液压缸试验方法
液压缸验收试验规程
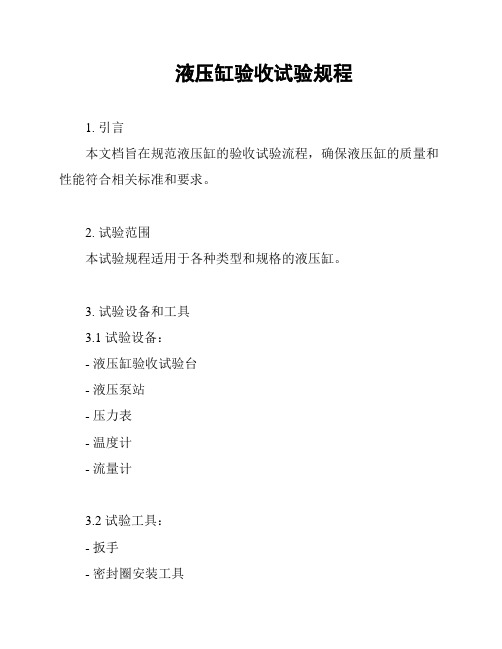
液压缸验收试验规程1. 引言本文档旨在规范液压缸的验收试验流程,确保液压缸的质量和性能符合相关标准和要求。
2. 试验范围本试验规程适用于各种类型和规格的液压缸。
3. 试验设备和工具3.1 试验设备:- 液压缸验收试验台- 液压泵站- 压力表- 温度计- 流量计3.2 试验工具:- 扳手- 密封圈安装工具- 液压油4. 试验内容4.1 外观检查- 检查液压缸的表面是否有明显的划痕、变形或油渍等。
- 检查液压缸的连接接头是否完好无损。
4.2 尺寸和封装检查- 检查液压缸的尺寸是否符合设计要求。
- 检查密封圈的封装是否正确,无泄漏。
4.3 工作性能测试- 连接液压缸至试验台,进行负荷承载能力测试。
- 测试液压缸的工作性能,包括行程、速度、压力等。
5. 试验要求5.1 外观检查合格标准:- 无明显的划痕、变形或油渍等。
- 连接接头完好无损。
5.2 尺寸和封装检查合格标准:- 尺寸符合设计要求。
- 密封圈封装正确,无泄漏。
5.3 工作性能测试合格标准:- 负荷承载能力测试通过。
- 工作性能符合设计要求。
6. 试验记录和报告6.1 试验记录:- 对每项试验内容进行记录,包括试验时间、试验结果等。
6.2 试验报告:- 根据试验记录编制试验报告,详细描述试验过程和结果。
7. 安全注意事项7.1 操作人员必须熟悉试验设备的使用方法和安全操作规程。
7.2 在试验过程中,需特别注意保护个人安全,避免液压压力过高造成危险。
7.3 如果试验过程中发现异常情况,应立即停止试验,并进行必要的维修和调整。
以上为液压缸验收试验规程的简要介绍,旨在为试验人员提供操作指南和质量标准。
具体的试验细节和要求应根据实际情况和相关标准进行补充和确认。
液压缸检验规范

1双作用液压缸检验标准
1.1出厂检验项目、内容、方法和要求
1.1.1全检项目(每一台产品上进行的检验)
序号
检验项目
试验方法
检验要求
1
空载运转
被试缸在无载工况下,全行程上进行5次试运转。活塞运源自平稳2最低启动压力
在空载运行时,从无杆腔逐渐施加压力,测其活塞的最低启动压力。
V
其他
Pn≤10MPa
Pn>10 MPa
Pn≤10 MPa
Pn>10 MPa
0.75MPa
0.09Pn
0.5MPa
0.06Pn
0.45MPa
0.06Pn
0.3MPa
0.04Pn
3
耐压试验
在被测缸无杆腔和有杆腔分别施加公称压力Pn的1.5倍(当Pn﹥16MPa时,应为1.25倍)将活塞分别停留在行程的两端,保持2min进行试验
不允许有外部渗油、爬升等不正常现象
2
耐压试验
在被测柱塞缸的柱塞处全部伸出位置,调节溢流阀使缸内的压力为额定压力的1.5倍,保压2min进行试验
1.不得有外部渗漏
2.全部零件均不得有永久变形
3
外部渗漏
全行程运行换向20次,然后测量柱塞杆处的渗漏量
≤0.025mL
2.1.2抽检项目(液压油缸的抽检数量为每批产品的2%,但不得少于2台,若抽检中有不合格项目,则对此项目应加倍复试,如仍不合格,则对该批产品全检)
序号
检验项目
试验方法
检验要求
1
最低启动压力
在无负荷情况下,调节溢流阀逐渐升压至柱塞开始运动时,测量柱塞缸内的压力,即为最低启动压力
≤0.56MPa
2
液压油缸检测报告2-1

日期:2014年10月21日
液压油缸检测报告
产品名称:工程机械液压缸
规格型号:HSG63/35-80
产品数量:16只
试验项目
试验方法
试验要求
检验结果
备注
试运转
液压缸在空负载工况下全行程往复动作5次以上
运转正常
正常
不正常□
最低启动压力
空载工况下,液压缸无杆腔通入液压油,溢流阀从零开始逐渐升压,观察压力表,记录液压缸活塞杆在启动时的最低启动压力
0.3MPa
正常
不正常□
耐压试验
将液压缸的活塞分别停留在行程两端。调节溢流阀使试验腔的压力为额定压力的1.25倍保压5min
全部零件均不得有破坏或永久变形等异常现象
正常
不正常□
内泄漏
液压缸的活塞分别固定在行程的两端,调节溢流阀,使液压缸的试验腔为额定压力,测量另一腔出油口处泄漏量
1.0~2.2ml/min
正常
不正常□
外渗漏
在检查内泄漏和耐压试验Байду номын сангаас观察活塞杆处及其它结合面渗油情况
在耐久性试验的连续运转中测量活塞杆处外渗漏量
活塞杆处无渗油,缸筒焊接无渗油
有□
无
行程
使液压缸的活塞分别停留在行程的两端位置,测量全行程长度
80±0.5mm
正常
不正常□
经检验,此液压缸各项技术指标均符合国家标准GB/T 15622-2005《中高压液压缸试验方法》的规定,质量合格
液压缸试压标准
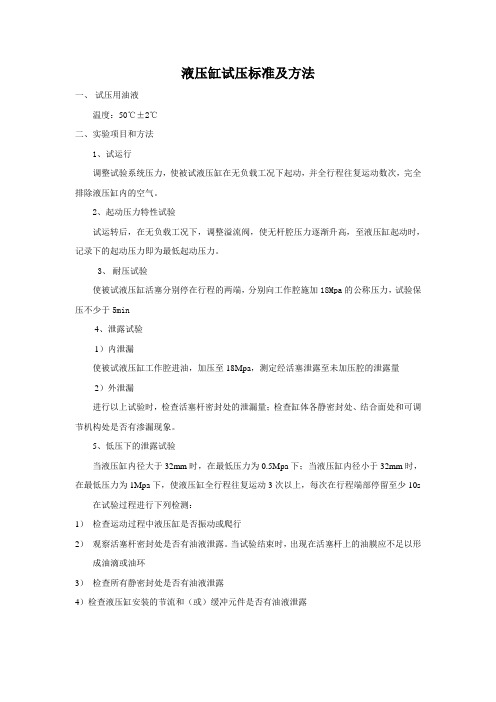
液压缸试压标准及方法
一、试压用油液
温度:50℃±2℃
二、实验项目和方法
1、试运行
调整试验系统压力,使被试液压缸在无负载工况下起动,并全行程往复运动数次,完全排除液压缸内的空气。
2、起动压力特性试验
试运转后,在无负载工况下,调整溢流阀,使无杆腔压力逐渐升高,至液压缸起动时,记录下的起动压力即为最低起动压力。
3、耐压试验
使被试液压缸活塞分别停在行程的两端,分别向工作腔施加18Mpa的公称压力,试验保压不少于5min
4、泄露试验
1)内泄漏
使被试液压缸工作腔进油,加压至18Mpa,测定经活塞泄露至未加压腔的泄露量
2)外泄漏
进行以上试验时,检查活塞杆密封处的泄漏量;检查缸体各静密封处、结合面处和可调节机构处是否有渗漏现象。
5、低压下的泄露试验
当液压缸内径大于32mm时,在最低压力为0.5Mpa下;当液压缸内径小于32mm时,在最低压力为1Mpa下,使液压缸全行程往复运动3次以上,每次在行程端部停留至少10s 在试验过程进行下列检测:
1)检查运动过程中液压缸是否振动或爬行
2)观察活塞杆密封处是否有油液泄露。
当试验结束时,出现在活塞杆上的油膜应不足以形成油滴或油环
3)检查所有静密封处是否有油液泄露
4)检查液压缸安装的节流和(或)缓冲元件是否有油液泄露。
液压试验报告
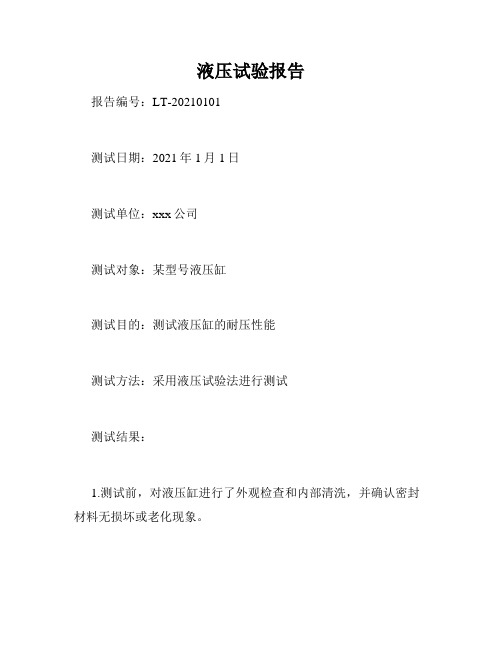
液压试验报告
报告编号:LT-20210101
测试日期:2021年1月1日
测试单位:xxx公司
测试对象:某型号液压缸
测试目的:测试液压缸的耐压性能
测试方法:采用液压试验法进行测试
测试结果:
1.测试前,对液压缸进行了外观检查和内部清洗,并确认密封材料无损坏或老化现象。
2.测试过程中,注入高压液体(压力1.5倍标准工作压力),并持续施加2小时,无明显泄漏。
3.测试结束后,按照要求进行了外观检查,并测定了压力回落情况,回落值小于5%。
结论:本次液压试验结果合格,液压缸耐压性能良好。
附注:本报告仅适用于测试对象所使用的液压缸。
任何未经核实的复制、转载、传播和使用本报告的行为均属于侵犯知识产权的行为,本公司将追究其法律责任。
金宇液压油缸执行标准
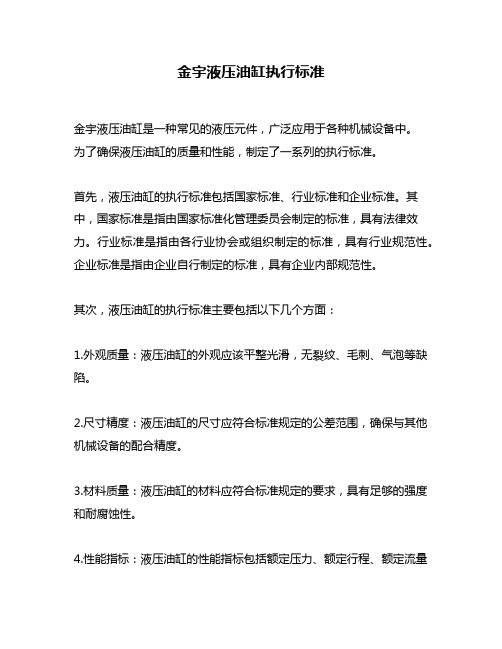
金宇液压油缸执行标准
金宇液压油缸是一种常见的液压元件,广泛应用于各种机械设备中。
为了确保液压油缸的质量和性能,制定了一系列的执行标准。
首先,液压油缸的执行标准包括国家标准、行业标准和企业标准。
其中,国家标准是指由国家标准化管理委员会制定的标准,具有法律效力。
行业标准是指由各行业协会或组织制定的标准,具有行业规范性。
企业标准是指由企业自行制定的标准,具有企业内部规范性。
其次,液压油缸的执行标准主要包括以下几个方面:
1.外观质量:液压油缸的外观应该平整光滑,无裂纹、毛刺、气泡等缺陷。
2.尺寸精度:液压油缸的尺寸应符合标准规定的公差范围,确保与其他机械设备的配合精度。
3.材料质量:液压油缸的材料应符合标准规定的要求,具有足够的强度和耐腐蚀性。
4.性能指标:液压油缸的性能指标包括额定压力、额定行程、额定流量
等,应符合标准规定的要求。
5.试验方法:液压油缸的试验方法应符合标准规定的要求,确保产品的质量和性能。
最后,液压油缸的执行标准对于产品的质量和性能具有重要的保障作用。
企业应该严格按照标准要求进行生产和检验,确保产品的合格率和稳定性。
同时,消费者在购买液压油缸时也应该关注产品是否符合标准要求,以确保产品的质量和性能。
液压油缸质量检验规范
液压油缸质量检验规范
前言
本规范用于液压油缸的质量检验,旨在保证液压油缸的质量,提高产品的可靠性和安全性。
检验标准
1. 外观检验
液压油缸的外观应该无裂纹、无变形、无划痕、表面无锈蚀,在装配后应该无泄漏。
2. 尺寸检验
液压油缸的内径、外径、活塞杆直径、活塞杆长度应该符合设计要求。
3. 强度检验
液压油缸在压力测试时,应该承受规定压力2倍的测试压力,无破裂、变形和泄漏等现象。
4. 密封性检验
液压油缸在压力测试时,应该保持规定压力10分钟,没有任何泄漏现象,且在经过密封性试验后活塞杆不会出现损坏。
检验方法
1. 外观检验
使用肉眼或放大镜仔细检查液压油缸表面,如果发现异常,应该进行更加细致的检查。
2. 尺寸检验
使用专业的检测设备,比如游标卡尺、外径千分尺、内景千分尺等,测量液压油缸的相关尺寸。
3. 强度检验
沿对称轴向液压油缸施加试验压力,在压力测试过程中观察液压油缸的变形情况和是否有漏油现象。
4. 密封性检验
涂抹液压油缸需要检验的密封部位,将液压油缸放入水中进行压力测试,观察是否有气泡冒出,检查活塞杆样子并观察密封性。
结论
液压油缸的检验可以保障其质量,减少使用过程中出现的故障,确保液压油缸能够在高压下稳定运行,提高设备的工作效率和安全性。
油缸耐久试验方法
油缸耐久试验方法
油缸耐久试验方法是一种用于评估油缸的耐久性能的测试方法。
下面是一个常见的油缸耐久试验方法:
1. 准备工作:选取一台测试设备,例如液压测试机。
准备好适合测试的油缸样品,并进行装配。
2. 设置测试条件:根据实际应用需求和相关标准,确定测试的负载、速度、压力、振动等参数。
这些参数应该在设备的工作范围内,并能够模拟实际工作环境。
3. 开始测试:将装配好的油缸样品安装在测试设备上,确保连接牢固。
启动测试设备,将设定的负载施加到油缸上。
4. 持续测试:持续对油缸施加负载并记录测试数据,例如使用传感器测量位移、力、压力等。
可以使用计算机控制和数据记录系统来自动记录数据。
5. 检查和维护:定期检查油缸的外观和内部状况,确保油缸没有明显的损坏或泄漏。
按照维护需求进行维护,例如更换密封件等。
6. 终止测试:继续测试直到达到一定的测试次数或耐久要求。
停止测试设备并关闭系统。
7. 数据分析:根据测试数据分析油缸的性能表现。
可以比较初始时和结束时的测试数据,评估油缸的耐久性能以及任何潜在
问题。
8. 结论和报告:根据测试结果提供结论,并撰写测试报告。
如果有发现问题或改进建议,应该提供解决方案或建议。
需要注意的是,油缸的耐久试验方法可能因应用领域的不同而有所差异,因此在进行测试之前应该确认适用的标准和要求。
油缸出厂检验报告
油缸出厂检验报告
1. 概述
本文档是针对油缸的出厂检验进行的报告,旨在对油缸的质量进行评估和确认。
油缸作为一种重要的工业设备,广泛应用于各种机械设备和工程项目中。
本文档将介绍油缸的基本信息、检验方法和结果,以及对检验结果进行的评估和建议。
2. 油缸基本信息
油缸是一种用于储存和传输液体或气体的容器,它通常由金属材料制成,具有一定的强度和密封性能。
油缸通常分为储油缸和液压缸两种类型,分别用于油气回路和液压系统中。
本次检验报告的对象是一台液压油缸。
3. 检验方法
为了对油缸的质量进行全面评估,我们采取了以下检验方法:
3.1 外观检验:检查油缸表面是否有明显的损伤、划痕或锈蚀。
3.2 尺寸检验:测量油缸的外径、内径、长度等尺寸,与设计要求进行对比。
3.3 压力测试:在设定的压力下,对油缸进行静态和动态负荷测试,观察其变形和漏液情况。
3.4 密封性检验:通过注入水或气体,检测油缸的密封性能,观察是否有漏液或漏气现象。
3.5 功能检验:安装油缸到相应设备中,测试其在实际工作环境中的功能和性能。
4. 检验结果
根据以上检验方法,我们对油缸进行了全面的检验,并得出以
下结果:
4.1 外观检验结果:油缸表面无明显损伤、划痕或锈蚀。
4.2 尺寸检验结果:油缸的外径、内径、长度等尺寸符合设计要求。
4.3 压力测试结果:油缸在设定的压力下未出现明显变形和漏液现象。
4.4 密封性检验结果:油缸密封性良好,未出现漏液或漏气现象。
液压缸试验要求
液压缸试验
1、液压缸外观要求:
a活塞杆镀层均匀,无磕碰划痕等缺陷
b缸筒及耳轴等外观无磕碰,涂漆均匀
c油缸接口平整无磕碰等缺陷
d耳轴铜套需符合规定要求
2、油缸空载试验:
A油缸接好后,反复动作几次将缸内气体全部排净
B慢慢调紧溢流阀螺钉逐步升压,观察油缸最小动作压力,工作压力的5%,反复动作两次无爬行现象
3、带负载在工作压力下,反复动作50次无爬行现象
4、带负载在工作压力下,活塞杆及接头密封等处无渗漏现象
5、内泄漏:油缸进出油口前分别接压力表高压球阀检测泄漏量,观察压力表,(允许有压力降20min 降2MPa左右)
6、耐压试验:工作压力的1.25倍,保压2min无泄漏
7、试验后,油口用油塞封堵,活塞杆要有防护措施,油缸外清理干净。
- 1、下载文档前请自行甄别文档内容的完整性,平台不提供额外的编辑、内容补充、找答案等附加服务。
- 2、"仅部分预览"的文档,不可在线预览部分如存在完整性等问题,可反馈申请退款(可完整预览的文档不适用该条件!)。
- 3、如文档侵犯您的权益,请联系客服反馈,我们会尽快为您处理(人工客服工作时间:9:00-18:30)。
液压缸试验方法
Document number:WTWYT-WYWY-BTGTT-YTTYU-2018GT
目录
液压缸试验方法
1 范围
本标准规定了液压缸试验方法。
本标准适用于以液压油(液)为工作介质的液压缸(包括双作用液压缸和单作用液压缸)的型式试验和出厂试验。
本标准不适用于组合式液压缸。
2 规范性引用文件
下列文件中的条款通过本标准的引用而成为本标准的条款。
凡是注日期的引用文件,其随后所有的修改单(不包括勘误的内容)或修订版均不适用于本标准,然而,鼓励根据本标准达成协议的各方研究是否可使用这些文件的最新版本。
凡是不注日期的引用文件,其最新版本适用于本标准。
GB/T 14039-2002 液压传动油液固体颗粒污染等级代号(ISO 4406:1999,MOD) GB/T 17446 流体传动系统及元件术语(GB/T 17446-1998,idtI SO 5598:1985) 3 术语和定义
在GB/T 17446中给出的以及下列术语和定义适用于本标准。
最低起动压力the minimum pressure
液压缸起动的最低压力。
无杆腔the cavity with out piston rod
液压缸没有活塞杆的一腔。
有杆腔the cavity with piston rod
液压缸有活塞杆伸出的一腔。
负载效率load efficiency
液压缸的实际输出力与理论输出力的比值。
4 符号和单位
本标准使用的符号及其单位见表l。
表1 符号和单位
5 试验装置和试验条件
试验装置
5.1.1液压缸试验装置见图1和图2。
试验装置的液压系统原理图见图3~图5。
图1 加载缸水平加载试验装置
图2 重物模拟加载试验装置
1——过滤器;
2——液压泵;
3——溢流阀;
4——单向阀;
5——电磁换向阀;
6——单向节流阀;
7——压力表开关;
8——压力表;
9——被试缸;
10——流量计;
11——温度计。
图3 出厂试验液压系统原理图
1——过滤器;
2——液压泵;
3——溢流阀;
4——单向阀;
5——流量计;
6——电磁换向阀;
7——单向节流阀;
8——压力表;
9——压力表开关;
10——被试缸;
11——加载缸;
12——截止阀;
13——温度计。
图4 型式试验液压系统原理图
1——过滤器;
2——液压泵;
3——压力表开关;
4——压力表;
5——单向阀;
6——流量计;
7——电磁换向阀;
8——单向节流阀;
9——被试缸;
10——测力计;
11——加载缸;
12——溢流阀;
13——温度计。
图5 多级液压缸试验台液压系统原理图
5.1.2测量准确度
测量准确度采用B,C两级。
测量系统的允许系统误差应符合表2的规定。
表2 测量系统允许系统误差
试验用油液
5.2.1黏度
油液在40℃时的运动黏度应为29mm2/s~74mm2/s。
注:特殊要求除外。
5.2.2 温度
除特殊规定外,型式试验应在50℃士2℃下进行;出厂试验应在50℃士4℃下进行。
出厂试验允许降低温度,在15℃~45℃范围内进行,但检测指标应根据温度变化进行调整,保证在50℃士4℃时能达到产品标准规定的性能指标。
5.2.3 污染度等级
试验系统油液的固体颗粒污染度等级不得高于GB/T 14039规定的19/15或一
/19/15。
5.2.4 相容性
试验用油液应与被试液压缸的密封件材料相容。
稳态工况
试验中,各被控参量平均显示值在表3规定的范围内变化时为稳态工况。
应在稳态工况下测量并
记录各个参量。
表3 被控参量平均显示值允许变化范围
6 试验项目和试验方法
试运行
调整试验系统压力,使被试液压缸在无负载工况下起动,并全行程往复运动数次,完全排除液压缸内的空气。
起动压力特性试验
试运转后,在无负载工况下,调整溢流阀,使无杆腔(双活塞杆液压缸,两腔均可)压力逐渐升高,至液压缸起动时,记录下的起动压力即为最低起动压力。
耐压试验
使被试液压缸活塞分别停在行程的两端(单作用液压缸处于行程极限位置),分别向工作腔施加倍的公称压力,型式试验保压2 min;出厂试验保压10s。
耐久性试验
在额定压力下,使被试液压缸以设计要求的最高速度连续运行,速度误差为士1000。
一次连续运行8h以上。
在试验期间,被试液压缸的零件均不得进行调整。
记录累计行程。
泄漏试验
6.5.1 内泄漏
使被试液压缸工作腔进油,加压至额定压力或用户指定压力,测定经活塞泄漏至未加压腔的泄漏量。
6.5.2 外泄漏
进行,,,6.5.1规定的试验时,检测活塞杆密封处的泄漏量;检查缸体各静密封处、结合面处和可调节机构处是否有渗漏现象。
6.5.3 低压下的泄漏试验
当液压缸内径大于32mm时,在最低压力为( 5bar)下;当液压缸内径小于等于32 mm时,在1 MPa(10 bar)压力下,使液压缸全行程往复运动3次以上,每次在行程端部停留至少10s。
在试验过程进行下列检测:
a)检查运动过程中液压缸是否振动或爬行;
b)观察活塞杆密封处是否有油液泄漏。
当试验结束时,出现在活塞杆上的油膜应不足以形成油滴或油环;
c)检查所有静密封处是否有油液泄漏;
d)检查液压缸安装的节流和(或)缓冲元件是否有油液泄漏;
e)如果液压缸是焊接结构,应检查焊缝处是否有油液泄漏。
缓冲试验
将被试液压缸工作腔的缓冲阀全部松开,调节试验压力为公称压力的50%,以设计的最高速度运行,检测当运行至缓冲阀全部关闭时的缓冲效果。
负载效率试验
将测力计安装在被试液压缸的活塞杆上,使被试液压缸保持匀速运动,按下式计算出在不同压力下的负载效率,并绘制负载效率特性曲线,如图6。
图6 负载效率特性曲线
高温试验
在额定压力下,向被试液压缸输人90℃的工作油液,全行程往复运行1h。
行程检验
使被试液压缸的活塞或柱塞分别停在行程两端极限位置,测量其行程长度。
7 型式试验
型式试验应包括下列项目:
——试运转(见;
——起动压力特性试验(见;
——耐压试验(见;
——泄漏试验(见;
——缓冲试验(见;
——负载效率试验(见 );
——高温试验(当对产品有此要求时)(见 );
——耐久性试验(见;
——行程检验(见。
8 出厂试验
出厂试验应包括下列项目:
——试运转(见;
——起动压力特性试验(见;
——耐压试验(见;
——泄漏试验(见;
——缓冲试验(见;
——行程检验(见。
9 试验报告
试验过程应详细记录试验数据。
在试验后应填写完整的试验报告,试验报告的格式参照表4。
表4 液压缸试验报告格式
10 标注说明(引用本标准)
当选择遵守本标准时,建议制造商在试验报告、产品目录和产品销售文件中采用以下说明:“液压缸的试验符合GB/T 15622-2005《液压缸试验方法》”。