QCSR015-2006《铁道车辆用铸钢件通用技术条件》
Q 球墨铸铁件通用技术条件

Q/ZZ 30015—××××
球墨铸铁件通用技术条件
1 范围
本标准规定了本公司使用的球墨铸铁件的通用技术要求、验收和检验方法。 本标准适用于在砂型或导热性与砂型相当的铸型中铸造的普通和低合金且石墨为球状的球墨铸铁 件(以下简称铸件)。
2 规范性引用文件
下列文件对于本标准的应用是必不可少的。凡是注日期的引用文件,仅所注日期的版本适用于本标 准。凡是不注日期的引用文件,其最新版本(包括所有的修改单)适用于本标准。
附件 2:
Q/ZZ
中国重型汽车集团有限公司企业标准
Q/ZZ 30015—××××
代替Q/ZZ 30015-2008
球墨铸铁件通用技术条件
(征求意见稿)
××××-××-××发布
××××-××-××实施
中国重型汽车集团有限公司 发布
Q/ZZ 30015—××××
前言
本标准以Q/ZZ 30015-2008版为基础,结合GB/T1348和当前实际生产情况和相关技术文件进行修订。 本标准代替Q/ZZ 30015-2008,与Q/ZZ 30015-2008相比,主要技术内容修订如下: ——结构方面做了较大修改; ——增加了“3.1 球墨铸铁牌号”; ——增加了球墨铸铁材料牌号ZQQT1300-3和相关技术要求,删除了D25-6球墨铸铁材料牌号和相关 技术要求, ——将硬度单位“HBS”更改为“HBW”,将“主要金相组织含量”更改为“主要基体组织”; ——增加了附铸试样、本体试样的相关技术要求; ——将渗碳体改为碳化物; ——删除了金相组织中关于珠光体形态的技术要求; ——修改了磷共晶的技术要求,将“磷共晶形态和数量:不得有三元磷共晶-渗碳体复合物和网状 磷共晶。其他形状的磷共晶不得多于1%”修改为“磷共晶数量:不得多于1%”; ——修改了“铸件加工余量”章节的内容,删除了图1—图5; ——修改了球墨铸铁订货要求,删除了“球墨铸铁件订货要求参照GB/T 9439附录D规定执行”,增 加了“4.1 订货信息”和“4.2订货要求”。 ——增加了“6.3铸件复验和其他检验按GB/T1348第10、11章规定执行”。 本标准由中国重型汽车集团有限公司提出。 本标准由中国重型汽车集团有限公司技术发展中心负责归口。 本标准起草单位:中国重型汽车集团有限公司技术发展中心。 本标准主要起草人:刘长森、黄国涛、王正军。 本标准替代标准的历次版本发布情况为: ——Q/ZZ 30015-95JT 、Q/ZZ 30015-2008。
QCSR018-2006《机车车辆用铸钢件补焊技术条件》

中国南方机车车辆工业集团企业标准
Q/CSR 018—2006
机车车辆用铸钢件补焊技术条件
Specifications for weld repair of steel castings for locomotive and Rolling stock
2006-02-20 发布
2006-04-01 实施
图 1 非贯通坡口的型式尺寸
a
1—垫板。 a 垫板焊后除去。如能两面施焊时,一面焊后,应清根,再焊另一面。
图 2 贯通单面坡口的型式尺寸
a
a 对厚断面,宜开双面坡口。一面焊后,应清根,再焊另一面。
图 3 贯通双面坡口的型式尺寸
2
Q/CSR 018不小于 3mm。正面焊接完成后,应将根部未焊透、焊瘤等焊接缺陷清
GB/T 5117—1995 碳钢焊条 (eqv ANSI/AWS A5.1:1991 ) GB/T 5118—1995 低合金钢焊条 (neq ANSI/AWS A5.5:1981) GB/T 811—1995 气体保护电弧焊用碳钢、低合金钢焊丝 ( neq ANSI/AWS A5.18:1979 ) GB 9448—1999 焊接与切割安全 (eqv ANSI/AWS Z49.1) JB/T 3223—1996 焊接材料质量管理规程 Q/CSR 014—2006 机车车辆用二氧化碳气体保护焊技术条件 Q/CSR 015—2006 机车车辆用铸钢件通用技术条件
I
Q/CSR 018—2006
机车车辆用铸钢件补焊技术条件
1 范围
本标准规定了碳素钢及低合金钢铸件缺陷补焊的基本要求、材料、焊前准备、施焊、热处理及质量 检验。
本标准适用于机车车辆用碳素钢及低合金钢铸件缺陷的补焊。
(整理)《铁道货车通用技术条件》GB.

铁道货车通用技术条件GB/T5600-2006铁道货车通用技术条件General technical specification for railway freight car 目次前言引言1 范围2 规范性引用文件3 一般要求4 材料要求5 制造要求6 涂装与标记7 各车种要求附录A(规范性附录) 通用敞、棚、平车技术要求附录B(规范性附录) 专用货车技术要求附录C(规范性附录) 罐车通用技术要求附录D(规范性附录) 机械冷藏车通用技术要求前言本标准代替GB/T5600-1997《铁道货车通用技术条件》。
与前版标准相比,本标准的主要内容变化如下:——一般要求中,新增了结构、运用、安全性等方面的内容;——材料要求中,取消了各类铸件、锻件、焊丝、弹簧等的材质要求,新增耐大气腐蚀钢、不锈钢、铝合金、铸钢件、涂料及其他金属、非金属的材质要求;——车体制造要求、转向架、制动装置、车钩缓冲装置、落成要求、涂装标记等按现车结构和新标准进行了修订;——新增了附录A“通用敞、棚、平车技术要求”;——新增了附录B“专用货车技术要求”;——新增了附录C“罐车通用技术要求”;——新增了附录D“机械冷藏车通用技术要求”。
本标准规定了铁道货车的基本要求,铁道货车的检查与试验规则见GB/T5601《铁道货车检查与试验规则》。
本标准的附录A、附录B、附录C、附录D为规范性附录。
本标准由铁道部提出。
本标准由铁道部标准计量研究所归口。
本标准起草单位:铁道部标准计量研究所、齐齐哈尔铁路车辆(集团)有限责任公司、株洲车辆厂、四方车辆研究所、北京二七车辆厂、西安车辆厂、太原机车车辆厂、武昌车辆厂、眉山车辆厂。
本标准主要起草人;齐兵、孙琰、卢静、雷青平、朱森、孙明道、田葆栓、章薇、肖江石、朱秀琴、刘翀原、王宏。
本标准所代替标准的历次版本发布情况为:——GB/T5600-1985、GB/T5600-1997。
在铁道标准体系中,货车整车标准除GB/T5600《铁道货车通用技术条件》外,对不同类型的货车还制定有单项标准。
铁路货车超偏载检测装置技术条件 本技术条件依据《铁路货车超偏载
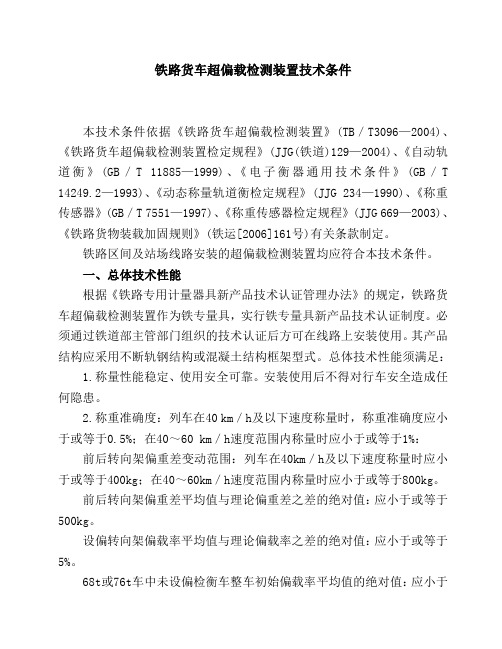
铁路货车超偏载检测装置技术条件本技术条件依据《铁路货车超偏载检测装置》(TB/T3096—2004)、《铁路货车超偏载检测装置检定规程》(JJG(铁道)129—2004)、《自动轨道衡》(GB/T 11885—1999)、《电子衡器通用技术条件》(GB/T 14249.2—1993)、《动态称量轨道衡检定规程》(JJG 234—1990)、《称重传感器》(GB/T 7551—1997)、《称重传感器检定规程》(JJG 669—2003)、《铁路货物装载加固规则》(铁运[2006]161号)有关条款制定。
铁路区间及站场线路安装的超偏载检测装置均应符合本技术条件。
一、总体技术性能根据《铁路专用计量器具新产品技术认证管理办法》的规定,铁路货车超偏载检测装置作为铁专量具,实行铁专量具新产品技术认证制度。
必须通过铁道部主管部门组织的技术认证后方可在线路上安装使用。
其产品结构应采用不断轨钢结构或混凝土结构框架型式。
总体技术性能须满足:1.称量性能稳定、使用安全可靠。
安装使用后不得对行车安全造成任何隐患。
2.称重准确度:列车在40 km/h及以下速度称量时,称重准确度应小于或等于0.5%;在40~60 km/h速度范围内称量时应小于或等于1%:前后转向架偏重差变动范围:列车在40km/h及以下速度称量时应小于或等于400kg;在40~60km/h速度范围内称量时应小于或等于800kg。
前后转向架偏重差平均值与理论偏重差之差的绝对值:应小于或等于500kg。
设偏转向架偏载率平均值与理论偏载率之差的绝对值:应小于或等于5%。
68t或76t车中未设偏检衡车整车初始偏载率平均值的绝对值:应小于或等于5%。
3.称重范围:18—120t。
4.自动判别机车车辆通过及确定通过速度;实现车种、车型、车号、机车车号及配属段的自动识别功能。
5.系统能够对传感器、通道、采集卡等部件的状态参数进行自检并实时上传。
能够自动累计传感器承受冲击次数,并对传感器剩余寿命预警。
铸造机械通用技术条件标准

3.3 铸造机械通用技术条件
3.3.2 GB/T 25711-2010 与JB/T 1644-2006结构
• • • • • 加工和装配质量 外观质量 试验方法 检验规则 标志、包装、运输和贮存
• • • • •
加工和装配质量 外观质量 检验和试验 包装、标志、运输 机器质量保证期
3.3 铸造机械通用技术条件
6 出厂的机器应保证成套性,备有能正常使用所需的备品备件、易损件,并在 相应的技术文件中规定 备品备件、易损件均应保证使用性能和互换性。
3.3 铸造机械通用技术条件
3.3.2 GB/T 25711-2010 与JB/T 1644-2006结构
• • • • 安全与卫生GB/T 25711-2010 机器应按GB 20905 和GB 5083的规定采取相应的安全措施防止对人或设备造 成损害。 机器排放的废气、废水、废渣等有害物,应符合国家有关法律、法规及标准 的规定 机器运转时不应有异常的声响,机器的噪声应符合国家法律法规及有关标准 的规定
3.3 铸造机械通用技术条件
3.3.2 GB/T 25711-2010 与JB/T 1644-2006结构
• • • 成套性GB/T 25711-2010 出厂的机器应保证成套性,备有能正常使用所需的备品备件、易损件和专用 工具,并在相应的技术文件中规定 备品备件、易损件均应保证使用性能和互换性。
3.3 铸造机械通用技术条件
3.3.2 GB/T 25711-2010 与JB/T 1644-2006结构
3.3.2 GB/T 25711-2010 与JB/T 1644-2006结构
• • • • GB/T 25711-2010 型号、名称和参数 机器的型号、名称应按照JB/T3000和JB/T9978的规定进行编制和给出 机器的型式、参数与尺寸应符合有关标准或技术协议的规定的规定。
ISO车辆标准(ISO vehicle standards)

修改件1.白炽灯.安全规范.第3部分:钨卤灯(非车用)
Amendment 1 - Incandescent lamps - Safety specifications - Part 3: Tungsten-halogen lamps (non-vehicle)
IEC 60349-1 Edition 1.1-2002
电力牵引.铁路与道路车辆用旋转电机.第1部分:除电子变流器供电的交流电动机之外的旋转电机
Electric traction - Rotating electrical machines for rail and road vehicles - Part 1: Machines other than electronic convertor-fed alternating current motors
IEC 60432-3 Edition 1.1-2005
白炽灯.安全规范.第3部分:钨卤灯(非车用)
IEC 60357 AMD 1-2006
卤钨灯(非车辆用).性能规范.修改件1
Tungsten halogen lamps (non-vehicle) - Performance specifications; Amendment 1
IEC 60357-2002
卤钨灯(非车辆用).性能规范
Tungsten halogen lamps (non-vehicle) - Performance specifications
IEC 60034-2 AMD 1-1995
旋转电机 第2部分:旋转电机损耗和效率的试验测定方法(不包括牵引车辆用电机) 修改1
Rotating electrical machines - Part 2: Methods of determining losses and efficiency of rotating electrical machinery from tests (excluding machines for traction vehicles); Amendment 1
机车车辆用球墨铸铁件通用技术条件
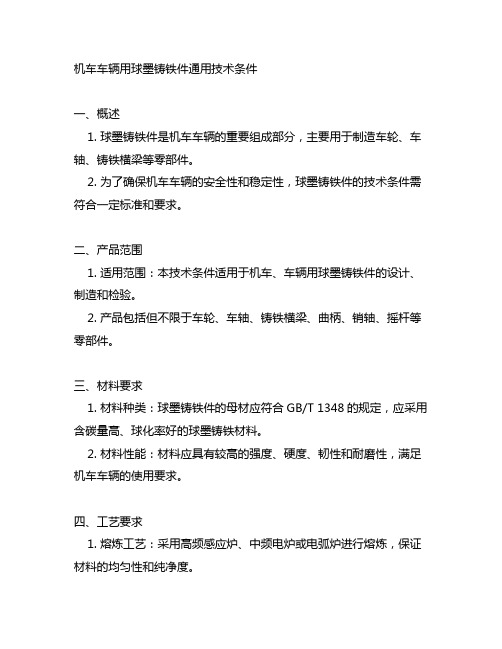
机车车辆用球墨铸铁件通用技术条件一、概述1. 球墨铸铁件是机车车辆的重要组成部分,主要用于制造车轮、车轴、铸铁横梁等零部件。
2. 为了确保机车车辆的安全性和稳定性,球墨铸铁件的技术条件需符合一定标准和要求。
二、产品范围1. 适用范围:本技术条件适用于机车、车辆用球墨铸铁件的设计、制造和检验。
2. 产品包括但不限于车轮、车轴、铸铁横梁、曲柄、销轴、摇杆等零部件。
三、材料要求1. 材料种类:球墨铸铁件的母材应符合GB/T 1348的规定,应采用含碳量高、球化率好的球墨铸铁材料。
2. 材料性能:材料应具有较高的强度、硬度、韧性和耐磨性,满足机车车辆的使用要求。
四、工艺要求1. 熔炼工艺:采用高频感应炉、中频电炉或电弧炉进行熔炼,保证材料的均匀性和纯净度。
2. 浇注工艺:采用自动化、精密化的浇注设备进行铸造,保证铸件的密度和无气孔、夹渣等缺陷。
五、外观要求1. 表面平整度:表面不得有明显的凹凸、裂纹等缺陷,保证外观质量。
2. 表面清洁度:表面不得沾有铁屑、油污等杂质,保证铸件的清洁度。
六、尺寸要求1. 全尺寸精度:按照设计要求进行尺寸检验,保证球墨铸铁件的准确性和稳定性。
2. 重量要求:球墨铸铁件的重量应符合设计要求,不得超过或低于标准重量。
七、机械性能要求1. 强度:球墨铸铁件的抗拉强度、屈服强度、延伸率等机械性能指标应符合相关标准。
2. 硬度:表面硬度和心部硬度应符合设计要求,保证零部件的使用寿命和稳定性。
八、表面质量检验1. 表面检验:采用目视、手感和放大镜等工具对球墨铸铁件的表面质量进行检验。
2. 探伤检验:采用超声波、X射线或磁粉探伤等技术对铸件进行内部缺陷检测。
九、检验方法1. 检验设备:应配备齐全的检测设备,包括硬度计、三坐标测量仪、金相显微镜等。
2. 检验程序:按照相关标准和规定执行检验程序,确保球墨铸铁件的质量可控。
十、贮存和包装要求1. 贮存条件:球墨铸铁件应存放在干燥、通风、无腐蚀性气体的仓库中。
铸件采购验收技术条件
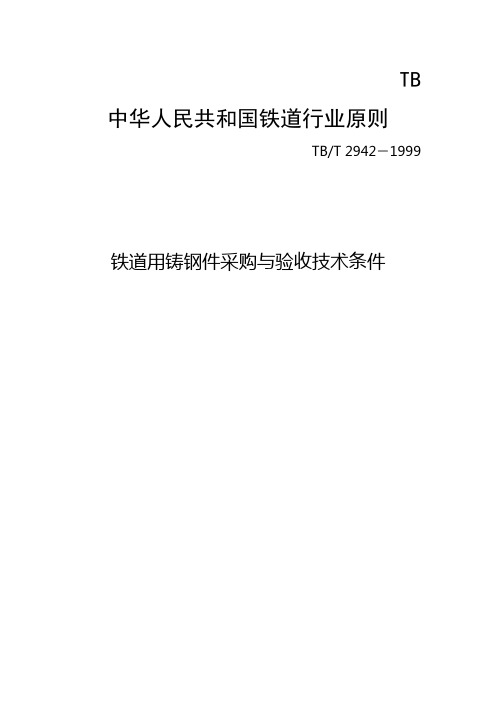
TB 中华人民共和国铁道行业原则TB/T 2942-1999 铁道用铸钢件采购与验收技术条件1999—02—13发布1999—09—01实行中华人民共和国铁道部发布铁道用铸钢件采购与验收技术条件1. 范畴本原则规定了铁道用铸钢件旳级别、技术规定,实验措施和检查规则。
本原则合用于机车车辆及其他多种用途旳级别为A、B、C、D和E旳碳素钢和合金钢铸件。
2. 引用原则下列原则所涉及旳条文,通过在本原则中引用而构成为本原则旳条文。
本原则出版时,所示版本均为有效。
所有原则都会被修订,使用本原则旳各方应探讨使用下列原则最新版本旳也许性。
GB/T 225—88 钢旳淬透性末端淬火实验措施GB/T 228—87 金属拉伸实验措施GB/T 229—94 金属夏比缺口冲击实验措施GB/T 231—84 金属布氏硬度实验措施GB/T 5117—1995 碳钢焊条GB/T 5118—1995 低合金钢焊条GB 6803—86 铁素体钢旳无塑性转变温度落锤实验措施ASTM E604—83 (1994复审) 金属材料旳动态扯破实验措施ASTM A255—95 钢旳淬透性末端淬火原则实验措施3. 采购旳基础除非另有规定,A级钢铸件应以不退火、退火或正火状态供货。
B级钢铸件应以正火、正火加回火状态供货。
C级钢铸件应以正火加回火或淬火加回火状态供货。
D级钢和E级钢铸件应以淬火加回火状态供货。
3.1. 根据采购方旳规定,检查合格证将成为验收旳根据。
检查合格证应涉及这样旳阐明,即铸件是按照本原则旳所有合用条款来进行制造、取样、实验和检查旳,并符合原则条款旳规定。
每一份提供旳检查合格证应由制造方旳指定代表签字。
4. 记录制造方应将所售铸件旳熔炼炉次旳力学性能和化学分析报告保存不少于5年。
这些报告供采购方备查。
5. 熔炼措施钢水可以用平炉、电弧炉、坩锅炉、转炉或氧气顶吹转炉熔炼。
6. 热解决铸件在热解决前应予清理。
铸件内腔不得留有成块旳造型材料或被造型材料所堵塞。
- 1、下载文档前请自行甄别文档内容的完整性,平台不提供额外的编辑、内容补充、找答案等附加服务。
- 2、"仅部分预览"的文档,不可在线预览部分如存在完整性等问题,可反馈申请退款(可完整预览的文档不适用该条件!)。
- 3、如文档侵犯您的权益,请联系客服反馈,我们会尽快为您处理(人工客服工作时间:9:00-18:30)。
中国南方机车车辆工业集团企业标准
Q/CSR 015—2006
机车车辆用铸钢件通用技术条件
General Technical Conditions of Steel Castings for Locomotive & Rolling Stock Application
2006-02-20 发布
620
415
22
—
45
淬火+回火 27(-40℃)
D级
725
585
17
—
35
E级
830
690
14
—
30
27(-40℃) 27(-40℃)
ZG200-400
400
200
—
25
40
30
ZG230-450
450
230
—
22
32
25
ZG270-500
500
270
—
18
25
22
ZG310-570
570
310
—
2006-04-01 实施
中国南方机车车辆工业集团公司 发布
Q/CSR 015—2006
前言
本标准是在原TB/T 146—1991《铁道机车车辆用碳钢铸件通用技术条件》的基础上制定的。 本标准与原TB/T 1464—1991相比主要变化如下: —— 铸件化学成分和力学性能增加了A级、B级、B+级、C级、D级和E级钢的内容; —— 铸件化学成分增加了对铜的要求; —— 修改了非加工面浇冒口残留量; —— 增加了铸件内部缺陷的规定; —— 增加了铸造表面粗糙度的要求; —— 取消了铸件圆角半径的规定; —— 增加了采购时,试样可从铸件上切取的要求。 本标准的附录A为规范性附录。 本标准由中国南方机车车辆工业集团公司提出。 本标准由中国南车集团标准化工作委员会工艺综合组归口。 本标准起草单位:中国南车集团株洲车辆厂、中国南车集团戚墅堰机车车辆工艺研究所、中国南车 集团戚墅堰机车车辆厂、中国南车集团浦镇车辆厂。 本标准主要起草人:骆毅、张耀宏、蒋田芳、彭春生、沈中青
b) 不影响组装,离边缘或孔边不小于 10 mm(小于 40 kg 铸件不小于 5 mm)、深不大于 1 mm, 每块面积不大于 4 cm2 和总面积不大于所加工面积 1/20 的黑皮。 3.14.3 非加工面上允许存在的缺陷
a) 小于 40 kg 铸件的面上,直径不大于 5 mm 或其周长不大于 15 mm、深不大于 4 mm 的缺陷; b) 壁厚小于 20 mm 铸件的面上,直径不大于 10 mm 或其周长不大于 30mm、深不大于 4 mm 的
下屈服强度 ReL
N/mm2
断后伸长率 %
A50 mm
A
断面收缩率 Z %
冲击吸收功(V 形缺口) Akv J
A 不退火
415
级 退火或正火
415
B级
485
B+级
552
205
22
—
30
205
26
—
38
260
24
—
36
345
24
—
36
— —
20(-7℃) 20(-7℃)
正火+回火 20(-18℃)
C级
4 试验方法和检验规则
4.1 铸件由质检部门进行检查、验收、签认合格证,用户有权根据本标准或供需合同抽查核对分析。 4.2 铸件化学成分以碳、硅、锰、磷、硫、铜为验收依据;力学性能以抗拉强度、下屈服强度、断后 伸长率和断面收缩率为验收依据,低合金钢应增加冲击吸收功为验收依据。
3
Q/CSR 015—2006
a) 直径不大于 5 mm 或其周长不大于 15 mm,深不大于该处壁厚 1/8(深度最大值 8 mm),在每 100 cm2 面积上(小于 100 cm2 面积按 100 cm2 计算)不多于两个,间距不小于 20 mm,离边缘(小于 10 kg 铸件不计)或孔边不小于 10 mm(直径和深度不大于 1 mm 的针孔不计)的缺陷。在缺陷背面的 相对位置上不允许同时存在;
b) 拉伸试样断在标距之外或断在机械刻划的标距标记上;
c) 试样加工不当;
d) 试样中存在铸造缺陷;
e) 试验设备故障。
4.6 铸件表面粗糙度的评定方法按 GB/T 15056—1994 规定执行。
4.7 铸件公称重量的检验按 GB/T 11352—1989 中 8.1 规定执行,铸件重量公差的检验按 GB/T 11351—
3.8 铸件尺寸公差等级应在图样上或技术条件中规定。铸件尺寸公差值和错型值应按 GB/T 6414—1999
的规定,由供需双方商定。
3.9 铸件起模斜度在图样上无规定时按 JB/T 5105—1991 的规定执行。
3.10 在图样上无规定时,铸造表面粗糙度 Ra 的上限值不大于 100µm。
2
Q/CSR 015—2006 3.11 铸件重量公差在图样、技术条件或供需合同上无规定时应符合 GB/T 11351—1989 的规定。 3.12 铸件加工余量在图样上无规定时应符合 GB/T 6414—1999 第 10 章的规定。 3.13 铸件的金相组织及非金属夹杂物应符合图样或有关文件规定。 3.14 在满足图样或技术条件规定的情况下,铸件表面允许存在不超过本标准规定范围内的缺陷。 3.14.1 加工面上允许存在加工余量范围内的缺陷。 3.14.2 加工后的表面上允许存在的缺陷:
3.5 不影响加工、组装和使用的浇冒口残留量应符合表 3 的规定。非加工面的残留部位应修至与铸件
表面平滑过渡。
表3
单位为毫米
浇冒口颈最大尺寸
≤100
>100~200
>200
加工面
±3
残留量
+6
+10
-3
-3
非加工面
±3
3.7 铸件图样上无规定时,铸件宜在热态下校正,ZG200-400、ZG230-450 铸件允许在常温下校正。
允许提高 0.04%的锰,对牌号 ZG200-400 的锰的最高含量为 1.00%,其余牌号的锰的最高含量为 1.20%。
3.1.2 除表 1 规定的成分外,其他元素的含量可由制造厂选择,以获得所规定的力学性能。
3.2 铸件力学性能应符合表 2 规定的最低要求。
表2
力学性能
铸钢牌号
抗拉强度 Rm
N/mm2
定值的 80%。
4.4.6 冲击试验按 GB/T 2291—994 规定,先试三个试样,平均值合格,允许其中一个值不低于规定值
的 2/3。不符合上述规定时,重新复试三个,试验结果与原始结果相加重新计算平均值合格,否则允许
重新热处理。
4.5 因下列原因之一使试验结果不合格,该试验无效。
a) 试样安装不当或试验功能不正常;
20 mm,离边缘(小于 10 kg 铸件不计)或孔边不小于 10 mm 的缺陷。在缺陷背面的相对位置 上不允许同时存在。 d) 离边缘(小于 10 kg 铸件不计)或孔边不小于 10 mm,直径和深度不大于 3 mm,其一块面积 或几块面积之和不大于该处面积 1/10(直径和深度不大于 1 mm 的针孔不计)的局部缩松和气 孔; e) 不影响加工和组装、离边缘(小于 40 kg 铸件不计)或孔边不小于 10 mm、一块面积或几块面 积之和不大于该面积的 1/20、深不大于 2 mm 的鼠尾、沟槽和高不大于 2 mm 的胀砂; f) 不影响加工、组装和使用的变形。 3.15 除图样或技术条件另有规定,超过 3.14 规定的缺陷允许按 Q/CSR018—2006 的规定进行焊修。 3.16 铸件内部缺陷由供需双方根据铸件的关键重要程度、铸件的重量、大小、壁厚等协商确定。 3.17 要求水、风、油压的铸件,因缩松、疏松等缺陷而泄漏,允许补焊后再经水、风、油压试验。 3.18 铸件质量保证期按产品技术条件或供需合同规定执行。
15
21
15
ZG340-640
640
340
—
10
18
10
3.3 铸件按 GB/T 11352—1989 中 4.4 和 TB/T 2942—1999 规定进行热处理,按 GB/T 5615—1985 规定
在图样上标注。
3.4 铸件上浇冒口、芯骨、芯砂与粘砂、多肉类等缺陷宜在热处理前清除,热处理后应清除氧化皮。
GB/T 222—1984 钢的化学分析用试样取样法及化学成分允许偏差 GB/T 223 钢铁及合金化学分析方法 GB/T 228—2002 金属材料 室温拉伸试验方法(eqv ISO 6892:1998) GB/T 229—1994 金属夏比缺口冲击试验方法(eqv ISO 148:1993) GB/T 5615—1985 铸钢件热处理状态的名称、定义及代号 GB/T 6414—1999 铸件尺寸公差与机械加工余量(eqv ISO 8062:1994) GB/T 11351—1989 铸件重量公差 GB/T 11352—1989 一般工程用铸造碳钢件 GB/T 15056—1994 铸造表面粗糙度 评定方法 JB/T 5105—1991 铸件模样 起模斜度 TB/T 2942—1999 铁道用铸钢件采购与验收技术条件 Q/CSR018—2006 机车车辆用铸钢件补焊技术条件
或技术条件规定。
4.4.2 试块应随其所代表的铸件同炉热处理
a) 同牌号不同熔炼炉次的一批铸件,同炉热处理时按熔炼炉次进行检验;在熔炼与热处理工艺稳定的
前提下,允许抽取一熔炼炉次试样进行检验;
b) 同一熔炼炉次的一批铸件在相同的热处理工艺和稳定的热处理条件下,分炉热处理时允许抽查。
4.4.3 低合金钢铸件的拉伸试样按 TB/T 2942—1999 的规定制取,碳素钢铸件的拉伸试样按 GB/T 228