哈工大机械制造技术基础大作业
(机械制造行业)哈工大机械设计大作业——螺旋起重器
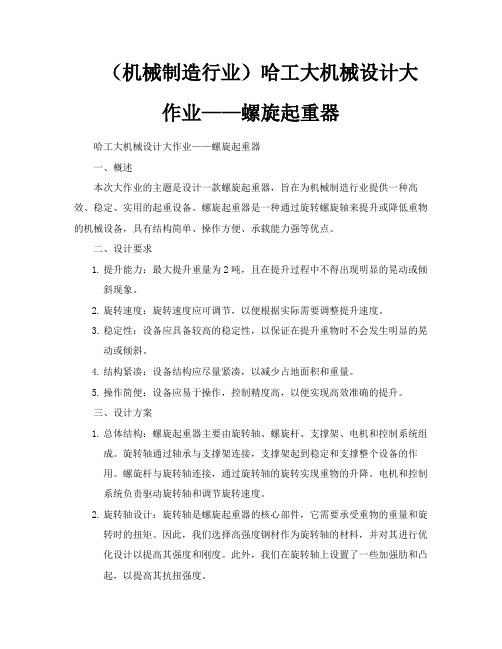
(机械制造行业)哈工大机械设计大作业——螺旋起重器哈工大机械设计大作业——螺旋起重器一、概述本次大作业的主题是设计一款螺旋起重器,旨在为机械制造行业提供一种高效、稳定、实用的起重设备。
螺旋起重器是一种通过旋转螺旋轴来提升或降低重物的机械设备,具有结构简单、操作方便、承载能力强等优点。
二、设计要求1.提升能力:最大提升重量为2吨,且在提升过程中不得出现明显的晃动或倾斜现象。
2.旋转速度:旋转速度应可调节,以便根据实际需要调整提升速度。
3.稳定性:设备应具备较高的稳定性,以保证在提升重物时不会发生明显的晃动或倾斜。
4.结构紧凑:设备结构应尽量紧凑,以减少占地面积和重量。
5.操作简便:设备应易于操作,控制精度高,以便实现高效准确的提升。
三、设计方案1.总体结构:螺旋起重器主要由旋转轴、螺旋杆、支撑架、电机和控制系统组成。
旋转轴通过轴承与支撑架连接,支撑架起到稳定和支撑整个设备的作用。
螺旋杆与旋转轴连接,通过旋转轴的旋转实现重物的升降。
电机和控制系统负责驱动旋转轴和调节旋转速度。
2.旋转轴设计:旋转轴是螺旋起重器的核心部件,它需要承受重物的重量和旋转时的扭矩。
因此,我们选择高强度钢材作为旋转轴的材料,并对其进行优化设计以提高其强度和刚度。
此外,我们在旋转轴上设置了一些加强肋和凸起,以提高其抗扭强度。
3.螺旋杆设计:螺旋杆是直接与重物接触的部件,其设计对设备的稳定性和提升能力有重要影响。
我们选择优质钢材作为螺旋杆的材料,并对其进行抛光和强化处理以提高其耐磨性和抗拉强度。
螺旋杆的长度和直径根据实际需要进行了优化设计,使其既能保证设备的稳定性,又能满足最大提升重量的要求。
4.支撑架设计:支撑架是整个设备的支撑结构,其稳定性直接关系到设备的性能。
我们采用高强度钢材制作支撑架,并对其进行优化设计以提高其抗弯强度和抗扭强度。
此外,我们还设置了多个支撑腿以增加设备的稳定性。
5.电机和控制系统设计:电机和控制系统是整个设备的驱动和控制中心。
哈工大机械制造大作业

哈工大机械制造大作业一、零件分析题目所给的零件是CA6140车床的拨叉。
它位于车床变速机构中,主要起换档,使主轴回转运动按照操作者的要求工作,获得所需的速度和扭矩的作用。
零件上方的孔与操纵机构相连,二下方的Φ55叉口则是用于与所控制齿轮所在的轴接触,拨动下方的齿轮变速。
其生产纲领为批量生产,且为中批生产。
图1-1 CA6140拨叉零件图二、零件的工艺分析零件材料采用HT200,加工性能一般,在铸造毛坯完成后,需进行机械加工,以下是拨叉需要加工的表面以及加工表面之间的位置要求:1、小头孔Φ25:该加工面为内圆面,其尺寸精度要求为;2、叉口半圆孔Φ55:该加工面为内圆面,其尺寸精度要求为;3、拨叉左端面:该加工面为平面,其表面粗糙度要求为,位置精度要求与内圆面圆心距离为;4、叉口半圆孔两端面,表面粗糙度要求为,其垂直度与小头孔中心线的垂直度为;5、拨叉左端槽口,其槽口两侧面内表面为平面,表面粗糙度要求为,其垂直度与小头孔中心线的垂直度为0.08mm。
6、孔圆柱外端铣削平面,加工表面是一个平面,其表面粗糙度要求为。
三、确定毛坯1、确定毛坯种类:零件材料为,查阅机械制造手册,有,考虑零件在机床运行过程中受冲击不大,零件结构又比较简单,故选择铸造毛坯。
图3-1 毛坯模型2、毛坯特点:(1)性能特点:(2)结构特点:一般多设计为均匀壁厚,对于厚大断面件可采用空心结构。
CA6140拨叉厚度较均匀,出现疏松和缩孔的概率低。
(3)铸造工艺参数:铸件尺寸公差:铸件公称尺寸的两个允许极限尺寸之差成为铸件尺寸公差。
成批和大量生产采用金属型时,铸钢和铸件尺寸公差等级为级,选择尺寸公差等级为CT8。
机械加工余量:查阅参考文献[5],铸铁件的加工余量等级为E、F、G,故设计铸件公差为。
最小铸出孔:由于孔深为,孔壁厚度为,此时灰铸铁的最小铸出孔直径大于,故孔不铸出,采用机械加工的方法加工。
3、毛坯尺寸的确定:图3-2如图所示,现对图中1、2、3、4处加工面进行余量计算。
哈工大机械制造技术基本可转位车刀设计

Harbin Institute of Technology课程大作业说明书课程名称:设计题目:院系:班级:设计者:学号:指导教师:设计时间:哈尔滨工业大学目录设计题目 (3)可转位端面车刀设计 (3)一、选择刀片夹固结 (3)二、选择刀片结构材料 (3)三、选择车刀合理角度 (3)四、选择切屑用量 (4)五、刀片型号和尺寸 (4)六、选择硬质合金刀垫型号和尺寸 (5)七、计算刀槽角度 (5)八、计算铣制刀槽时所需的角度 (7)九、选择刀杆材料和尺寸 (8)十、上压式结构 (8)十一、绘制车刀结构简图 (9)参考文献 (10)设计题目设计车小端端面的可转位车刀可转位端面车刀设计一、选择刀片夹固结工件的直径D为160mm,工件长度L=200mm。
因此可以在普通机床CA6140上加工。
表面粗糙度要求3.2μm,为精加工,但由于可转为车刀刃倾角通常取负值,切屑流向已s加工表面从而划伤工件,因此只能达到半精加工,按题设要求,采用上压式的夹紧方式。
二、选择刀片结构材料加工工件材料为HT200,且加工工序为粗车,半精车了两道工序。
由于加工材料为铸铁,因此刀片材料可以采用YG 系列,YG8用于粗加工脆性材料,YG6用于半精加工脆性材料,本题要求达到半精加工,因此材料选择YG6硬质合金。
三、选择车刀合理角度根据《机械制造技术基础》刀具合理几何参数的选择,并考虑可转位车刀几何角度的形成特点,四个角度做如下选择:前角0γ:根据参考文献[1]表3.16,工件材料为HT200,半精车,因此前角可选0γ8=︒, 后角o α:根据参考文献[1]表3.17,工件材料为HT200,半精车,因此后角可选0α4=︒, 主偏角γκ:/ 1.25L d =,工艺系统刚度良好,故采用正方形刀片,主偏角γκ75=︒, 负偏角'γκ:工艺系统刚度良好,为减小已加工表面的粗糙值,取负偏角'γκ5=︒, 刃倾角s λ:为了获得大于0的后角0α及大于0的副刃后角'0α,取刃倾角s λ5=-︒,后角0α的实际数值及副刃后角'0α和副偏角'γκ在计算刀槽角度时经校验确定。
哈工大-机械制造技术基础-大作业-CA6140车床拨叉设计-(完美版-得分4.5)

H a r b i n I n s t i t u t e o f T e c h n o l o g y机械制造技术基础大作业题目:院系:机械制造及其自动化班级:0808103姓名:XXX学号:********XX©哈尔滨工业大学一、零件的分析(一)零件的作用题目所给的零件是CA6140车床的拨叉。
它位于车床变速机构中,主要起换档,使主轴回转运动按照工作者的要求工作,获得所需的速度和扭矩的作用。
零件上方的Ф22孔与操纵机构相连,二下方的Ф55半孔则是用于与所控制齿轮所在的轴接触。
通过上方的力拨动下方的齿轮变速。
两件零件铸为一体,加工时分开。
(二)零件的工艺分析零件的材料为HT200,灰铸铁生产工艺简单,铸造性能优良,但塑性较差、脆性高,不适合磨削,为此以下是拨叉需要加工的表面以及加工表面之间的位置要求:1.小头孔以及与此孔相通的的锥孔、螺纹孔2.大头半圆孔Ф553.小头孔端面、大头半圆孔上下Ф73端面,大头半圆孔两端面与小头孔中心线的垂直度误差为0.07mm,小头孔上端面与其中心线的垂直度误差为0.05mm。
二、工艺规程设计(一)确定生产类型已知此拨叉零件的生产类型为中批量生产,所以初步确定工艺安排为:加工过程划分阶段;工序适当集中;加工设备以通用设备为主,大量采用专用工装。
(二)确定毛坯的制造形式确定毛坯种类:零件材料为HT200。
考虑零件在机床运行过程中所受冲击不大,零件结构又比较简单,生产类型为大批生产,故选择铸件毛坯。
查《机械制造工艺及设备设计指导手册》(后称《指导手册》)选用铸件尺寸公差等级CT9级。
(三)基面的选择(1)粗基准的选择对于零件而言,尽可能选择不加工表面为粗基准。
而对有若干个不加工表面的工件,则应以与加工表面要求相对位置精度较高的不加工表面作粗基准。
根据这个基准选择原则,现选取Ф40的外表面和底面为粗基准加工Ф22孔的上表面。
(2)精基准的选择主要应该考虑基准重合的问题。
“机械制造技术基础”课程大作业1

“机械制造技术基础”课程大作业
本课程安排大作业的目的在于,训练学生根据多样性的题目自主收集查询相关资料、综合运用各方面知识、系统解决较为复杂工程问题的能力,以深化对课程内容的理解和掌握。
题目一:工件的装夹方案设计
设计要求:
从教师所提供的各类工件及其加工要求中自选某个工件的加工,运用夹具设计和有关机构设计原理,查阅相关设计手册,综合分析、计算并设计符合该工序要求的装夹方案。
工作要求:
1、定位方案设计,主要包括定位原理分析、定位元件选择和定位误差计算。
2、夹紧方案选择,主要定性分析适合本序加工的工件夹紧方式,并选择夹紧机构。
3、完成设计说明书一份,装夹方案草图一张。
题目(自选其一):
题1:图示为中批量加工的某盘状零件的各部尺寸和技术要求,若该零件的
孔,试为该工序设计装夹方案。
最后加工工序为钻削8
题2:某零件主要加工要求如图,其加工的铣槽工序为最后工序,试为之设计装夹方案。
参考资料:
[1] 李旦.机械加工工艺手册:第1卷,工艺基础卷 .2版.北京:机械工业出
版社,2007.
[2] 徐鸿本.机床夹具设计手册.沈阳:辽宁科学技术出版社,2004.
[3] 王光斗,等.机床夹具设计手册.上海:上海科学技术出版社,2000.
[4] 赵家齐.机械制造工艺学课程设计指导书.2版.北京:机械工业出版社,
2002.
[5] 李益民.机械制造工艺设计简明手册.北京:机械工业出版社,1994.
[6] 李旦,等.机械制造工业学课程设计机床专用夹具图册.2版.哈尔滨:哈
尔滨工业大学出版社,2005.
50。
机械制造技术基础大作业一

题目要求:工件如下图所示,材料为45 钢正火,长200mm,横截面为φ80,要求设计可转位车刀,完成粗车外圆。
设计步骤:一、选择刀片加固结构考虑到加工在CA6140 普通机床上进行,且属于连续加工,采用偏心式刀片加工结构。
二、选择刀片材料硬质合金牌号,由原始条件给定:被加工材料为45 钢,连续切削,完成粗车工序。
按照硬质合金的选用原则,选取刀片材料为YT15。
三、选择刀片合理角度根据刀具合理几何参数的选择原则,并考虑到可转位车刀几何角度的形成特点,选取如下四个主要角度:①前角γ 0 =15°②后角αo =5°③主偏角κγ =75°④刃倾λs =-6°后角αo 的实际数值以及副后角α ' 和副偏角κ ' 在计算刀槽角度时经校验后确定。
o γ四、选择切削用量根据切削用量的选择原则,查表确定切削用量。
粗车时切削深度a p =3mm,进给量f=0.6mm/r。
五、选择刀片型号和尺寸(1)选择刀片有无中心孔r 由于刀片加固结构已选择为偏心式,因此应选用有中心孔的刀片。
(2)选择刀片形状按选定的主偏角 κγ =75°参照刀片形状的选择原则选用正方形刀片。
(3)选择刀片精度等级 参照刀片精度的选择原则,选用 M 级。
(4)刀片长度的确定根据已确定的背吃刀量 a p =3mm, 主偏角 κγ =75,刃倾角 λs =-6°,将 a p , κγ , λs 代入下 式可得刀刃的实际参加工作长 L se 为L se =∂ ρsin κγ cos λs 3 = sin75cos(-5)=3.12mm所选刀片的刃口长度 L>1.5×L se =4.68mm 即可。
(5)选择刀片厚度 s根据已选择的背吃刀量 a p =3mm ,进给量 f=0.6mm/r 及选择刀片厚度的诺莫图图,求得 刀片厚度 S ≥4.8mm 。
(6)选择刀尖圆弧半径 ε根据已选择的背吃刀量 a p =3mm,进给量 f=0.6mm/r 及选择刀尖圆角半径的诺莫图,求得 连续切削时 r ε =1.2mm 。
哈工大机械制造技术基础大作业
哈工大机械制造技术基础大作业一、零件加工图样在CA6140机床中,拨叉在变速箱中起到控制齿轮组的移动,改变啮合齿轮对,从而改变传动比实现变速功能。
零件材料采用200HT 灰铸铁,生产工艺简单、可铸性高,但材料脆性大不易磨削。
需要加工的部分及加工要求如下:1、0.0210Φ22+孔,还有与其相连的8M 螺纹孔和Φ8锥销孔;2、小孔的上端面,大孔的上下两端面;3、大头的半圆孔0.40Φ55+;4、Φ40上端面,表面粗5、糙度为 3.2Ra ,该面和Φ20孔中心线垂直度误差为0.05mm ;5、0.50Φ73+半圆形上下端面与Φ22孔中心线垂直度误差为0.07mm 。
二、零件加工工艺设计(一)确定毛坯的制造形式零件材料为HT200。
考虑到零件在机床运行时过程中所受冲击不大,零件结构又比较简单,生产类型为大批生产,故选择铸件毛坯。
选用铸件尺寸公差等级CT9级。
(二)工艺初步安排零件的加工批量以大批量为主,用通用机床加工,工序适当集中,减少工件装夹次数以缩短生产周期、保证其位置精度。
(三)选择基准基准的选择是工艺规程设计中的重要工作之一。
基准选择得正确合理,可以使加工质量得到保证,生产效率得以提高。
(1)粗基准的选择:以零件的底面为主要的定位粗基准,以两个小头孔外圆表面为辅助粗基准。
这样就能限制工件的五个自由度,再加上垂直的一个机械加紧,就可达到完全定位。
(2)精基准的选择:考虑到要保证零件的加工精度和装夹准确方便,依据“基准重合”原则和“基准统一”原则,以粗加工后的底面为主要定位基准,以两个小孔头内圆柱表面为辅助的定位精基准。
(四)制定工艺路线1.工艺方案分析此零件加工工艺大致可分为两个:方案一是先加工完与Φ22mm 的孔有垂直度要求的面再加工孔。
而方案二恰恰相反,先加工Φ22mm的孔,再以孔的中心线来定位加工完与之有垂直度要求的三个面。
方案一装夹次数较少,但在加工Φ22mm的时候最多只能保证一个面与定位面之间的垂直度要求。
哈工大机械制造基础大作业二
题目及要求(1) 机械加工工艺路线(工序安排)① 工艺方案分析 加工重点、难点② 工序编排 加工顺序、内容③ 加工设备和工艺装备(2) 关键问题分析① 加工工艺问题② 装夹问题③ 生产率问题④ 新技术(3) 解决关键问题的工艺措施(参阅资料)一、零 件 的 分 析零件的工艺分析:零件的材料为HT200,灰铸铁生产工艺简单,铸造性能优良,但塑性较差、脆性高,不适合磨削,为此以下是拨叉需要加工的表面以及加工表面之间的位置要求需要加工的表面:1。
小孔的上端面、大孔的上下端面;2。
小头孔0.021022+-Φmm 以及与此孔相通的8Φmm 的锥孔、8M 螺纹孔;mm;3。
大头半圆孔55位置要求:小头孔上端面与小头孔中心线的垂直度误差为0.05mm、大孔的上下端面与小头孔中心线的垂直度误差为0。
07mm.由上面分析可知,可以粗加工拨叉底面,然后以此作为粗基准采用专用夹具进行加工,并且保证位置精度要求。
再根据各加工方法的经济精度及机床所能达到的位置精度,并且此拨叉零件没有复杂的加工曲面,所以根据上述技术要求采用常规的加工工艺均可保证.二、零件加工工艺设计(一)确定毛坯的制造形式零件材料为HT200.考虑到零件在机床运行过程中所受冲击不大,零件结构又比较简单,生产类型为大批生产,故选择铸件毛坯。
选用铸件尺寸公差等级CT9级,该拨叉生产类型为大批生产,所以初步确定工艺安排为:工序适当分散;广泛采用专用设备,大量采用专用工装。
(二)基面的选择基面的选择是工艺规程设计中的重要工作之一。
基面选择得正确与合理,可以使加工质量得到保证,生产效率得以提高。
(1) 粗基准的选择:以零件的底面为主要的定位粗基准,以两个小头孔外圆表面为辅助粗基准。
这样就可以达到限制五个自由度,再加上垂直的一个机械加紧,就可以达到完全定位。
(2)精基准的选择:考虑要保证零件的加工精度和装夹准确方便,依据“基准重合"原则和“基准统一”原则,以粗加工后的底面为主要的定位精基准,以两个小头孔内圆柱表面为辅助的定位精基准。
哈工大机械工程测试基础大作业信号的分析与系统特性
"测试技术"课程大作业1作业题目:信号的分析与系统特性学生姓名:评阅教师作业成绩2015年春季学期信号的分析与系统特性一、设计题目写出下列信号中的一种信号的数学表达通式,求取其信号的幅频谱图(单边谱和双边谱)和相频谱图,若将此信号输入给特性为传递函数为)(s H 的系统,试讨论信号参数的取值,使得输出信号的失真小。
名称)(s H τ、n ω、ζ波形图三角波11)(+=s s H τ τ=0.02522240)(nn ns s s H ωζωω++= n ω=900,ζ=0.7二、求解信号的幅频谱和相频谱1、写出波形图所示信号的数学表达通式在一个周期中题中三角波可表示为如下所示:4T A ,4400T t T <<-=)(t x042T AA -,44400T t T <<其傅里叶级数展开式为...)5sin 2513sin 91(sin 8)(0002++-=t t t At x ωωωπ 2、求取其信号的幅频谱图和相频谱图 (1)单边谱幅频谱函数为228πn Aa n =,n=1,3,5… 2/π,n=1,5,9…相频谱函数为=n ϕ2/π-,n=3,7,11…则幅频图和相频图如下所示:)(t x t T 00 T 0/2A图1.单边幅频图图2.单边相频图(2)双边谱傅里叶级数的复指数展开为:]31[4)(000032322222⋯++-+=----t j j tj j tj jtj je e e e ee eeAt x ωπωπωπωππ则2222142121nA A b a C n n n n ⋅==+=π nnn a b arctan-=ϕ 则幅频谱、相频谱图如下图所示:图3.双边幅频图图4.双边相频图三、分析其频率成分分布由信号的傅里叶级数形式及其频谱图可以看出,三角波信号的频谱是离散的,其幅频谱只包含常值分量、基波和奇次谐波的频率分量,谐波的幅值以1/n 2的规律收敛,在其相频谱中基波和其各次谐波的相位为2π或-2π。
哈工大机械工程测试技术基础大作业(企业管理)
HarbinInstitute of Technology课程大作业说明书课程名称:院系:班级:设计者:学号:指导教师:设计时间:哈尔滨工业大学目录信号的分析与系统特性........................ (3)一、设计题目……………………………………………………………………3二、求解信号的幅频谱和相频谱............ (3)三、频率成分分布情况 (5)四、H(s)伯德图 (6)五、将此信号输入给特征为传递函数为H(s)的系统 (7)传感器综合运用 (10)一、题目要求 (10)二、方案设计……………………………………………………………………10三、传感器的选择………………………………………………………………11四、总体测量方案 (12)五、参考文献 (12)信号的分析与系统特性一、设计题目写出下列方波信号的数学表达通式,求取其信号的幅频谱图(单边谱和双边谱)和相频谱图,若将此信号输入给特性为传递函数为)(s H 的系统,试讨论信号参数的取值,使得输出信号的失真小。
名称)(s H、、波形图 方波11)(+=s s H τ=0。
1,0。
5,0.70722240)(nn n s s s H ωζωω++= =0。
5,0.707 =10,500作业要求(1)要求学生利用第1章所学知识,求解信号的幅频谱和相频谱,并画图表示出来。
(2)分析其频率成分分布情况。
教师可以设定信号周期及幅值,每个学生的取值不同,避免重复.(3)利用第2章所学内容,画出表中所给出的系统)(s H 的伯德图,教师设定时间常数或阻尼比和固有频率的取值.(4)对比2、3图分析将2所分析的信号作为输入)(t x ,输入给3所分析的系统)(s H ,求解其输出)(t y 的表达式,并且讨论信号的失真情况(幅值失真与相位失真)若想减小失真,应如何调整系统)(s H 的参数。
二、求解信号的幅频谱和相频谱002200-200211=(t)=+-=0TT T T T a w dt Adt Adt T T ⎛⎫ ⎪⎝⎭⎰⎰⎰tTT 0/A00220000-200222()cos()cos()-cos()0TT T T T n a w t nw t dt A nw t dt A nw t dt T T ⎛⎫==+= ⎪⎝⎭⎰⎰⎰00220000-20020000000022()sin()sin()-sin()4 2 cos()-cos()200 2TTT T T n b w t nw t dt A nw t dt A nw t dt T T A T T n A A nw t nw t nT T nw nw n π⎛⎫==+ ⎪⎝⎭⎛⎫⎧⎪ ⎪==⎨ ⎪ ⎪⎪⎩⎝⎭⎰⎰⎰为奇数为偶数式中000411(t)=(sin(w t)+sin(3w t)+sin(5w t)+)35Aw π…转换为复指数展开式的傅里叶级数:()()0000000000002-j 000-2000000011=(t)e=e +-e 1121 =(e -e ) =e -e | =e -e = 2T jnw tnw tjnw t n T jnw t jnw t jnw t jnw t jnw jnw c w dt A dt A dt T T A A AA dt j T T jnw T nw j n ττττττπ-----⎛⎫ ⎪⎝⎭⎰⎰⎰⎰当0,2,4,...n =±±时,0n C =; 当1,3,5,...n =±±±时,2n A C j n π=-则幅频函数为:2,1,3,5,...n AC jn n π=-=±±±42||,1,3,5,...n n AA C n n π===相频函数为:arctanarctan(),1,3,5, (2)nI n nR C n C πϕ==-∞=-=arctanarctan(),1,3,5, (2)nI n nR C n C πϕ==+∞==---双边幅频图:单边幅频图:相频图:三、频率成分分布情况由信号的傅里叶级数形式及其频谱图可以看出,矩形波是由一系列正弦波叠加而成,正弦波的频率由到3,5……,其幅值由4Aπ到43Aπ,45Aπ,……依次减小,各频率成分的相位都为0。
- 1、下载文档前请自行甄别文档内容的完整性,平台不提供额外的编辑、内容补充、找答案等附加服务。
- 2、"仅部分预览"的文档,不可在线预览部分如存在完整性等问题,可反馈申请退款(可完整预览的文档不适用该条件!)。
- 3、如文档侵犯您的权益,请联系客服反馈,我们会尽快为您处理(人工客服工作时间:9:00-18:30)。
一、零件加工图样
在CA6140机床中,拨叉在变速箱中起到控制齿轮组的移动,改变啮合齿轮对,从而改变传动比实现变速功能。
零件材料采用200HT 灰铸铁,生产工艺简单、可铸性高,但材料脆性大不易磨削。
需要加工的部分及加工要求如下:
1、0.0210Φ22+孔,还有与其相连的8M 螺纹孔与Φ8锥销孔;
2、小孔的上端面,大孔的上下两端面;
3、 大头的半圆孔0.40Φ55+;
4、 Φ40上端面,表面粗
5、 糙度为 3.2Ra ,该面与Φ20孔中心线垂直度误差为0.05mm ;
5、0.50Φ73+半圆形上下端面与Φ22孔中心线垂直度误差为0.07mm 。
二、零件加工工艺设计
(一)确定毛坯的制造形式
零件材料为HT200。
考虑到零件在机床运行时过程中所受冲击不大,零件结构又比较简单,生产类型为大批生产,故选择铸件毛坯。
选用铸件尺寸公差等级CT9级。
(二)工艺初步安排
零件的加工批量以大批量为主,用通用机床加工,工序适当集中,减少工件装夹次数以缩短生产周期、保证其位置精度。
(三)选择基准
基准的选择就是工艺规程设计中的重要工作之一。
基准选择得正确合理,可以使加工质量得到保证,生产效率得以提高。
(1)粗基准的选择:以零件的底面为主要的定位粗基准,以两个小头孔外圆表面为辅助粗基准。
这样就能限制工件的五个自由度,再加上垂直的一个机械加紧,就可达到完全定位。
(2)精基准的选择:考虑到要保证零件的加工精度与装夹准确方便,依据“基准重合”原则与“基准统一”原则,以粗加工后的底面为主要定位基准,以两个小孔头内圆柱表面为辅助的定位精基准。
(四)制定工艺路线
1、工艺方案分析
此零件加工工艺大致可分为两个:方案一就是先加工完与Φ22mm的孔有垂直度要求的面再加工孔。
而方案二恰恰相反,先加工Φ22mm的孔,再以孔的中心线来定位加工完与之有垂直度要求的三个面。
方案一装夹次数较少,但在加工Φ22mm的时候最多只能保证一个面与定位面之间的垂直度要求。
其她的两个面很难保证。
因此,此方案有很大弊端。
方案二在加工三个面时都就是用Φ22mm孔的中心线来定位,这样很容易就可以保证其与三个面之间的位置度要求。
2、总体工艺路线:
详细工艺安排:
工序1:以Φ22孔的外表面为基准,扩、精铰Φ22孔;
工序2:以Φ22孔的底面为基准,钻、扩、精铰Φ8锥销孔,攻Φ8螺纹;
工序3:以Φ22孔为基准,粗铣Φ40上端面;
工序4:以Φ22孔为基准,粗铣Φ73上下端面;
工序5:以Φ22孔为基准,镗、精镗Φ55孔;
工序6:铣断Φ73半圆;
工序7:半精铣Φ40上端面;
工序8:半精铣Φ73上、下端面;
工序9:检查,去毛刺。
加工工艺卡片
拨叉加工工艺过程
序号工序内容定位基准机床设备
1 扩、精铰Φ22孔Φ22孔的外表面立式钻床
2 钻Φ8锥销孔Φ22孔的底面立式钻床
3 精铰Φ8锥销孔Φ22孔的底面立式钻床
二、 零件加工工序设计
(一) 工艺装备的选择
1. 夹具选择简要说明:
在大批量生产中,应根据工序加工要求设计制造专用夹具。
在设计夹具时应该注意提高劳动生产率避免干涉,应使夹具结构简单、便于操作、降低成本,提高夹具性价比。
在此为铣床夹具选择了结构简单、制造容易、夹紧行程大、传力系数大、自锁性能好的螺旋夹具装置。
2. 刀具选择简要说明
刀具选择主要取决于工序所采用的加工方法、加工表面的尺寸、工件材料、所要求的加工精度与表面粗糙度、生产效率及经济性等。
在选择时尽可能采用标准刀具,在此选择6YG 硬质合金刀具。
(二) 加工余量及工序尺寸确定
1. 铣Φ40上端面加工余量及公差
圆柱Φ40上端面为自由尺寸公差,表面粗糙度值要求为 3.2Ra =,要求粗铣、半精铣。
办精铣的加工余量(单边)0.8Z mm =
粗铣加工余量(单边) 1.2Z mm =
2. 加工Φ22孔
先铸造出Φ20,再扩、半精铰、精铰。
内孔精度要求7IT ,确定工序尺寸及余量为: 扩孔:Φ21.8 2 1.8Z mm =
半精铰:Φ21.94 20.14Z mm =
精铰: Φ200.0210+
3.铣Φ55上端面
圆柱Φ55两端面精度要求11IT ,表面粗糙度要求为 3.2Ra =,要求粗铣,半精铣。
半精铣的加工余量(单边)0.8Z mm =
粗铣加工余量(单边) 4.2Z mm =
4、铣Φ55下端面
圆柱Φ55两端面精度要求11IT ,表面粗糙度要求为 3.2Ra =,要求粗铣,半精铣。
半精铣的加工余量(单边)0.8Z mm =
粗铣加工余量(单边) 4.2Z mm =
5、加工Φ55孔
毛坯为铸孔,内孔精度要求13IT 表面粗糙度为 3.2Ra =,要求粗镗、半精镗,确定工序尺寸及余量为:
粗镗Φ53.5, 2 3.5Z mm =
精镗Φ550.4+, 2 1.5Z mm =
6、钻锥孔Φ7.8及6M 底孔;半精铰、精铰Φ8锥孔,保证 1.6Ra =的表面粗糙度;攻8M 螺纹
半精铰加工余量20.14Z mm =
精铰加工余量20.06Z mm =
三、 参考文献
[1]李旦等、机械制造技术基础、哈尔滨:哈尔滨工业大学出版社,2011、1。