实验十 金属材料的滚动摩擦磨损
摩擦磨损实验报告

摩擦磨损实验报告一、引言摩擦磨损实验是工程领域中常见的一种实验方法,通过模拟材料或器件表面的微观接触,研究摩擦过程中的磨损特性和机理。
本实验报告旨在对摩擦磨损实验的目的、原理、实验装置和结果进行全面、详细、完整且深入地探讨。
二、目的本实验的目的是通过设计和进行摩擦磨损实验,探究不同材料在不同工况下的磨损特性及其机理,为工程设计和材料选择提供理论依据。
三、原理摩擦磨损实验的原理基于摩擦学和材料科学的知识。
在实验中,通过施加一定的载荷和运动速度,使两个试样或试样与摩擦片之间发生摩擦接触。
在摩擦接触过程中,表面微观起伏、化学反应和热效应等因素共同作用,导致材料表面的磨损和形貌变化。
摩擦磨损实验可分为干摩擦和润滑摩擦两种情况。
在干摩擦实验中,试样之间没有润滑剂的存在,摩擦过程可能引起大量的磨粒生成和表面热量积累,导致试样表面的磨损。
而润滑摩擦实验则通过添加润滑剂,减少试样间的摩擦热和磨损程度。
四、实验装置进行摩擦磨损实验需要一套实验装置,包括:1.摩擦磨损试验机:用于施加载荷和控制运动速度,一般具有高精度和可控性能。
2.试样和摩擦片:选择不同材料的试样和摩擦片,根据实验需求确定形状、尺寸和表面处理方式。
3.测量仪器:包括摩擦力传感器、位移传感器、温度传感器等,用于实时监测试样的摩擦力、位移和温度等参数。
4.润滑剂:用于润滑摩擦接触表面,减少磨损程度和摩擦热。
五、实验过程本次实验的具体过程如下:1.准备试样和摩擦片:根据实验要求选择不同材料的试样和摩擦片,进行尺寸加工和表面处理。
2.调节实验参数:根据实验设计,设置载荷大小、运动速度和实验时间等参数。
3.安装试样和摩擦片:将试样和摩擦片固定在实验装置上,确保摩擦接触表面平整、清洁。
4.启动实验:运行实验装置,开始施加载荷和控制运动速度,记录实验过程中的数据和现象。
5.停止实验:根据实验时间或实验目标要求,停止实验运行,取下试样和摩擦片进行观察和分析。
6.数据处理:根据实验结果,进行数据处理和曲线拟合,得到摩擦力、位移和温度等参数的变化趋势。
摩擦磨损性能测试试验
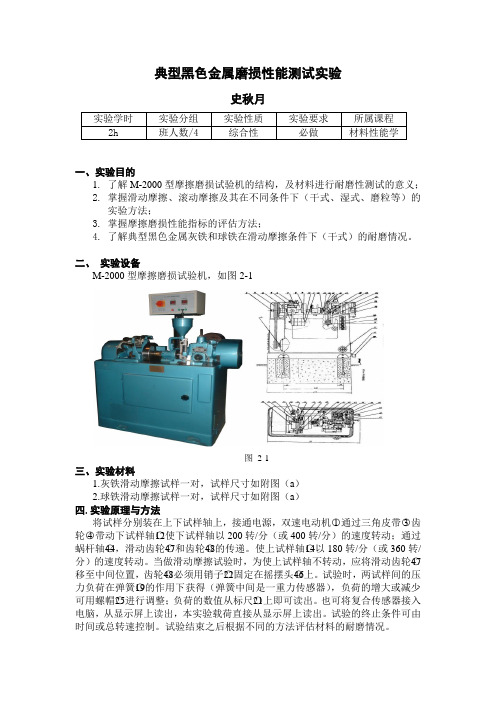
典型黑色金属磨损性能测试实验史秋月实验学时实验分组实验性质实验要求所属课程2h 班人数/4 综合性必做材料性能学一、实验目的1.了解M-2000型摩擦磨损试验机的结构,及材料进行耐磨性测试的意义;2.掌握滑动摩擦、滚动摩擦及其在不同条件下(干式、湿式、磨粒等)的实验方法;3.掌握摩擦磨损性能指标的评估方法;4.了解典型黑色金属灰铁和球铁在滑动摩擦条件下(干式)的耐磨情况。
二、实验设备M-2000型摩擦磨损试验机,如图2-1图2-1三、实验材料1.灰铁滑动摩擦试样一对,试样尺寸如附图(a)2.球铁滑动摩擦试样一对,试样尺寸如附图(a)四.实验原理与方法将试样分别装在上下试样轴上,接通电源,双速电动机○1通过三角皮带○3齿12使下试样轴以200转/分(或400转/分)的速度转动;通过轮○4带动下试样轴○48的传递。
使上试样轴○14以180转/分(或360转/47和齿轮○蜗杆轴○44,滑动齿轮○分)的速度转动。
当做滑动摩擦试验时,为使上试样轴不转动,应将滑动齿轮○47移至中间位置,齿轮○48必须用销子○22固定在摇摆头○46上。
试验时,两试样间的压力负荷在弹簧○19的作用下获得(弹簧中间是一重力传感器),负荷的增大或减少21上即可读出。
也可将复合传感器接入可用螺帽○25进行调整;负荷的数值从标尺○电脑,从显示屏上读出,本实验载荷直接从显示屏上读出。
试验的终止条件可由时间或总转速控制。
试验结束之后根据不同的方法评估材料的耐磨情况。
五、实验内容将加工好的滑动摩擦试样装在实验机上,在给定的条件下(干式、滑动摩擦、压力:200N、时间60min)进行试验,试验结束后将试样取下,评估耐磨性能。
根据所选取磨损试验方法的不同以及材料本质的差异,可以选择不同的耐磨性能评定方法,以期获得精确的试验数据,现简单例举下述几种方法以供参考。
1、称重法:采用试样在试验前后重量之差,本表示耐磨性能的方法,由于两试样之间的摩擦所引起的磨损量,可以采用精度达万分之一的分析天平称量出试样试验前后重量之差非凡获得。
摩擦磨损实验报告
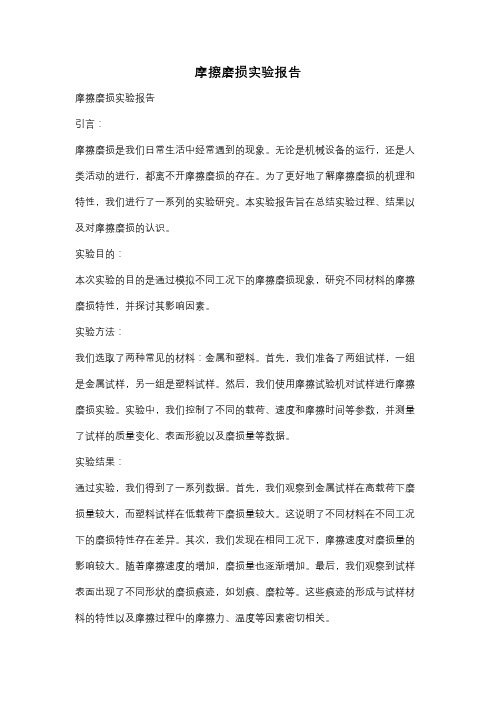
摩擦磨损实验报告摩擦磨损实验报告引言:摩擦磨损是我们日常生活中经常遇到的现象。
无论是机械设备的运行,还是人类活动的进行,都离不开摩擦磨损的存在。
为了更好地了解摩擦磨损的机理和特性,我们进行了一系列的实验研究。
本实验报告旨在总结实验过程、结果以及对摩擦磨损的认识。
实验目的:本次实验的目的是通过模拟不同工况下的摩擦磨损现象,研究不同材料的摩擦磨损特性,并探讨其影响因素。
实验方法:我们选取了两种常见的材料:金属和塑料。
首先,我们准备了两组试样,一组是金属试样,另一组是塑料试样。
然后,我们使用摩擦试验机对试样进行摩擦磨损实验。
实验中,我们控制了不同的载荷、速度和摩擦时间等参数,并测量了试样的质量变化、表面形貌以及磨损量等数据。
实验结果:通过实验,我们得到了一系列数据。
首先,我们观察到金属试样在高载荷下磨损量较大,而塑料试样在低载荷下磨损量较大。
这说明了不同材料在不同工况下的磨损特性存在差异。
其次,我们发现在相同工况下,摩擦速度对磨损量的影响较大。
随着摩擦速度的增加,磨损量也逐渐增加。
最后,我们观察到试样表面出现了不同形状的磨损痕迹,如划痕、磨粒等。
这些痕迹的形成与试样材料的特性以及摩擦过程中的摩擦力、温度等因素密切相关。
讨论与分析:通过对实验结果的分析,我们可以得出以下结论:1. 不同材料的摩擦磨损特性存在差异。
金属试样在高载荷下容易发生磨损,而塑料试样在低载荷下容易发生磨损。
这是由于金属材料的硬度较高,抗磨性较好,而塑料材料的硬度较低,抗磨性较差所致。
2. 摩擦速度对磨损量有明显影响。
摩擦速度越高,磨损量越大。
这是因为摩擦速度的增加会导致试样表面的摩擦热量增加,从而加剧了磨损现象。
3. 磨损痕迹的形成与多种因素有关。
试样材料的硬度、表面粗糙度以及摩擦过程中的温度、湿度等因素都会对磨损痕迹的形成产生影响。
结论:通过本次摩擦磨损实验,我们对摩擦磨损的机理和特性有了更深入的了解。
不同材料的摩擦磨损特性存在差异,摩擦速度对磨损量有明显影响,而磨损痕迹的形成与多种因素密切相关。
金属材料 磨损试验方法
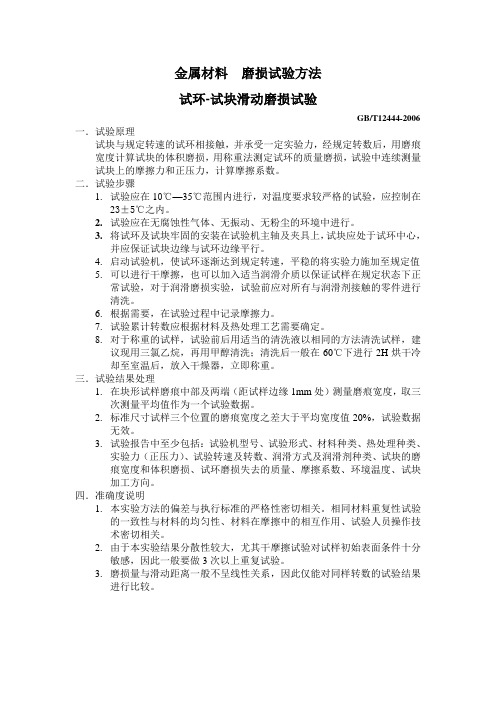
金属材料磨损试验方法试环-试块滑动磨损试验GB/T12444-2006 一.试验原理试块与规定转速的试环相接触,并承受一定实验力,经规定转数后,用磨痕宽度计算试块的体积磨损,用称重法测定试环的质量磨损,试验中连续测量试块上的摩擦力和正压力,计算摩擦系数。
二.试验步骤1.试验应在10℃—35℃范围内进行,对温度要求较严格的试验,应控制在23±5℃之内。
2.试验应在无腐蚀性气体、无振动、无粉尘的环境中进行。
3.将试环及试块牢固的安装在试验机主轴及夹具上,试块应处于试环中心,并应保证试块边缘与试环边缘平行。
4.启动试验机,使试环逐渐达到规定转速,平稳的将实验力施加至规定值5.可以进行干摩擦,也可以加入适当润滑介质以保证试样在规定状态下正常试验,对于润滑磨损实验,试验前应对所有与润滑剂接触的零件进行清洗。
6.根据需要,在试验过程中记录摩擦力。
7.试验累计转数应根据材料及热处理工艺需要确定。
8.对于称重的试样,试验前后用适当的清洗液以相同的方法清洗试样,建议现用三氯乙烷,再用甲醇清洗;清洗后一般在60℃下进行2H烘干冷却至室温后,放入干燥器,立即称重。
三.试验结果处理1.在块形试样磨痕中部及两端(距试样边缘1mm处)测量磨痕宽度,取三次测量平均值作为一个试验数据。
2.标准尺寸试样三个位置的磨痕宽度之差大于平均宽度值20%,试验数据无效。
3.试验报告中至少包括:试验机型号、试验形式、材料种类、热处理种类、实验力(正压力)、试验转速及转数、润滑方式及润滑剂种类、试块的磨痕宽度和体积磨损、试环磨损失去的质量、摩擦系数、环境温度、试块加工方向。
四.准确度说明1.本实验方法的偏差与执行标准的严格性密切相关。
相同材料重复性试验的一致性与材料的均匀性、材料在摩擦中的相互作用、试验人员操作技术密切相关。
2.由于本实验结果分散性较大,尤其干摩擦试验对试样初始表面条件十分敏感,因此一般要做3次以上重复试验。
3.磨损量与滑动距离一般不呈线性关系,因此仅能对同样转数的试验结果进行比较。
金属材料表面摩擦磨损机理研究

金属材料表面摩擦磨损机理研究一、引言金属材料是工业生产中使用广泛的材料之一,其表面的摩擦磨损问题影响着机械设备的性能和寿命。
因此,研究金属材料表面的摩擦磨损机理对于提高机械设备的可靠性有着重要意义。
本文将对金属材料表面摩擦磨损的机理研究进行梳理和总结。
二、金属材料表面摩擦磨损机理的分类1. 粘着磨损物体在摩擦过程中,由于接触表面产生的表面张力,导致物体表面产生差异形变, 造成损伤。
这种损伤形式我们称之为粘着(nowear)损伤.这种损伤是粒级以上(即微观尺度)表征摩擦过程的典型特征。
而微观尺度的磨损和水平方向的相互剪切是密切相关的。
当物体表面的粘着力越大,磨损越严重。
而硬度低, 表面粗糙度高的材料, 粘着损伤容易形成。
2. 疲劳磨损在应力循环的情况下,可能发生一系列的表面裂纹或者成为裂缝。
如果在这些裂纹处引入外力,就会使这些裂隙扩大甚至破裂,这种磨损形式我们称之为疲劳损伤。
疲劳磨损主要发生在金属材料经过重复循环或长时间的运动过程中,当材料表面应变过大或存在应力集中时,疲劳磨损很容易发生。
3. 磨粒磨损这种磨损模式的主要特征是物体表面明显存在磨损痕迹。
在物体表面经过长时间的运动过程中,很容易被杂质、粉尘、磨料等物质颗粒悬浮在介质中。
物质颗粒在物体表面上运动时,会产生表面切削,从而造成磨损。
磨粒磨损是金属材料摩擦磨损中最常见、最为普遍的一种机理。
三、金属材料表面摩擦磨损机理的原理1. 粘着磨损在两个金属物体的接触面上,会产生吸引力或剪切力,而这种力的大小与表面间的接触面积直接相关。
所以,当表面间的接触面积越大,粘着力越大,金属材料的表面粘着磨损越明显。
损伤的形式是由于表面接触部位接受高压力而形成的, 如盘状疲劳菲林(Fatigue Spalling)及磨耗铁锈(wear oxidation)等。
2. 疲劳磨损疲劳磨损的原理是由于物体表面裂纹处的应力集中效应,容易导致表面裂纹的形成和扩展。
在材料的裂纹阈值以下,材料表面裂纹会逐渐扩大和疲劳断裂,进而导致疲劳磨损。
滚动接触磨损疲劳试验

滚动接触磨损疲劳试验
滚动接触磨损疲劳试验是一种常见的材料磨损性能测试方法,用于评估材料在滚动接触条件下的耐久性能。
在这个试验中,我们将通过模拟实际使用条件下的滚动接触,对材料的磨损和疲劳性能进行评估。
我们需要明确滚动接触磨损疲劳试验的目的和意义。
这个试验是为了研究材料在滚动接触条件下的耐久性能,以便为工程设计和材料选择提供参考依据。
通过这个试验,我们可以了解材料在长期使用中的磨损情况,预测其使用寿命,并优化材料的设计和制造工艺。
在滚动接触磨损疲劳试验中,我们通常使用滚动接触磨损试验机进行测试。
这个试验机通过施加一定的载荷和转速,使试样在滚动接触下运动,模拟实际使用条件。
试样通常是圆柱形的,可以是金属、塑料或复合材料等。
在试验过程中,我们可以测量试样的磨损量、摩擦系数和疲劳寿命等参数。
滚动接触磨损疲劳试验的结果可以用于评估材料的耐磨性能和疲劳寿命。
通过对不同材料进行试验比较,我们可以选择最适合的材料,并优化设计和制造工艺,提高产品的使用寿命和可靠性。
需要注意的是,在进行滚动接触磨损疲劳试验时,我们需要考虑多个因素,如载荷、转速、润滑条件等。
这些因素会对试验结果产生影响,因此我们需要进行充分的实验设计和数据分析,以确保试验
结果的准确性和可靠性。
滚动接触磨损疲劳试验是一种重要的材料性能测试方法,可以评估材料在滚动接触条件下的耐久性能。
通过这个试验,我们可以了解材料的磨损情况和疲劳寿命,为工程设计和材料选择提供参考依据。
在进行试验时,我们需要考虑多个因素,并进行充分的实验设计和数据分析,以确保试验结果的准确性和可靠性。
金属的摩擦磨损实验
金属的摩擦磨损实验
金属的摩擦磨损实验是一种实验方法,用于研究金属材料在摩擦过程中的行为和性能。
该实验的目的是了解金属材料的摩擦系数、磨损率、耐久性以及在不同环境下的性能表现。
在金属的摩擦磨损实验中,通常采用滑动摩擦、滚动摩擦或冲击摩擦等实验条件,并采用各种摩擦磨损试验机进行测试。
根据实验要求,可以选择不同的试验机,如磨损试验机、往复摩擦试验机、滚动摩擦试验机等。
在实验过程中,需要测量金属材料的摩擦系数和磨损率。
摩擦系数是指材料在摩擦过程中所受的摩擦力与压力之比,反映了材料在摩擦过程中的润滑性能和耐磨性。
磨损率则是指材料在摩擦过程中损失的质量或体积与摩擦距离或时间的比值,反映了材料的耐久性和可靠性。
此外,在金属的摩擦磨损实验中,还需要考虑温度、湿度、载荷、速度等实验参数对金属材料性能的影响。
通过调整实验参数,可以研究金属材料在不同环境下的性能表现和变化规律,为材料的优化设计和改进提供依据。
总之,金属的摩擦磨损实验是一种重要的实验方法,可以帮助我们了解金属材料的性能和行为,为材料的优化设计和改进提供依据。
通过该实验,可以评估金属材料的耐磨性、耐久性和可靠性,为机械、汽车、航空航天等领域的工程应用提供技术支持。
磨损实验报告
磨损实验报告磨损实验报告摘要:本实验旨在研究不同材料在摩擦条件下的磨损情况,并探讨材料的磨损机理。
通过对不同材料的磨损实验,我们发现了磨损过程中的一些规律,为材料的选用和改进提供了实验依据。
引言:磨损是材料工程中一个重要的问题,它会导致材料的性能下降和寿命缩短。
因此,研究磨损机理对于材料的选用和改进具有重要意义。
本实验选取了几种常见的材料,通过模拟实际工况下的摩擦条件,观察其磨损情况,并分析磨损机理。
实验方法:1. 实验材料的准备:选取了铁、铜、铝和塑料等材料进行实验。
2. 实验装置的搭建:搭建了一个模拟摩擦的实验装置,包括一个转动的轴和一个与之接触的材料样品。
3. 实验过程:将材料样品与转动轴接触,并施加一定的压力和转速,模拟摩擦条件。
记录实验过程中的磨损情况和相关数据。
实验结果与分析:通过实验观察和数据记录,我们得出了以下结论:1. 不同材料的磨损情况存在明显差异。
铁材料在摩擦条件下磨损最为严重,而塑料材料的磨损相对较轻。
2. 磨损过程中,材料表面出现了磨痕和磨粒。
磨痕是由于材料表面的微小凸起与摩擦力的作用产生的,而磨粒是由于磨损过程中材料的剥落和破碎产生的。
3. 磨损过程中,材料的摩擦系数和磨损速率呈正相关关系。
摩擦系数越大,磨损速率也越大。
4. 磨损过程中,材料的硬度和韧性对磨损的影响较大。
硬度较高的材料更容易产生磨痕,而韧性较好的材料更容易产生磨粒。
结论:通过本实验,我们深入了解了不同材料在摩擦条件下的磨损情况,并探讨了磨损机理。
根据实验结果,我们可以得出以下结论:1. 在实际工程中,应根据具体工况选择合适的材料,以减少磨损带来的损失。
2. 在材料的设计和改进中,应注重提高材料的硬度和韧性,以增强其抗磨损能力。
3. 磨损实验是研究材料性能的重要手段之一,可以为材料的选用和改进提供实验依据。
展望:本实验只研究了几种常见材料的磨损情况,未来可以进一步扩大实验样本,研究更多材料的磨损性能。
同时,结合实际工程应用,可以通过改变摩擦条件和磨损环境,探索材料磨损的更多机理和规律,为材料的选用和改进提供更准确的指导。
金属材料滑动载流摩擦磨损测试方法
金属材料滑动载流摩擦磨损测试方法Test Method for Sliding Current-Carrying Friction and Wear of Metal目次目次 (I)前言 (II)1 范围 (1)2 规范性引用文件 (1)3 方法原理 (1)4 试样要求 (2)5 术语和定义 (2)5.1 接触压力 (2)5.2 线速度 (2)5.3 电流密度 (3)5.4 载流滑动距离 (3)5.5 平均载流摩擦系数 (3)5.6 载流摩擦系数波动性 (3)5.7 载流磨损率 (3)5.8 电流波动性 (4)5.9 燃弧率 (4)5.10 电弧能 (4)6 测试过程 (4)7 测试报告 (5)附录A (6)1金属材料滑动载流摩擦磨损测试方法1 范围本文件规定了金属材料的滑动载流摩擦磨损测试方法原理、试样要求、术语和定义、测试过程和测试报告。
本文件适用于金属材料滑动载流摩擦磨损的测试。
2 规范性引用文件下列文件对于本文件的应用是必不可少的。
凡是注日期的引用文件,仅注日期的版本适用于本文件。
凡是不注日期的引用文件,其最新版本(包括所有的修改单)适用于本文件。
GB/T 1031—2009 表面粗糙度参数及其数值GB/T 12444—2006 金属材料磨损试验方法试环-试块滑动磨损试验GB/T 17754—2012 摩擦学术语GB/T 2040—2008 铜及铜合金板材GB/T 3960—2016 塑料滑动摩擦磨损试验方法3 方法原理标引序号说明:1——旋转主轴2——盘试样3——销试样4——高速相机5——光敏元件6——卡具7——法向力传感器图1 测试方法原理12本文件测试方法采用滑动载流摩擦试验机,测试方法的基本原理见图1。
销试样装卡在导电卡具中,盘试样由旋转主轴驱动且两者绝缘,两个销试样和一个盘试样构成滑动载流摩擦副。
销试样和盘试样间的正压力由电液伺服阀和液压缸施加,实时动态法向力由法向力传感器测得。
摩擦磨损实验报告
摩擦磨损实验报告摩擦磨损是机械工程领域中非常重要的研究领域之一。
在工程实践中,物体之间的摩擦磨损现象经常发生,如机械零件在运动过程中的摩擦、轮胎与路面之间的摩擦等。
对摩擦磨损现象的深入研究和分析,可以为制造高品质的机械零件、提高机械传动效率、延长机械零件使用寿命提供基础和方向。
本实验采用球-盘式摩擦磨损试验机,对铜球和铜盘之间的摩擦磨损现象进行了研究。
通过测量铜球的质量变化和盘的重量损失,以及摩擦系数的变化,分析了摩擦磨损现象的特点和规律。
实验步骤1. 准备工作首先将球-盘摩擦试验机接通电源,打开加热器使得试验台的温度达到室温以上。
然后清洁试验台表面,将试验盘和铜球分别放置在试验台面上。
2. 实验操作打开摩擦试验机上的手动阀门,加入适量的机油到试验盘上,使其充分润滑。
然后将铜球放置在试验盘上,用扳手将附加的螺钉旋紧,使其固定在试验盘上。
接下来,打开摩擦试验机的电源,设定实验参数,如载荷大小、试验时间、旋转速率等,开始实验。
在实验过程中,通过计算器统计铜球经历的摩擦圈数,并及时记录实验数据。
3. 实验结束当实验时间达到设定时间后,关闭摩擦试验机的电源,停止试验。
然后将试验盘取下,用精密天平称量铜盘的重量,并计算铜盘的净重。
用精密天平称量铜球的质量,计算其在实验过程中的损失。
实验结果1. 铜球的磨损片断分析通过对摩擦试验机中铜球表面进行显微镜观察,可以看到铜球表面出现了明显的磨损痕迹,表现出不规则的形状和明显的划痕。
磨损片断的呈现表明了实验中铜球表面的摩擦磨损现象相当明显,在实验中出现了明显的摩擦现象。
2. 摩擦系数变化通过对球-盘式摩擦试验机的摩擦系数进行实时记录和卡片绘制,可以看到随着试验时间的延长,铜球与试验盘之间的摩擦系数逐渐变化,并表现出明显的上升趋势。
这说明,在实验中球-盘间的摩擦现象随时间的增加而加剧了。
通过测量实验过程中铜球质量的变化,可以看到铜球在实验过程中出现明显的损失。
在实验60min后,铜球的质量变化量达到了0.35g,这表明摩擦磨损现象相当明显,在实验过程中出现了明显的损耗现象。
- 1、下载文档前请自行甄别文档内容的完整性,平台不提供额外的编辑、内容补充、找答案等附加服务。
- 2、"仅部分预览"的文档,不可在线预览部分如存在完整性等问题,可反馈申请退款(可完整预览的文档不适用该条件!)。
- 3、如文档侵犯您的权益,请联系客服反馈,我们会尽快为您处理(人工客服工作时间:9:00-18:30)。
实验十金属材料滚动摩擦磨损
一、实验目的
1. 了解磨损试验机的结构及磨损试验方法
2. 掌握滚动摩擦磨损的步骤及方法
二、实验原理
各种滚动运动都可以视为以下三种基本滚动形式的组合,这三种滚动形式的表面作用和摩擦机理各不相同:
(1)自由滚动:圆柱体或球体沿着平面无约束地作直线滚动,这是最简单的滚动形式;
(2)具有牵引力的滚动:在接触区内同时受到法向载荷和切向牵引力的作用,例如摩擦轮传动;
(3)伴随滑动的滚动:当两个滚动体的几何形状造成接触面上的切向速度不相等时,滚动中必将伴随滑动,例如向心推力球轴承中球与滚道之间的滚动。
滚动摩擦机理显然与滑动摩擦不同。
除非接触面存在很大的滑动,滚动摩擦通常不存在犁沟效应,而粘着结点的剪切阻力也不是滚动摩擦的主要原因。
滚动摩擦阻力主要由以下四种因素组成:
(1)微观滑动:微观滑动是滚动过程中普遍存在的现象。
当两个弹性模量不同的物体作自由滚动时,由于接触表面产生不相等的切向位移,就将有微观滑动出现。
微观滑动所产生的摩擦阻力占滚动摩擦的较大部分,它的机理与滑动摩擦相同。
(2)塑性变形:在滚动过程中,当表面接触应力达到一定值时,首先在距表面一定深度处产生塑性变形。
随着载荷增加塑性变形区域扩大。
塑性变形消耗的能量表现为滚动摩擦阻力,可以根据弹塑性力学计算;
(3)弹性滞后:滚动过程中产生的弹性变形需要一定能量,而弹性变形能的主要部分在接触消除后得到回复,其中小部分消耗于材料的弹性滞后现象。
粘弹性材料的弹性滞后能量消耗远大于金属材料,它往往是滚动摩擦阻力的主要组成;
(4)粘着效应:滚动表面相互紧压形成的粘着结点在滚动中将沿垂直接触面的方向分离。
因为结点分离是受拉力作用,又没有结点面积扩大现象,所以粘着力很小,通常只占滚动摩擦阻力的很小部分。
1、耐磨性
耐磨性是材料抵抗磨损的性能,这是一个系统性质。
迄今为止,还没有一个统一的意义明确的耐磨性指标。
通常用磨损量来表示材料的耐磨性,磨损量越小,则材料的耐磨性越高。
磨损量即可用试样磨损表面法线方向的尺寸减少来表示,也可以用试样体积或质量损失来表示。
2、磨损机理
磨损后的形貌图和磨损后的XRD分析材料的磨损机理,对于探索提高材料的耐磨性方法具有重要的指导意义。
3、耐磨性的影响因素
磨损过程是一个非常复杂的过程,受到诸多因素的影响。
在实际过程中,一个或几个主要因素影响材料的耐磨性能;但随着摩擦磨损条件的改变,影响因素也在发生着变化。
下面分析几个主要的影响因素。
(1)材料的硬度:一般情况下,材料的硬度越高,其抗磨能力也越好(对于抗磨粒磨损能力尤为突出)。
(2)显微组织:材料的显微组织对耐磨性也有影响。
例如,对于钢中显微组织而言,马氏体耐磨性最好,铁素体耐磨性最差;在软基体中碳化物数量增加,弥散度增加,而耐磨性也提高,但在硬基体(基体与碳化物硬度接近)中,碳化物反而损害材料的耐磨性,因为此时碳化物如同内缺口一样,极易使裂纹扩展。
同时,碳化物的形状也对耐磨性有影响。
(3)晶粒尺寸:细化晶粒因为提高材料的屈服强度、硬度以及静载塑性,所以也能提高材料的耐磨性。
4、磨粒磨损
由外界硬质颗粒或硬表面的微峰在摩擦副对偶表面相对运动过程中引起表面擦伤与表面材料脱落的现象,称为磨粒磨损。
磨粒磨损性能采用被测试样磨损失重量进行评价。
在一定的试验条件下,磨损失重量越小,说明被测试耐磨粒磨损性能越好。
三、设备及试样
1. 磨损试验机(型号:MMS-2A)
2. 电子天平
3. 夹装工具
4. 试样
四、实验步骤
1. 设置磨损试验条件
2. 本试验的具体方法及步骤如下:
【测定不同载荷(10kg、50kg、100kg、150kg),不同速度时滑动摩擦的摩擦系数】(1)将滑动齿轮向右移到中间位置,并用螺钉紧固,同时将销子拔出
(2)调整螺钉,使弹簧芯杆在试样接触时离开弹簧芯杆座上平面2-3mm
(3)如做湿摩擦试验,应将油盒装于下试样下面,并在下试样轴上挂上链条,机器运转时,链条可自动将润滑剂带至摩擦表;也可在两试样的上方安装上油杯对试样进行润滑
(4)向下扳动摇摆头,调整螺母使上下试样表面相距约1-2mm,将试验力示值调整为零(5)确定试验速度,开车,将摩擦力矩示值调为零
(6)施加试验力,进行试验
五、实验报告要求
1
2、作图:试验力-时间-摩擦力矩
3、分析影响滚动摩擦测量结果的因素。