炼厂制氢工艺原理
工业氢气工作原理是什么

工业氢气工作原理是什么
工业氢气工作原理是通过水电解、蒸汽重整、部分氧化、加压吸附等不同的工艺手段将水或者有机物转化为氢气。
具体工作原理如下:
1. 水电解法:将水分子分解成氧气和氢气,电流通过水中的两个电极(阴极和阳极),在阴极反应处水发生还原反应生成氢气,而在阳极反应处发生氧化反应生成氧气。
2. 蒸汽重整法:通过加热水蒸汽和一定量的天然气或石油燃料,在高温高压条件下进行催化重整反应,生成合成气体,然后再通过水气转移反应或甲烷重整反应,最终得到含有丰富氢气的气体。
3. 部分氧化法:将天然气或石油燃料与一定量的氧气或空气在催化剂的作用下进行部分氧化反应,生成合成气体,然后通过水气转移反应或甲烷重整反应,最终得到含有丰富氢气的气体。
4. 加压吸附法:通过一系列的压缩、吸附、脱附等操作,将原料气中的氢气高效地吸附到特定的吸附剂上,再通过适当方式进行脱附,得到纯度较高的氢气。
这些工业氢气生产方法各有优劣,根据具体的应用需求可以选择不同的工艺进行生产。
工业制氢气的方法

工业制氢气的方法
工业制氢气的方法主要有以下几种:
1. 蒸汽重整法(Steam Methane Reforming,SMR):
•这是工业上最常用的制氢方法。
•首先,甲烷(天然气)与水蒸气反应产生一氧化碳和氢气。
•反应方程式:CH₄ + H₂O → CO + 3H₂
•然后,一氧化碳与水蒸气反应,生成二氧化碳和更多的氢气。
•反应方程式:CO + H₂O → CO₂ + H₂
•这个过程在高温下进行,通常需要使用催化剂。
2. 煤气化法(Gasification):
•煤、石油等碳质原料通过气化反应生成合成气,然后通过水煤气变换反应(Water Gas Shift,WGS)将一氧化碳转化为更多的氢气。
•反应方程式:CO + H₂O → CO₂ + H₂
3. 电解法(Electrolysis):
•通过电解水来分解水分子,将氢气和氧气分离。
•反应方程式:2H₂O → 2H₂ + O₂
•电解法有水电解和碱性水溶液电解等不同的方法。
4. 部分氧化法(Partial Oxidation):
•部分氧化法是在有限氧气条件下,使甲烷或其他碳氢化合物与氧气反应,生成氢气和一氧化碳。
•这个方法一般在高温下进行,通常需要催化剂。
5. 溶液法:
1/ 2
•通过将金属与酸性溶液反应来产生氢气。
•反应方程式:Zn + 2HCl → ZnCl₂ + H₂
不同的制氢方法具有各自的优缺点,选择取决于原材料的可用性、经济性、能源效率和环境考虑等因素。
在工业上,常根据具体需求和条件采用不同的制氢方法。
2/ 2。
煤制氢工艺原理

煤制氢工艺原理
氢气是一种极其重要而又稀缺的能源,被广泛用于各个领域。
在有限的自然资源的情况下,如何以更为可持续的方式生产氢气,以满足社会对氢气的日益增长的需求,是当今能源工业的主要课题。
近年来,煤制氢技术受到了越来越多的关注,它不仅可以满足社会对氢气的需求,而且具有较低的成本、较高的氢气得率和可再生性等优点,成为了能源工业发展的新热点。
煤制氢是一种以煤为原料,通过化学反应将碳形成氢气的工艺,其主要包括4个步骤:煤给料、气化反应、过滤及蒸汽改质等。
1、煤给料:给料是煤制氢工艺的第一步,主要是将煤粉熔炼成小圆球状,并进一步粉碎至指定的微细度,这样可以有效解决气化反应的流动问题,高气化反应效率,降低气体损耗。
2、气化反应:化反应是煤制氢工艺的核心部分,其主要是将碳和水结合,通过高温(600~800℃)和高压(5~25MPa)的复合环境进行气化反应,产生氢气和二氧化碳,其反应方程式:C + H2O= CO+ H2。
3、过滤:化反应产生的气体经过凝析和过滤处理后,将氢气分离出来。
4、蒸汽改质:过过滤的氢气,其含水率还是较高,因此,需要进行蒸汽改质,通过蒸汽干燥的方式,将氢气中的水分去除,从而获得纯度较高的氢气。
煤制氢工艺作为一种新兴的能源技术,具有可再生性和较低的成本等优点,在未来将可望成为氢能源的主要来源。
但是,这项技术也
存在着许多缺陷,如生产低纯度氢气,氢气含水率高和产生大量的固体废弃物等,其中一些问题需要通过科学实验和研究来解决。
因此,煤制氢技术的开发和应用,需要加大科研力量,推动其建立完善的技术系统,实现可持续发展,以保障能源安全。
工业制取氢气的关键技术

工业制取氢气的关键技术根据氢气生产来源和生产过程中的碳排放情况,一般可将氢能分为灰氢、蓝氢、绿氢。
灰氢,是通过化石燃料(例如石油、天然气、煤炭等)燃烧产生的氢气,在生产过程中会有二氧化碳等排放。
目前,市面上绝大多数氢气是灰氢,约占当今全球氢气产量的95%左右。
灰氢的生产成本较低,制氢技术较为简单,而且所需设备、占用场地都较少,但是碳排放较大。
蓝氢,是将天然气通过蒸汽甲烷重整或自热蒸汽重整制成。
虽然天然气也属于化石燃料,在生产蓝氢时也会产生温室气体,但由于使用了碳捕捉、利用与储存(CCUS)等先进技术,温室气体被捕获,减轻了对地球环境的影响,实现了低排放生产。
绿氢,是通过使用再生能源(例如太阳能、风能、核能等)制造的氢气,例如通过可再生能源发电进行电解水制氢,在生产绿氢的过程中,完全没有碳排放。
绿氢是氢能利用的理想形态,但受到目前技术及制造成本的限制,绿氢实现大规模应用还需要时间。
目前,氢的制取主要有三种较为成熟的技术路线:一是以煤炭、天然气为代表的化石能源重整制氢;二是以焦炉煤气、氯碱尾气、丙烷脱氢为代表的工业副产气制氢;三是电解水制氢。
1 灰氢制造技术1.1媒制氢煤制氢的本质是以煤中的碳取代水中的氢,最终生成氢气和二氧化碳(CO2),其成本低,技术成熟,运用广泛。
以煤气化为例,其工艺流程是将煤炭经高温气化形成合成气,然后通过水煤气变换反应进一步将合成气中的CO 与水反应,生成氢气与CO2,最后进行混合气体净化、分离、氢气提纯、尾气处理等工序,最终得到高纯度氢气。
由于煤中含有硫等杂质,由气化和变换反应生成的氢气需要采用脱硫和脱碳技术,后用变压吸附(PSA)纯化技术制成高纯度的氢气。
脱硫和脱碳一般采用低温甲醇洗或者SelexolTM 工艺技术。
1.2天然气制氢天然气水蒸气重整制氢(SMR)目前为国内外普遍采用的天然气制氢工艺路线,和煤制氢相比,用天然气制氢产量高、加工成本较低,排放的温室气体少。
在美国和中东等地,大部分专有制氢装置采用天然气制氢,因此天然气成为国外较普遍的制氢方法,但在中国,天然气价格相对较高,因此中国大多数制氢厂通过煤气化制氢。
炼厂制氢工艺原理
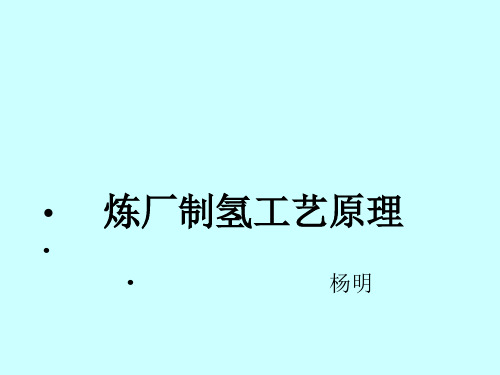
17
. 剂
• 2.4 变换催化剂 • ( 1 ) 中 变 催 化 剂 化 学 组 分 为 Fe2O3 、 Cr203 、 K20 ,使用时被还原为有活性的 Fe304 ,催化剂毒物为硫、磷、硅等,但 中变催化剂受毒物影响较小,如原料气硫 含量达到0.1%时才使Fe304转变为FeS, 使活性稍有下降,为新剂的 70 % -80 %。 工艺蒸汽中含杂质过多时会与原料气组分 反应,使催化剂结皮而降低活性。 • (2) 低变催化剂主要组分为CuO,添加 ZnO 、 A1203 、 Cr203 等。催化剂毒物主要 是硫、氯、水、氨也有影响。硫主要来自 原料气,它会与催化剂活性表面的铜晶粒 发生化学吸附和反应而影响活性。
一 、 氢 气 的 制 造 方 法
二、原料脱毒
• 1、催化剂毒物与催化剂中毒 • (1) 催化剂中毒的定义 • 催化剂的活性和选择性可能由于外来微 量物质的存在而下降,这种现象叫做催 化剂的中毒,而外来的微量物质叫做催 化剂毒物。 • (2) 催化剂毒物的危害与来源
二、原料脱毒
• 从广义来说,这些微量物质可能是反应物、产物或杂 质。而一般只是指会引起在催化剂的活性催化金属点 位上发生强化学吸附的杂质。毒物可能来自催化剂本 身或反应原料中,它们会堵塞活性位,而且也会引起 表面发生变化或形成新的化合物。在制氢、合成氨等 石油化工过程中,原料天然气、轻油、煤一般均含有 硫化物,有时也有氯、砷存在,这些都属原料所携带 的催化剂毒物,应予脱除。而在催化剂制造过程中因 所用原料纯度不高也会带人有害的重金属或硫化物等。
(3)轻烃水蒸汽转化法
• 合适的反应条件为:温度800~900℃,反应压力 1.5----3.0MPa,水蒸汽与原料气摩尔比2.5---6。所得转化反应气体的组成为:甲烷3—8%(V), 一氧化碳7%-8%,二氧化碳10%-15%,氢气70 %左右,采用催化剂(一般为镍催化剂),该催化 剂一般含15%—25%的NiO,以硅酸铝为载体。 在反应前将NiO还原为金属镍。对原料中砷含量 有严格的限制,以免使催化剂中毒失活。当原料 较重时,如重于石脑油,则往往采用非镍催化剂, 如锶、铝及钙的氧化物,有助于改善结构及抗硅 性能。
氢气制取原理

氢气制取原理
氢气是一种无色、无臭、无味的天然气体,是世界上最轻的元素之一。
它常用于化学工业、冶金工业和石油化工等领域。
氢气的制取主要有以下几种方法:
水分解法:通过电解或高压催化的方式将水分解成氢气和氧气。
这是目前最为常见的氢气制取方法。
煤气化法:将煤炭进行气化反应,生成含有大量氢气的煤气。
石油加氢法:将石油与氢气进行反应,生成含有大量氢气的石油加氢产物。
天然气加氢法:将天然气与氢气进行反应,生成含有大量氢气的天然气加氢产物。
以上是氢气制取的几种主要方法,具体的制取方法取决于氢气的用途和原料的供应情况。
1 / 1。
制氢的方法和基本原理
制氢的方法和基本原理氢是地球上最丰富的元素,也是最重要的能源之一。
它是发电、生产液体燃料和催化剂以及制造合成材料的关键原料。
因此,大量研究已经开始寻找有效的方法来制备氢。
一、电解水的方法电解水可以把水分解成氢气和氧气两种气体,这是一种简单有效的制氢方法。
电解反应是一种通过给定电流加热水蒸发时,水分子被电子分裂成氢原子和氧原子的反应过程。
这种反应通过电解单元内的两个钛压板实现,它们分别由一层碳和一层钛构成,它们分别被接在正极和负极上。
当电流流过它们时,正极将水中的氢离开,而负极将水中的氧离开。
二、燃烧反应的方法燃烧反应是一种将某种有机物配合水气转化为氢气的反应。
它通过将一定数量的化合物(如碳氢化合物和烷基化合物)与足够量的氧气混合并在一定温度和压力下燃烧来实现。
燃烧反应可以分解有机物,产出大量氢气和二氧化碳,而生物微处理则可以通常的用于分解废水中的有机物并产生氢气。
三、金属氢化物的方法金属氢化物可以把金属溶解在浓氢溶液中,将金属与氢结合形成金属氢化物,释放出大量氢气。
金属氢化物法是一种用可再生金属制备氢气得到了广泛应用。
这种方法首先将铁或铝等可再生金属溶解在浓氢溶液中,然后将金属溶剂与氢反应,释放出氢气。
本文讨论了三种制氢方法:电解、燃烧反应和金属氢化物法,它们在制备氢气时都有一定的优点,可以根据实际情况选择合适的制氢方法。
制氢的基本原理是给定部分能量使水分子发生析裂,形成氢气和氧气,并且可以利用燃烧反应将有机物与水转化为氢气,最后可以使用金属氢化物法将其转化为可再生的氢气。
综上,科学家可以更好地控制它们,利用能源和资源节约的优势,使氢的利用更加有效率。
石油化工厂里的工艺-制氢装置及工艺
制氢装置及工艺
本套装置采用烃类水蒸气制氢方法,我公司采用的原料是炼厂干气和水蒸气在催化剂上进行反应,产生的氢气在经过变压吸附将氢气提浓,外送氢气纯度达到99.9%。
主要包括以下几个过程。
1、干气脱硫部分
进入脱硫部分的原料气,首先进入加氢反应器(R4001),发生将有机硫转化为无机硫,然后再进入氧化锌脱硫反应器(R4002A.B)脱氯段脱除原料中的氯,最后进入氧化锌脱硫段,在此氧化锌与硫化氢发生脱硫反应。
精制后的气体要求硫含量小于0.5ppm,烯烃小于1%(V)、氯小于0.2ppm 进入转化部分。
2、转化部分
精制后的原料气按水碳比不小于3.2与水蒸汽混合,再经转化炉(F4001)对流段预热,进入转化炉辐射段。
在催化剂的作用下,发生复杂的水蒸汽转化反应,从而生产出氢气、甲烷、一氧化碳、二氧化碳和水的平衡混合物。
主要反应有:
C n H m + nH2O = nCO +(n+m/2)H2①
CO + 3H2 = CH4 + H2O △H o298=-206kJ/mol ②
转化反应是强吸热反应,转化炉内温度高达900度。
3、中变部分
由转化部分来的转化气进入中温变换反应器(R4003),在催化剂的作用下发生变换反应:
CO+H2O=CO2+H2△H o298=-41.4KJ/mol
将变换气中CO含量降至3%左右,同时继续生产氢气。
中变气经过汽包给水换热器(E4002A.B、E4003)、低温热水换热器(E4004)进行热交换回收部分余热后,再经中变气水冷却器(E4005)冷却至35℃左右,经分水后进入PSA 部分。
氢气制取方法
氢气制取方法
氢气是一种重要的化工原料,广泛应用于石油加工、化肥生产、氢化工艺等领域。
氢气的制取方法有多种,下面将介绍几种常见的
氢气制取方法。
1. 水电解法。
水电解法是一种常见的氢气制取方法,其原理是利用电解水分
解水分子,产生氢气和氧气。
通常采用的电解设备有电解槽和电极,电解槽内装满电解液,通过电极通电产生氢气和氧气。
这种方法制
取的氢气纯度较高,适用于实验室和小规模生产。
2. 天然气蒸汽重整法。
天然气蒸汽重整法是工业中常用的氢气制取方法之一,其原理
是利用天然气中的甲烷与水蒸气在催化剂的作用下进行重整反应,
生成氢气和一氧化碳。
这种方法制取的氢气规模较大,适用于工业
生产中对氢气纯度要求不高的场合。
3. 煤气干馏法。
煤气干馏法是利用煤炭进行干馏生成煤气,再通过煤气净化和
转化反应制取氢气的方法。
煤气中含有丰富的氢气,通过适当的处
理和转化反应,可以得到高纯度的氢气。
这种方法制取的氢气成本
较低,适用于煤炭资源丰富的地区。
4. 生物质气化法。
生物质气化法是利用生物质资源如木材、秸秆等进行气化反应,生成生物质气体,再通过气体净化和转化反应制取氢气的方法。
这
种方法制取的氢气具有较高的环保性,适用于生物质资源丰富的地区。
总结:
以上介绍了几种常见的氢气制取方法,每种方法都有其适用的
场合和特点。
在实际生产中,可以根据需要选择合适的制取方法,
以满足不同领域对氢气的需求。
希望本文能为大家对氢气制取方法
有所了解,谢谢阅读!。
制氢技术及利用
制氢技术及利用引言:随着能源危机日益严重和环境污染问题的日益突出,寻找可再生能源已经成为全球关注的焦点。
制氢技术作为一种清洁、可再生的能源技术,受到了广泛关注。
本文将介绍制氢技术的原理、分类以及其在能源、交通和工业领域的利用。
一、制氢技术的原理制氢技术是指将水或其他氢源物质通过化学反应转化为氢气的过程。
常见的制氢技术包括热解、电解和催化剂反应等。
其中,热解是利用高温将水分解成氢气和氧气的过程;电解是利用电能将水分解成氢气和氧气;而催化剂反应是利用催化剂促进水和其他氢源物质的反应生成氢气。
二、制氢技术的分类根据不同的原理和方法,制氢技术可以分为传统制氢技术和新型制氢技术两大类。
1. 传统制氢技术包括热解和电解。
热解技术是利用高温将水分解成氢气和氧气,常用的方法有高温蒸汽热解和焦炭热解。
电解技术是利用电能将水分解成氢气和氧气,常用的方法有碱性电解、酸性电解和固体氧化物电解等。
2. 新型制氢技术包括太阳能制氢技术、生物制氢技术和催化剂反应技术等。
太阳能制氢技术利用太阳能将水分解成氢气和氧气,是一种绿色、可再生的制氢方法。
生物制氢技术利用生物体内的微生物或酶类催化剂来产生氢气,具有环保、高效的特点。
催化剂反应技术则是利用催化剂促进水和其他氢源物质的反应生成氢气,具有高效、低能耗的特点。
三、制氢技术的利用制氢技术在能源、交通和工业领域具有广泛的应用前景。
1. 能源领域:制氢技术可将水和其他氢源物质转化为氢气,作为清洁能源储存和利用。
氢气可以通过燃烧发电、燃料电池等方式转化为电能,为能源供应提供了新的选择。
特别是太阳能制氢技术,可以将太阳光转化为氢气,解决了太阳能发电的间歇性问题,实现了能源的可持续利用。
2. 交通领域:氢燃料电池车是利用氢气与氧气反应产生电能驱动电动机的车辆。
制氢技术可以提供氢气作为燃料,实现车辆的零排放和零污染。
与传统燃油车相比,氢燃料电池车具有能源效率高、续航里程长等优势,是未来交通领域的发展方向之一。
- 1、下载文档前请自行甄别文档内容的完整性,平台不提供额外的编辑、内容补充、找答案等附加服务。
- 2、"仅部分预览"的文档,不可在线预览部分如存在完整性等问题,可反馈申请退款(可完整预览的文档不适用该条件!)。
- 3、如文档侵犯您的权益,请联系客服反馈,我们会尽快为您处理(人工客服工作时间:9:00-18:30)。
6
7 • (3)轻烃水蒸汽转化法。 • 反应是在有催化剂存在下进行,烃类与水蒸汽反 应生成CO和H2。所用原料主要是天然气,亦可用 丙烷、丁烷、液化石油气及石脑油。原料轻烃的 转化反应是较强的吸热反应,故提高温度可使平 衡常数增大,反应趋于完全,压力升高会降低平 衡转化率,但由于原料是在压力下,且反应产物 的后加工也需在加压下进行,在转化前将原料气 加压比转化后再加压在经济上更为有利,因此采 用加压操作。增加水蒸汽的配比可以提高转化率, 同时还可以防止或减少催化剂上积碳。
• 2.5 甲烷化催化剂 • ( 1 ) 催化剂的主要化学组分为 NiO 、 A1203 , 使用时还原为金属镍。主要毒物为硫、砷、 钒、碳酸钾和羰基镍等。 • (2) 对于甲烷化催化剂,硫是永久性毒物, 这是因为操作温度较低,活性镍一旦与硫化 氢生成Ni2S3后,即使除去H2S,也无法被氢气 再还原为活性状态。研究表明,甲烷化催化 剂中吸硫达到0.15%—0.2%时活性丧失50 %,若达到 0 . 5 %则活性全部丧失。因此进 甲烷化催化剂的原料气中硫含量越低越好, 一般要小于0.1ppm。甲烷化工序设在脱碳之 后,各种脱碳液带入均会造成不同的毒害。
• (3) 砷是转化催化剂的另一重要毒 物,来自原料气、蒸汽或脱碳液。 2 砷中毒不可逆,砷中毒严重时要更 3 换催化剂,甚至要清洗转化炉管。 • (4) 氯也和硫一样有害,要予以限 烃 量。少量氯的毒害是可逆的,但是 类 大量氯带入催化剂时会与催化物质 转 形成低熔点或易挥发的表面化合物, 使镍催化剂因烧结而破坏了结构, 化 导致永久失活。有些金属如铜、铅 催 等因会沉积在催化剂上不易除去而 化 降低其活性。
• (2)部分氧化法。 • 是以烃类为原料制取含氢气体的方法之一。 烃类与水蒸汽反应可制得氢气。该反应为一 强吸热反应,反应所需热量采用由燃烧部分 原料供给,故称之为部分氧化法。烃类原料 选择范围十分广泛,从天然气(CH4)到石油炼 制过程中所得重质渣油均适用。 • 当以天然气为原料时,加入不足量的氧 气,使部分甲烷燃烧为 C02 和 H2O 并放出大量 的热。 • CH4+202→C02+2H20 + 1802kJ •
18
2 4
. 变 换 催 化 剂
2.4 变换催化剂
19
研究表明,氯比硫的毒害严重,氯离子来自蒸汽和 原料气,对低变催化剂的毒害是与Cu、ZnO生成了 Cu7Cl4(OH)10(H20) 、 ZnCl2· 4Zn(OH)2 等 组 成 的 低 熔 点 而有挥发性的表面化合物,使ZnO失去间隔体作用 ,铜微晶迅速长大,破坏了催化剂的结构,使活性 大大下降。加之生成的氯化物易溶于水,在湿气条 件下,氯化物会沿床层迁移,毒害更多催化剂。凝 聚水和氨可以使催化剂中铜微晶生成铜氨络合物, 使催化剂中毒和侵蚀。
(3)轻烃水蒸汽转化法
• 反应是在有催化剂存在下进行,烃类与水蒸汽 反应生成CO和H2。所用原料主要是天然气,亦 可用丙烷、丁烷、液化石油气及石脑油。原料 轻烃的转化反应是较强的吸热反应,故提高温 度可使平衡常数增大,反应趋于完全,压力升 高会降低平衡转化率,但由于原料是在压力下, 且反应产物的后加工也需在加压下进行,在转 化前将原料气加压比转化后再加压在经济上更 为有利,因此采用加压操作。增加水蒸汽的配 比可以提高转化率,同时还可以防止或减少催 化剂上积碳。
2 、 制 氢 催 化 剂 的 毒 物
2、制氢催化剂的毒物
• (2) 引起此类催化剂失活的原因有三方面: • (1) NH3 会使催化剂暂时性中毒,其原因是 NH3 因其 有碱性而吸附在钴钼催化剂的酸性位上,影响了有 机硫化物在这些活性位上的吸附。当NH3被除去后, 催化剂活性可恢复。一般控制气体中 NH3 不得高于 100ppm(V)。 • (2) 催化剂表面积碳会引起半永久性失活,通过用氧 气燃烧可以再生。这种积碳主要是由于烃类在催化 剂上裂解所致,因此操作时氢分压不能过低,温度 不能过高。 • (3) 含砷化合物会与钴、镍生成化合物而引起催化剂 永久性中毒。
一、氢气的制造方法
• 当以重油为原料时,部分氧化反应可用下述反应展示: • CnHm+(n+1/4m)02→nC02+1/2mH20 (1) • CnHm+nC02→2nC02+1/2mH2 (2) • CnHm+nH20→nCO+(1/2m+n) H2 (3) • 反应 (1)为强放热反应,反应(2)、 (3) 为强吸热 反应。反应主要产物为CO及H2, • 反应温度为1200—1370℃,压力为3.2----8.3MPa, 不用催化剂。 1t 原料加入水蒸汽量约 400-----500kg 。 水蒸汽同时也可以缓冲炉温及抑制炭的生成。工业上采 用此法最终制得氢气,带经过几个过程,如空气分离设 备提供部分氧化法所需氧气、部分氧化法粗产物的净化 (如脱炭黑、脱酸性气体)、一氧化碳的转化及脱除等。
三、工艺原理
• 1、脱硫催化剂 • 制取氢所用的催化剂具有很高的活性 和选择性,但它们对毒物也十分敏感, 为了达到正常并长周期运转,确保经济 合理生产的目的,必须严格控制原料、 工艺用水和空气的纯度,因为通过催化 剂气体量非常大,即使毒物含量较低, 但累积的影响相当可观,它会使催化剂 的活性下降,缩短其使用寿命。 •
4
一 、 氢 气 的 制 造 方 法
一、氢气的制造方法
• 在高温及水蒸汽存在下,C02及水蒸汽可与未燃 烧的 CH4 反应,得到主要产物 CO 及 H2 燃烧所得 C02不多,反应为强吸热反应。 • CH4+C02→2C0+2H2 —206kJ • CH4+H2O→CO+3H2 —247kj • 综合:CH4+0.5O2→ C0+2H2 • 为了防止反应过程中碳析出,需补加人一 定量的水蒸汽。天然气部分氧化法可在有催化 剂存在下进行,也可不用催化剂。
10
•
(4)炼油厂及石油化工厂副产氢气。
• 在石油炼制过程中副产炼厂气中含有氢气组 分。炼厂气来源于各石油加工过程,如催化 裂化、热裂化、焦化、加氢裂化及催化重整 等过程。不同来源的炼厂气其组成各不相同, 其中氢含量也不相同。如催化重整气体中含 氢量很高,是炼油厂氢气的重要来源。 • 催化重整反应一般是以石脑油馏分为原料生 产高辛烷值汽油或生产芳烃。其化学反应中 包括了环烷烃脱氢及烷烃脱氢环化等主要反 应,因此在生产芳烃产物的同时得到大量的 氢气。
2、制氢催化剂的毒物
• 2.2 氧化锌脱硫剂 • 其本身是脱毒剂,用于脱除硫化氢和反 应性有机硫化合物。对氧化锌脱硫剂有毒 害的杂质主要是氯(HCl)。氯毒害的原因是 HCl 会与 ZnO 反应生成 ZnCl2 薄层,覆盖在 脱硫剂表面,阻止 H2S 进入其内部,从而 大大降低脱硫剂的性能。因为ZnCl2的熔点 较低,所以在300℃以上操作时,HC13
• 制氢工艺过程中广泛采用加氢转化催化 剂、氧化锌脱硫剂、烃类蒸汽转化催化 剂、中温变换催化剂、低温变换催化剂 和甲烷化催化剂。硫、氯、砷、磷、重 金属等均为可能的毒物。 • 2.1 加氢转化(脱硫)催化剂 • (1) 加氢转化(脱硫)催化剂本身就是脱 毒催化剂,可将有机硫化物加氢转化为 H2S,再被后续的氧化锌脱硫剂脱除,此 外还有使烯烃、有机氮、含氧有机化合 物、有机氯化合物加氢转化为烷烃、氨、 水、氯化氢的能力。
2 0
2 5 甲 烷 化 催 化 剂
.
2.5甲烷化催化剂
• 砷是永久性毒物,催化剂中砷含量达到 0.1%时便严重失活。甲烷化催化剂在 150℃以下操作时,活性镍与一氧化碳会 反应生成羰基镍Ni(CO)4,这是对人剧毒 的挥发物,还造成催化剂中镍的流失, 严重降低活性。因此,在床层降温至 150℃以下时不能再通工艺气,应改用氮、 氢气。
17
. 剂
• 2.4 变换催化剂 • ( 1 ) 中 变 催 化 剂 化 学 组 分 为 Fe2O3 、 Cr203 、 K20 ,使用时被还原为有活性的 Fe304 ,催化剂毒物为硫、磷、硅等,但 中变催化剂受毒物影响较小,如原料气硫 含量达到0.1%时才使Fe304转变为FeS, 使活性稍有下降,为新剂的 70 % -80 %。 工艺蒸汽中含杂质过多时会与原料气组分 反应,使催化剂结皮而降低活性。 • (2) 低变催化剂主要组分为CuO,添加 ZnO 、 A1203 、 Cr203 等。催化剂毒物主要 是硫、氯、水、氨也有影响。硫主要来自 原料气,它会与催化剂活性表面的铜晶粒 发生化学吸附和反应而影响活性。
一 、 氢 气 的 制 造 方 法
二、原料脱毒
• 1、催化剂毒物与催化剂中毒 • (1) 催化剂中毒的定义 • 催化剂的活性和选择性可能由于外来微 量物质的存在而下降,这种现象叫做催 化剂的中毒,而外来的微量物质叫做催 化剂毒物。 • (2) 催化剂毒物的危害与来源
二、原料脱毒
• 从广义来说,这些微量物质可能是反应物、产物或杂 质。而一般只是指会引起在催化剂的活性催化金属点 位上发生强化学吸附的杂质。毒物可能来自催化剂本 身或反应原料中,它们会堵塞活性位,而且也会引起 表面发生变化或形成新的化合物。在制氢、合成氨等 石油化工过程中,原料天然气、轻油、煤一般均含有 硫化物,有时也有氯、砷存在,这些都属原料所携带 的催化剂毒物,应予脱除。而在催化剂制造过程中因 所用原料纯度不高也会带人有害的重金属或硫化物等。
3
• (1)煤的高温干馏(亦称焦化)。 • 煤在隔绝空气的条件下在焦炉中加热到 900— 一 1100℃,在得到主要产物焦炭的同时,还副产 许多炼焦化学产品,如煤焦油、粗苯、氨及焦 、 炉气等。焦炉气中含有大量氢气,“原料煤可 氢 得焦炉气 (STP) 为 300-350m3 。焦炉气组成为氢 55%-66%(体积),甲烷23%—27%,一氧化碳 气 5 % —8 %, C2 以上不饱和烃 2 % —4 %,二氧化 的 碳1.5%—3%,氮3%-7%,氧0.3%-0.8%。 制 焦炉气在 20 世纪 50 年代以前是获取氢气的主要 来源之一。 造 • 从焦炉出来的焦炉气温度在 750—850℃, 方 经冷却并脱除其中所含的煤焦油、粗苯及氨等 组分。处理后焦炉气含氢约 50 % —60 %,若需 法 进一步提纯则可采用深冷分离法、变压吸附法 等进行处理。