电风扇叶注塑模设计
风扇叶片注塑模CAD/CAM/CAE一体化技术的应用

零 件壁 厚 05 mm
然 而 采 用 CAD CAM/ / CAE 体 化 技 术 流 程 , - 始 终 以 塑料 件 的 3 模 型 为 中心 ,模 具 设 计 、CAE D
警
幽 1
模拟分析 、模具CNCJI ,以及模具C J I MM ( 三坐
标 )检 测 、塑 料 件 C M检 测 都 完 全 基 于 这 些 塑 料 M 件3 D模 型 的 传 递 ,从 而 消 除 了 二 维 图传 递 几 何 信 息 的不 准 确 性 ,使最 终 生 产 的 塑料 件 和 设计 者 的意 图 保持 高 度 一 致 。还 使 得 整 个生 产 流 程 易 于 实现 自 动化 生 产 ,从 而 大幅 度 降 低 了技 术 工 人 的 工作 量 ,
本
图2 注 塑模生产流程
参磊
冷工 加
榭
6 1
拦旦圭挠i 誊玲
齿轮磨削加工快换夹具的广泛应用
德 国柯尼 格有 限公 司 费 永新
对 于 现 代 化 的 机 床 来 说 ,加 工 任 务 变 得 越 来 越 复 杂 ,加 工的 产 品 也 变得 越 来 越 多样 化 , 因此 相
d
风扇叶片注塑模C D C M C E A /A /A 体化技术的应用
一
湖北省 十堰市 技师学 院 (4 0 0 何 4 20 )
军
冯方根
赵道 明
李
图 1 示 为 一 电 风 扇 图形 ,零 件 厚 度 05 所 . mm, 材料 AB ,年产 1万 件 。需 对 其 进行 注 塑 模具 设 计 S 5
性运行的前提条件 。
I 问题 的提 出 .
有 别于 大 规 模 的 汽车 齿 轮 加 工 ,我 们所 面 对 的 越 来越 多 的 齿 轮加 工 厂 ,都是 针 对 不 同 行业 所 需 而 生 产相 应 规 格 的 齿轮 , 因此 势 必要 求 生 产 厂 家必 须 面 临一 个 小 批 量 ,多 品种加 工 的现 实 问题 ,如 果 加 工 主 要 是 依 靠 一些 高 效 率 的进 口磨 齿 机 床 的话 ,在 保 证 加 工 高 质 高效 的 前 提 下 ,厂 家 就 必 须要 在 工 装 ( )CAD 数 化 技 术 便 于 建 立 基 于 注 塑 模 具 5 参 的统 一 数 据 库 ,提 供 了模 具 开 发平 台 。 ( )利 用CA 6 M软 件 进 行C 高 速加 工技 术 , NC 与传 统 放 电加 工相 比 ,省 去 电极 制 造 一 环 ,缩 短 了 模 具 加 工 周期 ,提 高模 具 加 工精 度 。
电风扇叶片注塑模设计开题报告 (83)

毕业设计(论文)开题报告题目: 电风扇叶片注塑模设计图1扇叶三维模型图2 风扇扇叶二维主视图图3 轮毂二维图图4 风扇叶片二维左视图因塑料风扇叶片尺寸较大,形状复杂,故采用单型腔模。
且由于其壁厚较薄,外观精度要求较高,设计的浇道、浇口须具有快速充模、流动均匀的特点[17]。
方案一:采用单分型面一模一腔(如图5)侧边浇筑方式(如图6),将浇筑点设计成平缝式并将浇筑点选在扇叶顶部的边锋处浇筑完成后成型出一个扇叶模型。
图5 单模单腔注射模图6 侧缝浇筑方式方案二:采用双分型面一模一腔(如图7)点浇筑系统(如图8),此方法采用双分型面模具,并采用点浇筑系统,可以在脱模的同时将成型好的模型和浇筑余料分开来[18]。
图7 双分型面单腔注射模图8针点浇口设计综合分析[19]:由于家用电风扇是常用设备需要大量生产,故应选产量高,生产周期短的方案二。
三本课程的重点及难点:(1)家庭电风扇叶片造型设计(2)工艺分析及电风扇叶片材料选择(3)电风扇叶片三维造型设计(4)电风扇注塑模具成型系统结构设计(5)电风扇注塑模具导向系统结构设计(6)电风扇注塑模具冷却系统结构设计(7)电风扇注塑模具脱模系统结构设计四工作方案及进度计划:闰土机械外文翻译成品某宝dian 第1周-第3周:查阅资料,完成基础知识的积累和开题报告。
第4周-第6周:扇叶模具的几何尺寸计算。
第7周-第10周:三维建模软件对零件进行建模。
第11周-第13周:模具机构各个部分的具体设计。
第14周-第15周:完成毕业论文。
注:1)正文:宋体小四号字,行距20磅,单面打印;其他格式与毕业论文要求相同。
2)开题报告由各系集中归档保存。
3)开题报告引用参考文献注释格式可参照附录E“毕业设计(论文)参考文献样式”执行。
不进入正文,可以作为附件放在开题报告后面。
参考文献[1] 张洪峰.塑料模具设计与制造[J].高等教育出版社,2008,(4):60-62.[2] 罗继相.浅析我国模具行业现状及发展趋势和对策[J].模具技术,2001,03. (6):59-60.[3] 唐仁奎.许艳英注塑模具技术现状与发展趋势[J].科技风,2010,12:20-22.[4] 周永泰.中国塑料模具发展现状与出口期景[J]. 塑料制造,2008,(8):56-62.[5] 宋玉恒. 塑料注射模具设计[J].北京:航空工业出版社,1994,(7):45-47.[6] 屈华昌,李华光,陆飞剑等.关于塑料成型工艺与模具设计[J].高等教育出版社,2003,(8):35-38.[7] 张洪峰.塑料模具设计与制造[J].北京:高等教育出版社,2008,(7):67-69.[8] 周平,王瑞.浅谈我国模具发展[J].模具技术,2007,(4):23-27.[9] 曹延安.中国模具行业的现状与前景[J].金属加工,2012.(9):46-48.[10] 张荣清.模具设计与制造[M].高等教育出版社,2003,(5):60-63.[11] 江恩惠.注塑模具的发展回顾[J].广西轻工业,2009,(21):13-17.[12] 王忠洲.国内外模具发展概况[J].四川工业学院,2001,(15):107-110.[13] 石媛媛.论模具发展的市场与展望[J].现代模具,2010,02,(18):246-246.[14] 王大为.提高冷冲模使用寿命的工艺研究[J],机械工程与自动化.2004,02,(29):73-75.[15] 李健,石厚龙.模具使用寿命的影响及对策[J],金属加工(冷加工).2008,12,(14):46-47.[16] 许振山.塑料模具如何归类[J],材料工业.2009,(9):57-60.[17] Yu Tongmin , Li Guanhua . DESIGN TECHNOLOGY FOR INJECT10N MOLD RARTINGSURFACE BASED ON CASES AND KNOWLEDGE. GHINESE JOURNAL OF MECHANICAL ENGINEERING.2005,4,(18):609-613.[18] CHENG Xue wen, LI De-qun. Development of Integrated Simulation System for PlasticInjection Molding . CADDM. 2005,1,(15):9-16.[19] Bo Scensson, Fredrik Danielsson, Bengt Lennartson. An efficient algorithm for press lineoptimisatiom. The International Journal of Advanced Manufacturing Technology.2013,1,(89):78-80.。
第11章风扇叶模具设计

第十三页,共27页。
11.4.2 调整(tiáozhěng)模腔
• 由于“模架管理”对话框无模架的平移变换功能, 所以只能调整模腔。调整模腔过程包括模具坐标 系的重定义和工件的参数(cānshù)编辑。操作步 骤如下:
第十四页,共27页。
11.4.3 创建(chuàngjiàn)空腔
• 模架加载后,为了便于后续的设计,需先创建 (chuàngjiàn)出模腔在动、定模板上的空腔。操 作步骤如下:
• 使用“注塑模向导”工具条上的“腔体”工具在 模具定模部分中创建出浇注系统(xìtǒng)组件的 空腔。
第十九页,共27页。
11.6 创建(chuàngjiàn)顶出系统
• 本例产品无内、外侧凹或侧孔特征,所以顶出系 统的创建(chuàngjiàn)仅仅是加载并修剪顶杆。
第二十页,共27页。
11.6.1 加载顶杆
• (1)启动UG NX6.0,进入(jìnrù)基本环境界面中。 • (2)在“标准”工具条上执行“开始>所有应用模块>建模”命令,载
入建模模块,接着调入“特征”工具条、“曲面”工具条、“曲线”工具 条等。 • (3)在“标准”工具条上执行“开始>所有应用模块>注塑模向导”命 令,载入MoldWizard模块。 • (4)单击“标准”工具条上的“打开”按钮,弹出“打开”对话框。进 入(jìnrù)随书光盘中打开Example\ch11\fox.prt产品模型文件,如图112所示。
第一页,共27页。
11.1 设计(shèjì)任务
• 本章注塑模具设计实例产品为风扇叶,如图11-1所示。 • 产品规格:350mm×335mm×51mm。 • 产品壁厚:最大3mm,最小2mm。 • 产品设计、生产(shēngchǎn)任务: • 材料为ABS+PC; • 产品收缩率为0.0045; • 单腔模布局; • 产量15000个/年; • 产品外部表面光滑,无明显制件缺陷,如翘曲、缩痕、凹坑等;
电风扇叶片塑料模具设计说明

第1章注射模可行性分析1.1注射模设计的特点塑料注射模塑能一次性地成型形状复杂、尺寸精确或嵌件的塑料制品。
在注射模设计时。
必须充分注意以下三个特点:(1)塑料熔体大多属于假塑料液体,能剪切变稀。
它的流动性依赖于物料品种、剪切速率、温度和压力。
因此须按其流变特性来设计浇注系统,并校验型腔压力及锁模力。
(2)视注射模为承受很高型腔压力的耐压容器。
应在正确估算模具型腔压力的基础上,进行模具的结构设计。
为保证模具的闭合、成型、开模、脱模和侧抽芯的可靠进行,模具零件和塑件的刚度与强度等力学问题必须充分考虑。
1.2注射模组成凡是注射模,均可分为动模和定模两大部件。
注射充模时动模和定模闭合,构成型腔和浇注系统;开模时定模和动模分离,取出制件。
定模安装在注射机的固定板上,动模则安装在注射机的移动模板上。
根据模具上各个零件的不同功能,可由一下个系统或机构组成。
(1)成型零件指构成型腔,直接与熔体相接触并成型塑料制件的零件。
通常有凸模、型芯、成型杆、凹模、成型环、镶件等零件。
在动模和动模闭合后,成型零件确定了塑件的内部和外部轮廓尺寸。
(2)浇注系统将塑料熔体由注射机喷嘴引向型腔的流道称为浇注系统,由主流道、分流道、浇口和冷料井组成。
(3)导向与定位机构为确保动模与定模闭合时,能准确导向和定位对中,通常分别在动模和定模上设置导柱和导套。
深腔注射模还须在主分型面上设置锥面定位,有时为保证脱模机构的准确运动和复位,也设置导向零件。
(4)脱模机构是指模具开模过程的后期,将塑件从模具中脱出的机构。
(5)侧向分型抽芯机构带有侧凹或侧孔的塑件,在被脱出模具之间,必须先进行侧向分型或拔出侧向凸模或抽出侧型芯。
1.3塑料风叶设计与分析风叶是利用一定空间曲面的叶片,通过主体的高速旋转产生风能。
以前,大都是采用金属片材,经过模压制成风叶片。
然后与风叶主体固定安装成风叶。
由于模压叶片和装配等方面的原因,往往风叶的静、动平衡难以达到设计要求。
电风扇上盖注塑成型模具毕业主设计

电风扇上盖注塑成型模具毕业主设计摘要:本文主要介绍了电风扇上盖注塑成型模具的主要设计。
首先,根据产品的形状和尺寸要求,确定了模具的结构类型和材料选择。
然后,通过对模具进行分解和零件设计,得到了模具的零件图。
接着,对模具进行总体结构和顶出结构设计,并给出了模具总体布置图。
最后,对模具进行了工艺路线选择和模具加工方案设计。
1.引言电风扇上盖注塑成型模具是电风扇制造中的关键工具,其设计质量直接影响到产品的质量和生产效率。
因此,对该模具的设计要求非常高。
本文将从模具的结构类型、材料选择、零件设计、总体结构设计、顶出结构设计、整体布置以及工艺路线选择等方面进行详细介绍。
2.结构类型和材料选择电风扇上盖注塑成型模具的结构类型可以根据产品的形状和尺寸要求来确定。
一般来说,采用单腔结构,由于该产品形状比较简单,不需要多腔模具。
材料选择方面,一般采用工程塑料,如ABS、PC等,具有良好的耐热性、耐磨性和强度。
3.零件设计根据模具的功能和工艺要求,对模具进行了分解和零件设计。
主要包括模具座、模芯、定位销、导向柱、顶针、顶出板等零件。
通过对零件进行尺寸和结构的合理设计,保证模具的精度和稳定性。
4.总体结构设计根据产品尺寸和形状要求,确定了模具的总体结构。
采用的总体结构是上模板、下模板和支撑板的组合结构。
上模板和下模板分别安装模芯和模具座。
通过设计模具的总体结构,使得模具在生产过程中具有良好的稳定性和刚性。
5.顶出结构设计顶出结构是电风扇上盖注塑成型模具中非常重要的一部分。
通过对产品的形状和尺寸要求的分析,设计了合理的顶出结构。
采用了顶出板和顶针的结合形式,通过弹簧将顶出板与顶针连接,保证产品的顶出效果。
6.模具布置根据模具的总体结构和顶出结构,进行了模具的整体布置。
通过分析模具的零件尺寸和工艺要求,保证模具的合理布置。
同时,还考虑到了模具在生产过程中的操作便利性和安全性。
7.工艺路线选择根据模具的结构和尺寸要求,选择了合适的注塑工艺。
模具毕业设计55风扇叶片注射模具设计

模具毕业设计55风扇叶片注射模具设计一、设计背景和目的风扇作为现代生活中必不可少的电器之一,其叶片的设计和制造对于风扇的性能和使用效果具有重要影响。
因此,设计一款优质、高效的55风扇叶片注射模具对于提高风扇叶片的生产效率和质量具有重要意义。
本设计旨在设计一款能够满足产品需求的注射模具,通过优化模具设计和材料选择,提高模具的使用寿命和生产效率,并保证产品的质量。
二、设计步骤和流程1.研究分析:首先对现有55风扇叶片的设计进行详细研究,并分析其结构和生产工艺。
2.模具结构设计:根据风扇叶片的形状和尺寸,设计模具的整体结构,包括模具的上模、下模和侧模的形状和尺寸等。
3.模具材料选择:根据模具的使用寿命要求和生产效率要求,选择合适的模具材料,如优质钢材或耐磨合金材料等。
4.模具加工工艺:确定模具的加工工艺和加工设备,包括模具的精度要求、加工配件的尺寸要求等。
5.模具生产和试模:根据设计要求制造模具,并进行试模,测试模具的性能和生产效果。
6.模具调试和优化:根据试模结果进行模具的调试和优化,改进模具的结构和工艺参数,提高模具的生产效率和质量。
7.模具维护和保养:制定模具的维护保养计划,定期对模具进行保养和维修,延长其使用寿命。
三、设计要求和技术方案1.叶片形状设计:根据55风扇叶片的要求,设计叶片的外形和内部结构,保证叶片的强度和风力输出效果。
2.注射模具结构设计:根据叶片形状设计模具的上模、下模和侧模等,确保注射过程中的材料流动和成型效果。
3.模具材料选择:选择优质的钢材或耐磨合金材料,提高模具的硬度和使用寿命。
4.模具加工工艺:根据设计要求确定模具的加工工艺和加工设备,保证模具的精度和质量。
5.模具试模和调试:进行模具试模和调试,测试模具的生产效率和成型质量,进行必要的参数调整和优化。
6.模具维护和保养:制定模具的维护保养计划,包括定期润滑、清洁和维修等,延长模具的使用寿命。
四、设计成果和预期效果根据以上设计流程和技术方案,预计可以设计出一款满足生产需求的55风扇叶片注射模具,具备以下特点和效果:1.提高生产效率:优化模具设计和加工工艺,提高模具的开模速度和成型效率,提高生产效率。
风叶的注射塑模设计

风叶的注塑模设计摘要本文以PA为材料的风叶为例,主要介绍了注塑模具的设计。
此模具在设计时,充分考虑了生产批量、以提高生产效率、降低生产成本为主要宗旨。
通过对一个塑件的全面分析,选用合适的注塑机,确定模具的结构方案,再通过模具型芯、型腔等相关设计,绘制模具的零件图、装配图,完成设计,为了更进一步清楚形象的了解模具的结构设计过程,这次毕业设计使用UG NX6.0与Auto CAD 软件设计,给设计带来了很大的方便。
关键词:风叶加工工艺塑料模软件应用Injection mold designAbstract:The text mainly introduces to note the design of the molding tool of Plastics originally. Is it tell takingPA as material mould plastics idea course of mould mainly to design originally.This mould is in the design, fully consider production lot , regard improving production efficiency , reducing the production cost as the main aim.passing the structure characteristics to the overall analysis of a Plastics piece, choose to use to note the machine of Plastics fitly, make sure the structure project of the molding tool, then passes the related size of a heart of molding tool, a cavity calculation, draw the spare parts diagram of the molding tool and assemble the diagram,. For the sake of the structure design process of the understanding molding tool of the further clear image, this text still adopts the UG and Auto CAD as the three dimensional software, has brought very big convenient.Key Words:;Processing craft Plastic Software applications目录摘要 (I)Abstract (II)第一章引言 (5)1.1介绍 (5)1.2市场调查 (5)1.3塑料产品成型模具设计的一般原则 (5)第二章塑件的工艺性分析 (6)1.1塑件材料特性 (7)1.2 塑件结构精度分析 (8)1.3尺寸精度的选择及注意事项 (8)1.4塑件材料的成型性分析 (8)1.5塑件材料成型工艺参数 (11)第三章模具的基本结构 (11)1.1确定成形方法 (11)1.2型腔数目的确定 (11)1.3确定分型面 (11)第四章注射机的选择 (14)第五章浇注系统的设计 (17)1.1选择浇注系统 (17)1.2主流道 (1)第六章成型零件设计 (18)1.1凹模结构的设计 (18)1.2凸模如图所示 (18)第七章温度调节系统的作用 (19)第八章冷却系统的设计 (19)第九章推出机构设计 (21)第十章模架的选择 (22)第一章塑件的工艺性分析1.1塑件如图所示产品名称:风叶产品材料:PA产品数量:大批量生产塑件颜色:白色塑件要求:塑件表面光滑且均匀,不能有飞边等缺陷。
基于Pro/E的风扇叶片塑料模具设计
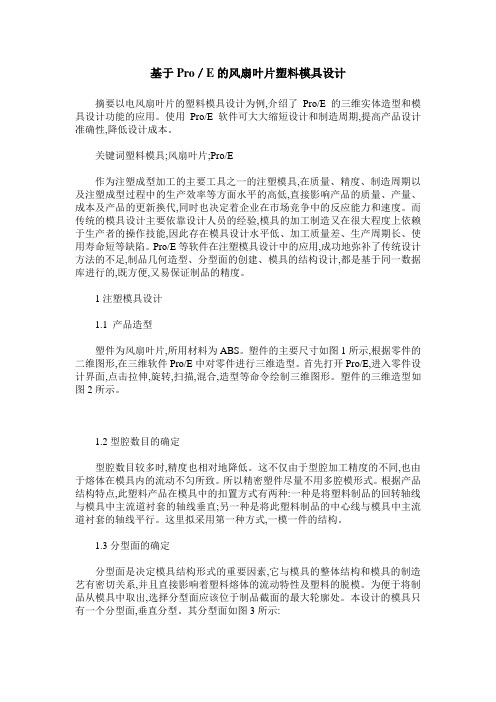
基于Pro/E的风扇叶片塑料模具设计摘要以电风扇叶片的塑料模具设计为例,介绍了Pro/E的三维实体造型和模具设计功能的应用。
使用Pro/E 软件可大大缩短设计和制造周期,提高产品设计准确性,降低设计成本。
关键词塑料模具;风扇叶片;Pro/E作为注塑成型加工的主要工具之一的注塑模具,在质量、精度、制造周期以及注塑成型过程中的生产效率等方面水平的高低,直接影响产品的质量、产量、成本及产品的更新换代,同时也决定着企业在市场竞争中的反应能力和速度。
而传统的模具设计主要依靠设计人员的经验,模具的加工制造又在很大程度上依赖于生产者的操作技能,因此存在模具设计水平低、加工质量差、生产周期长、使用寿命短等缺陷。
Pro/E等软件在注塑模具设计中的应用,成功地弥补了传统设计方法的不足,制品几何造型、分型面的创建、模具的结构设计,都是基于同一数据库进行的,既方便,又易保证制品的精度。
1注塑模具设计1.1 产品造型塑件为风扇叶片,所用材料为ABS。
塑件的主要尺寸如图1所示,根据零件的二维图形,在三维软件Pro/E中对零件进行三维造型。
首先打开Pro/E,进入零件设计界面,点击拉伸,旋转,扫描,混合,造型等命令绘制三维图形。
塑件的三维造型如图2所示。
1.2型腔数目的确定型腔数目较多时,精度也相对地降低。
这不仅由于型腔加工精度的不同,也由于熔体在模具内的流动不匀所致。
所以精密塑件尽量不用多腔模形式。
根据产品结构特点,此塑料产品在模具中的扣置方式有两种:一种是将塑料制品的回转轴线与模具中主流道衬套的轴线垂直;另一种是将此塑料制品的中心线与模具中主流道衬套的轴线平行。
这里拟采用第一种方式,一模一件的结构。
1.3分型面的确定分型面是决定模具结构形式的重要因素,它与模具的整体结构和模具的制造艺有密切关系,并且直接影响着塑料熔体的流动特性及塑料的脱模。
为便于将制品从模具中取出,选择分型面应该位于制品截面的最大轮廓处。
本设计的模具只有一个分型面,垂直分型。
- 1、下载文档前请自行甄别文档内容的完整性,平台不提供额外的编辑、内容补充、找答案等附加服务。
- 2、"仅部分预览"的文档,不可在线预览部分如存在完整性等问题,可反馈申请退款(可完整预览的文档不适用该条件!)。
- 3、如文档侵犯您的权益,请联系客服反馈,我们会尽快为您处理(人工客服工作时间:9:00-18:30)。
4 电风扇叶注塑模设计
4.1 注塑模设计的基本流程
传统方法的注塑模设计是在二维环境下进行,从图4.1中可以看出,传统的模具制造工艺路线只是典型的串行流程,任何其中一部分没有完成都会影响下面的工作,相互之间的制约性太大,这样的结果就是生产周期的延长,人工进行的工作量非常大,而且做工粗糙、精度不高,在CAD/CAM技术高速发展的今天,传统方法终将被取而代之。
基于UG 的注塑模具的设计是在三维环境下进行的,这用方法的采用不仅提高了生成型芯和型腔零件的速度和准确度还可以进行造型设计,还能完成模具的总装配,大大缩短了模具设计周期并及时发现模具设计中的错误,有效地避免工人重复劳动[16]。
图4.1传统方式的注塑模具设计过程图4.2 基于UG的注塑模设计工程
4.2 注塑模具的基本结构设计
4.2.1 扇叶材料的分析
风扇为人们日常生活常用品,需大批量生产,又与人们紧密接触,所以扇叶的材料必须无毒无害,同时考虑没有很高的强度要求,收缩率方面也无特殊要求,故选择ABS材料进行注塑生产。
ABS具有良好的成型加工型,制品表面光洁度高,且具有良好的涂装性和染色性,可电镀成多种光泽[17]。
塑料ABS具有以下性能:
(1)冲击强度极好,耐磨性优良,尺寸的稳定性好。
(2)从热学性能上来看热变形温度为85℃左右,制品经退火处理以后还可提高10℃左右。
在-40℃时仍能表现出一定的韧性,可在-40℃到85℃的温度范围内长期使用。
(3)ABS的电绝缘性较好,并且几乎不受温度、湿度和频率的影响。
(4)ABS流动性好,易溢料,具有优良的化学稳定性、不吸水,是易成型加工的材料可用于注塑。
4.2.2 分型面的选择
分型面是指上、下两模芯互相接触的表面,而分型面的设计在电风扇叶的注塑模设计中是非常重要的。
分型面一般是在确定浇注位置或被称为进料口的位置后再选择。
但在分析各种分型面方案的优缺点之后,也有可能需要重新调整浇注位置。
分型面选择原则有两个,首先要考虑到是塑件在开模时尽可能留在动模部分,同时由于塑件有曲面扇叶,所以也要尽可能留在动模部分。
另一方面考虑到浇注系统,有利于气体的排出。
图4.3 分型面选择
选择分型面应该尽量满足下面几个要求:
(1)应使塑件全部或大部分置于同一半型芯内;
(2)分型面的数目越少,塑件精度就越容易保证,且成型零件的数目也就相应减少。
(3)尽量减少分型面数目,简化其结构。
因此我们采用扇叶边缘及中心转轴的表面如图4.3虚线部分为产品的分型面。
当然,一个塑件的分型面,不是以上原则都要面面俱到,实际设计时分型面应有主要选择对象,根据实际生产条件的需要进行多方案的对比,并结合经验作出正确的判断,最终确定最佳方案。
4.2.3 扇叶注塑模具结构及工作原理
塑件采用注射成形方法。
为保证塑料表面质量,使用直接浇口成形,ABS 流动性好,塑件较大,而直接浇口属于非限制性浇口,浇口的流程短流动阻力小,进料速度快,有利于型腔排气,容易成型。
塑件形状较简单,质量比较小,生产批量较大。
所以使用一模一腔注射模。
这样模具尺寸较小,制造加工方便,生产率高,塑件成本低。
模具的结构形状为单型面注射模。
采用拉杆和限位销,控制分型面的打开距离,其开距应大于70mm ,方便浇口。
此模架是标准模架,且其各块模板的尺寸均选用标准尺寸,参照GB/T 12556.2—1990标准《塑料注射模中小型模架》,模架尺寸(B×L )为800mm×700mm 。
注塑机选用海天200XB ,其喷嘴直径为3.5mm ,喷嘴球面半径为16mm ,在卧式或立式注射机上使用的模具中,主流道垂直于分型面。
由于主流道要与高温塑料熔体及注射机喷嘴反复接触,所以只有在小批量生产时,主流道才在注射模上直接加工,大部分注射模中,主流道通常设计成可拆卸、可更换的浇口套[18]。
为了让主流道凝料能从浇口套中顺利拔出,主流道应设计成圆锥形,其锥角α为2°~6°,小端直径比注射机喷嘴直径大0.5~1mm ,并要求主流道球面半径R 比注射机喷嘴球面半径大1~2mm ,其深度H 为3~5mm 。
主流道各具体尺寸如下:
︒=3α mm R 18216=+=
mm H 3= mm L 90=
mm L d D 5.72tan 2=+=α
(4.1)
根据主流道尺寸可确定浇注系统如图4.4。
图4.4 浇注系统
单分型面注射模也称为两板式注射模,如图4.5所示,合模时,在导柱2和导套1的导向定位下,动模和定模闭和。
成型部分型腔由定模板10上的型腔与固定在动模板11上的型芯组成,锁模力是由注射机合模系统提供。
然后注射机开始注射,塑料熔体经定模上的浇注系统进入型腔,待熔体充满型腔并经过保压、补塑和冷却定型后开模。
开模时,注射机合模系统带动动模后退,模具从动模和定模分型面分开,塑件包在型芯上随动模一起后退,同时,拉料杆23将浇注系统的主流道凝料从浇口套6中拉出。
当动模移动一定距离后,注射机的顶杆接触推板18,推板机构开始动作,使推杆19和拉料杆23分别将塑件及浇注系统凝料从型芯和冷料穴中推出,塑件与浇注系统凝料一起从模具中落下,至此完成一次注射
过程。
合模时,推出机构靠复位杆15复位并准备下一次注射。
图4.5 扇叶的两板式注射模原理图
1-导套,2-导柱,3-定模座板,4-凹模,5-定位圈,6-浇口套,7-冷却水道,8-凸模,9-紧固螺钉,10-定模版,11-动模板,12-动模座板,13-垫块,14-弹簧,15-复位杆,16-支撑柱,17-推板固定板,18-推板,19-推杆,20-紧固螺钉,21-限位螺钉,22-支撑板,23-拉料杆。