车间规划设计.doc
生产车间规划设计
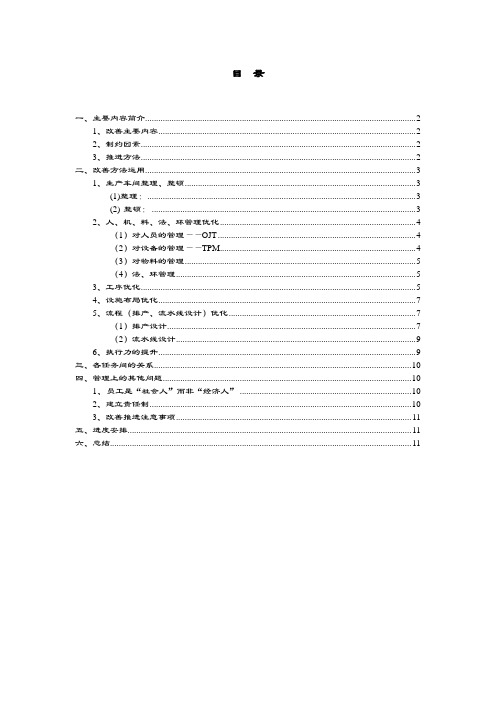
目录一、主要内容简介 (2)1、改善主要内容 (2)2、制约因素 (2)3、推进方法 (2)二、改善方法运用 (3)1、生产车间整理、整顿 (3)(1)整理: (3)(2) 整顿: (3)2、人、机、料、法、环管理优化 (4)(1)对人员的管理——OJT (4)(2)对设备的管理——TPM (4)(3)对物料的管理 (5)(4)法、环管理 (5)3、工序优化 (5)4、设施布局优化 (7)5、流程(排产、流水线设计)优化 (7)(1)排产设计 (7)(2)流水线设计 (9)6、执行力的提升 (9)三、各任务间的关系 (10)四、管理上的其他问题 (10)1、员工是“社会人”而非“经济人” (10)2、建立责任制 (10)3、改善推进注意事项 (11)五、进度安排 (11)六、总结 (11)生产车间规划设计一、主要内容简介生产车间规划设计是从科学管理角度出发,对人员、物料、设备、能源、信息等所组成的集成系统,运用数学、运筹学和社会科学的专门知识和技术,结合工程分析与设计的原理和方法,对该系统进行Plan(计划)、Do(实施)、Check(检查)、Action(处置)。
1、改善主要内容我认为今后生产车间改善主要内容如下:(1)生产车间5S,三定,目视化管理;(2)人、机、料、法、环管理优化;(3)工序优化;(4)设施布局优化;(5)流程优化[排产、加工方式(流水线)设计];(6)执行力的提升;2、制约因素改善计划能否顺利进行取决于以下几个因素:(1) 目标正确、领导支持;(2) 管理制度健全、执行坚决;(3) 方法科学、操作人员支持;(4)管理上的科学;3、推进方法改进永无止境,坚持先易后难、逐步、全面的推动改进工作,由粗到细,由细到精,进而精益求精。
二、改善方法运用1、生产车间整理、整顿当前我公司生产车间工具、物料等摆放还不够整齐,因此造成了准备时间、寻找工具等时间过长,因此改善初期,首当其冲的应该对生产车间进行整理整顿。
化工车间布置设计(DOC)

第五章 化工车间布置设计车间布置设计涉及的专业:以工艺、配管专业为主导与总图、土建、自控、电力、设备等专业配合第一节 车间布置设计概述一、车间布置的依据1.应遵守的设计规范和规定《建筑设计防火规范》(GBJ 16-87)、《石油化工企业设计防火规定》(GB50160-99)、《化工企业安全卫生设计标准》(HG20571-95)、《工业企业厂房噪声标准》(GB2348-90)、《爆炸和火灾危险环境电力装置设计规定》(GB50058-92)、《中华人民共和国爆炸危险场所电气安全规程》(试行)(1987)等。
2.基础资料① 厂区总平面布置图(包括本车间同其他生产车间、辅助车间、生活设施的相互联系,厂内人流物流的情况与数量)。
②对初步设计需要带控制点工艺流程图,对施工图设计需要管道仪表流程图;工艺流程图 设备设计并选型流 用管道将各工段、设备 连接起来 车间布置设计间厂地范围内的布置 和车间设备(包括电气、在车间中的布置③物料衡算数据及物料性质(包括原料、中间体、副产品、成品的数量及性质,三废的数据及处理方法);④设备一览表(包括设备外形尺寸、重量、支撑形式及保温情况);⑤公用系统耗用量,供排水、供电、供热、冷冻、压缩空气、外管资料;⑥车间定员表(除技术人员、管理人员、车间化验人员、岗位操作人员外,还包括最大班人数和男女比例的资料);⑦建厂地形及气象资料。
二、化工车间布置的内容(一)车间的组成1、生产设施2、生产辅助设施3、生活行政设施4、其他特殊用室5、通道6、最近发展余地三、车间布置原则1.车间布置设计要适应总图布置要求,与其它车间、公用系统、运输系统组成有机体。
2.最大限度地满足工艺生产包括设备维修要求。
3.经济效果要好;有效地利用车间建筑面积和土地;要为车间技术经济先进指标创造条件。
4.便于生产管理,安装、操作、检修方便。
5.要符合有关的布置规范和国家有关的法规,妥善处理防火、防爆、防毒防腐等问题,保证生产安全,还要符合建筑规范和要求。
车间设计方案

车间设计方案1. 引言车间设计是指将生产车间进行合理的规划和布局,以实现生产要求和生产效率的最大化。
一个良好的车间设计方案可以提高生产流程的效率、降低生产本钱、提高产品质量,并保障员工的工作平安和舒适度。
本文将讨论车间设计方案的重要性,并提供一些设计原那么和方法。
2. 设计原那么在车间设计方案中,应遵循以下原那么:2.1 空间利用合理利用车间内的空间是提高生产效率的关键。
设计师应根据生产设备的布局和工艺流程的要求,合理划分车间内的区域和行走通道,以最大化地利用空间。
2.2 流程优化车间的布局应符合生产流程的要求,使得物料和信息的流动能够到达最优化。
对于多个生产工序,应考虑工序之间的距离和物料的流动方向,以减少物料运输时间和人员移动。
2.3 平安性车间设计应考虑员工的工作平安。
应设置合理的平安通道和紧急出口,并为员工提供必要的平安设备和培训。
此外,应考虑危险源的隔离和防护,在设计时可采用防护设施和标识来提高工作平安性。
2.4 环境舒适度良好的工作环境可以提高员工的工作效率。
车间设计方案应考虑气候控制、噪音控制、照明和通风等因素,以提供舒适的工作环境。
2.5 灵巧性车间设计应具备一定的灵巧性,以适应未来的变化和扩展。
设计师应考虑到未来可能的设备增加和工艺改良,预留出足够的空间和电力容量。
3. 设计方法在进行车间设计方案的制定时,可以采用以下方法:3.1 数据采集和分析首先,需要对生产车间的原始数据进行采集。
这包括车间的尺寸、设备列表、工序流程、物料流动等方面的数据。
然后,通过对数据进行分析,了解车间的瓶颈和优化空间。
3.2 三维建模利用三维建模软件,设计师可以根据采集到的数据和分析结果,创立一个虚拟的车间模型。
通过模拟和优化,可以更好地理解车间布局的效果,并进行必要的调整和优化。
3.3 排布设计在进行车间的排布设计时,应根据生产流程和工艺要求进行布局规划。
通过合理划分区域和设备的位置,优化物料和信息的流动,并确保员工的平安和舒适。
装配车间规划设计(经典)
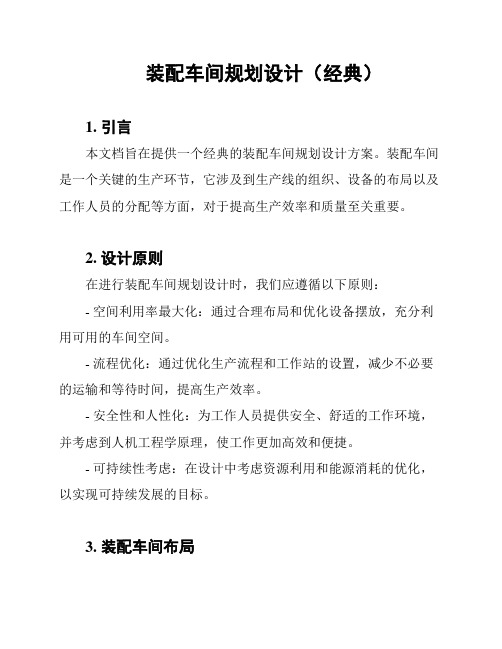
装配车间规划设计(经典)1. 引言本文档旨在提供一个经典的装配车间规划设计方案。
装配车间是一个关键的生产环节,它涉及到生产线的组织、设备的布局以及工作人员的分配等方面,对于提高生产效率和质量至关重要。
2. 设计原则在进行装配车间规划设计时,我们应遵循以下原则:- 空间利用率最大化:通过合理布局和优化设备摆放,充分利用可用的车间空间。
- 流程优化:通过优化生产流程和工作站的设置,减少不必要的运输和等待时间,提高生产效率。
- 安全性和人性化:为工作人员提供安全、舒适的工作环境,并考虑到人机工程学原理,使工作更加高效和便捷。
- 可持续性考虑:在设计中考虑资源利用和能源消耗的优化,以实现可持续发展的目标。
3. 装配车间布局装配车间布局应根据生产流程和产品特点进行规划。
以下是一个经典的装配车间布局示意图:![装配车间布局示意图]()车间布局包括以下主要的区域:- 原材料存储区:用于存放待装配的原材料和零部件,方便取用和管理。
- 生产线:按照产品的装配流程设置的工作站,工作人员按照一定的工序进行装配操作。
- 检测区:用于对装配完成的产品进行质量检测和测试。
- 成品存储区:存放已完成装配的产品,待进一步包装和发运。
4. 设备配置装配车间需要考虑所需的设备配置,以满足生产需求。
常见的设备包括:- 装配工作台:提供工作人员进行装配操作的工作台,设备应便于调整和适应不同的生产需求。
- 输送系统:用于将原材料、零部件和成品在生产线各个工作站之间进行顺畅的传送,提高生产效率。
- 检测设备:用于对产品进行质量检测和测试的设备,确保产品符合规定的质量标准。
- 存储设备:用于存放原材料、零部件和成品的货架、仓库等设备。
5. 人员分配合理的人员分配是提高装配车间效率的关键。
人员分配应根据生产流程和工作站的需求进行安排,确保每个工作站都有足够的工作人员。
此外,应进行培训和技能提升,以提高工人的操作技术和生产质量。
6. 安全与环境保护在装配车间规划设计中,我们应重视安全与环境保护。
第五章 车间布置设计

第五章车间布置设计第一节车间布置设计的内容和程序一、车间布置设计的程序、内容及相互关系在完成初步设计工艺流程图和设备选型之后,进一步的工作就是将各工段与各设备按生产流程在空间上进行组合、布置,并用管道将各工段和各设备连接起来。
前者称车间布置,后者称管道布置(配管设计)。
(一)车间布置初步设计车间布置初步设计的最后成果是一组平(剖)面布置图(初)或一只布置模型加有关照片。
(二)车间布置施工图设计车间布置施工图设计的最后成果是最终的车间布置平(剖)面图,这是工艺提供给其他专业的基本设计条件。
它给土建业提供建筑结构的尺寸和标高;设备支脚、操作平台、楼梯、通道、道路的位置与要求;防火、防爆、防腐和物料及设备运输要求。
它给设备设计部门提供容器与换热器的支脚形式与位置,管口方位等。
对电气和仪表专业提供配电室,控制室位置,电器及仪表的安装位置,电缆走向,开关板和仪表屏位置等。
(三)管道布置设计简单的小型车间可以直接在设备图上进行管道布置,一般规模较大和较复杂的车间应在配管模型上进行三度空间的配管。
管道布置的最后成果是:①经过补充和校核的车间布置平(剖)面图,供设备安装;②管道布置图或配管模型加管段图,供管道预制与安装。
二、车间布置设计的内容车间布置设计的内容可分为车间厂房布置和车间设备布置。
车间厂房布置是对整个车间各工段、各设施在车间场地范围内,按照它们在生产中和生活中所起的作用进行合理的平面和立面布置。
设备布置是根据生产流程情况及各种有关因素,把各种工艺设备在一定的区域内进行排列。
在设备布置中又分为初步设计和施工图设计两个阶段,每一个设计阶段均要求平面和剖面布置。
三、车间布置的依据1.常用的设计规范和规定主要设计规范和规定的名称,详细内容见《化工工艺设计手册》(国家医药管理局上海医药设计院编,化学工业出版社,1986年)及有关的标准和规范。
2.基础资料①对初步设计需要带控制点土艺流程图,对施工图设计需要管道仪表流程图;②物料衡算数据及物料性质(包括原料、中间体、副产品、成品的数量及性质,三废的数据及处理方法);③设备一览表(包括设备外形尺寸、重量、支撑形式及保温情况);④公用系统耗用量,供排水、供电、供热、冷冻、压缩空气、外管资料;⑤车间定员表(除技术人员、管理人员、车间化验人员、岗位操作人员外,还包括最大班人数和男女比例的资料);⑥厂区总平面布置图(包括本车间同其他生产车间、辅助车间、生活设施的相互联系,厂内人流物流的情况与数量)。
生产车间规划方案

目录1.基本概述1.1车间现状 (3)1.2 预留产能可扩展空间要求 .................................................................... ..32.车间布局2.1细节要求................................................................................................ . (4)2.2 车间布局........................................................................................ . . (5)3.工作条件 (6)3.1电源 (6)3.2供电线缆 (7)3.3 电气控制箱 (7)3.4气路配置 (7)3.4气管 (7)3.5压缩空气 (7)4.安装条件 (8)4.1 温度 (8)4.2 湿度 (8)4.3空气 (8)5. 地面条件 (9)5.1地面强度 (9)5.2 地面材料 (9)6.费用 (10)1.基本概述1.1车间现状生产中心一楼车间长度是44米,宽度为27米,总面积为1152平方米(不包含工装治具房),目前厂车前间面地为普通的水磨石地面,且没有建立起防静电系统,无法满足SMT车间的防静电要求,车间预留两个接地端子,后续可以建立SMT车间的静电防护系统。
车间内无调空和加湿设备,无法满足SMT车间对温湿间控度制的要求。
目前2条线备用车间电力充足,够满车足车间内所有设备的电力需求。
车间进入部分规划为后续的线边仓库,实现物料的快速配送。
1.2预留产能可扩展空间要求车间前期规划两条全自动化生产线,设备的尺寸示意图如图所示:生产设备最大的宽度为1.6M,总长度为18米,依据SMT标准的配置,如图所示:现有设备缺少SPI及AOI,需预留相应的空间为4米,总设备的长度需保证在24米内,随着公司的快速发张,且现有的SMT贴片机无法满足现有的产能,预留两条可扩展的SMT生产线。
维修车间简单设计方案
维修车间简单设计方案维修车间是一个专门用来进行车辆维修和保养的空间,为了提高工作效率和维修质量,设计一个合理的维修车间非常重要。
以下是一个简单的维修车间设计方案:一、空间布局:1. 车间应具备安全合理的布局,并分为不同的区域,包括车辆维修区、部件存放区、工具设备区和办公区等。
2. 车辆维修区应该设置在车间的中央位置,便于维修人员操作和车辆进出。
3. 部件存放区应设在车辆维修区附近,方便维修人员取用所需的部件。
4. 工具设备区应该整洁有序,方便维修人员找到所需的工具。
5. 办公区应位于车间的一侧,设置办公桌、文件柜等设施。
二、设备和工具:1. 维修车间应配备各种必要的维修设备,如千斤顶、电动工具、焊接设备等。
2. 车间还应配备必要的专业工具,如扳手、套筒等,以满足各类维修的需求。
三、照明和通风:1. 维修车间应充分利用自然光线,增加车间的可见度。
2. 同时,应在车间周围设置足够的窗户,保证车间有良好的通风条件,避免因长时间工作而引发的安全和健康问题。
四、电源和燃气:1. 维修车间应配备足够的电源插座,以便于维修设备的使用。
2. 如需要使用燃气设备,应有专门的燃气管道和燃气安全设施。
五、安全防护:1. 维修车间应设置明显的安全警示标识,并配备灭火器等消防设施,以应对突发火灾等事故。
2. 车间应有现行的安全操作规程,并配备足够的防护用品,如手套、护目镜等,保障工作人员的安全。
六、环保措施:1. 维修车间应设置专门的废品收集和处理区域,进行垃圾分类和处理,保护环境。
2. 如有需要,可以考虑安装环境监测设备,及时发现和处理有害气体等环境问题。
以上设计方案仅为简单设想,实际维修车间的设计应根据具体情况进行调整和优化,以确保车间的安全、高效运营。
食品生产车间规划图
. 整体规划.冷库车间平面图(3号-2号-12号)西北 东南2000031750 2500 3175030000 6000 30000 9000 20000 20000 20000 5000 65000冷库内走廊恒温库1号 设计使用温度 -15℃~-10℃ 20×30=600m 2恒温库6号 设计使用温度 -15℃~-10℃ 20×30=600m 2封闭式冷库外走廊 低温库4号 设计使用温度 -30℃~-25℃ 20×30=600m 2低温库L3号 设计使用温度 -30℃~-25℃ 20×17=340m 2 低温库5号 设计使用温度 -30℃~-25℃ 20×30=600m 2恒温库2号 设计使用温度 -15℃~-10℃ 20×30=600m 2 封闭式冷库内走廊 食品罐头车间12号 (可以生产糖水食品仁【多种软包、瓶装、马口铁装】、盐水食品仁、枫糖食品仁、蜂蜜食品仁、糖水黑食品、原味金黄食品酱、调味金黄食品酱、金食品膏、金黄食品沙、纯板食品蓉、食品蓉、冷冻原味食品茸、冷冻食品浆、冷冻食品泥、中式格拉帕食品、含气甘食品仁、含气枫糖板食品仁、含气食品【开口】、欧式真空食品、中式MARRON GLACE 、糖霜食品纳豆、冰皮食品甘纳豆、甜糯食品干、欧式即食食品酱、冷冻即食金黄食品酱、养生食品干)冷冻食品车间2号 (可以生产:速冻生制食品、速冻熟制食品、速冻开口笑栗速冻盐煮樱花食品、速冻樱花烤食品、速冻韩式烧食品、速冻糖炒板食品、速冻热烫板食品仁、速冻食品米、速冻糖炒食品仁、速冻蒸制食品仁、速冻刀削食品仁、速冻刀削糖渍食品仁、速冻香糯贡食品、速冻烤食品仁、矾水保鲜食品仁、真空保鲜食品米)-根据当地产品的品种特点可以开发其他类板栗产品。
食品调理类在调理车间生产(调理类包括食品万、食品布丁、食品羊羹、食品派、食品饼、食品铜锣烧、59秒食品浆等 13000制冷 机房 控制室60m3地下冷却池 东北西南冷库车间立面示意图东北面西北面西南面东南面说明:由于气温较高,耗冷量较大,图中标的设计温度看起来较低,主要考虑板栗收获季节会提前,板栗本身的田间热比较大,如果设计低了,很难降下温,板栗降不下温度是最大的忌讳,一般用麻袋收货的板栗要求入库12小时后温度降到8℃,用开眼蛇皮袋收货的板栗要求入库12小时后温度降到11℃。
生产车间规划方案
7.定期评估实施效果,持续优化调整。
六、总结
本生产车间规划方案从企业实际需求出发,遵循合规性、安全性、效率性、人本性和可持续性原则,为生产车间提供了全面、详实的规划。通过实施本方案,将有助于提升生产效率、保障产品质量、确保生产安全、提高员工满意度,为企业持续发展奠定坚实基础。
4.质量管理提升
-建立健全质量管理体系,确保产品质量稳定。
-强化生产过程质量控制,降低不良品率。
-提高员工质量意识,加强培训,提升操作技能。
5.安全生产保障
-制定完善的安全生产规章制度,明确各级人员职责。
-加强安全培训,提高员工安全意识和应急处理能力。
-定期进行安全检查,及时发现并整改安全隐患。
6.员工关怀与培训
生产车间规划方案
第1篇
生产车间规划方案
一、前言
本方案旨在为生产车间提供科学、合理、人性化的规划,以提高生产效率,保障产品质量,确保生产安全,同时遵循国家相关法律法规及行业标准。
二、规划目标
1.提高生产效率,降低生产成本。
2.优化生产流程,缩短生产周期。
3.提升产品质量,降低不良率。
4.确保生产安全,减少安全事故。
-设备布局符合工艺要求,减少物料搬运距离,降低劳动强度。
-合理设置安全通道,确保安全生产。
2.设备选型与布局
-选择高效、节能、环保的设备,满足生产需求。
-根据设备特性,合理布局,提高设备利用率。
-设备安装符合国家标准,确保设备安全运行。
3.生产流程优化
-分析现有生产流程,找出瓶颈环节,进行优化。
-采用先进的生产管理方法,提高生产效率。
六、总结
本生产车间规划方案立足于企业实际需求,遵循合法合规、安全第一、效率优先、人性化设计等原则,旨在为生产车间提供科学、合理、人性化的规划。通过实施本方案,将有效提高生产效率,保障产品质量,确保生产安全,提升员工满意度,为企业可持续发展奠定基础。
焊接车间规划
焊接车间规划1. 引言本文档旨在提供焊接车间规划的详细信息,以确保焊接车间的安全、高效和有效运营。
焊接车间作为一个核心生产环节,对工作人员的安全和产品质量至关重要。
合理的规划能够优化生产流程,并提高工作效率。
2. 设计目标焊接车间的设计目标包括以下几个方面:- 提供安全、健康的工作环境,保护工作人员免受可能的伤害;- 优化生产流程,减少生产时间,提高生产效率;- 提供适当的工作空间和设备,以满足不同焊接任务的需求;- 保证焊接质量,确保产品符合相关标准和要求。
3. 空间规划焊接车间的空间规划应根据工艺流程和生产需求进行布局设计。
具体需要考虑的因素包括:- 设备布局:根据焊接工艺流程和设备需求,合理布置焊接设备和工作站。
- 动线设计:建立高效的工作流程,减少工人的行走距离和时间浪费。
- 空间利用:最大限度地利用可用空间,确保设备和物料摆放有序并易于管理。
- 通风与照明:提供良好的通风系统和充足的照明设施,以确保工人的安全和舒适。
4. 安全措施焊接车间是一个潜在的危险环境,应采取必要的安全措施以保护工作人员的安全。
- 个人防护装备:提供必要的个人防护装备,如焊接面罩、防护服、耳塞、手套等。
- 安全培训和指导:确保工作人员接受焊接操作的安全培训,并定期进行安全指导。
- 灭火设备:配置灭火器和灭火设备,并确保操作人员熟知使用方法。
- 紧急撤离计划:制定紧急撤离计划,并定期组织演练,确保工作人员能够迅速、有序地撤离。
5. 质量控制焊接车间的质量控制是确保制品符合相关标准和要求的关键。
以下是一些常用的质量控制措施:- 焊接过程监控:使用专业的监测设备,监控焊接过程的各项参数,如电流、电压、温度等。
- 检测工具:配备必要的检测设备,如X射线检测仪、超声波探伤仪等,进行焊接质量的检测和评估。
- 质量记录:建立完整的质量记录和跟踪系统,以便追溯和处理可能出现的质量问题。
6. 维护与保养良好的设备维护与保养是确保焊接车间正常运行的关键。
- 1、下载文档前请自行甄别文档内容的完整性,平台不提供额外的编辑、内容补充、找答案等附加服务。
- 2、"仅部分预览"的文档,不可在线预览部分如存在完整性等问题,可反馈申请退款(可完整预览的文档不适用该条件!)。
- 3、如文档侵犯您的权益,请联系客服反馈,我们会尽快为您处理(人工客服工作时间:9:00-18:30)。
整车工厂冲压车间规划设计原理
摘要:结合实际案例,介绍整车工厂冲压设计冲压车间在规划设计阶段应考虑的原则,提出结合实际优化设计、降低投资和运行成本、提高生产效率、利于扩建需求的设计原则。
1、产品产能、工艺、设备与生产管理规划
1.1产品输入
(1)投产车型
不同的车型其工艺流程、工艺布局、设备选型、模具与物料缓冲区及扩建预留都不一样。
该基地投产车型包括7座家用车、紧凑车型、中型车、SUV等。
(2)自制件种类与数量
为保证产量和质量,确定车门外板、左/右翼子板、发动机盖、车顶盖、尾门外板等10多个重要车身覆盖件采取自制,内板有供应商提供,以减少自身生产规模建设投资及降低运行成本、风险。
1.2产能
依据工厂产量测算:月产能(冲次)=小时产量*每日工作小时数*每月工作日*模具数线;
月实际产能(冲次)=每分钟实际冲次*60*每日工作时间小时数*每月工作日
1.3工艺
车身外板多为三维非规则曲面。
尺寸大、形状复杂、,外观质量要求极高以满足造型、配合精度高、状和尺寸的一致性好以保证焊接和装配质量的对不同车型零件,冲压的工艺特点、设备、模具、材料都不同。
为精益的投资和运行成本、该车间选择4序而非5序工艺,两者优缺点如下:
(1)4序工艺有点是投资、运行成本相对较低,与本地其它工厂生产工艺相同,满足产品柔性;缺店是较复杂零件的模具设计难度较高、模具较负责、成产稳定性较差。
(2)5序工艺有点是可简化相应的模具设计,减小模具设计难度,降低模具结构复杂性,提高稳定性;缺点是公司其他共产均为4序压力机生产,若5序设备损坏,需5序设备损害,序5序生产较大影响,且占地与设备投资大。
1.4.1压力机
(1)根据产量、生产线自动化程度,按工艺流程排列,通常采用以双动力机为首的加上多台单动宽台面压力机,多以贯通纵向排列的形式。
(2)由于车身覆盖件形状复杂,单动压力机很难达到要求,在拉深工序,采用2250吨宽台面双动压力机
(3)由于车身覆盖件轮廓尺寸大而材料厚度小,同时为了缩短换模时间,其它切边、翻边、整形工序采用宽台面多点且带活动台面的1000吨压力机
为控制投资、便于生产维保、两条压力机线供应为济南二机床集团有限公司,其特点为:
1)适合高强度钢材的冲压使用;
2)配合单臂机械手及高速拆垛系统,可不停机更换料垛;
3)滑块运动曲线特性好,速度最高可达18转/分钟,能实现一模双件的冲压;
4)生产线的冲压效率有效提升;
5)整线设计最大冲压节拍为12次/分钟,能实现一模双件的冲压。
1.4.2落料翻转系统
主要车门板需要翻转,落料翻转单元采用10001吨的偏心轮式压力机,使用Fanuc六轴机器人搬运零件,落料与翻转工艺一体化程序启动后,机器人抓取板材送至落料压力机上,整形后再由另一端的Funuc六轴机器人去下在并放置在完工台上。
主要参数:清洗机速度最大120米/分钟(可调式),挤干輥上輥压力最大100PL1,泵输出量约600升/分钟,邮箱加热器功率6KW
1.4.4自动化输送线
零件输送一般有3中方式:
a机器人(六台机器人+拆垛对中+零件输送带)
b.传统机械手(八台机械手+3台穿梭机+拆垛对中+零件输送带)
c.高速机械手(5台机械手+拆垛对中+零件输送带)
该车间选择C模式
主要特点:
1、各轴驱动由电机提供电能,采用德国REXROTH伺服电机;
2、定位精准,可靠性高,搬运负载80kg;
3、可完成传统机械手取件、穿梭和上件三个设备的工作;
4、整线最高节拍可达12次,比普通机器人生产节拍提升40%以上;
5、零件在传送过程中不需要旋转、设备少、技术成熟。
1.4.5天车
天车用于吊运模具、板料等,为50T/10T桥式双梁起重机,由于大车、小车、小车轨道、护栏、大小卷扬、吊钩、滑轮、钢丝绳、驾驶室、变频室、变频器、遥控系统、大车轨道、电源安全滑触线等组成升起及行走机构采用变频调速控制,具备驾驶室控制、控制两种操作模式。
大车轨道采用50kg/m钢轨,小车轨道采用焊接压板、大车、小车、主钩、滑轮、副钩均采用变频调速,变频器附带用于设置参数和手动输入的面板,供应商为美国Allen-Brandly.
1.4.6废料输送线规划
新建整车厂产能一般超过30万辆/年,每天产生大量冲压废料,占材料比25%-40%,要做好废料排送和处理,方式一般为:
(1)从废料压力机冲模上排除下后经洞口落入地下室的废料输送带上;
(2)将废料率选到处理车间;
(3)将废料率选、分选,然后货车运送到厂区外
1.5 零件检测
设置如下工序:
(1)下线后首次质检:依靠专业员工的目测,触觉,同时借助砂纸、砂网等工具;
(2)抽检零件在专业监测的太进行平行光的质量光强监测;
(3)设有某车厂标准的质量评估体系,它是非常重要的检测环节,不仅能通过光学来检测和提升零件质量的高精度,同时还能检测模具,以进行保养和调整,确保后面零件在制作的过程中的合格率。
规划有板料质量,成型性监控、尺寸监控、检具监控维护、缺陷品处理、质量报警环节。
1.6生产管理
(1)生产计划管理:建立每日生产计划控制流程,板料和零件物料清单表等;
(2)运输管理:吊车运转板料、拖车运转零件、叉车近在库房装卸零件,运输路线规划;
(3)库存管理:支持零件数据跟踪、库房零件布局、最大最小库存设置、先进的先出保证;
(4)原材料管理:板料接收流程及库存设置,可疑板料处理;
(5)落料件管理:最大最小缓冲量设置,落料件质量控制;
(6)半成品管理:生产工序在24小时内完成工序并入库,试模、项目工序件隔离存放,专项处理;上述系统构成了冲压车间最基本的生产运行流程(见图1)
2、厂房平面规划
(1)
根据生产线条数和每条线生产前后缓冲面积、物流通道大小、叉车转弯半径等综合考虑生产区域面积
(2)根据面归回模具尺寸,直接计算模具面积。
模具面积乘以物流系数(物流通道、模具间存通道等)除以2得出实际所需面积大小
(3)根据规划零件工位器具尺寸、装箱定额,计算库房面积;考虑冲压件入库物流、焊装车间取件物流最短为原则,一般布在生产线尾并靠近焊装车间
(4)如数模尺寸已知道,直接计算检模具面积;如车型模具尺寸不清楚,采用现有相似的车型类比法;平均法计算检具面积大小,最后乘以物流系数(物流、检具间存放通道等)
(5)模修面积由模修设备所占面积、同时维修多少套模具多占面积构成,位置应考虑各线模具运转方便、物流最短、模修粉尘院里生产线等因素
(6)板料存放区根据产量、周转时间、板料平均大小计算。
现为了节省面积,一般采用里提货价、集中存放、统一发送的方式。
(7)根据钣金返修数量计算其钣金返修面积,叉车充电去应同时满足多少辆叉车充电区应同时满足多少辆叉车充电,考虑防爆设设施;
(8)办公生活去考虑管理人员、工程师、信息文档、参观接待、会议室、培训室、工具材料库房、卫生间等;(9)工段园地根据实际空间布局(10)考虑工
上下班进进入工厂车间、生产线员工与车间内部人员走动、人员参观路线
3、土建公用设计
考虑跨距和柱距、轨顶标高,电控平台长宽高度、车间大门及物流们、厂房载荷、工作环境、地坪涂料、采光要求、天车吨位、设备与废料输送线地沟深度与防水因素
(1)该车间厂房长为144m,宽度为3个30跨组成,方便柱距面8m,方便压机与自动化线电控箱、地面轨道车布置。
(2)轨顶标高主要考虑天车高度与压力机高度,并留有余量一。
一般天车的最低点比压机的最高点高出2米左右。
(3)电控箱平台高度根据工艺布局、电控箱平台低下用途来决定,长款要满足设备电柜摆放。
该车间的自动化县电控箱设在柱间电控平台上,平台底标高4.5m,荷载5KPa
(4)车间大门及物流门主要考虑其高度和宽度以及物流顺畅性。
(5)厂房载荷设计:
a、模具存放区、模修区、板料存放区、检具存放区安150KPa进行承载设计;
冲压件缓冲区为50KPa,其余100KPa。