化工厂危险源辨识、风险分级管控资料
化工厂主要危险源及防范

化工厂主要危险源及防范第一篇:化工厂主要危险源及防范化工厂主要危险源及防范2.1一氧化碳2.1.1外观与性状一氧化碳纯品为无色、无臭、无刺激性的气体。
易燃易爆,与空气混合能形成爆炸性混合物,遇明火、高热能引起燃烧爆炸。
2.1.2对健康影响一氧化碳进入人体之后会和血液中的血红蛋白结合,由于CO与血红蛋白结合能力远强于氧气与血红蛋白的结合能力,进而使能与氧气结合的血红蛋白数量急剧减少,从而引起机体组织出现缺氧,导致人体窒息死亡。
因此一氧化碳具有毒性。
一氧化碳是无色、无臭、无味的气体,故易于忽略而致中毒。
(1)轻度中毒。
患者可出现头痛、头晕、失眠、视物模糊、耳鸣、恶心、呕吐、全身乏力、心动过速、短暂昏厥。
(2)中度中毒。
除上述症状加重外,口唇、指甲、皮肤粘膜出现樱桃红色,多汗,血压先升高后降低,心率加速,心律失常,烦躁,一时性感觉和运动分离(即尚有思维,但不能行动)。
症状继续加重,可出现嗜睡、昏迷。
(3)重度中毒。
患者迅速进入昏迷状态。
初期四肢肌张力增加,或有阵发性强直性痉挛;晚期肌张力显著降低,患者面色苍白或青紫,血压下降,瞳孔散大,最后因呼吸麻痹而死亡。
经抢救存活者可有严重合并症及后遗症。
2.1.3急救措施迅速撤离泄漏污染区人员至上风处,并立即隔离150m,严格限制出入。
切断火源。
应急处理人员戴自给正压式呼吸器,穿防静电工作服。
尽可能切断泄漏源。
合理通风,加速扩散。
吸入:迅速脱离现场至上风口或空气新鲜处。
保持呼吸道通畅。
如呼吸困难,给予输氧。
呼吸心跳停止时,立即进行人工呼吸和胸外心脏按压术。
就医。
2.1.4灭火方法灭火方法:切断气源。
若不能切断气源,则不允许熄灭泄漏处的火焰。
喷水冷却容器,灭火剂:雾状水、泡沫、二氧化碳、干粉。
2.1.5主要存在地点甲醇合成、净化、硫回收、气化、变换热回收、渣水处理。
2.1.6防范措施不带火种进入现场,动火作业按要求办理动火票,进容器作业要求办理容器内作业票,现场工作时要求工艺人员监护,带CO气体报警仪。
化工厂安全生产风险分级管控资料
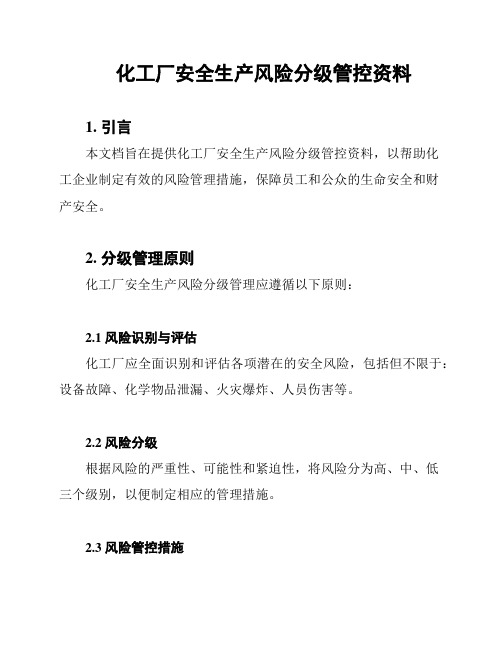
化工厂安全生产风险分级管控资料1. 引言本文档旨在提供化工厂安全生产风险分级管控资料,以帮助化工企业制定有效的风险管理措施,保障员工和公众的生命安全和财产安全。
2. 分级管理原则化工厂安全生产风险分级管理应遵循以下原则:2.1 风险识别与评估化工厂应全面识别和评估各项潜在的安全风险,包括但不限于:设备故障、化学物品泄漏、火灾爆炸、人员伤害等。
2.2 风险分级根据风险的严重性、可能性和紧迫性,将风险分为高、中、低三个级别,以便制定相应的管理措施。
2.3 风险管控措施根据风险等级,制定相应的风险管控措施,包括但不限于:安全培训、设备维护保养、应急预案制定、安全设备配备等。
2.4 定期评估和改进定期评估风险管理效果,并根据评估结果进行改进和完善,确保风险的管控措施可行有效。
3. 风险分级指南下面是一些可能存在于化工厂的风险及其分级指南:3.1 高级别风险- 设备故障导致的严重人员伤害或财产损失- 严重的化学物泄漏或火灾爆炸- 缺乏有效的安全管理措施和应急预案3.2 中级别风险- 设备故障可能导致的轻微人员伤害或财产损失- 化学物泄漏可能导致的中等程度的污染或安全威胁- 安全管理措施和应急预案需要进一步完善和改进3.3 低级别风险- 设备故障可能导致的轻微财产损失- 化学物泄漏可能导致的轻微污染,但无安全威胁- 安全管理措施和应急预案已基本可行4. 风险管控资料化工厂应编制并保持以下风险管控资料的完整性和及时性:- 风险识别与评估报告- 风险分级记录表- 风险管控措施计划- 应急预案及演练记录- 设备维护保养记录- 安全培训档案5. 结论化工厂安全生产风险分级管控资料的制定和实施对于保障员工和公众的安全至关重要。
化工企业应按照本文档提供的原则和指南,制定相应的风险管控措施,并定期评估和改进。
只有通过科学有效的风险管理,化工企业才能做到安全生产、可持续发展。
*请注意,以上内容仅供参考,并应根据具体情况进行调整和完善。
化工厂危险源辨识、风险分级管控资料

低风险
40
未断电
触电
漏电保护装置
停机后关闭电源及相关阀门。对现场及设备进行清理,确保现场整洁
2
3
6
4
低风险
41
蒸煮岗位作业
准备
误操作,接触运转或带电部位
触电、机械伤害
危险部位有防护罩。漏电保护装置
检查时,严禁通电,开启设备
1.三级安全教育培训,考核合格。2.进行年度安全教育培训,考核合格
配备防静电服、口罩、防护手套
车辆驶入
车辆超速,停车后滑动
车辆伤害
/
1.专人引导。2.厂区门口设置限速等警示标识。3.车辆停放严禁越线。停车、熄火,拉起制动手刹
1.三级安全教育培训,考核合格。2.进行年度安全教育培训,考核合格
配备安全帽、口罩、防护手套
1.制定应急预案,定期演练。2.立即停止作业及设备运行。3.事故发生时,将受伤者转移至安全区域进行抢救并就医
生产车间
生产车间
特定时间进行
2.1工作危害分析(JHA+LS)评价记录(生产作业)
序号
作业步骤
危险源或潜在事件
主要后果
现有控制措施
L
S
R
评价级别
风险分级
建议改进(新增)措施
备注
工程技术措施
管理措施
培训教育措施
个体防护措施
应急处置措施
1
硫酸卸车作业
车辆驶入
车辆超速,停车后滑动
车辆伤害
/
1.厂区内限速5公里。引导车辆进入卸车区,熄火,上交钥匙。垫上止滑木块。
活动频率
备注
1
生产作业
硫酸卸车作业
引导车辆进入、连接软管、开启阀门、泵等设备卸料,结束后清理
石油化工企业安全风险辨识分级管控清单
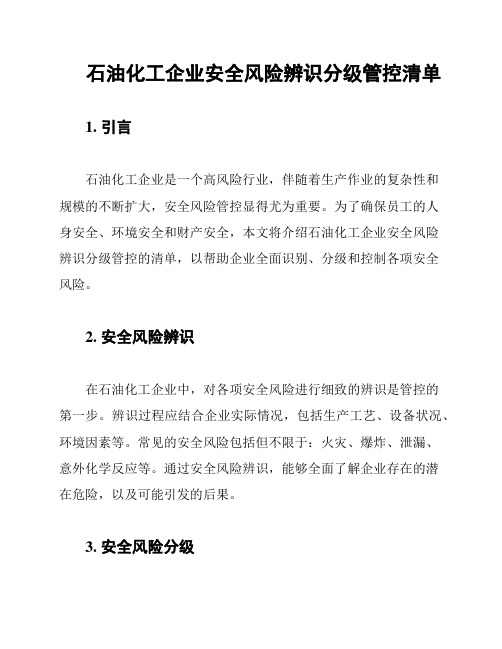
石油化工企业安全风险辨识分级管控清单1. 引言石油化工企业是一个高风险行业,伴随着生产作业的复杂性和规模的不断扩大,安全风险管控显得尤为重要。
为了确保员工的人身安全、环境安全和财产安全,本文将介绍石油化工企业安全风险辨识分级管控的清单,以帮助企业全面识别、分级和控制各项安全风险。
2. 安全风险辨识在石油化工企业中,对各项安全风险进行细致的辨识是管控的第一步。
辨识过程应结合企业实际情况,包括生产工艺、设备状况、环境因素等。
常见的安全风险包括但不限于:火灾、爆炸、泄漏、意外化学反应等。
通过安全风险辨识,能够全面了解企业存在的潜在危险,以及可能引发的后果。
3. 安全风险分级针对辨识出的安全风险,需要进行分类和分级。
通常,将安全风险分为高、中、低三个级别,并根据不同级别采取相应的管控措施。
下面是针对不同级别安全风险的一些建议:3.1 高风险级别高风险级别的安全风险可能导致重大伤亡、环境破坏以及巨大经济损失。
对于高风险级别的安全风险,石油化工企业应特别重视,并采取以下措施:- 建立完善的应急预案并进行定期演练;- 使用高可靠性的设备和材料,在设计阶段就考虑安全性;- 加强现场监测和控制措施,及时预警和处置危险情况;- 加强员工培训,确保员工具备应对高风险情况的能力。
3.2 中风险级别中风险级别的安全风险可能导致较大的伤亡、环境破坏和经济损失。
对于中风险级别的安全风险,石油化工企业应采取以下措施:- 制定详细的安全操作规程,确保操作人员按照规定进行作业;- 增加设备维护和检修频率,及时发现并修复潜在危险;- 加强现场巡查和安全检查,及时发现并处理安全隐患;- 原则上不允许非授权人员进入一些危险区域;- 注重设备和生产过程的监测和记录,及时调整控制参数。
3.3 低风险级别低风险级别的安全风险可能导致较小的伤害、环境污染和经济损失。
对于低风险级别的安全风险,石油化工企业应仍予以重视,并采取以下措施:- 定期检查和维护设备,确保其正常运转;- 配置相应的消防设备,并进行定期检验;- 加强员工安全意识培训,确保他们了解并遵守相关安全规定;- 做好设备日常巡检和记录,及时发现并处理潜在问题。
危险化工厂危险源辨识与风险评价清单
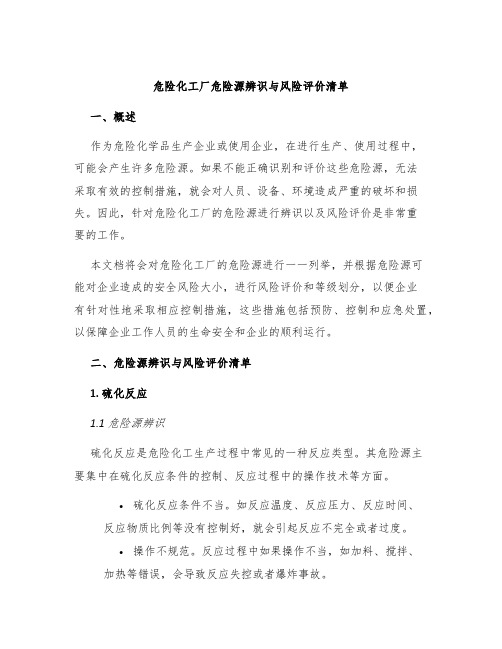
危险化工厂危险源辨识与风险评价清单一、概述作为危险化学品生产企业或使用企业,在进行生产、使用过程中,可能会产生许多危险源。
如果不能正确识别和评价这些危险源,无法采取有效的控制措施,就会对人员、设备、环境造成严重的破坏和损失。
因此,针对危险化工厂的危险源进行辨识以及风险评价是非常重要的工作。
本文档将会对危险化工厂的危险源进行一一列举,并根据危险源可能对企业造成的安全风险大小,进行风险评价和等级划分,以便企业有针对性地采取相应控制措施,这些措施包括预防、控制和应急处置,以保障企业工作人员的生命安全和企业的顺利运行。
二、危险源辨识与风险评价清单1. 硫化反应1.1 危险源辨识硫化反应是危险化工生产过程中常见的一种反应类型。
其危险源主要集中在硫化反应条件的控制、反应过程中的操作技术等方面。
•硫化反应条件不当。
如反应温度、反应压力、反应时间、反应物质比例等没有控制好,就会引起反应不完全或者过度。
•操作不规范。
反应过程中如果操作不当,如加料、搅拌、加热等错误,会导致反应失控或者爆炸事故。
1.2 风险评价硫化反应的不当操作,有可能引发很大的安全事故,导致人员伤亡、环境污染和设备破坏等问题。
根据事故可能带来的影响程度,将硫化反应的风险等级划分为三级:•一级:可能导致人员重伤或死亡,环境受到很大污染,设备严重损坏。
•二级:可能导致人员轻伤或死亡,环境受到较大污染,设备严重损坏。
•三级:可能导致人员受伤,环境受到轻度污染,设备受到轻微损坏。
1.3 控制措施对于硫化反应的控制措施,可以分为预防、控制和应急处置三部分。
•预防措施:加强硫化反应的安全技术培训,加强现场管理和现场监控,提高操作人员的安全意识。
•控制措施:加强现场巡视和监控,实时监测反应温度、压力等参数,加强安全隔离措施,对可能存在的危险源进行及时排查。
•应急处置措施:建立相应的事故预案和应急机制,提高应急处理的能力,组织及时有效的应急处置措施,以最小化事故对人员、设备和环境的危害。
化工厂危险源辨识与风险评价信息

化工厂危险源辨识与风险评价信息一、危险源辨识1.原料与中间体危险源:a)挥发性有机物:化工厂使用的大多数原料和中间体都属于挥发性有机物,如果泄漏或不当储存,可能导致火灾、爆炸等危险。
b)毒害性原料:一些原料和中间体具有毒害性,可能对工人健康造成危害,尤其是接触或吸入高浓度的情况下。
c)可燃物料:在化工厂内广泛使用的可燃物料,如气体、液体和固体,一旦泄漏或遇到火源,可能引发火灾、爆炸。
2.过程操作危险源:a)高温与高压:一些过程操作要求在高温和高压下进行,如果操作不当或设备失效,可能导致压力容器爆裂、管道破裂等严重事故。
b)化学反应:化工厂进行的化学反应可能产生剧烈的热效应,导致过热、爆炸等危险情况。
c)静电:由于化工厂操作中常产生静电,如果未进行适当的防范措施,静电可能引发火灾、爆炸等事故。
3.设备与装置危险源:a)不良设备:化工厂使用的生产设备、容器和管道如果存在设计缺陷、损伤或缺乏维护,可能导致泄漏、破裂等危险情况。
b)电气设备:如电气线路不符合安全标准、过载、漏电等问题,可能引发火灾、触电等事故。
c)高空作业:化工厂内进行的高空作业,如吊装、维修等,存在坠落、身体碰撞等风险。
4.环境危险源:a)废水、废气:化工厂的废水、废气中可能含有大量的有毒有害物质,对周围环境和生态系统造成污染和伤害。
b)噪声与振动:一些化工厂操作过程可能产生噪声和振动,对周围环境和工人的身体健康产生负面影响。
二、风险评价1.对风险概率的评价:a)重大风险:对于已发生过多起事故的危险源或已知存在的重大隐患,其发生概率较高,风险评估为重大。
b)较大风险:对于危险源或隐患存在可能导致事故的情况,其发生概率一般,风险评估为较大。
c)一般风险:对于危险源或隐患存在较低的风险,其发生概率较低,风险评估为一般。
2.对风险后果的评价:a)严重风险:对于已知后果重大或可能导致人员伤亡、设备损坏等重大后果的危险源,其风险评估为严重。
b)一般风险:对于可能导致一般程度的人员伤害、设备损坏等后果的危险源,其风险评估为一般。
石油化工企业安全风险辨识分级管控清单
石油化工企业安全风险辨识分级管控清单1. 简介本清单旨在帮助石油化工企业辨识和管理安全风险,确保安全生产和员工健康。
清单包括以下内容:辨识安全风险的步骤、分级管控措施以及建立有效的风险管理体系。
2. 辨识安全风险的步骤石油化工企业应按照以下步骤辨识安全风险:2.1 系统分析分析企业所涉及的各个环节和系统,包括生产流程、设备、职工安全意识等,确定可能存在的风险点和事故隐患。
2.2 事件树分析通过事件树分析对已识别的风险进行进一步评估,建立事件发展的逻辑模型,确定各个事件的概率和后果。
2.3 定性分析基于对已有数据的分析,对各个事件进行定性评估,确定其风险等级和优先级。
2.4 定量分析如果条件允许,可以进行定量分析,通过数学模型计算出风险的具体数值,辅助决策和优化管控措施。
3. 分级管控措施根据辨识的风险等级和优先级,采取相应的管控措施,确保风险得到合理的管理。
3.1 高风险的控制措施针对高风险事件,采取最严格的控制措施,包括但不限于:设立专人负责、加强设备检查和维护、加强培训和意识教育、实施紧急预案等。
3.2 中风险的控制措施针对中风险事件,采取适当的控制措施,包括但不限于:加强监测和检测、改进操作流程、加强安全检查和巡视等。
3.3 低风险的控制措施针对低风险事件,采取基本的控制措施,包括但不限于:明确职责和权限、制定标准操作规程、加强信息管理和记录等。
4. 建立风险管理体系石油化工企业应建立完善的风险管理体系,包括以下要素:4.1 风险辨识和评估明确辨识安全风险的方法和步骤,建立风险评估的标准和指标。
4.2 风险管控制定针对不同风险等级的管控措施,明确责任和权利,建立有效的监督和考核机制。
4.3 事故应急预案制定全面的事故应急预案,明确各个环节和部门的职责和流程。
4.4 持续改进建立持续改进机制,不断优化风险管理体系,提高企业安全管理水平。
5. 结论通过使用本清单,石油化工企业能够辨识和管理安全风险,确保安全生产和员工健康。
化工厂危险源辨识表与风险评价表
化工厂危险源辨识表与风险评价表1. 引言本文档旨在为化工厂提供一份完整的危险源辨识表与风险评价表,以便对工厂内存在的潜在危险源进行全面的辨识和评价,从而采取相应的预防和控制措施,保障工人和环境的安全。
2. 危险源辨识表2.1. 危险源辨识指南在进行危险源辨识时,请参考以下指南:- 仔细观察和分析化工厂的各个环节和工艺过程,寻找可能存在的危险源;- 考虑化学品的性质、储存方式、工艺处理方法等因素,寻找潜在的安全风险;- 参考相关法律法规和标准,对各类危险源进行分类和辨识。
2.2. 危险源辨识清单以下是常见的化工厂可能存在的危险源清单:- 化学品存储区域- 高温设备和高压- 处理有毒物质的工艺设备- 高能源设备,如锅炉和发电机组- 火源和爆炸源- 电气设备和线路- 噪音和振动源- 人为操作错误和事故风险3. 风险评价表3.1. 风险评价指南在进行风险评价时,请参考以下指南:- 综合考虑危险源的潜在风险和可能造成的后果;- 评估可能导致事故发生的概率和频率;- 考虑已有的防护措施和安全管理系统;- 依据相关法律法规和标准,对风险进行定性和定量评价。
3.2. 风险评价表格风险评价表格应包含以下内容:- 危险源的描述- 潜在风险和可能造成的后果- 事故发生的概率和频率- 已有的防护措施- 风险等级评定4. 结论通过全面的危险源辨识和风险评价,化工厂可以及时发现潜在的危险源和安全风险,并采取相应的措施进行预防和控制。
本文档提供了一份完整的危险源辨识表与风险评价表作为参考,化工厂可以根据自身情况进行调整和完善。
保障工人和环境的安全是化工厂的首要任务。
化工厂危险源辨识与风险评价信息
化工厂危险源辨识与风险评价信息化工厂是危险物品储存、生产以及加工的场所,危险因素非常多。
化工厂的事故不但极具危害性,而且容易失控或扩大,威胁到员工的安全及周边居民的生命财产安全。
因此,化工厂在生产过程中必须对危险源进行辨识并进行风险评价,以确保生产过程中的安全。
1. 危险源辨识危险源是导致事故和灾害发生的各种因素,只有了解和确定了危险源才能够针对不同的危险与风险制定有效的控制措施。
化工厂危险源辨识的主要内容包括:(1)物质危险源:各种危险化学品、爆炸品、易燃易爆物品等。
(2)设备危险源:各种生产设备、储罐、管道系统、加工设备等。
(3)人员危险源:员工在生产中的操作不当、职业病卫生等因素。
(4)环境危险源:周边自然环境和人类活动环境的影响因素。
(5)管理危险源:各种管理制度不完善、责任认定不明确等因素。
对于确定危险源,需要综合考虑化工厂的生产过程和现有的风险评价数据等信息,采用专业的危险源辨识方法和工具进行分析和判断。
2. 风险评价风险评价是一种从灾害链的各环节分别分析其可能发生的程度、频率和后果的一种分析方法。
风险评价主要分为三个方面的内容:(1)危险源识别:确定所有可能导致有害事件或事故发生的物质、设备或行为、作业等。
(2)风险分析:在危险源识别的基础上,分析导致事故发生的最相关环节,确定每一个环节的发生频率和危害程度。
(3)风险评估:基于危险源和风险分析结果,判断在一定时间内,能否有害事件或事故发生的概率和后果的一种预测方法。
风险评价可以帮助企业全面了解危险源的属性、性质、危险性等,并结合实际情况,制定相应的风险控制措施及应急措施,保障企业员工的生命财产安全,确保生产的可持续发展。
化工企业安全风险分级管控成套资料
化工企业安全风险分级管控成套资料一、概述化工企业是一类高危行业,面临着各种安全风险。
为了确保生产过程的安全和员工的健康,企业需要采取有效的风险分级管控措施。
本文档旨在提供化工企业安全风险分级管控的成套资料,帮助企业了解和应对潜在的安全风险。
二、安全风险分级化工企业的安全风险可以分为不同级别,依据风险的严重程度划分,常见的分类如下:1. 高风险级别高风险级别的安全风险是指对企业的生产、员工的健康和环境造成严重威胁的风险。
这些风险可能导致事故、污染、火灾等严重后果。
对于高风险级别的安全风险,企业需要采取最严格的管控措施,确保其得到有效控制。
2. 中风险级别中风险级别的安全风险是指对企业的生产和员工的健康可能造成较大威胁的风险。
这些风险可能导致轻微事故、污染或火灾等后果。
对于中风险级别的安全风险,企业需要制定相应的管控计划和应急预案,确保风险得到合理控制和处理。
3. 低风险级别低风险级别的安全风险是指对企业的生产和员工的健康可能造成较小威胁的风险。
这些风险可能导致一些轻微的操作失误或疏忽,但不会对企业的正常运转和员工的健康产生重大影响。
对于低风险级别的安全风险,企业需要建立相应的监测和管理机制,确保风险的及时发现和处理。
三、安全风险管控措施为了有效管控安全风险,化工企业需要采取一系列措施来控制和预防风险的发生。
以下是一些常见的安全风险管控措施:1. 制定详细的安全管理制度和操作规程,确保员工按照规定进行工作。
2. 进行安全风险评估和监测,及时发现和排除潜在风险。
3. 为员工提供必要的安全培训和教育,提高安全意识和应急处理能力。
4. 配备专业的安全设施和装备,包括消防设备、防爆设备等。
5. 建立健全的应急预案,及时应对突发事件和事故,并进行演练和测试。
6. 加强对供应商和承包商的安全管理,确保其符合相关安全标准。
7. 进行定期的安全检查和评估,及时发现和纠正存在的安全问题。
四、成套资料说明本文档提供了化工企业安全风险分级管控的成套资料,包括但不限于以下内容:1. 安全风险等级划分标准和说明文件。
- 1、下载文档前请自行甄别文档内容的完整性,平台不提供额外的编辑、内容补充、找答案等附加服务。
- 2、"仅部分预览"的文档,不可在线预览部分如存在完整性等问题,可反馈申请退款(可完整预览的文档不适用该条件!)。
- 3、如文档侵犯您的权益,请联系客服反馈,我们会尽快为您处理(人工客服工作时间:9:00-18:30)。
生产车间
特定时间进行
2.1工作危害分析(JHA+LS)评价记录(生产作业)
序号
作业步骤
危险源或潜在事件
主要后果
现有控制措施
L
S
R
评价级别
风险分级
建议改进(新增)措施
备注
工程技术措施
管理措施
培训教育措施
个体防护措施
应急处置措施
1
硫酸卸车作业
车辆驶入
车辆超速,停车后滑动
车辆伤害
/
1.厂区内限速5公里。引导车辆进入卸车区,熄火,上交钥匙。垫上止滑木块。
无
2
卸车
硫酸泄漏
灼烫
防腐泵静电接地,有漏电保护装置
2.卸车前,认真检查,确保管线无泄漏,记好液位,防止冒罐。卸车泵与车辆连接紧固,无泄漏。3.作业人员处于上风向,根据卸车泵压力情况,缓慢开启或关闭阀门。4.严禁擅自脱岗、离岗。经常检查设备及仪表情况。设备故障或异常,及时上报处理。巡查,及时制止违章违规行为
2
5
10
3
一般风险
3
漏电
触电
2
3
6
4
低风险
4
错误操作
灼烫
2
5
3
一般风险
5
防腐泵存在缺陷、故障运行
触电、灼烫
2
5
10
3
一般风险
6
结束
错误操作
灼烫、车辆伤害
/
5.对现场及设备进行清理,确保现场整洁。车辆启动及驶里,确保周边安全。
2
5
10
3
一般风险
7
液碱卸车作业
车辆驶入
车辆超速,停车后滑动
车辆伤害
/
1.厂区内限速5公里。引导车辆进入卸车区,熄火,上交钥匙。垫上止滑木块。
车辆驶入
车辆超速,停车后滑动
1.三级安全教育培训,考核合格。2.进行年度安全教育培训,考核合格
配备防护面罩、耐酸碱手套、围裙
1.制定应急预案,定期进行演练。2.硫酸接触皮肤时,先用干布吸去,用大量冷水冲洗,再用3%-5%碳酸氢钠溶液冲洗。眼睛接触时,立即提起眼睑,用大量流动清水或生理盐水彻底冲洗至少15分钟。就医。
2
3
6
4
低风险
特定时间进行
4
成品装车作业
引导车辆、装车、车上码垛、结束
储罐区
生产车间
特定时间进行
5
磺化反应岗位作业
磺化反应釜操作,检查、打料、反应、出料等
生产车间
生产车间
频繁进行
6
套洗反应岗位作业
套洗反应釜操作,检查、打料、套洗、出料等
生产车间
生产车间
频繁进行
7
蒸煮岗位作业
套洗反应釜操作,检查、打料、蒸煮、出料等
2
3
6
4
低风险
无
14
明火,可燃气体
火灾爆炸
3
5
15
2
较大风险
15
卸车
二氯乙烷泄漏
火灾爆炸、中毒窒息
防爆电机,静电接地,有漏电保护装置。设置可燃气体报警装置
2.卸车前,认真检查,确保管线无泄漏,记好液位,防止冒罐。卸车泵与车辆连接紧固,无泄漏。3.作业人员处于上风向,根据卸车泵压力情况,缓慢开启或关闭阀门。4.严禁擅自脱岗、离岗。经常检查设备及仪表情况。设备故障或异常,及时上报处理。巡查,及时制止违章违规行为
生产车间
生产车间
频繁进行
8
化验操作
设备仪器检查、化验
化验室
化验室
特定时间进行
9
巡检作业
生产过现场巡回检查
车间、厂区
生产车间
频繁进行
10
锅炉岗位
燃气锅炉操作,点火、运行、停机等
锅炉房
生产车间
频繁进行
11
污水处理作业
污水处理设备操作
污水处理车间
生产车间
频繁进行
12
检维修
机电检维修作业
工器具检查、相关生产设备维护保养
2
5
10
3
一般风险
9
漏电
触电
2
3
6
4
低风险
10
错误操作
灼烫
2
5
10
3
一般风险
11
防腐泵存在缺陷、故障运行
触电、灼烫
2
5
10
3
一般风险
12
结束
错误操作
灼烫、车辆伤害
/
5.对现场及设备进行清理,确保现场整洁。车辆启动及驶里,确保周边安全。
2
5
10
3
一般风险
13
二氯乙烷卸车作业
车辆驶入
车辆超速,停车后滑动
3
5
15
2
较大风险
16
漏电
触电
2
3
6
4
低风险
17
错误操作
火灾爆炸、中毒窒息
2
5
10
3
一般风险
18
设备存在缺陷、故障运行
触电、火灾爆炸、中毒窒息
2
5
10
3
一般风险
19
结束
错误操作
火灾爆炸、中毒窒息、车辆伤害
/
5.对现场及设备进行清理,确保现场整洁。车辆启动及驶里,确保周边安全。
2
5
10
3
一般风险
20
成品装车作业
车间、厂区
生产车间
特定时间进行
17
高处作业
检维修及生产过程中高处作业
车间、厂区
生产车间
特定时间进行
18
动火作业
危险区域电焊、气割等作业
车间、厂区
生产车间
特定时间进行
19
受限空间作业
检维修及生产过程中,进入罐体、釜体等受限空间作业活动
车间、厂区
生产车间
特定时间进行
20
抽堵盲板作业
工器具检查、管线检查、盲板抽堵
车辆伤害
车辆带有防火罩
1.厂区内限速5公里。引导车辆进入卸车区,熄火,上交钥匙。垫上止滑木块。
1.三级安全教育培训,考核合格。2.进行年度安全教育培训,考核合格
配备防护面罩、耐酸碱手套、围裙
1.制定应急预案,定期进行演练。2.事故发生时,疏散泄漏污染区人员至安全区,禁止无关人员进入污染区,切断火源。
活动频率
备注
1
生产作业
硫酸卸车作业
引导车辆进入、连接软管、开启阀门、泵等设备卸料,结束后清理
储罐区
生产车间
特定时间进行
2
液碱卸车作业
引导车辆进入、连接软管、开启阀门、泵等设备卸料,结束后清理
储罐区
生产车间
特定时间进行
3
二氯乙烷卸车作业
引导车辆进入、连接软管、开启阀门、泵等设备卸料,结束后清理
储罐区
生产车间
生产车间
生产车间
特定时间进行
13
吊装作业
现场及设备检查、相关设备、配件吊装
车间、厂区
生产车间
特定时间进行
14
管线防腐作业
工器具检查、预处理、涂漆等操作
车间、厂区
生产车间
特定时间进行
15
临时用电作业
工器具检查、临时线路连接作业
车间、厂区
生产车间
特定时间进行
16
焊接与热割
非易燃易爆危险区域电焊、气割等作业
1.三级安全教育培训,考核合格。2.进行年度安全教育培训,考核合格
配备防护面罩、耐酸碱手套、围裙
1.制定应急预案,定期进行演练。2.灼烫事故发生时,用大量冷水冲洗,至少15分钟。就医。
2
3
6
4
低风险
无
8
卸车
液碱泄漏
灼烫
防腐泵静电接地,有漏电保护装置
2.卸车前,认真检查,确保管线无泄漏,记好液位,防止冒罐。卸车泵与车辆连接紧固,无泄漏。3.作业人员处于上风向,根据卸车泵压力情况,缓慢开启或关闭阀门。4.严禁擅自脱岗、离岗。经常检查设备及仪表情况。设备故障或异常,及时上报处理。巡查,及时制止违章违规行为
安全生产风险分级管控资料
单位名称(盖章):印刷企业
1.作业活动清单
2.工作危害分析(JHA)及评价记录(生产作业、检维修)
3.设备设施清单
4.安全检查表分析(SCL)及评价记录(生产车间、公辅设施及区域)
5.安全风险点分级管控台账(告知牌)
1.作业活动清单
序号
作业活动名称
作业活动内容
岗位/地点
实施单位