扇形段轴承损坏原因分析(PDF X页)
轴承常见的损坏现象及原因

轴承常见的损坏现象及原因一、前言轴承是机械设备中的重要组成部分,其作用是支撑旋转的轴和减少摩擦。
然而,在长时间使用中,轴承会出现各种损坏现象,这些损坏现象会影响机器的正常运转,甚至导致机器停工。
因此,了解轴承常见的损坏现象及原因对于保护机器的安全运行具有重要意义。
二、常见的轴承损坏现象1. 疲劳裂纹疲劳裂纹是轴承最常见的故障之一。
它通常出现在滚道表面或滚珠上,并且与负荷、转速和润滑状态等因素有关。
疲劳裂纹会导致轴承失效并产生噪声。
2. 轨迹异常当轴承受到不适当的负荷或运行条件时,可能会出现轨迹异常。
这种情况下,滚道表面会变形或磨损,并且可能导致滚珠失去正确位置。
如果不及时处理,将导致更严重的故障。
3. 磨损轴承在长时间使用中会出现磨损现象,通常是由于摩擦和磨损引起的。
轴承的磨损会导致失效、噪声和振动等问题。
4. 锈蚀轴承在长时间使用中,如果没有得到良好的润滑和保护,就会出现锈蚀。
这种情况下,轴承表面会产生腐蚀或氧化,并且可能导致轴承失效。
5. 粘着当润滑不足或使用不当时,轴承可能会出现粘着现象。
这种情况下,滚珠和滚道之间的摩擦力增加,导致轴承失效。
三、常见的轴承损坏原因1. 载荷过大或不均匀当载荷过大或不均匀时,会导致轴承受到过度压力或负荷。
这种情况下,轴承容易出现裂纹、变形、磨损等问题。
2. 转速过高或过低当转速过高或过低时,都会对轴承造成影响。
转速过高可能导致润滑不足、温度升高等问题;转速过低则可能导致轴承失去润滑和冷却。
3. 润滑不良或污染润滑不良或污染是轴承损坏的主要原因之一。
如果轴承没有得到足够的润滑,就会导致磨损、摩擦、粘着等问题。
而污染物则会影响润滑油的性能,导致轴承失效。
4. 安装不当安装不当也是轴承损坏的原因之一。
如果安装时对轴承施加过大的力或者安装位置偏差过大,都会对轴承产生影响。
5. 环境因素环境因素也可能对轴承造成影响。
例如温度变化、湿度变化、腐蚀性气体等都可能导致轴承失效。
轴承损坏原因及分析
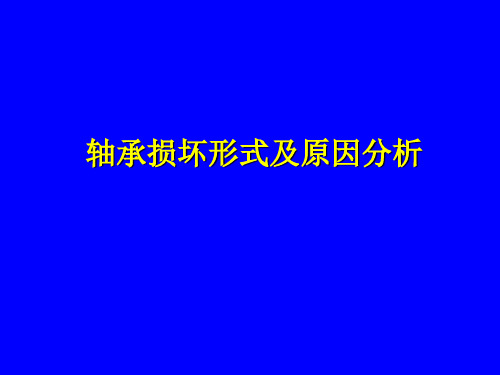
17) 微动腐蚀所造成的剥落 轴承环的滚道表面剥落。相对于此 处剥落的外表面有腐蚀现象。由于配 合太松或轴承箱形状不正确所致。
5、保持架的损坏
保持架的损坏,通常不易判断。若保持架坏了,轴承其它零件也 都坏掉了,这使得原因难以分析。造成架损坏主要原因有以下几种: 震动、转速太高磨损、卡死和歪斜等。 1)震动:当轴承处于震动状况下,轴承内部的力量可能导致保持 架出现疲劳裂痕,渐渐地,会使架破碎。 2)过高的转速:如果轴承以超出保持架材质所能承受的速度运转, 惯性力将使保持架破碎。 3)磨损:不当的润滑或坚硬的异物都能使保持架磨损,由于架是 由软材料制成的,运转中架与滚动体之间是滑动摩擦,一旦润滑不良, 架磨损速度相当快,渐渐地架的兜孔会因磨损间隙不断扩大,因此而 产生撞击力使架很快破碎。 4)卡死:零件的破碎物或坚硬的颗粒可能会卡在架与滚动体之间, 阻碍滚动体滚动,也会造成架破碎。
7) 外表面的磨伤 内环内孔与外环外表面有刻痕及 局部变色,此种情况是环与轴或轴承 箱有相对运动所致。解决的唯一方法 是加大环与轴或轴承箱的配合过盈量 来防止相互转动。轴向制动或夹紧无 法解决此类问题。 8) 表面坑痕: 滚道、滚动体表面或大端面小而 浅的坑痕,呈结晶壮的破坏壮。这是 由于润滑不良所致。例如;少油或由 于温升所造成的黏度改变,使油膜无 法将接触面分离,表面有瞬间的接触。 办法:改善润滑。
内环旋转,外环固定
外环旋转,内环固定
内
外
内
外
受力痕迹
受力痕迹
⑵、单向的轴向负荷: 内环或外环旋转。
⑶、单向的径向负荷 与轴向负荷组合。
内
ห้องสมุดไป่ตู้
外
受力痕迹,偏离一侧
受力痕迹
⑶、径向负荷与内环同 步旋转,外环固定
轴承损坏状态分析

轴承剥皮损伤分析
卡伤损伤状态
• 所谓卡伤是由于在滑动面伤产生的部分的 微小烧伤汇总而产生的表面损伤。滑道面、 滚动面圆周方向的线状伤痕。滚子端面的 摆线状伤痕靠近滚子端面的轴环面的卡伤。 原 因:过大载荷、过大预压。润滑不良。 异物咬入。内圈外圈的倾斜、轴的挠度。 轴、轴承箱的精度不良。措 施:检查载荷 的大小。预压要适当。改善润滑剂和润滑 方法。检查轴、轴承箱的精度
轴承压痕分析
轴承梨皮状点蚀状态分析
• 在滚道面上产生的弱光泽的暗色梨皮状点 蚀。原 因:润滑过程中出现异物咬入。由 于空气中的水分而结露。润滑不良。措 施:改善密封装置。充分过滤润滑油。使用 合适的润滑剂。
轴承梨皮状点蚀分析
轴承磨损状态分析
• 所谓磨损蚀由于摩擦而造成滚道面或滚动 面,滚子端面,轴环面及保持架的凹面等 磨损。原 因:异物侵入,生锈电蚀引起的 发展。润滑不良。由于滚动体的不规则运 动而造成的打滑。措 施:改善密封装置。 清洗轴承箱。充分过滤润滑油。检查润滑 剂及润滑方法。防止非直线性。
轴承磨损分析
轴承微振磨损状态分析
• 由于两个接触面间相对反复微小粉末, 因而页称微振磨损腐蚀。原 因:润滑不良。 小振幅的摇摆运动。过盈量不足。措 施: 使用适当的润滑剂,加预压,检查过盈量, 向配合面上涂润滑剂。
轴承微振磨损状态分析
轴承损坏状态分析
技术培训
轴承损伤状态分析
• 轴承再承受载荷旋转时,内圈、外圈的滚 道面或滚动体面由于滚动疲劳而呈现鱼鳞 状的剥离现象。原 因:载荷过大。安装不 良(非直线性)力矩载荷异物侵入、进水。 润滑不良、润滑剂不合适轴承游隙不适当。 轴承箱精度不好,轴承箱的刚性不均轴的 挠度大生锈、侵蚀点、擦伤和压痕(表面 变形现象)引起的发展。措 施:检查载荷 的大小及再次研究所使用的轴承改善安装 方法改善密封装置、停机时防锈轴承再承
板坯铸机扇形段辊子CARB轴承失效分析
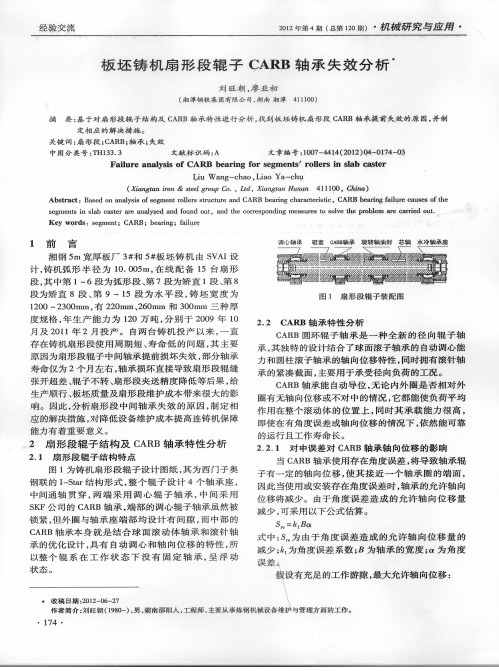
中间通 轴 贯 穿 , 端 采 用 调 心 辊 子 轴 承 , 间 采 用 两 中
子
因
位
S F公 司的 C R K A B轴承 , 端部 的调心辊子轴承虽然被
锁 紧 , # I N N 端 部 均设 计 有 I , 但 b - N  ̄N 司隙 而中部 的
轴 向位移 量/ m
“ 径向游隙 ( : 最小情况); 径向游隙 ( b: 最大情况); : C 角度误差
导
图 2 轴 向位移与径 向游 隙的关系
3
( )假设 轴承 内外 圈不存 在角度误 差 时 , 1 扣环侧
轴 向位移超过 52 m或非扣环侧轴 向位移达 1m .m m 2
时, 就会 出现 滚动体滑 出滑到 , 成轴 承损坏 。 造
响 。因此 , 分析扇形 段 中 间轴承 失 效 的原 因 , 制定 相
承
力
承
圈
应 的解决措施 , 对降低设备维护成本提高连铸机保障
能力 有着重要 意义 。
作
即
2 扇 形段辊 子结构及 C R A B轴承特 性分析
2 1 扇 形段 辊子结构特 点 .
的
2
图1 为铸机扇形段辊子设计 图纸 , 其为西 门子奥
出
严
经
配
因此 , 当存在角度误差 0 3 的情况下 , 于扣环 .。 对
侧, 为保证 滚动体不移 出滑道 , 向位 移 量应 小 于 5 轴 .
承
碳
2 19 = .4 m, — .6 3 2 m 对于非扣环侧 , 为保证有足够的工
3
作游隙 , 向位移量应小于 1— .6 1.4 m。 轴 19 = 0 m 2 0 当存在角度误差 O5 的情况下 , . o 对于扣环侧 , 为
连铸机扇形段分节辊轴承异常损坏成因浅析

均采 用分 节辊形 式 。2号 连铸 机 扇 形段 分 节 辊 采
用独 立分 节辊结 构 , 一组 辊 子 由两个 独 立 的辊 子 同心布置 , 独立 的辊 子两边 均有 轴承 座 , 轴 承座 和 辊子 均采用 机械 水冷却 。2 0 1 2年 投产 的二 炼 钢 3 号、 4号 连铸 机 扇 形 段应 用 了奥 钢 联 最 新 的 辊 子 设计 , 一组 辊子 由 3个 独 立 的 辊套 同心 装 配 在 一 共用 的芯 轴上 , 间 隔布置 4轴承座 支撑 辊子 芯轴 。
支撑 和导 向作用 , 使坯 壳沿 着预定 的轨 迹前 行 , 并 限制 它发 生 鼓 肚 变 形 _ 1 J 。新 设 计 的连 铸 机 多 数 设计 密排 辊列 布置 , 为提 高 辊 子 的 刚度 和 强 度 多
数 为分节 辊设计 结构 。
故下线 对铸 机功 能精度 、 备件 消耗 、 板坯质 量管理
等带来 了压 力 和难度 。 1 . 1 扇 形 段分节 辊轴 承损 坏下线 统计数 据分析 通过 收集 2 0 1 5年连 铸 机 扇 形段 事 故 下 线 记 录, 专 门将 连 铸辊 不 转 的故 障下 线 分类 整 理 。从
梅钢 自 2 0 0 3年 4月 从 奥 钢 联 引 进单 流 高效
1 扇形 段分节 辊近 期 的故 障调 查
3 ) 扇 形 段 分 节 辊 轴 承 卡 死 集 中在 中 间位 置 轴承 。一 炼钢 2号连 铸机 分节辊 子卡 阻多发 生在
2 0 1 5年上 半年来 , 连 铸 辊轴 承 损 坏导 致 扇形
・
3 0・
梅 山科技
2 0 1 6年第 6期
造成轴承损坏的原因

造成轴承损坏的原因
轴承损坏的原因多种多样,以下是一些常见的原因:
1. 工作负荷过重:轴承承受的工作负荷超过其设计负荷,例如超过额定转速、受到过大的力或扭矩等。
2. 不正常的运行条件:轴承在恶劣的环境中运行,例如高温、高湿度、腐蚀性介质等。
3. 不良的润滑条件:轴承未能得到足够的润滑,或者润滑脂质量不合格,或者长时间未更换润滑脂导致润滑性能丧失。
4. 磨损和疲劳:轴承长期运行时,由于磨擦和振动导致轴承表面磨损,最终使其失效。
5. 不正确的安装和对中:轴承安装时未能正确对中或者过紧或过松,导致轴承运行不平稳或轴线偏移,进而导致损坏。
6. 异物进入:轴承需要保持清洁,如果有杂质、尘埃、水等进入轴承内部,会导致轴承损坏。
7. 轴承质量问题:轴承制造或材料质量不良,也会导致轴承损坏。
要确保轴承运行正常,需要合理选择轴承型号、正确安装和维护,及时更换润滑脂或润滑油,同时避免过载和不正常的运行条件。
从轴承损坏症状表象分析具体原因
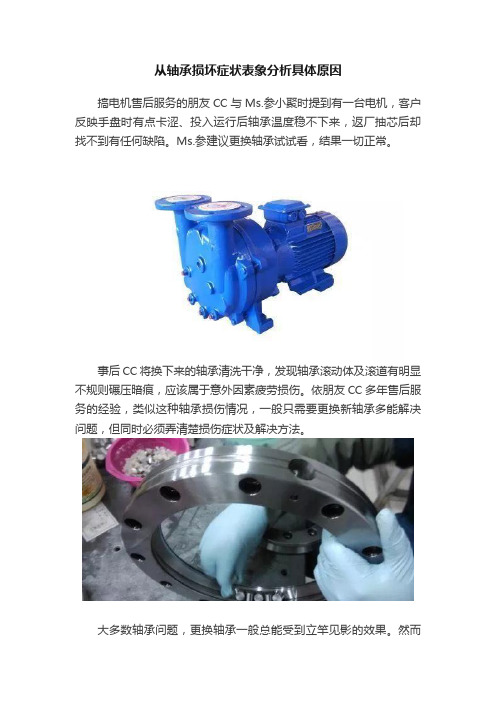
从轴承损坏症状表象分析具体原因搞电机售后服务的朋友CC与Ms.参小聚时提到有一台电机,客户反映手盘时有点卡涩、投入运行后轴承温度稳不下来,返厂抽芯后却找不到有任何缺陷。
Ms.参建议更换轴承试试看,结果一切正常。
事后CC将换下来的轴承清洗干净,发现轴承滚动体及滚道有明显不规则碾压暗痕,应该属于意外因素疲劳损伤。
依朋友CC多年售后服务的经验,类似这种轴承损伤情况,一般只需要更换新轴承多能解决问题,但同时必须弄清楚损伤症状及解决方法。
大多数轴承问题,更换轴承一般总能受到立竿见影的效果。
然而若认为如此简单处理就可以了,那就大错特错了,须先定性损伤症状、弄清原因。
轴承表面剥离轴承在承受载荷旋转时,轴承内圈和外圈的滚道面或滚动体面由于滚动疲劳而呈现鱼鳞状的剥离现象。
导致该问题的原因主要包括:●载荷过大、安装不良;●力矩载荷异物侵入、进水;●润滑不良、润滑剂不合适、轴承游隙不适当;●轴承室精度不好,轴承室的刚性不均;●轴的挠度大;●生锈、侵蚀点、擦伤和压痕等表面变形。
轴承表面剥皮轴承表面呈现出带有轻微磨损的暗面,如前述小C接手处置的一台轴承卡涩的故障电机案例。
暗面上由表面往里有多条深至5-10微米的微小裂缝,并在大范围内发生微小脱落。
导致该问题的主要原因包括:●润滑剂不合适;●异物进入了润滑脂内;●润滑剂不良造成表面粗糙;●配对滚动零件的表面粗糙度不符合要求。
轴承卡伤所谓卡伤是由于在滑动面上产生的部分微小烧伤导致轴承表面损伤。
在滑道面、滚动面圆周方向出现线状伤痕(搓板纹)。
滚子端面的摆线状伤痕、靠近滚子端面的轴环面卡伤。
其主要原因:●过大载荷、过大预压;●润滑不良。
异物咬入;●内圈外圈的倾斜、轴的挠度;●轴、轴承室的精度不良。
轴承局部断裂所谓断裂是指由于对滚道轮的挡边或滚子角的局部施加过大冲击力或过大载荷而导致一小部分断裂;原因可能是:●安装时受到了打击;●载荷过大;●跌落或使用不良。
轴承裂纹、裂缝所谓裂纹是指滚道轮或滚动体产生裂纹损伤。
轴承损坏原因分析

轴承负载过大,出现疲劳现象轴承缺失润滑轴承钢材质不达标轴承沾火过硬等原因在材质没有问题的情况下:内圈淬火过硬有很大的可能造成自现象大型初轧厂的热钢坯输送辊道采用长轴集中驱动、双列球面滚子轴承的支承。
在使用过程中发生轴承的外圈全部破碎及内圈断裂的恶性事故。
损坏轴承的安装部位见图2—11。
轴颈部位采用喷水冷却。
轴承型号是23144W33C3(相当于中国3G3003744Y),工作转速115r/min,使用硫磷型极压锂基脂N02进行集中给脂润滑。
损坏轴承所处的A14辊道已接近轧钢机,工作时冲击负荷很大,所输送的钢坯的最大质量约28000kg。
对轴承损坏情况进行检查:(1)轴承外圈全部破碎,内圈磨损十分严重,轴向已开裂,保持架断裂变形,圆锥滚动体严重扭曲;(2)轴承部位集中给脂系统工作正常,给脂管道畅通,该轴承总共运行6个月。
对其进行材料成分分析发现符合JISG4805轴承钢标准;对其进行宏观硬度检查表明轴承正常部位的硬度符合标准,而损伤严重的部位硬度下降;对其进行了损坏面表层材料分析,结果,表层边缘是一层白壳层,该区由淬火细小结晶状马氏体和粒状碳化物及少量残余奥氏体组成。
在白亮层下面是一层颜色较深的过渡区,它由回火屈氏体、粒状碳化物和少量残余奥氏体组成。
过渡区下面是回火隐晶马氏体、颗粒状碳化物和少量残余奥氏体,但也有少量回火屈氏体。
经显微硬度和扫描电镜高倍检验,表面是高温回火组织。
外圈有大量的表面龟裂,微裂纹是从表面淬火层开始,有的微裂纹已穿过过渡区,并汇合成一条较大的裂纹,显而易见,这种二次淬火裂纹是断裂的起源。
二次淬硬层厚度不均匀,大约从0.05~0.2mm,说明表面受热不均,二次淬硬层质脆,在冲击负荷和高接触应力下容易剥落。
经检查在外滚道中部的非负荷区发现材料表面有类似疲劳剥落的凹坑,在该区并不会发生滑动和滚动的摩擦,不存在金属的疲劳剥落,进一步检查,在这些凹坑中有氯离子和金属钠离子,根据现场使用条件判断,是属冷却水进入轴颈部位而形成的腐蚀孔。
- 1、下载文档前请自行甄别文档内容的完整性,平台不提供额外的编辑、内容补充、找答案等附加服务。
- 2、"仅部分预览"的文档,不可在线预览部分如存在完整性等问题,可反馈申请退款(可完整预览的文档不适用该条件!)。
- 3、如文档侵犯您的权益,请联系客服反馈,我们会尽快为您处理(人工客服工作时间:9:00-18:30)。
扇形段轴承损坏原因分析
尹秀锦①
(济南钢铁总厂机械设备制造公司 山东济南250101)
摘要 分析了济钢超低头板坯连铸机扇形段轴承损坏的原因,并找到了正确的解决措施。
关键词 扇形段 载荷 游隙 润滑
Ana lysis on Fa ilur e Ca uses of Seg m en t ′s Bea r i n g
Yin X iujin
(J inan Ir on and Steel Gr oup Cor por a tion M achine r y Pr oduc tion Co .,L td.,J inan 250101)
ABSTRAC T The fail ure cause s of seg ment ′s bearing in Jigang extra -lo w head continuous casting machine a re ana ly zed .The p roblem s are s olved w ith proper mea s ures .
KEY W O RDS Seg ment Load C learance space Lubrica ti on
1 概述济钢4#、5#板铸机为超低头板坯连铸机,4#板于1994年投产,其年生产能力为70万t,铸机工作拉速为0.7~
1.15m /m i n,铸坯规格为200×1400mm ,基本弧半径为5700mm 。
二次冷却区域共有7个扇形段,其中1-2段属
于弯曲段,3、4段属于矫直段,5-7段为水平段,从3段以后每一段上都有一对拉矫辊,各段都是6根辊子布置的小辊径,单节辊,密排布置方式,辊径分260mm 和280mm 两种,轴承为调心滚子轴承。
2007年4#
、5#
铸机扇形段下线
52台次,轴承原因造成的下线28次,占所有下线次数的53.85%,平均拉钢寿命为98.75天。
频繁下线造成炼钢
非计划停机,影响生产节奏,同时也增加了维修成本。
2 原因分析2.1 载荷分布不均
1)辊子同轴度偏差大。
在辊子修磨过程中辊子的同
轴度偏低,拉钢过程中辊子的弯曲量会加重,经过长时间的使用,导致个别辊子超负荷工作,使其损坏,同时也会使铸坯出现鼓肚、凹陷等质量问题。
2)对中间隙偏差大。
单片对中时,个别辊子辊面与
样规间隙值(对中间隙)是标准的上限,而其他几根辊子对中间隙是标准值的下限,导致这根辊子较其他辊子高,对中时个别辊子水平度偏差大,导致高的轴承承受大负
荷,长时间运转或者超负荷运转导致轴承先损坏。
3)轴承径向游隙不均匀。
同一根辊子上的轴承游隙
相差太大,导致辊子两侧轴承受力不均匀,如果同时存在上述任何一种影响因素,会加剧轴承的损坏。
2.2 径向游隙的影响
游隙的大小直接影响滚动轴承的载荷分布、振动、噪声、磨损、温升、使用寿命和机械运转精度等技术性能。
通过对损坏轴承的分析,认为轴承游隙大小不合适是造成轴承损坏的另一个因素。
2.3 润滑不良
1)润滑脂供给方式不合适。
滚动轴承的润滑主要为
了降低摩擦阻力和减轻磨损,也有吸振、冷却、防锈和密封等作用,但是装脂过多易于引起摩擦发热,影响轴承的正常工作。
扇形段在现场使用时润滑脂供给时间长,频次少,导致轴承先是满脂运转,后是少脂运转,没有为轴承提供一个良好的润滑条件。
2)油号不对导致甘油堵塞。
冬天维修好的扇形段存
放一段时间上线后就出现干油堵塞的问题,分析原因主要是北方冬天寒冷,润滑脂粘稠度增加,导致输送阻力增加。
2.4 灰尘等污染引起轴承损坏
1)密封结构不完善。
分析轴承密封结构(如图1)和
现场环境,发现密封不合适,辊子一侧的单唇骨架油封隔
—
6—
Extra Editi on (1)2009 冶 金 设 备M ET ALLUR GI CAL E QU IP MENT 2009年特刊(1)
①作者简介尹秀锦,女,年出生,助理工程师,年毕业于鞍山科技大学机械设计制作及自动化专业
2:19802004
尘,旋转水封一侧挡油,有漏封杂质的问题;而保护渣以及灰尘等容易在此侧堆积,轴承在工作以及停机检修清
理杂物时容易将杂质带进轴承内。
图1 原设计轴承密封结构简图
2)维修过程引入杂质。
由于润滑脂的不清洁和维修过程不按要求清洁装配轴承,导致轴承带病上线运行,引入杂质的轴承必定不能达到额定使用寿命。
3 解决措施3.1 均布载荷
装配前,精确测量辊子同轴度和轴承游隙值,选取辊子直径接近的放在一个扇形段上;安装轴承时选取游隙最相近的安装到同一根辊子上;对中精度提高到±0.05mm 以内,同一根辊子的水平度控制在0.05mm 以内。
3.2 合理选用轴承径向游隙
轴承径向游隙的选择按下式计算[1]
:
△=J -△L -△W -△J -△G 式中 △———轴承总径向游隙;
J ———轴承原始状态下的径向游隙(μm);
△L ———装配件表面压平的游隙缩减(μm );△W ———过盈配合引起游隙缩减(μm );△J ———温度差引起径向游隙缩减量(μm);△G ———由负荷引起的轴承径向游隙缩减量(μm)。
1)装配件表面压平的游隙缩减量与粗糙度的关系可
按表1参考值确定。
表1 压平缩减量与粗糙度的关系
配合件表面粗糙度Ra /μm
直径压平缩减量△L /μm
精磨0.8≈1细磨2≈2.5精车4≈5细车
6
≈7
2)温度差引起径向游隙缩减量可按下式计算:
△J =1000△t ×a 1[d +0.09(D -d )](
μm )式中 △t ———轴承内外圈的温度差,一般为5~10℃,有
相对气流的冷却可达15~20℃;
a ———铬钢线膨胀系数,a =11.2×10-6(1/℃);
D 、d ———轴承外圈和内圈的直径。
3)由负荷引起的轴承径向游隙缩减量计算式如下
[2]
:
ΔG =(0.04~0.06)F r 1/2-[(D /B )1/2-(d /B )1/2
](μm )
式中 F r ———径向载荷,N;
B ———轴承宽度,mm 。
通过计算,轴承安装后游隙△≈0,实际工作中的轴承在确定轴承的径向游隙时,除了考虑上述几项导致游隙缩减因素外,润滑不良和散热冷却条件不好引起的发热,也能导致轴承内部游隙丧失,同时还要考虑轴承制造时形状误差等因素的影响,所以实用中轴承的最佳有效游隙值一般都选在零或者稍正的安全一侧为宜。
重新选用
4级游隙的轴承取代原来的3级游隙轴承,径向游隙增加0.045mm 。
3.3 选用合理的润滑方式
1)更改现场润滑脂供给方式。
扇形段在现场使用时
润滑脂供给方式改为短时间,多频次的方式。
避免了装脂过多引起的摩擦发热,影响轴承正常工作。
2)根据季节不同选用不同型号的润滑脂,维修过程
中使用的润滑脂在冬天选用0#脲基润滑脂,夏天选用1#
脲基润滑脂。
减小了冬天干油阻力,夏天干油易流失的
问题。
3.4 确保轴承工作环境清洁
1)改善轴承密封结构。
将单唇骨架油封改为双唇骨
架油封,且主唇都是背对轴承安装,主唇实现了阻挡两侧灰尘进入的效果,副唇又能起到防止润滑脂过多流失的作用。
2)加强油品以维修过程的管理。
定期更换滤油器的
滤芯,维修过程中每一个暴露在外面的管接头都包裹起来,防止灰尘等杂质进入管路;装配轴承过程中严格按照轴承要求,清洁安装。
4 实施效果
2008年下线扇形段28台次,由于轴承损坏所占比例
为17.86%。
平均拉钢寿命为129.89天。
一台扇形段维修成本约为12.5万元,改造后共节省维修费用287.5万元。
同时减少了炼钢停机检修时间4140分钟,降低了炼钢损失82.8万元,年综合效益为370.3万元。
参考文献
[1]王赤,影响滚动轴承径向游隙因素的探讨,山西建筑,
2000(12)
[2]蔺二权,滚动轴承游隙组的选择,上海大中型电机,
2007(2)
(收稿日期:2009-03-09)
—
— 尹秀锦:扇形段轴承损坏原因分析
2009年特刊(1)
1172。