第五章 材料的断裂
断裂力学基础
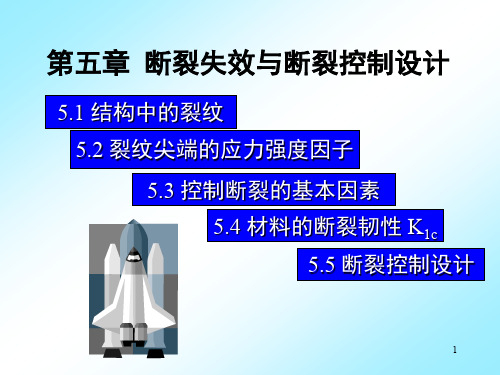
2
5.1 结构中的裂纹
低应力断裂: 在静强度足够的情况下发生的断裂。
低应力断裂是由缺陷引起的,缺陷的最严重形式是 裂纹。裂纹,来源于材料本身的冶金缺陷或加工、制造、 装配及使用等过程的损伤。
断裂力学 研究材料内部存在裂纹情况下强度问
W
2a
s 中心裂纹
s
a s
边裂纹
at s
2c s
表面裂纹
4
裂
应力集中
纹
严重
结构或构件 强度削弱
剩余强度: 受裂纹影响降低后的强度。
载荷或腐蚀环 境作用
裂纹尺寸 剩余强度
载荷
裂纹扩展 剩余强度下降
使用时间 a) 裂纹扩展曲线
最大设计应力 正常工作应力
可能 破坏 破坏
裂纹尺寸 b) 剩余强度曲线
在大的偶然载荷下,剩余强度不足,发生破坏。
裂纹面位移沿z方向,裂纹沿 z方向撕开。 7
一、断裂力学的处理方法
当外加应力在弹性范围内,而裂纹前端的塑性区很小 时,这种断裂问题可以用线性弹性力学处理,这种断裂力 学叫线弹性断裂力学(LEFM)。适用于高强低韧金属材料 的平面应变断裂和脆性材料如玻璃、陶瓷、岩石、冰等材 料的断裂情况。
对延性较大的金属材料,其裂纹前端的塑性区已大于 LEFM能够处理的极限,这种断裂问题要用弹塑性力学处理, 这种断裂力学叫弹塑性断裂力学(EPFM)。
这是进行抗断设计的基本控制方程。
f是裂纹尺寸a和构件几何(如W)的函数,查手册;
K1C是断裂韧性(材料抗断指标),由试验确定。
K由线弹性分析得到,适用条件是裂尖塑性区尺寸r远
小于裂纹尺寸a;即:
第五章 断裂
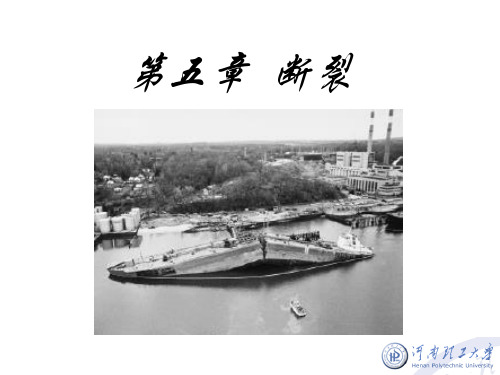
•如用实际晶体的E,a。,γ值代入式(56)计算,例如铁,E=2×105 MPa,a0=2.5×10-10 m,γ=2 J/m2, 则σm= 4×104 MPa≈E/5。 •高强度钢,其强度只相当于E/100,相差 20倍。 •在实际晶体中必有某种缺陷,使其断裂强 度降低。
5.3.2 格雷菲斯裂纹理论(Griffith)
• 当裂纹增长到2ac后,若再增长,则系统的总 能量下降。从能量观点来看,裂纹长度的继 续增长将是自发过程。临界状态为: (Ue+W)/ a =4γ-2πσ2a/E =0 (5-10) • 于是,裂纹失稳扩展的临界应力为: σc=(2Eγ/πa)1/2 (5-11) • 临界裂纹半长为 ac=2Eγ/πσ2 (5-12) • 式(5-11)便是著名的Griffith公式。 • σc 是含裂纹板材的实际断裂强度,它与裂 纹半长的平方根成反比;
摘要发表于 Int. J. of Fracture, Vol23, No.3, 1983 译文见 力学进展, Vol15,No2,1985
对策
普及断裂的基本知识,可减少损失29%(345亿/年)。
设计、制造人员了解断裂,主动采取改进措施, 如设计;材料断裂韧性;冷、热加工质量等。
利用现有研究成果,可再减少损失24%(285亿/年)。 包括提高对缺陷影响、材料韧性、工作应力的预测 能力;改进检查、使用、维护;建立力学性能数据 库;改善设计方法更新标准规范等。
• Griffith认为,裂纹尖端局部区域的材料强度可
达其理论强度值。 • 倘若由于应力集中的作用而使裂纹尖端的应 力超过材料的理论强度值,则裂纹扩展,引 起断裂。 • 根据弹性应力集中系数的计算,可以得到相似 公式 • Griffith公式适用于陶瓷、玻璃这类脆性材料。
材料失效分析(第五章-疲劳)

§2
疲劳裂纹萌生与扩展机理(模型)
一、疲劳裂纹萌生机理 1、挤出挤入模型—Wood模型
10
金属表面形成的挤出脊与挤入沟
11
2、位错销毁模型—藤田模型
两列平行的异号刃位错,在相距几个原子间隔 (约10埃)的两平行滑移面上互相对峙塞积;
由于这种位错排列所产生的高拉应力引起原子 面分离,形成孔洞
12
20
锯齿形断口或棘轮花样
轴类零件在交变扭转应力作用下产生的 有应力集中(轴颈)+扭矩作用
多源裂纹
裂纹以螺旋状方式向前扩展,最后汇合于轴的中央 若为单向交变扭转应力——棘轮花样 若为双向交变扭转应力——锯齿状断口
21
锯齿形断口
棘轮花样
22
3、瞬断区
形貌:具有断口三要素(放射区、剪切唇)的特征
对于塑性材料,断口为纤维状、暗灰色 对于脆性材料,断口为结晶状 位置:自由表面 断面中心
7
4、疲劳断裂过程
疲劳裂纹的萌生: 表面(次表面、内部) 疲劳裂纹的扩展(两个阶段)
8
第一阶段:裂纹起源于材料表面,向内部扩展
范围较小,约2—5个晶粒之内 显微形貌不好分辨 与拉伸轴约成45°角,裂纹扩展主要是由于τ 的作用
扩展速度很慢,每一应力循环只有埃数量级
第二阶段:断面与拉伸轴垂直,凹凸不平 裂纹扩展路径是穿晶的 扩展速度快,每一应力循环微米数量级 显微特征:疲劳辉纹
3、空穴模型—Mott模型
由于螺位错围绕着环形通道,进行连续交叉滑移运动, 结果从表面上挤出了材料的一个舌片,并相应地形成 了一个空穴,这个空穴就是疲劳裂纹源
13
4、位错交叉滑移模型—Cottrell和Hull模型
14
二、疲劳裂纹扩展模型
材料断裂分析

材料断裂分析
材料的断裂行为是指在外力作用下,材料发生破裂现象的过程。
材料断裂行为
的研究对于材料的设计、制备和工程应用具有重要的意义。
本文将对材料断裂行为进行分析,并探讨其影响因素和研究方法。
首先,材料的断裂行为受到多种因素的影响,包括材料的物理性质、化学成分、微观结构等。
其中,材料的韧性、强度、断裂韧性等是影响断裂行为的重要因素。
在材料设计和选择过程中,需要综合考虑这些因素,以确保材料具有良好的断裂性能。
其次,材料的断裂行为可以通过多种方法进行研究。
常用的方法包括拉伸试验、冲击试验、断口分析等。
通过这些方法,可以获取材料的断裂特征参数,如断裂韧性、断裂模式等,从而为材料的设计和评估提供依据。
另外,材料断裂行为的研究还可以借助于数值模拟和断裂力学理论。
通过建立
适当的数学模型,可以预测材料在不同加载条件下的断裂行为,为工程实践提供指导。
总的来说,材料的断裂行为是一个复杂的物理过程,受到多种因素的影响。
通
过对材料的物理性质、化学成分和微观结构等因素进行分析,可以更好地理解材料的断裂行为。
同时,通过多种方法和手段进行研究,可以为材料的设计和应用提供科学依据。
在工程实践中,需要充分考虑材料的断裂性能,选择合适的材料,并设计合理
的结构,以确保材料在使用过程中具有良好的断裂性能。
同时,需要不断深化对材料断裂行为的研究,提高材料的设计水平和工程应用水平。
第五章材料的断裂机理和断裂韧性_材料的宏微观力学性能
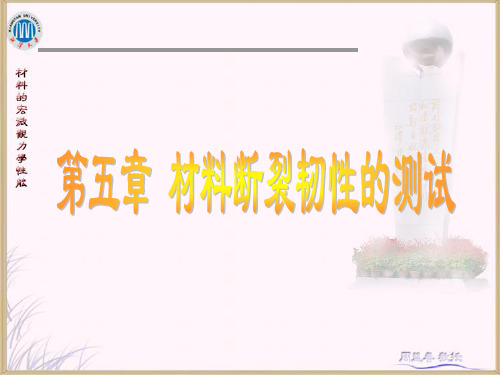
32
a 492.6 W
52
a 663.4 W
72
a 405.6 W
92
不同试件及其KIC的表达式 6.切口圆棒拉伸试件
K IC
P d f 32 D D
六种试件的适用范围
1、三点弯曲试件和紧凑拉伸试件均为标准试件。 三点弯曲试件所需的夹具较为简单;紧凑拉伸试件则所需的专 门夹具,加工困难,且不同厚度的试件需要有不同的夹具相匹配, 但紧凑拉伸试件省料,对于中强度钢大试件,这点更为突出。 2 、压力容器中,最危险的常是在环向拉应力作用下,裂纹沿厚度 (径向)方向扩展,采用C形试件和拱形三点弯曲试件,不仅加工方便, 而且充分利用管壁全厚,使其易满足小范围屈服,得到有效的KIC 。
P a K IC f 12 BW W
5.2 表面裂纹断裂韧性KIE的测试
脆性断裂一般都是由不穿透板厚的表面裂纹扩展引起
的,表面裂纹 ( 如图所示 ) 基本上属于平面应变状态类型。 其测试原理和步骤与测试 KIC时的很类似,在此只说明测试 原理。 1.KIE的表达式 测 试 原 理
KIC C πa f
K IC
P a f 12 BW W
2 a a πa πa f 7.51 3.00 0.50 sec tg W 2 W 2 W W
2.疲劳预制裂纹
为了模拟实际构件中存在的尖锐裂纹,使所得的 KIC数据可以对比和实际应用,试件必须用疲劳载荷预 制裂纹。 (1)裂纹要平直和足够的尖锐。 要 求 (2) 疲劳裂纹长度不少于 2.5% W,且不 小于1.5mm。 (3) 裂纹总长度 ( 预制切口加疲劳裂纹 ) 应控制在(0.45~0.55)W范围内。
材料基础第5章习题课

单晶体的塑性变形 ——孪生
1.定义:是指晶体的一部分沿一定晶面和晶向相对于另 一部分所发生的切变。
2.孪生的特点: ① 孪生使晶格位向发生改变; ② 所需切应力比滑移大得多, 变形速度极快, 接近声速; ③ 孪生时相邻原子面的相对位移量小于一个原子间距. ④ 孪生变形在应力-应变曲线上也很有特点 ⑤ HCP晶格金属滑移系少, BCC晶格金属只有在低温 或冲击作用下才发生孪生变形,FCC晶格金属,一 般不发生孪生变形。 ⑥ 对塑性变形贡献小
合金的塑性变形——多相合金
1.结构:基体+第二相。 2.分类依据:第二相粒子尺寸大小 聚合型两相合金 与基体晶粒尺寸属同一数量级, 两相性能接近:按强度分数相加计算。
弥散分布型两相合金 第二相粒子细小而弥散地分布 在基体晶粒中。 不可变形粒子的强化作用(位错绕过机制) ; 可变形微粒的强化作用(位错切割粒子的机制)。
材料科学与工程学院 材料科学基础
zhanglei.hubu@
1、什么是弹性变形?并用双原子模型来解释其物理本质。 【答】弹性变形是指外力去除后能够完全恢复的那部分变形, 可从原子间结合力的角度来了解它的物理本质。 原子处于平衡时,其原子间距为r0,位能U处于最低 位臵,相互作用力为零,这是最稳定的状 态。当原子受力后将偏离其平衡位臵,原 子间距增大时将产生引力;原子间距减小 时将产生斥力。这样,外力去除后,原子 都会恢复其原来的平衡位臵,所产生的变 形便完全消失,这就是弹性变形。
孪生与滑移的异同
滑 移 相同点
晶体位向
孪 生
是塑变的形式;沿一定的晶面、晶向进行;不改变结构 。
不改变(对抛光面观察无重 现性) 改变,形成镜面对称关系(对 抛光面观察有重现性)
不 同 点
断裂力学讲义第五章8-12应变能释放率
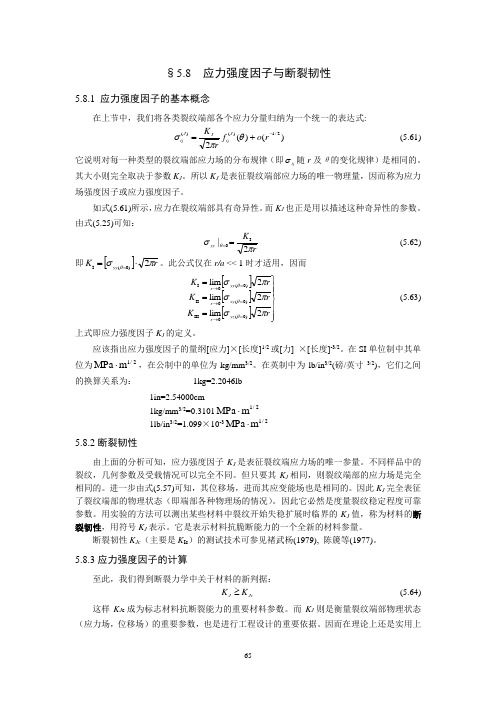
§5.8 应力强度因子与断裂韧性5.8.1 应力强度因子的基本概念在上节中,我们将各类裂纹端部各个应力分量归纳为一个统一的表达式:)()(22/1)()(-+=r o f r K J ij JJ ij θπσ (5.61) 它说明对每一种类型的裂纹端部应力场的分布规律(即ij σ随r 及θ的变化规律)是相同的。
其大小则完全取决于参数K J 。
所以K J 是表征裂纹端部应力场的唯一物理量,因而称为应力场强度因子或应力强度因子。
如式(5.61)所示,应力在裂纹端部具有奇异性。
而K J 也正是用以描述这种奇异性的参数。
由式(5.25)可知:rK yy πσθ2|I0== (5.62) 即[]r K yy πσθ2)0(I ⋅==。
此公式仅在r/a << 1时才适用,因而[][][]⎪⎪⎭⎪⎪⎬⎫====→=→=→r K r K r K yz r xy r yy r πσπσπσθθθ2lim 2lim 2lim )0(0III)0(0II )0(0I (5.63)上式即应力强度因子K J 的定义。
应该指出应力强度因子的量纲[应力]×[长度]1/2或[力] ×[长度]-3/2。
在SI 单位制中其单位为2/1mMPa ⋅,在公制中的单位为kg/mm 3/2。
在英制中为lb/in 3/2(磅/英寸3/2),它们之间的换算关系为: 1kg=2.2046lb1in=2.54000cm1kg/mm 3/2=0.31012/1mMPa ⋅ 1lb/in 3/2=1.099×10-32/1mMPa ⋅5.8.2断裂韧性由上面的分析可知,应力强度因子K J 是表征裂纹端应力场的唯一参量。
不同样品中的裂纹,几何参数及受载情况可以完全不同。
但只要其K J 相同,则裂纹端部的应力场是完全相同的。
进一步由式(5.57)可知,其位移场,进而其应变能场也是相同的。
因此K J 完全表征了裂纹端部的物理状态(即端部各种物理场的情况)。
05 材料的断裂韧性

思考题:
5.3 裂纹尖端塑性区的大小及修正
由弹性应力场公式:
KI y 2 r
r 0时,σy ∞,但对韧性材料,当σ>σs时,发生塑性变 形,其结果是材料在裂纹扩展前,其尖端附近出现塑性变形 区,塑性区内应力应变关系不是线性关系,上述KI判据不再 适用。
试验表明:如果塑性区尺寸r0远小于裂纹尺寸a( r0 /a<0.1)时或塑性区周围为广大的弹性区包围时,即在 小范围屈服下,只要对KI进行适当修正,裂纹尖端附 近的应力应变场的强弱程度仍可用修正的KI来描述。
5.4 裂纹扩展能量释放率GI
通过分析裂纹扩展过程中能量转化讨论断裂条件。
裂纹扩展能量释放率定义:裂纹扩展单位面积时,弹性系 统所能释放(或提供)的能量,也叫裂纹扩展力(GI)。
U GI A
(量纲为MJ· m-2或Mpa· m)
当裂纹长度(中心穿透裂纹)为2a,裂纹体的厚度(板厚)为B时
含裂纹试样的断裂应力与试样内 部裂纹尺寸的试验结果:
K c a
1 c a Y
(Y与裂纹形状、试样几 何尺寸和加载方式有关)
c a Y 常数
KIc= c a Y
(该常数与裂纹大小、几何形状及加 载方式无关,而取决于材料本身)
断裂韧性
KIC表征材料抵抗裂纹失稳扩展的能力
a
1 0.177( / s ) 2
修正后,KI值变大,对平面应力状态,当σ>0.7σs时, 需要修正。 当r0 /a>0.1时,线弹性断裂力学已不适用,要采用弹塑 性断裂力学。
例:
一块含有长为16mm中心穿透裂纹的钢板, 受到350MPa垂直于裂纹平面的应力作用。 (1)如果材料的屈服强度是1400MPa, 求塑性区尺寸和裂纹顶端有效应力场强度 因子值; (2)如果材料的屈服强度为385 MPa,求塑 性区尺寸和裂纹顶端有效应力场强度根据裂纹形 状、试样尺寸和加载方式查手册。
- 1、下载文档前请自行甄别文档内容的完整性,平台不提供额外的编辑、内容补充、找答案等附加服务。
- 2、"仅部分预览"的文档,不可在线预览部分如存在完整性等问题,可反馈申请退款(可完整预览的文档不适用该条件!)。
- 3、如文档侵犯您的权益,请联系客服反馈,我们会尽快为您处理(人工客服工作时间:9:00-18:30)。
低温冲击试验
42
韧脆转变温度
韧脆转变温度测试方法
基本方法 将试样冷却到不同温度 测定冲击功,观察断口形貌特征 绘制冲击功和温度关系曲线,确定韧脆转变温度 断口形貌法
50%FATT 结晶状断口面积50%
43
韧脆转变温度
韧脆转变温度测试方法
能量法 低于某一温度NDT时,冲 击功基本不随温度变化,材 料断裂前无塑性变形,断口 100%结晶区组成(解理断 口)——低阶能 高于某一温度FTP,对应 100%纤维状断口——高阶能 高低阶能平均值FTE——韧 脆转变温度
习题2
30
*弹塑性条件下的断裂韧性
裂纹尖端张开位移CTOD
4 K I2 4GI = δ = 2V = πEσ s πσ s
断裂判据
δ ≥ δc
J积分与J判据
1 −ν 2 2 J IC = GIC = K IC E
31
4. 冲击韧性
32
切口强度
切口
定义 影响 改变零件应力和应变的分布 造成应力集中和应力多向性 促使材料发生低应力脆断 切口敏感性 使零构件外形具有几何不连续性
裂纹长度与塑性区尺度的对比
衡量指标和判据
线弹性条件 应力场强度因子与K判据 裂纹扩展能量释放率与G判据 *弹塑性条件 J积分与J判据 裂纹尖端张开位移
19
线弹性条件下的断裂韧性
裂纹尖端的应力场
裂纹扩展模式
裂纹尖端应力场 应力场强度因子
K I = σ πa
一般形式
K I = Yσ a
20
线弹性条件下的断裂韧性
例题1
已知材料的断裂韧度KIC与实际裂纹长度a, 材料的剩余强度是多少?
剩余强度
例题2
σ r = K IC / Y a
已知材料的断裂韧度KIC与实际工作应力σ, 材料的允许最大裂纹尺寸是多少?
临界裂纹尺寸
例题3
a = (K IC / Yσ )
2
(旧书) P79例题1 P79例题2
29
断裂韧性的应用
裂纹扩展
断裂
宏观塑性变形分类 脆性断裂 韧性断裂 裂纹扩展途径分类 穿晶断裂 沿晶断裂 微观断裂机理分类 解理断裂 剪切断裂
4
断裂的类型
按宏观塑性变形程度
脆性断裂 基本不发生明显宏观塑性变形 没有明显预兆,突然发生 断口齐平光亮 韧性断裂 有明显宏观塑性变形 裂纹扩展缓慢,消耗大量变形能 断口呈灰暗色,纤维状 主要区别 断裂前所产生的应变大小 以断面收缩率5%作为界限
26
断裂韧性的影响因素
显微组织 不同组织和亚结构对断裂韧度有很大影响 第二相弥散强化的材料断裂韧度较高 热处理和压力加工对断裂韧度的影响也很大 温度 温度降低通常会降低断裂韧度——韧脆转变 强度较高的材料,温度对断裂韧度的影响减弱 应变速率 增加应变速率会降低断裂韧度 应变太快时,形变热量来不及 传导,造成局部区域绝热状态引 起温度升高,断裂韧度反而上升
7
断裂的类型
按微观断裂机理
解理断裂 正应力下原子结合键断裂引起的穿晶断裂 断口微观形貌有大量台阶汇成的河流花样 解理是脆性断裂 的微观机理之一 机制——裂纹与螺型位错相交形成台阶 其他机制——裂纹沿孪晶扩展形成舌状花样
8
断裂的类型
按微观断裂机理
解理断裂——河流花样 同号台阶汇合长大 异号台阶相互抵消 河流方向与裂纹扩展方向一致 准解理断裂 起源于晶内硬质点 河流纹不完全,局部有韧窝
冲击吸收功AK 低阶能 高阶能
0
韧脆转变温度FTT
T/ ℃
44
低温脆性的影响因素
内在因素
晶体结构 化学成分 金相组织 晶粒尺寸
晶界
阻碍裂纹扩展 塞积的位错减少,降低应力集中 杂质浓度减少,避免沿晶断裂
外部因素
试样外形尺寸 加载速率
45
应力场强度因子
*不同形状因子
K I = Yσ a
中心穿透裂纹
体内椭圆裂纹
表面半椭圆裂纹
Y = π sec( πa / W )
Y = π / ϕ0
Y = 1.1 π / Q
21
线弹性条件下的断裂韧性
应力场强度因子
裂纹失稳扩展的临界状态下
临界应力场强度因子KIC
断裂韧度
断裂K判据
K Ic = Yσ c ac
*切口强度估算 切口强度只能定性判定材料的切口敏感度
35
冲击韧性
冲击载荷的特点
作用时间短 冲击力F是一个变力
用能量变化来衡量
冲击韧性实验
试件
夏氏切口 梅氏切口
36
冲击韧性
冲击韧性实验
实验原理
实验设备 实验结果——冲击吸收功
Ak = GH1 − GH 2 = Ai + Ap + A f + ∆E
5
断裂的类型
按裂纹扩展途径
沿晶断裂 裂纹沿晶界扩展 晶界结合力较弱,有脆性第 二相、夹杂物、晶界损伤等 断口呈结晶状脆性断口 共价键晶体较为常见 穿晶断裂 裂纹沿晶内扩展 可能是脆断,也可能是韧断 离子键晶体较为常见
6
断裂的类型
按微观断裂机理
剪切断裂 切应力下滑移面分离引起的断裂 韧性断裂通常是剪切断裂 断口宏观形貌大多呈纤维状 断口微观形貌分布着大量的韧窝 机制——微孔形核、长大、聚合,最后断裂 微孔来源——夹杂物、第二相质点、气孔、微裂纹
习题1
有一个构件,实际应力1.3GPa,试从传统安 全系数设计观点和断裂力学观点判断那种材 料最优,并以此判断应选择那种材料?Y=1.5, 最大裂纹尺寸2.0mm,有两种备选材料: 甲钢:σ=1950MPa,KIC=45MPa · m1/2 乙钢:σ=1560MPa,KIC=75MPa · m1/2 有一大型板件,材料的σ0.2=1200MPa, KIC=115MPa · m1/2 ,探伤发现有20mm长的裂纹, 若在平均轴向应力900MPa下工作,该构件是 否安全? Y=π1/2
断裂G判据 裂纹失稳扩展的力学条件
GI ≥ GIc
25
断裂韧性的影响因素
化学成分和结构 细化晶粒的合金元素提高强度和塑性,提高断裂韧度 强固溶元素大大降低塑性,从而降低断裂韧度 形成金属间化合物的元素因第二相引起断裂韧度降低 增强键合强度的组元,都将提高断裂韧度 基体相 易发生塑性变形和韧性断裂,断裂韧度高 形变强化对断裂韧度有影响 晶粒尺寸 夹杂和第二相的影响
定义 表征材料在平面应变状态下抵抗裂纹失稳扩展的能力 KIc越大,断裂裂纹尺寸或应力越大,越难断裂 用KIc表征材料的力学性能指标 K I ≥ K Ic 脆性断裂的条件
22
线弹性条件下的断裂韧性
断裂韧度的测定
试验方法与试样
紧凑拉伸试验
三点弯曲单边裂纹试验
四点弯曲单边裂纹试验
试验步骤 加工试样,预制裂纹 加载让裂纹扩展,测定载荷与裂纹张开位移 测量裂纹长度,求断裂韧度
不能真正反映材料的韧脆程度
37
冲击韧性
冲击韧性
定义 特点
Akv α kv = SN
SN——缺口处截面积
揭示材料的变脆倾向
不能真正代表材料的韧脆程度 缺口冲击韧性对材料内组织变化及外界温度很敏感 冲击试验简单易行 用途 评定原材料冶金质量和热处理后的产品质量 确定材料的冷脆倾向和韧脆转变温度,用于低温材料设计 反映材料一次或少数次大能量冲击断裂的抗力 建立冲击功和其他力学性能指标间的关系,代替复杂实验
裂纹扩展
12
2. 断裂强度
13
断裂强度
理论断裂强度
Eγ σm = a 0
1/ 2
实际材料的断裂强度仅 为理论的1/10~1/1000
裂纹
14
断裂强度
Griffith裂纹理论
裂纹失稳扩展
塑性变形功
临界应力 临界裂纹半长
2 Eγ σc = π a
2 S k2 − σ 0 .2 ac = 2D
材料断裂前吸收塑性变形功和断裂功的能力
衡量材料韧性大小的力学性能指标
应力σ /MPa
静力韧度
弹性能
0
应变ε / %
18
断裂韧性
断裂韧性概述
实际材料的断裂强度仅为理论的1/10~1/1000
裂纹
研究方法 断裂力学 线弹性条件下的断裂韧性 弹塑性条件下的断裂韧性
9
断裂的类型
几种断裂类型小结
脆性断裂 解理断裂 穿晶断裂 沿晶断裂 宏观塑性变形 微观断裂机理 裂纹扩展方式
10
韧性断裂 剪切断裂
断口特征与分析
分析方法
宏观断口观察断裂类型 微观断口形貌分析确认断裂机理 成分与夹杂分析辅助
常见断口特征
11
裂纹形核与扩展
*裂纹形核
位错塞积理论 位错反应理论 脆性第二相开裂理论
本章要点
材料的断裂简介
断裂的类型与断裂机理 断口特征与分析 裂纹形核扩展过程
断裂强度 断裂韧性
线弹性条件下的断裂——断裂韧度 断裂韧性的影响因素 工程领域的应用
冲击韧性 低温脆性
2
1. 材料的断裂
3
断裂的概述
断裂的定义 固体材料在力的作用下分成若干部分的现象 断裂的过程
裂纹形核
断裂的分类
ac = 2 Eγ
1/ 2
实际材料Orowan修正
πσ 2
E (2γ + W ) σc = πa
1/ 2
15
断裂强度
真实断裂强度
真应力应变曲线
应力σ /MPa
真实断裂强度Sk
静力韧度a
0
应变ε / %
16
3. 断裂韧性
17
韧性概述
韧性 韧度
定义 分类 静力韧度——静拉伸曲线下塑性变形和断裂功 断裂韧度——断裂力学方法研究材料抵抗断裂的能力 冲击韧度——切口和冲击条件下的断裂韧性