烟气脱硫系统节能优化措施
循环流化床脱硫系统节能降耗措施浅谈
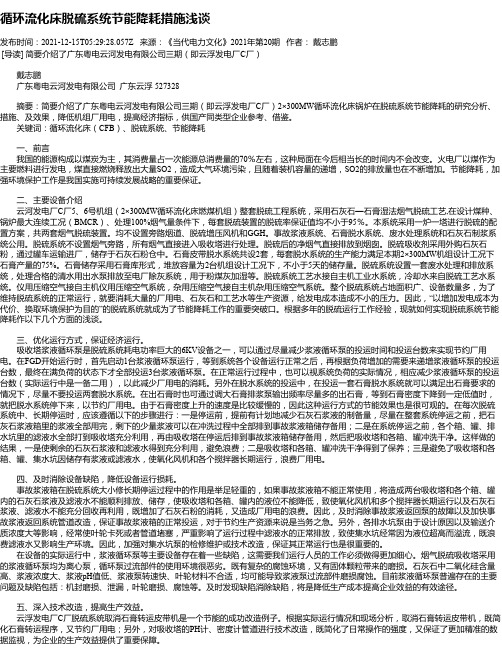
循环流化床脱硫系统节能降耗措施浅谈发布时间:2021-12-15T05:29:28.057Z 来源:《当代电力文化》2021年第20期作者:戴志鹏[导读] 简要介绍了广东粤电云河发电有限公司三期(即云浮发电厂C厂)戴志鹏广东粤电云河发电有限公司广东云浮 527328摘要:简要介绍了广东粤电云河发电有限公司三期(即云浮发电厂C厂)2×300MW循环流化床锅炉在脱硫系统节能降耗的研究分析、措施、及效果,降低机组厂用电,提高经济指标,供国产同类型企业参考、借鉴。
关键词:循环流化床(CFB)、脱硫系统、节能降耗一、前言我国的能源构成以煤炭为主,其消费量占一次能源总消费量的70%左右,这种局面在今后相当长的时间内不会改变。
火电厂以煤作为主要燃料进行发电,煤直接燃烧释放出大量SO2,造成大气环境污染,且随着装机容量的递增,SO2的排放量也在不断增加。
节能降耗,加强环境保护工作是我国实施可持续发展战略的重要保证。
二、主要设备介绍云河发电厂C厂5、6号机组(2×300MW循环流化床燃煤机组)整套脱硫工程系统,采用石灰石—石膏湿法烟气脱硫工艺,在设计煤种、锅炉最大连续工况(BMCR)、处理100%烟气量条件下,每套脱硫装置的脱硫率保证值均不小于95%。
本系统采用一炉一塔进行脱硫的配置方案,共两套烟气脱硫装置。
均不设置旁路烟道、脱硫增压风机和GGH。
事故浆液系统、石膏脱水系统、废水处理系统和石灰石制浆系统公用。
脱硫系统不设置烟气旁路,所有烟气直接进入吸收塔进行处理。
脱硫后的净烟气直接排放到烟囱。
脱硫吸收剂采用外购石灰石粉,通过罐车运输进厂,储存于石灰石粉仓中。
石膏皮带脱水系统共设2套,每套脱水系统的生产能力满足本期2×300MW机组设计工况下石膏产量的75%。
石膏储存采用石膏库形式,堆放容量为2台机组设计工况下,不小于5天的储存量。
脱硫系统设置一套废水处理和排放系统,处理合格的清水用出水泵排放至电厂除灰系统,用于粉煤灰加湿等。
石灰石-石膏湿法烟气脱硫脱水系统运行优化

石灰石-石膏湿法烟气脱硫脱水系统运行优化石灰石-石膏湿法烟气脱硫脱水系统是烟气脱硫脱水技术中常见的一种方法,对于工业生产中排放的烟气进行净化处理具有重要意义。
系统的运行优化对于提高处理效率、降低能耗、保障环境安全同样至关重要。
本文将对石灰石-石膏湿法烟气脱硫脱水系统运行优化进行探讨,并提出相关建议和解决方案。
一、系统结构与工作原理石灰石-石膏湿法烟气脱硫脱水系统主要由烟气脱硫脱水装置、石灰石浆液制备系统、脱水系统、石膏脱水再生系统等部分组成。
其工作原理是将排放的烟气经过脱硫塔,利用石灰石浆液中的Ca(OH)2与SO2反应生成CaSO3、CaSO4等沉淀物,并将烟气中的SO2、NOx 等有害物质吸收、氧化、转化成固体废物,然后通过脱水系统将脱硫脱水产生的石膏脱水,达到排放标准后进行再生利用。
二、系统运行优化1. 设备优化石灰石-石膏湿法烟气脱硫脱水系统中的关键设备包括脱硫塔、搅拌器、脱水设备等,对于这些设备的工作状态进行优化是系统运行优化的重要环节。
首先要做好设备的定期维护保养工作,保证设备的正常运行和使用寿命。
其次是对设备进行技术改造和升级,采用先进的技术手段完善设备功能,提高设备的稳定性和耐久性。
还要加强对设备运行数据的监测和分析,及时发现并处理设备运行中的问题,保障系统的平稳运行。
2. 工艺优化石灰石-石膏湿法烟气脱硫脱水系统的工艺优化主要包括石灰石浆液制备、脱硫反应、石膏脱水等环节。
在石灰石浆液制备过程中,应注意石灰石粉末与水的比例、搅拌速度、搅拌时间等参数的调整,以保证制备出浆液的浓度和稳定性。
在脱硫反应过程中,应根据烟气中SO2、NOx的含量和流速等参数,调整脱硫塔中浆液的供应量和分布方式,实现对有害物质的高效吸收和转化。
在石膏脱水环节,应根据脱水设备的特性,合理控制脱水速度和温度,提高脱水效率和质量。
3. 能耗优化石灰石-石膏湿法烟气脱硫脱水系统的运行中涉及大量的能源消耗,包括水泵、搅拌器、脱水设备等设备的驱动能耗,石灰石浆液制备、脱硫反应、石膏脱水等过程中的能量消耗等。
scr脱硝技术节能技术措施

scr脱硝技术节能技术措施SCR脱硝技术是一种用于燃煤电厂和工业锅炉等燃烧设备中降低氮氧化物排放的先进技术。
它通过在烟气中注入氨水和催化剂,将氮氧化物转化为氮气和水蒸气,从而达到脱硝的目的。
SCR脱硝技术不仅能有效降低氮氧化物的排放浓度,还具有节能的特点。
SCR脱硝技术的节能技术措施主要包括以下几个方面:1. 充分利用余热:在SCR脱硝过程中,注入的氨水需要提前加热到一定温度才能发挥催化作用。
而烟气中含有大量的余热,通过合理设计脱硝装置,可以利用余热对氨水进行加热,减少外部能源的消耗,从而达到节能的目的。
2. 优化催化剂设计:SCR催化剂是SCR脱硝技术的核心部分,催化剂的性能和设计对脱硝效率和能耗有直接影响。
通过优化催化剂的成分、结构和形状等参数,可以提高催化剂的活性和稳定性,降低脱硝过程中的能耗。
3. 控制氨气的使用量:在SCR脱硝过程中,氨水中的氨气是催化剂发挥作用的关键。
合理控制氨气的使用量,可以减少氨气的浪费和排放,降低能源消耗。
4. 优化脱硝装置的运行参数:SCR脱硝装置的运行参数的优化也是节能的重要措施。
通过合理调整烟气温度、氨水的注入量和催化剂的分布等参数,可以提高脱硝效率,降低能耗。
5. 维护和清洗催化剂:催化剂在使用一段时间后会受到积灰和硫化物等污染物的影响,降低催化剂的活性。
定期对催化剂进行维护和清洗,可以恢复催化剂的活性,提高脱硝效率,减少能源的消耗。
6. 系统运行优化:SCR脱硝技术需要配合其他设备一起运行,如除尘设备、脱硫设备等。
通过对整体系统的运行进行优化,可以降低系统的能耗,提高整体的节能效果。
SCR脱硝技术作为一种先进的脱硝技术,具有较高的脱硝效率和较低的能耗。
通过合理的节能技术措施,可以进一步提高脱硝技术的节能效果,减少能源消耗,降低对环境的影响。
在未来的发展中,我们还应该不断探索和研究,进一步提高SCR脱硝技术的节能效果,为建设清洁、低碳的能源体系做出贡献。
燃气工程节能环保方案
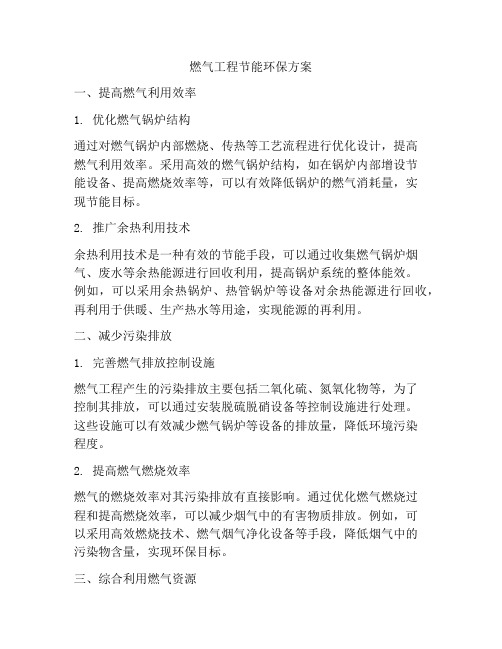
燃气工程节能环保方案一、提高燃气利用效率1. 优化燃气锅炉结构通过对燃气锅炉内部燃烧、传热等工艺流程进行优化设计,提高燃气利用效率。
采用高效的燃气锅炉结构,如在锅炉内部增设节能设备、提高燃烧效率等,可以有效降低锅炉的燃气消耗量,实现节能目标。
2. 推广余热利用技术余热利用技术是一种有效的节能手段,可以通过收集燃气锅炉烟气、废水等余热能源进行回收利用,提高锅炉系统的整体能效。
例如,可以采用余热锅炉、热管锅炉等设备对余热能源进行回收,再利用于供暖、生产热水等用途,实现能源的再利用。
二、减少污染排放1. 完善燃气排放控制设施燃气工程产生的污染排放主要包括二氧化硫、氮氧化物等,为了控制其排放,可以通过安装脱硫脱硝设备等控制设施进行处理。
这些设施可以有效减少燃气锅炉等设备的排放量,降低环境污染程度。
2. 提高燃气燃烧效率燃气的燃烧效率对其污染排放有直接影响。
通过优化燃气燃烧过程和提高燃烧效率,可以减少烟气中的有害物质排放。
例如,可以采用高效燃烧技术、燃气烟气净化设备等手段,降低烟气中的污染物含量,实现环保目标。
三、综合利用燃气资源1. 发展燃气余热发电技术燃气余热发电技术是一种综合利用能源的方法,可以通过收集燃气余热能源进行发电,实现能源的有效利用。
这种技术不仅提高了燃气能源的利用效率,同时也降低了排放污染物的数量,是一种可持续发展的节能环保方案。
2. 推广燃气供暖技术燃气供暖技术是一种利用燃气热能进行供暖的方法,相比传统供暖能源如煤、油等,燃气供暖更具有清洁、高效等特点。
通过优化供暖系统设计、提高燃气锅炉效率等措施,可以减少对环境的影响,实现节能环保。
四、加强管理和监督1. 建立健全节能环保管理体系通过建立健全的节能环保管理体系,包括加强燃气工程设备的检测监测、加强能源利用效率评估等措施,可以促进企业的节能环保工作。
提高企业的节能环保意识、加强对相关政策法规的宣传和执行,对于实现节能环保目标具有积极的作用。
降低脱硫设备用电量
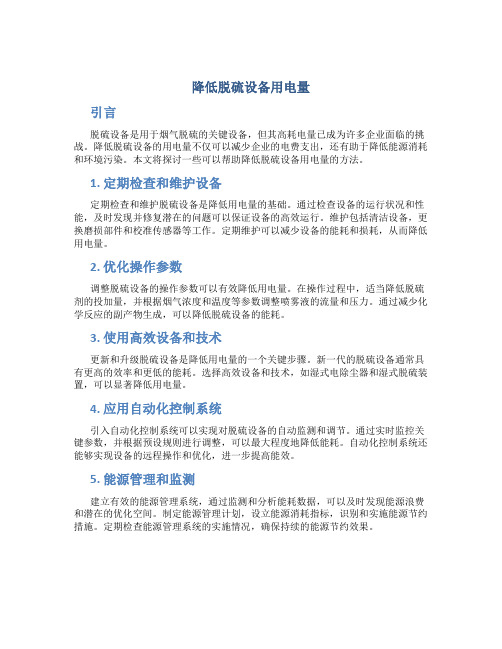
降低脱硫设备用电量引言脱硫设备是用于烟气脱硫的关键设备,但其高耗电量已成为许多企业面临的挑战。
降低脱硫设备的用电量不仅可以减少企业的电费支出,还有助于降低能源消耗和环境污染。
本文将探讨一些可以帮助降低脱硫设备用电量的方法。
1. 定期检查和维护设备定期检查和维护脱硫设备是降低用电量的基础。
通过检查设备的运行状况和性能,及时发现并修复潜在的问题可以保证设备的高效运行。
维护包括清洁设备,更换磨损部件和校准传感器等工作。
定期维护可以减少设备的能耗和损耗,从而降低用电量。
2. 优化操作参数调整脱硫设备的操作参数可以有效降低用电量。
在操作过程中,适当降低脱硫剂的投加量,并根据烟气浓度和温度等参数调整喷雾液的流量和压力。
通过减少化学反应的副产物生成,可以降低脱硫设备的能耗。
3. 使用高效设备和技术更新和升级脱硫设备是降低用电量的一个关键步骤。
新一代的脱硫设备通常具有更高的效率和更低的能耗。
选择高效设备和技术,如湿式电除尘器和湿式脱硫装置,可以显著降低用电量。
4. 应用自动化控制系统引入自动化控制系统可以实现对脱硫设备的自动监测和调节。
通过实时监控关键参数,并根据预设规则进行调整,可以最大程度地降低能耗。
自动化控制系统还能够实现设备的远程操作和优化,进一步提高能效。
5. 能源管理和监测建立有效的能源管理系统,通过监测和分析能耗数据,可以及时发现能源浪费和潜在的优化空间。
制定能源管理计划,设立能源消耗指标,识别和实施能源节约措施。
定期检查能源管理系统的实施情况,确保持续的能源节约效果。
6. 培训和人员意识提升提高员工的意识和培训水平是实施节能措施的重要环节。
通过加强培训,使员工了解脱硫设备的工作原理和操作要点,掌握节能技巧和能源管理知识。
员工的参与和支持是节能措施顺利实施的关键。
结论通过定期检查和维护设备,优化操作参数,使用高效设备和技术,应用自动化控制系统,建立能源管理和监测机制以及提升人员意识和培训水平,企业可以有效降低脱硫设备的用电量。
脱硫工程烟气系统调试方案
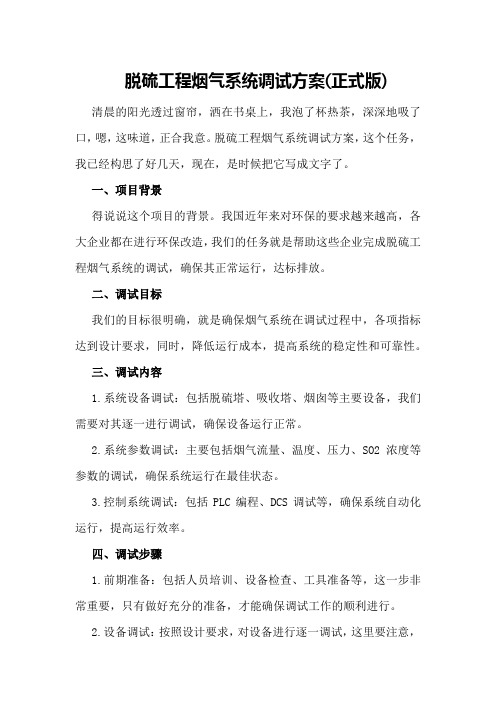
脱硫工程烟气系统调试方案(正式版)清晨的阳光透过窗帘,洒在书桌上,我泡了杯热茶,深深地吸了口,嗯,这味道,正合我意。
脱硫工程烟气系统调试方案,这个任务,我已经构思了好几天,现在,是时候把它写成文字了。
一、项目背景得说说这个项目的背景。
我国近年来对环保的要求越来越高,各大企业都在进行环保改造,我们的任务就是帮助这些企业完成脱硫工程烟气系统的调试,确保其正常运行,达标排放。
二、调试目标我们的目标很明确,就是确保烟气系统在调试过程中,各项指标达到设计要求,同时,降低运行成本,提高系统的稳定性和可靠性。
三、调试内容1.系统设备调试:包括脱硫塔、吸收塔、烟囱等主要设备,我们需要对其逐一进行调试,确保设备运行正常。
2.系统参数调试:主要包括烟气流量、温度、压力、SO2浓度等参数的调试,确保系统运行在最佳状态。
3.控制系统调试:包括PLC编程、DCS调试等,确保系统自动化运行,提高运行效率。
四、调试步骤1.前期准备:包括人员培训、设备检查、工具准备等,这一步非常重要,只有做好充分的准备,才能确保调试工作的顺利进行。
2.设备调试:按照设计要求,对设备进行逐一调试,这里要注意,调试过程中要严格遵守操作规程,确保人身和设备安全。
3.参数调试:在设备调试完成后,对系统参数进行调试,这一步需要根据实际情况进行调整,以达到最佳运行状态。
4.控制系统调试:在设备参数调试完成后,进行控制系统调试,确保系统自动化运行。
五、调试方法1.现场调试:通过现场操作,对设备进行调试,这一步需要我们的工程师具备丰富的经验和熟练的操作技能。
2.远程调试:利用先进的通信技术,对系统进行远程调试,提高调试效率。
3.数据分析:通过收集系统运行数据,进行数据分析,为调试提供依据。
六、调试注意事项1.安全第一:在调试过程中,要始终把安全放在第一位,严格遵守操作规程,确保人身和设备安全。
2.细致入微:调试过程中,要注重细节,对每个环节都要认真对待,确保调试效果。
某300MW机组脱硫装置电耗测试与节能优化

0 引 言
东北 地 区某发 电厂一期 1 、号2X 0 M 号 2 0 W机组 3 烟 气脱 硫 装 置 用石 灰 石 一 石膏 湿 法 脱硫 技 术 ,一 炉 一 “ 塔” 配置 , 设烟气换热器G H % G 及10 烟气旁路 , 0 脱硫效 率按不小于9 %设计 。 5 该脱硫装置主要由烟气系统、 吸 收塔 系 统 、石灰 石浆 液制 备 及输送 系 统 、石 膏脱 水 系 统、 废水 处 理 系 统 、 故 浆 液 系统 及 排 水坑 系统 、 事 工艺 水系统 、 压缩空气 系统等系统组成 。受电厂委托对 1 号
机 组 脱硫 装 置进 行 电耗测 试试 验 ,并 对该 装置 的 电耗 水 平 作 出分 析评 价及 节能 优化 建议 。
1 、号 机 组脱 硫 装 置包 括 烟 气 系统 、 G 号 2 G H系 统 、
吸收塔 系统 、 石灰 石 上料 系统 、 制浆 系统 、 脱水 系统 、 公 用 系统 等 。主要 耗 电设 备 有增 压风 机 、 液循 环泵 、 浆 湿
D : 1 . 6 /. S 2 9 — 4 92 1 . . 4 OI 03 9J S N. 5 3 2 . 20 0 9 I 0 0 4 0
中图分类号 : M6 17 T 2_ 文献标识码 : B 文章编号 :0 5 3 2 ( 0 0 — 0 - 4 29 — 4 92 1 4 0 1 0 2) 3
某3 0 Mw 机组脱硫 装置 电耗测试 与节能优化 0
王仁雷 姬海宏 张春融 柴 , , , 磊 宋广 田 ,
( 电 电 力科 学研 究 院 。 江 杭 州 3 0 3 ) 华 浙 1 0 0
摘 要 :对 某 电7 3 0 0 MW 机 组 脱 硫装 置进 行 了电耗 测试 试 验 , 分析 了系统 运行 存 在 的 问题 , 出 并 提 了节 能优 化 方案 , 实施 后 可 以起 到 比较 明显 的节能 降耗 效果 。 关键 词 :烟 气g  ̄ 电耗 ; 节 能 ; 优 化运 行 4L;
脱硫运行管理制度

脱硫系统运行治理制度一、脱硫系统投运率和脱硫效率掌握1. 脱硫系统投运率掌握。
(1)脱硫系统的检修工作进度应与主机同步,锅炉点火前,脱硫吸取塔系统和烟气系统应具备备用状态。
(2)机组并网,锅炉燃烧稳定,油枪退出运行,应马上将脱硫系统投入运行,尽早关闭脱硫旁路挡板。
(3)机组停运,油枪投入运行前,开启烟气旁路挡板,退出脱硫系统运行,尽量延长脱硫系统的运行时间。
(4)严禁开启烟气旁路挡板运行或严禁脱硫设施无故停运。
2.脱硫效率掌握。
(1)环保部门考核指标脱硫效率月均值≥98.5﹪,或净烟气 SO2 排放浓度<100mg/Nm3。
(2)我公司掌握脱硫效率班均值≥98.5﹪,或净烟气 SO2 排放浓度班均值<70mg/Nm3。
严格 SO2 分阶指标考核执行二、脱硫系统运行参数调整(一) 脱硫效率调整1.当脱硫效率低于98.5﹪时,应做如下处理。
(1)首先检查脱硫系统入口 SO2 浓度是否超过设计值,超过设计值应调整锅炉制粉系统不同煤种出力,降低 SO2 浓度至设计值,调整不成功汇报主管领导申请降负荷运行。
(2)脱硫系统入口 SO2 浓度未超过设计值,检查吸取塔浆液 pH 值是否在5.4~5.8,并通知化验人员手工测量吸取塔浆液 pH 与在线数据比照,假设 ph 较低,增加石灰石浆液的供给量,提高 pH。
(3)假设 ph 已接近 5.8,效率照旧低,检查吸取塔浆液密度是否在1110~1130kg/m3,密度较低,应停顿出石膏,增加石灰石浆液的供给量,密度较高,应尽快出石膏,降低吸取塔浆液密度。
(4)检查吸取塔浆液循环泵的运行台数,假设负荷较高或吸取塔入口 SO2 浓度较高,运行 3 台浆液循环泵。
(5)检查旁路挡板关闭是否严密,密封风机运行是否正常,否则通知检修处理。
(6)检查氧化风温度和压力、风量运行是否正常。
(7)脱硫系统运行参数和设备运行正常,通知热工人员检查烟气监测装置。
2.脱硫净烟气 SO2 浓度掌握(1)机组负荷较高或入炉煤硫份较高,应保证脱硫效率不低于 98.5﹪,或净烟气SO2 浓度不能高于100mg/Nm3。
- 1、下载文档前请自行甄别文档内容的完整性,平台不提供额外的编辑、内容补充、找答案等附加服务。
- 2、"仅部分预览"的文档,不可在线预览部分如存在完整性等问题,可反馈申请退款(可完整预览的文档不适用该条件!)。
- 3、如文档侵犯您的权益,请联系客服反馈,我们会尽快为您处理(人工客服工作时间:9:00-18:30)。
烟气脱硫系统节能优化措施
1背景
根据国家发展改革委、环境保护部等“关于印发《煤电节能减排升级
与改造行动计划(2014—2020年)》的通知”(发改能源[2014]2093号)中明确了燃煤电厂节能减排主要参考技术。
其中,针对现役机组节
能部分提出了脱硫系统运行优化,预计可以降低供电煤耗约0.5g/kWh。
本文主要对现有脱硫运行优化措施进行简单的描述。
2节约设备运行电耗
因为旋转设备较多,脱硫系统的厂用电率占整个机组运行电耗的1%以上,降低脱硫系统的运行电耗,可以有效的降低机组的运行费用。
在
脱硫系统中,浆液循环泵的电机功率约在1000kW左右、氧化风机的电
机功率约在600kW左右,石膏脱水系统中的真空泵的电机功率也超过200kW,均为高压电机(6kV或者10kV),想降低脱硫系统的运行成本,
必须有效降低高压大电机的运行电耗。
2.1引增合一改造目前新建机组均不在单独设置增压风机。
处于安全及经济性考虑,有增压风机的在役机组大多进行了引增合一改造,改
造增压风机后,针对600MW机组而言,可有效降低厂用电率0.05%以上。
2.2降低浆液循环泵的运行电耗(1)在现役机组进行脱硫系统改造时,有条件时可以通过对吸收塔的塔型进行优化,调整石灰石浆液的pH值、脱硫系统的钙硫比等数值,或者通过调整塔内的烟气流速参数,使浆
液循环泵的运行功率达到最低值。
如果设置烟气换热器后,吸收塔入
口的烟气温度会大大降低,烟气的体积流量也会随之降低。
在液气比
等参数不变的情况下,浆液循环泵的流量可以相对应的减少,泵的耗
电量可以随之降低。
(2)合理的选取系统的设计阻力,使浆液循环泵的
扬程降低,可以减少泵的耗电量。
例如适当加大浆液循环管的管径,
使系统的流速降低,一是可以在停泵时避免损坏滤网,同时又减少系
统的水力损失。
(3)根据机组的实际情况来调整泵的运行方式。
受上网
负荷及燃料来源的影响,大多机组的负荷率存有一定的波动范围,而且燃料的含硫量变化也较大。
此时,可以根据实际情况,在保证SO2排放浓度的前提下,适当减少浆液循环泵的运行数量,达到降低脱硫系统电耗的目的。
2.3降低真空泵的运行电耗根据设计规程,石膏脱水系统为两台机组公用设施,一般设置很多于2台真空皮带脱水机。
在设计时,可适当优化脱水系统的设备出力,使单台设备出力为2台机组设计工况的100%。
开启1套脱水设备,即可满足机组额定的运行要求。
同时通过加装浆液切换管道及石膏浆液分配器等措施来简化系统,降低真空泵的运行电耗。
2.4采取有效措施,降低烟气系统阻力综合考虑引增合一及加装烟气换热器等改造,可以优化脱硫系统的烟道布置,选取适当的烟道截面积来降低烟气流速;通过管线的合理优化设计,减少烟道弯头的数量,管道的长度等措施,甚至可以考虑采用圆烟道等,来降低烟气系统阻力,使系统阻力减少,可有效降低引风机的运行功耗。
2.5电机的变频改造受燃料的影响,锅炉的烟气量及烟气中SO2浓度会有一定的变化,此时,可将脱硫系统中部分低压的电机进行变频改造,以适当降低系统的运行电耗。
3节水
石灰石—石膏湿法脱硫工艺的用水量比较大,2台660MW等级机组脱硫系统的水耗量约在280t左右。
因此,如何降低脱硫系统的耗水量成为人们日益关注的课题。
根据脱硫系统水平衡的计算公式,工艺水量+烟气带入的水量=烟气带出的水量+石膏副产品带离系统的附着水和结晶水量+排放废水量。
引风机后的原烟气进入吸收塔是个放热的过程,而脱硫反应也是个放热过程,会将部分水分蒸发为水蒸气,虽然有除雾器进行除雾,但随着设备出力的下降及制造工艺本身的原因,一部分水汽会随着净烟气经烟囱排入大气。
因此,有效减少脱硫系统的放热,即可有效的降低脱硫系统的水耗。
在保证脱硫效率的前提下,脱
硫反应是不可能减少的,所以必须有效降低原烟气的放热,即降低原
烟气的温度。
目前国内的主要手段是在原烟道加装烟气换热器(低温省
煤器)或GGH(气-气换热器)。
根据目前掌握的资料来看,设置有GGH
的脱硫系统,300M和600MW机组的水耗分别会减少约25t/h和50t/h
左右。
但因为设置GGH会带来运行费用高,脱硫系统安全性降低等负
面影响,现有机组一般均不设或拆除GGH。
3.1加装烟气换热器烟气换热器布置在引风机出口的原烟道上,用烟气余热加热凝结水,对600MW机组而言,可将烟气温度从约135℃降低到90℃(具体工程应具体分析),加热的凝结水进入热力系统,减少了
加热器的用汽量。
经初步估计,机组的供电标煤耗可以降低约1g/kWh,单台机组可节水约50t/h,按年利用5000h、水价2元/t计,全厂全年可节水约50×104t、水费约100万元。
3.2回收冷凝液根据机组的实际运行工况,吸收塔出口的净烟气温度约在46℃左右,已经接近烟气中的水露点。
当净烟气流经净烟道和烟
囱时,温度会进一步的降低,烟气中的水蒸汽大多随烟气带出烟囱,
另外一部分会冷凝析出。
经初步估算,单台600MW机组烟囱冷凝液约
2.5t/h。
因此,建议净烟道有一定的倾斜角度,从而在烟囱内筒及入
口膨胀节低位处、净烟道的低位处设计液滴回收装置来回收冷凝液,
一是可以有效预防石膏雨的产生,同时可以降低脱硫系统的补水量。
3.3选用好的真空皮带机石灰石—石膏湿法脱硫系统的副产品是石膏,石膏中的是主要是石膏的结晶水和游离水。
而结晶水是石膏结晶必不
可少的重要的组成部分。
根据实际的运行情况,石膏晶体一般带有10%的游离水。
当石膏含水率超标时,应及时调整石膏脱水系统运行情况,优化真空皮带的脱水效率,有效的减少游离水的损失。
3.4冷却水及冲洗水的回收利用脱硫系统的冷却水一般采用开式水或闭式水。
如果采用闭式水,则会和主厂房闭式水系统统一考虑,脱硫
系统的闭式水一般会回主厂房回收利用。
如果采用开式水,一般脱硫
系统的冷却水会单独设置,可将该部分回水接至工艺水箱。
同时,未
利用完的机封冷却水也可接至工艺水箱。
目前的脱硫系统会设置集水
坑及集水泵,临时排放的浆液及设备的冲洗水排入集水坑,用集水泵达到吸收塔内循环利用,有效的节约用水。
3.5脱硫废水的治理措施目前,脱硫废水零排放的深度治理技术国内已经有电厂开始实施,不过造价较高。
国内主要有两种脱硫废水深度处理工艺,一是“预处理+正渗透MBC系统+结晶”工艺;二是“预处理+MVR蒸发+结晶”工艺。
4节约石灰石
石灰石耗量和石灰石的品质:石灰石品质的优劣决定着石灰石耗量的大小。
根据国内的运行经验,在购买石灰石时,石灰石中CaCO3的含量一般不应低于90%。
同时,通过优化浆液的pH值,合理选择钙硫比等措施可以直接影响脱硫效率。
一般而言,pH值越高,SO2向液膜主体扩散的速率越快,传质系数就越大,有利于促进SO2的吸收,但是容易造成浆液沉淀、堵塞系统。
同时,石膏中的CaCO3质量分数也越高,相对应增大了钙硫比,造成石灰石耗量的增加。
pH值越小,浆液酸性越强,酸性气体SO2就越难被吸收,造成脱硫率下降。
因此,确定合理的pH值控制范围就成为湿法脱硫系统工艺设计的关键所在。
5建议
现役机组通过脱硫系统运行优化及改造,可有效降低厂用电率,节约脱硫系统水耗,减少石灰石耗量等,预计可以降低供电煤耗约
0.5g/kWh,达到节能降耗的目的。
烟气脱硫系统节能优化措施。