玻璃退火问题与切割
浮法玻璃退火产生的缺陷及控制

浮法玻璃中退火产生的缺陷及控制理工大学战营一、玻璃的退火玻璃退火的目的是减弱和防止玻璃制品中出现过大的剩余应力和光学不均匀性,稳定玻璃部的构造。
玻璃的退火可分成两个主要过程:一是玻璃中应力的减弱或消失,二是防止应力的重新产生。
玻璃中应力的减弱和消除是以松弛理论为根底的,所谓应力松弛是指材料在分子热运动的作用下使应力消散的过程,应力的松弛速度在很大程度上决定于玻璃所处的温度。
玻璃在加热或冷却过程中,由于其导热性较差,在其外表层和层之间必然产生温度梯度,因而在外层之间产生应力。
这种由于温度梯度存在而产生的应力称为温度应力或热应力,此种应力的大小,既取决于玻璃中的温度梯度,又与玻璃的热膨胀系数有关〔玻璃的化学成分决定玻璃的热膨胀系数〕。
热应力按其存在的特点可分为暂时应力和永久应力。
暂时应力,当玻璃受不均匀的温度变化时产生的热应力,随着温度差的存在而存在,随温度差的消失而消失,被称为暂时应力。
应力的建立和消失过程。
当制品冷却开场时,因为玻璃的外层冷却速度快,所以外部温度比部温度低,外层收缩大,而这时层温度较高,且力求阻碍外层收缩,这样造成玻璃外层产生应力,部产生压应力。
在应力过渡到压应力之间存在着中间层,其应力值为零。
当冷却接近完毕时,外层体积几乎不再收缩,但此时玻璃部仍有一定的温度,其体积力求收缩,此时造成外部受压应力,层受应力。
由此可见,在冷却完毕时,产生的应力恰好和冷却开场时产生的应力性质相反,两者可以得到局部抵消。
冷却全部完毕时,即当玻璃的外层温度和层温度趋向完全一致时,上述两种应力恰好抵消。
我们称这种应力为暂时应力。
永久应力,当温度消失时〔制品的外表和部温度均等于常温时〕,残留在玻璃中的热应力称为永久应力,又称为应力。
玻璃中永久应力的成因,是由于在高温的弹塑性阶段热应力松弛而形成的温度变形被“冻结〞下来的缘故。
当玻璃板逐渐冷却到室温均衡时,玻璃中残存的应力实际等于玻璃在高温阶段松弛掉的热弹应力,但方向相反。
玻璃的退火与钢花

第15章玻璃的退火与钢化玻璃制品在生产过程中(即由熔融状态的玻璃液变成脆性固体玻璃制品),玻璃经受激烈的不均匀的温度变化,使内外层产生温度梯度,硬化速度不一样,引起制品中产生不规则的热应力。
这种热应力能降低制品的机械强度和热稳定性,也影响玻璃的光学均一性,若应力超过制品的极限强度,便会自行破裂。
所以玻璃制品中存在不均匀的热应力是一项重要的缺陷。
退火是一种热处理过程,可使玻璃中存在的热应力尽可能地消除或减小至允许值。
除玻璃纤维和薄壁小型空心制品外,几乎所有玻璃制品都需要进行退火。
对于光学玻璃和某些特种玻璃,退火要求十分严格,必须在退火的温度范围内保持相当长的时间,使它各部分的结构均匀,然后以最小的温差进行降温,以达到要求的光学性能,这种退火称为精密退火。
玻璃制品存在热应力并不经常是有害的。
若通过人为的热处理过程使玻璃表面层产生有规律的、均匀分布的压应力,还能提高玻璃制品的机械强度和热稳定性。
这种热处理方法称为玻璃的钢化。
化学组成相同的玻璃钢化与不钢化具有截然不同的性能。
但并非所有的玻璃制品都能进行钢化。
15.1 玻璃中的应力物质内部单位截面上的相互作用力称为内应力。
玻璃的内应力根据产生的原因不同可分为三类:因温度差产生的应力,称为热应力;因组成不一致而产生的应力,称为结构应力;因外力作用产生的应力,称为机械应力。
15.1.1 玻璃中的热应力玻璃中的热应力按其存在的特点,分为暂时应力和永久应力。
15.1.1.1 暂时应力温度低于应变点而处于弹性变形温度范围内的玻璃,在加热或冷却的过程中,即使加热或冷却的速度不是很大,玻璃的内层和外层也会形成一定的温度梯度,从而产生一定的热应力。
这种热应力,随着温度梯度的存在而存在,随着温度梯度的消失而消失,所以称为暂时应力。
图15-l表明玻璃经受不同的温度变化时,暂时应力的产生和消失过程。
设一块一定厚度、没有应力的玻璃板,从常温加热至该玻璃应变点以下某一温度,经保温使整块玻璃板中不存在温度梯度[图15-l(a)]。
玻璃的退火工艺

玻璃的退火工艺一、玻璃的退火工艺包括哪几个阶段为了清理玻璃中的应力,必须把玻璃加热到低于玻璃转变温度Tg 附近某一温度进行保温均热,以清理玻璃各部分的温度梯度,使应力松弛,这个选定的保温均热温度称玻璃的退火温度.玻璃在退火温度下,由于粘度很大还不会发生可测得的变形.玻璃的退火上限温度是指在此温度下经过 3min 能清理 95 %的应力;退火下限温度是指在此温度下经 3min 只能清理 5 %的应力,上下限退火温度之间为退火温度范围.大部分器皿玻璃的退火上限温度为550 ± 20 ℃ ,平板玻璃为 550 ~ 570 ℃ 、瓶罐玻璃为550 ~ 600 ℃ .实际上,一般采用的退火温度都比退火上限温度低20 ~ 30 ℃ ,低于退火上限温度50 ~ 150 ℃ 的为退火下限温度. 玻璃的退火温度与其化学组成有关.凡能降低玻璃粘度的组成也能降低退火温度,如碱金属氧化物 Na 2 0 、 K 2 O 等. SiO 2 、 Al 2 O 3 、 CaO 等都增加玻璃粘度,所以随着它们含量的增加其退火温度都提高.玻璃的退火制度与制品的种类、形状、大小、容许的应力值、退火炉内温度分布等情况有关.目前采用的退火制度有多种形式.根据退火原理,退火工艺可分为四个阶段:加热阶段、均热阶段、慢冷阶段和快冷阶段.按上述四个阶段可作出温度-时间曲线,此曲线称退火曲线.1 .加热阶段不同品种的玻璃有不同的退火工艺.有的玻璃在成型后直接进入退火炉进行退火,称为一次退火;有的制品在成型冷却后再经加热退火,称为二次退火.所以加热阶段对有些制品并不是必要的.在加热过程中,玻璃表面产生压应力,所以加热速率可相应高些,例如20 ℃ 的平板玻璃可直接进入700 ℃ 的退火炉,其加热速率可高达300 ℃ / rain .考虑到制品大小、形状、炉内温度分布的不均性等因时间素,在生产中一般采用的加热速率为20/a 2 ~ 30/a 2 ( ℃ /min) ,对光学玻璃制品的要求更高.2 .均热阶段把制品加热到退火温度进行保温、均热以清理应力.在本阶段中首先要确定退火温度,其次是保温时间.一般把比退火上限温度低20 ~ 30 ℃ 作为退火温度.退火温度除直接测定外,也可根据玻璃成分计算粘度为10 12 Pa ? s 时的温度.当退火温度确定后,保温时间可按 70a 2 ~ 120a2 进行计算,或者按应力容许值进行计算.3 .慢冷阶段为了使玻璃制品在冷却后不产生应力,或减小到制品所要求的应力范围内,在均热后进行慢冷是必要的,以防止过大的温差.4 .快冷阶段玻璃在应变点以下冷却时,如前述只产生暂时应力,只要它不超过玻璃的较限强度,就可以加快冷却速度以缩短整个退火过程、降低燃料消耗、提高生产率.在生产上,一般都采用较低的冷却速度,这是由于制品或多或少存在某些缺点,以免在缺点与主体玻璃间的界面上产生张应力.对一般技术玻璃采用此值的 15 %~ 20 %,通常还应在生产实践中加以调整.二、退火玻璃的详细制作流程为了避免冷却过快而造成玻璃炸裂,玻璃毛坯定型后立即转入退火用的箱式电阴炉中,在退火温度下保温30min左右,然后按照冷却温度制度降温到一定温度后切断电源停止加热,让其随炉自然缓慢冷却至100℃以下,出炉,在空气中冷却至室温.若玻璃试样退火后经应力检验不合格,须重新退火,以防加工时碎裂.重新退火时首先将样品埋没于装满石英砂的大坩埚中,再把坩埚置于马弗炉内,升温至退火温度保温1h,然后停止加热让电炉缓慢降温(必要时在上、下限退火温度范围内每降温10℃保温一段时间),直至100℃以下取出.相关概念热应力温度改变时,物体由于外在约束以及内部各部分之间的相互约束,使其不能完全自由胀缩而产生的应力。
玻璃的退火过程改善玻璃的抗压性能

玻璃的退火过程改善玻璃的抗压性能玻璃是一种常见的建筑材料和装饰材料,其优良的透明性和质地使其成为许多领域中不可或缺的材料之一。
然而,玻璃的脆弱性常常限制了其在某些应用中的使用。
退火是一种经常被用来改善玻璃抗压性能的工艺,通过在特定的温度范围内加热和冷却玻璃,可以显著提高其抗压性能,使其更加耐用和可靠。
退火是一种热处理工艺,通过加热和冷却材料来改变其内部结构和性能。
在玻璃的制备过程中,由于快速冷却的原因,玻璃中会存在大量的内部压应力。
这些内部压应力会降低玻璃的抗压性能,使其更容易在外力作用下破碎。
因此,需要对玻璃进行退火处理,以消除内部压应力,提高其抗压性能。
退火过程通常包括加热和冷却两个步骤。
在加热过程中,玻璃被加热到退火温度,这个温度通常比玻璃的软化温度略高。
在这个温度下,玻璃的内部结构开始松弛,内部压应力得以释放。
然后,玻璃被冷却到室温,形成新的内部结构,这个结构相对较为稳定,玻璃的抗压性能也得以显著提高。
退火温度是影响退火效果的重要因素之一。
温度过高或者过低都会影响到退火效果。
温度过高可能导致玻璃变得过软,而温度过低则可能无法使内部结构得到充分松弛。
因此,选择合适的退火温度是提高玻璃抗压性能的关键。
此外,退火的时间也是影响退火效果的重要因素之一,时间过长或者过短都可能影响到退火效果的达成。
除了影响玻璃抗压性能的材料本身的因素,退火还受到加热和冷却速率的影响。
加热速率过快或者加热温度过高可能导致玻璃发生热应力,从而影响到退火效果。
同样,冷却速率过快也可能导致内部结构重新产生应力,降低退火效果。
因此,在实际的退火过程中,需要综合考虑加热和冷却速率,以及温度选择等因素,来达到最佳的退火效果。
总的来说,玻璃的退火过程可以显著改善其抗压性能。
通过合理选择退火温度和时间,以及控制加热和冷却速率等因素,可以使玻璃的内部结构得到充分松弛,内部压应力得以释放。
从而提高玻璃的抗压性能,使其更加耐用和可靠。
退火工艺的应用使得玻璃材料在建筑和装饰等领域中能够发挥更大的作用,并且有望在未来得到更广泛的应用。
玻璃的退火工艺制度

玻璃退火在建筑 玻璃中的应用
建筑玻璃作为建筑外墙、 窗户等重要部件,需要经 过退火工艺来提高其强度 和耐久性。通过退火工艺 可以使得建筑玻璃在受到 外力冲击时不易破裂,保 障建筑物的安全性。
玻璃退火在工艺玻璃中的应用
弯曲玻璃
保证形状和性能
夹胶玻璃
增加透光性和强度
智能制造应用
借助智能技术提升 生产效率
绿色生产理念
推动工艺向绿色生 产方向转变
玻璃退火工艺的创新 模式
01 智能化生产
引入智能设备提升生产效率
02 定制化服务
根据客户需求提供个性化定制服务
03
● 06
第六章 总结与展望
玻璃的退火工艺 制度
玻璃退火工艺作为玻璃制 造中重要的工艺环节,通 过释放内部应力、提高玻 璃品质,为玻璃产品的生 产和应用提供了重要支撑。 在未来的发展中,玻璃退 火工艺将继续发挥重要作 用,为玻璃产业的创新和 发展做出更大贡献。
谢谢观看!
玻璃退火的影响因素
温度
影响退火效果的重要因素之一
时间
控制退火过程的持续时间
冷却速率
影响玻璃内部结构的形成
玻璃厚度
决定退火参数的设定
玻璃退火的实践应用
01 工艺优化
不断改进退火工艺,提高玻璃产品质量
02 生产控制
严格控制退火参数,确保产品稳定性
03 技术创新
引入新技术提升退火效率和效果
总结
玻璃的退火工艺制度对玻璃制品质量和性能起着至关重要的 作用。通过合理控制退火参数,可以使玻璃内部应力得到释 放,提高玻璃的强度和耐热性,从而满足不同领域对玻璃产 品的需求。
提升品质
满足高品质需求
个性化处理
浮法玻璃超厚板成形、退火工艺控制

0引言超厚板成形控制的难点主要有玻璃液的堆积能力、厚薄差的控制、板型稳定性的控制;退火控制难点主要有炸板、裂边、在线切裁问题、客户切裁使用投诉。
上述问题严重影响浮法玻璃的实物质量和成品质量,造成浮法玻璃产量和总成品率下降、质量成本上升,不但影响企业利润,而且对企业的声誉构成威胁。
对以上问题进行有效的解决和稳定的控制对超厚板生产显得尤为重要。
本文在阐述厚板成形、退火理论的基础上,结合多年实际生产经验提出对应问题的解决方案。
1超厚板成形控制(1)厚薄差控制主要通过流道温度和高温区水包控制成形温度来调整厚薄差;对拉边机的定位及其他拉边机的间距设置也是决定厚薄差好坏的重要硬件条件;拉边机速度和角度的匹配对调整厚薄差起到了非常重要的辅助作用。
拉引量和净板宽的大小也是影响厚薄差的重要因素,一般情况拉引量越大、成品板宽越宽厚薄差就相对越难控制。
(2)锡槽内板型控制控制拉边机车位偏差,使板型尽量保持居中,压入深度也要保持基本一致,以免因受力不均或者温度场相差太大导致板型偏移。
锡液深度及深池、浅池的匹配,锡槽挡畦的布局、直线电机的使用等可以调整锡液流向,是决定锡槽板型是否稳定的硬件条件。
拉边机参数的匹配、拉引量的波动、光边的大小,对超厚板锡槽内板型的稳定也都有较大的影响,因此需要有较为合理成熟的拉边机参数、保持拉引量的稳定、合理的光边大小。
(3)锡槽内玻璃液的堆积能力锡槽内的玻璃液的堆积能力是影响超厚板生产的重要因素。
影响锡槽内玻璃液堆厚的因素主要包括拉引量的大小、流道成形温度的高低、拉边机的布局和数量、拉边机参数的设置等。
在生产超厚板时一般都会考虑适当降低拉引量来减小成形堆积压力;拉边机使用数量要比常规厚度多,拉边机角度、速度也要比常规厚度生产时大,以此来提高玻璃液在锡槽内的堆积能力。
2超厚板退火控制(1)炸板炸板主要分为横炸和纵炸两大类。
横炸原因:玻璃板边部压应力大。
处理措施:加大敞开区边部风阀,降低敞开区边部温度(或减少敞开区中部风阀开度);纵炸原因:玻璃板过紧。
压延玻璃退火工艺及退火窑的基本组成
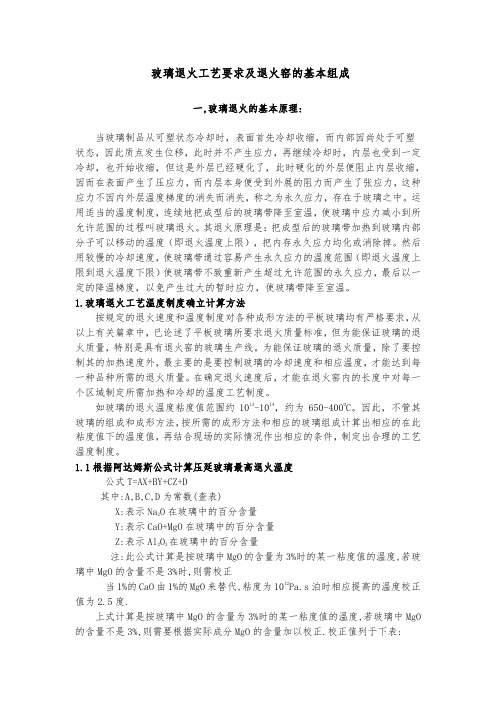
玻璃退火工艺要求及退火窑的基本组成一,玻璃退火的基本原理:当玻璃制品从可塑状态冷却时,表面首先冷却收缩,而内部因尚处于可塑状态,因此质点发生位移,此时并不产生应力,再继续冷却时,内层也受到一定冷却,也开始收缩,但这是外层已经硬化了,此时硬化的外层便阻止内层收缩,因而在表面产生了压应力,而内层本身便受到外展的阻力而产生了张应力,这种应力不因内外层温度梯度的消失而消失,称之为永久应力,存在于玻璃之中。
运用适当的温度制度,连续地把成型后的玻璃带降至室温,使玻璃中应力减小到所允许范围的过程叫玻璃退火。
其退火原理是:把成型后的玻璃带加热到玻璃内部分子可以移动的温度(即退火温度上限),把内存永久应力均化或消除掉。
然后用较慢的冷却速度,使玻璃带通过容易产生永久应力的温度范围(即退火温度上限到退火温度下限)使玻璃带不致重新产生超过允许范围的永久应力,最后以一定的降温梯度,以免产生过大的暂时应力,使玻璃带降至室温。
1.玻璃退火工艺温度制度确立计算方法按规定的退火速度和温度制度对各种成形方法的平板玻璃均有严格要求,从以上有关篇章中,已论述了平板玻璃所要求退火质量标准,但为能保证玻璃的退火质量,特别是具有退火窑的玻璃生产线。
为能保证玻璃的退火质量,除了要控制其的加热速度外,最主要的是要控制玻璃的冷却速度和相应温度,才能达到每一种品种所需的退火质量。
在确定退火速度后,才能在退火窑内的长度中对每一个区域制定所需加热和冷却的温度工艺制度。
如玻璃的退火温度粘度值范围约1013-1014,约为650-4000C。
因此,不管其玻璃的组成和成形方法,按所需的成形方法和相应的玻璃组成计算出相应的在此粘度值下的温度值,再结合现场的实际情况作出相应的条件,制定出合理的工艺温度制度。
1.1根据阿达姆斯公式计算压延玻璃最高退火温度公式T=AX+BY+CZ+D其中:A,B,C,D为常数(查表)X:表示Na2O在玻璃中的百分含量Y:表示CaO+MgO在玻璃中的百分含量Z:表示Al2O3在玻璃中的百分含量注:此公式计算是按玻璃中MgO的含量为3%时的某一粘度值的温度,若玻璃中MgO的含量不是3%时,则需校正当1%的CaO由1%的MgO来替代,粘度为1012Pa.s泊时相应提高的温度校正值为2.5度.上式计算是按玻璃中MgO的含量为3%时的某一粘度值的温度,若玻璃中MgO 的含量不是3%,则需要根据实际成分MgO的含量加以校正.校正值列于下表:根据给定的成分计算与玻璃粘度相应的温度常数玻璃中1% CaO由1%的MgO来代替校正值1.2,常用压延玻璃的工艺参数1.2.1.玻璃化学成分(%)SiO2 Al2O3 CaO MgO Na2O*KaO FeO72.1 1.2 9.3 2.6 14.15 微1.2.2计算:T=AX+BY+CZ+D=(-7.32)×14.15+3.49×(9.3+2.6)+5.37×1.2+603.40=-103.578+41.531+6.444+603.40=547.837=548℃其中 MgO 为2.6 校正数为548℃-2.5×2.6=542℃所以根据计算压延玻璃最高退火温度为548℃2.2退火曲线温度的确定玻璃内应力过多存在主要为玻璃带在退火范围内冷却不当而造成。
影响玻璃切割断面质量的因素及表征性能

0引言随着建筑工程玻璃功能化日益普及并向高端化应用发展,厚板玻璃(厚度大于10 mm的玻璃称为厚板玻璃)的加工与应用需求与日俱增,笔者所在公司2019—2021年厚板玻璃加工产量年均上涨10.8%。
计算机技术的普遍应用使现代切割机配备非常精确的可编程系统,可以精确地进行直线和异形切割,使用优化程序来控制切裁率。
提高掰边质量有效减少留边量与磨边量,是工程玻璃中厚板玻璃加工的行业开发热点,其切割工艺与应用技术是工程玻璃行业的重要技术发展方向之一。
因此,重点关注切割理论与切割工艺革新,提高断面质量与精准度,减少留边量与磨边量,对于进一步提高综合切裁率,具有重大意义。
1玻璃应力学与断裂力学理论(1)钠钙硅玻璃配料组成与玻璃应力钠钙硅浮法玻璃通常含有69%的SiO2,17%的Na2O,6%的CaO 和少量Al2O3/MgO、K2O。
平板工艺通过压延冷却固化后在玻璃原片表面进行机械研磨抛光,相对于浮法工艺其机械性能较低,更容易切割。
各浮法玻璃原片企业均有其不同的工艺配方。
在不同的退火条件下,同一玻璃配方组成的应力属性均不同。
根据Fluegel的理论强度数据模型,以配方为69%的SiO2,17%的Na2O,6%的CaO,4%的Al2O3,3%的MgO,1%的K2O建模玻璃性能,不同玻璃配方组成下,玻璃的杨氏模量均呈现不同变化,如图1所示。
图1 不同玻璃配方组分对玻璃杨氏模量的梯度影响由图1可以看出,此配方的玻璃杨氏模量为68.4 GPa(不考虑瑕疵的理论强度),氧化钙/氧化铝/氧化镁/石英砂配料变化与杨氏模量呈正相关,氧化钾/纯碱配料变化与杨氏模量呈负相关。
其中每摩尔百分比变化下,氧化钙对杨氏模量影响梯度最大,石英砂对杨氏模量影响梯度最小。
当添加更多的氧化钾/氧化钠时,玻璃的应力会下降,氧化钠要比氧化钾下降得更快一些。
由此,本文提出玻璃企业在玻璃切割工艺中应对玻璃原片配方加以考量,将不同原片企业的应力数据作为玻璃切割工艺的第一前提。
- 1、下载文档前请自行甄别文档内容的完整性,平台不提供额外的编辑、内容补充、找答案等附加服务。
- 2、"仅部分预览"的文档,不可在线预览部分如存在完整性等问题,可反馈申请退款(可完整预览的文档不适用该条件!)。
- 3、如文档侵犯您的权益,请联系客服反馈,我们会尽快为您处理(人工客服工作时间:9:00-18:30)。
玻璃退火问题与切割一、厚玻璃退火问题的解决(1 ) 生碴( 糖状物) 产生生碴的根本原因在于表层应力曲线不合理、板芯温度高、残余的板芯张应力过大, 玻璃板在横掰时经常在断面上出现白色的生碴。
在退火曲线上表现为降温速度过快, 调节的方法为降低锡槽出口温度, 使A 区入口温度保持在575~580℃左右, 提高B1 区温度10℃左右、B2 区15~20℃左右、C1 区20~25℃左右、C2 区出口15℃左右, 上述数值是与5mm 玻璃退火温度相比的。
(2 ) 裂口玻璃板在横掰处, 在刀口断面上有小的裂纹延伸到板里约1~10mm 左右。
这种玻璃在冷端斜坡输送辊上稍微受力就会自动炸开, 有的在装箱后运输中炸裂。
这种情况出现的原因, 一种是因为横掰辊子抬得过高引起, 这可以通过调节辊子高度解决; 另一种是因为退火造成的, 又可分为两种情况:①裂口处在退火区温度相对较高, 退火后区裂口处温度偏低, 使此部位张应力太大。
可通过降低退火区裂口对应部位玻璃温度或升高退火后区裂口对应部位玻璃温度解决。
②板上下温差过大, 有的C区板下温度比板上要高60~70℃ , 而F 区离横切较近, F区风管由于板下比板上堵塞严重, 这就造成板下比板上风量小, 这些因素使端面上部受张应力过大, 强行掰断就易产生裂口。
调解上可以将C区板上温度适当上调。
有时裂口与生碴同时出现, 调解上可先按处理生碴的方法调解, 这时裂口有时会同时消失, 若消失不了再按处理裂口方法调解。
(3 ) 中分表现为中分不走刀口, 出现多角或少角。
某厂曾对12mm 玻璃进行过大片离线应力检测, 应力曲线如图5-11 ( a ) 所示。
冷风工艺的应力曲线应为图5-11( b ) 所示。
(注: 应力单位为度, 1 度= 3. 27m μ光程差)由此可以看出, 板中与两肋受永久压应力, 造成中分不走刀口。
这种情况一般可通过提高B 区中部温度或降低C 区中部温度, 增大横向温差, 从而增大中间的张应力加以解决。
(4 ) 掰边表现为掰边时出现多角或少角, 掰不完整。
这种情况主要由自由边薄、散热快、温度低及退火窑边部密封不好使边部压应力过大引起的。
可以通过提高边部张应力加以解决, 解决的方法主要有①通过烧边火提高边部温度。
②在自动掰边机的基础上增加杠杆机械轮、顶轮、压轮等辅助掰边设备。
用拉边机成形的厚玻璃, 板边比齿印内的玻璃薄, 边部散热比板中部多, 因此, 板边比中部温度低。
在退火区, 这种温差的存在, 将使温度均衡后的玻璃边部受压应力,中部受张应力, 切割掰断时, 切口出现多角或少角, 也就是说横切边部不走刀线。
在冷却区, 这种温差的存在, 边部将受张应力, 中部将受压应力, 厚度越厚, 温差越大, 边部极易发生纵炸。
在生产10mm、12mm 厚的玻璃板时, 常出现沿齿痕附近的纵炸条, 损失严重。
二、薄玻璃的退火用拉边机成形的薄玻璃与厚玻璃边部温度情况相反, 边部比齿印内部的温度高, 在退火区这种温差的存在, 将使温度均衡后的玻璃边部受张应力, 中部受压应力, 切割后, 玻璃中分时, 不走刀线, 切口出现多角或少角。
在冷却区, 这种温差的存在, 边部将受压应力, 中部将受张应力, 玻璃越薄温差越大, 此时易发生横向炸裂。
在玻璃厚为3mm 时, 常出现较大的荷叶边, 主要也是这个原因。
薄玻璃生产中, 退火问题处理不好, 同样影响成品率和产量, 为减少薄玻璃的生产损失, 同样需要改善退火质量, 可采取如下一些措施。
(1 ) 同样加强退火窑的保温和密封, 使玻璃板面各处温度不受外界环境影响。
(2 ) 在退火窑各区, 相应降低边部温度的设定值。
同样, 这种降低是有限度的, 否则在冷却区易发生纵炸。
(3 ) 有条件的情况下, 可在敞开的冷却区内另加一套临时风冷措施, 专门冷却较厚的边部, 这种冷却要稳定、可调。
(4 ) 通过成形各参数的调整, 使玻璃的横向厚薄差减少, 同时光边控制到最小限度, 有利于温度的合理分布。
(5 ) 合理控制退火区的冷却速度, 不能超过允许应力值, 否则, 炸裂现象严重, 无法切割。
三、实际退火操作中玻璃炸裂的分析与处理玻璃在退火过程中, 不论厚度方向还是平面方向, 只要有温度梯度存在, 就会使玻璃产生永久内应力或暂时内应力。
当这些应力大于玻璃极限强度时, 玻璃就发生破裂。
尤其是在温度不对称分布和温度差过大时, 会给玻璃退火带来更大的缺陷。
一般有下面几种情况。
1、玻璃边部由于张应力———边子紧而产生的纵向炸裂当玻璃边部张应力值大于玻璃的拉伸强度时, 玻璃总是首先在张应力处炸裂。
一旦玻璃中存在有薄弱区域, 如结石、夹杂物、粘锡等图5-12 玻璃带纵向炸裂时的应力曲线原因, 纵向炸裂就会开始产生。
出现纵向炸裂时的应力分布如图5-12 所示。
生产中发现,纵向裂纹处于应力曲线零点附近( 图中A 点附近) , 再逆玻璃走向延伸。
在大多数情况下, 玻璃纵裂往往发生在退火窑的冷却区( 即C 区) 后部和切割机之间。
发生这种纵裂的情况, 主要是因为玻璃带在退火区域以下板边冷却速度太快的缘故, 必须很好地检查, 仔细地进行调整。
当退火窑在负压下操作时, 辊子两端轴头密封不好, 或侧墙有裂缝, 使大量的冷空气从两边进入窑中, 是发生上述问题的关键。
产生纵向炸裂时, 应仔细地检查每个区的情况, 并关注各种干扰因素, 如气流、玻璃带摆动造成边部忽热忽冷等因素。
必要的话, 以每次1℃左右的调节量逐渐调节控制器的设定值, 等待并确认其结果的有效性。
(1 ) 在退火区内的调整与玻璃带中部相比, 因边部温度太高产生的纵炸, 应减少对玻璃带边部的加热, 或减少对玻璃带中部的冷却。
(2 ) 在退火后区内的调整与玻璃带中部相比, 因边部温度太低产生的纵炸应视不同原因作如下调整:①因边部冷却强度太大、则需减少边部的冷却;②因敞开区处( RET 区与F 区之间或F 区) 的气流太大(有穿堂风) , 则需关闭车间厂房的门, 并且在大风量冷却区周围设置隔离挡帘;③因玻璃带边部距加热元件太远, 则只使用外侧而不使用内侧电加热, 或者加大中部的冷却;④生产厚玻璃时, 因使用反向拉边机造成玻璃带边部较薄的问题, 可在退火窑入口之前的过渡辊台处, 给这些极薄的边部加设辅助烧嘴加热; 如果在保温段出口处玻璃的薄边仍然太冷, 同样可在保温段出口处或在出口处与RET 区之间加设烧嘴加热。
(3 ) 纵炸时的应急处理先在玻璃带裂纹的尾部进行局部保温或加热, 使该处的温度明显的高于周围的温度, 使其周围产生一个较大的暂时压应力, 压住裂纹, 并阻止裂纹继续延伸, 然后再逐步加以调节。
2、玻璃边部由于压应力———边子松而产生的横向炸裂当玻璃带边部一侧或两侧的压应力值太高时, 或玻璃带存在某些弱点时( 如结石、夹杂物、粘锡等) , 会产生横向炸裂。
一侧或两侧边部压应力值太高时出现横向炸裂的应力分布如图5-13 所示。
在压应力高的一侧往往产生Y 形裂纹, 特别是在横掰时尤为明显。
通常横向炸裂是由于波浪形的边部引起的。
在退火区之前产生的波浪形称为波形弯曲;在退火区或退火后区产生的波浪形称为凹凸变形。
(1 ) 波形弯曲锡槽出口处玻璃带温度太高, 进入预退火区因强度不够, 在辊子的间距间造成波形。
这种情况应降低锡槽出口处玻璃带的温度。
因辊子标高不同也可能造成波形, 这时应适当调整辊子的标高。
锡槽边部锡液温度太低, 产生的波形将永久不会消失。
可在锡槽出口端死角位置设置一对线性马达, 使锡液横向温度均匀。
当拉引速度很高时, 玻璃带边部与中间的温差加大, 可在锡槽出口端增加一点电功率。
在预退火区, 如遇阀门卡住、有穿堂风、中部淤积热量太多时, 则应检查阀门, 并通过控制器在玻璃带横向视情况并行加热和冷却。
(2 ) 凹凸变形凹凸变形看起来像波形弯曲一样, 但是其产生的原因却来源于玻璃的应力。
凹凸变形是由于在退火窑中不恰当的冷却造成的。
在退火区, 玻璃带边部过冷, 边部产生很大的压应力。
调整的方法是减少玻璃带边部的冷却量或增加中部的冷却量。
在退火后区, 玻璃带边部过热, 边部产生很大的压应力。
调整的方法是减少玻璃带边部的加热量, 如有可能, 对边部增加冷却量, 或增加中部的加热量。
3、掉边玻璃板掉边是指玻璃板的边部承受压应力而且容易用手指抬起。
有经验的操作工人能够将此情况与边部承受张应力的情况区别开来。
当此压应力超过玻璃极限强度时就发生破裂,此时往往是横向破裂。
玻璃板边部出现掉边的情况, 是由于玻璃在退火区域以下冷却时, 其板边比中部冷得慢, 板中部力图收缩而缩短, 但边部又力图使中部不缩短, 于是板中部产生张应力, 边部产生压应力, 其结果, 到某一定点, 板边脱落, 也就是掉边。
如果板中部的张应力超过玻璃的极限强度时, 玻璃带就会发生横向破裂。
玻璃在退火区域中, 如果板边比板中冷得快, 则在室温中, 板边将会掉边; 而在退火区域以下, 如果边部比中部冷得快, 将会在退火窑中发生掉边。
总之, 发生掉边现象, 是由于玻璃板边部承受高压应力而超过玻璃极限强度的结果。
因此, 如在室温下发生掉边, 说明玻璃在退火区域中, 边部冷得太快, 需要加强轴头密封和边部适当加热, 以消除或减少板边和板中的温度差, 防止掉边和横向破裂的发生。
如果在退火窑中发生掉边和横裂, 则说明玻璃在冷却区中, 边部比中部冷得慢, 需要在边部加强冷却, 以消除或减少板边和中部的温度差。
不过后者在实际生产中很少发生。
4、向上弯曲和向下弯曲玻璃在退火冷却过程中, 由于玻璃板上下表面不对称冷却, 致使玻璃板的上下表面的温度不一致, 造成玻璃板的厚度方向应力分布不对称而引起玻璃板变形, 即向上弯曲或向下弯曲。
为了测量板的弯曲度和向上或向下弯曲, 可将玻璃板沿纵向切成若干块小条, 每块小条宽度为100~125mm, 长度为1. 5~1. 8m。
取一小条玻璃放在测定装置上, 测定装置是由支架和千分表组成, 如图5-14 所示。
先将玻璃条上表面向上测量, 记下千分表上的指示, 然后将小条翻过来, 下表面朝上, 再记下千分表的指示。
两次测定值之差, 就是由于上述原因所造成的偏差值, 即弯曲度的两倍( 向上或向下弯)。
对于一小条玻璃的两次测定[ 图5-15 ( a )、( b) ] 的结果进行比较, 可知板是向上弯曲还是向下弯曲。
如果上表面朝上测定时的弯曲度大, 则为向上弯曲, 以( - ) 表示, 如果下表面朝上测定时的弯曲度大, 则为向下弯曲, 以( + ) 表示。
可以根据在室温下测定的结果, 来调整退火区的温度, 测量结果如图5-15 所示的3 种例子。
(1 ) 全板向下弯曲, 而且板边弯曲度比较小。
这种情况表明, 玻璃在退火区上表面比下表面冷得快, 即上表面比下表面的温度低, 而且板的中部上下表面的温度差比边部上下表面的温度差更大, 如图5-15( a ) 所示。