油田中的二氧化碳腐蚀
某油田开发中二氧化碳腐蚀的危害性现状分析

某油田开发中二氧化碳腐蚀的危害性现状分析要想降低油气田开采中的二氧化碳腐蚀,必须对腐蚀机理以及类型基质影响因素这些进行分析和研究。
通过对腐蚀机理调研可以发现,二氧化碳会产生碳酸,进而产生电化学反应,最终造成钢材腐蚀。
在腐蚀种类上有均匀和冲刷以及坑点腐蚀,影响因素较多。
现在开发中防腐蚀措施也较多,现在主要对腐蚀的危害以及方式方式进行论述。
标签:二氧化碳;腐蚀机理;防腐方式前言:在油田开发中,二氧化碳腐蚀会造成巨大损失同时也会发生灾难性后果。
二氧化碳还石油和天然气开发中产生的常见气体。
在溶于水之后对金属会有加强的腐蚀性,这些对材料造成的破坏可以称之为二氧化碳腐蚀。
这些腐蚀会使得油井寿命大大低于设计寿命,也会使得设备腐蚀失效,现在掌握好腐蚀问题研究现状以及趋势,为减少损失提升效益提供借鉴。
1 二氧化碳腐蚀的机理二氧化碳腐蚀问题一直是人们关注的主要问题。
因为在二氧化碳溶于水之后PH 值升高,不断加速管材腐蚀,金属表面附着的H2C03中没有被电离的分子会被还原为H2分子,在电解质溶液中扩散到金属表面形成H2C03。
从此也可以看出碳酸造成的腐蚀要明显比电离要严重。
腐蚀学认为,坑腐蚀诱发主要是因为有台地腐蚀机制以及流动诱导机制等都会造成膜破损。
也有人通过腐蚀产物膜生产和发展过程,提出台地腐蚀机制:坑蚀最早出现在几个点,之后发展为一片,小孔腐蚀介质会破坏腐蚀产物膜,从而造成腐蚀。
2 二氧化碳腐蚀中的影响因素二氧化碳腐蚀是一个复杂的电化学过程,主要影响因素为PH 值以及二氧化碳分压、温度和流速、水量等各种因素。
2.1 PH 值。
溶液内PH 值会影响到H2C03在水中存在方式,在研究中可以发现PH﹤4 时,主要存在形式为H2C03;在4≤PH≤10 时,主要是以HC03 的形式出现,在PH>10 时,存在形式是CO2。
同时随着PH 值持续增加,H+增加而不断下降,腐蚀速率也会逐渐降低。
随着FeCO3 内的溶解度持续下降,更方便FeCO3 腐蚀膜的形成,这样也会降低腐蚀速率。
二氧化碳腐蚀性的介绍

二氧化碳腐蚀性的介绍一、关于二氧化碳的腐蚀性“二氧化碳腐蚀”这个术语1925年第一次被API(美国石油学会)采用。
1943年,首次认为出现在T exas油田的气井下油管的腐蚀为CO2腐蚀。
二氧化碳在水介质中能引起钢铁迅速的全面腐蚀和严重的局部腐蚀,管道和设备发生早期腐蚀,往往造成严重的后果。
在前苏联,油田设备二氧化碳腐蚀是在1961~1962年开发克拉斯诺尔边疆区油气田时首次发现的,设备内表面的腐蚀速度达5~8mm·a-1,导致设备损坏和产生事故隐患。
美国Little Creek油田实施CO2驱油试验期间,在无任何抑制的情况下,不到5个月的时间采油井油管管壁就腐蚀穿孔,腐蚀速度高达12.7mm·a-1。
油气田中这种恶性事故是CO2腐蚀的直接结果,它不仅造成巨大的经济损失,而且造成严重的社会后果。
类似的二氧化碳腐蚀破坏事故在南海油田、四川油气田都发生过。
在化肥生产等化工设备中,也常发生二氧化碳腐蚀。
如镇海石化总厂的大型化肥厂的高压CO2水冷器,将CO2气体冷却到合适温度后进入高压合成系统。
该设备是U型管换热器。
第一台U型管材质为3074L不锈钢,壁厚3mm,投产后一个半月因发生严重的点蚀,而造成泄漏。
第二台管子材料换成2RE69不锈钢,使用40多天又因泄漏管太多而报废。
在制氢装置的给水预热器、冷却器等部件,由于输送含CO2、CO 等气体,也经常发生CO2腐蚀破坏事故,主要是露点附近的二氧化碳腐蚀,这种腐蚀呈点蚀状态,压力愈高水分愈多,则露点愈低,腐蚀愈严重。
对于碳钢,在压力15×105Pa条件下,腐蚀速度会高达17mm/a。
1996年荷兰的Zeist城,煤气管道和煤气储罐(直径3m)发生的爆炸事故,以及1966年6月世界上最早的日本大型有机药品制造装置的管道系统中的碳钢凸绕、喷嘴等的焊接区发生了开裂,造成内部气体喷出,这两类事故后来经调查研究都被认为是在CO2-CO-H2O介质中发生的应力腐蚀裂开造成的。
抽油机井二氧化碳防腐技术应用

抽油机井二氧化碳防腐技术应用一、前言部分区块油井因二氧化碳腐蚀造成频繁躺井,直接影响油田的正常生产,油井二氧化碳腐蚀是制约油田生产开发的一个重要因素。
采用投放缓蚀剂、阴极保护器等措施效果不明显,通过对油井腐蚀机理的分析,提出防止油井二氧化碳腐蚀工艺措施,减少油井的腐蚀,延长了油井的检泵周期,节约了油田的检测和维修成本,提高油田的开发水平。
二、腐蚀影响因素研究1.腐蚀因素二氧化碳腐蚀钢材主要是二氧化碳溶于水生成碳酸而引起电化学腐蚀所致,主要考虑以下影响因素:1、二氧化碳分压的影响:二氧化碳分压小于0.021MPa 不产生腐蚀;在0.021~0.21MPa间为中等腐蚀;大于0.21MPa产生严重腐蚀。
2、矿化度的影响:溶液中以Cl-的影响最为突出,Cl-浓度越高,腐蚀速度越大,特别是当Cl-浓度大于3000mg/L 时腐蚀速度尤为明显。
3、流速的影响:一般认为随流速的增大,H2CO3和H+等去极化剂能更快地扩散到电极表面,使阴极去极化增强,消除扩散控制,同时使腐蚀产生的Fe2+迅速离开腐蚀金属的表面,因而腐蚀速率增大。
2.产出物分析2.1产出水在研究的过程中我们对30样本井进行了数据分析与采集,研究治理提供可靠依据。
通过对30口油井产出水的PH值、矿化度、氯离子含量和硫酸盐还原菌等指标进行分析,PH值为5.5~6.0,矿化度为44023~84040 mg/L,Cl-平均含36762mg/L ,SRB含量450~1000个/ml。
2.2伴生气将分析的伴生气中二氧化碳的含量和计算出的分压进行分析可知油井伴生气中二氧化碳的平均含量为1.78%,平均分压为0.28MPa。
油田产出水的二氧化碳含量相对较多,属于严重腐蚀等级,同时产出液的PH值较低(5.5~6.0),由此会产生严重的电化学腐蚀。
3.腐蚀影响因素认识通过腐蚀因素的实验分析,可以得出造成油井腐蚀的主要原因是:3.1油井含水率高,平均含水94.5%,介质的矿化度较高,Cl-、HCO3-等强腐蚀性离子含量高,溶液的PH值介于5.5~6.0之间,呈弱酸性,势必会造成油管、杆的电化学腐蚀。
二氧化碳腐蚀的机理与防护

二氧化碳腐蚀的机理与防护摘要:本文从阴阳两极的电化学反应出发,进行了详细阐述,对二氧化碳腐蚀类型进行了论述,最后给出几种可行的防护措施,需要将多种方法综合利用,才能有效控制腐蚀。
关键词:CO2 腐蚀机理防护措施在油气田开发中,尤其是在石油天然气工业中,二氧化碳腐蚀是一个由来已久的问题,也是一个不容忽视的严重问题。
1、二氧化碳腐蚀的机理二氧化碳腐蚀破坏行为在阴极和阳极处表现不同,在阳极处铁不断溶解导致了均匀腐蚀或局部腐蚀,表现为金属设施与日俱增的壁厚变薄或点蚀穿孔等局部腐蚀破坏;在阴极处二氧化碳溶解于水中形成碳酸,释放出氢离子。
氢离子是强去极化剂,极易夺取电子还原,促进阳极铁溶解而导致腐蚀,同时氢原子进入钢中,导致金属构件的开裂。
这个腐蚀过程可用如下反应式表示:众多实验研究结果一致认为,在常温无氧的二氧化碳溶液中,钢的腐蚀速率受析氢动力学控制,同时发现,从二氧化碳溶液中的析氢过程有两种不同的机理。
第一种机理,氢从氢离子的电化学反应式中析出:第二种机理,在金属界面上二氧化碳水合为碳酸,吸附的碳酸可以直接还原。
反应式如下:上述腐蚀机理是对裸露的金属表面而言的,在实际过程中,随着二氧化碳腐蚀的进行,金属表面将被腐蚀产物膜所覆盖,可用如下方程式表示:腐蚀产物膜一旦形成,腐蚀行为将与之有密切关系,腐蚀速度将受膜的结构、厚度、稳定性及渗透性等性能所控制。
2、二氧化碳腐蚀类型1、均匀腐蚀——电化学过程2、环状腐蚀——发生在经过热处理的管端3、冲蚀——发生在管子截面变化部位、收缩截流部位。
4、腐蚀开裂——在金属表面沿较脆的方向,以单项或类似枝状形式形成裂缝5、深坑型腐蚀——周边锐利、界面清晰的坑,产生坑蚀原因有三点:(1)二氧化碳气体溶于凝结在管壁上的水滴引起的(2)管壁表面形成的疏松不均匀腐蚀产物层或垢层,气体侵入后垢下腐蚀(3)涂层局部脱落和漏点处二氧化碳对钢材的腐蚀。
3、二氧化碳腐蚀的防护措施3.1钢材的选用镍也能增强钢的耐腐蚀性,但作用不很明显,含9%镍的钢用于二氧化碳分压高的环境中,耐腐蚀效果令人满意,但偶尔也发生开裂和点蚀。
新疆油田呼图壁储气库气井二氧化碳腐蚀因素初探

中腐 蚀 性 气 体 C 2 % , 2  ̄7 / 因此 , 要 考 O ≤2 H S mgm , < 需
虑 二 氧 化碳 的腐 蚀 问题 。一 般 认 为 ,二 氧化 碳 分 压 ( c2> .MP , 重 腐 蚀 ;c2 00  ̄ . a 腐 蚀 ; P o) O2 a 严 P o= .2 02 MP , P o< .2 a 没 有 腐 蚀 。预 计 储 气 库 采 出 时井 底 压 c:0 MP , 0 力 为 3 MP , 4 a 由此 得 出土 库 曼斯 坦 进关 的天 然气 P o e 为 06 MP , 于严 重 腐 蚀 。 由于 呼 图壁 气 藏 含有 地 . 8 a属
金属 表 面 的速度 共 同决 定 ,于是 以均 匀腐 蚀 为 主 : 在 6 ~ o , 成 的腐 蚀 产物 厚 而松 , 晶粗 大 , 均 0 10C时 形 1 结 不 匀, 易破 损 , 局部 孑 蚀 严 重 。 则 L 当温度 高 于 10C . 5  ̄ 时 腐 蚀产 物 细致 、 密 、 着力 强 , 一定 的保 护 性 , 得 紧 附 有 使 腐 蚀 率下 降 。 呼图壁 地层 温 度为 9 ℃, 生产 过程 中 , 3 在 可能 发生 局部 腐蚀 。
二 氧化碳 腐 蚀 的环 境 因素 进行 研 究 , 为储 气 库 气井 采
6 ℃时 , 于 不能 形 成 保 护 性 的腐 蚀 产 物 膜 , 蚀 速 0 由 腐
率 是 由 C : 解 于 水 生成 碳 酸 的速 度 和 C O 溶 O 扩散 至
取恰 当的 防腐措 施提 供依 据 。
2 二 氧 化 碳 腐 蚀 的 影 响 因 素 分 析
呼 图壁 气 田影 响二 氧 化 碳 腐 蚀 的环 境 影 响 因素
主 要 有 二氧 化 碳 分 压 、地 层 水 矿 化度 及 C 一 量 、 l 含 温
油气田CO2腐蚀及防控技术
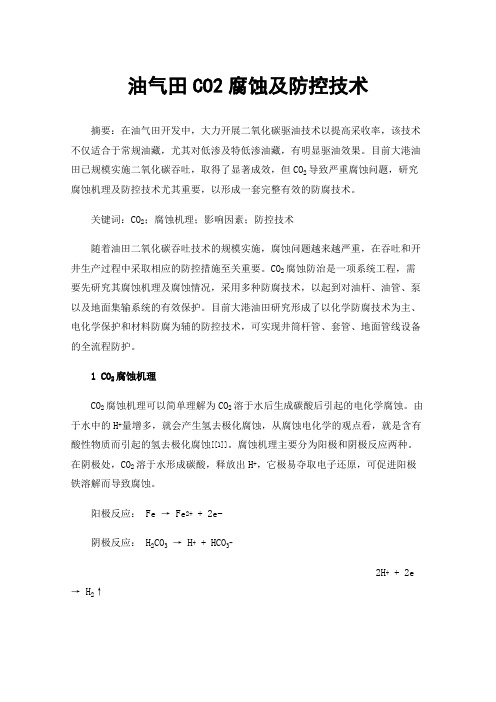
油气田CO2腐蚀及防控技术摘要:在油气田开发中,大力开展二氧化碳驱油技术以提高采收率,该技术不仅适合于常规油藏,尤其对低渗及特低渗油藏,有明显驱油效果。
目前大港油田已规模实施二氧化碳吞吐,取得了显著成效,但CO2导致严重腐蚀问题,研究腐蚀机理及防控技术尤其重要,以形成一套完整有效的防腐技术。
关键词:CO2;腐蚀机理;影响因素;防控技术随着油田二氧化碳吞吐技术的规模实施,腐蚀问题越来越严重,在吞吐和开井生产过程中采取相应的防控措施至关重要。
CO2腐蚀防治是一项系统工程,需要先研究其腐蚀机理及腐蚀情况,采用多种防腐技术,以起到对油杆、油管、泵以及地面集输系统的有效保护。
目前大港油田研究形成了以化学防腐技术为主、电化学保护和材料防腐为辅的防控技术,可实现井筒杆管、套管、地面管线设备的全流程防护。
1CO2腐蚀机理CO2腐蚀机理可以简单理解为CO2溶于水后生成碳酸后引起的电化学腐蚀。
由于水中的H+量增多,就会产生氢去极化腐蚀,从腐蚀电化学的观点看,就是含有酸性物质而引起的氢去极化腐蚀[[1]]。
腐蚀机理主要分为阳极和阴极反应两种。
在阴极处,CO2溶于水形成碳酸,释放出H+,它极易夺取电子还原,可促进阳极铁溶解而导致腐蚀。
阳极反应:Fe → Fe2+ + 2e-阴极反应: H2CO3→ H+ + HCO3-2H+ + 2e → H2↑碳酸比相同pH值下的可完全电离的酸腐蚀性更强,在腐蚀过程中,可形成全面腐蚀和局部腐蚀。
全面研究二氧化碳的腐蚀机理十分关键,2CO2腐蚀影响因素二氧化碳对金属材料的腐蚀受多种因素影响,有材质因素、压力、温度、流速、pH、介质中水和气体、有机酸、共存离子、细菌腐蚀等,本文主要介绍三种重要因素。
2.1 二氧化碳压力碳钢等金属的腐蚀速度随二氧化碳分压压力增大而加大,溶于水介质中CO2的含量增大,酸性增强,H+的还原反应就会加速,腐蚀性加大。
通过高温高压动态腐蚀评价来验证压力的影响,选取二氧化碳不同压力作为试验条件,对采出液在不同压力下评价腐蚀性。
油气田开发中的二氧化碳腐蚀及影响因素

自发现 CO2 腐蚀以来,便开始了对其腐蚀机理的 研究,并且随着科学技术的发展,其研究越来越深 入。虽然许多专家都对此提出了自已的观点,但是到
全面腐蚀控制
万里平等: 油气田开发中的二氧化碳腐蚀及影响因素 2003年第17卷第2期
速度。在含 CO2 介质中,钢表面腐蚀产物膜组成、结 构、形态及特征会受介质组成、Pco2、T、pH 值和钢 组成的影响。膜的稳定性和渗透性会影响钢的腐蚀特
性。视钢种、介质和环境状态参数的不同,膜组成为
CO 2(吸附) + H 2O → H2 CO 3(吸附)
+
H
C
O
3
- (吸附)
H C O3-(吸附) + H 3O+ → H 2CO 3(吸附) + H2O
支持后一机理的实验结果还表明:(1)不同金属
材料有不同的催化活性,因而腐蚀速率也不同;(2)在
一定的 pH 值范围内(pH 值为 4~6),pH 值对阴极反
—14 —
CO2 含量高达 12% 左右;大庆油田、吉林油田也都发 生过因 CO2 腐蚀而造成设备严重腐蚀的情况。CO2 腐 蚀也是一个世界性的问题,例如挪威的Ekofisk油田、 德国北部地区的油气田、美国的一些油气田以及中东 油田等均存在 CO2 腐蚀问题。挪威Ekofisk 气田 1 号 井,CO2 分压高达 0.62MPa,水相 pH 值为 6.0,温度 为93℃,Fe2+浓度为120mg/L,流速在6.4~7.9m/s,在 正常生产309 天后,于井深1740m处的油管便因腐蚀 而断裂,按此估计,其CO2 腐蚀速度为10.2mm/a。由 上诸多实例可以看出,无论在国内还是国外,CO2 腐 蚀都已成为一个不容忽视的问题[1-3]。
3.2 CO2分压 CO2 分压是衡量 CO2 腐蚀的一个重要参数。通常 认为,当 CO2 分压超过 20KPa 时,流体具有腐蚀性, 这是一条判别准则。在较低温度下(低于 60℃),由 于温度较低,没有完善的FeCO3 保护膜,腐蚀速度随 CO2 分压的增大而加大。在 100℃左右,FeCO3 膜的 保护不完全,出现坑蚀等局部腐蚀,其腐蚀速度也随 CO2 分压的增大而加大。在150℃左右,致密的FeCO3 保护膜形成,使腐蚀速度大为降低。1975 年, De Waard 和Milliams提出了在无FeCO3保护膜下CO2对 炭钢的腐蚀速度计算公式[5]。该公式已在工业上广泛 应用,其形式如下: lgCR=0.67lg(Pco2)+C 式中:CR 为腐蚀速度,mm/a;Pco2 为 CO2 分压, 105Pa;C 为温度影响校正常数。由上式可以看出:腐 蚀速度与 CO2 分压的 0.67 次幂成正比。 许多实验表明,在温度低于 60℃时,金属表面
二氧化碳腐蚀试验

二氧化碳腐蚀试验引言:二氧化碳腐蚀是一种常见的金属腐蚀现象,特别是在工业环境中,如石油化工、能源、航空航天等领域,二氧化碳腐蚀对设备和结构的安全和可靠性造成了威胁。
因此,研究二氧化碳腐蚀机理和寻找有效的防护措施具有重要意义。
一、二氧化碳腐蚀的机理二氧化碳腐蚀是指金属与二氧化碳气体发生化学反应,导致金属表面出现腐蚀现象。
这种腐蚀通常发生在高温高压的工业环境中,如油气田、化工装置等。
二氧化碳腐蚀主要有以下几个方面的机理:1. 电化学腐蚀:二氧化碳溶解在水中会生成碳酸,而碳酸具有一定的电离能力,形成的氢离子可以加速金属的腐蚀过程。
2. 碱性腐蚀:二氧化碳溶解在水中会生成碳酸根离子,而碳酸根离子具有一定的碱性,对金属具有腐蚀性。
3. 氧化腐蚀:二氧化碳中的氧气和金属表面发生氧化反应,导致金属表面形成氧化物,进而引发腐蚀。
二、二氧化碳腐蚀试验的目的和方法为了研究二氧化碳腐蚀的机理和评估材料的腐蚀性能,科学家们开展了二氧化碳腐蚀试验。
这些试验的主要目的是测量材料在二氧化碳环境中的腐蚀速率和腐蚀形态,以及评估不同防护措施对腐蚀的效果。
常用的二氧化碳腐蚀试验方法包括:1. 重量损失法:将试样暴露在二氧化碳环境中一定时间后,通过测量试样的重量变化来计算腐蚀速率。
2. 电化学法:使用电化学方法测量试样在二氧化碳环境中的腐蚀电流和电位,以评估材料的腐蚀性能。
3. 表面分析法:通过扫描电子显微镜(SEM)、能谱分析(EDS)等表面分析技术,观察和分析试样表面的腐蚀形貌和化学成分。
三、二氧化碳腐蚀试验的影响因素二氧化碳腐蚀的严重程度受多种因素的影响,包括二氧化碳浓度、温度、压力、流速、材料成分等。
其中,二氧化碳浓度是影响二氧化碳腐蚀最重要的因素之一。
随着二氧化碳浓度的增加,腐蚀速率也相应增加。
此外,温度、压力和流速的增加也会加剧二氧化碳腐蚀的程度。
四、二氧化碳腐蚀的防护措施为了减轻二氧化碳腐蚀对设备和结构的损害,科学家们提出了多种有效的防护措施。
- 1、下载文档前请自行甄别文档内容的完整性,平台不提供额外的编辑、内容补充、找答案等附加服务。
- 2、"仅部分预览"的文档,不可在线预览部分如存在完整性等问题,可反馈申请退款(可完整预览的文档不适用该条件!)。
- 3、如文档侵犯您的权益,请联系客服反馈,我们会尽快为您处理(人工客服工作时间:9:00-18:30)。
油田中的二氧化碳腐蚀
CO2是油田生产中常见的腐蚀介质,油田单井、流程、海管中介质含有CO2均可能产生CO2腐蚀,尤其是流体含水量超过30%的情况下。
CO2通常状况下是一种无色、无臭、无味无毒的气体,能溶于水,在25℃溶解度为0.144g (100g水)。
密度约为空气的1.5倍。
干燥的CO2气体本身是没有腐蚀性的,但CO2溶于水后对钢铁材料具有比较强的腐蚀性。
CO2较容易溶解在水中,而在碳氢化合物(如原油)中的溶解度则更高,气体CO2与碳氢化合物的体积比可以达到3:1。
当CO2溶解在水中时,会促进钢铁发生电化学腐蚀。
CO2腐蚀除产生均匀腐蚀外,在大多数情况下产生局部腐蚀损伤。
根据CO2腐蚀的不同腐蚀破坏形态,能提出不同的腐蚀机理。
以CO2对钢铁和含铬钢的腐蚀为例,有全面腐蚀,也有局部腐蚀。
根据介质温度的不同,腐蚀的发生可以分为三类:在温度较低时,主要发生金属的活泼溶解,对碳钢主要发生金属的溶解,为全面腐蚀,而对于含铬钢可以形成腐蚀产物膜;在中间温度区间,两种金属由于腐蚀产物在金属表面的不均匀分布,主要发生局部腐蚀,如点蚀等;在高温时,无论碳钢和含铬钢,腐蚀产物可以较好地沉淀在金属表面,从而抑制金属的腐蚀。
1.二氧化碳全面腐蚀机理
二氧化碳腐蚀是气体二氧化碳溶解于水中所产生的电化学腐蚀。
首先环境中的二氧化碳溶解于水中并形成碳酸。
然后碳酸经过两步电离,使溶液呈现酸性。
CO2+H2O⇌H2CO3
H2CO3⇌H++HCO3−
HCO3−⇌H++CO32−
在含有二氧化碳的腐蚀溶液中,钢铁材料的阳极反应为:
F e→F e2++2e−
阴极反应为:
2H++2e−→H2↑
总的腐蚀反应为:
CO2+H2O+F e→F e CO3+H2
由总反应式可知,阳极溶解的铁离子和溶液中碳酸根离子形成F e CO3,F e CO3为规则的块状附着在金属表面。
当金属表面形成F e CO3腐蚀膜后,这种腐蚀膜没有明显的保护性。
在
较高温度情况下,由于增大了钢铁表面初始的F e2+溶出速率而在钢铁表面生成致密的保护膜,该层膜结晶致密,可以阻止钢铁的进一步腐蚀。
同时在高温100℃环境下,会发生化学腐蚀,腐蚀产物的形成对腐蚀过程有一定的阻滞作用。
2.二氧化碳局部腐蚀机理
二氧化碳的局部腐蚀现象主要包括点蚀、台地侵蚀、流动诱导局部腐蚀等。
二氧化碳的腐蚀破坏往往是由局部腐蚀造成的。
这些腐蚀形态的形成与CO2腐蚀环境的具体条件有关,也与其起始的腐蚀损伤与点腐蚀有关。
在金属表面大部分区域,腐蚀产物膜和试样表面紧密接触,腐蚀介质难以穿过膜层到达金属表面,金属处于相对钝态,而在最靠近试样表面的腐蚀产物膜不完整的缝隙,或局部PH值低与高氯离子浓度的地方表面产生破坏,腐蚀介质可到达金属表面,这些区域便成为电化学反应的阳极,而其他处于钝化态的金属表面便成为阴极,形成宏观腐蚀电池效应。
这种小阳极大阴极腐蚀将使金属在很短时间内形成严重的局部腐蚀区,同时在膜中孔隙处及腐蚀坑底部,腐蚀介质不流通还可引起自催化腐蚀反应而加剧局部腐蚀,导致金属表面点腐蚀。
如果点腐蚀在各个方向的生长速度相同,则腐蚀损伤胃形状接近半球形的腐蚀坑。
如果腐蚀坑的四周处于钝化态,腐蚀坑底处于活化态,则形成细而深的腐蚀坑。
对凝析气井的金属管道,含CO2天然气中的水分凝结在金属表面,先形成点腐蚀,而受气流和凝结水滴形状的影响,腐蚀在顺流速的方向生长的速率比较高,则形成癣状腐蚀。
在流动的液态或气态环境中,当腐蚀坑形成后,腐蚀坑四周的腐蚀速率高于腐蚀坑底的生长速率,则腐蚀坑形成后向四周生长,形成台地腐蚀损伤。
在流动性腐蚀溶液中,流动的介质可进入腐蚀坑,减轻腐蚀坑内的闭塞电池效应和自催化作用,使腐蚀坑发展速率显著降低。
流体对腐蚀坑的机械作用,使腐蚀坑壁的腐蚀产物膜脱落失去保护作用,腐蚀坑壁发展形成台地,在台地上又可产生腐蚀坑,又会形成新的台地。
如果当介质流速很高或在管道的弯头部位,流体对腐蚀坑壁产生很大的机械作用时,则产生冲刷腐蚀。
在含CO2的介质中,腐蚀产物FeCO3、垢CaCO3或其他的生成物膜在钢铁表面不同的区域覆盖度不同,不同覆盖度的区域之间形成了具有很强自催化特性的腐蚀电偶或闭塞电池。
CO2的局部腐蚀就是腐蚀电偶作用的结果。
2.1介质中H2S的含量对二氧化碳腐蚀的影响
H2S、CO2是油气工业中主要的腐蚀性气体。
在无二氧化碳(sweet gas)油气介质中也难免存在少量硫化氢。
钢材设备上,硫化氢可形成FeS膜,引起局部腐蚀,导致氢鼓泡、硫化物应力腐蚀开裂(SSCC),并能和CO2共同引起应力腐蚀开裂(SCC)。
不同浓度的硫化氢对CO2的影响如表所示,其中H2S对CO2腐蚀的影响可以分为三类。
第一类:环境
温度较低(60℃左右),H2S浓度低于3.3mg.kg-1,H2S通过加速腐蚀的阴极反应而加速腐蚀的进行。
第二类,温度在100℃左右,H2S浓度超过33mg.kg-1时,局部腐蚀降低但是均匀腐蚀速度增加。
当温度在150℃附近时,发生第三类腐蚀,金属表面会形成FeCO3或FeS 保护膜,从而抑制腐蚀的进行。
2.2介质中O2的含量
O2与CO2共存于水中会引起严重的腐蚀。
O2还是铁腐蚀反应中的主要阳极去极化剂之一,此外,O2在二氧化碳腐蚀的催化机制中起到了重大作用:当钢铁表面未生成保护膜时,O2含量的增加,使得碳钢腐蚀速率增加;如果在钢铁表面生成保护膜,则O2的存在几乎不会影响碳钢的腐蚀速率,因为此时CO2的存在也将会大大提高钢铁的腐蚀速率,CO2在腐蚀中起到催化剂的作用。
2.3介质水的含量
无论在气相还是在液相中,CO2腐蚀的发生都离不开水对钢铁表面的浸湿作用。
因此,水在介质中的含量是影响CO2腐蚀的一个重要因素。
通常,当水中的含量小于30%(质量)时,会形成油包水(水/油)乳化液,水包含在油中,这时水对钢铁表面的浸湿将会受到抑制,发生二氧化碳腐蚀的倾向较小;当水的含量大于40%(质量)时,会形成水包油(油/水)乳液,油包含在水中,这时水相对钢铁表面发生浸湿而引起CO2腐蚀。
所以,30%(质量)的含水量是判断是否发生CO2腐蚀的一个经验判断。
随着含水量的增大,CO2的腐蚀速度增大。
在含水率为45%(质量)左右,CO2的腐蚀速度出现一个突越,原因是介质从油包水乳化液向水包油乳化液转变的缘故。
2.4介质温度
大量的研究结果显示,温度是CO2腐蚀的重要参数;且很多研究结果表明:在60℃附近CO2腐蚀在动力学上有质的变化。
FeCO3溶解度具有负的温度系数,溶解度随温度升高而降低,即反常溶解现象。
根据温度对腐蚀的影响,铁的CO2腐蚀可以分为以下四种情况:
(1)T<60℃,腐蚀产物为FeCO3,软而无附着力,金属表面光滑,主要发生均匀腐蚀;
(2)60~110℃,钢铁表面可以生成具有一定保护性的腐蚀产物膜,局部腐蚀较突出;
(3)在110℃附近,均匀腐蚀速度高,局部腐蚀严重(深孔),腐蚀产物为厚而疏松的FeCO3粗结晶;
(4)150℃以上,生成细致、紧密、附着力强的FeCO3和Fe3O4膜,腐蚀速率较低。
2.5二氧化碳分压
二氧化碳分压在判断CO2腐蚀中起着重要的作用。
DNV于1981年颁布的TNB111认为,当油气的相对湿度大于50%,二氧化碳超过1Mpa、O2分压超过100Pa、H2S分压超过1Mpa时,油气具有腐蚀性。
目前在油气工业中根据CO2分压判断CO2腐蚀性的规律如下表:
在油气工业中CO2分压可以采用以下的计算方法:
输油管线中CO2分压=井口回压× CO2百分含量
井口二氧化碳分压=井口油压× CO2百分含量
井下CO2分压=饱和压力(或流压)× CO2百分含量
2.6介质的pH值
pH值的变化直接影响H2CO3在水溶液中的存在形式。
当pH值小于4时,主要以H2CO3形式存在;当pH值在4~10之间,主要以HCO3-形式存在;当pH值大于10时,主要以CO32-存在。
一般来说,pH值增大,H+含量减少,降低了原子氢还原反应速度,从而降低了腐蚀速度。
裸钢在pH值低于3.8的含CO2除O2的水中,腐蚀速率随PH降低而增加,表明此时CO2对腐蚀的影响主要体现在pH对腐蚀的影响。
2.7介质的流速
在固定的设备(容器)中,流速的变化直接改变含CO2介质的流动状态。
流体的流动主要分为层流和湍流两种不同的流动形式。
由雷诺数(Re)来表示流动状态:
Re=d×V×ρ/ u
其中d为管道内径(m),V为液体流速(m.s-1);ρ为液体密度(kg.m-3);u为液体粘度(kg.m-1.s-1)。
Re和流体状态的关系为:Re<2300为层流;Re>4000为湍流。
流速的增大,使H2CO3和H+等去极化剂更快的扩散到电极表面,使阴极去极化剂增强,消除扩散控制,同时使腐蚀产生的Fe2+迅速离开金属表面,这些作用使腐蚀速率增大。
2.8垢
影响油、气、水系统结垢的因素很多,其中最重要的是油田产出水及其溶质类型。
在油田生产过程中,地下储层、采油井井筒、地面油气集输设备、管线内均可以产生无机盐结垢,尤其是在含有CO2的油气井中,当含有Ca2+时,会形成大量的CaCO3垢和相应的腐蚀产物。
垢会沉积在钢铁表面,引起垢下腐蚀,另外,垢层覆盖部分和裸露部分的金属管道也会形成电偶腐蚀。