进料检查记录表
供应商年度审核计划及查检表

实得分:
G部分: 环境保护
审 核 记 录 G1 员工有无环境保护的意识 G2 垃圾的有效分类 G3 废水的有效处理 G4 废气的有效处理 G5 废渣的有效处理 G6 ROHS要求的实现 G部分权重为5% 现场反谈 现场查看 现场查看 现场查看, 现场查看 检测报告 差 0 0 0 0 0 0 一般 1 1 1 1 1 1 良 2 2 2 2 2 2
实得分:
B部分: 品质管理和控制
B1 来料检验(IQC) B1.1 检验范圍 B1.2 检查指引 B1.3 检验记录 B1.4 检验/测试设备 B1.5 检验环境 B1.6 部件状态识別 B1.7 有效期检验要求 B1.8 对供应商的控制 B1.9 拒收的处理 B2 制程的检验和监督 B2.1 检验指引 B2.2 检验记录 B2.3 改善行动要求(CAR) B2.4 大量生产前之样品批核 B2.5 对测试设备,治具功能确认及检查 B2.6 检验环境 B3 最终检验(FQC) B3.1 检验指引 B3.2 检验記录 B3.3 检验/测试设备 B3.4 检验环境 B3.5 成品状況标识 B3.6 改善行动要求(CAR)系統 B3.7 拒收批之处理 B3.8 产品的可靠性测试 B部分权重为25%。 审 核 记 录 现场查看、检验控制程序 现场查看、进料检验指导书 进料检验记录表 进料/成品检验记录表 现场查看 现场查看 现场查看、检验控制程序 供方评审管理程序文件及评审记录 纠正措施报告 现场查看、制程管控文件 现场查看、制程检验指导书 巡查检验记录表 纠正措施报告、改善对策记录 产前会议记录及产前报告 设备日常检查表、保养计划表 现场查看 成品检查标准、杨品检验报告 成品检查指导书 成品检验报告 成品检验报告 现场查看 现场查看、产品标识性管理文件 没有建立CAP系统 纠正措施报告、改善对策记录 查看第三方产品安全检测报告 差 0 0 0 0 0 0 0 0 0 差 0 0 0 0 0 0 差 0 0 0 0 0 0 0 0 一般 1 1 1 1 1 1 1 1 1 一般 1 1 1 1 1 1 一般 1 1 1 1 1 1 1 1 良 2 2 2 2 2 2 2 2 2 良 2 2 2 2 2 2 良 2 2 2 2 2 2 2 2
供应商现场考核表

得分
备注
70≤X<80分
合格
有配套能力
X≥80分
合格
有较强配套能力
评审人: 日期:
供应商:
日期:
第 4 页,共 4 页
记录或看板
2 现场5S管理
现场评审
3
图纸、工艺作业指导书,检验规程的有 效性版本
相关资料
4 标识及在产产品可追溯性
现场评审
生
5
不良品统计分析、改进处置与措施状况 及信息传递性
相关记录
产 管
6 工装、夹具/模具的管理
管理文件
理
过
7 工装、夹具/模具,台帐、履历卡
相关记录
程
8 工装、夹具/模具维修、维护计划
计
2 计量人员的资历
量
管
理
3 不良品的处理、分析、处置措施
过
程
4 内外校定计划
相关记录 相关记录 相关记录
5 测量系统分析
相关记录
1 出厂检验规范
文件
出
厂 检
2
出厂包装规范及用户要求(贮存与防护 管理)
文件
验
第 2 页,共 4 页
过
供方现场评价记录表
供方名称:
编号:
出
评/审项厂检过目程
序 号
检查内容及要求
5 不合格品处理是否记录
相关记录
6 不合格原因分析是否有记录
相关记录
原仓 料库 部管 件理 成过 品程 库/
7 不合格纠正措施是否有实效
相关记录
1
标识、摆放、先进先出、帐物卡、产品 防护情况等
现场评审
仓库管理 2
库存周转率如何做
文件 库存周转率报表
进料检验流程图及表格

1、进料检验流程图
1.1进料检验通知单(送检单)
被通知部门:________________ 通知单编号:______________
仓储部主管:______________ 收料仓管专员:______________ 1.2进料检验记录表
1.3进料检验报告表
编号:日期:
限,则判定物料验收结果为“合格”;若检验物料的不合格数量达到或超过企业规定的数量,则判定物料验收结果为“不合格”
进厂零件质量检验表
零件编号:零件名称:号码:
检验主管:检验员:检验日期:年月日进厂零件检验报告表
编号:填写日期:年月日
进厂材料试用检验表
编号:填写日期:
进料检验质量异常处理报告
编号:____________ 填表日期:______________
进料检验日统计表
原材料供应商质量检测表
供应商名称:编号:
外协厂商质量检查表
填写日期:年月日
检验主管:检验人员:
十二、供应商不合格品记录表
年度:月份:编号:
十三、供应商物料拒收月统计表
月份:日期:
主管:制表:
十四、供应商质量评价体系表
十五、供应商综合评价表
编号:填写日期:
岗位职责
1、进料检验主管
2、进料检验专员。
来料、制程、成品抽样检验规范【范本模板】
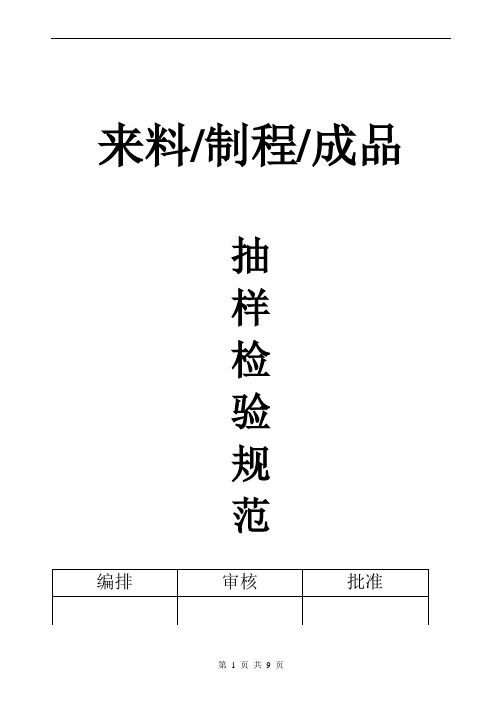
来料/制程/成品抽样检验规范1.目的:规范来料检验、成品检验之抽样水准、抽样方案以统一检验标准,确保来料及成品的质量稳定、良好.2.范围:适用本公司监督检查委外加工厂执行状况及委外加工厂执行IQC进料检验、制程检验、OQC成品出货检验的所有产品。
3.职责:a)IQC、IPQC、OQC负责执行本规定b)品管部负责监督执行并视产品实际情况制定、修改本规定4.内容:4。
1.来料检验1)抽样标准:按MIL-STD—105D Ⅱ级检查水平一次抽样进行2)合格质量水准AQL规定:①电子料MAJOR:0。
65;MINOR:2。
5②结构料MAJOR:1.0;MINOR:2.53)检查严格度:正常检验4)抽样方式:随机抽样5)抽样批量:每一订单作为一个检查批次6)生产部驻厂质检员对来料抽检的规定为,对3C关键性元器件采取每四批至少抽检一批确认外协加工厂来料检查执行情况,一般性器件采取每七批抽检一批的比例执行。
以上规定了来料检验通用抽样检验标准,部分物料特别规定的除外,参见具体物料检验标准,特殊情况由物料QE决定。
4。
2.制程检验1)抽样标准:按MIL—STD—105D Ⅱ级检查水平一次抽样进行2)合格质量水准AQL规定:①功能不良MAJOR:0.65;MINOR:2。
5②外观不良MAJOR:1.0;MINOR:2.53)检查严格度:正常检验4)抽样方式:随机抽样5)抽样批量:每四小时生产作为一个批量,低于4小时按照实际生产数量作为送检数量.6)生产部质检员依据每四批至少抽检一批的标准执行。
作业依据参见具体《物料检验标准》及《成品检验标准》,特殊情况由研发工程师决定.4。
3.成品出货检验1)抽样标准:按MIL—STD-105E(等同GB2828-87)Ⅱ级检查水平一次抽样方案进行2)合格质量水准AQL规定:①主机/键盘:CR:0。
4,MAJOR:0。
65;MINOR:2.53)检验严格度:正常检验4)抽样方式:随机抽样5)抽样批量①一般以客户每次的订单数量作为一个批量检验。
铜材线材IQC检验记录表样板

检验日期:年月日检验编号(IQC NO.):
料号
验收单号
厂商
规格
采购单号
生产日期
检验依据
送验量
进料日期
1.尺寸检测:(单位:mm)抽样数:允收/拒收MA: /
序号
标准尺寸
NO.1
NO.2
NO.3
NO.4
NO.5
NO.6
检验设备名称及编号
1
2
尺寸判定
□OK
□NG
□OK
□NG
□OK
□NG
□OK
□NG
□OK
□合格
□不合格
PS*以上若不良,全部用红笔标示
检验批总判定结果:
□合格□不合格--□提______不合格批最后处理意见:依_________NO:____________之结果为
□退货□特采□特采入重工仓
检验员
审查
核准
表单编号:FB141-09
□NG
□OK
□NG
尺寸项目判定:
□合格□不合格
2.外观检查:
抽样数
不良数
不良说明
允收/拒收MI: /
外观项目判定:
□合格□不合格
主缺:起泡、边缘破损、边缘卷曲、摺叠、异物介入、孔洞、扭结、夹层、橘皮表面、蚀孔、压痕、裂缝裂片、瑕疵
次缺:翘曲、毛边、端部翘曲、截面拱起、扇形、平整度、扭转、波浪形边缘
3功能Biblioteka 检验项目不良原因
抽样数
不良数
不良说明
允收/拒收MA: /
功能项目判定
□合格□不合格
3.1特理特性
断裂、龟裂、裂缝
3.2硬度测试:(单位:HV) (红笔标示为不良)抽样数:允收/拒收MA: /
GJB9001C-2017采购产品检验试验控制程序含记录表格
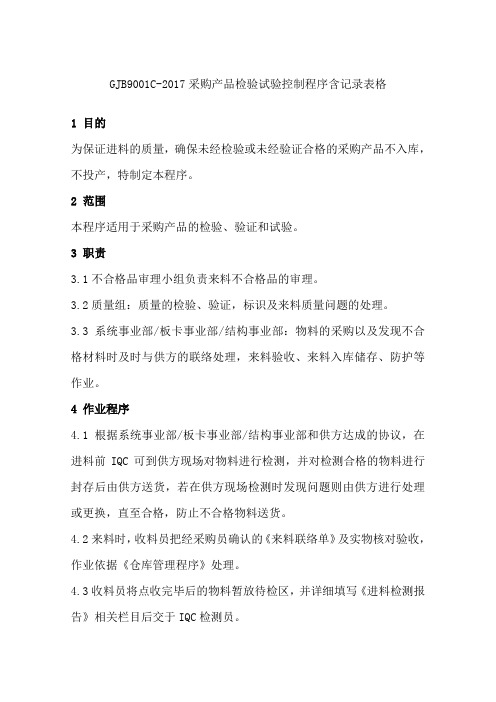
GJB9001C-2017采购产品检验试验控制程序含记录表格1 目的为保证进料的质量,确保未经检验或未经验证合格的采购产品不入库,不投产,特制定本程序。
2 范围本程序适用于采购产品的检验、验证和试验。
3 职责3.1不合格品审理小组负责来料不合格品的审理。
3.2质量组:质量的检验、验证,标识及来料质量问题的处理。
3.3 系统事业部/板卡事业部/结构事业部:物料的采购以及发现不合格材料时及时与供方的联络处理,来料验收、来料入库储存、防护等作业。
4 作业程序4.1 根据系统事业部/板卡事业部/结构事业部和供方达成的协议,在进料前IQC可到供方现场对物料进行检测,并对检测合格的物料进行封存后由供方送货,若在供方现场检测时发现问题则由供方进行处理或更换,直至合格,防止不合格物料送货。
4.2来料时,收料员把经采购员确认的《来料联络单》及实物核对验收,作业依据《仓库管理程序》处理。
4.3收料员将点收完毕后的物料暂放待检区,并详细填写《进料检测报告》相关栏目后交于IQC检测员。
4.4 IQC检测员检查《进料检测报告》所列内容和实物是否一致,IQC 检验员从仓库待检区领料并按《进料检验标准》或顾客指定的特殊要求,对物料进行全检或抽检;若物料为抽检,则通常情况下,以GB2828.1中正常检验一次抽样方案进行抽样检验,AQL值为:严重:0.15;一般:0.65;轻微:1.5。
若顾客有特殊要求,则抽样比例按顾客要求进行。
对所有低于100pics物料,要求IQC检测员进行全检。
4.5 当来料IQC判为合格时,检测员详细填写《进料检测报告》相关栏目,由各事业部负责审核。
4.6 需要做环境实验的物料随报告转实验室做环境实验。
在做环境实验时,根据产品特性和公司要求抽样。
实验员在做完实验后需详细填写《进料检测报告》相关栏目。
4.7 当物料通过了IQC检测和环境试验后,IQC在此批物料包装箱上贴上绿色“IQC合格证”标签,填写相关内容。
来料检验表格填写
来料检验表格填写篇一:来料检验记录单钣金材料来料检验记录单备注: 编号规则按入库单号填写表格生效日期:2011年6月1日铝箔来料检验记录单备注: 编号规则按入库单号填写表格生效日期:2011年6月1日备注: 编号规则按入库单号填写表格生效日期:2011年6月1日备注: 编号规则按入库单号填写表格生效日期:2011年6月1日备注: 编号规则按入库单号填写表格生效日期:2011年6月1日篇二:进料检验规范(含表格)进料检验规范(ISO9001:2015)1.目的:为加强零配件及原材料的质量管理,确保来料质量符合标准,防止不合格品入库,特制定本规范。
2.定义:来料检验又称进料检验,是本公司防止不合格物料进入生产环节的首要控制点。
致命缺陷(CR):凡是对人体或机器产生伤害或危及生命财产的缺点严重缺陷(MA):可能造成产品损坏,功能NG或使用者需要额外加工的缺点轻微缺陷(MI):不影响产品功能的缺点,泛指一般外观轻微不良或差异3.范围:适用于本公司所有进料检验作业。
4:引用标准:抽样计划按MIL-STD-105E单次抽样II级CR:0 MAJ:0.65 MIN:1.5执行5:来料检验流程图:见附件一6.来料检验流程:6.1采购部根据原材料到货日期、品种、规格等通知仓管部和品质部准备来料验收及检验工作。
6.2原材料到厂时,由仓管员,根据采购单,对产品规格、品种、数量、包装方式进行确认,并把来料放置待检区,并通知检验人员对该批物料进行检验,6.3IQC检验PASS合格后,则仓库执行入库处理。
6.4对检测不合格的物料根据《不合格品控制程序》的规定处置,不合格的物料禁止入库,应将其做好相应标识移入不合格品区放置。
6.4.1不合格物料评审,对不合格物料IQC填写IQC检验报告,并附不良样板经品质主管确认后,由公司MRB委员会进行物料评审,最终决定不合格物料的处理方式。
6.4.2评审结果为退货,由IQC在物料上贴不良标签,并注明不良原因和附不良样板,通知采购,由采购开具退货单,由仓库作退货处理。
进料检验规范标准
商提供当批的材质报告或证明〕。
5 / 15
.
机械设备
6 / 15
.
抽样标准 项 检验 次 项目 1 外观
2 尺寸
不锈钢类检验项目对照表
MIL STD-105E
单次抽样 检验水准Ⅱ 正常抽样
AQL
CRI
文件名称 制订部门
版本/版次
A0 B0
.
进料检验规 品质部
机械设备
文件编号 制订日期
修订日期 2014/4/1
文件修订履历 新版文件发行。
TY-W-014 2011-5-4
修订容
版本:B0 页数:共 14 页
核准
审查
制订
文件发行章
1 / 15
.
机械设备
名 称 进料检验规
制定部门 品质部
版本
编号 B0 制定日期
于测定 304 材料〕 (2) 假设无红色出现直接生成淡黄色或淡白色,说明该材料含 NI<7.5%。〔Ni8 测定液: 用于测
定 304 材料〕 (3) 假设生成玫瑰红络合物且不褪色,说明该材料含 MO≥2%。〔 MO2 测定液:用于测定 316 材
料〕 (4) 假设生成红色络合物立即褪色,说明该材料不含 MO.〔 MO2 测定液:用于测定 316 材料〕 (5) 假设生成玫瑰红络合物且马上褪色为深黄色,说明该材料含 MO<2%.〔 MO2 测定液:用于测
MAJ
MIN
0
0.65
1.5
检验 依据
检验 方式
应抽 样本数
缺点 分析
不良判定 CRI MAJ MIN 视公差 备注
来料检验记录表模板
规格型号:定单编号:供应商:
进料日期:物料代码:物料名称:
检验日期:进料数量:抽样数量:
GB/T 2828.1-2012抽样依据:
检验依据:
序号
检查项目
标准值
实测值
不良数
判定
样品1
样品2
3样品
样品4
5样品
一、
外观检查
二、
尺Байду номын сангаас检查
尺寸区域
尺寸值
样品1
样品2
样品3
样品4
5样品
三、
其它检查
四、
包装检查
对于公司不具备检验能力的要求厂家提供质量保证书。
备注:
□不合格检验结果:□合格
最终处理方案:□让步接收□退货退回数量:不合格:挑选结果:合格:□挑选使用
IQC检验员
日期
主管QC
日期
:若判定不合格,按不合格品控制流程处理处理单号
.
精品文档
.
LPA检查表(生产管理人员及质量工程师适用)
11
IQC检验时是按照规定的抽样标准在抽取样 本吗?
进料检验不良时,不合格品的处理是否按规 12 定及时间处理?有无超过规定期限未处理情
况?
13
对生产中发现的来料不良,IQC是否及时进行 处理?
M03-01-W01-07
平和精工(太仓)
1/3
内容版本:01
Action Owner 负责人
Remark 备注
15
制程PPM达到目标了吗?如果没有,相关的行 动由谁在主持展开?Q图每日都有更新吗?
16
来料有合格标识并作追塑性记录吗?对来料 不良有标示隔离吗?
17
有作业前的点检表格并记录按要求实施了吗 (手拿已填好的记录来一项一项检查)?
防错样件确认其保存完好(清洁,在有效期
18
内),并在防错点检中被使用.(随机抽查一 个,能证明被有效检测)?同时验证产线所有
Check Record / 检查记录
Y/N? 判定
Dept. 部门
3
待验区物料摆放是否整齐,物料的批次号是 否有按先入先出要求整理?
4
IQC检验出的不良品是否及时与良品作出区 隔?标示是否明确?
5 发料是否实行先入先出?
良品退库是否保留了原有标签或复制原来标 6 签(需有零件号、数量、LOTNO等信息)?
Check Record / 检查记录
Y/N? 判定
Dept. 部门
23
预防性维护记录按计划实施了吗?抽查至少 一周的记录
24
所有的工装,治具,测量仪器等工具有完好无 损的编号吗?有指定有效期的有效吗?
25 现场产品追溯记录是否完整?
26 信息看板保持最新状态吗?
27
对该项目过去发生的客户投诉,相关员工清 楚吗?有反映到现有制程控制的措施吗?