电阻焊常见缺陷及控制方法
pcb阻焊常见缺陷原因与措施
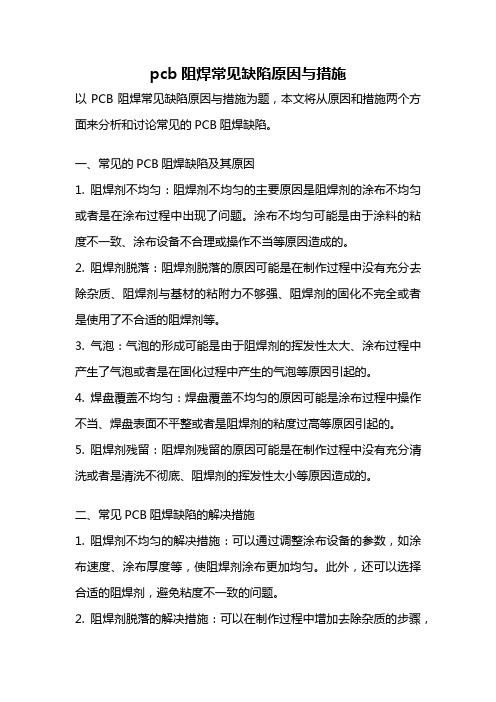
pcb阻焊常见缺陷原因与措施以PCB阻焊常见缺陷原因与措施为题,本文将从原因和措施两个方面来分析和讨论常见的PCB阻焊缺陷。
一、常见的PCB阻焊缺陷及其原因1. 阻焊剂不均匀:阻焊剂不均匀的主要原因是阻焊剂的涂布不均匀或者是在涂布过程中出现了问题。
涂布不均匀可能是由于涂料的粘度不一致、涂布设备不合理或操作不当等原因造成的。
2. 阻焊剂脱落:阻焊剂脱落的原因可能是在制作过程中没有充分去除杂质、阻焊剂与基材的粘附力不够强、阻焊剂的固化不完全或者是使用了不合适的阻焊剂等。
3. 气泡:气泡的形成可能是由于阻焊剂的挥发性太大、涂布过程中产生了气泡或者是在固化过程中产生的气泡等原因引起的。
4. 焊盘覆盖不均匀:焊盘覆盖不均匀的原因可能是涂布过程中操作不当、焊盘表面不平整或者是阻焊剂的粘度过高等原因引起的。
5. 阻焊剂残留:阻焊剂残留的原因可能是在制作过程中没有充分清洗或者是清洗不彻底、阻焊剂的挥发性太小等原因造成的。
二、常见PCB阻焊缺陷的解决措施1. 阻焊剂不均匀的解决措施:可以通过调整涂布设备的参数,如涂布速度、涂布厚度等,使阻焊剂涂布更加均匀。
此外,还可以选择合适的阻焊剂,避免粘度不一致的问题。
2. 阻焊剂脱落的解决措施:可以在制作过程中增加去除杂质的步骤,确保基材的表面干净;同时,选择具有较强粘附力的阻焊剂,并确保其固化完全。
3. 气泡的解决措施:可以选择挥发性较小的阻焊剂,减少气泡的产生;在涂布过程中要注意操作,避免气泡的形成;在固化过程中要控制好温度和时间,确保气泡能够顺利排出。
4. 焊盘覆盖不均匀的解决措施:可以通过调整阻焊剂的粘度,使其更易于涂布;此外,还可以选择合适的涂布工艺和设备,确保阻焊剂能够均匀地覆盖在焊盘表面。
5. 阻焊剂残留的解决措施:在制作过程中要充分清洗阻焊剂,确保其完全去除;可以选择具有较大挥发性的阻焊剂,加快其挥发速度,减少残留。
PCB阻焊常见缺陷的原因有阻焊剂不均匀、阻焊剂脱落、气泡、焊盘覆盖不均匀和阻焊剂残留等。
电阻焊常见问题解决方法

电阻焊常见问题解决方法一、车身点粘电极及炸枪1、前言粘电极是点焊时电极与零件形成非正常焊接而产生的电极与零件的粘连现象。
严重时造成电极被拔出,冷却水外流使零件生锈。
炸枪是点焊时电极与零件之间产生瞬时强电弧并发出爆炸声的异常现象。
这种现象造成电极与零件的烧损,造成浪费。
2.1粘电极的原因(1)两电极工作面不平行。
此情况造成电极工作面与零件局部接触,电极与零件的接触电阻增大,这会使焊接回路的电流有所下降。
但是电流集中于局部接触点,使接触点的电流密度大于正常焊接时电极工作面的电流密度,造成接触点的温度升高到电极与零件的可焊接温度,形成电极与零件的熔合。
(2)电极工作面粗糙。
电极工作面与零件不能完全贴合,只有凸出的一些部位与零件接触。
此情况同样会造成(1)中的情况。
(3)电极压力不足。
接触电阻与压力成反比。
电极压力不足造成电极与零件之间接触电阻增大,接触部位电阻热增加,使电极与零件接触面的温度升高到可焊温度,形成电极与零件熔合连接。
(4)焊枪冷却水出口的水管接反或冷却水循环受阻,电极温度升高,在连续点焊时可造成电极与零件的熔合连接。
2.2粘电极的解决方法(1)修锉电极头,使两电极的工作面平行、表面无粗糙缺陷。
将焊接程序选择为修磨程序(无电流输出),通过空打焊枪来观察两电极工作面是否平行。
(2)在修磨状态下,将焊枪空打5~10次。
目的为锻压两电极的工作面,使其在规定的电极头直径范围内增大接触面积,同时提高表面硬度。
(3)用氧乙炔火焰加热电极的工作面,使电极工作面形成氧化层(氧化铜),氧化铜的热稳定性好,熔点可达1300ºC。
可以提高电极工作面的熔点,同时破坏电极与零件之间的焊接性。
(4)在电极工作面涂以钳工配制的红丹,以破坏电极与零件之间的焊接性。
(5)调整电极压力,使用高压力、大电流、短通电时间的焊接参数。
(6)定期清理冷却水管。
保证冷却水流量。
3.1炸枪的原因(1)电极长度不足。
这种情况下气缸不能将电极推到位,使两电极工作面之间存在间隙。
电阻焊常见问题解决方法

电阻焊常见问题解决方法一、车身点粘电极及炸枪1、前言粘电极是点焊时电极与零件形成非正常焊接而产生的电极与零件的粘连现象。
严重时造成电极被拔出,冷却水外流使零件生锈。
炸枪是点焊时电极与零件之间产生瞬时强电弧并发出爆炸声的异常现象。
这种现象造成电极与零件的烧损,造成浪费。
2.1粘电极的原因(1)两电极工作面不平行。
此情况造成电极工作面与零件局部接触,电极与零件的接触电阻增大,这会使焊接回路的电流有所下降。
但是电流集中于局部接触点,使接触点的电流密度大于正常焊接时电极工作面的电流密度,造成接触点的温度升高到电极与零件的可焊接温度,形成电极与零件的熔合。
(2)电极工作面粗糙。
电极工作面与零件不能完全贴合,只有凸出的一些部位与零件接触。
此情况同样会造成(1)中的情况。
(3)电极压力不足。
接触电阻与压力成反比。
电极压力不足造成电极与零件之间接触电阻增大,接触部位电阻热增加,使电极与零件接触面的温度升高到可焊温度,形成电极与零件熔合连接。
(4)焊枪冷却水出口的水管接反或冷却水循环受阻,电极温度升高,在连续点焊时可造成电极与零件的熔合连接。
2.2粘电极的解决方法(1)修锉电极头,使两电极的工作面平行、表面无粗糙缺陷。
将焊接程序选择为修磨程序(无电流输出),通过空打焊枪来观察两电极工作面是否平行。
(2)在修磨状态下,将焊枪空打5~10次。
目的为锻压两电极的工作面,使其在规定的电极头直径范围内增大接触面积,同时提高表面硬度。
(3)用氧乙炔火焰加热电极的工作面,使电极工作面形成氧化层(氧化铜),氧化铜的热稳定性好,熔点可达1300ºC。
可以提高电极工作面的熔点,同时破坏电极与零件之间的焊接性。
(4)在电极工作面涂以钳工配制的红丹,以破坏电极与零件之间的焊接性。
(5)调整电极压力,使用高压力、大电流、短通电时间的焊接参数。
(6)定期清理冷却水管。
保证冷却水流量。
3.1炸枪的原因(1)电极长度不足。
这种情况下气缸不能将电极推到位,使两电极工作面之间存在间隙。
电阻焊接机对焊接质量的影响因素及控制方法

电阻焊接机对焊接质量的影响因素及控制方法电阻焊接是一种常用的金属焊接方法,广泛应用于工业生产中。
电阻焊接机是实现电阻焊接过程的主要设备之一,其对焊接质量影响较大。
本文将从电阻焊接机的角度,探讨焊接质量的影响因素以及相应的控制方法。
一、影响电阻焊接质量的因素1. 材料选择电阻焊接的材料选择直接影响焊接质量。
在电阻焊接过程中,需要对接的金属材料具有一定的导电性和可焊性。
不同材料之间的相容性和界面特性也会对焊接质量产生影响。
2. 焊接电流焊接电流是影响焊接质量的重要参数之一。
电流大小直接影响焊接接头的热量和金属结晶状态。
如果焊接电流过大,容易造成焊接过热,导致焊缝断裂;而电流过小,则会导致焊接接头强度不足。
3. 焊接时间焊接时间是指电流通过焊接接头所需的时间。
焊接时间过长可能导致接头过热,焊接质量下降;而时间过短则可能导致接头焊接不牢固,焊缝出现裂纹。
4. 电极压力电极压力是控制焊接接头的质量的重要参数之一。
适当的电极压力能够保证接头与电极之间的充分接触,加强导电性,提高焊接接头的强度。
电极压力过大或过小都会对焊接质量产生不良影响。
5. 焊接环境焊接环境的气氛对焊接质量也有一定影响。
在某些特殊环境下,如高温、高湿度、有腐蚀性气体等环境下进行焊接,可能会导致焊接接头出现气孔、熔洞等缺陷。
6. 焊接设备状态焊接设备的运行状态和性能也对焊接质量有直接影响。
如果电阻焊接机的电流不稳定、电极磨损严重,都会导致焊接质量下降。
二、电阻焊接质量的控制方法1. 严格控制焊接参数合理选择焊接材料,控制焊接电流和电压,确保电极间的良好接触,并保持焊接时间适中。
通过严格控制这些参数,可以提高焊接质量,并确保焊接接头的牢固性。
2. 定期维护与检查焊接设备定期对电阻焊接设备进行维护保养,检查电极磨损情况,保证设备正常运行。
合理安排焊机的使用周期,避免设备过度磨损,及时更换磨损严重的电极,以确保焊接质量始终稳定。
3. 提供良好的焊接环境在进行电阻焊接时,应确保焊接环境干燥、清洁,避免湿度过高或有腐蚀性气体的存在。
常见焊接缺陷及防止措施
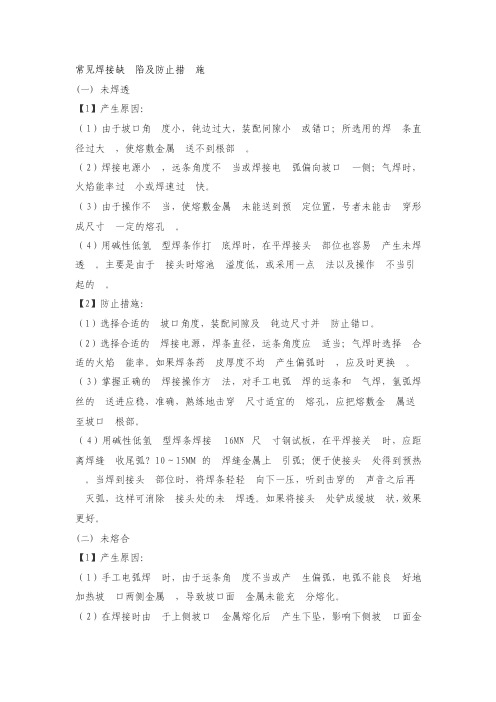
常见焊接缺陷及防止措施(一) 未焊透【1】产生原因:(1)由于坡口角度小,钝边过大,装配间隙小或错口;所选用的焊条直径过大,使熔敷金属送不到根部。
(2)焊接电源小,远条角度不当或焊接电弧偏向坡口一侧;气焊时,火焰能率过小或焊速过快。
(3)由于操作不当,使熔敷金属未能送到预定位臵,号者未能击穿形成尺寸一定的熔孔。
(4)用碱性低氢型焊条作打底焊时,在平焊接头部位也容易产生未焊透。
主要是由于接头时熔池溢度低,或采用一点法以及操作不当引起的。
【2】防止措施:(1)选择合适的坡口角度,装配间隙及钝边尺寸并防止错口。
(2)选择合适的焊接电源,焊条直径,运条角度应适当;气焊时选择合适的火焰能率。
如果焊条药皮厚度不均产生偏弧时,应及时更换。
(3)掌握正确的焊接操作方法,对手工电弧焊的运条和气焊,氩弧焊丝的送进应稳,准确,熟练地击穿尺寸适宜的熔孔,应把熔敷金属送至坡口根部。
(4)用碱性低氢型焊条焊接16MN尺寸钢试板,在平焊接关时,应距离焊缝收尾弧?10~15MM的焊缝金属上引弧;便于使接头处得到预热。
当焊到接头部位时,将焊条轻轻向下一压,听到击穿的声音之后再灭弧,这样可消除接头处的未焊透。
如果将接头处铲成缓坡状,效果更好。
(二) 未熔合【1】产生原因:(1)手工电弧焊时,由于运条角度不当或产生偏弧,电弧不能良好地加热坡口两侧金属,导致坡口面金属未能充分熔化。
(2)在焊接时由于上侧坡口金属熔化后产生下坠,影响下侧坡口面金属的加热熔化,造成“冷接”。
(3)横接操作时,在上、下坡口面击穿顺序不对,未能先击穿下坡口后击穿上坡口,或者在上、下坡口面上击穿熔孔位臵未能错开一定的距离,使上坡口熔化金属下坠产生粘接,造成未熔合。
(4)气悍时火焰能率小,氩弧焊时电弧两侧坡口的加热不均,或者坡口面存在污物等。
电阻焊常见缺陷及产生原因
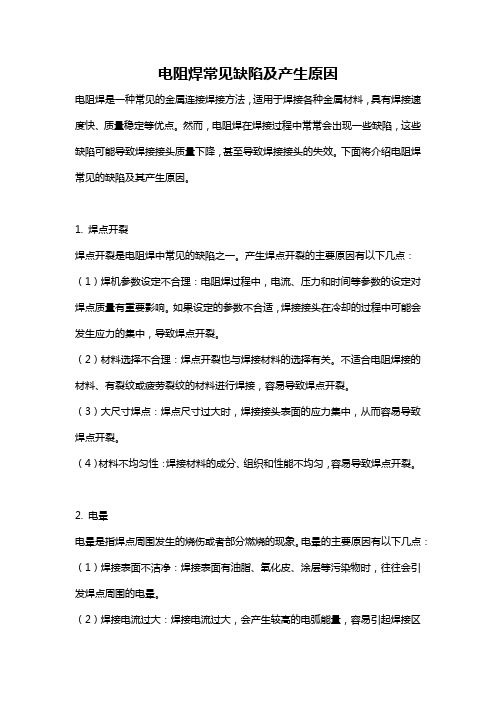
电阻焊常见缺陷及产生原因电阻焊是一种常见的金属连接焊接方法,适用于焊接各种金属材料,具有焊接速度快、质量稳定等优点。
然而,电阻焊在焊接过程中常常会出现一些缺陷,这些缺陷可能导致焊接接头质量下降,甚至导致焊接接头的失效。
下面将介绍电阻焊常见的缺陷及其产生原因。
1. 焊点开裂焊点开裂是电阻焊中常见的缺陷之一。
产生焊点开裂的主要原因有以下几点:(1)焊机参数设定不合理:电阻焊过程中,电流、压力和时间等参数的设定对焊点质量有重要影响。
如果设定的参数不合适,焊接接头在冷却的过程中可能会发生应力的集中,导致焊点开裂。
(2)材料选择不合理:焊点开裂也与焊接材料的选择有关。
不适合电阻焊接的材料、有裂纹或疲劳裂纹的材料进行焊接,容易导致焊点开裂。
(3)大尺寸焊点:焊点尺寸过大时,焊接接头表面的应力集中,从而容易导致焊点开裂。
(4)材料不均匀性:焊接材料的成分、组织和性能不均匀,容易导致焊点开裂。
2. 电晕电晕是指焊点周围发生的烧伤或者部分燃烧的现象。
电晕的主要原因有以下几点:(1)焊接表面不洁净:焊接表面有油脂、氧化皮、涂层等污染物时,往往会引发焊点周围的电晕。
(2)焊接电流过大:焊接电流过大,会产生较高的电弧能量,容易引起焊接区域局部温度过高,从而导致电晕的发生。
(3)焊接参数设定不合理:焊接过程中,电流、压力和时间等参数的设定不合理,也会导致电晕的发生。
3. 气孔气孔是指焊接接头中产生的孔洞状缺陷。
气孔的产生原因主要有以下几点:(1)焊接区域含有气体:焊接区域杂质、氧化物或者其他含气体的物质,会在焊接过程中释放出气体,进而产生气孔。
(2)焊接材料含水量高:焊接材料含有过多的水分,焊接过程中蒸发的水分会形成气泡,从而形成气孔。
(3)焊接区域氧气过量:焊接区域的氧气含量过高,氧气和金属之间的反应会产生气体,并形成气孔。
4. 金属飞溅金属飞溅是指焊接过程中,熔融金属在电极与焊件之间产生的喷溅现象。
金属飞溅的产生原因主要有以下几点:(1)电流过大:焊接电流过大,熔融金属的喷溅量会增加,从而导致金属飞溅的产生。
电阻焊常见缺陷及产生原因
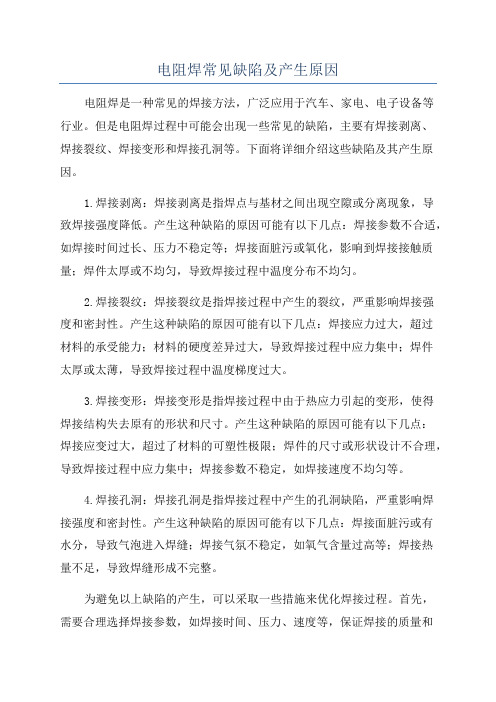
电阻焊常见缺陷及产生原因电阻焊是一种常见的焊接方法,广泛应用于汽车、家电、电子设备等行业。
但是电阻焊过程中可能会出现一些常见的缺陷,主要有焊接剥离、焊接裂纹、焊接变形和焊接孔洞等。
下面将详细介绍这些缺陷及其产生原因。
1.焊接剥离:焊接剥离是指焊点与基材之间出现空隙或分离现象,导致焊接强度降低。
产生这种缺陷的原因可能有以下几点:焊接参数不合适,如焊接时间过长、压力不稳定等;焊接面脏污或氧化,影响到焊接接触质量;焊件太厚或不均匀,导致焊接过程中温度分布不均匀。
2.焊接裂纹:焊接裂纹是指焊接过程中产生的裂纹,严重影响焊接强度和密封性。
产生这种缺陷的原因可能有以下几点:焊接应力过大,超过材料的承受能力;材料的硬度差异过大,导致焊接过程中应力集中;焊件太厚或太薄,导致焊接过程中温度梯度过大。
3.焊接变形:焊接变形是指焊接过程中由于热应力引起的变形,使得焊接结构失去原有的形状和尺寸。
产生这种缺陷的原因可能有以下几点:焊接应变过大,超过了材料的可塑性极限;焊件的尺寸或形状设计不合理,导致焊接过程中应力集中;焊接参数不稳定,如焊接速度不均匀等。
4.焊接孔洞:焊接孔洞是指焊接过程中产生的孔洞缺陷,严重影响焊接强度和密封性。
产生这种缺陷的原因可能有以下几点:焊接面脏污或有水分,导致气泡进入焊缝;焊接气氛不稳定,如氧气含量过高等;焊接热量不足,导致焊缝形成不完整。
为避免以上缺陷的产生,可以采取一些措施来优化焊接过程。
首先,需要合理选择焊接参数,如焊接时间、压力、速度等,保证焊接的质量和强度。
其次,要保证焊接面的清洁和氧化处理,提高焊接接触质量。
此外,还需合理设计焊接结构和尺寸,避免应力集中和变形。
最后,要保证焊接热量的充分供应,避免焊缝产生缺陷。
总之,电阻焊过程中常见的缺陷包括焊接剥离、焊接裂纹、焊接变形和焊接孔洞等。
产生这些缺陷的原因多种多样,包括焊接参数不合适、焊件质量差、焊接应力过大等。
为减少这些缺陷的发生,需要优化焊接过程,包括合理选择焊接参数、保证焊接接触质量、设计合理的焊接结构和尺寸等。
电阻焊(点焊)产品质量缺陷及解决方法
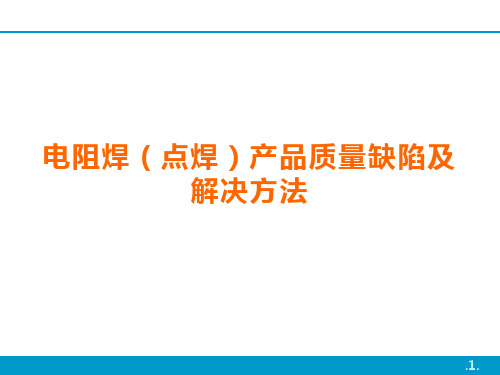
.4.
电阻焊的工作程序
电阻焊三要素
➢ 焊接电流 ➢ 加压力 ➢ 通电时间
.5.
二、电阻焊的主要过程参数与控制
焊接电流
由热量公式Q = I2Rt,可见电流对产热 的影响比电阻R和时间 t两者都大。因此焊 接时必须保证焊接电流的适宜和稳定。
焊接时电流选用应接近C点处,抗剪强 度增加缓慢,越过C后,由于飞溅或工件 表面压痕过深,抗剪强度会明显降低
.22.
铝合金的点焊
电导率和热导率较高:必须采用较大电流和较短时间,才能做到既有足够的热量形成熔核;又能减少表面过热、避免电极粘附和 电极铜离子向纯铝包复层扩散、降低接头的抗腐蚀性。塑性温度范围窄、线膨胀系数大:必须采用较大的电极压力,电极随动性 好,才能避免熔核凝固时,因过大的内部拉应力而引起的裂纹。也可以采用在焊接脉冲之后加缓冷脉冲的方法避 免裂纹。表面易生成氧化膜:焊前必须严格清理,否则极易引起飞溅和熔核成形不良,使焊点强度降低。 铝合金点焊时,由于电流密度大和氧化膜的存在,很容易产生电极粘着,不仅影响外观质量,还会因电流减小而降低接头强度,为此 需经常修整电极。
将给、排水用的橡胶管牢固连接在焊机本体侧面的给水口和进水口处。 请使用不含杂质尤其是盐份的优质水。(电阻率大于5K.cm)
压缩空气系统的装配
清除金属切管上的切削、灰尘后将进气胶管牢固连接在焊机本 体的进气口上。 气压应确保为5 ~ 7 kgf / cm2,胶管耐压大于7 kgf / cm2。 为延长焊机使用寿命,请使用干燥雾气小的优质空气。
4500 5000 5500 6500 7200 7700 9100 10300 11300 12900
3.2 3.5 4.0 4.5 5.0 5.5 6.3 7.0
- 1、下载文档前请自行甄别文档内容的完整性,平台不提供额外的编辑、内容补充、找答案等附加服务。
- 2、"仅部分预览"的文档,不可在线预览部分如存在完整性等问题,可反馈申请退款(可完整预览的文档不适用该条件!)。
- 3、如文档侵犯您的权益,请联系客服反馈,我们会尽快为您处理(人工客服工作时间:9:00-18:30)。
h
16
电焊质量控制方法
5、焊点边界样本 是一种目视的质量标准,如图1-5所示,员工可以通过培训学习,更为形象地认识合格 与不合格焊点,防止缺陷焊点出现及遗漏。
h
17
电焊质量控制方法
6、超声波检测 是一种新兴的检测方法,如图1-5所示。经验证,发现超声波技术对电阻焊进行无损检查 效率高,而且几乎能够识别各种有缺陷焊点,因此超声波检测越来越多用于各个汽车厂 家。超声波检测缺点在于不能在线检测,需要专人检测,优点是可以识别各种类型缺陷 焊点。
Circumference Crack are
Discrepant. 周遍裂缝不允许
h
7
常见电焊缺陷
3.焊穿
Holes through the
weld are Discrepant. 穿孔是不允许的
h
8
常见电焊缺陷
4.边缘焊点(没有包括钢板所有边缘部分的焊点)
Not OK不好
F E
D
Acceptable 可接受
h
18
谢谢!
h
19
Min Nugget Req. 焊点直径最小值
3.0 mm 3.5 mm 4.0 mm 4.5 mm 5.0 mm 5.5 mm 6.0 mm 6.5 mm 7.0 mm
d D
熔核直径 = D+d 2
h
d D
6
常见电焊缺陷
2.裂缝
Surface Crack confined within the impression left by the electrode. 通过电极产生的内部表 面裂缝
h
3
电阻焊介绍
Heat =I2RT
• 电阻点焊时,热量是由焊接电流和焊件间的接触电阻形成的, 大小由焦耳-楞次定律决定.
• 钢铁的电阻值范围是60到150微欧. • 电阻焊接钢铁的焊接电流范围是7000-18000安培 • 焊接时间范围是8到48个周波(1周波=0.02秒)
h
4
电阻焊介绍 什么是电阻点焊的三大要素? 电流 – 压力 – 时间
焊接非坏性检 查
h
13
电焊质量控制方法
2、焊接破坏性检查:
利用液压张力钳或气动凿子将所有焊点全 部撕开。如在一件母材上留下撕洞,在另一件 母材上附有焊核,且焊核尺寸符合标准要求, 则此焊点合格,否则为不合格。可借助游标卡 尺或直尺对焊核尺寸进行测量。
h
14
电焊质量控制方法
3、焊点试片检查 焊点试片检查主要用于非破坏性检查无法或不方便检查的焊点。试片的厚度根据所检查焊点 的钣金厚度进行选择,厚度一般为0.8~1.4mm。
C B
A
h
9
常见电焊缺陷 5.位置偏差的焊点
要求的4焊点
6.Extra多余的
要求4焊点
.当图纸上没有给出尺寸时公差范围是±20毫米,给出尺 寸时是±10毫米
h
2个多余的焊点,工艺需要调 整
10
常见电焊缺陷 7.钢板变形超过25度的焊点
与垂直面角度大于25 °的焊点会扭曲,必须调整焊接工艺
Angle of Distortion扭曲角度
h
15
电焊质量控制方法
4、焊接参数检测 一般来说焊点质量监控可分为预防、监控和检验。预防指的是,在没有进行焊接之前,采取相应的措 施防止不合格焊点的产生。焊接参数检测就是预防的有效措施之一,比如定期检查焊枪电流、压力及 通电时间,以保证电流、压力及通电时间符合工艺要求。一般来说检测的频次为关键焊点1次/月,非 关键焊点1次/2月或1次/季度。
h
5
常见电焊缺陷
1.虚焊(无熔核或熔核尺寸小于4mm)
Thinnest Sheet 薄板尺寸
0.40 - 0.59 0.60 - 0.79 0.80 - 1.39 1.40 - 1.99 2.00 - 2.49 2.50 - 2.99 3.00 - 3.49 3.50 - 3.99 4.00 - 4.50
> 25° Not Ok
h
11
常见电焊缺陷
8.压坑过深的焊点(材料厚度减少50%)
BA
A/B > 50% No Ok C/D > 50% No Ok
9.漏焊
CD
h
12
电焊质量控制方法
1、焊接非破坏性检查:
采取各种物理的、目视的和量具等手段,不损坏被检查焊接性能和完整性而检查其焊接缺陷的检 验方法。
电阻焊常见缺陷及控制方法
h
1
车身车间运作过程
车身车间
零部件
零件拼装
如何控制白车身质量?(从哪几方面?)
➢焊接质量控制
➢涂胶质量控制
➢尺寸控制
➢选装件
➢扭矩控制
➢表面质量控制
h
电阻焊在车身车间 有什么作用?
白车身
2
电阻焊介绍
什么是电阻点焊?
电阻点焊是对两层或两层以上的金属板材加压并保持,同 时进行通电加热,以获得金属熔核的一种焊接方法。