熔体粘度
13熔体物性测定-粘度

M 1 1 ( 2 2) 4 h r R
外柱体半径,常数 内柱体半径,常数
转头浸入熔体深度,常数
转头转速,可设定在200 或300r/min
2014-8-22 李桂荣:冶金熔体粘度的测定 12
3旋转柱体法测粘度
M 1 1 ( 2 2) 4 h r R
K
8
2014-8-22
…
…
速度矢量
李桂荣:冶金熔体粘度的测定
3旋转柱体法测粘度
刚玉转杆 高温熔体 内柱体: 钼质转头
由于粘性力作用, 在柱体将产生一个 h 力矩与之平衡。
V r
外柱体: 石墨坩埚
R
2014-8-22
李桂荣:冶金熔体粘度的测定
9
3旋转柱体法测粘度
温 度 显 示 区
控温区
测试过程显示区
使流体产生单位速度梯度所需要的内摩擦力 (剪应力)。 单位:Pa· S(SI制) 其他:1厘泊(CP)=10-2泊(P)=10-3Pa· s
2014-8-22
李桂荣:冶金熔体粘度的测定
7
2 粘度测试
靠壁位置
径向向里
测试假设: 流体流速很小 各液层运动方向互 相平行 速度变化连续 该流动状态称为 “层流”。
物质 水 铁水 钢水 稀熔渣 黏度中等渣 稠熔渣 温度(℃) 25 1425 1595 1595 1595 1595
黏度(Pa· s) 0.00089 0.0015 0.0025 0.0020 0.020 0.20
FeO
CaO SiO2 Al2O3
2014-8-22
1400
接近熔点 1942 2100
剪切应力
2014-8-22
塑料加工助剂-熔体强度和熔体压力

石陶网-塑料用加工助剂全球塑料行业的发展非常迅速,年均增长率达到了4%~6%,超过了全球GDP 的增长水平。
这种增长最重要的原因就是塑料材料继续在替代着传统材料如金属、木材、和矿物。
其实,树脂中添加的各种添加剂对于塑料材料的成功应用也大有帮助。
在使用到的各类型添加剂中,聚合物抗冲击改性剂和加工助剂为聚合物提供了最独到和最宝贵的卓越性能,同时还提高了产品的加工性能。
增韧处理、流变性能控制、外观美观性、加工性能以及经济因素都是重要的性质属性。
种种这些添加剂已经使用多年,经过长期的发展衍生出了一系列广泛品种。
造成这种情况的一个主要原因是乳液聚合过程各种多样,这就使得科学家们不断去设计适合的聚合物组分、聚合物结构、聚合物形态以及聚合物分子量/分子量分布。
由于生产成本低,而且所得的乳液产品易于分离,因此,乳液聚合在商业化生产中还是非常有吸引力的。
1956年,第一种用于乳液聚合技术的聚合物添加剂被开发出来,它是由甲基丙烯酸酯-丁二烯-苯乙烯(MBS)制备的核壳结构抗冲击改性剂。
随后出现的是各种丙烯酸类加工助剂和丙烯酸类抗冲击改性剂。
最初,这些添加剂主要用来改善聚氯乙烯(PVC)的加工性能和韧性。
而用于PVC的加工助剂主要是{TodayHot}为了促进PVC的熔融、提升熔体强度、提高分散性能和表面质量。
超高分子量加工助剂则是发泡PVC中的重要组成部分。
借助加工助剂,PVC泡沫能够获得更加均一的发泡结构,减少闭泡的破裂而且泡沫密度会更低一些。
起润滑作用的加工助剂能够有效防止熔融的塑料粘结在金属表面,改善制品表面质量,提高生产效率。
有很多塑料材料的应用范围非常有限,这是因它们要么不具备所需的物理性质,要么其加工性能非常差,加工助剂正是用来增强塑料的熔体加工性、提高产量、减少停车检修时间以及提供产品更好的质量的。
20世纪50年代,罗门哈斯公司率先开发出了第一种商业化生产的加工助剂产品,该产品被用于硬质PVC生产。
在此之后,这种前所未有的技术很快被业界所熟知,并且因而引发了PVC工业的生产热潮。
熔指、熔体强度和熔体粘度
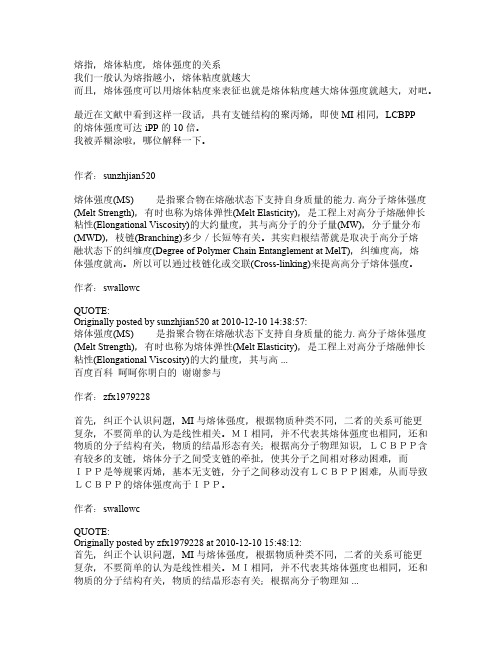
熔指,熔体粘度,熔体强度的关系我们一般认为熔指越小,熔体粘度就越大而且,熔体强度可以用熔体粘度来表征也就是熔体粘度越大熔体强度就越大,对吧。
最近在文献中看到这样一段话,具有支链结构的聚丙烯,即使MI相同,LCBPP的熔体强度可达iPP的10倍。
我被弄糊涂啦,哪位解释一下。
作者:sunzhjian520熔体强度(MS) 是指聚合物在熔融状态下支持自身质量的能力. 高分子熔体强度(Melt Strength),有时也称为熔体弹性(Melt Elasticity),是工程上对高分子熔融伸长粘性(Elongational Viscosity)的大约量度,其与高分子的分子量(MW),分子量分布(MWD),枝链(Branching)多少/长短等有关。
其实归根结蒂就是取决于高分子熔融状态下的纠缠度(Degree of Polymer Chain Entanglement at MelT),纠缠度高,熔体强度就高。
所以可以通过枝链化或交联(Cross-linking)来提高高分子熔体强度。
作者:swallowcQUOTE:Originally posted by sunzhjian520 at 2010-12-10 14:38:57:熔体强度(MS) 是指聚合物在熔融状态下支持自身质量的能力. 高分子熔体强度(Melt Strength),有时也称为熔体弹性(Melt Elasticity),是工程上对高分子熔融伸长粘性(Elongational Viscosity)的大约量度,其与高 ...百度百科呵呵你明白的谢谢参与作者:zfx1979228首先,纠正个认识问题,MI与熔体强度,根据物质种类不同,二者的关系可能更复杂,不要简单的认为是线性相关。
MI相同,并不代表其熔体强度也相同,还和物质的分子结构有关,物质的结晶形态有关;根据高分子物理知识,LCBPP含有较多的支链,熔体分子之间受支链的牵扯,使其分子之间相对移动困难,而IPP是等规聚丙烯,基本无支链,分子之间移动没有LCBPP困难,从而导致LCBPP的熔体强度高于IPP。
熔融指数与粘度的关系

熔融指数与粘度的关系
熔融指数和粘度是塑料材料的重要性能指标,两个参数之间存在一定的关系。
熔融指数是指在一定条件下,塑料在加热状态下熔融流动的速度,单位为g/10min。
粘度则是材料流动阻力的大小,通常用牛顿数(Pa·s)来表示。
一般来说,熔融指数和粘度呈反比例关系,即熔融指数越大,粘度越小。
这是因为熔融指数较大的材料,分子链较短,松散度较大,相互之间的阻力较小,流动性能较好,因此粘度较小。
反之,熔融指数较小的材料,分子链较长,松散度较小,相互之间的阻力较大,流动性能较差,因此粘度较大。
此外,除了分子链长度的影响外,熔融指数和粘度还受到材料的分子量、熔体温度、载荷压力等因素的影响。
因此,在实际应用中,需要综合考虑这些因素,以确定最适合的熔融指数和粘度范围,以满足不同的塑料加工需求。
- 1 -。
PVC塑化、黏度、流动性

PVC-U的塑化性能、熔体粘度与熔体强度一、塑化度的定义:PVC树脂是由多层粒子聚合而成。
在硬质PVC加工过程中多层粒子结构的形态会发生很大变化。
这种变化是在受热和剪切力的同时作用下产生的。
首先是50-250μm的树脂颗粒破碎游离出1―2μm的初级粒子(或称二次粒子)。
随着加工的进行(如物料在料筒内的输送)物料受到更高温度和剪切力的作用初级粒子破碎。
一般当料温高于190℃时次级粒子可以全部破碎晶体熔化粒子边界消失而形成三维网络结构。
这种三维网络的形成过程称为凝胶化或塑化。
所以,塑化度的重点,是粒子边界消失。
消失的程度决定了塑化度的高低。
假设有10g塑化度100%的PVC颗粒,通过某种不会破坏PVC分子结构的方式,将该颗粒进行破碎。
分别测量破碎为100万份和破碎为1万份后的两种材料的塑化,二者会有显著的不同。
破碎100万份的塑化度会低于破碎1万份的。
这就要求我们关注加工过程中所体现的塑化不足的真实原因。
例如:管材挤出时,相同的材料、设备、挤出模具与工艺。
A条件下,口模光滑,产出的管材表面也是光滑的,进行二氯甲烷试验完全无腐蚀;B条件下,口模表面吸附了较多的析出物,造成管材表面哑光或者粗糙,进行二氯甲烷试验时,可能会出现一定程度的腐蚀。
这种结果显然是口模粗糙导致了管材表面熔体出现破裂现象;除了清理口模,我们假设有一种高度光滑的材料,我们把这种材料加入到PVC混好料中,这种材料不会影响PVC的塑化度,但是挤出时,会析出到管材表面,改善了熔体与口模之间的摩擦力,二氯甲烷试验则会完全无腐蚀。
又例如:生产PVC管件时,相同的材料、设备、注塑模具与工艺。
A条件下,管件烘箱试验完全无开裂;B条件下,将浇口套内径由8mm更换为4mm,此时甚至可能出现无法注满型腔的现象。
即使注满,烘箱试验时,也极为容易出现浇口开裂的现象。
上述两个例子,都是成型过程发生了变化,对材料塑化度的要求没有变化,但是对加工性能提出了更高的要求。
影响塑料熔体粘度的因素

塑料熔体的剪切变稀塑料熔体为非牛顿流体,一个与注射成型密切相关的加工性是塑料熔体的剪切变稀,流体的粘度不随剪切速率变化而变化,这种流体称之为牛顿流体,如水、气体、低分子化合物液体或溶液为典型的牛顿流体,如果流体的粘度依赖于对其的剪切速率,这样的流体为非牛顿流体,大部分塑料熔体表现为非牛顿流体的特性。
非牛顿流体也有多种,塑料在熔融状态下表现出来的特性在图4的坐标中,呈现的是一条切应力先迅速上升而后缓慢上升的曲线,并且不存在屈服应力,这就是塑料熔体剪切变稀的流动特性。
即剪切速率的增加要比切应力的增加来得快,如图4所示。
与之相对应的是剪切变厚的现象。
但是常见的塑料熔体都呈现的是剪切变稀,也就是随着剪切速率的增加,熔体的粘度要降低,粘度降低有助于塑料熔体在模具型腔中的流动和填充。
注塑过程中塑料要通过料筒加热,然后经过注塑机的喷嘴,进入模具的主流道,流道以及模具的浇口,最后进入型腔。
熔体经过各个部分的剪切速率和粘度关系如图5所示,该图表明,塑料熔体在料筒中粘度较高,流动速度也小,到达浇口后,由于浇口的收缩作用,使得熔体流动速度增加,增大了剪切速率,降低了熔体的粘度,有利于熔体的充模。
宽MWD树脂比窄分布树脂剪切变稀程度大。
影响粘度的几个因素粘度是塑料加工性最重要的基本概念之一,是对流动性的定量表示,影响粘度的因素有熔体温度、压力、剪切速率以及相对分子质量等,下面分别叙述。
(1)温度的影响由前面的分析已经知道,塑料的粘度是剪切速率的函数,但是,塑料的粘度同时也受到温度的影响。
所以,只有剪切速率恒定时,研究温度对粘度的影响才有实际意义。
一般说,塑料熔体粘度的敏感性要比对剪切作用敏感强。
研究表明,随着温度的升高,塑料熔体的粘度呈指数函数方式下降。
这是因为,温度升高,必然使得分子间,分子链间的运动加快,从而使得塑料分子链之间的缠绕降低,分子之间的距离增大,从而导致粘度降低。
易于成型,但制品收缩率大,还会引起分解,温度太低,熔体粘度大,流动困难,成型性差,并且弹性大,也会使制品的形状稳定性差。
熔体粘度名词解释

熔体粘度1. 简介熔体粘度是指在高温下,固体物质变为液体时的流动性质。
熔体粘度的大小与物质的内部结构、分子间相互作用力以及温度有关。
熔体粘度是研究材料物理性质、熔融加工以及流变学等领域的重要参数。
2. 测量方法熔体粘度的测量通常使用粘度计进行,常见的粘度计有旋转粘度计、滴定粘度计和振荡粘度计等。
下面将介绍常见的旋转粘度计的测量原理。
2.1 旋转粘度计的原理旋转粘度计是通过测量物质在旋转圆柱体内的粘度来确定熔体粘度的一种方法。
其原理基于牛顿粘度定律,即粘度与剪切应力成正比。
旋转粘度计由旋转圆柱体和固定圆柱体组成。
在测量过程中,样品被放置在旋转圆柱体内,然后旋转圆柱体开始旋转。
通过测量旋转圆柱体所受到的剪切应力以及旋转圆柱体的转速,可以计算出熔体的粘度。
2.2 测量步骤旋转粘度计的测量步骤如下:1.准备样品:将待测样品加热至熔融状态,并确保样品没有气泡和杂质。
2.调节温度:根据需要测量的温度范围,将样品的温度调节到合适的范围。
3.放置样品:将样品倒入旋转圆柱体中,确保样品填满圆柱体。
4.开始测量:启动旋转圆柱体的旋转,并记录下旋转圆柱体的转速。
5.计算粘度:根据旋转圆柱体所受到的剪切应力以及旋转圆柱体的转速,使用相应的计算公式计算出熔体的粘度。
3. 影响因素熔体粘度的大小受到多种因素的影响,下面将介绍几个主要的影响因素。
3.1 温度温度是影响熔体粘度的最主要因素。
一般来说,随着温度的升高,熔体粘度会降低。
这是因为温度升高会使分子的热运动增强,相互作用力减弱,从而使熔体的流动性增加。
3.2 分子结构分子结构也是影响熔体粘度的重要因素。
分子结构的复杂性会增加分子间的相互作用力,从而使熔体粘度增大。
例如,分子链较长的聚合物具有较高的熔体粘度。
3.3 浓度物质的浓度也会对熔体粘度产生影响。
一般来说,浓度较高的物质具有较高的熔体粘度。
这是因为浓度的增加会增加分子间的相互作用力,从而使熔体粘度增大。
4. 应用领域熔体粘度在许多领域都有广泛的应用,下面将介绍几个主要的应用领域。
氧化铝熔体粘度

氧化铝熔体粘度
氧化铝熔体粘度是指在高温状态下,氧化铝固体逐渐融化形成的液态熔体的黏度。
氧化铝熔体是一种常见的高温熔体,具有很高的化学稳定性和机械强度。
在工业生产中,氧化铝熔体被广泛应用于陶瓷、玻璃纤维、金属氧化物陶瓷、电子陶瓷和其他高温材料的制备中。
氧化铝熔体的粘度受多种因素的影响,包括温度、压力、物质浓度、添加剂等等。
一般而言,随着温度升高,氧化铝熔体的粘度会逐渐降低。
这是由于高温下分子间距离增大、熔体流动性增强的原因。
另外,在压力升高的情况下,氧化铝熔体的粘度也会增加,因为高压会增加分子间的相互作用力,使得分子在流动时相互碰撞更加频繁,从而导致熔体黏度的增加。
在氧化铝熔体的制备中,添加剂的使用也会对其粘度产生影响。
例如,添加少量的碱金属氧化物(如Na2O、K2O)可以有效地降低氧化铝熔体的粘度,从而提高制备效率。
此外,对于氧化铝熔体的应用来说,控制其粘度也是非常重要的,因为熔体的粘度决定了其在制备过程中的流动性和涂覆性能等重要特征。
总之,氧化铝熔体粘度是制备和应用过程中需要考虑的一个关键因素,它受多种因素的影响,需要进行细致的控制和调整。
- 1 -。
- 1、下载文档前请自行甄别文档内容的完整性,平台不提供额外的编辑、内容补充、找答案等附加服务。
- 2、"仅部分预览"的文档,不可在线预览部分如存在完整性等问题,可反馈申请退款(可完整预览的文档不适用该条件!)。
- 3、如文档侵犯您的权益,请联系客服反馈,我们会尽快为您处理(人工客服工作时间:9:00-18:30)。
成型性能
常用塑料改进流动性能的方式
序号 塑料代号
俗名
改进方式
1
PE
聚乙烯
提高螺杆速度
2
PP
聚丙烯
提高螺杆速度
3
PA
尼龙(聚酰胺)
提高温度
4 POM
聚甲醛
提高螺杆速度
5
PC
聚碳酸酯
提高温度
6
PS
聚苯乙烯
两者都行
7
ABS
——
提高温度
8 PVC
聚氯乙烯
提高温度
9 PMMA 聚甲基丙烯酸甲酯 提 高 温 度
P E 105~136 0~126.6
HDPE 105~137 14~175.8
LDPE 105~125 14~175.8
MDPE 110~120 14~175.8
P P 160~176 14~175.8
粘度增 大倍数
134 100 14 4.1 5.6 6.8 7.3
成型性能
• 热塑性树脂存在这样一种倾向,如果其熔体 粘度对温度敏感的话对剪切速度就表现得不 敏感;相反,对剪切速度敏感的话对温度就 不敏感。唯一例外的树脂是聚苯乙烯,它的 熔体粘度不仅对温度敏感而且对剪切速度也 敏感。
2.11熔体粘度
成型性能
熔体粘度是反映塑料熔体流动的难易程 度的特性,是熔体流动阻力的度量,粘度越 高,流动阻力越大,流动越困难。
聚乙烯的分子形状及其分子量分布的不 同,其熔体粘度将有不同的表现。
❖从图1-1可以看出 ,乙酸纤维素、聚苯乙烯、聚甲基丙烯甲酯、 尼龙及聚碳酸酯等树脂,它们都是随着温度的增加粘度急剧下
表 观 103 粘 度 /Pa. s
聚丙烯T=210℃ 聚丙烯T=260℃
102
热塑性聚酯T=265℃
10
102
103
图1-3剪切速度/s-1
成型性能
压力对塑料熔体粘度的影响(示例)
序号
1 2 3 4 5 6 7
名称
熔点温度 (℃)
压力变化 范围/MPa
P S 131~165 0~126.6
A B S 130~160 14~175.8
降的,因此曲线的斜率较大,而聚乙烯及聚甲醛树脂则对温度 不敏感。
表
10 CA
8
观6
粘 度
4
3 LDPE
2
/Pa.
s
10 8
6
4
3
2
150
PS
PC
PMMHADPE
200 250
温度/℃
POM
PA 300
图1-1塑料熔体粘度与温度的关系
塑料熔体粘度对剪切速率的敏感度
成型性能
序号 1 2 3 4 5 6 7 8
10 8
PS
CA
表 6 PC
观
4 3
粘 HDP
度
2
E PA
/P 10
a.s
Байду номын сангаас
8 6
PAMPOMM LDPE
4 1.0 2.0 4.0 8.0
3 2
图161-2塑料施熔加体压粘力度M与p压a 力的关系
成型性能
❖图1-3中把热塑性聚酯和聚丙烯作了比较,如在100cm/S的低 速度区域,当剪切速度改变时热塑性聚酯的粘度几乎不变,而 聚丙烯树脂的粘度则随剪切速度的增加而急剧下降。
成型性能
• 聚苯乙烯(PS)之所以是最容易成型加工的树脂, 就是因为能简单地通过提高熔融温度,或通过提 高熔融树脂注入到模具时的速度(注射速度)的 方法来降低其树脂粘度。象尼龙含有官能团的树 脂其最佳成型温度(实际的注射温度)都在熔融 温度附近,而且其温度可调范围较小;由不活泼 原子团组成的加聚物,其最佳成型温度高得多, 温度可调范围大,通过提高注射速度的方法等都 可降低其熔体粘度,加聚物树脂的特性通过多级 注射速度的注塑机会得到更好的发挥。
塑料 ABS(最敏感)
PC PMMA PVC
PA PP PS LDPE(最不敏感)
敏感度
对剪切的敏感 度依次降低
图1-2和图1-3表示测定时因加压引起速度(称之为剪切速度)变 化时,各树脂熔体粘度的变化情况。从图1-2可知,聚苯乙烯及 各种聚乙烯树脂的熔体粘度随速度的增加表现出急剧下降的倾向, 而尼龙、聚甲醛、聚甲基丙烯酸甲酯及聚碳酸酯的熔体粘度则对 速度不敏感。