液力变矩器叶片设计
液力变矩器的叶片设计与研究_田国富

Algorithm for Text Segmentation and Its Application Based on Mean Shift
YANG Fuyuan , ZHOU Xiaodong
(School of Mechanical Engineering, Changchun University of Technology, Changchun 130012, China)
0
引
言
如图 1 所示, 直线 NMW、 N′M′W′分别为中间流线 M 和 M′处的法线, N 点和 W 点分别为外环和内环上的两个 点, N 点的坐标为 (ZN, RN ) RW ) 。根据 (ZW, , W 点的坐标为 液力变矩器循环圆的设计原则,设计时应保证循环圆各 处的过流面积相等。液力变矩器过流断面积 Fm=K · FD, 变 矩器的有效总面积 FD=πD2/4。所以 Fm=K · πD2/4,式中 K K=0.166~0.27, 对于圆形循环圆, K 的最佳值 为经验系数, 取 0.23。 M 点处椭圆的法线方程为 RM-RN = RN-RW = a · sinθ 。 ZM-ZN ZN-ZW b · cosθ
变矩器的性能。叶片设计采用的方法有三种: 基形设计、 统计设计及基于流场理论设计。前两种都是根据现有的液力变 矩器进行改进设计, 而基于流场理论的设计对于叶片理论方面的发展具有重要意义 。 文中基于 MATLAB 几何方式推导 循环圆及流线方程, 并据此对叶片进行设计研究。 液力变矩器; 关键词: 叶片设计; 循环圆
制造业信息化
MANUFACTURING INFORMATIZATION
仿真 / 建模 / CAD/ CAM/ CAE/ CAPP
液力变矩器的叶片设计与研究
液力变矩器结构设计_毕业论文

摘要液力变矩器具有的优良特性,自动适应性、无级变速、良好稳定的低速性能、减振隔振及无机械磨损等,是其它传动元件无可替代的。
历经百年的发展,液力变矩器的应用不断扩大,从汽车、工程机械到石油、化工、矿山、冶金机械等领域都得到了广泛的应用。
本文主要介绍了CL315液力变矩器的结构设计,结构的设计主要是指变矩器的循环圆设计、叶片设计、特性计算、整体结构设计以及一些关键零部件的设计,由于叶片参数直接影响到变矩器的性能,因而是液力变矩器的设计的关键是叶片设计,叶片设计的方法有很多,本次叶片设计采用的是环量分配法。
关键词:液力变矩器叶片设计环量分配法目录摘要 (I)第1章绪论 (1)1.1液力变矩器综述 (1)1.2液力变矩器的国内外研究现状 (1)1.3液力变矩器设计方法研究进展 (2)1.4本课题研究的意义目的 (3)第2章液力变矩器的基本知识 (5)2.1液力变矩器的构造 (5)2.2液力变矩器的工作原理 (6)2.3液力变矩器中循环流量的确定 (7)2.3.1通流损失 (7)2.3.2冲击损失 (8)2.4液力变矩器几何参数的计算 (11)2.4.1计算工作轮特性参数和几何参数的关系 (11)第3章液力变矩器结构设计 (13)3.1设计方法 (13)3.2循环圆的确定 (15)3.3叶片的设计 (17)3.3.1泵轮叶片的设计 (17)3.3.2涡轮叶片设计 (21)3.3.3导轮叶片设计 (24)结论 (26)参考文献 (27)致谢 (28)第1章绪论1.1液力变矩器综述液力变矩器是以液体为工作介质的一种非刚性扭矩变换器,是液力传动的型式之一。
液力变矩器具有的优良特性,自动适应性、无级变速、良好稳定的低速性能、减振隔振及无机械磨损等,是其它传动元件无可替代的。
历经百年的发展,液力变矩器的应用不断扩大,从汽车、工程机械到石油、化工、矿山、冶金机械等领域都得到了广泛的应用。
液力变矩器的流场理论、设计和制造、实验等研究工作,近年来,也得到了突飞猛进的发展。
(三)液力变矩器涡轮叶片二维平面设计
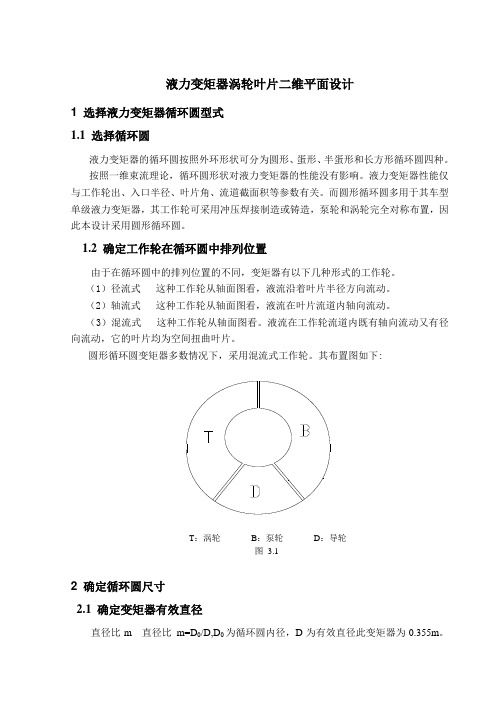
液力变矩器涡轮叶片二维平面设计1 选择液力变矩器循环圆型式1.1 选择循环圆液力变矩器的循环圆按照外环形状可分为圆形、蛋形、半蛋形和长方形循环圆四种。
按照一维束流理论,循环圆形状对液力变矩器的性能没有影响。
液力变矩器性能仅与工作轮出、入口半径、叶片角、流道截面积等参数有关。
而圆形循环圆多用于其车型单级液力变矩器,其工作轮可采用冲压焊接制造或铸造,泵轮和涡轮完全对称布置,因此本设计采用圆形循环圆。
1.2 确定工作轮在循环圆中排列位置由于在循环圆中的排列位置的不同,变矩器有以下几种形式的工作轮。
(1)径流式这种工作轮从轴面图看,液流沿着叶片半径方向流动。
(2)轴流式这种工作轮从轴面图看,液流在叶片流道内轴向流动。
(3)混流式这种工作轮从轴面图看。
液流在工作轮流道内既有轴向流动又有径向流动,它的叶片均为空间扭曲叶片。
圆形循环圆变矩器多数情况下,采用混流式工作轮。
其布置图如下:T:涡轮B:泵轮D:导轮图3.12 确定循环圆尺寸2.1 确定变矩器有效直径直径比m 直径比m=D0/D,D0为循环圆内径,D为有效直径此变矩器为0.355m。
一般m=0.38即m=D0/0.355=0.38 (3.1)即D0=0.1349所以循环圆外环半径为:R1=(D-D0)/4 (3.2)=(0.355-0.1183)/4=0.0552.2 确定循环圆形状尺寸已知外环后,开始确定内环、设计流线。
确定内环、设计流线的原则是使液流速度沿流道均匀变化。
为此假定在同一过流断面上各点的轴面速度Vm相等,各相邻流线所形成的过流面积相等。
根据最佳过流面积为循环圆面积的23%的原则,对于有效直径为355mm的变矩器,其最佳过流面积为0.02276m2。
1)循环圆初步设计首先设定一些元线如下图,为方便计算,从上面正垂直的元线开始,递增角度为15°,根据在任意元线上的过流面积F为:F=(Rs2-Rc2)∏/cosθ(3.3)式中θ为元线相对垂直线的夹角,所有元线均垂直设计流线Rs 为任一元线与外环交点上的半径Rc 为同一元线与内环交点上的半径R2 为同一元线与设计流线交点上的半径其次,选定一些任意的元线,并算出内环和设计流线的初步轮廓。
现代设计方法在液力变矩器叶片设计中的

现代设计方法在液力变矩器叶片设计中的应用研究许睿(鼎盛天工工程机械股份有限公司,天津 300384)摘要:本文从实际生产需要出发,提出了一种液力变矩器叶片的现代设计方法。
该方法有机结合了修正能头损失的束流理论、叶片的三维成型法以及流场数值模拟技术,大大提高了叶片的设计精度和设计效率。
关键词:现代设计方法;叶片设计;数值模拟中图分类号:文章标识码:文章编号:Research on the Applications of Modern Design Method in the blades design ofTorque ConverterXU Rui(DINGSHENG TIANGONG CONSTRUCTION MACHINERY CO., LTD., Tianjin 300384, China) Abstract: According to the practical requirements of production, a kind of modern design method for blade system of torque converter is raised in this paper. It combines the beam current theory which amends head loss, three-dimension formation method and the technology of numerical stimulation of flow field, which can improve the accuracy and efficiency of blade design greatly.Key Word: Modern Design; Blade design; Numerical simulation1 引言在CAD、CFD技术高速发展的今天,现代设计方法正逐步代替传统设计方法成为液力变矩器设计的主要方法[1]。
基于环量分配法的某型号液力变矩器叶片设计
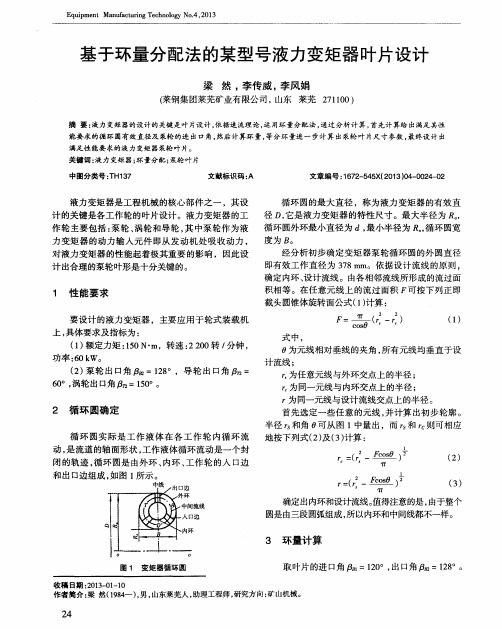
2 循环 圆确 定
首先选定一些任 意的元线 , 并计算 出初步轮廓 。 半径 r s 和角 0 可 从 图 1中量 出 ,而 r s 和r c 则 可 相应 循 环 圆实 际是工作 液体 在各工 作轮 内循环 流 地按 下列 式 ( 2 ) 及( 3 ) 计算 : 动, 是流道 的轴面形状 , 工作液体循环流动是一个封 ( r 一— F c o — s 0) ( 2 ) 闭 的轨 迹 , 循环 圆是 由外 环 、 内环 、 工 作 轮 的人 口边
( 5 ) 、 ( 6 ) 计算 出 r :
一
叶形坐标 。 利用 内外环半径和偏移量 , 依据公式( 1 O ) 叶片元线上 的偏移量 , 相邻两点间的弧长公式( 1 1 ) , 可以方便并精准的确定叶片形状 。
X , k=r k s i n ( y+
上
,
∞ ±
、 / ( ∞ ) + 一 4 ( G 2 c o r m - r m ,  ̄ , l f m ) T s
F=
C OS U
( 一 )
u _
( 1 )
上, 具体要求及指标为 : 式中, ( 1 ) 额定力矩 : 1 5 0 N・ m,转速 : 2 2 0 0 转/ 分钟 , 0为元 线 相对 垂线 的夹 角 , 所有 元线 均 垂 直 于设 功率 : 6 0 k W。 计 流线 ; ( 2 ) 泵 轮 出 口角 =1 2 8 。,导 轮 出 口角 / 3 = 为任意 元线 与外 环 交 点上 的半径 ;
E q u i p me n t Ma n u f a c t u r i n g T e c h n o l o g y No . 4, 2 0 1 3
液力变矩器叶片参数的正交试验优化设计
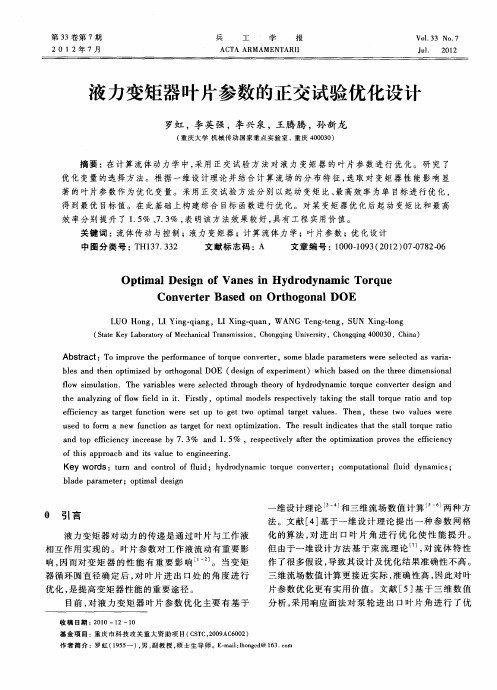
LUO o g,L n — a g, L n - u n,W ANG n —e g,S H n IYi g qin IXi g q a Te g t n UN n -o g Xi g ln
( tt Ke a oaoyo c a ia T a s sin,C o g igU iest,C o g ig4 0 3 Sae yL b rtr f Me h nc l rnmi o s h n qn nv ri y h n qn 0 0 0,C ia hn )
Key wor ds:t r n o to ffu d; h d o y a c o q e c n et r o utto a u d y a c ; u n a d c n r lo i l y r d n mi tr u o v re ;c mp a in lf i d n mi s l
A b tac :To i p o e t epef r a c ftr u o v re sr t m r v h rom n eo o q e c n etr,s me b a e p rm ee swe e s l ce sv ra o ld a a t r r ee t d a a i—
液力变矩器叶片厚度及冲角适配减速带捕能装置

doi:10.3969/j.issn.1009-3230.2021.03.001液力变矩器叶片厚度及冲角适配减速带捕能装置罗㊀政ꎬ薛松杰ꎬ葛传洁(华北电力大学动力工程系ꎬ保定071003)摘㊀要:液力变距器是广泛运用在传动系统中的一种液力设备ꎬ其结构参数如叶片厚度㊁叶片冲角等直接影响其传动工作效率ꎮ基于国内外研究现状ꎬ在参考大部分减速带能量捕获装置模型和运行参数的前提下ꎬ建立液力变矩器涡轮㊁泵轮㊁导轮的单通道模型ꎮ采用ANSYS-CFX对液力变矩器内液体流动进行仿真ꎬ分析了泵轮叶片厚度㊁涡轮叶片厚度对于泵轮㊁涡轮输出转矩的影响ꎮ研究表明:两种叶片厚度对于输出转矩有着明显的影响ꎬ总体呈下降趋势ꎬ且对泵轮和涡轮输出转矩分为两个阶段ꎬ两个阶段的平均变化率分别为2 8%和3 4%ꎮ两者对于输出转矩的影响有着交互效应ꎬ而并非孤立ꎮ研究结果可以为液力变矩器适配在其他液压传动装置上提供参考ꎮ关键词:液力变矩器ꎻ泵轮ꎻ涡轮ꎻ输出转矩中图分类号:TK414 4㊀㊀文献标志码:A㊀㊀文章编号:1009-3230(2021)03-0001-05HydraulicTorqueConverterBladeThicknessandAngleofAttackAdaptedtoSpeed-reductionBeltEnergyHarvestingDeviceLUOZhengꎬXUESong-jieꎬGEChuan-jie(DepartmentofPowerEngineeringꎬNorthChinaElectricPowerUniversityꎬBaoding071003ꎬChina)Abstract:Thehydraulicpitchchangerisakindofhydraulicequipmentwidelyusedinthetransmissionsystem.Itsstructuralparameterssuchasbladethicknessandbladeattackangledirectlyaffectitstransmissionefficiency.Basedonthecurrentresearchstatusathomeandabroadꎬandonthepremiseofreferringtomostmodelsandparametersofenergycapturedevicesforspeedbumpsꎬasingle-channelmodeloftorqueconverterturbineꎬpumpwheelandguidewheelisestablished.UseANSYS-CFXtosimulatetheliquidflowinthetorqueconverter.Theinfluenceofthethicknessoftheimpellerbladeandthethicknessoftheturbinebladeontheoutputtorqueoftheimpellerandturbineisanalyzed.Researchshowsthatthetwobladethicknesseshaveasignificantimpactontheoutputtorqueꎬandtheoveralltrendisdownward.Theaveragechangerateofthetwostagesofthepumpwheelandturbineoutputtorqueis2.8%and3.4%ꎬrespectively.Thetwohaveaninteractiveeffectontheoutputtorqueꎬnotinisolation.Theresearchresultscanprovidereferencesforadaptingthetorqueconvertertootherhydraulictransmissiondevices.Keywords:hydraulictorqueconverterꎻpumpwheelꎻturbineꎻoutputtorque0㊀引㊀言收稿日期:2021-01-22㊀㊀修订日期:2021-02-24基金项目:河北省大学生创新创业训练项目(S2020100 ̄79016)作者简介:罗㊀政(2000-)ꎬ男ꎬ本科生ꎬ研究方向为动力机械ꎮ随着人类社会和科学技术的不断发展ꎬ 能源危机 逐渐成为限制人类社会的主要问题ꎮ而在这样的环境大背景下ꎬ不断寻找新的可替代能源和减少能量消耗成为社会应对能源危机的主旋律ꎮ为此ꎬ用来使汽车减速的减速带受到了人们的关注ꎮ城市路口㊁高速路口集中分布了许多的减速带ꎬ如果能将减速带损失的这一部分能量加以利用ꎬ也是对捕获能量的一种新的想法ꎮ而液力变矩器作为一种液压传动装置和减速带能量捕获装置组合的适配也就成为了一个问题ꎮ针对以上问题国内外学者做了以下研究ꎮ刘迪在液力变矩器循环圆直径不变的情况下ꎬ通过优化泵轮叶片形状ꎬ增加泵轮出口叶片角ꎬ增加泵轮力矩系数的办法ꎬ使液力变矩器在低速比时具有高效率的性质[1]ꎻ刘安然对长短叶片泵轮对外特性的影响进行研究ꎬ发现长短叶片泵轮对外特性的改善起到积极作用ꎬ在转速比在0.519~0.692之间效率值增加1.31%~2.72%ꎬ启动工况变矩比k由3 91提高到4.1[2]ꎻ罗准等对具体的减速带装置和双液压缸式换能器进行了建模ꎬ利用Amesim进行数值计算ꎬ建立了气缸内径㊁储能器气体体积等参数与减速带弹簧刚度等参数的关系[3]ꎻDar ̄rellRobinette针对液力变矩器对于汽车运行的适配性做了研究ꎬ对三个具有近似精确几何相似度的变矩器进行了尺寸分析ꎬ以显示相关性在预测整体外部对流换热机制中的适用性[4]ꎮ总体而言ꎬ对于减速带建模ꎬ液力变矩器建模和数值模拟的研究已经相对成熟ꎬ但对于液力变矩器和减速带的适配问题的研究还不多见ꎮ文中通过对液力变矩器进行建模分析ꎬ研究变矩器叶片厚度对常见减速带能量捕获装置的适配性ꎬ并利用模拟退火算法ꎬ寻求最优解ꎮ研究结果可为液力变矩器使用在其他领域的适配问题提供参考ꎮ1㊀模型建立及实验工况设置国内外对于液力变矩器的叶片厚度㊁冲角适配的研究并不多见ꎬ文中以等叶片厚度的冲焊型液力变矩器为研究对象ꎬ采用ANSYS-CFX软件对本问题进行数值模拟ꎬ研究叶片厚度㊁叶片冲角对于变矩器工作性能的影响ꎮ试验因素为泵轮叶片厚度㊁涡轮叶片厚度㊁各叶片冲角ꎬ参考某冲焊型液力变矩器相关参数[5]ꎬ设置具体实验变量(见表1ꎬ表2)ꎮTp为泵轮叶片厚度ꎬTt为涡轮叶片厚度ꎬαP为泵轮叶片冲角ꎬαT为涡轮叶片冲角ꎬαS为导轮叶片冲角ꎮ由于试验中的因素个数较少ꎬ所以采用全因素试验方法ꎬ评估所有因素在所有水平上的可能组合ꎮ㊀表1冲焊型液力变矩器实验参数变量上限下限步长Tp/mm410.5Tt/mm410.5㊀表2变矩器叶片冲角实验参数变量上限下限步长αP/ʎ4-41αT/ʎ4-41αS/ʎ4-41图1㊀液力变矩器单通道物理模型㊀㊀分析采用ANSYS-CFX进行计算ꎬ对于单流道模型建立图一中的物理模型ꎬ如图1ꎬ图2所示ꎮ采用ICEM对物理模型进行网格化离散处理ꎬ处理结果网格数为322万ꎮ将网格导入后ꎬ检查网格质量为0.76ꎬ可以满足本问题计算需求ꎮ对于计算模型进行选择ꎬ由于研究问题是一个稳态的流动问题ꎬ选择以压力为基础的绝对速度稳态模型ꎮ算法模型选择能量方程和k-epsilon-SST湍流模型ꎬ而离散形式选择更容易收敛的一阶迎风格式ꎬ松弛因子选用默认值ꎮ固体域选用常见金属材料钢ꎬ内部流动液体选用22号透平油ꎮ对于边界条件:入口设置为压力入口ꎬ温度为368Kꎬ相对压力为0.07MPaꎻ出口设置为速度出口ꎻ对于壳内壁面ꎬ设置为绝热边界无滑移ꎬ温度350Kꎮ图2㊀液力变矩器各叶片物理模型(左泵轮ꎬ中涡轮ꎬ右导轮)2㊀结果分析参考流场分析结果ꎬ共设置三个响应量ꎬ最高效率ηmaxꎬ最大能容系数λ0maxꎬ起动变矩比K0ꎬ输出转矩Toꎮ基于闫东清[5]对主效应㊁交互效应的相关研究ꎬ涡轮叶片厚度和泵轮叶片厚度虽然对效率有交互影响作用ꎬ但其对于变矩器的影响主要还是集中在涡轮和泵轮的输出转矩上ꎬ故将输出转矩作为评判变矩器性能的指标ꎮ2.1㊀叶片厚度对泵轮输出转矩的影响根据不同情况ꎬ分别取泵轮叶片厚度Tp为定值2mmꎬ涡轮叶片厚度Ts为定值2mmꎬ速比为0 2ꎬ研究泵轮输出转矩的变化ꎮ为研究两者交互影响ꎬ以及所有水平上可能的两个叶片厚度的组合变化ꎬ获得其对泵轮输出转矩的影响规律ꎮ叶片厚度对泵轮输出转矩的影响如图3所示ꎬ涡轮㊁泵轮叶片对泵轮输出转矩的交互影响如图4所示ꎮ根据不同叶片厚度下泵轮转矩数值的对比图ꎬ无论是涡轮叶片厚度增加或者泵轮叶片厚度图3㊀叶片厚度对泵轮输出转矩的影响图4㊀涡轮、泵轮叶片对泵轮输出转矩的交互影响增加都会导致输出转矩的减小ꎬ这种趋势再叶片厚度较大时更为明显ꎮ由于叶片厚度加厚ꎬ导致边界层分离点后移ꎬ产生启动涡需要更大的逆压力梯度ꎬ导致了输出转矩的变小ꎮ在1~3mm的范围内泵轮输出转矩的变化平均为2%ꎬ最大值为2.3%ꎬ在3~4mm范围内泵轮输出转矩的平均变化率为3%ꎬ最大值为3.8%ꎮ且对于泵轮输出转矩ꎬ改变泵轮叶片厚度时ꎬ输出转矩始终低于同水平涡轮7%左右ꎮ2.2㊀叶片厚度对涡轮输出转矩的影响分别取泵轮叶片厚度Tp为定值2mm和涡轮叶片厚度Ts为定值2mmꎬ速比为0.2ꎬ研究泵轮输出转矩的变化ꎮ为研究两者交互影响ꎬ以及所有水平上可能的两个叶片厚度的组合变化ꎬ分析其对涡轮输出转矩的影响ꎮ叶片厚度对涡轮输出转矩的影响如图5所示ꎬ涡轮㊁泵轮叶片对涡轮输出转矩的交互影响如图6所示ꎮ图5㊀叶片厚度对涡轮输出转矩的影响图6㊀涡轮、泵轮叶片对涡轮输出转矩的交互影响根据不同叶片厚度下涡轮转矩数值的对比图ꎬ不同于泵轮ꎬ涡轮输出功率对于两种叶片厚度变化的响应差异不大ꎬ原因为涡轮和泵轮功能上本质的不同ꎬ涡轮将输入不稳定的机械能转化成稳定压力势能ꎬ泵轮将压力势能转化成稳定的机械能ꎬ所以两者对转矩的响应呈不同趋势ꎮ同时无论是涡轮叶片厚度增加或者泵轮叶片厚度增加都会导致输出转矩的减小ꎬ这种趋势在叶片厚度较大时更为明显ꎬ涡轮在1~3mm的范围内泵轮输出转矩的变化平均为2.2%ꎬ最大值为2.5%ꎬ在3~4mm范围内泵轮输出转矩的平均变化率为3.4%ꎬ最大值为4.2%ꎮ2.3㊀叶片冲角对变矩器工作性能的影响由于改变冲角对输出转矩的影响并不明显ꎬ为研究导轮㊁泵轮㊁涡轮不同叶片冲角对液力变矩器性能的影响ꎬ更换泵轮转矩系数作为响应量ꎬ保持其它设计参数不变ꎬ改变叶片冲角的数值ꎬ更新模型ꎬ分别划分网格ꎬ建立流场仿真计算模型ꎬ采用相同的流场仿真方法开展研究ꎮ叶片冲角对泵轮转矩系数的影响如图7所示ꎮ图7㊀各叶片冲角对泵轮转矩系数的影响不同类型的叶片的冲角对液力变矩器泵轮转矩系数的影响不同ꎬ对于涡轮叶片ꎬ冲角增大ꎬ转矩系数逐渐增长ꎬ增长总体水平一致ꎬ平均变化率1.4%ꎮ对于泵轮叶片ꎬ冲角增大ꎬ转矩系数先增大后减小ꎬ转矩系数最大值5.5ꎬ此时冲角为2ʎꎮ对于导轮叶片ꎬ冲角增大ꎬ转矩系数总体呈减小ꎬ后有略微增大ꎬ转矩系数最小值为5.35ꎬ此时冲角为2ʎꎮ2.4㊀模型优化为了使变矩器适配减速带能量捕获装置ꎬ整合之前对于减速带㊁捕获装置建模所得数据ꎬ提出以下目标函数:Tt㊀TP=argmax(To)(1)㊀㊀由于数值仿真的局限性ꎬ无法得到具体的表达式来用数学方法求解最优解ꎮ所以将叶型数据整合ꎬ采用模拟退火算法对以上目标函数寻找最优解ꎮ结果见表3ꎮ由表3可知ꎬ在涡轮和泵轮叶片厚度分别为2.075mm和2.10mm时ꎬ输出转矩达到最大ꎮ㊀表3输出转矩最优解叶片类型最优解/mm泵轮2.10涡轮2.0753㊀结束语鉴于已有变矩器数值模拟结果ꎮ文中通过创建单流道的液力变矩器物理模型ꎬ基于减速带能量捕获装置的特性ꎬ对液力变矩器和减速带捕能装置行适配ꎬ寻求两者的最佳性能参数ꎮ研究表明:(1)涡轮㊁泵轮叶片厚度增大会导致泵轮输出转矩减小ꎮ两种叶片厚度对于涡轮输出转矩的影响并没有显著的差别ꎮ(2)采用模拟退火算法ꎬ得到了可行域内的最优解ꎬ泵轮叶片厚度为2.1mmꎬ涡轮叶片厚度为2.075mmꎮ(3)不同类型叶片冲角改变对于转矩系数影响不同ꎬ对于涡轮叶片ꎬ冲角增大ꎬ转矩系数逐渐增大ꎻ对于泵轮叶片ꎬ冲角增大ꎬ转矩系数先增大后减小ꎻ对于导轮叶片ꎬ冲角增大ꎬ转矩系数总体呈减小ꎬ后有略微增大ꎮ研究结果可为液力变矩器涡轮㊁泵轮优化设计提供参考ꎮ参考文献[1]㊀王㊀迪ꎬ常㊀山ꎬ岳彦炯.CFD仿真设计新型双涡轮导叶可调式液力变矩器[J].热能动力工程ꎬ2018ꎬ33(12):93-97.[2]㊀刘安然ꎬ李延频ꎬ石祥钟.长短叶片泵轮对液力变矩器性能改进的研究[J].液压与气动ꎬ2020(4):42-46.[3]㊀罗㊀准ꎬ冯武卫ꎬ周中华ꎬ等.自发电减速带在道路交通中的设计应用[J].机械工程师ꎬ2019(10):74-76.[4]㊀RobinetteDꎬBloughJ.TransientHeatTransferandEn ̄ergyBalanceModelforHydrodynamicTorqueConvert ̄ersWhileOperatingatExtremeSpeedRatio[C].In ̄ternationalSymposiumonTransportPhenomena&Dy ̄namicsofRotatingMachineryꎬ2016.[5]㊀闫清东ꎬ李新毅ꎬ魏㊀巍ꎬ等.冲压叶片厚度对液力变矩器性能的影响[J].北京理工大学学报ꎬ2020ꎬ40(5):471-476.。
《液力变矩器》课件
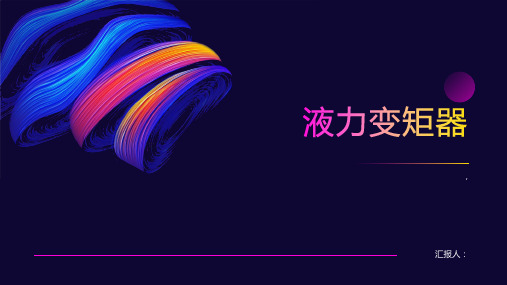
控制策略:根据液力变矩器的工作原理和性能要求,选择合适的控制策略 优化目标:提高液力变矩器的工作效率、降低能耗、提高稳定性等 优化方法:采用优化算法,如遗传算法、神经网络等,对控制策略进行优化 优化效果:提高液力变矩器的工作效率、降低能耗、提高稳定性等
PART SIX
材料选择:选择合适的材料,如钢、铝、铜等 铸造:将材料熔化,铸造成所需的形状和尺寸 加工:对铸造好的零件进行加工,如车削、铣削、磨削等 装配:将加工好的零件装配成液力变矩器 测试:对液力变矩器进行性能测试,如耐久性、可靠性等 包装:将液力变矩器包装好,准备发货
发展趋势:随着新能源汽车的普及,液力变矩器在电动汽车中的应用逐渐增多 竞争格局:国内外市场竞争激烈,需要不断提高产品质量和技术水平,以适应市 场需求
智能化:液力变矩器将更加智能化,能够自动调节扭矩和转速 节能环保:液力变矩器将更加注重节能环保,降低油耗和排放 轻量化:液力变矩器将更加轻量化,提高车辆的燃油经济性和操控性
扭矩传递能力与液力变矩器 的结构有关
液力变矩器可以传递较大的 扭矩
液力变矩器可以适应不同的 转速和扭矩需求
液力变矩器可以提供稳定的 扭矩输出
自动换挡:根据车速和发动机转速自动选择合适的挡位 平稳起步:在起步时提供平稳的动力输出,避免起步时的抖动和冲击 节能省油:通过自动换挡和发动机转速控制,实现燃油经济性 驾驶舒适性:提高驾驶舒适性,降低驾驶疲劳感
材料选择:根据液力变矩器的工作 环境和性能要求,选择合适的材料
材料选择原则:满足液力变矩器的 工作要求,保证其使用寿命和可靠 性
添加标题
添加标题
添加标题
添加标题
特性:材料的机械性能、热性能、 耐磨性、耐腐蚀性等
材料选择方法:根据液力变矩器的 设计要求和使用环境,选择合适的 材料,并进行试验验证
- 1、下载文档前请自行甄别文档内容的完整性,平台不提供额外的编辑、内容补充、找答案等附加服务。
- 2、"仅部分预览"的文档,不可在线预览部分如存在完整性等问题,可反馈申请退款(可完整预览的文档不适用该条件!)。
- 3、如文档侵犯您的权益,请联系客服反馈,我们会尽快为您处理(人工客服工作时间:9:00-18:30)。
外环之交点上的半径;
k——元线的序号,k=0,1,2····
以泵轮元线9为例,计算叶片偏移量x1
针对元线1,列出公式
x9= r9
对于元线0,有
= = 0.4370
= 116.38°
= = 0.4936
= 118.36°
对于外环,y = 0,j10= e ,取e=2.4 = 12.45 mm
9.46
98.56
4.19
3
14.38
49.16
9.46
6.34
97.62
5.78
4
6.19
48.62
11.83
3.79
97.22
7.78
5
0.00
47.13
13.91
0.00
97.02
10.86
6
6.19
48.18
19.37
3.79
97.22
15.86
7
14.26
49.83
28.41
6.34
97.62
106°2′
107°17′
115°56′
6
0.2878
106°15′
108°56′
115°78′
7
0.2996
107°47′
109°78′
116°23′
8
0.3127
108°50′
110°18′
116°46′
9
0.3468
108°53′
111°58′
117°49′
出口10
0.3547
110°
112°08′
表4-1变矩器泵轮角度计算参数
元线序号
设计流线上的
外环上的
内环上的
0
0.3568
110°
104°32′
109°25′
1
0.3608
110°15′
105°13′
108°46′
2
0.3645
110°22′
106°26′
108°55′
3
0.3678
110°27′
107°56′
107°23′
4
0.3711
110°40′
元线序号
设计流线上的
外环上的
内环上的
进口0
0.3649
114°
113°
118°
1
0.3726
115°
113°28′
117°26′
2
0.3735
115°8′
114°46′
116°78′
3
0.3776
115°25′
115°26′
115°26′
4
0.2818
115°50′
106°15′
115°28′
5
0.2857
计算出循环轴面流速为9.632 m/s
对泵轮带入这些数值: rB1= rB1( B1+ VB1 B1),所得数值为:0.906。
类似的,在出口处: rB2= rB2( B2+ VB2 B2),所得数值为:4.0732。
则 r改变量 rB2 rB1,即得:4.0732-0.906=3.1672。
4.1
液
力
变
矩
器
叶
片
设
计
学 院:机械学院
专 业:机自(车辆)
学 号:*********
*********
液力变矩器是AT自动变速箱的核心部件之一,液力变矩器的工作轮主要包括:泵轮、涡轮和导轮。
其设计的关键是各工作轮的叶片设计。本次设计采用的是环量分配法。环量设计法的理论基础是束流理论,认为其在选定的设计速比下,循环圆平面中间流线上每增加相同的弧长,液流沿叶片中间流线应增加相同的动量矩,以保证流道内的流动状况良好。设计过程为:
118°37′
表4-4涡轮叶片最终尺寸
元线
序号
外环
内环
轴向距离/mm
半径/mm
叶片偏移量/mm
轴向距离/mm
半径/mm
叶片偏移量/mm
0
25.34
75.00
12.35
11.64
91.28
15.26
1
30.21
86.56
5.33
15.18
94.16
19.16
2
33.39
95.26
20.89
18.48
97.36
计算出循环轴面流速为9.632 m/s
对泵轮带入这些数值:
rB1= rB1( B1+ VB1 B1)
所得数值为:0.802。
类似的,在出口处:
rB2= rB2( B2+ VB2 B2)
所得数值为:3.1865。
则 r改变量 rB2 rB1,即得:
r=3.1865-0.802=2.3845
表4-3变矩器涡轮角度计算参数
根据前期循环圆的确定,在泵轮转矩方程TB= Q( rB2 rB1)中 rB2 rB1项是确定泵轮动量矩变化的一个因数,经计算测量得出泵轮进口角 B1=120°,进口半径外环为95mm,内环为123.5mm,出口角 B2=110°,半径外环196mm,内环167mm,这样转速比为0.5,在1800r/min时输出转矩为140N·m[11]。则根据公式:
4.1泵轮叶片设计图
将此改变量分为十份,按其中九分各占10.5%,一份占5%划分,元线9与
元线10之间的增量为5%,以减少液体在叶片出口处的能量增量及其涡流损失。
其次,在设计流线上,每一点的相应叶片角可根据公式计算
=
计算出每一截面元线在设计流线上的角度后,就应求内环和外环上的相应角度。为了确定元线与内环之交点处的叶片角 ,采用按反势流分布计算公式 ,类似地,外环上可以利用下列公式计算: ,所以在叶片入口处: , ,计算后整理成表:
r = r
导轮叶片设计图
表4-5变矩器导轮角度计算参数
元线序号
设计流线上的
外环上的
内环上的
进口0
0.4659
95°
92°12′
97°95′
1
0.4706
95°17′
93°32′
96°56′
2
0.4765
95°32′
94°21′
96°13′
3
0.4787
95°62′
95°30′
95°53′
4
0.4832
则j10=12.45 = 8.78mm
计算后,以直接连接内外环之相应点,即可作出叶片形状[12]。计算结果和最终尺寸填在下表:
表4-2泵轮叶片的最终尺寸
元线
序号
外环
内环
轴向距离/mm
半径/mm
叶片偏移量/mm
轴向距离/mm
半径/mm
叶片偏移量/mm
0
68.81
86.00
32.00
21.61
103.36
32.35
128.61
11.29
6
52.42
152.19
15.91
29.19
134.34
9.63
7
46.12
163.62
13.93
26.56
139.30
7.29
8
35.53
171.59
10.36
18.36
143.21
5.93
9
15.31
175.03
5.59
8.51
146.56
2.67
10
0.00
179.56
100°
101°28′
98°44′
表4-6导轮叶片最终尺寸
元线
序号
外环
内环
轴向距离/mm
半径/mm
叶片偏移量/mm
轴向距离/mm
半径/mm
叶片偏移量/mm
0
32.96
60.32
0.00
13.77
100.06
0.00
1
29.16
55.16
4.28
1.21
99.26
3.45
2
22.65
51.16
7.16
21.00
1
71.05
98.53
31.21ຫໍສະໝຸດ 25.36106.3018.69
2
73.56
110.65
30.56
30.56
111.32
16.32
3
74.34
122.31
26.89
32.78
117.24
15.21
4
73.78
133.74
22.35
33.13
123.11
13.68
5
62.42
142.72
18.49
108°
107°32′
5
0.3778
111°06′
108°47′
107°41′
6
0.3831
111°18′
109°26′
107°56′
7
0.3891
111°21′
110°32′
108°11′
8
0.3909
111°35′
111°21′
108°25′
9
0.3976
111°43′
111°78′
109°56′
0.00
0.00
0.00
0.00
注 内外环轮廓相对位置应保证叶片垂直于外环。
4.
进口角: =42°出口角: =142°。涡轮叶片计算与泵轮叶片计算顺序相似。