含硅低碳贝氏体钢冷却速度与组织的关系
共析钢的c曲线和冷却过程指出各点处的组织

共析钢的c曲线和冷却过程指出各点处的组织钢的C曲线是描述钢在冷却过程中的硬度变化曲线,也是评价钢的淬透性能的重要指标之一。
冷却过程是指将高温钢材迅速冷却至室温的过程,这个过程会导致钢材的微观组织发生明显的变化。
下面我们将分别讨论钢的C曲线和冷却过程的各个阶段以及各点处的组织。
钢的C曲线是通过在冷却过程中对不同硬度的试样进行淬透试验,得到试样的硬度与淬透时间的关系曲线。
C曲线通常呈现出一个类似S形的曲线,如下图所示:[图片]在C曲线的最左侧,即淬火刚过程中,试样的硬度较低,这是因为冷却速度非常快,导致组织中的碳元素没有足够的时间扩散,形成了细小而分散的马氏体结构,马氏体的硬度较低。
此时的硬度主要由马氏体的体积分数决定,而马氏体的体积分数与碳的含量有关。
接下来是C曲线的陡峭部分,即最大淬透硬度,此时试样的硬度最高。
这是因为随着冷却时间的延长,马氏体逐渐增多,并出现了更多的残余奥氏体。
而奥氏体的硬度较低,所以整个试样的硬度会下降。
此时的硬度是由马氏体和残余奥氏体的体积分数共同决定的。
在C曲线的右侧,即逆硬度过程中,试样的硬度会再次上升。
这是因为冷却时间更长,奥氏体开始分解,转变为更硬的贝氏体和余量奥氏体。
贝氏体的形成速度较慢,而冷却时间增长正好有利于贝氏体的形成。
在逆硬度过程中,试样中贝氏体和余量奥氏体的体积分数会不断增加,从而提高试样的硬度。
在冷却过程中,钢的组织也会发生明显的变化。
在淬火刚过程中,钢材的组织主要由马氏体组成,因为冷却速度很快,没有足够的时间让碳元素扩散,导致马氏体形成。
马氏体的形态取决于钢的成分和冷却速度,常见的有板状马氏体、针状马氏体和高碳马氏体等。
随着冷却时间的延长,奥氏体逐渐出现并与马氏体共存。
奥氏体的形态也受到冷却速度的影响,常见的有等轴奥氏体、层状奥氏体和颗粒状奥氏体等。
奥氏体是面心立方结构,硬度较低,常常被认为是“软”组织。
然而,奥氏体的稳定性较好,能够长时间保持其形态而不发生相变。
冷却介质对新型贝氏体铸钢组织和性能的影响

关键 词 :冷却介质 ;贝氏体 铸钢 ;组织 ;性 能 中图分 类号 :T 5 . 文 献标 识码 :A 文章 编号 :10 — 9 7 (0 6 l一 2 1 0 G16 2 3 0 14 7 2 0 ) l 10 — 3
Ef c f oig Me im n Mir sr cu e a d Pr p t so f t e o Co l d u o c o tu t r n o ere f n i
a v na e u o e h n e e t s n h ss p o e is o G3 Cr 2 2 d a t g o s t n a c m n y t e i r p r e f Z t 0 Mn SiMo wi lv t g c ol g t ee ai o i h n n
c m p s t s r c u e f r i u n h n o wa e g a s u n h n o wa e q e c ig. Is o o i e tu t r a e o I t q e c i g r t r ls q e c i g r t r u n hn t '
n w t p b i i c s s e 1 we e s u id T e r s l s o e ye a nt e a t t e r t de . h e u t s h w t a , a e a s e i ig. t e h t f r u t nt n t i z h m i r s r c u e 0 G 3 Cr 2 2 o s s f b i i e r e a d r t ie u t nt e t p c 0 tu t r fZ 0 Mn Si Mo c n ito a nt f ri n e a n d a s e i i a n w y e e t e s
碳钢的热处理工艺对组织与性能的影响

实验三碳钢的热处理工艺对组织与性能的影响一、实验目的1.了解碳钢热处理工艺操作。
2.学会使用洛氏硬度计测量材料的硬度性能值。
3.掌握热处理后钢的金相组织分析。
4.For personal use only in study and research; not for commercial use5.6.探讨淬火温度、淬火冷却速度、回火温度对45和T12钢的组织和性能(硬度)的影响。
7.巩固课堂教学所学相关知识,体会材料的成分-工艺-组织-性能之间关系。
二、实验内容1.45和T12钢试样淬火、回火操作,用洛氏硬度计测定试样热处理前后的硬度。
工艺规范见表6—1。
2.制备并观察标6—2所列样品的显微组织。
3.观察幻灯片或金相图册,熟悉钢热处理后的典型组织:上贝氏体、下贝氏体、片状马氏体、条状马氏体、回火马氏体等的金相特征。
三、概述1.淬火、回火工艺参数的确定。
Fe—Fe3C状态图和C—曲线是制定碳钢热处理工艺的重要依据。
热处理工艺参数主要包括加热温度,保温时间和冷却速度。
(1)加热温度的确定淬火加热温度决定钢的临界点,亚共析钢,适宜的淬火温度为A c3以上30~50℃,淬火后的组织为均匀而细小的马氏体。
如果加热温度不足(<A c3),淬火组织中仍保留一部分原始组织的铁素体,造成淬火硬度不足。
过共析钢,适宜的淬火温度为A c1以上30~50℃,淬火后的组织为马氏体十二次渗碳体(分布在马氏体基体内成颗粒状)。
二次渗碳体的颗粒存在,会明显增高钢的耐磨性。
而且加热温度较A cm低,这样可以保证马氏体针叶较细,从而减低脆性。
回火温度,均在A c1以下,其具体温度根据最终要求的性能(通常根据硬度要求)而定。
(2)加热,保温时间的确定加热、保温的目的是为了使零件内外达到所要求的加热温度,完成应有的组织转变。
加热、保温时间主要决定于零件的尺寸、形状、钢的成分、原始组织状态、加热介质、零件的装炉方式和装炉量以及加热温度等。
钢的热处理及其对组织和性能的影响
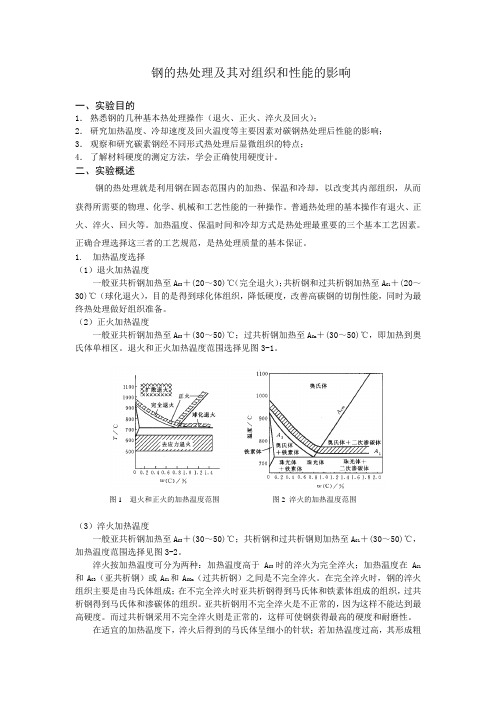
钢的热处理及其对组织和性能的影响一、实验目的1.熟悉钢的几种基本热处理操作(退火、正火、淬火及回火);2.研究加热温度、冷却速度及回火温度等主要因素对碳钢热处理后性能的影响;3.观察和研究碳素钢经不同形式热处理后显微组织的特点;4.了解材料硬度的测定方法,学会正确使用硬度计。
二、实验概述钢的热处理就是利用钢在固态范围内的加热、保温和冷却,以改变其内部组织,从而获得所需要的物理、化学、机械和工艺性能的一种操作。
普通热处理的基本操作有退火、正火、淬火、回火等。
加热温度、保温时间和冷却方式是热处理最重要的三个基本工艺因素。
正确合理选择这三者的工艺规范,是热处理质量的基本保证。
1.加热温度选择(1)退火加热温度一般亚共析钢加热至A C3+(20~30)℃(完全退火);共析钢和过共析钢加热至A C1+(20~30)℃(球化退火),目的是得到球化体组织,降低硬度,改善高碳钢的切削性能,同时为最终热处理做好组织准备。
(2)正火加热温度一般亚共析钢加热至A C3+(30~50)℃;过共析钢加热至A Cm+(30~50)℃,即加热到奥氏体单相区。
退火和正火加热温度范围选择见图3-1。
图1 退火和正火的加热温度范围图2 淬火的加热温度范围(3)淬火加热温度一般亚共析钢加热至A C3+(30~50)℃;共析钢和过共析钢则加热至A C1+(30~50)℃,加热温度范围选择见图3-2。
淬火按加热温度可分为两种:加热温度高于A C3时的淬火为完全淬火;加热温度在A C1和A C3(亚共析钢)或A C1和A CCm(过共析钢)之间是不完全淬火。
在完全淬火时,钢的淬火组织主要是由马氏体组成;在不完全淬火时亚共析钢得到马氏体和铁素体组成的组织,过共析钢得到马氏体和渗碳体的组织。
亚共析钢用不完全淬火是不正常的,因为这样不能达到最高硬度。
而过共析钢采用不完全淬火则是正常的,这样可使钢获得最高的硬度和耐磨性。
在适宜的加热温度下,淬火后得到的马氏体呈细小的针状;若加热温度过高,其形成粗针状马氏体,使材料变脆甚至可能在钢中出现裂纹。
热变形后冷却速度对铁素体-贝氏体微合金钢组织演变的影响
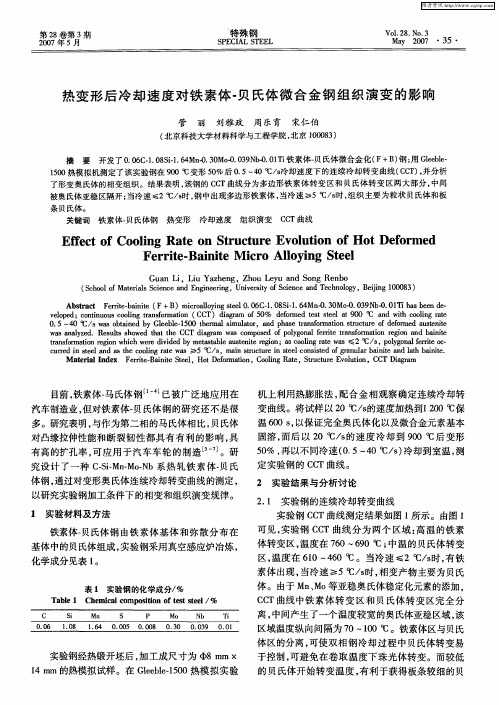
20 07年 5月
第2 8卷第 3期
‘ 特殊 钢
S E I EL P C AL S E r
V0 . 8 N . 12 . o 3
Ma 2 0 ・3 ・ y 素体 - 氏体 微 合 金 钢 组 织演 变 的影响 贝
Gu n Li i z e g,Zh u L y n o g Re b a ,L U Ya h n o eua dS n n o
( col f t i sSi c n nier g U i ri f c n eadT c nlg , eig10 8 ) Sho o Mae a c n eadE gne n , n esyo i c n eh ooy B in 0 0 3 rl e i v t Se j
目前 , 素体 . 氏体 钢 ¨ 已被 广泛 地 应 用在 铁 马 汽车制 造业 , 对铁 素体 一 氏体 钢 的研究 还 不 是很 但 贝
机上利用热膨胀法 , 配合 金相观察确定连续冷却转 变曲线 。将试样 以 2 0℃/ 的速度加热到1 0 s 0℃保 2 温 60S 以保证完全奥 氏体化 以及微合金元素基本 0 , 固溶 , 而后 以 2 0℃/ 的速度冷却到 90℃后变形 s 0
被奥 氏体亚稳 区隔开 ; 当冷速 42 ̄ / 时 , 中出现多边形铁素体 , Cs 钢 当冷速 t5 ̄ / 时 , 织主要 为粒状 贝氏体 和板 > Cs 组 条贝氏体 。 关键词 铁素体. 贝氏体钢 热变形
冷却速度
组织演变
C T曲线 C
Efe to o i g Ra e o t u t r o u i n o tDe o me f c f Co l t n S r cu e Ev l to fHo f r d n Fe rt - i ie M ir ly n t e r ie Ban t c o Al i g S e l o
钢的热处理(答案)
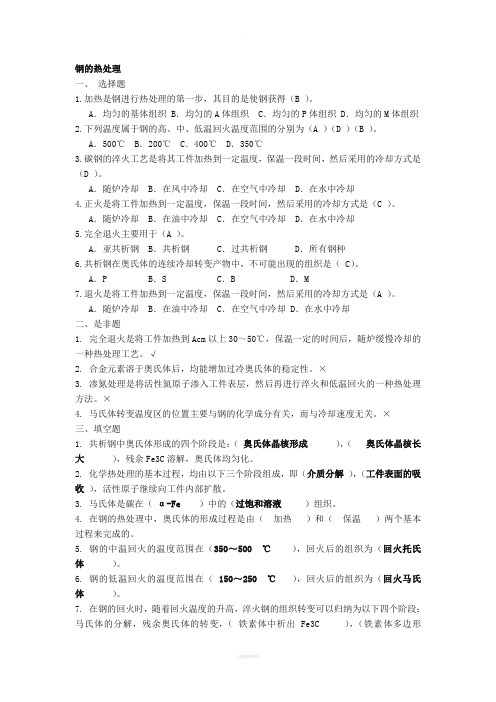
钢的热处理一、选择题1.加热是钢进行热处理的第一步,其目的是使钢获得(B )。
A.均匀的基体组织 B.均匀的A体组织 C.均匀的P体组织 D.均匀的M体组织2.下列温度属于钢的高、中、低温回火温度范围的分别为(A )(D )(B )。
A.500℃ B.200℃ C.400℃ D.350℃3.碳钢的淬火工艺是将其工件加热到一定温度,保温一段时间,然后采用的冷却方式是(D )。
A.随炉冷却 B.在风中冷却 C.在空气中冷却 D.在水中冷却4.正火是将工件加热到一定温度,保温一段时间,然后采用的冷却方式是(C )。
A.随炉冷却 B.在油中冷却 C.在空气中冷却 D.在水中冷却5.完全退火主要用于(A )。
A.亚共析钢 B.共析钢 C.过共析钢 D.所有钢种6.共析钢在奥氏体的连续冷却转变产物中,不可能出现的组织是( C)。
A.P B.S C.B D.M7.退火是将工件加热到一定温度,保温一段时间,然后采用的冷却方式是(A )。
A.随炉冷却 B.在油中冷却 C.在空气中冷却 D.在水中冷却二、是非题1. 完全退火是将工件加热到Acm以上30~50℃,保温一定的时间后,随炉缓慢冷却的一种热处理工艺。
√2. 合金元素溶于奥氏体后,均能增加过冷奥氏体的稳定性。
×3. 渗氮处理是将活性氮原子渗入工件表层,然后再进行淬火和低温回火的一种热处理方法。
×4. 马氏体转变温度区的位置主要与钢的化学成分有关,而与冷却速度无关。
×三、填空题1. 共析钢中奥氏体形成的四个阶段是:(奥氏体晶核形成),(奥氏体晶核长大),残余Fe3C溶解,奥氏体均匀化。
2. 化学热处理的基本过程,均由以下三个阶段组成,即(介质分解),(工件表面的吸收),活性原子继续向工件内部扩散。
3. 马氏体是碳在(α-Fe)中的(过饱和溶液)组织。
4. 在钢的热处理中,奥氏体的形成过程是由(加热)和(保温)两个基本过程来完成的。
钢在加热及冷却时的组织转变

共析碳钢 曲线与曲线的比较
1、同一成分的钢的曲线位 于C曲线右下方。要获得 同样的组织,连续冷却 转变比等温转变的温度 要低些,孕育期要长些 。
光镜形貌
电镜形貌
形成温度为650600℃,片层较薄, 800-1000倍光镜下可 辨,用符号S 表示。
(3)托 氏 体 形 貌 像
形成温度为600-550℃,片层极薄,电镜下可辨,用符 号T 表示。
电镜形貌
光镜形貌
2)贝氏体型转变 -中温等温转变( 550~230℃ ):
(1)550~350℃: B上; 40~45;脆性大,几乎无价值。
3、奥氏体晶粒长大及其控制措施
钢加热时珠光体向奥氏体转变刚刚结束时,奥氏体晶 粒是比较细小的。如果继续加热或保温,奥氏体晶粒 会变粗大,影响热处理后钢的强度、塑性、韧性较低。 因此,加热时获得细小晶粒的奥氏体对提高热处理效 果和钢的性能有重要的意义。
控制奥氏体晶粒长大措施: 1)合理选择加热温度和保温时间 2)采用快速加热和短时间保温 3)加入一定量合金元素(除锰、磷外)
10
102
103
104
时间(s)
1)、珠光体型转变—高温转变(A1~550 ℃
)
共析碳钢三种珠光体型组织
第一节 钢在加热和冷却时的组织转变
⑴ 珠光体形貌
形成温度为A1~650℃ ,片层较厚,500倍光 镜下可辨,用符号P表示 .
三维珠光体如同放在水中的包心菜
一种屈服强度550MPa低碳贝氏体钢CCT曲线
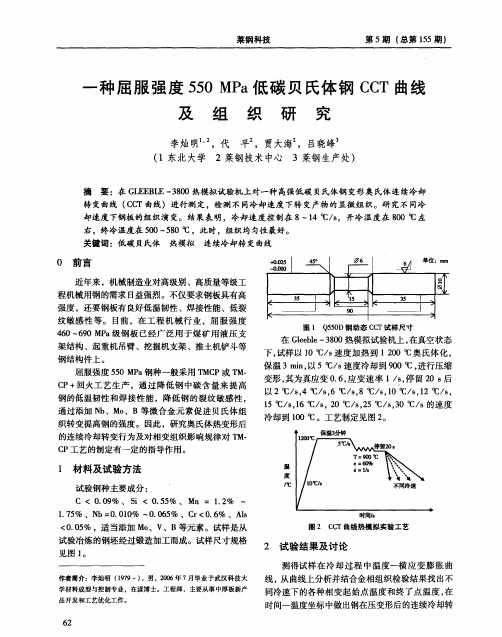
l 5℃/ ,6℃/ , 0℃/ ,5℃/ ,0 / s1 s2 s2 s3 s的速度
冷却到 10o 。工艺制定见图 2 0 C 。
C P工艺的制定有一定的指导作用 。
1 材料及试验 方法
试验钢种主要成分 :
C < 0 0 % 、 S < 0 5 % 、 Mn = 1 2 .9 i .5 . % 一 1 7 % 、 Nb:O 0 0 .5 . 1 % 一0 0 5 、 C .6 % r<0 6 、 A s . % l
3 结 语
1 )对 于试 验钢 而言 ,冷速 为 2 ̄/ C s至 8 ̄/ Cs
2 -0 83 .
特邀 编辑 :周
平
A CCT C r e o o Ca b n Ba n t te t ed S r n t f5 0 I P u v f L w r o i ie S e l h Y-l t e g h o 5 I a V
温
度
, ℃
时 Il  ̄a l
< .5 ,适 当添加 M 、V O0 % o 、B等元素。试样是从 试验冶炼的钢坯经过锻造加工而成。试样尺寸规格
见 图 1 。
作者简 介:李灿 明 (9 9 ,男 , 0 6 7 17 一) 2 0 年 月毕业 于武汉科技大
图 2 C T曲线 热模 拟实验 工艺 G
Y 1 ,
、
3 5
I
、
日
强度 ,还要钢板有 良好低温韧性、焊接性能、低裂 纹敏感性等 。 目前 ,在工 程机械行业 ,屈服强度
、
J ,、 9 , 0 、
图 1 Q 5 D钢动态 C T试样尺寸 50 C
- 1、下载文档前请自行甄别文档内容的完整性,平台不提供额外的编辑、内容补充、找答案等附加服务。
- 2、"仅部分预览"的文档,不可在线预览部分如存在完整性等问题,可反馈申请退款(可完整预览的文档不适用该条件!)。
- 3、如文档侵犯您的权益,请联系客服反馈,我们会尽快为您处理(人工客服工作时间:9:00-18:30)。
Ξ
含硅低碳贝氏体钢冷却速度与组织的关系
南昌航空工业学院 周贤良 华小珍
摘 要: 研究了低碳含硅贝氏体钢冷却速度对组织的影响。
实验发现,在贝氏体中温区可分别转变为粒状贝氏体、粒状组织、混合组织。
粒状贝氏体与粒状组织中都存在(M-A)岛。
随冷速增加,岛的平均直径减小,岛的形状由颗粒状向条状、甚至膜状转变。
关 键 词: 粒状贝氏体 粒状组织 冷却速度
钢中粒状贝氏体形态、形成条件、转变机理及其力学性能的研究虽近30年,但至今无统一认识。
近些年发现主要有两种不同的组织。
一种是(M-A)岛无规则地分布在块状铁素体基体上,称为粒状组织;另一种是(M -A)岛有序分布于板条铁素体间,称为粒状贝氏体。
这两种组织的力学性能有很大差距[1,2]。
本文探讨了冷却速度对Si2Mn2Mo 系低碳贝氏体钢组织形态的影响。
1 试验方法
试验用钢的化学成分(%):C0116,Mn 2.92,Si1.56,Mo0.26,S小于01016,P小于01035。
用Formaster-D型热膨胀仪测定试验钢的CCT曲线;用光学显微镜、透射电镜(TEM)、扫描电镜(SEM)分析钢组织;用定量金相法测定不同冷速下粒状组织和粒状贝氏体量及(M-A)岛的平均直径。
2 结果与讨论
211 CCT曲线
测绘出试验钢的CCT曲线,见图1。
从图1可见,该钢的贝氏体转变起始线B s和转变终止线B f具有较平的特点,即使冷速很小,高温区也不出现贝氏体转变,表明在较宽的冷速范围内都可以得到贝氏体组织。
实验在018℃/min冷速时也未发现珠光体类组织。
这给我们启示:在低碳Si2Mn2Mo系钢中,只要适应选择较高的含锰量,即使用很低的含钼量也可开发出实用的贝氏体钢。
图1 试验钢的CCT曲线
212 显微组织
试验钢按图1所示的各种冷速处理后,其组织见图2。
由图2可知,当冷速大于贝氏体转变临
第18卷第2期 1998年4月 江 西 冶 金
J IAN GXI METALLUR GY
Vol.18,No.4
April 1998
Ξ收稿日期:1998208227
界冷速时,组织中主要是板条马氏体(图
2a );当冷速小于贝氏体转变临界冷速时,主要为粒状贝氏体和粒状组织的混合组织,并且随冷速的增大,粒状组织减少,粒状贝氏体增多(图2c ,2d ),粒状贝氏体量和冷速呈线性关系(图3);当冷速为018℃/min 时,基本上均为粒状组织(图2e );而冷速156℃/min 时,几乎全部为粒状贝氏体(图2b )。
a
2680℃/min b 156℃/min c 85℃/min
d 35℃/min
e 0.8℃/min
图2 试验钢不同冷速下形成的组织,×800
图4为粒状贝氏体和粒状组织的透射电
镜图像。
经选区衍射后可知,两种组织中的岛都由马氏体和奥氏体组成,未发现其他组织,故一般称之为(M -A )岛。
从图4可见,粒状贝氏体由板条铁素体及其间分布有序的(M -A )岛组成,岛的尺寸较小,多呈条状分布,铁素体板条含有较高的位错密度;粒状组织由块状铁素体基体上分布无序的(
M -A )岛组成,岛的尺寸较大,多呈等轴状,而且块状铁素体基体的位错密度较低。
由此可知,在试验钢的中温区存在完全不同的两类组织,应该加以区分。
图3 粒状贝氏体量随冷速的变化
・41・江 西 冶 金 1998年4月
213 冷速对(M -A )岛的影响 为了显示(M -A )岛的形貌随冷速的变
化,采用扫描电镜进行分析,见图5。
a 粒状贝氏体
b 粒状组织
图
4 TEM 像,×30000
a
156℃/min b 85℃/min
c 35℃/min
d 018℃/min
图5 不同冷却速度下的SEM 像,×4000
从图5可以看出,随着冷速的增大,(M -A )岛由颗粒状(小块状)逐渐地转变为条状,甚至转变为膜状。
定量金相分析结果表明,随着冷速的增大,(M -A )岛的平均直径逐渐减小(图6)。
3 结论
(1
)Si 2Mn 2Mo 系低碳贝氏体钢连续冷却时可形成粒状贝氏体、粒状组织及其混合
图6 (M -A)岛平均直径随冷速的变化
・
51・第18卷第2期 周贤良等:含硅低碳贝氏体钢冷却速度与组织的关系
组织。
粒状贝氏体和粒状组织是两类不同的组织。
(2)随着冷速增大,试验钢组织中的(M -A)岛平均直径减小,形状由颗粒状向条状转变。
通过控制冷却速度可以获取不同的组织。
参 考 文 献
1 许念坎等.粒状贝氏体转变的表面浮凸效应和组织分析.理化检验(物理分册),1983;(4):2
2 郭新成.钢中的粒状贝氏体.金属热处理,1983;(2):1
(上接第5页)
率、慢风率从1~9月的6.18%,18.04%骤降至10月的1.44%,6.40%,11月进一步降至1.10%,0.90%,保障了高炉顺行。
萍钢302号高炉1997年1~11月主要经济技术指标见表2。
表2 302号高炉1997年主要经济技术指标
时 间1~9月10月11月
利用系数,t/(m3・d) 1.50011820 2.027入炉焦比,kg/t648549537
治炼强度,t/(m3・d)019780.991 1.100风量,m3/min709741815
喷煤比,kg/t456166
平均风温,℃973992984
休风率,%611811441110
慢风率,%1810461400190
平均风压,kPa136150154
炉顶压力,kPa454650
煤气含CO2,%12.413.013.5
入炉矿品位,%511315311153123焦炭负荷,t/t218723*********生铁含Si,%112401910151
炼钢铁比率,%6318585167100
生铁含S,%010330104101045坐料次数,次211614
塌料次数,次131811
炉渣碱度,R2112051117711242炉渣(MgO),%819291289122
矿石批重,t310641636167
熟料率,%811678411787163生铁合格率,%991851001005 结束语
萍钢高炉生产在1997年10月取得突破,11月高炉利用系数接近210t/(m3・d),主要采取了如下措施:
(1)重视精料工作,把好原燃料入厂关,改善烧结矿和焦炭质量,提高入炉矿综合品位及熟料率,抓好槽下筛分工作,减少入炉粉末。
(2)转变观念,强化管理,深化改革。
靠严格管理保证技术措施到位,靠严格管理创出效益。
(3)采用合理的高炉操作制度。
根据高炉炉况,降低铁水[Si]含量,缩小[Si]偏差;采用全风作业,增加鼓风动能;扩大矿批,改善煤气利用,保证炉况稳定顺行。
(4)加强设备维护,减少设备故障,精心指挥,精心操作,减少炉内炉外事故,大幅度降低了休风率和慢风率。
今后,仍要加强管理,深化改革,严格执行技术规程,改进操作,使全厂高炉利用系数达到2.0t/(m3・d)以上,各项技术经济指标再上新台阶。
・
6
1
・江 西 冶 金 1998年4月。