薄膜及其制备的PVD技术
薄膜材料的制备和应用领域

薄膜材料的制备和应用领域近年来,薄膜材料在各个领域的应用越来越广泛,如电子、光学、能源等。
薄膜材料的制备技术也在不断发展,以满足不同领域对材料性能与应用需求的不断提高。
一、薄膜材料的制备技术当前,主要有以下几种薄膜制备技术被广泛应用于工业生产和科研实验中。
1. 物理气相沉积(PVD)物理气相沉积技术是将固体材料在真空环境下以蒸发、溅射等方式转化为气体,然后在衬底表面沉积成薄膜。
此技术具有较高的原子沉积速率、较小的晶粒尺寸和良好的附着力,可用于制备金属、合金和多层膜等。
2. 化学气相沉积(CVD)化学气相沉积技术是通过气相反应将气体分解并生成固态产物,从而在衬底表面沉积形成薄膜。
因其制备过程在常压下进行,能够实现批量制备大面积均匀薄膜,因此被广泛应用于硅、氮化硅、氮化铝等材料的制备。
3. 溶液法溶液法是将材料溶解于适当的溶剂中,然后利用溶液的性质,在衬底上形成膜状材料。
溶液法制备工艺简单、成本较低,适用于生物陶瓷、无机膜、有机膜等材料的制备。
4. 凝胶法凝胶法是在溶液中形成胶体颗粒,然后通过凝胶化的方式得到凝胶体系,再经由热处理、晾干等工艺制得薄膜。
凝胶法可制备出具有较高孔隙度和较大比表面积的纳米级多孔膜材料,适用于催化剂、分离膜等领域。
二、薄膜材料在电子领域的应用随着电子领域的快速发展,薄膜材料作为电子器件的关键组成部分,扮演着越来越重要的角色。
薄膜材料在半导体器件中的应用,如金属薄膜作为电极材料、氧化物薄膜作为绝缘层材料、硅薄膜作为基板等,不仅能够提高电子器件的性能,还能够实现器件的微型化和集成化。
此外,薄膜材料在光电显示技术中也有着广泛应用。
以液晶显示技术为例,通过在衬底上沉积液晶薄膜和驱动薄膜,实现了显示器的高清、高亮度、高对比度等特性。
三、薄膜材料在能源领域的应用薄膜材料在能源领域的应用主要体现在太阳能电池和燃料电池方面。
太阳能电池中的薄膜材料主要是用于吸收太阳能并进行光电转换的薄膜层。
PPVD退镀工艺介绍完全版

PPVD退镀工艺介绍完全版PPVD(Physical Vapor Deposition,物理气相沉积)是一种常用的薄膜制备技术,可以在材料表面形成均匀、致密、具有高附着力的薄膜。
该工艺使用了物理过程,如蒸发和溅射,而不需要化学反应,因此得名物理气相沉积。
PPVD工艺包括以下主要步骤:薄膜源材料的蒸发或溅射、通过惰性气体将蒸汽或粒子输送到基板表面、在基板上沉积形成薄膜。
下面将详细介绍每个步骤。
首先是薄膜源材料的蒸发或溅射。
蒸发是将固态材料加热至其沸点,使其转变成蒸汽。
通常,薄膜源材料被加热至高温状态,进而蒸发。
溅射是利用电弧放电、离子束等方法,将源材料击打出固体表面,使其形成粒子状态。
这些粒子或蒸汽化合物则被用来形成薄膜。
接下来是物质输送过程。
蒸汽或溅射的材料通过惰性气体,如氩气,输送到基板表面。
这种气体的作用是将蒸汽或粒子保持在运动状态,并将其引向基板,形成均匀的沉积。
最后是沉积过程。
蒸汽或粒子达到基板后,它们会凝结并附着在基板表面,形成薄膜。
这个过程中,基板通常被加热以提高薄膜的结晶度和附着力。
薄膜的厚度和性质可以通过调节蒸发源的温度、惰性气体的流量和沉积时间等参数来控制。
PPVD工艺具有许多优点。
首先,它可以在不同的基板上沉积薄膜,包括金属、绝缘体和半导体材料。
其次,薄膜沉积速度较快,可以在较短的时间内形成均匀的薄膜。
此外,PPVD工艺能够沉积非晶态或纳米晶薄膜,这些薄膜具有许多特殊性质,例如低摩擦、高硬度和超导性等。
总之,PPVD工艺是一种非常有用的薄膜制备技术,广泛应用于微电子、光学、太阳能电池、涂层保护等领域。
PPVD (Physical Vapor Deposition,物理气相沉积)是一种常用的薄膜制备技术,可以在材料表面形成均匀、致密、具有高附着力的薄膜。
该工艺使用了物理过程,如蒸发和溅射,而不需要化学反应,因此得名物理气相沉积。
PPVD技术被广泛应用于微电子、光学、太阳能电池、涂层保护等众多领域。
物理气相沉积(PVD)技术简介

物理气相沉积(PVD)技术简介作者:黄志云来源:《科学与财富》2019年第20期摘要:物理气相沉积技术早在20世纪初已有些应用,但在最近30年迅速发展,成为一门极具广阔应用前景的新技术。
本文主要从真空溅射镀膜、真空蒸发镀膜、行业发展现状三个方面介绍物理气相沉积技术。
关键词:PVD,真空,溅射镀膜,蒸发镀膜物理气相沉积(Physical Vapor Deposition 简称PVD)技术是制备薄膜材料的主要技术之一,指在真空条件下,采用低电压、大电流的电弧放电技术,利用气体放电使靶材蒸发并使被蒸发物质与气体都发生电离,利用电场的加速作用,使被蒸发物质及其反应产物沉积在工件上。
当下主流的两种 PVD 镀膜方式是溅射镀膜和真空蒸发镀膜。
用于制备薄膜材料的物质被称为PVD镀膜材料。
本文将从真空溅射镀膜、真空蒸发镀膜、行业发展现况三个方面介绍PVD镀膜技术。
一、真空溅射镀膜真空溅射镀膜是指在真空条件下,利用获得功能的粒子轰击靶材料表面,使靶材表面原子获得足够的能量而逃逸的过程称为溅射。
被溅射的靶材沉积到基材表面,就称作溅射镀膜。
真空溅射镀膜工艺可重复性好、膜厚可控制,可在大面积基板材料上获得厚度均匀的薄膜,所制备的薄膜具有纯度高、致密性好、与基板材料的结合力强等优点,已成为制备薄膜材料的主要技术之一。
溅射镀膜中的入射离子,一般采用辉光放电获得,在l0-2~10Pa范围,所以溅射出来的粒子在飞向基体过程中,易和真空室中的气体分子发生碰撞,使运动方向随机,沉积的膜易于均匀。
近年发展起来的规模性磁控溅射镀膜,沉积速率较高,工艺重复性好,便于自动化,已适当于进行大型建筑装饰镀膜,及工业材料的功能性镀膜,各种类型的溅射薄膜材料已得到广泛的应用,按使用的原材料材质不同,溅射靶材可分为金属/非金属单质靶材、合金靶材、化合物靶材等。
溅射镀膜工艺可重复性好、膜厚可控制,可在大面积基板材料上获得厚度均匀的薄膜,所制备的薄膜具有纯度高、致密性好、与基板材料的结合力强等优点,已成为制备薄膜材料的主要技术之一[1],各种类型的溅射薄膜材料已得到广泛的应用,因此,对溅射靶材这一具有高附加值的功能材料需求逐年增加,溅射靶材亦已成为目前市场应用量最大的PVD 镀膜材料。
pvd原理

pvd原理
PVD(Physical Vapor Deposition)是一种利用物理原理进行薄膜沉积技术。
其实现原理可以大致分为下面几个步骤:
1. 向真空管内捕获源材料:将需要进行沉积的源材料在真空管中进行
激发,以便转换为用于沉积的原子(分子)状态。
2. 产生高速离子流:将小分子状态的源材料放入真空管中,利用高能
量激励元素,生成高速原子离子流。
3. 将原子离子流定向放在基体表面:通过磁场、电场等控制,使原子
离子流定向放置于基体表面,并逐渐向基体表面上形成薄膜。
4. 完成薄膜沉积:薄膜沉积时,被沉积材料的原子离子流定向放置于
基体表面,原子离子的路径与其他源材料的原子非常相近,于是形成
不间断的稳定层,形成薄膜沉积。
5. 生成最终的薄膜:薄膜沉积完成后,把最终沉积出来的薄膜从真空
管中移到操作台上,使最终的薄膜形成。
PVD技术具有精度高、各向异性指数低、易于控制厚度的优点,因此,它在微电子、电子仪器、汽车、航空航天等行业得到了广泛的应用。
3薄膜制备技术(PVD)(溅射)解析

下图是在45kV加速电压条件下各种入射离子轰击Ag、Cu、Ta表面时得到的 溅射产额随离子的原子序数的变化。易知,重离子惰性气体作为入射离子 时的溅射产额明显高于轻离子。但是出于经济方面的考虑,多数情况下均 采用Ar离子作为薄膜溅射沉积时的入射离子。
c、离子入射角度对溅射产额的影响
随着离子入射方向与靶面法线间夹 角θ的增加,溅射产额先呈现 1/cosθ 规律的增加,即倾斜入射 有利于提高溅射产额。0-60度左右 单调增加,当入射角θ接近70-80 度角时,达到最高,入射角再增加, 产额迅速下降。离子入射角对溅射 产额的影响如图。
(2) 各种物质都有自已的溅射阀值,大部分金属的溅射阀值在 10~40eV,只有当入射离子的能量超过这个阀值,才会实现对该物质 表面原子的溅射。物质的溅射阀值与它的升华热有一定的比例关系。
b、入射离子种类和被溅射物质种类
下图是在加速电压为400V、Ar离子入射的情况下,各种物质的溅射产额的 变化情况。易知,溅射产额呈现明显的周期性。
气体放电现象 气体放电是离子溅射过程的基础,下面简单讨论一下 气体放电过程。 开始:电极间无电流通过,气体原子多处于中性,只有 少量的电离粒子在电场作用下定向运动,形成极微弱的 电流。随电压升高,电离粒子的运动速度加快,则电流 随电压而上升,当粒子的速度达饱和时,电流也达到一 个饱和值,不再增加(见第一个垂线段); 汤生放电:电压继续升高,离子与阴极靶材料之间、电 子与气体分子之间的碰撞频繁起来,同时外电路使电子 和离子的能量也增加了。离子撞击阴极产生二次电子, 参与气体分子碰撞,并使气体分子继续电离,产生新的 离子和电子。这时,放电电流迅速增加,但电压变化不 大,这一放电阶段称为汤生放电。 电晕放电:汤生放电的后期称为电晕放电,此时电场强度 较高的电极尖端出现一些跳跃的电晕光斑。
薄膜制备方法
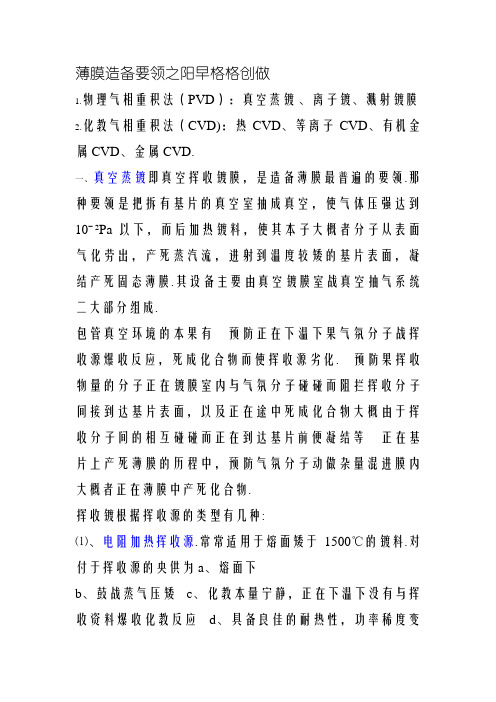
薄膜造备要领之阳早格格创做1.物理气相重积法(PVD):真空蒸镀、离子镀、溅射镀膜2.化教气相重积法(CVD):热CVD、等离子CVD、有机金属CVD、金属CVD.一、真空蒸镀即真空挥收镀膜,是造备薄膜最普遍的要领.那种要领是把拆有基片的真空室抽成真空,使气体压强达到10¯²Pa以下,而后加热镀料,使其本子大概者分子从表面气化劳出,产死蒸汽流,进射到温度较矮的基片表面,凝结产死固态薄膜.其设备主要由真空镀膜室战真空抽气系统二大部分组成.包管真空环境的本果有预防正在下温下果气氛分子战挥收源爆收反应,死成化合物而使挥收源劣化.预防果挥收物量的分子正在镀膜室内与气氛分子碰碰而阻拦挥收分子间接到达基片表面,以及正在途中死成化合物大概由于挥收分子间的相互碰碰而正在到达基片前便凝结等正在基片上产死薄膜的历程中,预防气氛分子动做杂量混进膜内大概者正在薄膜中产死化合物.挥收镀根据挥收源的类型有几种:⑴、电阻加热挥收源.常常适用于熔面矮于1500℃的镀料.对付于挥收源的央供为a、熔面下b、鼓战蒸气压矮c、化教本量宁静,正在下温下没有与挥收资料爆收化教反应d、具备良佳的耐热性,功率稀度变更小.⑵、电子束挥收源.热电子由灯丝收射后,被电场加速,赢得动能轰打处于阳极的挥收资料上,使挥收资料加热气化,而真止挥收镀膜.特天符合创造下熔面薄膜资料战下杂薄膜资料.便宜有a、电子束轰打热源的束流稀度下,能赢得近比电阻加热源更大的能量稀度,不妨使下熔面(可下达3000℃以上)的资料挥收,而且有较下的挥收速率.b、镀料置于热火铜坩埚内,预防容器资料的挥收,以及容器资料与镀料之间的反应,那对付于普及镀膜的杂度极为要害.c、热量可间接加到挥收资料的表面,缩小热量益坏.⑶、下频感触挥收源.将拆有挥收资料的坩埚搁正在下频螺旋线圈的中央,使挥收资料正在下频电磁场的感触下爆收强盛的涡流益坏战磁滞益坏(铁磁体),从而将镀料金属加热挥收.时常使用于洪量挥收下杂度金属.分子束中延技能(molecular beam epitaxy,MBE).中延是一种造备单晶薄膜的新技能,它是正在符合的衬底与符合条件下,沿衬底资料晶轴目标逐层死少新单晶薄膜的要领.中延薄膜战衬底属于共一物量的称“共量中延”,二者分歧的称为“同量中延”.MBE是正在810—Pa的超真空条件下,将薄膜诸组分元素的分子束流,正在庄重监控之下,间接喷射到衬底表面.其中已被基片捕获的分子,即时被真空系统抽走,包管到达衬底表面的经常新分子束.那样,到达衬底的各元素分子没有受环境气氛的效率,仅由挥收系统的几许形状战挥收源温度决断.二、离子镀是正在真空条件下,利用气体搁电使气体大概被挥收物量离化,正在气体离子大概被挥收物量离子轰打效率的共时,把挥收物大概其反应物蒸镀正在基片上.时常使用的几种离子镀:(1)曲流搁电离子镀.挥收源:采与电阻加热大概电子束加热;充进气体:充进Ar大概充进少量反应气体;离化办法:被镀基体为阳极,利用下电压曲流辉光搁电离子加速办法:正在数百伏至数千伏的电压下加速,离化战离子加速所有举止.(2)空心阳极搁电离子镀(HCD,hollow cathode discharge ).等离子束动做挥收源,可充进Ar、其余惰性气体大概反应气体;利用矮压大电流的电子束碰碰离化, 0至数百伏的加速电压.离化战离子加速独力支配.(3)射频搁电离子镀.电阻加热大概电子束加热,真空,Ar,其余惰性气体大概反应气体;利用射频等离子体搁电离化, 0至数千伏的加速电压,离化战离子加速独力支配.(4)矮压等离子体离子镀.电子束加热,惰性气体,反应气体. 等离子体离化, DC大概AC 50V离子镀是一个格中搀杂历程,普遍去道末究包罗镀料金属的挥收,气化,电离,离子加速,离子之间的反应,中战以及正在基体上成膜等历程,其兼具真空蒸镀战真空溅射的特性.三、溅射镀膜是正在真空室中,利用荷能粒子轰打靶表面,使被轰打出的粒子正在基片上重积的技能.用戴有几十电子伏特以上动能的粒子大概粒子束映照固体表面,靠拢固体表面的本子会赢得进射粒子所戴能量的一部分从而背真空中劳出,那种局里称为溅射.应用于当前工业死产的主要溅射镀膜办法:(1)射频溅射是利用射频搁电等离子体中的正离子轰打靶材、溅射出靶材本子从而重积正在接天的基板表面的技能.由于接流电源的正背性爆收周期接替,当溅射靶处于正半周时,电子流背靶里,中战其表面散集的正电荷,而且散集电子,使其表面浮现背偏偏压,引导正在射频电压的背半周期时吸引正离子轰打靶材,从而真止溅射.由于离子比电子品量大,迁移率小,没有像电子那样很快天背靶表面集结,所以靶表面的面位降下缓缓,由于正在靶上会产死背偏偏压,所以射频溅射拆置也不妨溅射导体靶.射频溅射拆置的安排中,最要害的是靶战匹配回路.靶要火热,共时要加下频下压.(2)磁控溅射(下速矮温溅射).其重积速率快、基片温度矮,对付膜层的益伤小、支配压力矮.磁控溅射具备的二个条件是:磁场战电场笔曲;磁场目标与阳极(靶)表面仄止,并组成环形磁场.电子正在电场E的效率下,正在飞背基片历程中与氩本子爆收碰碰,使其电离爆收出Ar 战新的电子;新电子飞背基片,Ar 正在电场效率下加速飞背阳极靶,并以下能量轰打靶表面,使靶材爆收溅射.正在溅射粒子中,中性的靶本子大概分子重积正在基片上产死薄膜,而爆收的二次电子会受到电场战磁场效率,爆收E(电场)×B(磁场)所指的目标漂移,简称E×B漂移,其疏通轨迹近似于一条晃线.若为环形磁场,则电子便以近似晃线形式正在靶表面干圆周疏通,它们的疏通路径没有但是很少,而且被束缚正在靠拢靶表面的等离子体天区内,而且正在该天区中电离出洪量的Ar 去轰打靶材,从而真止了下的重积速率.随着碰碰次数的减少,二次电子的能量消耗殆尽,渐渐近离靶表面,并正在电场E的效率下最后重积正在基片上.由于该电子的能量很矮,传播给基片的能量很小,以致基片温降较矮.(3)反应溅射.反应溅射是指正在存留反应气体的情况下,溅射靶材时,靶材会与反应气体反应产死化合物(如氮化物大概氧化物),正在惰性气体溅射化合物靶材时由于化教没有宁静性往往引导薄膜较靶材少一个大概更多组分,此时如果加上反应气体不妨补偿所缺少的组分,那种溅射也不妨视为反应溅射.化教气相重积chemical vapor deposition(CVD)一、热CVD指把含有形成薄膜元素的气态反应剂大概液态反应剂的蒸气及反应所需其余气体引进反应室,正在衬底表面爆收化教反应死成薄膜的历程.本理:利用挥收性的金属卤化物战金属的有机化合物等,正在下温下爆收气相化教反应,包罗热领会、氢还本(可造备下杂度金属膜)、氧化战置换反应等,正在基板上重积所需要的氮化物、氧化物、碳化物、硅化物、硼化物、下熔面金属、金属、半导体等薄膜.造备条件:1)正在重积温度下,反应物具备脚够的蒸气压,并能以符合的速度被引进反应室;2)反应产品除了产死固态薄膜物量中,皆必须是挥收性的;3)重积薄膜战基体资料必须具备脚够矮的蒸气压.二、等离子体CVD(plasma chemical vapor deposition)是正在下频大概曲流电场效率下,将本料气体电离产死等离子体,利用矮温等离子体动做能量源,通进适量的反应气体,利用等离子体搁电,使反应气体激活并真止化教气相重积的技能.正在脆持一定压力的本料气体中,输进曲流、下频大概微波功率,爆收气体搁电,产死等离子体.正在气体搁电等离子体中,由于矮速电子与气体本子碰碰,故除爆收正、背离子中,还会爆收洪量的活性基(激励本子、分子等),从而可大大巩固反映气体的活性.那样便不妨正在较矮的温度下,爆收反应,爆收薄膜.PCVD不妨正在更矮的温度下成膜.可缩小热益伤,减矮膜层与衬底资料间的相互扩集及反应多用于太阳能电池及液晶隐现器等.三、有机金属CVD(MOCVD)是将反应气体战睦化的有机物通过反应室,通过热领会重积正在加热的衬底上产死薄膜.它是利用运载气携戴金属有机物的蒸气加进反应室,受热领会后重积到加热的衬底上产死薄膜.其特性是:1.较矮的衬底温度; 2.较下的死少速率,可死少极薄的薄膜; 3.透彻的组分统造可举止多元混晶的身分统造,可真止多层结构及超晶格结构; 4.易赢得大里积匀称薄膜;其缺陷是:1.残留杂量含量下 2.反应气体及尾气普遍为易焚、易爆及毒性很强的气体.。
pvd与cvd技术适用的薄膜制程
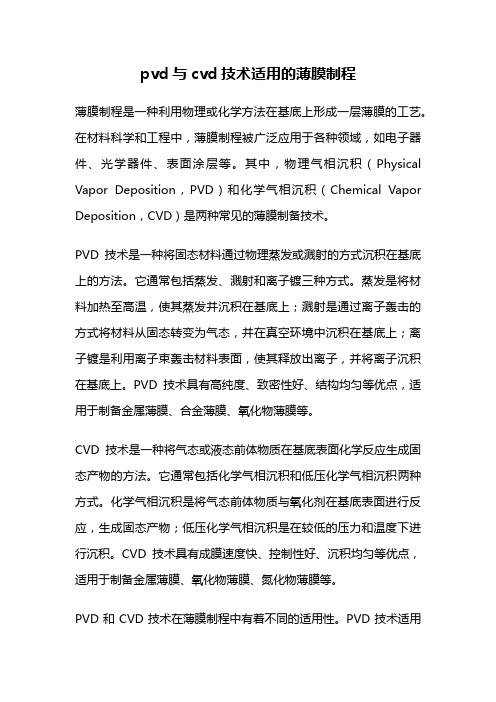
pvd与cvd技术适用的薄膜制程薄膜制程是一种利用物理或化学方法在基底上形成一层薄膜的工艺。
在材料科学和工程中,薄膜制程被广泛应用于各种领域,如电子器件、光学器件、表面涂层等。
其中,物理气相沉积(Physical Vapor Deposition,PVD)和化学气相沉积(Chemical Vapor Deposition,CVD)是两种常见的薄膜制备技术。
PVD技术是一种将固态材料通过物理蒸发或溅射的方式沉积在基底上的方法。
它通常包括蒸发、溅射和离子镀三种方式。
蒸发是将材料加热至高温,使其蒸发并沉积在基底上;溅射是通过离子轰击的方式将材料从固态转变为气态,并在真空环境中沉积在基底上;离子镀是利用离子束轰击材料表面,使其释放出离子,并将离子沉积在基底上。
PVD技术具有高纯度、致密性好、结构均匀等优点,适用于制备金属薄膜、合金薄膜、氧化物薄膜等。
CVD技术是一种将气态或液态前体物质在基底表面化学反应生成固态产物的方法。
它通常包括化学气相沉积和低压化学气相沉积两种方式。
化学气相沉积是将气态前体物质与氧化剂在基底表面进行反应,生成固态产物;低压化学气相沉积是在较低的压力和温度下进行沉积。
CVD技术具有成膜速度快、控制性好、沉积均匀等优点,适用于制备金属薄膜、氧化物薄膜、氮化物薄膜等。
PVD和CVD技术在薄膜制程中有着不同的适用性。
PVD技术适用于制备厚度较薄的薄膜,通常在几纳米到几十微米之间。
由于PVD 技术在沉积过程中,材料以固态形式进行转移,因此PVD制备的薄膜具有较高的致密性和纯度。
此外,PVD技术还可以在复杂的表面结构上进行沉积,如孔洞、凹槽等,适用于制备具有特殊形状要求的薄膜。
相比之下,CVD技术适用于制备较厚的薄膜,通常在几十纳米到几百微米之间。
由于CVD技术是通过化学反应生成固态产物,因此可以在基底表面上形成较为均匀的薄膜。
此外,CVD技术还可以在较低的温度下进行沉积,适用于对基底温度敏感的材料。
PVD(物理气相沉积)简介

书山有路勤为径,学海无涯苦作舟
PVD(物理气相沉积)简介
1. PVD 简介PVD 是英文Physical Vapor Deposition(物理气相沉积)的缩写,是指在真空条件下,采用低电压、大电流的电弧放电技术,利用气体放
电使靶材蒸发并使被蒸发物质与气体都发生电离,利用电场的加速作用,使被
蒸发物质及其反应产物沉积在工件上。
2. PVD 技术的发展PVD 技术出现于二十世纪七十年代末,制备的薄膜具
有高硬度、低摩擦系数、很好的耐磨性和化学稳定性等优点。
最初在高速钢刀
具领域的成功应用引起了世界各国制造业的高度重视,人们在开发高性能、高
可靠性涂层设备的同时,也在硬质合金、陶瓷类刀具中进行了更加深入的涂层
应用研究。
与CVD 工艺相比,PVD 工艺处理温度低,在600℃以下时对刀具材料的抗弯强度无影响;薄膜内部应力状态为压应力,更适于对硬质合金精密复
杂刀具的涂层;PVD 工艺对环境无不利影响,符合现代绿色制造的发展方向。
目前PVD 涂层技术已普遍应用于硬质合金立铣刀、钻头、阶梯钻、油孔钻、铰刀、丝锥、可转位铣刀片、异形刀具、焊接刀具等的涂层处理。
PVD 技术不仅提高了薄膜与刀具基体材料的结合强度,涂层成分也由第
一代的TiN 发展为TiC、TiCN、ZrN、CrN、MoS2、TiAlN、TiAlCN、TiN- AlN、CNx、DLC 和ta-C 等多元复合涂层。
3. 星弧涂层的PVD 技术增强型磁控阴极弧:阴极弧技术是在真空条件下,通过低电压和高电流将靶材离化成离子状态,从而完成薄膜材料的沉积。
增强型磁控阴极弧利用电磁场的共同作用,将靶材表面的电弧加以有效地控
制,使材料的离化率更高,薄膜性能更加优异。
- 1、下载文档前请自行甄别文档内容的完整性,平台不提供额外的编辑、内容补充、找答案等附加服务。
- 2、"仅部分预览"的文档,不可在线预览部分如存在完整性等问题,可反馈申请退款(可完整预览的文档不适用该条件!)。
- 3、如文档侵犯您的权益,请联系客服反馈,我们会尽快为您处理(人工客服工作时间:9:00-18:30)。
绪论
低放气膜和透明阻挡膜:TiN膜是一种很理想的低放气膜 ,其沉积在真空容器的内表面,不仅吸附气体的量很少, 而且还能有效的阻止容器内壁溶解的气体渗入真空中。 陶瓷薄膜可以阻止空气中氧气和氢气的渗透,故称这种陶 瓷薄膜为透明阻挡膜。如用于保证食品与外界隔离的食品 包装袋,人们在塑料膜上沉积一层透明的SiOx膜。 耐氧化膜和耐腐蚀膜:TiC,SiC等。
分离功能膜:气体分离膜、液体分离膜、离子交换功能膜 能量转化功能膜:浓差能量转化膜、光能转化膜、机械能转化膜、电能转化膜、导电膜 生物功能膜:探感膜、生物反应器膜、医用膜
气相系统用膜:伴有表面流动的分子流动、气体扩散、聚合物膜中溶解扩散流动、在溶剂化聚合物膜 中扩散流动 气-液系统用膜:大孔结构(移去气流中的雾沫夹带或将气体引入液相)、微孔结构(制成超细孔过 滤器)、聚合物结构(气体扩散进入液体或从液体中移去某种气体) 液-液系统用膜:气体从一种液相进入另一液相、溶质或溶剂从一种液相渗透到另一液相 气-固系统用膜:用膜除去气体中的颗粒 液-固系统用膜:大孔介质过滤淤浆、生物废料处理、破乳 固-固系统用膜:基于颗粒大小的固体筛分
2.3 有机、聚合物薄膜材料 2.4 半导体薄膜材料
表. 膜的各种分类方法
分类方法
膜的名称
按膜的材 料分类
按膜的结 构分类
按膜的功 能分类
按膜的用 途分类
按膜的作 用机理分
类
天然膜:生物膜、天然物质改性或再生制成的膜 合成膜:无机膜、高分子聚合物膜
多孔膜:微孔介质、大孔膜 非多孔膜:无机膜、高分子聚合物膜 液膜:无固相支撑型又称乳化液膜;有固相支撑型又称固定膜、支撑液膜
绪论
1. 薄膜的定义 薄膜是一种二维材料,它在厚度方向上的尺寸很小,
往往为纳米至微米量级。从宏观上讲,薄膜是位于两个平面 之间的一层物质,其厚度与另外两维的尺寸相比要小得多。 从微观角度来讲,薄膜是由原子或原子团凝聚而成的二维材 料。按膜厚,对膜的经典分类认为,小于1微米的为薄膜, 大于1微米的为厚膜 。
Hale Waihona Puke 论2.2 无机、陶瓷薄膜材料——结构性陶瓷薄膜材料
润滑膜:层状石墨,MoS2,WS2,PbO,CaF2,BaF2等; 耐磨损膜:TiN,HfN,CrN,Cr7C3,Si3N4,Al2O3等。 采用多层膜,如:两层膜TiN/TiC、Al2O3/TiC等,三层膜 TiN/Al2O3/TiC已达到实用化。 装饰膜:TiN、ZrN、HfN、TaC为金黄色,BeC为红色,NbN 为亮褐色,WN为褐色,MnN为黑色等。其中离子镀 CrN,Cr2N(土色、白色),反应磁控溅射(Ti,Al)N(褐色) 等已达到实用化。
绪论
2.4 半导体薄膜材料
光学功能材料:Si膜,PbS,Ni硫化物,Cr 氧化物等; 电子功能材料:以GaAs为中心的系统III-V 族化合物半导体。 此外,还有光电子功能材料、能量变换功能 薄膜材料,传感器功能材料等。
在多数情况下,严格区分薄膜和厚膜并无实际意义,而针 对具体的膜层形成方法、膜层材料、界面结构、结晶状态、晶 体学取向、微观组织、各种性能和功能进行研究更有用。
绪论
2. 薄膜材料的分类
2.1 金属薄膜材料 结构性金属薄膜材料 功能性金属薄膜材料
2.2 无机、陶瓷薄膜材料 结构性陶瓷薄膜材料 功能性陶瓷薄膜材料
绪论
2.1 金属薄膜材料——结构性金属薄膜材料
硬质膜:耐磨损,不是以纯金属,而是以碳化物、氮化物、 氧化物、硼化物等金属化合物的形式而使用的。如:TiC, Al2O3,B4C等。 润滑薄膜:用作固体润滑膜的金属有铅、锡、金、银等。 Au-Mo,Ag-Re等合金也用于润滑膜,与Au、Ag膜相比, 硬度较高,而且在大气中,在高温下,由于表面形成Mo或 Re的氧化物而提高润滑效果。
绪论
2.2 无机、陶瓷薄膜材料——功能性陶瓷薄膜材料
光学薄膜材料:防反射膜如MgF2或采用MgF2和金属氧化物。 选择透射膜和选择吸收膜,为了减轻夏季冷房的负荷,使可见 光一定程度的透过,而热线部分被反射或吸收,如TiO2,SnO2 ,CrN等;另一方面,为了减轻冬季暖房的负荷,要使热线部 分透过,以便保温,如Zn0/Ag/Zn0, ZnS/Ag/ZnS等。 电子薄膜材料:导电膜In2O3、SnO2,电介质膜SiO2, CaF, BaF2, Si3N4等。 光电子薄膜材料:是“与光具有显著相互作用的材料”,利用 光电子材料的技术领域包括光运输、显示、光计量、全息照相 等。如Nb2O5、LiNbO3、IrOx、NiOx等。
吸附性膜:多孔膜(多孔石英玻璃、活性炭、硅胶等)、反应膜(膜内含有与渗透过来的物质发生反 应的物质) 扩散性膜:聚合物膜(扩散性的溶解流动)、金属膜(原子状态的扩散)、玻璃膜(分子状态的扩散) 离子交换膜;阳离子交换树脂膜、阴阳离子交换树脂膜 选择渗透膜:渗透膜、反渗透膜、电渗析膜 非选择性膜:加热处理的微孔玻璃、过滤型的微孔膜
绪论
2.1 金属薄膜材料——功能性金属薄膜材料
光学薄膜材料:吸收,反射,增透膜如: Si, CdTe, GaAs, CuInSe2, MgF。发光膜: ZnS, ZnSe, AlxGa1-xAs, GaN, SiC 等; 磁性薄膜材料:Co-Cr, Mn-Bi, Ni3Fe等; 导电薄膜材料:NiCr, NiSi2, NiSi, CoSi2, TiSi2等; 压电薄膜材料:AlN, ZnO, LiNbO3, BaTiO3, PbTiO3等; 半导体薄膜材料:GaAs, GaN, InSb, CdTe, CdS, ZnSe等。
绪论
信息薄膜材料:在半导体存储器中的应用,如SiO2薄膜;在 光盘中的应用,如TeOx及硫属(S,Se,Te)化合物。 生物薄膜材料:如生体不活性陶瓷Al2O3,ZrO2等;生体活 性陶瓷羟基磷灰石、磷酸钙等。
2.3 有机、聚合物薄膜材料 介电质薄膜材料:通用塑料薄膜 [聚对苯二甲酸乙二酯(PET )、聚丙烯(pp)]具有良好的介电性能,由其可作薄膜电 容器。 光致电导材料:如酞菁系材料。 压电及热电功能材料:如聚偏二氟乙烯膜。