烧结机自动化控制系统设计
烧结厂烧结机设备
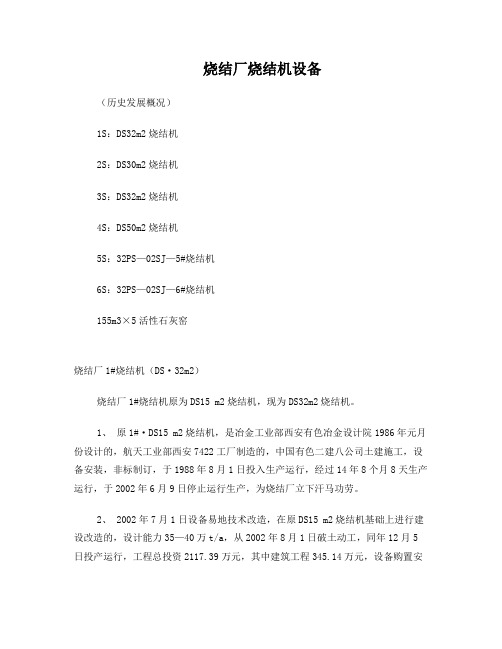
烧结厂烧结机设备(历史发展概况)1S:DS32m2烧结机2S:DS30m2烧结机3S:DS32m2烧结机4S:DS50m2烧结机5S:32PS—02SJ—5#烧结机6S:32PS—02SJ—6#烧结机155m3×5活性石灰窑烧结厂1#烧结机(DS·32m2)烧结厂1#烧结机原为DS15 m2烧结机,现为DS32m2烧结机。
1、原1#·DS15 m2烧结机,是冶金工业部西安有色冶金设计院1986年元月份设计的,航天工业部西安7422工厂制造的,中国有色二建八公司土建施工,设备安装,非标制订,于1988年8月1日投入生产运行,经过14年8个月8天生产运行,于2002年6月9日停止运行生产,为烧结厂立下汗马功劳。
2、 2002年7月1日设备易地技术改造,在原DS15 m2烧结机基础上进行建设改造的,设计能力35—40万t/a,从2002年8月1日破土动工,同年12月5日投产运行,工程总投资2117.39万元,其中建筑工程345.14万元,设备购置安装1664.44万元,其他107.81万元,工程由四大部分组成:烧结系统、原料系统、成品输送系统、除尘系统;烧结机系统生产运行80块台车,设计82块台车。
3、 DS32m2烧结机设计单位为冶金工业部西安有色冶金设计院设计。
4、 DS32m2烧结机系统设备施工单位为“十二冶安装公司、十冶设备安装公司、十二冶一公司、厂建安公司、江苏防腐工程公司进行承建。
5、 DS32m2烧结机系统工程项目确定后,龙钢集团规划部成立了一烧改造工程项目,全权处理工程施工过程中的各项业务,而在整个施工过程中该项目组的同志齐心协力、积极主动完成了领导交给的任务,克服了原旧址地下障碍物较多、基础开挖难度大、施工场地狭小、工期紧,与原生产衔接紧密等不利因素给工程的建设带来了很大的困难。
烧结厂2#烧结机(DS30m2)烧结厂2#烧结机原为DS28m2烧结机,西安有色冶金设计院设计的,山西省省建一公司三处承担土建施工,非标制标,设备安装于1993年元月份施工,当年12月30日投入生产运行,工程总投资为1723万元,设计共有80块台车,运行生产台车79块。
钢铁厂设备维护手册

钢铁厂设备维护手册第一章钢铁厂设备概述 (3)1.1 设备分类 (3)1.1.1 炼铁设备 (3)1.1.2 炼钢设备 (3)1.1.3 轧钢设备 (3)1.1.4 辅助设备 (4)1.1.5 自动化控制系统 (4)1.2 设备重要性 (4)1.2.1 保证生产效率 (4)1.2.2 保证产品质量 (4)1.2.3 提高安全功能 (4)1.2.4 节约能源和成本 (4)1.2.5 促进技术创新 (4)第二章设备维护基本概念 (4)2.1 维护定义 (4)2.2 维护类型 (5)2.3 维护原则 (5)第三章设备检查与监测 (5)3.1 检查流程 (5)3.1.1 准备工作 (5)3.1.2 实施检查 (6)3.1.3 检查结果分析 (6)3.2 监测方法 (6)3.2.1 在线监测 (6)3.2.2 离线监测 (6)3.2.3 人工监测 (6)3.3 检查周期 (6)3.3.1 设备检查周期 (6)3.3.2 检查周期的调整 (7)第四章设备润滑管理 (7)4.1 润滑剂选择 (7)4.2 润滑周期 (7)4.3 润滑设备维护 (7)第五章设备故障分析与处理 (8)5.1 故障类型 (8)5.2 故障原因分析 (8)5.2.1 机械故障原因 (8)5.2.2 电气故障原因 (8)5.2.3 液压故障原因 (8)5.2.4 润滑故障原因 (9)5.2.5 控制系统故障原因 (9)5.3.1 机械故障处理方法 (9)5.3.2 电气故障处理方法 (9)5.3.3 液压故障处理方法 (9)5.3.4 润滑故障处理方法 (10)5.3.5 控制系统故障处理方法 (10)第六章设备维修与保养 (10)6.1 维修流程 (10)6.1.1 故障报告 (10)6.1.2 故障诊断 (10)6.1.3 维修实施 (10)6.1.4 维修验收 (10)6.2 保养周期 (10)6.2.1 定期保养 (10)6.2.2 特殊保养 (11)6.3 保养内容 (11)6.3.1 一级保养 (11)6.3.2 二级保养 (11)第七章设备更新与改造 (11)7.1 更新原则 (11)7.1.1 实用性原则 (11)7.1.2 先进性原则 (11)7.1.3 安全性原则 (11)7.1.4 经济性原则 (12)7.1.5 可持续性原则 (12)7.2 改造方法 (12)7.2.1 技术改造 (12)7.2.2 结构改造 (12)7.2.3 功能改造 (12)7.2.4 管理改造 (12)7.3 更新与改造周期 (12)7.3.1 设备更新周期 (12)7.3.2 设备改造周期 (12)7.3.3 更新与改造计划 (12)第八章设备安全管理 (12)8.1 安全制度 (12)8.1.1 制定目的 (12)8.1.2 适用范围 (13)8.1.3 安全制度内容 (13)8.2 安全培训 (13)8.2.1 培训目的 (13)8.2.2 培训对象 (13)8.2.3 培训内容 (13)8.3 应急预案 (14)8.3.2 应急预案内容 (14)第九章设备维护成本控制 (14)9.1 成本构成 (14)9.1.1 直接成本 (14)9.1.2 间接成本 (14)9.2 成本控制方法 (14)9.2.1 预防性维护 (15)9.2.2 经济性维护 (15)9.2.3 资源整合与优化 (15)9.3 成本分析 (15)9.3.1 成本核算 (15)9.3.2 成本优化 (15)9.3.3 成本控制效果评价 (16)第十章设备维护团队建设与培训 (16)10.1 团队组织结构 (16)10.1.1 组织架构设计 (16)10.1.2 团队人员配置 (16)10.2 培训计划 (16)10.2.1 培训目标 (16)10.2.2 培训内容 (17)10.2.3 培训方式 (17)10.3 培训效果评估 (17)10.3.1 评估方法 (17)10.3.2 评估周期 (17)第一章钢铁厂设备概述1.1 设备分类钢铁厂的设备种类繁多,根据其功能和用途,可分为以下几类:1.1.1 炼铁设备炼铁设备主要包括高炉、热风炉、烧结机、球团设备等,这些设备主要用于将铁矿石转化为铁水。
莱钢265m 2烧结机综合自动化控制系统

关键词 : 烧结 ; 综合 自 动控制 ; 基础 自 动化 ; 终点控制 ; 过程控制
中图分类号 : P 9 T 23 文献标识码 : A 文章编 号:0 4 4 2 (0 0 0 — 0 3 0 10 — 60 2 1 )4 0 5 — 3
莱钢 银 山型钢 炼铁 厂 2台 2 5i 烧 结 机 的控制 6 n 均 采 用施 耐 德 Q A T M系 列 P C, 然 基础 自动 U NU L 虽
的消除 。 12 下料流 量恒定 控制策 略 . 宽带 给料 P D调节 主要 通过 变频器 调节宽 带速 I
混 的水 分 蒸 发等 问题 。反馈 信 号 为 来 自二 混 的水 分测 试仪 检测 信 号 , 与二混 的设 定 值进行 比较后修 正 前馈 信 号 , 二 混加 水量 进行 反馈 校正 。系统 的 对
I
L——— —1 透气率控 制系统 卜_ 原料透气率检测 卜 — — _ 1 _ _
输 出量变化 影 响宽 带转 动 的稳定 性 ; 三是 实 现无 扰 动 投入 , 先确 定好 宽带 转速 初值 , 带启 动 时经 3 宽 ~
5 期 的 运行 , 周 当瞬 时 流量 在 P D调 节 范 围 内输 出 I 时, 自动 切换 到 P D调 节 ; I 四是 当工 况不 稳 时 , 瞬 如
第3卷 第4 2 期
21年 8 00 月
^ 1 / ^ 1 地
山 东 冶 金
S a d n Me al r y hnog tl g u
V0 _2 No 4 l . 3 Au u t 2 0 g s 01
》 息化建设《 信
~ !
菜钢 2 5m2 结机综合 自动化控 制 系统 6 烧
时流 量 波 动较 大且 无 规 律 , 可采 用 累计 调 节 方式 ,
冶金自动化之烧结球团工艺流程及主要设备简介

冶金自动化之烧结球团工艺流程及主要设备简介烧结工艺流程介绍---- 冶金自动化系列专题【导读】:为了保证供给高炉的铁矿石中铁含量均匀,并且保证高炉的透气性,需要把选矿工艺产出的铁精矿制成10-25mm的块状原料。
铁矿粉造块目前主要有两种方法:烧结法和球团法。
两种方法所获得的块矿分别为烧结矿和球团矿。
本专题将详细介绍烧结生产的工艺流程,主要工艺设备的工作原理以及控制要求等信息,其次,我们将简要介绍球团法生产的工艺流程,主要工艺设备的工作原理以及控制要求等信息。
由于时间的仓促和编辑水平有限,栏目中难免出现遗漏或错误的地方,欢迎大家补充指正。
铁矿粉造块的目的:◆综合利用资源,扩大炼铁用的原料种类。
◆去除有害杂质,回收有益元素,保护环境。
◆改善矿石的冶金性能,适应高炉冶炼对铁矿石的质量要求。
铁矿粉造块的方法:烧结法和球团法。
铁矿粉造块后的产品:分别为烧结矿和球团矿。
(供高炉炼铁生产的主要原料)一、烧结生产的工艺流程介绍:烧结是钢铁生产工艺中的一个重要环节,它是将铁矿粉、粉(无烟煤)和石灰、高炉炉尘、轧钢皮、钢渣按一定配比混匀。
经烧结而成的有足够强度和粒度的烧结矿可作为炼铁的熟料。
利用烧结熟料炼铁对于提高高炉利用系数、降低焦比、提高高炉透气性保证高炉运行均有一定意义。
烧结生产的流程目前生产上广泛采用带式抽风烧结机生产烧结矿。
烧结生产的工艺流程如图下所示。
主要包括烧结料的准备,配料与混合,烧结和产品处理等工序。
(附件五铁矿粉烧结工艺流程简介)烧结的原材料准备:含铁原料:含铁量较高、粒度<5mm的矿粉,铁精矿,高炉炉尘,轧钢皮,钢渣等。
一般要求含铁原料品位高,成分稳定,杂质少。
熔剂:要求熔剂中有效CaO含量高,杂质少,成分稳定,含水3%左右,粒度小于3mm的占90%以上。
在烧结料中加入一定量的白云石,使烧结矿含有适当的MgO,对烧结过程有良好的作用,可以提高烧结矿的质量。
燃料:主要为焦粉和无烟煤。
对燃料的要求是固定碳含量高,灰分低,挥发分低,含硫低,成分稳定,含水小于10%,粒度小于3mm的占95%以上。
3 烧结过程计算机应用

结生产多样全方位信息海量化、巨型化。
3 烧结过程计算机应用
3.1.3 烧结过程控制方案
(1) 烧结过程的控制方法
难以建立精确的数学模型,采用多种方法相结合 的智能集成优化控制。 软测量技术 预测模型 智能控制
计算机在钢铁冶金中的应用
3 烧结过程计算机应用
3.1.3 烧结过程控制方案
转数、风机入口阀门开度,相应调节热风流量。
余热回收风机 出口温度、压力的测量显示和报警
主抽风机
入口处的排气温度、压力、流量
计算机在钢铁冶金中的应用
3 烧结过程计算机应用
3.2.7 余热回收及主排气系统
余热发电
计算机在钢铁冶金中的应用
3 烧结过程计算机应用
3.2.8 除尘和水处理系统
机头
机尾
配料 成品
3.1.2 烧结过程的特征
3.1.3 烧结过程控制方案
计算机在钢铁冶金中的应用
3 烧结过程计算机应用
3.1.1 烧结工艺流程简介
计算机在钢铁冶金中的应用
3 烧结过程计算机应用
3.1.2 烧结过程的特征
复杂性 滞后性
工艺方面 流程长、环节多、影响因素复杂 机理方面
不确定性
强耦合性 高度非线性 信息多样性
第三章 烧结过程计算机应用
第三章 烧结过程计算机应用
3.1 烧结过程的特征和控制方案 3.2 烧结生产基础自动化 3.3 烧结生产信息采集和处理系统 3.4 烧结矿化学成分的控制 3.5 烧结过程状态的控制
计算机在钢铁冶金中的应用
3 烧结过程计算机应用
3.1 烧结过程的特征和控制方案
3.1.1 烧结工艺流程简介
烧结厂设计

烧结厂设计(engineering design of sinter piant)将细颗粒的铁(或锰)精矿、粉矿或二者的混合物配入一定量的熔剂、燃料,然后烧结加工成符合高炉(或铁合金电炉)冶炼所要求的粒度和成分的烧结矿的工厂设计。
烧结是工业生产上常用的一种造块方法,通过烧结还可以改善入炉原料的冶金性能。
烧结厂设计范围包括:烧结原料接受,贮存和混匀设施设计,烧结燃料准备设施设计,烧结熔剂准备设施设计,烧结配料室设计,烧结混合室设计,烧结室设计,烧结主抽风系统设计,烧结矿冷却设施设计,烧结矿整粒系统设计,烧结矿贮存设施设计,烧结厂废气余热利用设施设计,烧结厂自动化功能设计,烧结厂检验室设计等。
当冶金工厂设有冶金原料准备场时,烧结厂的设计范围可以从烧结料的配料工序设施开始。
简史铁烧结矿的生产从1905年在德国使用间歇作业的鼓风式烧结锅开始,1911年在美国太平洋沿岸的比尔波罗(Birdboro)的布罗肯(Brooke)公司投产了第一台连续作业的带式烧结机(Dwight—Lloyd型),20世纪30年代在德国建设了一批较大型的带式烧结机,台车宽2.5m,烧结面积达75m2。
70年代以后日本、西欧等工业发达国家烧结工业发展迅速,带式烧结机的烧结面积已发展到单台为300~550m2,台车宽度3~5m,1975年在日本投产了600m。
带式烧结机,台车宽度5m,这是直至1993年为止世界上最大型的带式烧结机。
1926年在中国的鞍山投产了4台1.07×20.27m=21.8m。
带式烧结机,以后拆除。
中华人民共和国建立后,1955年在鞍山钢铁公司第一烧结厂设计投产了两台50m2带式烧结机,此后中国在烧结机型方面有了很大的发展。
1957年在鞍山钢铁公司投产了75m2烧结机,1970年在攀枝花钢铁公司和梅山冶金公司投产了130m2烧结机,1985年在上海宝山钢铁总厂投产了450m2烧结机。
此外,从1986年至1990年在中国陆续设计建成了一批较大型的烧结机,其规格有90m2、105m2、132m2、180m2、193m2和265m2。
300平米烧结机烧结厂设计

摘要烧结矿在高炉炼铁生产中是很重要的一种含铁原料,它的质量好坏和产量的高低直接影响高炉的冶炼效果。
因此,设计一个合理的烧结工艺流程是非常重要的。
在整个设计过程中吸收了很多国内外先进厂家的经验和技术,根据所学的专业知识,设计一台300 m2的烧结机。
其技术指标为年产烧结矿307.48万吨,R=1.8,T Fe≥57%,成品矿粒度50-5 mm,转鼓指数≥70%。
本设计说明书中对所设计的烧结厂工艺进行了简要的介绍,并进行了物料平衡及工艺流程的计算,设备选择计算,确定了含铁原料、熔剂、燃料等需要量,并选择了与之相应的设备配置。
全文分为:绪论;原料、熔剂和燃料;生产规模,工作制度及产品方案;烧结工艺流程及物料平衡;烧结物料平衡与热平衡计算;环境保护与综合利用六个部分。
本设计中,充分考虑了设备自动化控制及环境保护等方案的需要,选择了当前先进的工业设备。
在计算基础上又绘制了图纸说明并编写了设计说明书。
关键词:烧结厂设计;工艺流程;自动化控制;环境保护AbstractIn blast furnace ironmaking, the sinter is an important iron material. The productivity and quality of the sinter have directly effect on blast furnace ironmaking. So it is very important to design a sensible singtering craft.In the design prossess, Some advanced experience and technology of domestic and foreign manufactures has adopted. According to the study of expertise, the requirement is to design a 300 m2of sintering craft. The technical indicators is following: the year quantity of sinter is 307.48 ten thousand ton, R=1.8, TFe≥57%, drum index is no less than 70%, finished mine size is from 50 mm to 5 mm.It is introduced the process of the sintering plant in the design specification. And calculation in material balance, process and equipment selection, determine the ferrous materials, flux, fuel and other requirements, and selection of the corresponding fitness equipment configuration are displayed. The thesis is composed of six sections: introduction; material of iron ores, fluxes, flues; capacity, working rules and production program of the sinter plant; process and material balance calculation; sintering material balance and thermal equilibrium calculation; environment protection and comprehensive utilization.The equipment autocontrol and environmental protection are fully considered in the design. The current advanced craft equipment was used. On the base of calculation,the drawings were drawn and the design specification was complied.Keywords: Sintering plant design; Technical processing; Automated control;Environmental protection;目录前言 (1)1 绪论 (2)1.1 烧结厂设计目的 (2)1.2 烧结厂设计依据及概况 (2)1.3 烧结厂设计要求 (2)1.4 厂区概况及厂址特点 (3)1.4.1 厂区概况 (3)1.4.2 厂址特点 (3)1.5 设计特点 (3)2 原料、熔剂和燃料 (4)2.1 概述 (4)2.2 含铁原料 (4)2.3 熔剂 (4)2.4 燃料 (5)2.5 配比确定 (6)3 生产规模,工作制度及产品方案 (7)3.1 主要技术经济指标确定 (7)3.1.1 作业率确定 (7)3.1.2 利用系数确定 (7)3.1.3 其他经济技术参数 (7)3.2 生产能力确定 (8)3.2.1 日生产能力 (8)3.2.2 小时生产能力 (8)3.3 工作制度 (8)3.4 产品方案 (8)3.5 烧结厂厂房布置及设备布置 (9)3.5.1 烧结厂设备配置原则 (9)3.5.2 工艺建筑配置原则 (9)3.5.3 原料车间配置 (10)3.5.4 烧结室配置 (10)3.5.5 抽风除尘系统的配置 (11)3.5.6 烧结矿处理设备配置 (11)4 烧结工艺流程及物料平衡 (13)4.1 工艺流程确定原则及特点 (13)4.1.1 工艺流程 (13)4.1.2 工艺流程的原则 (13)4.1.3 工艺流程概述 (13)4.2 配料计算 (19)4.2.1 烧结矿烧成率、全铁量、碱度 (19)4.2.2 混合料量 (20)4.2.3 各种原料所需的干料量、湿料量、含水量 (20)4.2.4 外加水量 (21)4.2.5 返矿量 (21)4.2.6 烧结矿年产量 (21)4.3 烧结矿成分计算 (21)4.3.1 各项成分计算 (21)4.3.2 烧结物料收支平衡表 (24)4.4 物料平衡计算 (24)4.4.1 各种物料每小时配料量 (24)4.4.2 熔剂破碎筛分工艺流程及物料平衡 (24)4.4.3 配料工段物料平衡 (26)4.4.4 混合工艺物料平衡 (26)4.4.5 烧结工艺物料平衡 (26)4.4.6 冷却工艺物料平衡 (27)4.4.7 整粒工艺物料平衡 (27)5 烧结物料平衡与热平衡计算 (28)5.1 烧结物料平衡 (28)5.1.1 铺底料量 (28)5.1.2 点火所需燃料、空气量及废气组成 (28)5.1.3 烧结过程总物料收入 (33)5.1.4 烧结过程总物料支出 (33)5.1.5 烧结过程机械损失 (33)5.2 烧结热平衡计算 (34)5.2.1 烧结热量收入 (34)5.2.2 烧结热量支出 (35)5.2.3 烧结热量损失 (36)6 主要设备选型计算 (37)6.1 工艺设备选型依据 (37)6.2 熔剂破碎与筛分设备选型计算 (37)6.2.1 破碎设备 (37)6.2.2 熔剂筛分设备 (38)6.3 燃料破碎设备选型计算 (38)6.3.1 粗碎设备选择 (38)6.3.2 细碎设备选择 (39)6.4 配料设备选型计算 (39)6.4.1 给料设备 (39)6.4.2 配料附属设备 (40)6.5 混合设备选型计算 (41)6.5.1 一次混合设备规格确定 (41)6.5.2 二次混合设备规格确定 (42)6.6 烧结机及附属设备选型计算 (43)6.7 烧结矿热破碎设备选择 (46)6.8冷却设备选型计算 (46)6.9 整粒设备选型计算 (49)6.10 抽风除尘设备选型计算 (51)7环境保护与综合利用 (53)7.1 环境保护的内容 (53)7.1.1 环境除尘 (53)7.1.2 烟气脱硫 (53)7.1.3污水处理 (54)7.2综合利用 (55)参考文献 (56)致谢 (57)附录A:设计图纸明细表 (58)前言烧结厂设计依据在手,根据矿石特性和试验研究成果,设计合理工艺流程,选择合适工艺设备,进行合理工艺配置,确保生产正常进行。
烧结机自动化控制系统设计

2 系 统 设 计
21 P C控 制 系统 设 计 . L
按 配 比关 系 自动 配料 ,保 证碱 度 需求
配料 的 目的是将烧结矿 的品位、含碳量和碱度控制在指 定
的范围内。本工程配料系统由宽带给料机、配料秤;螺旋给料 机、螺旋 给料秤组成。P c对参与烧结 的各种含铁原料、溶剂 L 和燃料根 据高炉冶炼的要求进行 精确 的配料 计算 ,对下料量和 配 比系数进 行设定 ,通过 给料机变 频实时调节各配 料下料量 , 以保证烧结矿 的含铁量 、C O含 量、碱度 、Mg a O、A103及 2 含硫 量等主要成分控制在规定范 围内。 根据烧 结工艺过程对 自动控制系统的要求设计的 自动化系 统为基础 自动化 ,按 “ 电一体化 ”的原则考虑 。上位监控系 三
1 概述
烧 结生产过程是把粉矿加入一定比例 的熔剂 ,燃料经过混 合后,在一定温度下烧 结成高炉需要的原料 。主要生产工 艺包 括燃料破碎系统 、配料室供料 系统 、混料系统、烧结冷却系统 、 成品整粒系统、成 品矿仓储等 。烧结工艺是一个连续性的生产 过程, 节多, 环 控制对象复杂、滞后时间长且受干扰影响大,为 了保汪烧结矿品质稳定,提高产量和降低燃料消耗,必须对生 产过程进行 自动化控制 。
P C与现场变频 器采 用 MB L +网通讯 。从 根本 上解 决了总线传
输控 制 的弱 点 :
和校核流量公式,所 以就保证 了该节流装置的可靠性和可信性。
( 5)温 度 测 量
①
监控层 ;采 用星型 以太 网结 构 ,以太 网具有 传输 速
度 高、低耗、易于安装和 兼容性好等方面 的优势,而且几乎支
所有操 作都通 过烧 结调节画 面进行 。 主抽 风机 安全运 行控制
- 1、下载文档前请自行甄别文档内容的完整性,平台不提供额外的编辑、内容补充、找答案等附加服务。
- 2、"仅部分预览"的文档,不可在线预览部分如存在完整性等问题,可反馈申请退款(可完整预览的文档不适用该条件!)。
- 3、如文档侵犯您的权益,请联系客服反馈,我们会尽快为您处理(人工客服工作时间:9:00-18:30)。
1 概述
烧结生产过程是把粉矿加入一定比例的熔剂,燃料经过混合后,在一定温度下烧结成高炉需要的原料。
主要生产工艺包括燃料破碎系统、配料室供料系统、混料系统、烧结冷却系统、成品整粒系统、成品矿仓储等。
烧结工艺是一个连续性的生产过程,环节多,控制对象复杂、滞后时间长且受干扰影响大,为了保证烧结矿品质稳定,提高产量和降低燃料消耗,必须对生产过程进行自动化控制。
2 系统设计
2.1 PLC控制系统设计
根据烧结工艺过程对自动控制系统的要求设计的自动化系统为基础自动化,按“三电一体化”的原则考虑。
上位监控系统由六台工控机组成,现场控制站由四套QUANTUM PLC组成,分别完成对燃料破碎系统、配料系统、烧结冷却系统、成品系统的监视和控制。
图1 系统网络配置图
烧结机网络化控制系统采用与QUANTUM PLC相配套的Concept 2.6编程软件实现硬件组态配置与程序编制;采用Montor PRO 7.2监控软件完成数据库与监控画面的开发。
通讯网络采用工业以太网,通讯协议为TCP/IP。
系统网络配置图1所示。
2.2 系统功能
(1)设备的联锁控制
根据烧结工艺要求,烧结燃料破碎系统、配料系统、烧结冷却系统、成品系统等整条生产料线的控制方式分为:自动控制、集中手动控制、机旁手动控制。
控制方式的选择设在集中操作室内的主操作台上或通过机旁箱选择。
(2)重点参数调节
?按配比关系自动配料,保证碱度需求
配料的目的是将烧结矿的品位、含碳量和碱度控制在指定的范围内。
本工程配料系统由宽带给料机、配料秤;螺旋给料机、螺旋给料秤组成。
PLC对参与烧结的各种含铁原料、溶剂和燃料根据高炉冶炼的要求进行精确的配料计算,对下料量和配比系数进行设定,通过给料机变频实时调节各配料下料量,以保证烧结矿的含铁量、CaO含量、碱度、MgO、Al2O3及含硫量等主要成分控制在规定范围内。
配料量由上位机统一设定,可进行采集和处理各配料控制回路来的称量信号与开关量状态,实现整个系统的给料、称量检测、料量调节,选择和切换料仓等配料过程的自动控制。
?对烧结重点参数如圆辊给料机、烧结机、环冷机速度联锁控制,控制烧结料层厚度。
?自动控制点火炉炉膛温度
点火器燃烧控制系统是烧结工艺的一个重要环节,点火炉炉温为主调参数,煤气流量和空气流量为辅调参数,以温度调节器的输出作为煤气流量调节器和空气流量调节器的设定值进行PID调节。
?烧结机速通过画面设定机速给定值调节变频器来实现,所有操作都通过烧结调节画面进行。
?主抽风机安全运行控制
主抽风机的轴承温度、定子温度、轴承振动、润滑油压、润滑油温等过程参数均设置报警、连锁信号,保证风机安全稳定运行。
(3)监控画面
系统采用Montor PRO 7.2监控软件完成烧结数据采集与工艺监控。
充分应用Montor PRO 7.2的可视化功能和动态属性,使监控画面形象生动,简单易懂。
图形系统实现整条生产线的集中起停、选择、数据输出等操作,系统设备状态和过程数据的实时监控、历史数据分析,故障显示,报警。
画面划分为:总貌画面(模拟屏画面)、分组画面、状态画面、仪表操作画面、报警画面、趋势画面、打印报表等。
同时还具有生产过程参数报警、记录;重要设备事故按优先级显示报警信息等功能。
(4)网络数据传输
监控站与PLC,PLC与PLC之间通过光纤以太环网通讯,PLC与现场变频器采用MB+网通讯。
从根本上解决了总线传输控制的弱点:
①监控层:采用星型以太网结构,以太网具有传输速度高、低耗、易于安装和兼容性好等方面的优势,而且几乎支持所有流行的网络协议。
②工业以太环网:通常的远程控制网络采用总线结构,这种结构简单易组建,但当某一节点出现故障时可能引起全局瘫痪。
而自愈环网在节点出现故障时自动切换线路,不会影响设备通讯控制,保证控制的实时性与连续性。
2.3 现场仪表控制系统设计
根据自动化技术的现状及发展趋势,生产过程参数的数据采集、控制、显示、报警等功能由PLC完成。
除各别操作外,不设二次仪表盘。
2.3.1 仪表选型
根据烧结生产工艺的要求,现场仪表设备选型以经济、适用、先进、安全为原则,充分考虑生产环境的实际需要。
仪表防护按IP65考虑,煤气区域采用防爆仪表。
压力/差压变送器选用E+H系列智能产品,水流量测量选用横河电机有限公司的电磁流量计。
煤气流量测量选用内藏式节流装置。
调节阀采用蝶阀或单/双座阀,执行机构采用模块化智能电子式产品。
料位测量采用雷达式料位计。
温度测量采用热电偶和热电阻。
配料秤采用徐州拉姆齐产品。
(1)水流量测量
由于水为导电液体,所以最理想的流量测量方法就是采用电磁流量计。
电磁流量计的测量原理是基于法拉第电磁感应定律。
电磁流量计具有许多优点:
?测量管内无突出部件,因此无附加压力损失。
?由于信号在整个充满磁场的空间中形成,它是管道截面上的平均值,因此,从电极平面至传感器上游端平面间所需直管段相对较短,约为5倍的导管内径。
?传感器信号是一个与平均流速成精确的线性关系的电压信号。
测量结果与液体的温度、压力、密度、粘度、导电率(不小于最低导电率)等物理参数无关,所以测量精度高,工作可靠。
(2)压力测量
压力测量主要是对介质压力进行测量。
为了减少电磁信号对压力检测的干扰,采用SIEMENS压力变送器进行压力检测。
输出信号:4~20mA,2线制;HART 通讯;防护等级:IP65;按键操作;高精度;先进的诊断功能。
(3)料位测量
料位采用雷达式料位计进行测量。
能量很低的极短的微波脉冲通过天线系统发射并接收。
微波以光速运行,微波运行时间可以通过电子部件转换成物位信号,一种特殊的时间延伸方法可以确保计短时间内稳定和精确的测量。
(4)煤气流量测量
焦炉煤气流量测量采用内藏式节流装置和差压变送器配合。
内藏式节流装置是在工艺管道内设有一圆锥体,锥体最大横截面处形成喉部。
它的主要特点是可以用来测量各种比较脏的气体流量。
另外,该节流装置的流动阻力小,所以产生的流动损失小,节约能量。
该流量计以流体力学的理论为基础,经过风洞实验,确定和校核流量公式,所以就保证了该节流装置的可靠性和可信性。
(5)温度测量
热电阻电阻值随测量温度的变化而发生变化,所以热电阻的电阻值大小便可反映出测量温度的高低。
热电偶的电极由二根不同导体材质组成。
当测量端与参比端存在温差时,就会产生热电势,PLC便会显示出热电势所对应的温度值。
热电阻、热电偶信号直接连接到具有变送功能的PLC的模拟量输入模块上,所以这种测温变送方法测量精度高、工作稳定可靠。
对烧结风箱的温度检测,由于被测介质对保护管有一定的磨损性,同时现场振动较大,采用带耐振动、耐磨损保护管。
2.3.2 主要检测内容
生产过程参数的检测和控制仪表以满足生产要求为原则,并与工艺整体装备水平和工
厂的自动化技术水平相适应。
为此,主要设置以下检测和控制项目:
?各燃料、熔剂、配料、成品矿料仓料位检测;
?配料室配料量检测;
?燃气、热力管道过程参数检测;
?烧冷系统过程参数检测;
?主抽风机系统过程参数检测;
?燃料除尘、机头除尘、机尾除尘、配料除尘、整粒除尘系统参数检测。
3 结束语
莱钢银山前区265。