨性和耐蚀性。
常见的氮化处理方法有氮气渗透、离子氮化等。
2. 热处理技术热处理技术是通过控制材料的加热和冷却过程,改变材料的组织结构和性能的加工方法。
常见的热处理技术包括:2.1. 淬火淬火是将材料加热到适当的温度,然后迅速冷却,使材料形成马氏体或贝氏体的加工方法。
通过淬火可以提高材料的硬度和强度,但也会使材料变脆。
常见的淬火方法有油淬、水淬等。
2.2. 回火回火是将经过淬火处理的材料加热到适当的温度,然后缓慢冷却的加工方法。
通过回火可以减轻材料的脆性和内应力,提高材料的韧性和强度。
常见的回火方法有低温回火、中温回火等。
2.3. 焊后热处理焊后热处理是将焊接接头进行热处理的加工方法,旨在消除焊接产生的应力和改善接头性能。
常见的焊后热处理方法有焊接后回火、焊后退火等。
3. 精密加工技术精密加工技术是一种通过高精度的设备和控制手段,对材料进行精细和精确的加工的技术。
常见的精密加工技术包括:3.1. 放电加工放电加工是利用电脉冲进行烧蚀和加工的一种高精度加工方法。
特种加工方法及各自的应用
特种加工方法及各自的应用1.引言1.1 概述概述部分的内容可以按照以下方式撰写:概述部分可以对特种加工方法及其应用进行简单介绍,提供读者对接下来内容的整体认知和了解。
在本文中,我们将探讨不同的特种加工方法及其在不同领域中的应用。
特种加工方法是指那些非传统的、针对特定需求的加工技术。
与传统加工方法相比,特种加工方法在加工效率、产品质量、加工能力等方面具有更大的灵活性和创新性。
这些特种加工方法通常需要特殊的工艺设备、材料和工艺流程。
本文将深入研究三种常用的特种加工方法,即方法1、方法2和方法3,并对它们的关键要点进行详细阐述。
每种特种加工方法都有其独特的优势和适用领域。
通过了解这些特种加工方法的原理和特点,我们可以更好地应用它们来解决不同领域中的加工问题。
在后续章节中,我们将对每种特种加工方法进行深入探讨,并分析其在工业制造、材料科学、生物医药等领域中的应用。
我们将重点介绍特种加工方法在这些领域中所取得的成就,以及未来的发展方向。
通过本文的研究,读者将能够对特种加工方法有一个全面的了解,并能够根据所学知识来选择适合自己领域的特种加工方法,以提高加工效率和产品质量。
特种加工方法的应用也将在不同领域中发挥重要作用,推动技术进步和产业发展。
参考以上内容,你可以根据自己的理解和需要进行适当调整和修改。
1.2文章结构1.2 文章结构本文主要探讨了特种加工方法及其各自的应用。
文章结构如下:2. 正文2.1 特种加工方法12.1.1 要点12.1.2 要点22.2 特种加工方法22.2.1 要点12.2.2 要点22.3 特种加工方法32.3.1 要点12.3.2 要点23. 结论3.1 总结3.2 应用展望在正文部分,我们将详细介绍三种特种加工方法及其各自的要点。
每种特种加工方法都将包含详细的解释和应用示例,以便读者更好地理解和应用这些方法。
在结论部分,将总结本文的主要观点和论点,并展望特种加工方法在未来的应用前景。
各类特种加工方法
特种加工是指传统的切削加工以外的新的加工方法。
特点:不是主要依靠机械能而是其他能量;工具硬度可以低于工件;加工过程中,工具与工件直接没有显著的机械切削力电火花加工原理:通过工具和工件之间脉冲性火花放电时电腐蚀现象来蚀除多余金属进行零件加工特点:适合于任何难切削的导电材料;可以加工特殊复杂形状的表面和零件一般加工速度慢存在电极损耗:多数情况下只能加工导电材料范围:机械(模具制造)宇航航空,电子,机电产品,精密仪器,汽车,轻工等行业电火花线切割加工原理:利用移动的细金属丝导线做电极,利用数控技术对工件进行脉冲火花放电加工特点:一般没有稳定的电弧放电现象;存在着“疏松接触”式轻压放电现象;可以加工微细异型孔窄缝和复合形状的工件;电极丝损耗极少;省掉成形电极工具,大大降低成本范围:模具加工;切割电火花成形用电极;直接切割加工零件新产品电化学加工原理:通过电解液、电路中电子的流动,使得阴极金属放生电解蚀除来加工工件特点:加工范围广,效率高,可达到较好的表面粗糙度;电极工具理论上无消耗,可长期使用;电极工具设计修正比较麻烦;造价高,占地多;电解产物有污染范围:激光加工原理:利用光的能量经过透镜聚焦,在焦点上达到很高的能量密度,靠光热效应来加工特点:可以加工任何材料,精密加工,无工具损耗,无污染范围:激光打孔,激光切割,激光刻蚀打标记电子束加工原理:在真空条件下,将具有很高速度和能量的电子束,聚焦在被加工材料上,电子的动能觉大部分转化为热能,使材料局部瞬间熔融,汽化蒸发来加工材料特点:焦点小,能量密度高,生产率高,加工过程便于实现自动化,污染少,设备贵应用:高速打孔,加工型孔及特殊表面,刻蚀,焊接,热处理,电子光刻设备离子束加工原理:在真空条件下,将具有很高速度和能量的离子束加速聚焦,使之碰撞工件表面,通过机械撞击能量来加工工件特点:最精密最微细的加工方法,当代的纳米加工技术,污染少,加工应力、热变形极小,设备成本高范围:刻蚀加工,镀膜加工,离子注入加工超声加工原理:利用工具端面做超声频振动,通过磨料悬浮液加工脆硬材料特点:加工脆硬材料,特别是不导电非金属材料。
特种加工常用加工方法
特种加工常用加工方法
1.数控加工
数控加工是指利用数控技术集成机械、数学、电子、计算机科学等多种领域的技术,实现高速、高精度、高效率的零部件加工方法。
常见的数控加工设备包括数控铣床、数控车床、数控钻床等。
2.激光加工
激光加工是一种非接触式的热加工方法,通过高能量密度的激光束对材料表面进行切割、打孔或表面雕刻等。
常见的激光加工设备包括激光切割机、激光打标机等。
3.电火花加工
电火花加工是一种利用电释放现象切削和加工金属的方法,它采用电极和工件之间的间隙放电来移除材料表面。
常见的电火花加工设备包括数控电火花加工机、手动电火花加工机等。
4.线切割加工
线切割加工是一种切割和加工导电材料的方法,它采用细直线电极在工件表面进
行剪切,通过电热效应将材料加热到熔点以上进行切割和加工。
常见的线切割加工设备包括数控线切割机、手动线切割机等。
5.喷砂加工
喷砂加工是一种利用高速喷射磨料将工件表面进行研磨和打磨的方法。
常见的喷砂加工设备包括压力式喷砂机、吸风式喷砂机等。
6.化学加工
化学加工是一种利用化学反应在材料表面进行刻蚀、腐蚀、清洗等加工方法。
常见的化学加工方法包括酸洗、碱洗、电解抛光等。
- 1、下载文档前请自行甄别文档内容的完整性,平台不提供额外的编辑、内容补充、找答案等附加服务。
- 2、"仅部分预览"的文档,不可在线预览部分如存在完整性等问题,可反馈申请退款(可完整预览的文档不适用该条件!)。
- 3、如文档侵犯您的权益,请联系客服反馈,我们会尽快为您处理(人工客服工作时间:9:00-18:30)。
4000瓦
10000瓦
脉冲性能
上升达到同样的功率,脉 可调制成脉冲输出模式, 冲爬升时间比快轴流激光 最高频率5KHZ,响应时 器多五倍,峰值功率持续 间小于100us,打孔能力、 时间远短于快轴流激光器, 转角加工质量能量还,保 所以打孔能力、转角加工 证切割尖角和质量拐角质 质量、消除零件下表面挂 量。 渣能力较差。 碳钢、不锈钢,连续切割 可连续大量加工一些难加 工的金属铜、磷青铜、钼 时对射频管影响大。 等。 18-20mm 8-10mm 5-6mm(不能连续切割) 厚板稍慢,由于割缝细, 速度较慢 15-20mm 8-10mm 6-8mm 薄板速度快,是CO2切割 速度的2-3倍,切割质量 好,断面完美。
电火花线切割加工、激光加 工、水切割加工技术的比较
xxx
主要内容
1.分析三者的工作原理,比较能量利用率;
2.分析三者加工范围,精度,生产效率,性 价比;
3.分析各自的互补性,列出各自的优缺点, 发展趋势。
加工原理的比较
加工种类 区别 火花线切割加工时,在电极 丝和工件之间进行脉冲放电。 电极丝接脉冲电源的负极, 工件接脉冲电源的正极。 激光加工就是利用其所具有 的输出光线的高指向性和高 能量,进行微小孔及狭缝等 的精密加工、切割、细微焊 接等。 水切割又叫水射流切割,主 要是运用高压水射流,利用 刚度差进行切割。 加工原理 共性
加工范围
加工种类 加工范围(加工材料,使用范围) 加工模具:各种形状的冲模,只需要一次编成。采用电火花线 切割整体加工,使配合精度提高,制造周期缩短,成本降低。 加工电火花成型加工用的电极。加工零件:用于试制新产品; 电火花线切割 单件小批量生产;特殊难加工材料的加工;贵重金属下料。 按走丝的快慢可分为:快走丝:走丝速度为6~12 m/s;中走 丝;慢走丝电火花线切割的走丝速度为0.2m/s。 激光穿孔,如加工航空发动机涡轮叶片等,达到无再铸层、无 微裂纹的效果。激光切割薄材,如耐热合金、钛合金、复合材 料制成的零件等等。主要是应用于飞机三维蒙皮、框架、舰船 船身板架、直升机旋翼、发动机燃烧室等。激光焊接,对高熔 点、高反射率、高导热率和物理特性相差很大的金属焊接特别 有利。大部分用于汽车工业、宇航和仪表工业等行业。还有激 光表面强化;激光快速成形技术等等。 可以切割高硬度和不可溶的材料,比如: 石材、玻璃、陶瓷、 硬质合金、金刚石等。特殊的场地和环境下切割:水下、有可 燃气体环境,而电火花以及激光切割却无法实现。
电能利用率低:只有20%25%。脉冲利用率低,其 影响因素较多,也不稳定, 包括脉宽、峰值电流、电 极、加工材料、加工极性 等因素。加工对象局限为 导电体(金属)。加工速 度慢。
激光加工
(1)既可以加工金属,也可以加工非金属,如木材、 亚克力、PP、有机玻璃等。(2)激光加工速度快, 热影响区小,工件变形小。(3)激光束的发散角可 小于1毫弧,光斑直径可小到微米量级,作用时间可以短 到纳秒和皮秒。同时,大功率激光器的连续输出功率又 可达千瓦至十千瓦量级,因而激光既适于精密微细加工, 又适于巨型机加工。
水射流切割加工的发展趋势
五轴水切 割、机器 人水切割 机等等
更高压 力超高 压水切 割
水射流 切割
耐高压 的辅助 设备
便携式 水切割
补充:“便携式水切割系统”
主要技术:高压柱塞泵、碳纤维磨料射流 发生装臵、转动夹具。 应用更广:应用于反恐、救援、航空、石 油、天然气管道、各种易燃易爆场合等领 域,是一项新型、节能、安全、实用的高 新技术。它是高危作业领域唯一的冷切割 设备,具有独特的安全性和适用性。
数字显示(%) 加工状态 有效脉冲 短路脉冲 空载 比例显示(%) 有效放电 短路
正常进给
欠进给 过进给
27.5
15.8 52.30.4Βιβλιοθήκη 0.2 1.573.6
86.4 60.8
25.8
13.2 34.6
0.6
0.4 4.6
激光加工技术的能源利用率
激光能量的80%-90%被材料反射而浪费, 因此只有10%-20%的利用率。 影响因素:激光与材料实际作用是,能量 的吸收收到激光波长、温度、材料表面涂 敷和粗糙度等因素的影响。因此,材料吸 收能量的大小及分布及吸收谱是影响能量 利用率的重要参数。
能源利用率低,只有10%20%。与其他加工工艺方 法比较,激光加工设备的 前期投资较大。除了光纤 激光器外,都需要增设外 光路设备,来保证激光能 源利用率,维护成本较高。
水切割
切割成本低廉;绿色环保;适用性更广;冷态 加工过程。与激光切割相比:水切割前期投资 比激光切割设备小的多,切割材料范围广,效率 较高,操作维修方便。
•原因(二)与脉冲利用率有关
脉冲利用率的影响因素有: (1)脉宽、峰值电流,有实验证明:脉宽 达到50-80微秒时,脉冲利用率达到其最大 值70%-80%。峰值电流 一旦小于5A时, 脉冲利用率不到10%。 (2)电极的选用不当、加工材料的不同、加 工极性的选用不当都会造成脉冲利用率下 降。
(3)加工状态也会影响脉冲利用率:
技术特点
光纤激光器的优点:技术成 熟及其光纤的可绕行所带来 的小型化、集约化,高亮度 高转换率。高能量输出高质 量光束,省电无需维修。
激光器产生激光的气体消耗 光电转化效率 激光器内光路及机床外光路 镜片消耗 激光器电功率消耗 激光器水冷却系统电耗
5.1元/小时 8%-10% 3.73元/小时 35KW/h 15KW/h 涡轮机轴承寿命8000小时, 8万元每对;射频阀约9万 元/根,保修4000小时; 激光器需2000小时点检一 次,费用5000元。
激光加工
水切割
加工类型
加工参数的比较
加工参数
切割效率一般为20~60毫米2/分,最高可达300毫米2/分;加工精 度一般为±0.01~±0.02毫米,最高可达±0.004毫米;表面粗糙度一 电火花线 般为Rα2.5~1.25微米,最高可达Rα0.63微米;切割厚度一般为40~60 切割 毫米,最厚可达600毫米。 激光制孔的最小孔径已达0.002mm;激光划线技术是生产集成电路的 关键技术,其划线细、精度高(线宽为15~25微米,槽深为5~200 微米),加工速度快(可达200毫米/秒),成品率可达99.5%以上。 激光加工 激光蚀刻技术比传统的化学蚀刻技术工艺简单、可大幅度降低生产成 本,可加工0.125~1微米宽的线,非常适合于超大规模集成电路的制 造。 水切割比电火花线切割效率高,但是精度低于电火花线切割。其切割 工件之精度介于0.1mm~0.25mm之间,而电火花线切割最大可以达 到:±0.002 mm以内。但是,利用水刀切割会产生斜边:大部份所 看到好的切割品质之单侧斜边为0.1mm左右。
激光加工技术的发展趋势
激光器输入参数的提高,从kW级到10kW级CO2激光器和百瓦到千瓦 级YAG激光器完成对各种资料的切割、焊接、打孔、刻划和热处臵等。 YAG激光器的发展:如今打孔用的YAG激光器平均输入功率已由5年前 的400w提高到了800w至1000w,甚至达到2000W-2500W。国际目前比 拟成熟的激光打孔的运用是在天然金刚石和自然金刚石拉丝模的消费 及手表宝石轴承的消费中。 激光器的未来发展趋势集中在半导体激光器、光纤激光器、碟片激光 器等。 欧美发达国家CO2激光器三维加工技术日趋成熟,光纤激光器技术逐 渐发展。光纤激光由于它可以通过光纤传输,柔性化程度空前提高, 特别是针对汽车行业,由于基本上都是的薄板曲面加工,光纤激光配 合同样柔性化的机器人系统,成本低,故障点1mm左右少,维护方便, 速度奇快,当仁不让地稳稳占领了这块市场。 激光打孔峰值功率高达30~50kw,打孔用的脉冲宽度越来越窄,重复频率 越来越高。
精度低于电火花线切割。 利用水刀切割会产生斜 边:大部份所看到好的 切割品质之单侧斜边为 0.1mm左右。
电火花低速走丝线切割的发展趋势
加工效率明显提高:
(1)最高加工效率 由于ns级大峰值电流脉冲电源技术及检测、控制、抗干扰技术的发展,低速 走丝电火花线切割机的加工效率也在不断提高。苏州三光机床使用标准电极 丝时,加工效率为 350 mm2/min。 (2)较大厚度工件的加工效率 日本三菱电机公司FA-V系列机床在切割300 mm厚的工件时,加工效率可达 170 mm2/min。这是很有实际意义的技术提升。 (3)厚度变化工件的加工效率 自动检测加工件的厚度,自动调整加工参数,防止断丝,达到该状态的最高 加工效率。 (4)双丝自动交换技术 瑞士阿奇夏米尔公司推出的ROBOFIL 2030S1-TW机床能采用0.20~0.02 mm 的电极丝自动进行双丝切换加工。采用粗丝进行第一次切割,一般丝径为0.25 mm,以提高加工效率,并可无芯切割;然后采用细丝进行修整,一般采用 0.10 mm的细丝,切割出小圆角,并可提高精度。总体可节省30%~50%的切 割时间。 (5)快速自动穿丝技术 日本牧野公司称自动穿丝时间<15 s;日本沙迪克公司称穿丝时间为13 s.日本 三菱电机公司,当板厚为50 mm 时,穿丝时间为10 s,切丝、穿丝总时间为25 s。
可切割材料种类 切割能力: 碳钢 不锈钢 铝合金 切割板材速度
水切割的性价比
加工种类 优点
优缺点比较 缺点
电火花线切 割
(1)不需要制造形状复杂的工具电极,就能加工出 以直线为母线的任何二维曲面。(2)能切割0.05毫 米左右的窄缝。加工中并不把全部多余材料加工成为 废屑,提高了能量和材料的利用率。(3)在电极丝 不循环使用的低速走丝电火花线切割加工中,由于电 极丝不断更新,有利于提高加工精度和减少表面粗糙 度。
无气体消耗 30%以上 1.6元/小时 7KW/h 6KW/h 免维护
维护成本
光束特性
最大功能率
ROFIN DC025横向边缘放电,光 激光单模输出,能量呈搞死分布。 束呈不规则状态,内部需要增加 原始光束均匀,金属切割断面完 4片镜片对光束进行整形,由于 美。 其原始光斑不规则,所以切割断 面相对粗糙,有在厚板上更明显。