推荐-350万吨年常减压装置操作规程 精品
35万吨重整350万吨常减压工程施工组织设计_最终版

(此文档为word格式,下载后您可任意编辑修改!)35万吨重整350万吨常减压工程施工组织设计目录1、编制说明2、编制依据3、工程概况3.1工程性质3.2工程简介3.3工程特点3.4主要实物工程量3.5 工程条件4、施工进度计划及工期保证措施4.1施工总进度控制计划4.2施工网络图4.3施工部署4.4工期保证措施5、施工组织5.1项目管理机构5.2主要管理人员简历5.3现场主要技术人员简历5.4劳动力组织5.5计划投入的主要施工机械设备6、施工方法及主要施工技术措施A钢结构工程B工艺管道工程C设备安装工程D加热炉安装工程E筑炉工程F管道、设备保温工程G焊接工程H电气工程I仪表工程J冬季及夜间施工技术措施7、质量目标及保证措施7.1质量方针及目标7.2质量体系及组织机构7.3质量保证措施8、安全生产及文明施工保证措施8.1 安全生产方针目标8.2安全生产保证体系8.3安全及文明施工保证措施9、施工总平面布置9.1布置原则9.2临时设施9.3施工现场平面布置10、项目管理及项目控制10.1项目管理10.2进度控制10.3质量控制10.4技术管理10.5 材料控制11、工程分包与转包12、拟执行的标准规范一览表1、编制说明本组织设计针对****炼油厂350万吨年常减压装置改造工程而编制。
它包括了钢结构、加热炉、设备、工艺管道及给排水、电气、仪表各工程的拆除、改造、移位、安装、施工全过程的工作内容。
它是该工程施工的全面性技术文件。
该设计在编制当中充分的进行了调查研究,广泛地发动技术人员及工人的建议,使施工组织设计切合实际,达到指导施工的目的。
2、编制依据2.1 ****炼油厂****号招标文件;2.2 ****炼油厂350万吨年常减压装置(改造)施工图;2.3 与本工程有关的工程施工验收规范及相关标准。
3、工程概况3.1 工程性质该工程性质为技术改造扩建。
3.2 工程简介该工程位于****炼油厂一联合常减压装置原位置。
35万吨重整350万吨常减压工程施工组织设计

35万吨重整350万吨常减压工程施工组织设计一、项目概况本项目为建设一个年处理能力为35万吨的重整厂和一个年处理能力为350万吨的常减压工程。
二、施工组织机构1.总指挥部总指挥部负责项目的总体协调、决策和督导工作,并负责与业主进行沟通和协调。
2.项目管理部项目管理部负责施工项目的管理和协调工作,包括项目计划的编制和实施、资源的调配和协调、施工技术的指导和监督等。
3.施工现场指挥部施工现场指挥部负责具体的施工现场管理工作,包括施工队伍的组织和管理、设备材料的调配和管理、施工安全的监督和控制等。
4.施工队伍施工队伍根据项目需要组织施工作业,包括土建施工队、设备安装队、管道焊接队、电气安装队等。
三、施工工序及施工方法1.土建施工工序及施工方法(1)场地平整:采用机械平整和人工清理相结合的方式,确保施工现场的平整和清洁。
(2)基础施工:按照设计要求进行基坑开挖、基础桩基施工和混凝土浇筑。
(3)主体结构施工:采用钢结构,先进行钢梁和钢柱的安装,再进行屋面和墙体的安装。
(4)室内装修:进行室内地面、墙面的装修工作,包括瓷砖贴贴、墙面涂料施工等。
2.设备安装工序及施工方法(1)设备吊装:采用起重机进行设备吊装安装,确保设备的安全和稳定。
(2)设备固定:使用膨胀螺栓对设备进行固定,保证设备的稳定和牢固。
(3)设备接口连接:根据设备接口要求进行管道连接和电缆接线等。
(4)设备调试:对安装好的设备进行逐一调试,确保设备的正常运行。
3.管道焊接工序及施工方法(1)管道准备:对管道进行切割、修整和清洗等准备工作。
(2)管道焊接:采用手工氩弧焊进行焊接作业,保证焊接质量和焊缝无损害。
(3)管道测试:对焊接好的管道进行压力测试和气密性测试,确保管道的安全和正常使用。
4.电气安装工序及施工方法(1)电缆敷设:根据设计要求进行电缆敷设和布线工作。
(2)电气设备安装:对电气设备进行定位安装和接线工作。
(3)接地系统:进行接地电阻测试和接地系统的安装。
常减压操作规程

常减压装置操作规程目录概述:第一章本装置的工艺原理及生产数据-----------------------------------------------------第一节工艺原理---------------------------------------------------------------------------第二节生产数据---------------------------------------------------------------------------第二章工艺流程------------------------------------------------------------------------------ 附:工艺流程图、装置平面布置图、供排水图、精制、脱盐流程图第三章设备一览表------------------------------------------------------------------------------- 第一节塔------------------------------------------------------------------------------------- 第二节加热炉-------------------------------------------------------------------------------- 第三节容器----------------------------------------------------------------------------------- 第四节换热器、冷却器-------------------------------------------------------------------- 第五节机泵----------------------------------------------------------------------------------- 第六节安全阀-------------------------------------------------------------------------------- 第七节仪表量程及调节器的作用--------------------------------------------------------第四章开停工操作-------------------------------------------------------------------------- 第一节开工操作----------------------------------------------------------------------第二节停工操作----------------------------------------------------------------------------- 第三节装置开工中容易出现的事故及原因--------------------------------------------第五章岗位操作规程---------------------------------------------------------------------------- 第一节常压岗位操作法-------------------------------------------------------------------- 第二节减压岗位操作法------------------------------------------------------------------- 第三节加热炉岗位操作法----------------------------------------------------------------- 第四节司泵岗位操作法--------------------------------------------------------------------- 第五节精制岗位操作法--------------------------------------------------------------------- 第六节脱盐岗位操作法--------------------------------------------------------------------- 第六章事故处理--------------------------------------------------------------------------------第七章安全规程------------------------------------------------------------------------------------- 第一节冬季防冻凝规定--------------------------------------------------------------------- 第二节硫化氢安全知识---------------------------------------------------------------------- 第三节防火防爆规定-------------------------------------------------------------------------- 第四节检修操作及人身安全规定---------------------------------------------------------- 第八章环境保护规定-----------------------------------------------------------------------------概述第一章本装置的工艺原理及生产数据第一节工艺原理原油是一种由碳氢化合物组成的混合物,它们的沸点不同,常减压装置主要利用混合物的沸点差,把原油通过加热炉加热在精馏塔内产生汽化,精馏塔内在有回流的情况下,上升气体穿过塔板液相时,汽液两相进行热交换,汽体中的重组份被冷凝下来,留在塔板液相液体中,轻组份被上升气体加热后重新汽化,上升至上层塔板。
常减压装置岗位操作法

常减压装置岗位操作法第一节常压部分操作法一、操作特点和主要任务1、常压岗位的操作特点是:反应灵、变化快,对整个装置的平稳操作起主导作用,并掌控着主要的产品质量。
2、初馏塔的主要任务是脱除原油中所含的水分和部分轻组分,为常压操作打下基础,提高初馏塔的拔出率还能降低常炉热负荷,有利于提高处理能力。
3、常压塔的主要任务是根据原油性质及工艺要求,合理切割各种产品,努力提高操作水平,保证产品质量,稳定减压炉进料量及催化料性质,不断提高常压拔出率,有利于提高装置的总拔出率。
二、初馏塔操作法1、作用:初馏塔的作用在于预先蒸出原油中的水分和部分轻组分,塔顶馏出产品与常压塔顶汽油合并外送至汽油罐,减轻常压炉负荷。
2、原油含水大的影响(1)原油含水增大后,初馏塔的汽相负荷加剧使塔的操作压力增高,塔顶回流罐的水界位上升,同时塔底液位不稳,甚至冲塔。
(2)由于水在换热器中吸收热量后汽化,产生气阻使加工量提不上来,又使原油换热温度显著下降。
同时有可能由于换热温度低,水不能完全汽化而造成初底泵抽空,或增加了常压塔的负荷,严重时原油中的水不能从常压塔顶蒸发出来,引起常压操作事故发生。
(3)大量蒸发后的水蒸气,需要用常压塔系统的冷却器冷凝,增大了冷却系统的负荷。
冷不下来使回流量增多,逐步达到恶性循环,低压瓦斯增多,既浪费又不安全。
(4)原油含水量增大,使塔的进料温度降低,影响闪蒸效果,增加了常压炉的负荷。
3、处理方法:(1)联系调度和罐区,加强切水或换罐。
(2)降量,适当提高塔顶温度。
4、影响初馏塔底液位的因素(1)换热温度变化。
换热温度高,蒸发量增大,液面下降;反之,则上升。
液面变化要及时调节原油一、二路流量。
(2)原油含水变化及原油性质变化。
原油含水量大,液面下降。
(3)塔顶温度及塔顶压力变化。
顶度高,塔顶压力小,蒸发量大,液面下降,反之则上升。
(4)进料量或抽出量变化。
进料量大或抽出量少,液面上升,反之则下降。
(5)仪表失灵引起量的波动,从而引起液面波动。
常减压装置操作规程

安全操作规程编制人:***审核人:批准人:淄博汇丰石油化工有限公司常减压车间目录第一章装置工艺流程简述第一节装置简介 (3)第二节生产工艺流程 (4)第三节工艺操作指标 (8)第二章岗位操作法第一节常压岗位操作法 (9)第二节减压岗位操作法 (15)第三节机泵操作法 (19)第四节司炉岗位操作法 (21)第一章装置工艺流程简述第一节装置简介我厂常减压蒸馏装置是97年设计并当年投产达效,现己运行9周年。
该装置设计能力为8万吨/年,后经01、04两次改造,现生产能力为30吨/年,并在01年改造加设初馏塔及闪二塔,是典型的三段常减压蒸馏装置。
在2005年3月份改造中又将闪二塔去掉。
在2006年3月份改造将原常压塔换成新塔及附属常压气提塔及增加了部分冷换设备,对换热流程进行较大的改造。
2006年7月份新增加了原油电脱盐系统及附属设备,提高了装置安全运行系数。
目前,装置可运行多个加工方案,可根据原油的情况进行调整。
常减压的主要产品有直馏汽油、常柴、催化原料、减压渣油,并在原油合适的情况下可生产沥青。
第二节生产工艺流程一、原油加热:原油罐区将70℃的原油脱水后,用自然压力送入原油泵入口,原油经原油泵加压,经流量表累计计量后,进行换热。
原油经E101常顶循/原油换热器、E102减一线/原油换热器、E103 原油换热器/渣油Ⅳ、E104常二线 /原油换热器、E105混蜡Ⅱ/原油换热器、E106混蜡Ⅰ/原油换热器、E107常一中/原油换热器,进入电脱脱盐脱水后至E108 原油换热器/渣油Ⅲ、E109柴油/原油换热器、E110减二线∕原油换热器、E111减三线Ⅱ∕原油换热器、E112原油换热器∕渣油Ⅱ、E113减三线Ⅰ∕原油换热器、E114减四线Ⅰ∕原油换热器、E115原油换热器∕渣油Ⅰ换热至(210℃~270℃),进入闪蒸塔,闪顶油进常塔第14层塔盘或常顶汽油混合进EC101冷凝器,EC102冷却槽进入汽油回流罐。
常减压装置操作规程

减三及减二中(一)换热器
D-103
减顶油气分水罐
E-118/1.2
减渣(一)换热器
D-104
常顶瓦斯分液罐
E-119/1.2
一级排水二级电脱注水换热器
D-105/1.2
破乳剂配制罐
E-120/1.2
常顶空冷器
D-106
减顶瓦斯分液罐
E-121/1.2
常顶后冷器
D-108/1.2
缓蚀剂配制罐
设备位号
设备名称
设备位号
设备名称
C-101
闪蒸塔
E-112/1.2
常一中换热器
C-102
常压塔
E-113
常二中(二)换热器
C-103
常压汽提塔
E-114/1.2
减二及减一中换热器
C-104
减压塔
E-115
减渣(三)换热器
D-101/1.2
电脱盐罐
E-116/1.2
减渣(二)换热器
D-102
常顶产品回流罐
注缓蚀剂泵
P-111/1.2
减顶循及减一线油泵
P-120/1.2
燃料油泵
P-112/1.2
减一中及减二线油泵
P-121/1.2
真空泵
P-113/1.2
减二中及减三线油泵
P-123/1.2
二级电脱注水泵
P-124
隔离液装置
P-125
轻污油泵
D-128
燃料油罐
P-126/1.2
塔顶注水泵
第二章工艺流程
一、工艺流简述
(3)不停工冲洗,可定期排污;
(4)采用组合式电极板;
(5)设低液位开关,以保证装置操作安全;
常减压装置操作规程

常减压装置操作规程常减压装置操作规程1.安全要求1.1 操作人员必须通过相关培训,并具备使用常减压装置的资格和证书。
1.2 操作人员必须严格遵守安全操作规程,并牢记“安全第一”的原则。
1.3 操作人员必须熟悉常减压装置的结构、工作原理和操作步骤,并能够正确使用常减压装置。
1.4 操作人员必须穿戴个人防护装备,如安全帽、安全鞋、防护眼镜、防护手套等。
1.5 在操作过程中,必须保持机器周围的工作环境整洁,并清除可能导致危险的杂物和障碍物。
1.6 在操作过程中,必须注意机器的状态,及时发现并处理设备故障和异常情况。
2.操作流程2.1 准备工作2.1.1 在操作之前,必须检查常减压装置是否处于正常工作状态,包括检查是否有损坏或松动的零件,以及油液是否充足。
2.1.2 在操作之前,必须清理常减压装置及其周围的脏污和杂物,确保机器表面干净。
2.1.3 在操作之前,必须检查紧固部件是否牢固,并清理工作区域,避免杂物和障碍物。
2.2 操作步骤2.2.1 打开常减压装置的电源,确保电源连接正常。
2.2.2 根据需要调节常减压装置的工作压力和流量,确保输出压力和流量符合要求。
2.2.3 在操作之前,必须确认周围人员已远离常减压装置的工作区域,确保操作安全。
2.2.4 打开常减压装置的气源开关,使气体进入装置,同时打开输出阀门。
2.2.5 观察常减压装置的工作状态,确保其正常运行,如有异常情况必须立即停止操作并排除故障。
2.2.6 在操作过程中,必须保持专注,严禁随意触动机器的运动部件和控制部件,以免发生意外。
2.2.7 操作结束后,必须关闭常减压装置的气源开关,并关闭输出阀门。
2.3 维护保养2.3.1 在操作结束后,必须对常减压装置进行日常维护,包括清洁机器表面,清除灰尘和杂物。
2.3.2 定期检查常减压装置的工作状态,包括检查零部件的磨损程度,润滑系统的运行情况等。
2.3.3 如发现设备故障和异常情况,必须及时排除故障,并进行相应的维修和保养。
常减压装置年产350万吨计算
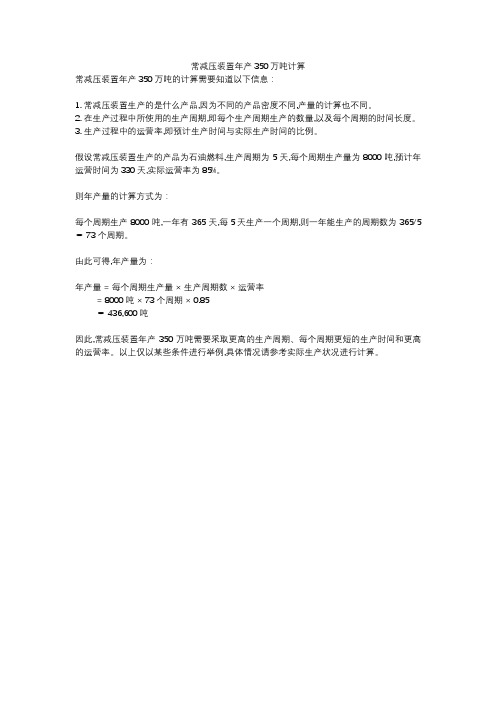
常减压装置年产350万吨计算
常减压装置年产350万吨的计算需要知道以下信息:
1. 常减压装置生产的是什么产品,因为不同的产品密度不同,产量的计算也不同。
2. 在生产过程中所使用的生产周期,即每个生产周期生产的数量,以及每个周期的时间长度。
3. 生产过程中的运营率,即预计生产时间与实际生产时间的比例。
假设常减压装置生产的产品为石油燃料,生产周期为5天,每个周期生产量为8000吨,预计年运营时间为330天,实际运营率为85%。
则年产量的计算方式为:
每个周期生产 8000 吨,一年有 365 天,每5天生产一个周期,则一年能生产的周期数为 365/5 ≈ 73 个周期。
由此可得,年产量为:
年产量 = 每个周期生产量× 生产周期数× 运营率
= 8000 吨× 73 个周期× 0.85
≈ 436,600 吨
因此,常减压装置年产 350 万吨需要采取更高的生产周期、每个周期更短的生产时间和更高的运营率。
以上仅以某些条件进行举例,具体情况请参考实际生产状况进行计算。
- 1、下载文档前请自行甄别文档内容的完整性,平台不提供额外的编辑、内容补充、找答案等附加服务。
- 2、"仅部分预览"的文档,不可在线预览部分如存在完整性等问题,可反馈申请退款(可完整预览的文档不适用该条件!)。
- 3、如文档侵犯您的权益,请联系客服反馈,我们会尽快为您处理(人工客服工作时间:9:00-18:30)。
版本:A 受控状态:NO.KSH/CJ—350万吨/年常减压装置操作规程编制:审核:批准:20XX-12-06发布20XX-12-06实施本规程由生产技术部组织相关单位依据本装置的具体情况及有关设计资料制定。
归口部门:生产技术部审核人:批准人:第一章装置简介 (1)第二章工艺流程说明 (2)第三章常减压装置岗位操作法第一节常压部分操作法 (8)第二节减压部分操作法 (14)第三节加热炉岗位操作法 (19)第四节司泵岗位操作法 (25)第五节电脱盐装置操作法 (31)第四章开工方案第一节常减压装置开工吹扫方案 (36)第二节减压装置单机试运、水冲洗、水联运方案 (39)第三节常减压装置设备及管线的贯通试压 (43)第四节常减压装置开工方案 (46)第五节电脱盐装置开工方案 (54)第五章岗位紧急事故处理方案第一节设备事故 (56)第二节操作事故 (61)第三节动力事故 (67)第六章岗位安全操作规程第一节安全规程 (71)第二节防冻凝规程 (72)第三节检修时的技术安全规程 (73)第四节一般安全知识 (74)第五节有关消防设备原理简介 (78)第一章装置简介350万吨/年常减压装置于20XX年12月31日开工投产,由中国石油天然气华东勘察设计研究院设计,中石化十公司施工,装置设计点规模为220×104t/a (设计弹性:上限250万吨/年,下限120万吨/年)。
本装置工艺设备的特点是:1、原油蒸馏采用三级蒸馏:初馏、常压蒸馏和减压蒸馏;2、初顶油气和常顶油气均与原油换热,回收低温位热量;3、原油电脱盐系统采用二级交直流电脱盐技术;4、应用先进的工艺模拟软件(ASPEN PLUS)对全装置进行模拟计算,优化操作条件;5、采用窄点技术(ASPEN PINCH)优化换热网络,在适当部位选用高效换热设备,提高换热强度;6、加热炉设空气预热系统,降低排烟温度,提高加热炉效率;7、初馏塔顶、常压塔顶和减压塔顶的馏出线上采取了注水、注中和缓蚀剂和缓蚀剂防腐措施;8、初馏塔、常压塔、汽提塔采用高效浮阀塔盘,减压塔采用全填料干式减压塔;9、采用DCS集散控制系统,并设紧急停车和安全连锁保护系统(ESD&SIS)。
第二章工艺流程说明一、原油换热及初馏部分原油经原油泵P1001 A-C升压进入装置后分为两路,一路与原油—初顶油气换热器E1001AB换热,然后经过原油—常顶循(II)换热器E1003、原油—减一及减一中换热器E1004、原油—常一中(II)换热器E1005AB、原油—常三线(II)换热器E1006AB,换热后温度升至134℃,与另一路换后原油合并进电脱盐罐V1001;另外一路与原油—常顶油气换热器E1002AB换热后,依次经过原油—常顶循(I)换热器E1007、原油—常一线换热器E1008、原油—常二线(II)换热器E1009、原油—减渣(V)换热器E1010A-C,温度升至138℃,与另一路合并。
合并后温度为136℃的原油至电脱盐。
脱盐后的原油分为两路,一路脱后原油分别经过E1011AB、E1012AB、E1013AB、E1014A-C、E1015AB,分别与减三线(II)、常二线(I)、常二中(II)、减渣(IV)、减二及减二中换热,温度升至240℃。
另一路脱后原油分别经过E1016、E1018、E1019AB、E1020A-C,分别与减二线、常一中(I)、减三线(I)、减三及减三中(II)换热,温度升至236℃,然后与从E1015AB 来的脱后原油合为一路进入初馏塔T1001。
初馏塔顶油气经过E1001AB,与原油换热后再经初顶油气空冷器Ec1001AB、后冷器E1041AB,冷凝冷却到40℃后,进入初馏塔顶回流罐V1002进行气液分离,V1002顶不凝气进入低压瓦斯罐,然后引至加热炉F1001燃烧。
初顶油进入初顶油泵P1002AB,升压后一路作为初馏塔顶回流返回到T1001顶部,另一路作为汽油馏分送至罐区(汽油)。
初馏塔底油经初底泵P1003AB抽出升压后分为两路,一路经初底油—减渣(III)换热器E1021A-D、初底油—常三线(I)换热器E1022、初底油—减三及减三中(I)换热器E1026A-C,换热至297℃;另一路经过初底油—常二中(I)换热器E1025A-C、初底油—减渣(II)换热器E1026A-D换热后温度升至291℃,二路混合后温度为294℃,进入初底油—减渣(I)换热器,温度升至311℃进常压炉F1001,经加热炉加热至369℃后,进入常压塔T1002进行分离。
二、常压蒸馏部分常顶油气106℃经原油—常顶油气换热器E1002AB换热至101℃,经常顶油气空冷器Ec1002A-F、常顶油气后冷器E1042AB换热至40℃后,进入常顶回流罐V1003,不凝气经低压瓦斯罐引至加热炉F1001,液相经常顶回流泵P1004AB升压后,一部分作为塔顶回流返回常压塔顶,另一部分作为汽油馏分送至罐区(汽油)。
常一线油自常压塔T1002第15层塔板自流入常一线油汽提塔,用过热蒸汽进行汽提,汽提后的气相返回常压塔T1002第13层板,液相由泵P1005AB 抽出,经原油—常一线换热器E1108换热器E1008换热至126℃,经常一线油—瓦斯换热器E1044、常一线油—热水换热器E1031AB、常一线水冷器E1043AB,冷至40℃后,送至罐区(轻柴)。
常二线自常压塔T1002第29层塔板自流入汽提塔T1003中段,用过热蒸汽气提,汽提后的气相返回常压塔T1002第27层塔板,液相由泵P1006AB抽出,经原油—常二线换热器(I)E1012、原油—常二线换热器E1032AB、常二线油空冷器Ec1003AB,冷至50℃后,送至罐区(轻柴)。
常三线自常压塔T1002第41层塔板自流入汽提塔T1003下段,用过热蒸汽气提,汽提后的气相返回常压塔T1002第39层塔板,液相由泵P1007AB 抽出,经初底油—常三线换热器(I)E1022、原油—常三线换热器(II)E1006AB换热至153℃后,再经常三线油—热水换热器E1033AB换热和常三线空冷器Ec1004AB冷至60℃后,送至罐区(蜡油)。
常顶循油自常压塔T1002第5层塔板由泵P1009AB抽出,经原油—常顶循换热器(I)E1007、原油—常顶循(II)E1003AB,换热至89℃后,返回常压塔顶。
常一中油自常压塔T1002第19层塔板由泵P1010AB抽出,经脱后原油—常一中换热器(I)E1018、原油—常一中换热器(II)E1005AB,换热至150℃后,返回常压塔第16层塔盘。
常二中油自常压塔T1002第33层塔板由泵P1012AB抽出,经初底油—常二中换热器(I)E1025A-C、脱后原油—常二中换热器(II)E1013AB,换热至202℃后,返回常压塔第30层塔盘。
常压渣油由泵P1012AB抽出,升压后分为两路,一路送至减压炉F1002加热至339℃后,送至减压塔进行分离;另一路经脱后原油—常渣换热器E1014 C、原油—常渣换热器E1010 C 换热后,再分为两路,一路去蜡油罐,一路经常渣—热水换热器E1037后送至燃料油罐。
三、减压部分减压塔为全填料干式减压塔。
减顶温度为75℃,残压为15mmHg。
减顶油气从减压塔顶出来后,经过增压器后进入减顶增压器EJ1001AB、空冷器Ec1008A-F冷凝冷却至38℃,凝缩油经大气腿流入减顶分水罐V1004;未凝气体经减顶一级抽空器EJ1002AB后,再经减顶一级空冷器Ec1007AB冷凝冷却至40℃,液相经大气腿流入减顶分水罐V1004,气相被减顶二级抽空器EJ1003AB抽出至减顶分水罐V1004,减顶分水罐内的减顶油经减顶油泵P1014AB升压后合并到减一线油出装置,气相至减顶瓦斯罐V1020,分液后引至减压炉F1002烧掉。
减一线油由减一及减一中油泵P1015AB自T1004第I段填料下集油箱抽出升压,经原油—减一及一中换热器E1004、减一及一中—热水换热器E1034AB换热后至减一线及一中空冷器EC1005冷却至50℃分为两路:一路作为回流打回T1004顶部,一路作为蜡油出装置。
减二线油由减二及减二中油泵P1016AB自T1004第III段填料下集油箱抽出升压,经脱后原油—减二及二中换热器E1015AB、减二及二中蒸汽发生器ER-1001,温度降为203℃分为两路:一路作为中段回流打回T1004,另一路经脱后原油—减二线换热器E1016后再分为两路,一路作为热进料至催化裂化装置,另一路经减二线—热水器换热器E1035AB冷至90℃后出装置。
减三线油由减三及减三中油泵P1017AB自T1004第IV段填料下集油箱抽出升压,经初底油—减三及三中(I)换热器E1023A-D、脱后原油—减三及减三中(II)换热器E1020A-C,换热至246℃分为两路:一路作为中段回流打回T1004,另一路经脱后原油-减三线(I)换热器E1019AB、脱后原油—减三线(II)换热器E1011AB后再分为两路,一路作为热进料至催化裂化装置,另一路经减三线—热水换热器E1036AB冷至90℃后出装置。
减压渣油由减压渣油泵P1019A-C抽出,经初底油—减渣(I)换热器E1027AB、初底油—减渣(II)换热器E1026A-D、初底油—减渣(III)换热器E1021A-D、脱后原油—减渣(IV)换热器E1014A-C、原油—减渣(V)换热器E1010A-C换热至156℃,作为焦化原料热进料至焦化装置。
四、司炉部分常压渣油由P1012AB抽出,经原油—常渣换热器E1014C、原油—常渣换热器E1010C、常渣—热水换热器E1037后,送至燃料油罐,经燃料油泵P1032AB后分为两路,一路进常压路,一路进减压炉。
高压瓦斯自催化来,经高压瓦斯罐U1010、常一线换热器E1044后,进两炉。
五、一脱三注部分净化水自装置外引入电脱盐注水罐V1006后,由电脱盐注水泵P1022AB 升压后经过电脱盐排水—注水换热器E1028AB换热至100℃后,注入二级电脱盐混合器前;二级电脱盐排水经泵P1021AB升压后注入一级电脱盐罐混合器前。
一级电脱盐罐排水经换热器E1028AB换热至70℃后再经电脱盐排水冷却器E1045冷却至50℃后出装置。
桶装破乳剂运至装置,用气动泵加入到破乳剂配置储罐中,用除盐水配成一定浓度的溶液,由注破乳剂泵P1024AB抽出,分别注入各级电脱盐罐入口混合阀前。
桶装中和剂运至装置,用气动泵加入到缓蚀剂配置储罐中,用除盐水配成一定浓度的溶液,由中和剂泵抽出,分别注入初馏塔、常压塔和减压塔顶气相馏出线上。
除盐水进入塔顶注水罐V1007AB,经塔顶注水泵P1023AB升压后注入到初馏塔、常压塔和减压塔顶气相馏出线上,多余部分排至污水管道。