13 拉式计划体系
精益生产术语
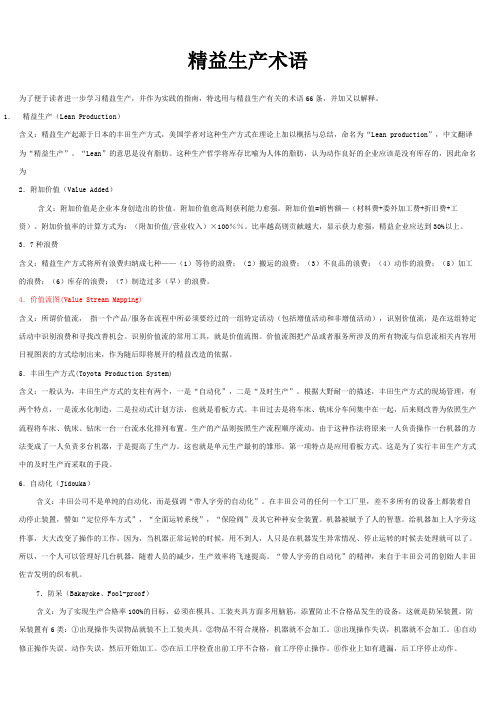
精益生产术语为了便于读者进一步学习精益生产,并作为实践的指南,特选用与精益生产有关的术语66条,并加又以解释。
1.精益生产(Lean Production)含义:精益生产起源于日本的丰田生产方式,美国学者对这种生产方式在理论上加以概括与总结,命名为“Lean production”,中文翻译为“精益生产”。
“Lean”的意思是没有脂肪。
这种生产哲学将库存比喻为人体的脂肪,认为动作良好的企业应该是没有库存的,因此命名为2.附加价值(Value Added)含义:附加价值是企业本身创造出的价值。
附加价值愈高则获利能力愈强。
附加价值=销售额—(材料费+委外加工费+折旧费+工资)。
附加价值率的计算方式为:(附加价值/营业收入)×100%%。
比率越高则贡献越大,显示获力愈强,精益企业应达到30%以上。
3.7种浪费含义:精益生产方式将所有浪费归纳成七种——(1)等待的浪费;(2)搬运的浪费;(3)不良品的浪费;(4)动作的浪费;(5)加工的浪费;(6)库存的浪费;(7)制造过多(早)的浪费。
4.价值流图(Value Stream Mapping)含义:所谓价值流,指一个产品/服务在流程中所必须要经过的一组特定活动(包括增值活动和非增值活动),识别价值流,是在这组特定活动中识别浪费和寻找改善机会。
识别价值流的常用工具,就是价值流图。
价值流图把产品或者服务所涉及的所有物流与信息流相关内容用目视图表的方式绘制出来,作为随后即将展开的精益改造的依据。
5.丰田生产方式(Toyota Production System)含义:一般认为,丰田生产方式的支柱有两个,一是“自动化”,二是“及时生产”。
根据大野耐一的描述,丰田生产方式的现场管理,有两个特点,一是流水化制造,二是拉动式计划方法,也就是看板方式。
丰田过去是将车床、铣床分车间集中在一起,后来则改善为依照生产流程将车床、铣床、钻床一台一台流水化排列布置。
生产的产品则按照生产流程顺序流动。
美国国家导弹防御体系
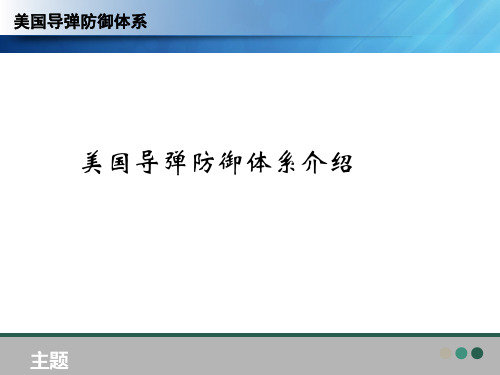
• 及第少二许级氯气的化学激光;这种激光能藉其内燃作用自行
发电,而且其光束在行进远距离后也不会涣散。并用一
• 种第由三“级调整型镜片”组成的系统,这套系统可以装置在
•
飞第机四上级,当机鼻的望远镜看到敌方导弹来袭时,会先发
出一道试探激光“读取”大气层的资料,这道激光碰到
• 目第标五后级反弹回到飞机上,让机上计算机获得应如何将光
发展过程
5
“国家导弹防御系统”的主体是陆基导弹拦截系统。布
什• 总单统由击上于台此国后处家,导编加弹快辑防了母御研系版制统和文违部本反署了样国美家式国导和弹苏防联御于系1统97的2年步签
伐署,的并《将反拟弹议道中导的弹美条国约导》弹(防《御反系导统条扩约展》为)由,陆布基什、政海府基先
和是• 空寻第基求二拦修截改级导这弹一组条成约多,层遭次俄防方御拒体绝系后;于并20谋01求年建12立月一决体定化单 的和方约• 导“面》第弹退国。三防出家御。导级系2弹0统0防2,年御将系6月克统1林”3日顿合,时二布期为什的一政,“府统战正称区式导导退弹弹出防防《御御反系系导统统条” (•MD第- M四is级sile Defense) 。
定向能武器为主、包括攻击卫星和截击导弹的新型反弹道导弹 系统。这项计划后被称作“星球大战计划”。
发展过程
3
后来,随着华沙条约组织瓦解和苏联解体,美国认为俄
罗1•9斯9单3已年击经5无此月法宣处继布编续终与辑止美“母国星版在球军文大事战本上”样进计行式划抗,衡开,始克着林手顿“总弹统道于导 弹• 防第御二”计级划。该计划包括两个部分:用于保护美国海外驻 军(•Th及第e相at三e关r 盟级M国iss免ile遭D导ef弹en威se胁s的ys“tem战区-- T导M弹D防) 和御用系于统保”护美国 本• 土第免四受导级弹袭击的“国家导弹防御系统” (National M“• i国s第s家ile五导D弹级efe防ns御e系sy统st”em的-主- N要M区D别)。在“于战,区前导者弹是防使御一系个统地”区和
jit精益生产准时化物流看板均衡化流程化

11. 推动式生产:(Push Production )是指按照MRP 的计算逻辑,各个部门都是按照公司规定的生产计划进行生产。
上工序无需为下工序负责,生产出产品后按照计划把产品送达后工序即可,这种方式称之为推动式生产。
2. 拉式生产:就是指一切从市场需求出发,根据市场需求来组装产品,借此拉动前面工序的零部件加工3.制造过程时间:加工时间和停滞时间之和,资料显示,一般停滞时间占整个生产时间的80-90%。
3.产生停滞的原因与解决方法:4.准时化生产计划体系:25.目视管理:利用形象直观而又色彩适宜的各种视觉感知信息来组织现场生产活动,达到提高劳动生产率的一种管理手段,也是一种利用视觉来进行管理的科学方法。
6. 生产看板例图:7.领料看板例图:8.看板数量计算:S L D B+=CL D N )1(α+=B 为订货点库存量; 为平均日/小时需求量(单位时间);L 为采购/生产提前期; S为安全库存量;N 为看板的数量; a 为安全系数;C 为盛放物料容器的容量。
L 为工序内生产看板摘下至要求生产的物料送达到存放处所需要的时间,简称为生产过程时间(生产看板循环时间、生产看板周转时间),一般包括看板回收时间、物料加工时间、物料搬运时间和等待时间等。
3S T L D M ++=)(CT T L D N s )(++=M 为基准量; 为平均日需求量;L 为采购提前期;T 为定货间隔期,S 为安全库存量;N 为看板的数量; Ts 为安全库存时间;C 为盛放物料容器的容量。
T 为两次领取之间的时间间隔,也叫做看板周期;Ts 为安全库存时间,相当于零部件在存放处的停留时间。
L+T 也称为领取看板循环时间 。
9.厂外物流:大型企业各专业厂间的运输物流或独立工厂与材料、配件供应厂之间的物流。
10.厂内物流:包括车间之物流、生产线物流和受入物流。
受入物流(生产线物流、配货场物流、集货场物流。
11.三个基本原则:一、生产线物流的基本原则:(1)操作人员安排尽量紧凑,减少走动浪费。
管理学案例:通用电气公司的组织变革

案例:通用电气公司的组织变革1878年10月,世界著名的发明家爱迪生在他的科学实验室的基础上建立了爱迪生电气照明公司。
为适应竞争的需要,1892年4月15日,爱迪生电气照明公司与美国的另一家主要的电力工业公司——汤姆森·休斯顿公司合并,正式命名为通用电气公司(GE)。
一个多世纪来,GE公司得到了迅速的发展。
1892年GE公司只有照明、铁路运输、发电和供应4个产业部门,年销售额1 200万美元。
现在GE公司已拥有包括从飞机发动机到工业自动化,从发电机到新兴工业材料,从家用电器到医疗设备,从银行到全国三大电视广播网之一的NBC等13个产业集团,在近30个国家设有130多家制造厂。
1991年销售额高达602亿美元,1996年公司市场价值排名世界第一。
GE公司以其经营范围广阔,产品服务繁多,资本技术实力雄厚而成为世界超级跨国公司。
一百多年的发展,使西方国家里崛起了一批像GE公司一样庞大的跨国工业组织,如美国的埃克森、通用汽车、福特、杜邦,英国的壳牌、帝国化学,荷兰的飞利浦,法国的雷诺、圣戈班,德国的西门子、大众汽车,意大利的菲亚特,日本的三井和三菱等等。
就是这么一批经济巨人,进入80年代后突然患病,行动迟缓,肌体老化,工作效益急剧下降。
它们渡过了50年代和60年代调整发展的时代,但自70年代开始,飞速前进的车轮慢了下来。
到了80年代,有的大企业已重病在身,步履艰难。
显赫的庞然大物正面临着一场生命的更新和管理上的革命。
GE公司也患上了巨人症,步履蹒跚,困难重重,亏损严重。
公司共有350家大小工厂,40多万员工,经营着几乎无所不包的产品,并且机构重叠,错综复杂。
350家企业中约有1/4正在亏损,1/3的企业正在走下坡路。
这个大家族中,小企业太多,其中混杂了许多薄弱企业,它们不仅影响高效益的经营,也影响管理的精力。
是让这棵百年大树慢慢枯萎?还是给这棵老树注入新的生机? GE公司面临着严重的选择。
当时的公司领导人是瑞吉诺德·琼斯,是一个身体赢弱、声音柔和的理财专家。
OEE与拉速管理
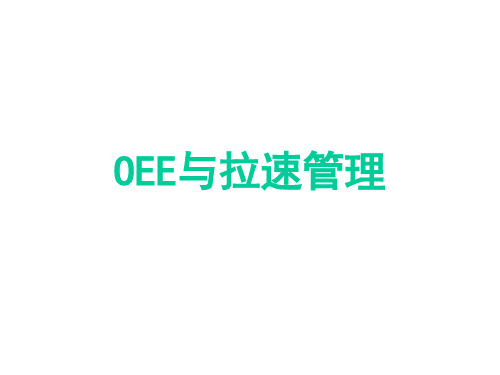
全局设备效率OEE OEE数据收集表
工程分析
一、何谓工程分析
一般的工厂,总是把原材料经过一系列的加工、检查、 搬运、保管的过程,最后转化为成品出售。过程中,若干 相关作业的集合,按照一定的顺序进行,可以产生一定范 围的效果,称之为工程。
例如:电子厂电路板的插件、焊接、检查一般可称为 “基板组装工程”;电冰霜的涂装生产线一般可称为“涂 装工程”。
OEE与拉速管理
如何控制生产线节拍
: 节拍 Cycle time每相鄰兩個產品通過生產線尾端的間隔時間 (平均每生產一個
產品﹐所需的時間隔間)﹒
節拍= 生產時間 =
生產數量
上層客戶要求出貨時間-開始生產時間 客戶要求的出貨計划數量
節拍時間﹑周期時間﹑損失時間 40
周期時間: 26+18+12+13+13+8=90 損失時間: 8+14+13+13+18=66
设某设备某天工作时间为8h, 班前计划停机15min, 故障停机30min,设
备调整25min, 产品的理论加工周期为0.6 min/件, 一天共加工产品450件, 有 20件废品, 求这台设备的OEE。
根据上面可知: 计划运行时间=8x60-15=465 (min) 实际运行时间=465-30-25=410 (min) 有效率=410/465=0.881(88.1%) 生产总量=410(件) 理想速度x实际运行时间=1/0.6 x 410=683-----(410/0.6=683,实际运行的时 间) 表现性=450/683=0.658(65.8%) 质量指数=(450—20)/450=0.955(95.5%)
物流学概论复习自用版
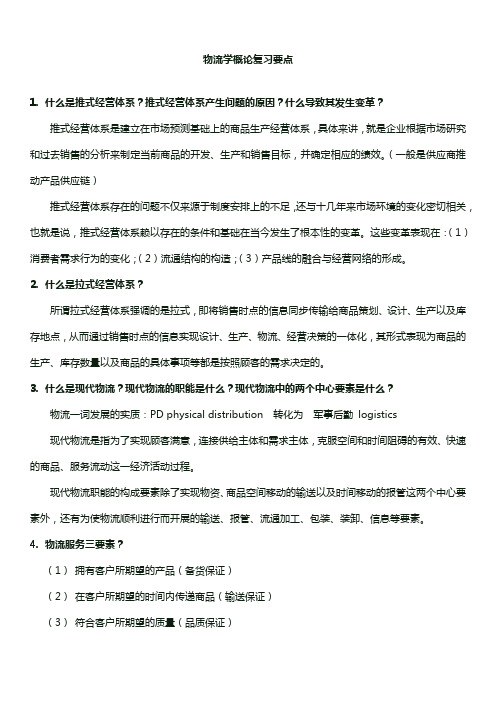
物流学概论复习要点1.什么是推式经营体系?推式经营体系产生问题的原因?什么导致其发生变革?推式经营体系是建立在市场预测基础上的商品生产经营体系,具体来讲,就是企业根据市场研究和过去销售的分析来制定当前商品的开发、生产和销售目标,并确定相应的绩效。
(一般是供应商推动产品供应链)推式经营体系存在的问题不仅来源于制度安排上的不足,还与十几年来市场环境的变化密切相关,也就是说,推式经营体系赖以存在的条件和基础在当今发生了根本性的变革。
这些变革表现在:(1)消费者需求行为的变化;(2)流通结构的构造;(3)产品线的融合与经营网络的形成。
2.什么是拉式经营体系?所谓拉式经营体系强调的是拉式,即将销售时点的信息同步传输给商品策划、设计、生产以及库存地点,从而通过销售时点的信息实现设计、生产、物流、经营决策的一体化,其形式表现为商品的生产、库存数量以及商品的具体事项等都是按照顾客的需求决定的。
3.什么是现代物流?现代物流的职能是什么?现代物流中的两个中心要素是什么?物流一词发展的实质:PD physical distribution 转化为军事后勤logistics现代物流是指为了实现顾客满意,连接供给主体和需求主体,克服空间和时间阻碍的有效、快速的商品、服务流动这一经济活动过程。
现代物流职能的构成要素除了实现物资、商品空间移动的输送以及时间移动的报管这两个中心要素外,还有为使物流顺利进行而开展的输送、报管、流通加工、包装、装卸、信息等要素。
4.物流服务三要素?(1)拥有客户所期望的产品(备货保证)(2)在客户所期望的时间内传递商品(输送保证)(3)符合客户所期望的质量(品质保证)5.对于问题类、金牛类、瘦狗类、明星类产品所应开展的物流服务是哪种?按产品类型开展的物流服务6.供应链和产品的匹配情况(功能型和创新型分别对应什么供应链)费舍尔提出了差异化的供应链物流—产品匹配理论,他根据产品的需求模式将产品分为两类:功能型产品和创新型产品。
精益生产试题与答案

精益生产知识试题库一、填空题1.1960年开始,以丰田为代表的日本汽车制造业通过实施JIT生产模式,以低成本、高质量的突出优势迅速占领美国汽车市场,引发了美日之间长达十年的汽车贸易战。
2. JIT的基本思想是:只在需要的时候、按需要的量、生产所需的产品,故又被称为准时制生产、适时生产方式、看板生产方式。
3. 精益生产的核心理念是:消除一切浪费。
4.精益生产方式的产品特点:多样化,系列化;要求操作技能高;库存水平低;产品质量高;属于买方市场。
5.精益生产追求的7个零的目标:零切换、零库存、零浪费、零不良、零故障、零呆滞、零事故。
6.精益生产的实现必须满足2个条件:零故障、零不良。
7.生产资源管理的4M1I:Man、Material、Machine、Method、Information。
8.获得利润的两大手法:降低成本,提高效率。
9.工厂中的七大浪费:制造过剩的浪费、等待的浪费、搬运的浪费、动作的浪费、库存的浪费、加工过剩的浪费、生产不良的浪费。
10.精益生产的两大支柱:自动化、准时化。
11.准时化生产的定义:在必要的时间按必要的数量生产必要的产品。
12.库存的危害:增加利息负担、占用场地厂房、管理人员增加、出入库的搬运增多、防护工作的浪费、长时间失效的浪费、最大的问题在于掩盖了工厂里的问题。
13. IE面向微观管理,注重三化工业简化、专业化、标准化,是IE重要原则。
14. 改善四原则取消、合并、重排、简化。
15. 作业流程四种工序分别是作业、移动、检查、等待。
16. PDCA循环中PDCA分别表示计划、执行、检查、总结。
17. 标准时间是在正常的操作条件下,以标准的作业方法及合理的劳动强度和速度下完成符合质量工作要求的作业时间。
18. 生产线平衡是对生产的全部工序进行平均化,调整作业负荷,以使各作业时间尽可能相近的技术手段与方法。
19. JIT物料运动的目标是在正确的时间,以正确的方式,按正确的路线,把正确的物料送到正确的地点。
供应链管理期末考试当选多选复习题
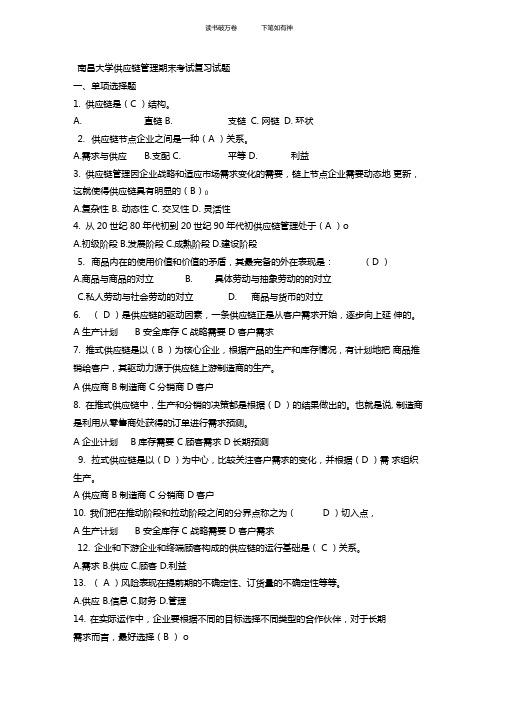
南昌大学供应链管理期末考试复习试题一、单项选择题1.供应链是(C )结构。
A.直链B. 支链C. 网链D. 环状2.供应链节点企业之间是一种(A )关系。
A.需求与供应B.支配C. 平等D. 利益3.供应链管理因企业战略和适应市场需求变化的需要,链上节点企业需要动态地更新,这就使得供应链具有明显的(B)0A.复杂性B. 动态性C. 交叉性D. 灵活性4.从20世纪80年代初到20世纪90年代初供应链管理处于(A )oA.初级阶段B.发展阶段C.成熟阶段D.建设阶段5.商品内在的使用价值和价值的矛盾,其最完备的外在表现是:(D )A.商品与商品的对立B. 具体劳动与抽象劳动的的对立C.私人劳动与社会劳动的对立D. 商品与货币的对立6.( D )是供应链的驱动因素,一条供应链正是从客户需求开始,逐步向上延伸的。
A生产计划 B 安全库存 C战略需要 D 客户需求7.推式供应链是以(B )为核心企业,根据产品的生产和库存情况,有计划地把商品推销给客户,其驱动力源于供应链上游制造商的生产。
A供应商 B制造商 C分销商 D客户8.在推式供应链中,生产和分销的决策都是根据(D )的结果做出的。
也就是说, 制造商是利用从零售商处获得的订单进行需求预测。
A企业计划B库存需要 C顾客需求 D长期预测9.拉式供应链是以(D )为中心,比较关注客户需求的变化,并根据(D )需求组织生产。
A供应商 B制造商 C 分销商 D客户10.我们把在推动阶段和拉动阶段之间的分界点称之为( D )切入点,A生产计划 B 安全库存 C 战略需要 D 客户需求12.企业和下游企业和终端顾客构成的供应链的运行基础是( C )关系。
A.需求B.供应C.顾客D.利益13.( A )风险表现在提前期的不确定性、订货量的不确定性等等。
A.供应B.信息C.财务D.管理14.在实际运作中,企业要根据不同的目标选择不同类型的合作伙伴,对于长期需求而言,最好选择(B ) oA.有影响力的合作伙伴B.战略性合作伙伴C.竞争性的合作伙伴和技术性的合作伙伴D.普通合作伙伴15.企业在众多供应商中,选出几个供应条件对自己较为有利的合作伙伴,同他们分别进行协商,再确定适当的合作伙伴,这种方法是( B )。
- 1、下载文档前请自行甄别文档内容的完整性,平台不提供额外的编辑、内容补充、找答案等附加服务。
- 2、"仅部分预览"的文档,不可在线预览部分如存在完整性等问题,可反馈申请退款(可完整预览的文档不适用该条件!)。
- 3、如文档侵犯您的权益,请联系客服反馈,我们会尽快为您处理(人工客服工作时间:9:00-18:30)。
XJTU-IE, 2007.9-2008.9, M: xuchen.xuchen@(徐琛), lucifer_tcl@(李慰祖)第三篇 实践的原则In matters of style, swim with the current;In maters of principle, stand like a rock.——托马斯·杰斐逊第十三章 拉式计划体系We think in generalities, we live in detail.——AN怀特海13.1 引言回忆起我们在本书的开始指出运营教育的三大基本要素是基础知识(Basics)1.直觉(Intuition)2.3.综合(Synthesis)第一篇和第二篇中,我们几乎全部在讨论前两项。
例如,第一篇中引进的工具和术语(如,EOQ、(Q,r)、BOM、MPS)与第二篇中变动性的量度(如,变异系数)和基本的排队概念都是对于制造经理极为重要的基础知识。
传统库存模型提供的洞察力,MRP,在第一篇中观察的JIT,产出、WIP与周期时间的工厂物理学关系以及在第二篇中开发的变动性原理都是制定良好运营决策所需要的强有力直觉的重要组成部分。
然而,除了运营与第十一章的行为科学的比较,以及第十二章的质量的广泛方面有一些综合之外,我们几乎没有涉及过第三项,综合(synthesis)。
现在我们要通过建立一个将第一篇和第二篇中发展的原则应用到实际制造问题的框架来填补这个重要的空白。
我们的方法建立在两个前提之上:组织不同层级处的问题需要不同水平的细节、建模建设和计划频率。
1.不同层级之间的计划和分析工具必须一致。
2.第一个前提促使我们针对具体的问题使用不同的工具。
不幸的是,在体系内使用不同的工具和程序容易与第二个前提冲突。
由于这种潜在的不一致性,常常可以看到工业中的某些计划工具被扩展应用到了它们不适合的场所。
例如,我们曾工作过的一家工厂使用的排配工具计算各台机器处细节的、一分钟一分钟的(minute-by-minute)产量来产生两年的集结生产计划。
这个工具对于短期计划(如,一条或一周)可能还是合适的,但用于长期计划就太麻烦了(输入数据和调试就用了一周时间!)。
此外,向前几周之后它就非常不精确了,以致千辛万苦得到的排配实际上根本没有在车间内实施。
(408|409)为了开发既适合于具体应用又在应用中彼此一致的方法,我们介绍以下的计划体系开发步骤:适当地将划分系统(Divide the overall system appropriately)。
针对流程的不同部分、 1.不同的产品类别、不同的计划展望期、不同的转产(shift)等等,可以使用不同的计划方法。
关键是寻找一套区划(divisions),使得每一部分可以管理,而各个部分又能够整合。
确定各区划之间的联系(Identify links between the divisions)。
例如,如果共享同一 2.加工中心的两种产品分别制定生产计划,它们应当通过共享的加工中心的产能联系起来。
如果使用不同的工具计划不同展望期的生产需求,就应当确保各个计划与其对产能、产品组合、人力等等的假定相调和。
使用反馈来加强协调(Use feedback to enforce consistency)。
所有的分析、计划和控 3.制工具都使用估计的参数(如,产能、机器速率、产出、失效与修复速率、需求速率以及其他许多的)。
当系统运行时,我们应当持续更新对这些数值的知识。
应当明确地使用已更新的知识来促使系统使用实时的、一致的信息,而不是以非正式、不匹配的方式来估计各种工具的输入。
在本章余下的部分,我们来预览一个与这些原则以及先前给出的工厂物理学原则一致的计划体系。
我们并不认为它是与这些原则一致的唯一体系。
相反地,我们将它看作是途径之一,并致力于从充分宽广的视野提出各个层级的议题从而为各种具体制造环境的定制留下余地。
第三篇中的余下章节将会更加详细地讨论这个体系的主要组块。
13.2 拆分(Disaggregation)建立计划结构的第一步是将各种决策问题分解成可管理的子问题。
如我们将要讨论的,这一点可以通过建立规范计划层级来明确地实现。
它也可以通过使用不同的模型和假定逐个地解决各种决策问题来模糊地实现。
不管远见的水平如何,某种形式的拆分都是必须的,因为现实世界所有的生产系统都太复杂而不能用单一模型来解决。
(409|410)13.2.1 生产计划的时间尺度制造系统的典型拆分沿用的重要维度之一就是时间。
其首要原因是,制造决策因其各自结果的持续时间而大为不同。
例如,新厂的建设可能在几年或几十年内对企业的位置有影响,而在某一工站处选用某一部件来加工的影响在几小时或几分钟内就消失了。
这使得在决策制定过程中使用不同的计划展望期(planning horizon)尤为重要。
因为建设新厂的决策将在数年的时间内影响运营,所以我们必须向前数年预测这些影响从而得出合理的决策。
故而,这个问题的计划展望期应该很长。
显然地,我们不必为评估在工站处加工什么而向前想得如此长远,故而它的计划展望期较短。
计划展望期的合适长度也因产业和组织的层级而不同。
某些产业,如石油和长途电话,往往使用长达数十年的计划展望期,因为它们业务决策的后果将会持续那么长的时间。
对于给定的公司,较长时间的展望期一般用在负责长期业务计划的企业办公室里,而不是用在制定每日任务的工厂里。
在本书中,我们主要关注与经营工厂相关的决策,并在这种情境下将计划展望期划分为长期(long)、中期(intermediate)和短期(short)。
在工厂层级,长期的计划展望期可能是从一年到五年,以两年为典型。
中期的计划展望期可能是从一周到一年,一以月为典型。
短期的计划展望期可能是从一小时到一周,以一天为典型。
(410|411)表13.1列举了制定于长期、中期与短期的计划展望期的制造决策。
注意到在一般情况下,长期决策通过考虑生产什么、如何生产、如何融资、如何销售、在哪生产、从哪获取物料以及运营这个系统的一般原则等等问题指出战略(strategy)。
中期决策通过决定加工什么、谁来加工、设备维护采取什么措施、什么产品由销售推动等等问题指出战术(tactics)。
这些战术决策必须在战略性的长期决策设立的物理或逻辑约束内制定。
最后,短期决策通过移动物料与工人、调整制程和设备以及采取为使系统持续朝向目标运行而需要的任何措施指出控制(control)。
长期战略和中期战术决策建立了控制决策制定时必须遵守的约束。
表13.1 战略、战术和控制决策不同的计划展望期意味着不同的更新频率(regeneration frequency)。
基于未来数年的信息的长期决策不需要经常重新审议,因为对如此之久的未来将发生的事的估计不会很快改变。
例如,工厂重新评价它该生产什么产品是件好事,却不是每周都该做的事。
一般地,长期问题一季度至一年评议一次,非常长期的议题(如,我们应当位于何种业务领域?)则更不频繁地提起。
中期问题通常一周至一月评议一次。
短期问题实时或一天评议一次。
当然了,这些仅仅是典型的数值,它们在不同的企业和决策问题中变化很大。
除了更新频率不同之外,有着不同计划展望期的问题在细节的水平(level of detail)上也不同。
一般地,计划展望期越短,建模和数据收集所需的细节就越多。
例如,如果制定关于即将建立的工厂的规模的长期战略性产能决策,我们不需要对部件要经过的工艺路线知道太多。
对各部件在各制程处所需的时间有个粗略估计就足够用来估计产能需求了。
最后,在短期的控制层级,我们需要清楚地知道部件的工艺路线,包括某一部件是否需要重工和特殊的关注,从而引导部件通过系统。
与这种战略/战术/控制的区分很相似的例子是绘图法(mapmaking)。
长期问题就像长途旅行。
我们需要覆盖很远距离却不很详细的地图。
显示了主要的公路,可能就足以满足需求。
类似地,长期决策问题需要覆盖很长的时间(即,长的计划展望期)却不很详细的工具。
与之相反,短期问题就像短途旅行。
我们需要没有显示太远距离却详细展示其内容的地图。
显示城市的街道甚至是单个建筑的地图,可能才合适。
类似地,对于短期决策,我们需要没有覆盖很长时间(即,短的计划展望期)却对其内容给出许多细节的工具。
13.2.2 拆分的其他维度除了时间,生产计划与控制问题一般还有其他几种拆分的维度。
由于现代工厂很大很复杂,常常不可能在做出具体决策时将其视为一个整体。
以下的三种维度可以用于将工厂分解成较易于分析和管理的组块:(411|412)制程(Process)。
传统上,许多工厂按物理制造过程组织。
铸造、研磨、钻孔和热处 1.理等等业在位于不同地点、接受不同管理的独立部门执行。
在JIT运动的尾流中这种制程式组织没有以前流行了;但是通过它的流动导向(flow-oriented)的单元布置,制程的区分仍然存在。
例如,钢铁厂内铸造与轧制在操作上区别很大,并且有时物理布置离得很远。
半导体制造业也有类似的例子。
(Likewise,mass lamination of copper and fiberglass cores in large process is distinct- physically, operationally, and logistically- from the circuitizing process in which circuitry is etched into the copper in a photo-optical/chemical flow line process.)在此类情形下,常常为不同的制程安排各自的经理。
使用不同的计划、排配和控制工具也是合理的。
产品(Product)。
尽管存在着专注于单一产品的工厂(如,一家聚苯乙烯工厂),现 2.在的大多数工厂生产多种产品。
确实,通过种类与定制来竞争的压力很可能已经提高了一般工厂产品种类的平均数量。
例如,有20,000种不同料号(即,合计制成品和子组件)的工厂并不罕见。
由于在这种情况下单独考虑每种料号非常困难,许多制造工厂就将料号集结归入大类,以实现计划和管理的目的。
一种集结的形式是将相同工艺路线的部件结合起来。
一般来说,工艺路线比料号少得多。
例如,在一个生产几千种不同电路板的印制电路板工厂,可能只有两种基本工艺路线(basic routings)(如,小型板线和大型板线)。
然而常常也会这样,如果考虑工艺的微小变更(如,额外的测试步骤、个别作业外包(vendoring of individual operations)、接触面镀金),实际的工艺路线数目可能比基本路线多出许多。
对于计划,一般可取的是通过忽略微小变更来保持“官方”工艺路线最少。