光刻 ntd工艺
半导体光刻工艺流程
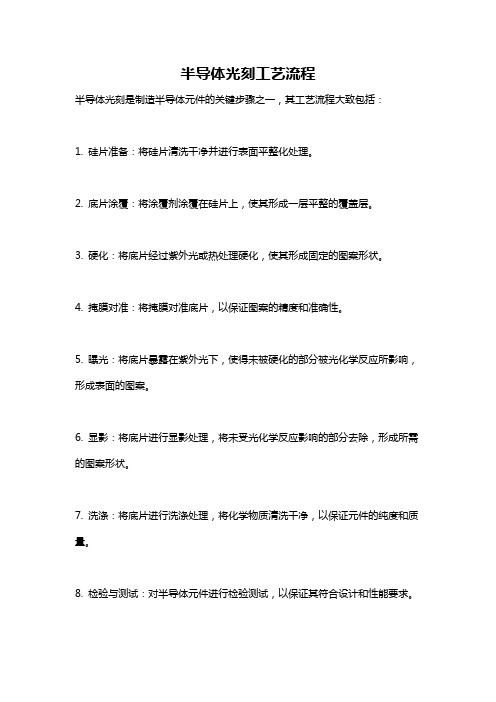
半导体光刻工艺流程
半导体光刻是制造半导体元件的关键步骤之一,其工艺流程大致包括:
1. 硅片准备:将硅片清洗干净并进行表面平整化处理。
2. 底片涂覆:将涂覆剂涂覆在硅片上,使其形成一层平整的覆盖层。
3. 硬化:将底片经过紫外光或热处理硬化,使其形成固定的图案形状。
4. 掩膜对准:将掩膜对准底片,以保证图案的精度和准确性。
5. 曝光:将底片暴露在紫外光下,使得未被硬化的部分被光化学反应所影响,形成表面的图案。
6. 显影:将底片进行显影处理,将未受光化学反应影响的部分去除,形成所需的图案形状。
7. 洗涤:将底片进行洗涤处理,将化学物质清洗干净,以保证元件的纯度和质量。
8. 检验与测试:对半导体元件进行检验测试,以保证其符合设计和性能要求。
整个工艺流程需要精密的仪器设备和复杂的程序控制,以确保半导体元件的高质量制造。
光刻工艺介绍

光刻工艺介绍一、定义与简介光刻是所有四个基本工艺中最关键的,也就是被称为大家熟知的photo,lithography,photomasking, masking, 或microlithography。
在晶圆的制造过程中,晶体三极管、二极管、电容、电阻和金属层的各种物理部件在晶圆表面或表层内构成,这些部件是预先做在一块或者数块光罩上,并且结合生成薄膜,通过光刻工艺过程,去除特定部分,最终在晶圆上保留特征图形的部分。
光刻其实就是高科技版本的照相术,只不过是在难以置信的微小尺寸下完成,现在先进的硅12英寸生产线已经做到22nm,我们这条线的目标6英寸砷化镓片上做到0.11um。
光刻生产的目标是根据电路设计的要求,生成尺寸精确的特征图形,并且在晶圆表面的位置正确且与其它部件的关联正确。
二、光刻工艺流程介绍光刻与照相类似,其工艺流程也类似:实际上,普通光刻工艺流程包括下面的流程:1)Substrate Pretreatment 即预处理,目的是改变晶圆表面的性质,使其能和光刻胶(PR)粘连牢固。
主要方法就是涂HMDS,在密闭腔体内晶圆下面加热到120℃,上面用喷入氮气加压的雾状HMDS,使得HMDS和晶圆表面的-OH健发生反应已除去水汽和亲水健结构,反应充分后在23℃冷板上降温。
该方法效果远比传统的热板加热除湿好。
2)Spin coat即旋转涂光刻胶,用旋转涂布法能提高光刻胶薄膜的均匀性与稳定性。
光刻胶中主要物质有树脂、溶剂、感光剂和其它添加剂,感光剂在光照下会迅速反应。
一般设备的稳定工作最高转速不超过4000rpm,而最好的工作转速在2000~3000rpm。
3)Soft Bake(Pre-bake)即软烘,目的是除去光刻胶中溶剂。
一般是在90℃的热板中完成。
4)Exposure即曝光,这也是光刻工艺中最为重要的一步,就是用紫外线把光罩上的图形成像到晶圆表面,从而把光罩上面的图形转移到晶圆表面上的光刻胶中。
光刻工艺步骤介绍

光刻工艺步骤介绍光刻工艺是半导体芯片制造中不可或缺的一步,其目的是将芯片设计图案转移到光刻胶上,然后通过化学腐蚀或蚀刻的方式将这些图案转移到芯片表层。
下面是一个光刻工艺的详细步骤介绍:1.准备工作:首先需要清洗芯片表面,以去除表面的杂质和污染物。
清洗可以使用化学溶液或离子束清洗仪等设备。
同时,需要准备好用于光刻的基板,这通常是由硅或其他半导体材料制成的。
2.底层涂覆:将光刻胶涂覆在基板表面,胶层的厚度通常在几微米到几十微米之间。
胶液通常是由聚合物和其他添加剂组成的,可以通过旋涂、喷涂或浸涂等方法进行涂覆。
3.烘烤和预烘烤:将涂覆好的光刻胶进行烘烤和预烘烤。
这一步的目的是除去胶液中的溶剂和挥发物,使胶层更加均匀和稳定。
烘烤的温度和时间可以根据不同的胶液和工艺要求来确定。
4.掩膜对位:将掩膜和基板进行对位。
掩膜是一个透明的玻璃或石英板,上面有芯片设计的图案。
对位过程可以通过显微镜或光刻机上的对位系统来进行。
5.曝光:将掩膜下的图案通过光源进行曝光。
光源通常是由紫外线灯或激光器组成的。
曝光时间和光照强度的选择是根据胶层的特性和所需的图案分辨率来确定的。
6.感光剂固化:曝光后,光刻胶中的感光剂会发生化学反应,使胶层中的暴露部分固化。
这一步被称为光刻胶的显影,可以通过浸泡在显影剂中或使用喷雾设备来进行。
7.显影:在光刻胶上进行显影,即移去显影剂无法固化的胶层。
显影的时间和温度可以根据胶层的特性和图案的要求来确定。
显影过程通常伴随着机械搅动或超声波搅拌,以帮助显影剂的渗透和清洗。
8.硬化:为了提高图案的耐久性和稳定性,可以对显影后的芯片进行硬化处理。
硬化可以通过烘烤、紫外线照射或热处理等方法来实现。
9.检查和修复:在完成光刻工艺后,需要对光刻图案进行检查。
如果发现图案存在缺陷或错误,可以使用激光修复系统或电子束工作站等设备进行修复。
10.后处理:最后,需要对光刻胶进行去除,以准备进行下一步的制造工艺。
去除光刻胶的方法可以采用化学溶剂、等离子体蚀刻或机械刮伤等。
光刻工艺步骤介绍

光刻工艺步骤介绍光刻工艺是一种重要的微电子制造技术,用于将电子芯片的图案转移至硅片上。
下面我将详细介绍光刻工艺的步骤。
第一步:准备硅片在光刻工艺开始之前,首先需要准备好硅片。
这包括清洗硅片表面以去除任何杂质,并在其表面形成一层薄的光刻胶。
光刻胶一般是由聚合物(如光刻胶),溶剂和添加剂组成的混合物。
第二步:涂覆光刻胶准备好的硅片放置在旋涂机上,然后将光刻胶涂覆在硅片表面。
旋涂机会以高速旋转硅片,使光刻胶均匀地覆盖在整个表面上。
涂覆的光刻胶会在硅片上形成一层均匀的薄膜。
第三步:预烘烤涂覆光刻胶后,硅片需要进行预烘烤。
预烘烤的目的是将光刻胶中的溶剂挥发掉,使光刻胶更加稳定。
预烘烤是在较低的温度下进行的,一般在90-100°C之间。
第四步:对准和曝光在对准和曝光步骤中,使用光刻机将芯片的图案转移到光刻胶层上。
首先,在光刻机的对准系统下,将硅片和图案的掩膜进行对准。
对准系统使用电子束或激光进行确切的对准。
一旦对准完成,光刻机会使用紫外线光源照射光刻胶。
光刻胶的激发使其发生化学反应,形成了曝光图案。
第五步:后烘烤曝光完成后,硅片需要进行后烘烤。
后烘烤的目的是将光刻胶中的曝光图案进行固化,并增强其耐久性。
后烘烤的温度和时间会根据光刻胶的类型和用途而有所不同。
第六步:显影显影是将曝光图案从光刻胶中暴露出来的步骤。
使用化学溶液将未曝光的光刻胶部分溶解掉,只留下曝光图案。
这一步骤在洗涤机中进行,确保均匀地清洗掉不需要的光刻胶部分。
第七步:清洗显影完成后,硅片需要通过化学溶液进行清洗,以去除任何剩余的光刻胶和杂质。
清洗过程往往需要使用多种溶液和机械清洗的步骤,以确保硅片表面干净。
第八步:测量和检验最后一步是对光刻结果进行测量和检验。
使用显微镜、扫描电子显微镜(SEM)等设备,检查光刻图案是否与设计要求相符。
测量和检验可以帮助确认制造过程中的任何错误或缺陷,以便及时进行修正。
光刻工艺简要流程介绍

光刻工艺简要流程介绍光刻工艺是半导体制造中非常重要的一个步骤,主要用于将芯片的电路图案传输至硅片上。
以下是光刻工艺的简要流程介绍。
1.准备工作在进行光刻之前,需要先对硅片进行一系列的准备工作。
包括清洁硅片表面、附着光刻胶、烘干等。
2.光刻胶涂布在准备完毕的硅片上,使用涂胶机将光刻胶均匀地涂布在硅片表面。
光刻胶是一种高分子有机聚合物,具有粘附性能。
3.预烘将涂布光刻胶的硅片放入预烘炉中,通过升温和恒温的方式,将光刻胶中的溶剂挥发,使得光刻胶中的聚合物形成薄膜,并在硅片表面形成一层均匀的保护膜。
4.掩模对位将预烘完毕的硅片和掩模放入对位仪中,在显微镜下进行精确对位。
掩模是一个透明的玻璃衬底上覆盖有芯片的图案。
5.紫外曝光将已对位好的硅片放入紫外曝光机中,打开紫外光源,光束通过掩模上的图案进行投射,将图案的细节库流到硅片上。
6.开发曝光完毕后,将硅片放入显影机中进行开发。
开发液会溶解掉曝光过程中没有暴露到光的光刻胶,显示出光刻胶图案。
7.软烘将开发完毕的硅片放入软烘炉中,通过温度升高将余留在硅片上的开发液挥发,使得光刻胶更加稳定。
8.硬烘将软烘完毕的硅片放入硬烘炉中,通过更高的温度和较长的时间,硬化光刻胶,使其具有更好的耐蚀性。
9.除胶将硬烘完毕的硅片放入去胶机中,用一定的化学液将光刻胶除去,还原出硅片表面的芯片图案。
10.检测和清洁除胶完毕后,需要对硅片进行检测,确保图案的质量和正确性。
之后进行清洁,除去可能残留在硅片上的任何污染物。
光刻工艺是半导体制造中至关重要的一步,其决定了芯片上电路图案的制备质量和精确度。
随着技术的不断进步,光刻工艺也不断改进,以适应更高的图案分辨率和更复杂的电路设计。
集成电路制造工艺总结

集成电路制造工艺总结学习了集成电路制造工艺的课程,了解和掌握了很多关于集成电路的设计与具体细节的知识,在此总结一下最近学习的情况和心得。
通过整体学习掌握了微电子工艺的初步理论知识和制作细节,所谓微电子工艺,就是指用半导体材料制作微电子产品的方法、原理、技术。
不同产品的制作工艺不同,但可将制作工艺分解为多个基本相同的小单元,再将不同的小单元按需要顺序排列组合来实现。
具体以一个最常用的芯片设计为例,首先将大自然中仅次于氧含量的硅做成硅棒,然后切片,再经过20到30步工艺步骤做成硅片然后再对做好的芯片进行测试,再经过封装成成品,完了再经过成品测试找出不符合标准的芯片,再包装到上市出售。
公司的联合创始人之一戈提出了一个很著名的论断:即“摩尔定律”,集成电路上能被集成的晶体管数目,将会以每18个月翻一番的速度稳定增长。
该论断到目前为之还在适用,但到以后会不会出现如此的情况就很难下定论,因为随着工艺的成熟,技术的进步,加工水平的提升,该速度会不会面临艰难的挑战也是一个谜。
在本次学习过程中,首先了解了硅作为集成电路的基础性材料,主要是由于它有一下几个特点:原料充分;硅晶体表面易于生长稳定的氧化层,这对于保护硅表面器件或电路的结构、性质很重要;重量轻,密度只有2.33g/cm3;热学特性好,线热膨胀系数小,2.510-6/℃,热导率高,1.50W/cm·℃;单晶圆片的缺陷少,直径大,工艺性能好;机械性能良好。
在掌握了硅的优点之后,熟悉了单晶硅的生长。
采用熔体生长法制备单晶硅棒:多晶硅→熔体硅→单晶硅棒;按制备时有无使用坩埚又分为两类:有坩埚的:直拉法、磁控直拉法;无坩埚的:悬浮区熔法。
单晶硅的生长原理为:固体状态下原子的排列方式有无规则排列的非晶态,也可以成为规则排列的晶体。
决定因素有三方面:物质的本质:原子以哪种方式结合使系统吉自由能更低。
温度高时原子活动能力强,排列紊乱能量低,而低温下按特定方式排列结合能高可降低其总能量----这是热力学的基本原则。
光刻工艺步骤介绍

光刻工艺步骤介绍光刻工艺是半导体工艺中关键的步骤之一,它用于制造各种微细结构,如晶体管、光栅、电容或电阻等。
光刻工艺具有高分辨率、高精度和高可重复性的特点,被广泛应用于微电子、光电子、光伏等领域。
下面将对光刻工艺的步骤进行详细介绍。
1.掩膜设计:在光刻工艺中,需要首先进行掩膜设计。
掩膜是一种光刻胶的图形模板,确定了最终要形成的微细结构的形状和位置。
掩膜设计常用计算机辅助设计软件进行,设计完成后生成掩膜模板。
2.光刻胶涂覆:在光刻工艺中,需要将光刻胶均匀涂覆在待制作器件表面,这是为了保护器件表面免受光刻过程中的腐蚀或损伤。
涂覆一般使用旋涂机或喷涂机进行,确保光刻胶均匀薄膜的形成。
3.预烘烤:涂覆光刻胶后,需要进行烘烤步骤来消除光刻胶中的溶剂,使光刻胶能够形成均匀的薄膜层。
预烘烤也有助于增加光刻胶的附着力和稳定性,并使其更容易与待制作器件表面结合。
4.曝光:曝光是光刻工艺的核心步骤,也是形成微细结构的关键。
在曝光过程中,掩膜模板被置于光源下,通过透过模板的局部区域将光刻胶暴露于紫外线或可见光源。
光刻胶对光线的敏感性使其在接受曝光后发生化学或物理变化,形成暴光区域。
曝光完毕后,去除掩膜模板。
5.显影:显影是指将曝光后的光刻胶通过溶液处理,使其在暴露区域溶解去除,形成所需的微细结构。
显影液对未曝光区域没有任何溶解作用,所以它只会溶解曝光区域中的光刻胶。
显影的时间和温度需要根据光刻胶的特性和所需结构来进行控制。
6.后烘烤:显影后的光刻胶需要进行后烘烤,以固化和增加其机械强度。
后烘烤可以通过烤箱、烘干机或者其他热源进行。
在烘干的过程中,通过将温度升高,光刻胶中的溶剂会完全挥发并交联,形成具有所需形状和特性的微细结构。
7.检查和测量:制作微细结构后,需要对其进行检查和测量,以确保其满足设计规格。
常见的检查和测量方法有光学显微镜、扫描电子显微镜和原子力显微镜等,这些设备可以对微细结构的尺寸、形状和位置等进行分析和评估。
tft 光刻工艺

tft 光刻工艺
TFT光刻工艺是指薄膜晶体管(Thin Film Transistor)的光刻制程。
薄膜晶体管是一种用于驱动液晶显示屏的关键元件,广泛应用于平板电视、电脑显示器等电子产品中。
TFT光刻工艺包括以下步骤:
1. 底片准备:选择适当的玻璃底片,经过清洗、去除杂质等处理,以获得干净的表面。
2. 掺杂:在底片表面用化学气相沉积或离子注入等方法向底片中注入特定的掺杂材料,以改变底片的电导性能。
3. 光刻胶涂布:在底片表面涂布一层光刻胶,通常使用光刻机进行涂布。
4. 曝光:使用光刻机将光刻胶曝光于紫外光下,通过掩膜将需要光刻的图形线路呈现在光刻胶上。
5. 显影:将曝光后的光刻胶在显影液中进行处理,使其未曝光部分溶解,形成光刻胶的图形模式。
6. 蚀刻:使用蚀刻机将未被光刻胶保护的区域进行物理或化学蚀刻,以去除底片上的材料,形成薄膜晶体管的结构。
7. 清洗:清洗底片以去除光刻胶和蚀刻过程中产生的残留物。
8. 检测与测试:对制程完成的底片进行检测和测试,确保制造的薄膜晶体管的质量和性能符合要求。
TFT光刻工艺的精细制程和高精度要求是实现高分辨率和高性能液晶显示屏的关键。
光刻技术的发展和进步在TFT制程中起着重要作用,能够制造出更小尺寸的图形线路,提高显示屏的分辨率和灵活性。
- 1、下载文档前请自行甄别文档内容的完整性,平台不提供额外的编辑、内容补充、找答案等附加服务。
- 2、"仅部分预览"的文档,不可在线预览部分如存在完整性等问题,可反馈申请退款(可完整预览的文档不适用该条件!)。
- 3、如文档侵犯您的权益,请联系客服反馈,我们会尽快为您处理(人工客服工作时间:9:00-18:30)。
光刻与NTD工艺:微电子制造中的关键步骤
一、引言
光刻与NTD(纳米晶体管技术)工艺是微电子制造中的两个关键步骤。
这些技术不仅影响微电子设备的性能和可靠性,而且也对其制造成本和生产效率产生深远影响。
本文将详细讨论这两个过程,强调它们在微电子制造中的重要性,并探讨其发展趋势和未来挑战。
二、光刻技术
光刻是半导体制造过程中的一个核心步骤,用于将电路图案从光刻板转移到硅片上。
这个过程需要使用光刻机,将光通过掩模照射在光敏材料上,形成所需的电路图案。
光刻技术的精度和效率对微电子设备的性能有着直接的影响。
随着微电子制造技术的发展,光刻技术也在不断进步,以适应更小线宽和更复杂的电路图案的需求。
例如,极紫外(EUV)光刻技术的出现,使得在7纳米及以下的工艺节点上进行制造成为可能。
然而,光刻技术也面临着一些挑战。
例如,随着线宽的减小,光的衍射效应变得更加明显,使得图案的转移更加困难。
此外,掩模的制作成本也在不断增加,这对微电子制造的成本产生了影响。
三、NTD工艺
NTD工艺是一种先进的晶体管技术,它利用纳米级别的晶体管来提高微电子设备的性能。
NTD工艺能够实现更小的晶体管尺寸,从而提高设备的运行速度和能效。
NTD工艺的实现需要使用先进的材料科学和纳米制造技术。
例如,高k金属栅极材料和鳍式场效应晶体管(FinFET)结构的使用,可以显著提高晶体管的性能。
此外,NTD工艺还需要精确的控制晶体管的掺杂和应力,以实现最佳的性能。
然而,NTD工艺也面临着一些挑战。
首先,随着晶体管尺寸的减小,量子效应变得更加明显,这可能对设备的性能产生负面影响。
其次,NTD工艺需要高精度的制造和测试设备,这增加了制造成本。
此外,随着微电子制造向更环保的方向发展,NTD工艺也需要考虑其对环境的影响。
四、光刻与NTD工艺的相互影响
光刻和NTD工艺在微电子制造中是相互影响的。
光刻技术的精度和效率直接影响到NTD工艺的实现。
如果光刻过程无法准确地将电路图案转移到硅片上,那么NTD工艺就无法制造出预期的晶体管结构。
同样地,NTD工艺的进步也对光刻技术提出了更高的要求。
例如,更小的晶体管尺寸需要更高精度的光刻技术来实现。
五、未来展望
随着微电子制造的持续发展,光刻和NTD工艺将继续面临挑战和机遇。
在光刻技术方面,EUV光刻技术有望在未来几年内成为主流技术,但同时也需要解决其成本高昂和生产效率低的问题。
在NTD工艺方面,随着晶体管尺寸的不断减小,新的材料和结构将被开发出来以维持设备的性能。
此外,随着人工智能、物联网等技术的快速发展,对高性能、低功耗的微电子设备的需求将不断增加,这将进一步推动光刻和NTD工艺的发展。
六、结论
总的来说,光刻和NTD工艺是微电子制造中的两个关键步骤。
它们的发展不仅对微电子设备的性能和可靠性产生深远影响,而且也决定了微电子制造的成本和生产效率。
随着微电子制造的持续发展,我们需要不断研究和改进这些技术,以适应未来的需求和挑战。