机械制造技术基础 第四章 机床夹具原理与设计
机械制造技术基础课件最新版第四章机床夹具原理与设计第3节
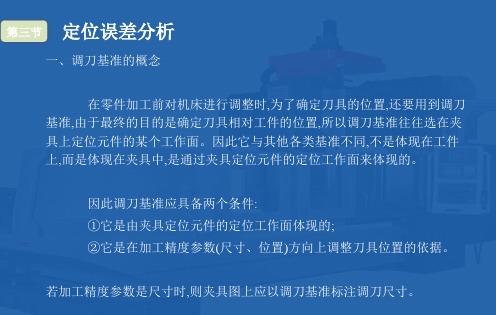
第三节定位误差分析
在用夹具装夹加工一批工件时,一批工件的设计基准相对夹具调刀基 准发生最大位置变化是产生定位误差的原因,包括两个方面:
➢由于定位基准与设计基准不重合,引起一批工件的设计基准相对于定位 基准发生位置变化; ➢由于定位副的制造误差,引起一批工件的定位基准相对于夹具调刀基准 发生位置变化。
定位误差的定义可进一步概括为:一批工件某加工参数(尺寸、位置) 的设计基准相对于夹具的调刀基准在该加工参数方向上的最大位置变化量 Δdw,称为该加工参数的定位误差。
图4-34 定位误差及其产生的原因
第三节 定位误差分析
三、定位误差的计算 通常,定位误差可按下述三种方法进行分析计算:
一是代数法,先分别求出基准位移误差和基准不重合误差,再求出其在 加工尺寸方向上的代数和, Δdw=,若设计基准与调刀基准位于定位基准异侧, 取“+”号,反之,取“-”号;
第三节 定位误差分析
一、调刀基准的概念
在零件加工前对机床进行调整时,为了确定刀具的位置,还要用到调刀 基准,由于最终的目的是确定刀具相对工件的位置,所以调刀基准往往选在夹 具上定位元件的某个工作面。因此它与其他各类基准不同,不是体现在工件 上,而是体现在夹具中,是通过夹具定位元件的定位工作面来体现的。
不准确,将会使设计基准在加工尺寸方向上产生偏移。往往导致加工后工件 达不到要求。设计基准在工序尺寸方向上的最大位置变动量,称为定位误差, 以Δdw表示。
产生定位误差的原因: 1.定位基准与设计基准不重合产生的定位误差
图4-32 基准不重合产生的定位误差
第三节 定位误差分析
2.定位副制造不准确产生的基准位移误差 若将工件定位工作面与夹具定位元件的定位工作面合称为“定位副”, 则由于定位副制造误差,也直接影响定位精度。这种由于定位副制造不准确, 使得定位基准相对于夹具的调刀基准发生位移而产生的定位误差,称为“基准 位移误差”,用Δjw表示。
机械制造技术基础第四版卢秉恒机床夹具原理与设计知识点总结
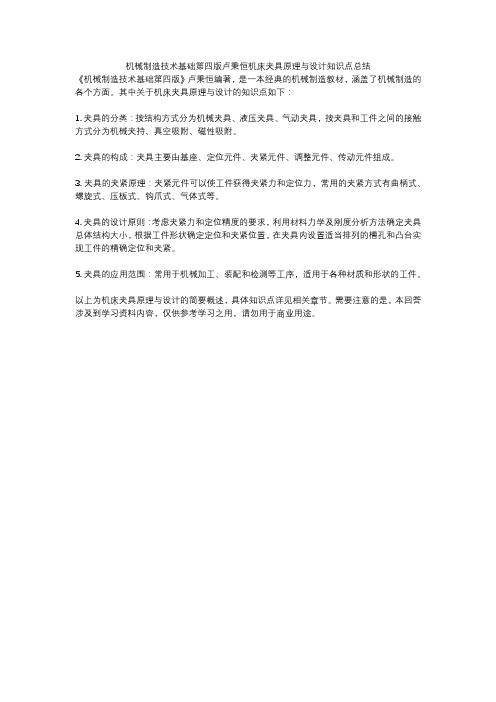
机械制造技术基础第四版卢秉恒机床夹具原理与设计知识点总结
《机械制造技术基础第四版》卢秉恒编著,是一本经典的机械制造教材,涵盖了机械制造的各个方面。
其中关于机床夹具原理与设计的知识点如下:
1. 夹具的分类:按结构方式分为机械夹具、液压夹具、气动夹具,按夹具和工件之间的接触方式分为机械夹持、真空吸附、磁性吸附。
2. 夹具的构成:夹具主要由基座、定位元件、夹紧元件、调整元件、传动元件组成。
3. 夹具的夹紧原理:夹紧元件可以使工件获得夹紧力和定位力,常用的夹紧方式有曲柄式、螺旋式、压板式、钩爪式、气体式等。
4. 夹具的设计原则:考虑夹紧力和定位精度的要求,利用材料力学及刚度分析方法确定夹具总体结构大小,根据工件形状确定定位和夹紧位置,在夹具内设置适当排列的槽孔和凸台实现工件的精确定位和夹紧。
5. 夹具的应用范围:常用于机械加工、装配和检测等工序,适用于各种材质和形状的工件。
以上为机床夹具原理与设计的简要概述,具体知识点详见相关章节。
需要注意的是,本回答涉及到学习资料内容,仅供参考学习之用,请勿用于商业用途。
机械制造技术基础课件机床夹具设计原理

消除或减少过定位的方法主要有:
(1) 提高工件定位基准之间及定位元件工作表面之间的位置精度,减少过定位对加 工精度的影响,使不可用过定位变为可用过定位;
(2) 改变定位方案,避免过定位。改变定位元件的结构,如圆柱销改为菱形销、长 销改为短销等;或将其重复限制作用的某个支承改为辅助支承(或浮动支承)。
4.过定位
图4.5 连杆大头孔加工时工件在夹具中的定位
如图4.5所示的连杆定位方案,长销限制了
、 4个自由度,支承板
限制了
、 3个自由度,其中 被两个定位元件重复限制,这就产生了过定
位。当连杆小头孔与端面有较大的垂直度误差时,夹紧力F将使长销弯曲或使连杆
变形,见图4.5(b)、(c),造成连杆加工误差,这时为不可用过定位。若采用图4.5
4.1 机床夹具概述
4.1.4 机床夹具的功能
(1)保证工件的加工精度,稳定产品质量。机床夹具的首要任务是 保证加工精度,特别是保证被加工工件的加工面与定位面之间以及被加工 表面相互之间的尺寸精度和位置精度。使用夹具后,这种精度主要靠夹具 和机床来保证,不再依赖于工人的技术水平。
(2)提高劳动生产率、降低成本。使用夹具后可减少划线、找正等 辅助时间,而且易于实现多件、多工位加工。在现代夹具中,广泛采用气 动、液压等机动夹紧等装置,还可使辅助时间进一步减小。因而可以提高 劳动生产率、降低生产成本。
(3)通用可调夹具和成组夹具
(4)组合夹具
(5)随行夹具
4.1 机床夹具概述
4.1.2 机床夹具的分类
2)按使用的机床分类
按所使用的机床不同,夹具可分为车床夹具、铣床夹具、钻床夹 具、镗床夹具、磨床夹具、齿轮机床夹具和其他机床夹具等。
3)按夹紧动力源分类
机械制造技术基础课件最新版第四章机床夹具原理与设计第6节

采用这种夹紧方法必须保证工件在 随行夹具的运送过程中不发生任何位移。
图4-58 活塞加工自动线的随行夹具 1—随行夹具 2、4—定位销 3—盖板 5—定位套
第六节 现代机床夹具
数控机床夹具常采用网格状的固定基础板。它长期固定在数控机床 工作台上,板上加工出准确孔心距位置的一组定位孔和一组紧固螺孔,它们成 网格分布。网格状基础板预先调整好相对数控机床的坐标位置。
利用基础板上的定位孔可装各种夹具。角铁支架上也有相应的网格 状分布的定位孔和紧固螺孔以便安装有关可换定位元件和其他各类元件和 组件以适应相似零件的加工。
h)合件
第六节 现代机床夹具
右图所示是钻斜孔的组合夹具
图4a所示是工件,在其上钻ϕ2.9mm的斜孔。 工件以背面在支承件上定位,底面则支承在一定位销 和一定位盘上。
根据斜角要求,按正弦原理计算出定位销轴 线和定位盘轴线间的垂直与水平距离尺寸,工件右端 则由挡销定位。
斜孔加工需要有确定钻模板上钻套轴线位置
✓不同点: 设计指导思想——
➢通用可调夹具的应用对象不明确,只提出 一个大致的加工规格和范围
➢成组夹具是根据成组工艺,针对某一组零 件的加工而设计的,应用对象十分明确
图4-61 通用可调铣床 夹具的可换钳口调整图
图4-62 钻杠杆小头孔 的成组夹具
第六节 现代机床夹具
四、数控机床夹具
数控机床的特点是在加工时机床、刀具、夹具和工件之间应有严格 的相对坐标位置,所以数控机床夹具在机床上应相对数控机床的坐标原点具 有严格的坐标位置,以保证所装夹的工件处于规定的坐标位置上。
机械制造技术基础课件最新版第四章机床夹具原理与设计第1节

➢定位元件 ➢夹紧装置 ➢对刀元件 ➢导引元件 ➢其他装置 ➢连接元件和连接表面 ➢夹具体
图4-4 分度钻床夹具 1—分度操纵手柄 2—钻模板 3—分度轮(棘轮) 4—钻套 5—定位心轴 6—开口垫圈 7—夹紧螺母 8—工件 9—对定机构(棘爪) 10—夹具体
把工件直接放在机床工作台上或放在单动卡盘、机用虎钳等机床附 件中,根据工件的一个或几个表面用划针或指示表找正工件准确位置后再进 行夹紧,也可以先按加工要求进行加工面位置的划线,然后再按划出的线痕进 行找正实现装夹。
这类装夹方法劳动强度大、生产效率低、要求工人技术等级高、定 位精度较低。由于常常需要增加划线工序,所以增加了生产成本,但由于只需 使用通用性很好的机床附件和工具,因此能适用于加工各种不同零件的各种 表面,特别适于单件、小批量生产。
第一节 机床夹具概述
2.用夹具装夹工件
工件装在夹具上,不再 进行找正,便能直接得到准确 加工位置的装夹方式。
图4-1 铣槽工序用的铣床夹具 1—定位键 2—支承板 3—齿纹顶支承钉 4—平头支承钉 5—侧装对刀块
6—夹具底座 7—底板 8—螺旋压板 9—夹紧螺母 10—对刀塞尺
第一节 机床夹具概述
二、机床夹具的工作原理和在机械加工过程中的作用 1.夹具的主要工作原理:
1)使工件在夹具中占有正确的加工位置。 2) 达到工件加工面对定位基准的相互位置精度要求。 3)使刀具相对有关的定位元件的定位工作面调整到准确位置,这就保 证了刀具在工件上加工出的表面对工件定位基准的位置尺寸。
图4-2 铣槽夹具在立式铣床上的工作原理图 1—铣床床身 2—铣床升降台 3—立铣刀 4—铣槽夹具 5—夹具的定位键 6—铣床工作台 7—铣床溜板
第一节 机床夹具概述
机械制造技术基础-卢秉恒 答案 第四章 PPT课件

4-9定位误差产生的原因有哪些?其实质是什么?
答:定位误差产生的原因:(1)定位基准与设计 基准不重合产生的定位误差——基准不重合误差△jb (2)定位副制造不准确产生的基准位移误差——基准 位移误差△jw。
实质:一批工件某加工参数(尺寸,位置)的设计 基准相对夹具的调刀基准在该加工参数方向上的最大位 置变化量△dw,为加工参数的定位误差。
4-15分别简述车、铣、钻床夹具的设计特点
(2)铣床夹具:1铣床加工中切削力较大,振动也较 大,故需要较大的夹紧力,夹具刚性也要好。2借助 对刀装置确定刀具相对夹具定位元件的位置,此装置 一般固定在夹具体上。3借助定位键确定夹具在工作 台上的位置4由于铣削加工中切削时间一般较短,因 而单件加工时辅助时间相对较长,故在铣床夹具设计 中,需特别注意降低辅助时间。
某一组零件的加工而设计的,应用对象十分明确。
4-19.数控机床夹具有什么特点?
答:数控机床夹具在机床上应对相对数控机床的坐标原 点有严格的坐标位置,以保证所装夹的工件处于规定的 坐标位置上.为此数控机床夹具常采用网格状的固定基 础板,它长期固定在数控机床工作台上,板上加工出准 确孔仅距位置的一组定位孔和一组紧固螺孔,它们成网 格分布,利用基础板上的定位孔列装各种夹具.结构要 求简单紧凑,体积小,采用机动夹紧方式,以满足数控加 工的要求.
4-2工件在机床上的装夹方法有哪些?其原理 是什么?(2)
(2)用夹具装夹工件——夹具使工件在夹具中占有正确加 工位置,而且夹具相对于机床保证有准确的相对位置,而夹 具结构保证定位元件的定位工作面对夹具与机床相连接的表 面之间的相对位置准确,使刀具相对有关定位元件和定位工 作面调整到准确位置,这就保证了刀具在工件上加工出的表 面对工件定位基准的位置尺寸。
机械制造技术基础-第4章-机床夹具设计原理-课后答案
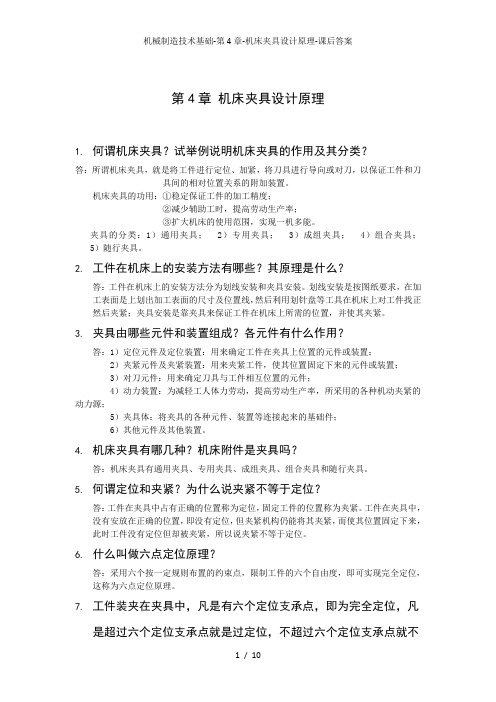
第4章机床夹具设计原理1.何谓机床夹具?试举例说明机床夹具的作用及其分类?答:所谓机床夹具,就是将工件进行定位、加紧,将刀具进行导向或对刀,以保证工件和刀具间的相对位置关系的附加装置。
机床夹具的功用:①稳定保证工件的加工精度;②减少辅助工时,提高劳动生产率;③扩大机床的使用范围,实现一机多能。
夹具的分类:1)通用夹具; 2)专用夹具; 3)成组夹具; 4)组合夹具;5)随行夹具。
2.工件在机床上的安装方法有哪些?其原理是什么?答:工件在机床上的安装方法分为划线安装和夹具安装。
划线安装是按图纸要求,在加工表面是上划出加工表面的尺寸及位置线,然后利用划针盘等工具在机床上对工件找正然后夹紧;夹具安装是靠夹具来保证工件在机床上所需的位置,并使其夹紧。
3.夹具由哪些元件和装置组成?各元件有什么作用?答:1)定位元件及定位装置:用来确定工件在夹具上位置的元件或装置;2)夹紧元件及夹紧装置:用来夹紧工件,使其位置固定下来的元件或装置;3)对刀元件:用来确定刀具与工件相互位置的元件;4)动力装置:为减轻工人体力劳动,提高劳动生产率,所采用的各种机动夹紧的动力源;5)夹具体:将夹具的各种元件、装置等连接起来的基础件;6)其他元件及其他装置。
4.机床夹具有哪几种?机床附件是夹具吗?答:机床夹具有通用夹具、专用夹具、成组夹具、组合夹具和随行夹具。
5.何谓定位和夹紧?为什么说夹紧不等于定位?答:工件在夹具中占有正确的位置称为定位,固定工件的位置称为夹紧。
工件在夹具中,没有安放在正确的位置,即没有定位,但夹紧机构仍能将其夹紧,而使其位置固定下来,此时工件没有定位但却被夹紧,所以说夹紧不等于定位。
6.什么叫做六点定位原理?答:采用六个按一定规则布置的约束点,限制工件的六个自由度,即可实现完全定位,这称为六点定位原理。
7.工件装夹在夹具中,凡是有六个定位支承点,即为完全定位,凡是超过六个定位支承点就是过定位,不超过六个定位支承点就不会出现过定位,这种说法对吗,为什么?答:不对;过定位是指定位元件过多,而使工件的一个自由度同时被两个以上的定位元件限制。
《机械制造工程原理》第4章

如对孔系的加工,常用划针在毛坯上按零件图要求先划线,
画出中心线、对称线或各加工表面的加工位臵,然后,按
其划线找正工件在机床上的正确位臵。这种方法称为划线 特点:划线找正的误差较大,因为线宽约有0.2-0.5mm, 找正安装法。 且划线时也会有误差。划线时虽能兼顾各表面的加工余量、 壁厚和装配要求等因素,但由此也增加了划线时间,又需 技术水平高的划线工。这种安装法也仅在单件小批量生产 中使用
2.工件定位的四种方式 (限制工件自由度与加工要求的关系) 工件在夹具中的定位问题,是夹具设计中首先要解 决的主要问题。在分析工件定位的问题时,定位基准 的选择是一个关键问题。工件定位基准一旦被选定, 则其定位方案也基本被确定了。定位基准一般在工艺 规程中选定,设计夹具时可直接引用。但当工艺规程 选定的定位基准不合理时,夹具设计者应会同工艺人 员共同协商进行改选,以使所设计出的夹具结构合理, 操作简便。必须指出,与定位支承点相接触的工件表 面称为定位基面。工件的定位是通过工件定位基面与 定位支承点相接触来实现的。
2. 机床夹具的分类
1)按夹具的使用范围可分为: 通用夹具、专用夹具、可调夹具、组合夹具等。 2)按所用的机床不同夹具可分为: 钻床夹具、镗床夹具、车床夹具、磨床夹具、拉床夹具等。 3)按夹具上所采用的夹紧动力装置不同可分为: 手动夹具、气动夹具、液压夹具、磁力夹具等。
三爪卡盘
四爪卡盘
万向平口钳
回转工作台
常见定位分析
完全定位:
侧挡销 短圆柱销
平面支承 图2-54 连杆钻孔定位方案
常见定位分析
不完全定位:
侧挡销 短圆柱销
平面支承 图2-54 连杆钻孔定位方案
Z
Y X Z X a)
Z Y X b) Z
- 1、下载文档前请自行甄别文档内容的完整性,平台不提供额外的编辑、内容补充、找答案等附加服务。
- 2、"仅部分预览"的文档,不可在线预览部分如存在完整性等问题,可反馈申请退款(可完整预览的文档不适用该条件!)。
- 3、如文档侵犯您的权益,请联系客服反馈,我们会尽快为您处理(人工客服工作时间:9:00-18:30)。
二、定位误差组成及其计算方法
定位误差 ∆ DW 由基准位置误差 ∆ JW 和基准不重合误差 ∆ JB 两部分组成。 定位基准的最大变化量称为 基准位置误差 。 工序基准相对定位基准理想位置的最大变动量称为 基准 不重合误差
按定位误差定义进行计算
∆ DW = A1 A2 = O1 A 2 − O1 A1 = O1O 2 + O 2 A2 − O1 A1 = O1 O2 +
• (3) 夹紧力的作用点应尽量靠近加工表面,以 减小切削力对夹紧点的力矩,防止或减小工 件的加工振动或弯曲变形。
工件以几个表面同时定位的 , 称为“ 组合表面定位 ” 一个平面和两个与其垂直的孔的组合 一个平面和两个与其垂直的外圆柱的组合 一个孔和一个平行于孔中心线的平面的组合
第三节 定位误差分析
工件在夹具中加工时加工误差的组成
( 1)对定误差 ∆ DD :与夹具相对刀具及切削成形运动的位 置有关的加工误差。其中包括与夹具相对刀具位置有关的加 工误差 — 对刀误差 ∆ DA 和与夹具对成形运动的位置有关的加 工误差 — 夹具位置误差 ∆W 。 ( 2)安装误差 ∆ AZ :与工件在夹具中安装有关的加工误差。 其中包括工件在夹具中定位不准确所造成的加工误差 —定位 ∆ DW 误差 以及工件夹紧时工件和夹具变形所造成的加工误 ∆J 差 —夹紧误差 。 (3) 过程误差 ∆ GC :与加工过程中一些因素有关的加工 误差。包括工艺系统受力变形、热变形、磨损等因素所 造成的加工误差。 为了得到合格产品,必须使各项加工误差之总和等 于或小于规定的工件的工序尺寸公差。
∆ DD + ∆ AZ + ∆ GC ≤ T
一、定位误差及其产生的原因
定位误差
∆ DW
是指由于定位不准确而造成某一工序在工
序尺寸或位置要求方面的加工误差。它的表现形式为工序 基准相对加工表面可能产生的最大尺寸或位置变动量。 1. 定位基准与工序基准不重合产生的定位误差 2. 定位元件制造不准确产生的定位误差 定位误差产生的原因是工件的制造误差、定位元件的 制造误差,两者配合间隙及基准不重合等。定位误差在调 整法加工时存在,在试切法加工时不存在。
第四节 工件在夹具中的夹紧
一、夹紧装置的组成及基本要求
夹紧装置组成:
力源装置 中间传力机构 夹紧元件
夹紧装置的基本要求:
(1)在夹紧过程中应能保持工件的既定位置或更 好地使工件得到定位。 (2)夹紧应可靠和适当,使工件在加工过程中不 产生移动和振动,同时又不使工件产生不允许的 变形和表面损伤,夹紧力要稳定。 (3)夹紧装置应有足够的夹紧行程,操作应安全、 方便、省力。 (4)夹紧装置的自动化程度及复杂程度应与工件 的产量和批量相适应。 (5)夹紧装置的结构要便于制造、调整、使用和 维修,尽可能使用标准夹具零件和部件。
第一节 机床夹具概述
:在机械加工过程中,为了保证加工精度, 夹具 夹具: 固定工件,使之占有确定位置以接受加工或检夹的实质 工件装夹的方法 定位和夹紧 找正安装 用专用夹具安装
直接找正法示例 a)磨内孔时工件的找正 b)刨槽时工件的找正
钻套 支承板
2. 夹具的作用
1)易于保证加工精度; 2)能大大地提高生产率,缩短辅助时间; 3)装夹方便,能大大地减轻工人劳动强度。
三、机床的分类与组成
1. 夹具的分类
按夹具的应用范围分类 通用夹具:成为机床的一种标准附件 专用夹具:为加工某一零件的某一工序而设计 可调夹具:通用可调整夹具和成组夹具,夹具的 部分元件可以更换,部分装置可以调 整,以适应不同零件的加工 随行夹具:这是一种在自动线或柔性制造系统中 使用的夹具 组合夹具:由一套完全标形化的元件,根据零件 的加工要求拼装而成
• (2) 夹紧力的方向应与工 件刚度最大的方向一 致,以减小工件变形。 • (3) 夹紧力的方向应尽量与工件受到的切削力、 重力等的方向一致,以 减小夹紧力。
• 2. 确定夹紧力作用点的原则 • (1) 夹紧力的作用点应正对支承元件或位于支 承元件所形成的支承面内。
• (2) 夹紧力作用点应位于工件刚性较好的部位。 如果必须在工件刚性较差的部位夹紧时,应 采用多点夹紧或使夹紧力均匀分布。
3 外圆表面定位时的定位误差 工件外圆表面定位,采用 V 形块定心定位
4 表面组合定位时的定位误差 很多工件是以多个表面作为定位基准,在夹具中实现 表面组合定位的。 ①箱体类工件以三个相互垂直的平面或一面两孔作为 定位基准来组合定位; ②套类、盘类或连杆类工件以平面和内孔表面作为定 位基准来组合定位; ③阶梯轴类工件以两个外圆表面或两个顶尖孔作为定 位基准来组合定位的。
第四章
机床夹具原理与设计
(一)教学的基本要求: 要求学生掌握工件定位概念和六点定位原 理、四种定位情况、常用定位元件及其所限制的自由度;掌握定位误 差的计算与分析方法;掌握夹紧力三要素的设计原则,初步掌握夹具 的设计方法。 (二)教学具体内容:工件在夹具中的定位;夹紧装置及夹具体; 各 类机床夹具的结构类型及设计要点;专用夹具的设计方法。 (三)教学重点和难点:六点定位原理的理解与应用,定位误差分析 与计算,各类机床夹具的结构类型及设计要点
�� XY
�⌢⌢ Z XY
⌢ Z
� ⌢ ⌢ X Y Z
⌢ X
� Y
� Z
工件定位中的几种情况
完全定位: 工件的六个自由度完全被限制的定位 不完全定位: 根据加工的技术要求,并不需要限制工件的 全部自由度 欠定位: 根据加工的技术要求,应该被限制的自由度 没有被限制的定位 过定位: 工件的同一自由度被两个或两个以上的支承 点重复限制的定位
• 工件定位的基本定律: 也称 “六点定位定律 ” • 工件在夹具中的定位,可以转化为在空间直 角坐标系中 用定位支承点约束工件的自由度 。 • 定位点的确定要从加工要求出发,只要对影 响本工序加工尺寸的自由度加以限制即可, 不要求定全定位。 • 一般地说,一个定位支承点只能限制一个 自由度,因此,工件在夹具中定位时,即使 其全部自由度都被限制, 定位支承点的数目 充其量也决不会多于六个 。 • 定位支承点要合理分布 ,每个定位点所限 制的自由度,原则上 不允许重复或互相矛盾
2 圆孔表面定位时的定位误差 圆孔表面定位的主要方式是定心定位,常用的定位元件 为各种定位销、定位心轴和 V 形块。 ① 工件上圆孔与刚性心轴或定位销过盈配合;定位元件 水平或垂直放置。
2 圆孔表面定位时的定位误差 ② 工件上圆孔与刚性心轴或定位销间隙配合,定位元件 水平放置
2 圆孔表面定位时的定位误差 ③ 工件圆孔与刚性心轴或定位销间隙配合 ,定位元件垂直 放置
按机床分类 车床夹具 铣床夹具 钻床夹具 镗床夹具 按动力源分类 手动夹具 气动夹具 液压夹具 电动夹具 磁力夹具
2.夹具的组成
机 床 连 接 元 件 定 位 元 件
工 件 夹 紧 装 置 其 它 装 置
刀 具 对刀 —导 引元件或 装置
夹具体
第二节 工件在夹具中的定位
一、基准的概念
基准的概念: 零件上用来确定其它点、线、面的位置时, 作为参考的其它的点、线、面。 设计基准 基准的分类 工艺基准 工序基准 定位基准 测量基准 装配基准
• ⑵ 支承板:
• ⑶ 可调支承:
• ⑷ 自位支承(浮动支承):
• ⑸ 辅助支承:
工件以圆孔定位 2. 2.工件以圆孔定位
定位销
定位心轴
工件以外圆定位 3. 3.工件以外圆定位
V形块 定位套筒 半圆孔定位座
V 形块结构形式
固定 V形块
活动V 形块
工件以组合表面定位 4. 4.工件以组合表面定位
支承板
支承钉 支承钉 支承钉 用专用夹具安装工件
二、机床夹具的工作原理和在 机械加工过程中的作用
1. 夹具的主要工作原理 使工件在夹具上占有正确的位置 夹具对于机床应先保证有准确的相对位置 , 而夹具结 构又保证定位元件的定位工作面对夹具与机床相联 接的表面之间的相对准确位置 使刀具相对有 关的定位元件的定位工作面调整到准 确位置
• 二、夹紧力的确定原则
夹紧的实质:通过一定的夹紧机构,对 工件施加一个大小、方向和作用点合适的夹 紧力,以保持工件在夹具中由定位元件所确 定的正确位置,不致因在加工过程中受到其 它力作用而发生变动。 • 1. 确定夹紧力作用方向的原则 • (1)夹紧力的方向应使定位基面与定位元件接 触良好,保证工件 定位准确可靠 。 • 主要夹紧力的方向应朝向主要定位基面。 •
∆ DW ( L2 ) = ∆ JB( N ) = L1 max − L1 min = 45 .2 − 44. 8 = 0 .4
5 提高工件在夹具中定位精度的主要措施误差 (1 )消除或减少基准误差的措施 选用基准位置误差小的定位元件;合理布置定位元件 在夹具中的位置;提高工件定位表面与定位元件的配合精 度;正确选取工件上的第一、第二和第三定位基准。 (2 )消除或减少基准不重合误差的措施 在夹具设计时,为了消除或减少基准不重合误差,应 尽可能选择该工序的工序基准为定位基准。当一个工件在一 道工序的加工中,对加工表面有几项加工精度要求时,则应 根据各项加工精度要求的高低相应选取工件定位时的第一、 第二和第三定位基准。
• 工序基准:工艺文件上尺寸标注的起点
• 度量基准:用于加工或加工完毕进行测量所 用的。
• 二、六点定位原理
� X
�⌢ YZ
�⌢⌢ ZX Y
• 六点定位(完全定位):用六个独立作用的支 承点与工件接触 ,每个支承点限制工件一个 自由度,便可把六个自由度完全限制,从而 确定工件在空间的正确位置
• 必须指出: 定位支承点必须与工件定位基准始终保持 • 紧密贴合,不得脱离 。 • 在分析工件定位时,不考虑夹紧力的影响。 • 定位和夹紧是两个概念,不要混淆。 • 在具体的夹具中,支承 点是由定位元件来体现 的。 • 定位元件相当支承点的 数目,由该定位元件限 制的工件自由度数来判 断。