塑料制品黑点,晶点分析报告
注塑件黑点释疑
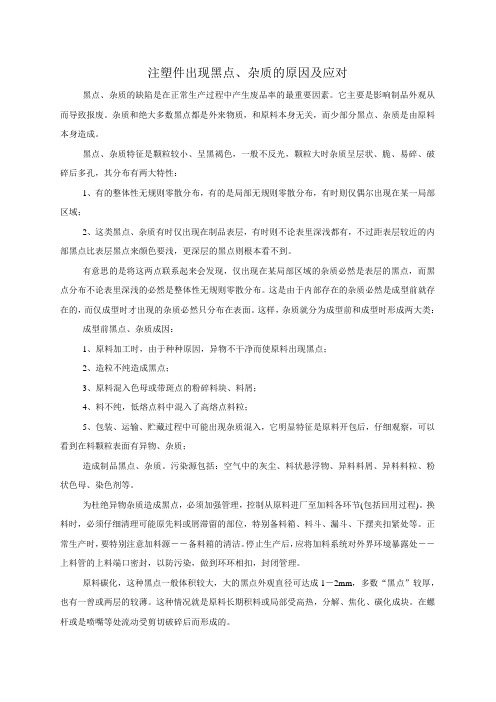
注塑件出现黑点、杂质的原因及应对黑点、杂质的缺陷是在正常生产过程中产生废品率的最重要因素。
它主要是影响制品外观从而导致报废。
杂质和绝大多数黑点都是外来物质,和原料本身无关,而少部分黑点、杂质是由原料本身造成。
黑点、杂质特征是颗粒较小、呈黑褐色,一般不反光,颗粒大时杂质呈层状、脆、易碎、破碎后多孔,其分布有两大特性:1、有的整体性无规则零散分布,有的是局部无规则零散分布,有时则仅偶尔出现在某一局部区域;2、这类黑点、杂质有时仅出现在制品表层,有时则不论表里深浅都有,不过距表层较近的内部黑点比表层黑点来颜色要浅,更深层的黑点则根本看不到。
有意思的是将这两点联系起来会发现,仅出现在某局部区域的杂质必然是表层的黑点,而黑点分布不论表里深浅的必然是整体性无规则零散分布。
这是由于内部存在的杂质必然是成型前就存在的,而仅成型时才出现的杂质必然只分布在表面。
这样,杂质就分为成型前和成型时形成两大类:成型前黑点、杂质成因:1、原料加工时,由于种种原因,异物不干净而使原料出现黑点;2、造粒不纯造成黑点;3、原料混入色母或带斑点的粉碎料块、料屑;4、料不纯,低熔点料中混入了高熔点料粒;5、包装、运输、贮藏过程中可能出现杂质混入,它明显特征是原料开包后,仔细观察,可以看到在料颗粒表面有异物、杂质;造成制品黑点、杂质。
污染源包括:空气中的灰尘、料状悬浮物、异料料屑、异料料粒、粉状色母、染色剂等。
为杜绝异物杂质造成黑点,必须加强管理,控制从原料进厂至加料各环节(包括回用过程)。
换料时,必须仔细清理可能原先料或屑滞留的部位,特别备料箱、料斗、漏斗、下摆夹扣紧处等。
正常生产时,要特别注意加料源――备料箱的清洁。
停止生产后,应将加料系统对外界环境暴露处――上料管的上料端口密封,以防污染,做到环环相扣,封闭管理。
原料碳化,这种黑点一般体积较大,大的黑点外观直径可达成1―2mm,多数“黑点”较厚,也有一曾或两层的较薄。
这种情况就是原料长期积料或局部受高热,分解、焦化、碳化成块。
共混改性塑料黑点超标原因分析报告
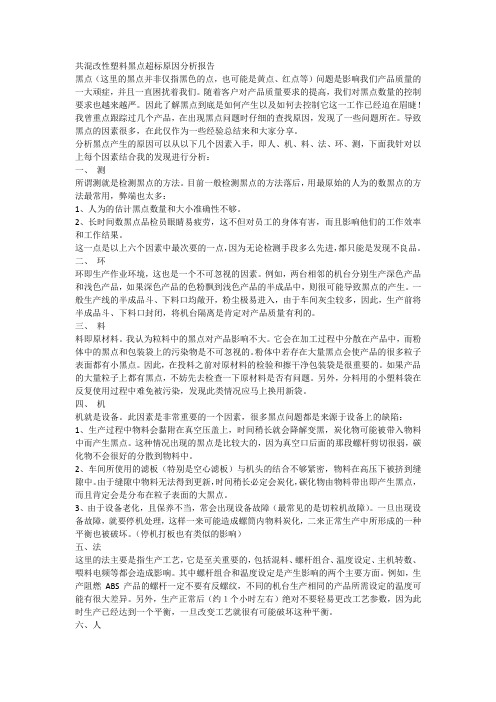
共混改性塑料黑点超标原因分析报告黑点(这里的黑点并非仅指黑色的点,也可能是黄点、红点等)问题是影响我们产品质量的一大顽症,并且一直困扰着我们。
随着客户对产品质量要求的提高,我们对黑点数量的控制要求也越来越严。
因此了解黑点到底是如何产生以及如何去控制它这一工作已经迫在眉睫!我曾重点跟踪过几个产品,在出现黑点问题时仔细的查找原因,发现了一些问题所在。
导致黑点的因素很多,在此仅作为一些经验总结来和大家分享。
分析黑点产生的原因可以从以下几个因素入手,即人、机、料、法、环、测,下面我针对以上每个因素结合我的发现进行分析:一、测所谓测就是检测黑点的方法。
目前一般检测黑点的方法落后,用最原始的人为的数黑点的方法最常用,弊端也太多:1、人为的估计黑点数量和大小准确性不够。
2、长时间数黑点品检员眼睛易疲劳,这不但对员工的身体有害,而且影响他们的工作效率和工作结果。
这一点是以上六个因素中最次要的一点,因为无论检测手段多么先进,都只能是发现不良品。
二、环环即生产作业环境,这也是一个不可忽视的因素。
例如,两台相邻的机台分别生产深色产品和浅色产品,如果深色产品的色粉飘到浅色产品的半成品中,则很可能导致黑点的产生。
一般生产线的半成品斗、下料口均敞开,粉尘极易进入,由于车间灰尘较多,因此,生产前将半成品斗、下料口封闭,将机台隔离是肯定对产品质量有利的。
三、料料即原材料。
我认为粒料中的黑点对产品影响不大。
它会在加工过程中分散在产品中,而粉体中的黑点和包装袋上的污染物是不可忽视的。
粉体中若存在大量黑点会使产品的很多粒子表面都有小黑点。
因此,在投料之前对原材料的检验和擦干净包装袋是很重要的。
如果产品的大量粒子上都有黑点,不妨先去检查一下原材料是否有问题。
另外,分料用的小塑料袋在反复使用过程中难免被污染,发现此类情况应马上换用新袋。
四、机机就是设备。
此因素是非常重要的一个因素,很多黑点问题都是来源于设备上的缺陷:1、生产过程中物料会黏附在真空压盖上,时间稍长就会降解变黑,炭化物可能被带入物料中而产生黑点。
注塑成型杂质黑点.ppt
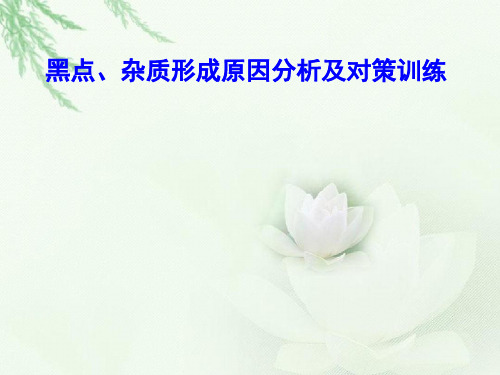
1)对于成型中黑点,成型中黑点必定先附于型腔表 面,然后被熔料裹挟固定于制品表面,所以这种黑 点去除办法及有让它不会在型腔中。对确定材质不 良的模具,还要先确定原因、确定位置。所有有相 对移动的型腔,模芯包括滑块、中子、顶针/块,都 有可能烧伤,确定烧伤后,要修复破损部位,另外 要减小滑动部位的摩擦,加润滑油。另外,要减小 滑动部位相对运动速度,如顶进/退,开合模,滑块 移动时尽量要慢,滑块与模板间生锈和其它污渍, 要卸下滑块,将锈和其它污渍清除干净,将水咀扎 紧。对于油或水溅到模腔光滑成型面,造成黑点应 该经常擦拭易出油、水处,杜绝其在成型面上的出 现。
1)对空熔胶清洗螺杆(熔胶后空射)根据
需要可以加入一些专用螺杆清洗剂,效果会 更好。
2)、拆卸螺杆,对螺杆、料筒、三件套进 行彻底清洗。
Quesiton? Welcome!
3、料筒间隙过大,螺筒与螺杆的 间隙太大,会使料在料筒中滞留,
而滞留的料经过长期过热分解, 产生黑点。
8 、助剂降、分解变色,助剂包括防静电剂, 紫/红外线吸收剂和一般的染色剂,其性质 一般都在比原料活泼,在加工温度剪切力作 用下,原料未分解时,它们已经分解,变成 暗色、黄褐色以至黑色,成型时形成黑点、 杂质。
“黑点”较厚,也有一曾或两层的较薄。这 种情况就是原料长期积料或局部受高热,分 解、焦化、碳化成块。在螺杆或是喷嘴等处
流动受剪切破碎后而形成的。
原料碳化原因有:
1、 熔体温度太高,料温太高会造成过热分 解,形成碳化物,尤其是对一些热敏性材料 温度范围窄,必须控制料筒味部温度不能过 高。2 、积料焦化:如果熔融塑料滞留某处 时间过长,会出现焦化积料,引起黑点,可 能引起料滞留的区域,有射头与螺筒的连接 处,螺筒壁、熔胶环,射嘴与浇口的接触部 位,热流道拐弯处,主流道的死角等部位。
塑胶制品常见不良现象及分析
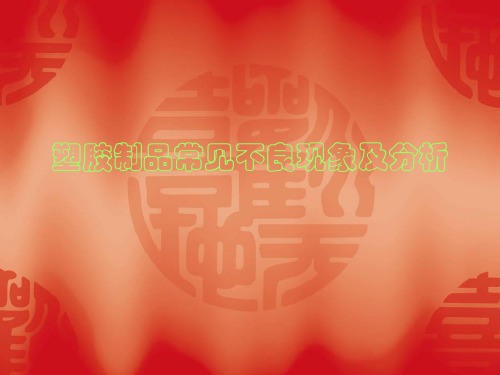
背压太低
树脂温度太高 螺杆速度太高 射出压力太高 射出速度太高
水分太高 颗粒中的孔隙 回料比例太高
银纹
树脂烘干不充分 烘干机功率不够 管道缺陷等
成型机
成型工艺
辅助设备
改进方法
材料
▪增加塑料熔体的流动性
模具设计
▪改变浇口的位置 ▪增设排气槽
工艺条件
▪增加注塑压力和保压压力 ▪增加熔体温度 ▪降低脱模剂的使用量
塑胶制品常见不良现象及分析
注塑过程中的常见问题
流痕 欠注 银纹/水花 缩痕 熔接痕
气眼 黑点或黑纹 发脆 烧焦/焦痕 飞边/毛边 分层起皮
成型问题-气眼
气眼是指空气被困在型腔内而使制件产生气泡的现象. 它是由于两股熔体前锋交汇时气体无法从分型面、顶杆或排气孔中排出造成的。 气眼通常位于熔体最后填充的地方。 缺少排气口或排气口尺寸不足将导致在最后填充部位产生气眼或其他表面缺陷. 如果制件设计薄厚不均,也非常容易造成气眼现象。
浇口设计不合适,通道 小,位置和形状不适当
模具表面残留 脱膜剂或水分
收缩率太大
流道设计不合适(尺 寸小,形状不适当)
内浇道设计不合适 (通道小,梯度小)
喷嘴温度大低
模具温度控 制线路故障
排气不充分
树脂温度太高 射出保压太低
粘度太高
再生料比例 太高
气泡
模具温度太低 背压太低
射出速度不合适 (混有气体)
案例 (分层起皮)
改进方法
材料
▪避免不相容的杂质或受污染的回收料混入原料中
模具设计
▪对所有存在尖锐角度的流道或浇口进行倒角处理,实现平滑过度.
工艺条件
▪增加料筒和模具温度 ▪成型前对材料进行恰当的干燥处理. ▪避免使用过多的脱模剂
注塑生产黑点问题
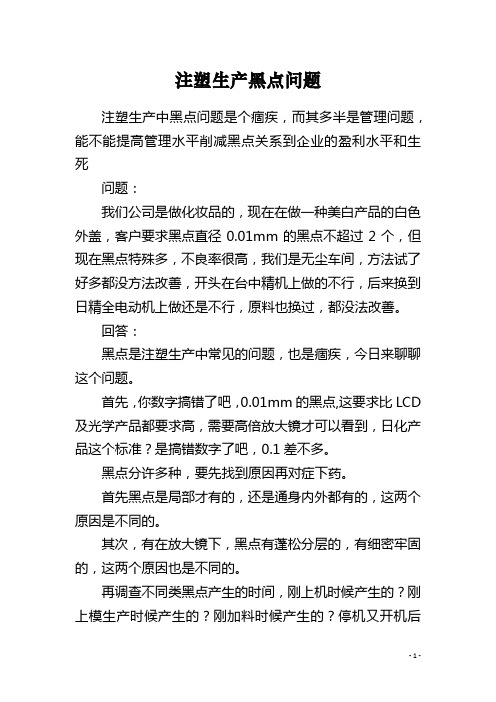
注塑生产黑点问题注塑生产中黑点问题是个痼疾,而其多半是管理问题,能不能提高管理水平削减黑点关系到企业的盈利水平和生死问题:我们公司是做化妆品的,现在在做一种美白产品的白色外盖,客户要求黑点直径0.01mm的黑点不超过2个,但现在黑点特殊多,不良率很高,我们是无尘车间,方法试了好多都没方法改善,开头在台中精机上做的不行,后来换到日精全电动机上做还是不行,原料也换过,都没法改善。
回答:黑点是注塑生产中常见的问题,也是痼疾,今日来聊聊这个问题。
首先,你数字搞错了吧,0.01mm的黑点,这要求比LCD 及光学产品都要求高,需要高倍放大镜才可以看到,日化产品这个标准?是搞错数字了吧,0.1差不多。
黑点分许多种,要先找到原因再对症下药。
首先黑点是局部才有的,还是通身内外都有的,这两个原因是不同的。
其次,有在放大镜下,黑点有蓬松分层的,有细密牢固的,这两个原因也是不同的。
再调查不同类黑点产生的时间,刚上机时候产生的?刚上模生产时候产生的?刚加料时候产生的?停机又开机后产生的?。
原因也是不同。
最终你说你的车间是无尘室,那实际颗粒等级测了没有?能不能达到1万等级?详细管控细节就多了:1.顶针油润滑油是无挥发的吗?2.修理工具上有没有挥发性油品?3.人和其他进入车间的物品的除尘执行的怎么样?4.空气湿度管控如何?5.进料是独立密闭通道吗?经过2次吹尘处理?6.循环风的过滤执行的如何?7.车间是正压?压力差在标准范围内?8.螺杆清洗过程规范吗?……黑点问题原因复杂,所以要先确定原因再对症下药。
说不定最终一查是规范执行的原因。
特殊是假如黑点许多的话,多半是车间管控的问题,先把该做的做好,等问题较少了,最终原因就很简单水落石出了。
后记:1.注塑生产制造过程中的问题多半原因不止一种,假如戴着有色眼镜仅仅从一个方面进行论证那一定会失之偏颇,所以独立的第三方的专业的分析很重要,这是技术咨询公司存在的意义。
2.影响注塑量产生产效率的原因中,黑点是最主要的原因(没有之一),不得不重视。
塑胶产品缺陷的粗劣分析

塑胶产品缺陷的粗劣分析1.表面起膜树脂的添加剂流经产品表面时,形成的白色、灰色的蔓延现象被称为表面起膜。
产生的主要原因:1、树脂内部的添加剂是主要原因1、造成过度应力的注塑条件等也是引发原因2.飞边产生的主要原因1、注塑机加工不良2、注塑机容量不足3、加工条件不良4、锁模力不足5、模具贴得不紧6、模具的变形7、树脂流动太好8、Gas Vent过大9、注塑压力较大10、模具面上存在异物3.透明性底下PPS、SAN等透明产品出现的透明性低下的现象产生的主要原因1、脱模剂使用过多2、混入其它树脂3、混入其它型号4、模具的加工状态,模具温度等加工条件不合适。
4.异色、褪色产品的颜色与标准颜色不同的现象。
树脂颜色不同为异色;注塑后颜色发生改变的现象为变色。
产生的主要原因1、着色错误2、树脂污染3、过多使用粉碎品4、注塑机污染5、树脂的热化等5.表面突起产生的主要原因1、原料内混入异物2、颜料未分散3、模具加工状态4、使用再利用原6.未填满树脂没有填满Cavity的全部,冷却凝固后成型品的一部分出现不足的现象。
进料调节不当A缺料B多料注射压力不妥料量过低模具温度低或温度分布不合理塑料流动性高喷嘴配合不良塑料熔块堵塞加料通道喷嘴冷料入模模具设计不合理模具浇注系统有缺陷7.流痕树脂没有填满Cavity的全部,冷却凝固后成型品的一部分出现不足的现象。
进料调节不当A缺料B多料注射压力不妥料量过低模具温度低或温度分布不合理塑料流动性高喷嘴配合不良塑料熔块堵塞加料通道喷嘴冷料入模模具设计不合理模具浇注系统有缺陷8.黑线产品表面形成黑色线条的现象挥发物润滑剂或脱膜剂树脂的热化黑色颜料注塑要清洁不良模具表面受到污染(油、油脂等异物)排气不良成型机的老化及损伤过多使用再利用原料9.成型收缩成型品的尺寸产生影响的因素多种多样,其主要变数有模具、产品形状、成型条件及后工程、树脂的种类等。
(a)随模具的设计及成型品的形状而产生的差异。
膜内注塑黑点分析报告
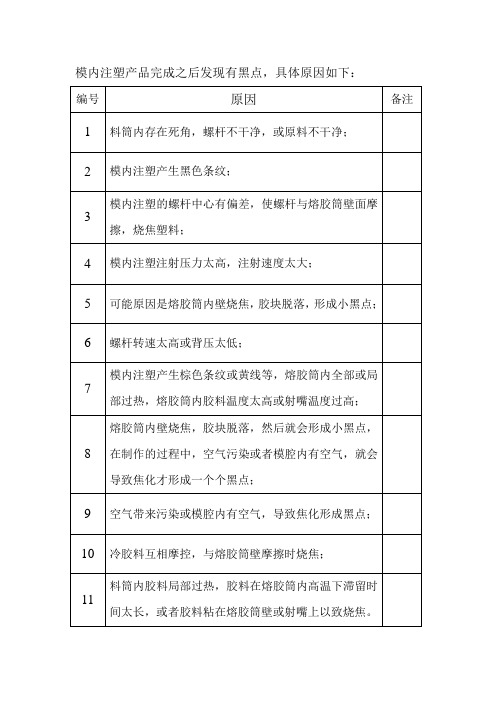
编号
原因
备注
1
料筒内存在死角,螺杆不干净,或原料不干净;
2
模内注塑产生黑色条纹;
3
模内注塑的螺杆中心有偏差,使螺杆与熔胶筒壁面摩擦,烧焦塑料;
4
模内注塑注射压力太高,注射速度太大;
5
可能原因是熔胶筒内壁烧焦,胶块脱落,形成小黑点;
6
螺杆转速太高或背压太低;
11
料筒内胶料局部过热,胶料在熔胶筒内高温下滞留时间太长,或者产生棕色条纹或黄线等,熔胶筒内全部或局部过热,熔胶筒内胶料温度太高或射嘴温度过高;
8
熔胶筒内壁烧焦,胶块脱落,然后就会形成小黑点,在制作的过程中,空气污染或者模腔内有空气,就会导致焦化才形成一个个黑点;
9
空气带来污染或模腔内有空气,导致焦化形成黑点;
10
冷胶料互相摩控,与熔胶筒壁摩擦时烧焦;
塑胶件黑点检验准则要求

塑胶件黑点检验准则要求塑胶件黑点检验是对塑胶制品进行质量检验的重要环节之一、黑点指的是塑胶制品表面或内部出现的黑色污点,这些污点可能是塑胶材料本身的不纯物质或者是制造过程中污染物的残留。
黑点不仅影响产品的外观质量,还可能对产品的物理性能和使用寿命造成不良影响。
因此,制定塑胶件黑点检验准则是确保产品质量的重要措施。
一、塑胶件黑点检验方法1.目视检查法:对于外观要求较高的产品,可以进行目视检查来判断是否存在黑点。
检验员应将产品放在明亮的环境下进行观察,注意黑点的数量、分布和大小,以及是否与产品表面或内部有关。
2.放大镜检查法:对于外观要求较高但黑点较小且分布不均匀的产品,可以使用放大镜进行检查。
检验员应将产品放在光线充足的地方,用放大镜观察黑点的数量、分布和大小,以及是否与产品表面或内部有关。
3.摄影检查法:对于黑点数量多、分布范围广的产品,可以使用摄影检查法。
检验员应使用高分辨率的相机对产品进行拍摄,然后将照片放大观察黑点的数量、分布和大小,以及是否与产品表面或内部有关。
4.X射线检查法:对于黑点分布在产品内部的情况,可以使用X射线检查法。
检验员应将产品放在X射线设备下,通过扫描获取产品内部的影像,然后观察黑点的数量、分布和大小,以及是否与产品表面或内部有关。
二、塑胶件黑点检验准则针对塑胶件黑点的检验准则可以根据产品的外观要求、使用环境和性能要求等因素来制定1.黑点数量:准则应规定产品上允许存在的黑点数量的上限。
通过不同级别的分类,如A级、B级和C级,来表示黑点数量的不同容忍程度。
A级表示允许的黑点数量最少,C级表示允许的黑点数量最多。
2.黑点分布和大小:准则应规定黑点在产品表面或内部的分布范围和大小要求。
一般来说,黑点应均匀分布在产品表面或内部,不应集中在其中一区域。
而且,黑点的大小也应符合规定的要求,不能超过一定的尺寸。
3.黑点与产品质量的关系:准则应明确黑点对产品质量的影响程度和容忍程度。
一些黑点可能会直接影响产品的物理性能和使用寿命,而一些黑点只是影响外观质量,对产品性能没有明显影响。
- 1、下载文档前请自行甄别文档内容的完整性,平台不提供额外的编辑、内容补充、找答案等附加服务。
- 2、"仅部分预览"的文档,不可在线预览部分如存在完整性等问题,可反馈申请退款(可完整预览的文档不适用该条件!)。
- 3、如文档侵犯您的权益,请联系客服反馈,我们会尽快为您处理(人工客服工作时间:9:00-18:30)。
产品黑点,晶点问题分析改进报告
黑点问题是影响我们产品质量的一大顽症,随着客户对产品质量要求的提高,我们对黑点数量的控制要求也越来越严。
因此了解黑点到底是如何产生,以及如何去控制它这一工作已经迫在眉睫。
以妮维雅几个产品为重点,研究分析了黑点的来源,原因,并提出了改善措施。
一,黑点的来源
我们采集了吹塑一楼的黑点产品2000只,吹塑二楼的黑点产品2000只,通过肉眼观察,及显微镜放大观察分析得出以下结论:
黑点、杂质特征是颗粒较小、呈黑褐色,一般不反光,颗粒大时杂质呈层状、脆、易碎、破碎后多孔。
其分布特性:有的整体性无规则零散分布,有的是局部无规则零散分布,有时则仅偶尔出现在某一局部区域。
黑点可能为:
1,原料碳化物;(大部分为此类黑点,占70%)
2,随回料及外界环境带入的外来杂质;(此类黑点占20%)
3,设备内金属破碎颗粒;(此类黑点占8%)
4,色母未分散的斑点晶点及其他。
(此类黑点占2%)
以下图片为0.3mm黑点及晶点放大100倍后的图片
原料碳化的黑斑回料带入的杂质
原料碳化的黑块金属颗粒(粉碎机)
色粉积垢(流道) 原料碳化物
色粉积垢(流道) 金属颗粒(粉碎机) 流道色粉积垢(流道处)
珠光色母团聚(晶点)
原料碳化
二、黑点的成因
从影响质量的五大因素(人、机、料、法、环)入手,分析了黑点成因:
人
人这一因素是最重要的,也是最难控制的。
车间由主管到一线的员工是过程的直接控制者,也是对过程最了解的人,积极主动的一起去发现问题,解决问题,黑点也能有效控制。
机
机就是设备,很多黑点问题都是来源于设备上的缺陷:
由于设备老化,且保养不当,常会出现设备故障,一旦出现设备故障,就要停机处理,这样一来可能造成螺筒内物料炭化。
由于螺杆或料筒的长期使用造成间隙过大使熔料卡入而屯积,经受长时间固定加热造成分解,产生碳化物料。
设备套件磨损或里面有金属异物,在设备强力剪切下碎裂产生黑点。
塑料在料筒内受到高热而交联焦化,在几乎维持原来颗粒形状情形下,难以熔融,被螺杆压破碎后夹带进入制件。
(长时间加温会产生)
料
料即原料色母及回料。
原料及色母自身带入。
原料中的黑点对产品影响不大。
它会在加工过程中分散在产品中,但是包装袋上的污染物可能会带入原料中,从而产生杂质。
粉碎回料带入。
回料中由于环境等种种原因会带入杂质,从而引起黑点。
法
法主要是指生产工艺,包括混料、螺杆间隙、温度设定、主机转数(接头颈产生摩擦热)、等都会造成影响。
其中螺杆间隙和温度设定是产生影响的两个主要方面,温度过高及螺杆间隙过大不合理都容易产生物料碳化。
环
环即生产作业环境,是一个不可忽视的因素。
例如,两台相邻的机台分别生产深色产品和浅色产品,如果深色产品的色粉飘到浅色产品的半成品中,则很可能导致黑点的产生。
一般生产线的半成品斗、下料口均敞开,粉尘极易进入,由于车间灰尘较多也容易产生黑点。
三、改善措施
1,按《车间卫生清洁程序》规定对车间进行清洁,并记录在“环境卫生清洁表”中,严格控制生产、开包、混料至料筒的各个环节的清洁,通过环境的改善防止异物混入引起黑点。
原料开封前需清除灰尘后开封拌料,拌料后需立即封口。
车间环境需定时清理,不允许有粉尘堆积情形,机台面及所有与原料接触的设备输送带均应保持洁净不可有粉尘污染。
2,设备责任部门对设备重新进行检查,改善设备漏油情况,控制漏油滴至输送带,防止输送带受液压油污染。
对出现磨损设备导致漏油的油缸和油封进行更换。
3,严格按照工艺卡工艺要求生产,设定加工温度,生产周期。
加强原料温度工艺设定的准确性如有异常需立即检查,温度不可过高造成原料碳化,待机加温时间不可过长,长时间待机加温会造成原料碳化附着在螺杆和料管壁上产生黑点
4,消除螺筒、喷嘴、流道中的死角碳化原料,使其转弯处有平缓过渡,消除可能有料滞留的区域。
清洗降解沉积或已有碳化料沉积在螺纹面及螺筒壁上的黑点。
5,严格按照规定比例添加回料不超过30%,严格按照比例设备搅拌回料和新料保证比例均匀,无法使用完毕回料退回仓库,不得当班使用。
6,产品黑点需挖除后才可以粉碎回收,不然将会产生更多的黑点, 回料粉碎前需检查是否有污染,需将污染物清除后粉碎,不可盲目投料产生更多黑点,原料桶需定时清理擦拭防止粉尘污染。
7,粉碎机需定时清除灰尘尤其是下料口处要加强清理,粉碎刀需保持锋利架刀间隙不可大于0.5mm,间隙过大会造成回料空转摩擦产生粉末进入刀座间隙造成黑点。
粉末过多需使用筛网过滤粉碎的回料,最大可能减少粉状原料比例,从而减少由于粉状回料加热后产生的黑点。
6+6设备流道清理
模头,流道清理
流道抛光
四,验证
1,6+6机台不同回料比例对黑点的影响
我在6+6机台上,使用全新料、10%回料,20%回料,30%回料不同回料比例生产产品,统计黑点产生的比例,结果如下:
雅琪6+6设备A 班黑点统计
0.00%
1.00%
2.00%
3.00%
4.00%
5.00%全新料
10%回料
20%回料
30%回料
小于0.2黑点大于0.2黑点所有黑点
雅琪6+6设备B 班黑点统计
0.00%
2.00%4.00%6.00%8.00%全新料
10%回料
20%回料
30%回料
小于0.2黑点大于0.2黑点所有黑点
2、2+2机台不同回料比例对黑点比例的影响
在2+2机台上,使用全新料、10%回料、20%回料、30%回料不同回料比例生产产品,统计黑点产生的比例,结果如下:
2+2设备A班黑点统计
2+2设备B班黑点统计
从以上数据可以得出以下结论:
●回料比例上升,黑点比例呈现明显上升趋势。
其中6+6机台由全新料的2.0%黑点比例,
当回料添加到30%时,黑点比例上升到5.3%。
●不同的机台黑点比例呈显著差异。
6+6机台在回料比例从0%-30%之间,产生的黑点比例
在1.5%-6.0%范围内,而2+2机台在回料比例从0%-30%之间,产生的黑点比例在12%-38%范围内,有明显差异。
我们认为可能和设备内物料碳化程度有很大关系。
●原料不同也会导致黑点比例的上升,同样添加30%回料,5502原料黑点比例为37%左右,
而5621D原料黑点比例为59%。
分析原因可能和换了原料后,原料物性有差别,在一段时间内黑点比例明显上升
回料经过筛选处理和未筛选处理对黑点的影响
我们将回料经过筛选处理和未筛选处理(筛选处理的方法为用筛子将粉末状态的回料剔除),都添加30%的比例,统计回料经过筛选处理对黑点的影响:
结论:经过筛选后的回料用于生产,黑点比例显著下降,从49%下降到19%。
4、设备模头螺杆料筒等部件清理后对黑点的影响
我们将筛选后的回料用于设备模头清理前后的生产,对比设备模头螺杆等部件清理前后对黑点问题的影响:
结论:设备模头螺杆料筒等部件经过清理后,黑点比例显著下降由4.8%下降到0.9%。
设备模头螺杆料筒等部件经过清理后,黑点比例下降显著。
5、总结
经过上述分析及试验验证,得到以下结论:
黑点产生的关键原因为回料添加比例,回料中粉状物体,设备模头,螺杆,料筒等部件是否清理到位,在以后的生产中要严格控制回料比例,对回料进行筛选并定期清理设备模头,螺杆,料筒等部件,可以将黑点有效控制。
回料回收为黑点产生主要原因,回料控制请参考原料利用率改善方法
原料利用率控制改善:
严格控制头尾料长度,按品项制定标准列入工艺卡中受控,
成品克重必须调整在标准值偏下0.5克,超出标准克重会有原料损耗及能源损耗.
1,车间人员必须有正常生产中无报废料的观念,掉落地面的头尾料应立即捡起,相同原料更换颜色必需控制到无报废产生。
2,设备改善防止头尾料掉落.
3,粉碎机刀片检查每周需检查定刀及动刀情况,装刀间隙不可大于0.5mm,,盛料斗改善粉碎料不可掉落地面。
4,设备模头及流道发现漏料应立即停机改善。
5,量产中如有异常情况需处理,料胚需用不锈钢盘盛接回收使用,不可结成料块或脏污无法回收。
6,清洁机台掉落的头尾料不可与油污一起扫除,应捡起擦拭干净后回收使用。
7,报废原料需分类分班记录,严格控制报废原料不可超过当日生产原料总量的%0.2.。
8,停机过管产品及试模打样本色料均要回收使用不可报废。
9,回料回收粉碎过程需严谨检查发现异物立即挑除。
10,印刷及烫金不良品去除印刷字体后可回收的原料需回收使用。
11,PE原料产品印刷不良粉碎后需集中加工抽成黑色原料生产黑色产品。
12,厂内报废原料目前委托外包处理,如厂内自行规划人员处理可节余更多原料损耗。