齿轮表面热处理
齿轮的热处理要求

齿轮的热处理要求
嘿,朋友们!今天咱就来聊聊齿轮的热处理要求,这可真是个超级重要
的事儿啊!
你想想看,齿轮就好比是机械世界的小战士,它们得坚强、耐用才行啊!那热处理就是让这些小战士变得厉害的秘密魔法啦!比如说,汽车里的齿轮吧,如果热处理没做好,那在高速运转的时候,会不会“嘎吱嘎吱”响,甚至突然就坏掉啦?那多吓人呐!
对于齿轮的热处理要求,那可真是一点儿都不能马虎。
首先就是温度啦!就像我们做饭要掌握好火候一样,热处理的温度得恰到好处,不能太高也不能太低。
太高了,齿轮可能就被烧变形啦;太低了呢,又起不到强化的效果。
这就好比烤面包,温度合适才能烤出香喷喷、又松又软的面包呀!
还有时间呢,也得把握得刚刚好。
时间太短,效果达不到;时间太长,
又可能会过头。
就好像做一件事情,时间不够做不好,时间太久又可能会变得很累赘呀!而且不同的齿轮材料,要求还都不一样呢。
再说说冷却,这冷却速度的快慢也很关键呐!冷却太快,齿轮可能会变得很脆;冷却太慢,又可能达不到想要的硬度。
这不就像是跑步冲刺,一下子冲太快可能会摔倒,慢慢跑又拿不到好成绩一样嘛!
在实际操作中,热处理师傅们那可是要小心翼翼、全神贯注的。
他们就像是齿轮的超级英雄,要保证每一个齿轮都能经过完美的热处理。
他们得时刻关注着温度、时间和冷却等各种因素,稍有差错可不行啊!
总之,齿轮的热处理要求真的是至关重要啊!这关系到各种机械设备能不能正常运转,能不能长久使用。
我们可千万不能小瞧了它呀!大家一定要重视起来哟!。
齿轮热处理工艺流程

齿轮热处理工艺流程齿轮热处理是制造过程中不可或缺的一环,旨在提高齿轮的耐磨性和强度,确保其在使用中的可靠性和寿命。
下面将介绍一种常见的齿轮热处理工艺流程。
首先,需要对齿轮进行预处理。
预处理的目的是去除齿轮表面的氧化物和油污等杂质,以保证后续的热处理效果。
常见的预处理方法包括溶剂清洗和热气蒸发等。
接下来,将齿轮置入高温炉中进行加热。
加热温度根据齿轮材料的不同来确定,常见的温度范围为800°C至1000°C。
在加热过程中,需要控制加热速度和保温时间,以确保齿轮均匀加热,避免产生过多的残余应力。
在加热结束后,需要进行淬火处理。
淬火是齿轮热处理工艺的关键步骤,它通过迅速冷却来改变齿轮的组织和性能。
常见的淬火介质有水、油和气体等,不同介质的选择将影响齿轮的硬度和韧性。
在淬火过程中,需要控制冷却速度,以避免产生过高的残余应力和变形。
淬火完成后,需要进行回火处理。
回火是为了减少由淬火过程中产生的脆性,提高齿轮的韧性和可靠性。
回火温度根据齿轮的要求来确定,一般在200°C至500°C之间进行。
回火时间需要根据齿轮的尺寸和材料来确定,一般在几小时至十几小时之间。
最后,进行除锈和加工后处理。
除锈是为了去除齿轮表面的氧化物和锈蚀物,以保证齿轮的表面质量。
加工后处理包括对齿轮进行排气和清洁等,以确保齿轮的精度和质量。
总之,齿轮热处理工艺流程包括预处理、加热、淬火、回火和后处理等步骤。
每个步骤都具有其特定的目的和要求,需要在严格的控制下进行。
只有合理地选择工艺参数和正确地操作,才能得到符合要求的齿轮产品。
齿轮常用材料及热处理

齿轮常用材料及热处理
为了保证齿轮工作的可靠性,提高其使用寿命,齿轮的材料及其热处理应根据工作条件和材料的特点来选取。
对齿轮材料的基本要求是:应使齿面具有足够的硬度和耐磨性,齿心具有足够的韧性,以防止齿面的各种失效,同时应具有良好的冷、热加工的工艺性,以达到齿轮的各种技术要求。
常用的齿轮材料为各种牌号的优质碳素结构钢、合金结构钢、铸钢、铸铁和非金属材料等。
一般多采用锻件或轧制钢材。
当齿轮结构尺寸较大,轮坯不易锻造时,可采用铸钢;开式低速传动时,可采用灰铸铁或球墨铸铁、低速重载的齿轮易产生齿面塑性变形,轮齿也易折断,宜选用综合性能较好的钢材;高速齿轮易产生齿面点蚀,宜选用齿面硬度高的材料;受冲击载荷的齿轮,宜选用韧性好的材料。
对高速、轻载而又要求低噪声的齿轮传动,也可采用非金属材料、如夹布胶木、尼龙等。
常用的齿轮材料及其力学性能列于下表。
根据热处理后齿面硬度的不同,齿轮可分为软齿面齿轮(≤350HBS)和硬齿面齿轮(>350HBS)。
一般要求的齿轮传动可采用软齿面齿轮。
为了减小胶合的可能性,并使配对的大小齿轮寿命相当,通常使小齿轮齿面硬度比大齿轮齿面硬度高出30~
50HBS。
对于高速、重载或重要的齿轮传动,可采用硬齿面齿轮组合,齿面硬度可大致相同。
常用齿轮材料及其力学性能。
齿轮材料及热处理
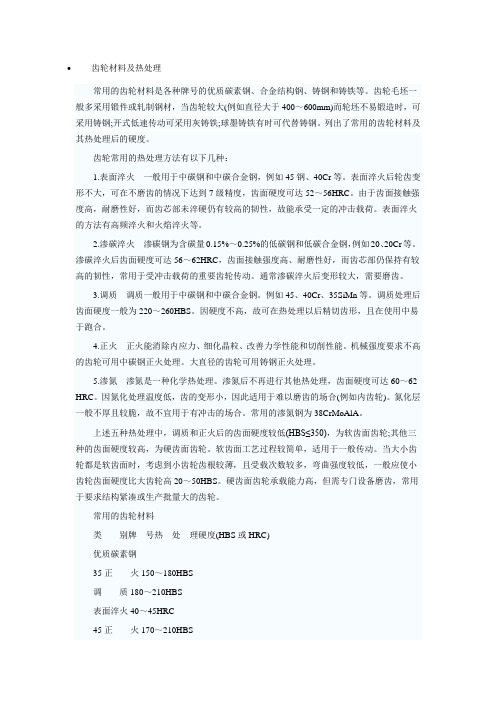
齿轮材料及热处理常用的齿轮材料是各种牌号的优质碳素钢、合金结构钢、铸钢和铸铁等。
齿轮毛坯一般多采用锻件或轧制钢材,当齿轮较大(例如直径大于400~600mm)而轮坯不易锻造时,可采用铸钢;开式低速传动可采用灰铸铁;球墨铸铁有时可代替铸钢。
列出了常用的齿轮材料及其热处理后的硬度。
齿轮常用的热处理方法有以下几种:1.表面淬火一般用于中碳钢和中碳合金钢,例如45钢、40Cr等。
表面淬火后轮齿变形不大,可在不磨齿的情况下达到7级精度,齿面硬度可达52~56HRC。
由于齿面接触强度高,耐磨性好,而齿芯部未淬硬仍有较高的韧性,故能承受一定的冲击载荷。
表面淬火的方法有高频淬火和火焰淬火等。
2.渗碳淬火渗碳钢为含碳量0.15%~0.25%的低碳钢和低碳合金钢,例如20、20Cr等。
渗碳淬火后齿面硬度可达56~62HRC,齿面接触强度高、耐磨性好,而齿芯部仍保持有较高的韧性,常用于受冲击载荷的重要齿轮传动。
通常渗碳淬火后变形较大,需要磨齿。
3.调质调质一般用于中碳钢和中碳合金钢。
例如45、40Cr、35SiMn等。
调质处理后齿面硬度一般为220~260HBS。
因硬度不高,故可在热处理以后精切齿形,且在使用中易于跑合。
4.正火正火能消除内应力、细化晶粒、改善力学性能和切削性能。
机械强度要求不高的齿轮可用中碳钢正火处理。
大直径的齿轮可用铸钢正火处理。
5.渗氮渗氮是一种化学热处理。
渗氮后不再进行其他热处理,齿面硬度可达60~62 HRC。
因氮化处理温度低,齿的变形小,因此适用于难以磨齿的场合(例如内齿轮)。
氮化层一般不厚且较脆,故不宜用于有冲击的场合。
常用的渗氮钢为38CrMoAlA。
上述五种热处理中,调质和正火后的齿面硬度较低(HBS≤350),为软齿面齿轮;其他三种的齿面硬度较高,为硬齿面齿轮。
软齿面工艺过程较简单,适用于一般传动。
当大小齿轮都是软齿面时,考虑到小齿轮齿根较薄,且受载次数较多,弯曲强度较低,一般应使小齿轮齿面硬度比大齿轮高20~50HBS。
齿轮常用材料及热处理

齿轮常用材料及热处理
为了保证齿轮工作的可靠性,提高其使用寿命,齿轮的材料及其热处理应根据工作
条件和材料的特点来选取。
对齿轮材料的基本要求是:应使齿面具有足够的硬度和耐磨性,齿心具有足够的韧性,以防止齿面的各种失效,同时应具有良好的冷、热加工的工艺性,以达到齿轮的各种技术要求。
常用的齿轮材料为各种牌号的优质碳素结构钢、合金结构钢、铸钢、铸铁和非金属
材料等。
一般多采用锻件或轧制钢材。
当齿轮结构尺寸较大,轮坯不易锻造时,可采用铸钢;开式低速传动时,可采用灰铸铁或球墨铸铁、低速重载的齿轮易产生齿面塑性变形,轮齿也易折断,宜选用综合性能较好的钢材;高速齿轮易产生齿面点蚀,宜选用齿面硬度高的材料;受冲击载荷的齿轮,宜选用韧性好的材料。
对高速、轻载而又要求低噪声的齿轮传动,也可采用非金属材料、如夹布胶木、尼龙等。
常用的齿轮材料及其力学性能列于下表。
钢制齿轮的热处理方法主要有以下几种
•表面淬火
表面淬火常用于中碳钢和中碳合金钢,如45、40Cr钢等。
表面淬火后,
齿面硬度一般为 40〜55HRC特点是抗疲劳点蚀、抗胶合能力高。
耐磨性好;由于齿心部分未
淬硬,齿轮仍有足够的韧性,能承受不大的冲击载荷。
根据热处理后齿面硬度的不同,齿轮可分为软齿面齿轮(< 350HBS和硬齿面齿轮
(> 350HBS)。
一般要求的齿轮传动可采用软齿面齿轮。
为了减小胶合的可能性,并使配对的大小齿轮寿命相当,通常使小齿轮齿面硬度比大齿轮齿面硬度高岀30〜 50HBS。
对于高速、重载或重要的齿轮传动,可采用硬齿面齿轮组合,齿面硬度可大致相同。
硬齿面齿轮常用热处理方式

硬齿面齿轮常用热处理方式概述硬齿面齿轮是一种常见的机械传动元件,用于传递动力和扭矩。
为了提高其硬度和耐磨性,常常需要进行热处理。
本文将介绍硬齿面齿轮常用的热处理方式,包括淬火、渗碳、氮化等。
1. 淬火(Quenching)淬火是一种通过快速冷却来改变材料的组织结构和性能的方法。
对于硬齿面齿轮来说,淬火可以提高其硬度和强度,增加其耐磨性和使用寿命。
淬火过程中,首先将齿轮加热至适当的温度,使其达到奥氏体组织。
然后迅速将其浸入冷却介质中,如水或油中,以快速降低温度。
这样可以使奥氏体转变为马氏体组织,并产生较高的硬度。
2. 渗碳(Carburizing)渗碳是一种通过在材料表面添加富含碳元素的材料层来增加表面硬度和耐磨性的方法。
对于硬齿面齿轮来说,渗碳可以提高其表面硬度,增加其抗磨损能力。
渗碳过程中,首先将齿轮放置在含有富含碳元素的固体、液体或气体环境中。
通过加热和保持一定时间,使碳元素渗透到齿轮表面,并与基体材料发生化学反应。
这样可以形成一层富含碳元素的淬火层,提高齿轮的硬度。
3. 氮化(Nitriding)氮化是一种通过在材料表面添加氮元素来提高硬度和耐磨性的方法。
对于硬齿面齿轮来说,氮化可以增加其表面硬度,改善其抗疲劳性能。
氮化过程中,首先将齿轮放置在富含氨气的环境中。
通过加热和保持一定时间,使氨气分解并释放出氮原子。
这些氮原子会渗透到齿轮表面,并与基体材料发生化学反应。
这样可以形成一层富含氮元素的淬火层,提高齿轮的硬度。
4. 碳氮共渗(Carbonitriding)碳氮共渗是一种通过在材料表面同时添加碳和氮元素来提高硬度和耐磨性的方法。
对于硬齿面齿轮来说,碳氮共渗可以增加其表面硬度,并改善其抗疲劳性能和韧性。
碳氮共渗过程中,首先将齿轮放置在含有富含碳和氮元素的固体、液体或气体环境中。
通过加热和保持一定时间,使碳和氮元素渗透到齿轮表面,并与基体材料发生化学反应。
这样可以形成一层富含碳和氮元素的淬火层,提高齿轮的硬度。
齿轮加工消除热处理变形的工艺

齿轮是一种常见的机械传动元件,广泛应用于各种机械设备中。
在齿轮加工的过程中,常常会遇到热处理变形的问题,这会影响齿轮的精度和使用寿命。
如何在齿轮加工过程中消除热处理变形成为了重要的技术课题。
一、热处理工艺1. 热处理工艺的种类热处理工艺包括退火、正火、淬火和回火等。
这些工艺对齿轮的硬度、强度和耐磨性都会有不同程度的影响。
2. 热处理变形的原因在热处理过程中,齿轮会受到热膨胀和热应力的影响,从而产生变形。
特别是在淬火过程中,由于齿轮的不均匀冷却会导致变形更为严重。
二、消除热处理变形的工艺1. 预留余量在设计齿轮的尺寸时,可以适当增加一些余量,以便在热处理后进行修磨,从而达到消除变形的效果。
2. 低温回火在淬火后,将齿轮进行低温回火处理,可以有效减少热处理变形的产生。
低温回火可以消除淬火后的残余应力,使齿轮保持较好的形状精度。
3. 调整热处理工艺参数通过调整热处理工艺的温度、时间和速度等参数,可以减小热处理变形的影响。
选择合适的热处理工艺参数对消除变形至关重要。
4. 多次热处理在齿轮加工中,可以采用多次热处理的方法,即在不同阶段对齿轮进行热处理,这样可以减少每次热处理产生的变形量,使齿轮在每次热处理后都能保持尽可能好的形状。
5. 后加工在热处理后进行修磨和整形,可以消除一部分热处理变形,提高齿轮的精度和表面质量。
三、工艺控制1. 设计优化在齿轮的设计阶段,可以通过优化结构和材料选用等,减少热处理变形的产生。
合理的设计能够在一定程度上消除热处理变形。
2. 热处理设备的改进在热处理设备上进行改进,比如采用先进的淬火方式、控制工艺参数等,可以减小热处理变形的产生。
3. 质量控制加强对齿轮加工过程中的质量控制,确保每一道工序都符合要求,这也是避免热处理变形的重要手段。
消除热处理变形的工艺在齿轮加工中至关重要。
通过合理的热处理工艺和工艺控制,可以有效减少热处理变形的影响,提高齿轮的精度和使用寿命。
随着技术的发展,相信在未来会有更多的创新工艺出现,为消除热处理变形提供更多的解决方案。
高温渗碳齿轮热处理工艺
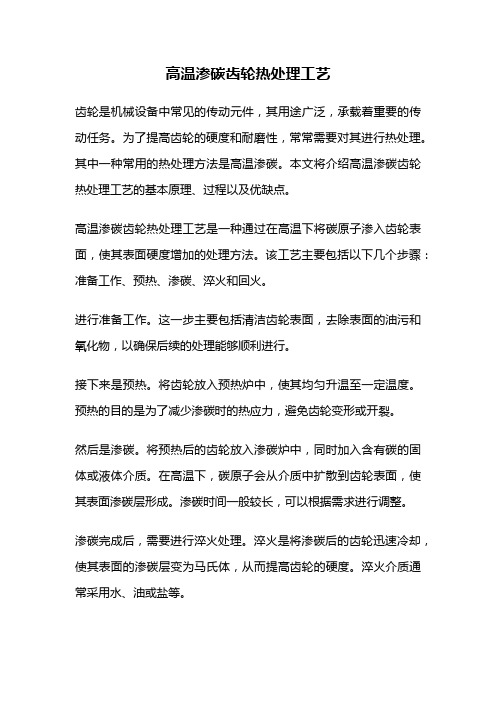
高温渗碳齿轮热处理工艺齿轮是机械设备中常见的传动元件,其用途广泛,承载着重要的传动任务。
为了提高齿轮的硬度和耐磨性,常常需要对其进行热处理。
其中一种常用的热处理方法是高温渗碳。
本文将介绍高温渗碳齿轮热处理工艺的基本原理、过程以及优缺点。
高温渗碳齿轮热处理工艺是一种通过在高温下将碳原子渗入齿轮表面,使其表面硬度增加的处理方法。
该工艺主要包括以下几个步骤:准备工作、预热、渗碳、淬火和回火。
进行准备工作。
这一步主要包括清洁齿轮表面,去除表面的油污和氧化物,以确保后续的处理能够顺利进行。
接下来是预热。
将齿轮放入预热炉中,使其均匀升温至一定温度。
预热的目的是为了减少渗碳时的热应力,避免齿轮变形或开裂。
然后是渗碳。
将预热后的齿轮放入渗碳炉中,同时加入含有碳的固体或液体介质。
在高温下,碳原子会从介质中扩散到齿轮表面,使其表面渗碳层形成。
渗碳时间一般较长,可以根据需求进行调整。
渗碳完成后,需要进行淬火处理。
淬火是将渗碳后的齿轮迅速冷却,使其表面的渗碳层变为马氏体,从而提高齿轮的硬度。
淬火介质通常采用水、油或盐等。
最后是回火。
齿轮经过淬火后,表面硬度较高,但同时也会变脆。
为了增加齿轮的韧性和韧度,需要进行回火处理。
回火温度和时间的选择需要根据具体情况进行调整,以保证齿轮的性能达到要求。
高温渗碳齿轮热处理工艺具有以下几个优点。
首先,可以有效提高齿轮的硬度和耐磨性,延长使用寿命。
其次,渗碳层与基体的结合牢固,不易脱落。
此外,该工艺适用于各种不同形状和尺寸的齿轮,具有较好的适应性。
然而,高温渗碳齿轮热处理工艺也存在一些不足之处。
首先,渗碳过程中需要较长的时间,增加了生产周期和成本。
其次,如果渗碳过程控制不当,可能会导致齿轮变形或开裂。
此外,渗碳层的厚度通常较薄,对于一些特殊要求的齿轮可能不适用。
高温渗碳齿轮热处理工艺是一种常用的齿轮热处理方法,通过在高温下使碳原子渗入齿轮表面,提高其硬度和耐磨性。
该工艺具有一定的优点,但也存在一些局限性。
- 1、下载文档前请自行甄别文档内容的完整性,平台不提供额外的编辑、内容补充、找答案等附加服务。
- 2、"仅部分预览"的文档,不可在线预览部分如存在完整性等问题,可反馈申请退款(可完整预览的文档不适用该条件!)。
- 3、如文档侵犯您的权益,请联系客服反馈,我们会尽快为您处理(人工客服工作时间:9:00-18:30)。
I齿的转动,带动了II齿 的转动,啮合点A的位置 也会由上而下地在II齿 表面移动直到II齿的根 部。 在啮合点A处还有一个特 点,就是两个齿表面有 相对的滑动,滑动方向 与压应力垂直。
当齿表面磨损到一定程度,就会使两齿的啮合不平稳。
于是,大的噪声、大的振动就会接踵而来,使车床主
轴产生度可达3200℃,用 它加热钢的表面,加热速度快,使钢表层一定深度内加热 到橘红色,大约850℃,而钢的里边温度还不高。
这时,浇上水,表面和里面很快冷却,表层一定深度 内就淬火了,硬度很高,很耐磨,而里面却因为温度低,
淬不上火,硬度就低,韧性好,这不就达到三高了吗?!
在整个齿轮齿面表面淬火后,还不能直接用,因为表 面虽然很硬了,但脆性大,用起来容易裂,也容易崩块。
控制感应线圈对零件的感应加热时间,就可有效地控制加 热温度,待表面达到所需的温度就可将感应线圈移开、喷水, 使零件在加热深度范围内淬火,获得高硬度的淬火层。
对于钢,加热温度850℃以上时,加热深度与感应电 流频率的关系为:
式中,δ f
50 (cm)
f
加热深度(cm) 感应电流频率(Hz)
例如,当f=8000Hz时,加热深度为0.56cm,即5.6mm; 当f=1MHz时,加热深度为0.O5cm,即0.5Omm。
齿轮用感应加热表面淬火法就很 容易达到三高(高耐磨性、高强 度、高韧性)的要求。
无论是碳钢还是合金钢,可以通 过加热和冷却来改变它们的性能。
把 三 块 45 钢 ( 碳 的 质 量 分数为0.45%的一种碳 钢)放在电炉里都加热 到 830℃ , 一 块 取 出 投 入水盆中冷却,一块取 出放在地上在空气中自 然冷却,最后一块就放 在电炉里停了电后让它 同炉子一块冷却。
当它们都冷到室温后,测 定它们的洛氏硬度,您就 会惊奇地发现:它们的硬 度差别很大:所以,人们 就可以按需要采用不同的 加热和冷却方去来得到所 想要得到的性能了。
当代,随着科学技术的 发展,火焰加热表面热处 理方法的不足,取而代之 的是感应加热表面淬火法、 高密度能源表面淬火法。
感 应加热表面淬火法、高密 度能源表面淬火法,是近代表面 热处理技术。
感应圈接通高频电源后, 就会产生高频的磁场。
置于高频磁场中的钢制 零件中就会产生感应的高 频电流。
高频电流在零件中的分 布是不均匀的,表面层的 电流密度高,而中心的电 流密度低,这种现象称为
众所周知,钢虽是导体,但有电阻。
电流流过有电阻的导体,就会产生热量, 即
Q=0.24I2Rt(J)
式中,Q-热量(J) I-电流强度(A) R-电阻(Ω) t-时间(s)
热量Q就可用来加热零 件。
不过对零件的加热并不 是在整个截面上均匀的,而 是集中在电流密度高的表层。
显然,加热的深度跟频 率有关。
第1块很硬,为HRC55;第2块比较硬,为 HRC25;第3块软得很,为HRCl8。
第1种水冷方法称为淬火;
第2种空冷方法叫正火; 第3种随炉冷方法叫退火。
这三种“火”都有一个特点,就是一块钢,要硬都硬, 要软都软,也就是整体热处理。 前面所说的齿轮若接受淬火,齿表面的硬度高了,耐磨 性好了,但齿却一冲即断-太脆了! 相反,若接受退火,齿是不会一冲即断了,但齿表面却 不耐磨了。
为了去掉脆性,还要最后用氧-乙炔火焰扫一遍,把 表面加热到200℃左右。
这个过程称为淬火后的低温回火,能去掉脆性和去 掉由于加热、冷却引起的内应力。
两步合起来,就称为钢的火焰表面热处理,这样, 齿轮就可用了。
火焰表面热处理的不足: 首先,用氧-乙炔火焰加热时,零件表面的温度只能 凭目视颜色变化来估计,这就只能依靠操作者的经验。 第二,整个操作过程都是手工操作,再加上火焰温度 有限,使工作效率和应用范围受到了限制。 这种表面热处理方法只适用于处理简单而且不大的零 件表面,或者处理大零件的局部范围。
传动齿轮在啮合时的受力情况是很复杂的。 上图是用光弹试验的方法所显示的齿轮的受力情况。
图中的“黑色”齿是 主动齿(用I表示),II 是被动齿。 I齿压在II齿的A点, 不仅传递了动力,而 且使II齿变成了“花 脸”。
上图的线条表示了应力的大小和分布,线条愈密,应 力就愈大。由图可以清楚地看到,两齿的啮合点A处 压应力最大。
根据摩擦磨损的原理,两个表面 承受压应力,又有相对滑动,两 个表面就必然会产生磨损。
图中,还要注意一个 危险点,这就是B点。 I齿和II齿在A点啮合传 动,使齿根部的B点受 到大的拉应力,C点受 到大的压应力。
这就意味着,A点啮合产生的压应力可以变成 一个弯矩,想把这个II齿折断。
对齿轮来说,改变一个档次,齿轮就会受一次 冲击;车床开动或停止,也会使齿轮受到冲击。
汽车、拖拉机在起步、刹车,以及走在高低不 平的路面上时,所有的传动齿轮部会受到冲击。冲击 载荷的危害可比上述的弯矩产生的危害大多了。
假如齿抗不住冲击载荷,那只有一冲即断了!
三
若把上述各点归纳一下,可以看到,齿
高
轮的表面要高耐磨性,齿的芯部
又要有高的强度和高的冲击韧性。
这个“三高”,缺一不可!
大家知道:要使钢的强度高、硬度高(亦即耐磨 性高),那么它只能降低冲击韧性;或者相反,要提 高冲击韧性,就必然使强度和硬度降低。 因此,在一般条件下,三高是没法同时达到的。
碳钢与合金钢
钢是人们最熟悉也是使用极广的一种材料。 它是铁(Fe)与碳的合金,但碳的质量分数只能低于 2.11%,超过这个比例就是铸铁了。
有一类钢只由铁和碳组成,称为碳钢;还有一 类钢中除了铁和碳外,还有其他的元素,如硅(Si)、 锰(Mn)、铬(Cr)、镍(Ni)、钼(Mo)、钨(W)、钒(V) 等,这类钢称为合金钢。
整体热处理不能解决齿轮的三高性能要求的问题。
用氧-乙炔火焰加热钢的表面, 这时浇上水,使其很快冷却, 再把表面加热到200℃左右。称 为钢的火焰表面热处理。
用一把气焊枪连接好氧气管和乙炔管后,开启气焊枪, 点着氧-乙炔火焰,调到中性焰,用火焰逐个加热齿面。 加热到表面出现橘红色时就开水管冷却,直到每个齿都 处理完。最后,再将每个齿快速地用焊枪火焰扫一遍。