高炉炼铁原理
烧结及高炉炼铁基本原理及工艺

降低了煤气还原能力,影响还原速度.
CaCO3在低温区分解放出CO2进入煤气,降低了CO的 浓度,冲淡了还原气氛
在高温区分解出的CO2与焦炭发生反应, CO2+C焦=2CO 是吸热反应,而且直接消耗焦 炭,使焦比升高.
13
二、高炉还原过程
高炉冶炼用CO,H2和固体碳作还原剂. 氧化物的还原顺序: 高炉冶炼条件下,各种氧化物由易到难的还原 顺序. CuO→PbO→FeO→MnO→SiO2 →Al2O3→MgO→CaO
三元碱度:R3=(CaO+MgO)/SiO2,一般为1.3左 右
-Q -Q -Q -Q -Q
2.碳水反应的影响:
当温度大于1000℃时:
H2O汽 + C = H2 + CO
-Q
用H2还原铁氧化物在高温区时:
FeO+H2 = Fe+H2O
+ H2O+C = H2+CO
FeO+C = Fe+CO
在低温区时,用H2还原铁氧化物的产物与CO作用
FeO+H2 = Fe+H2O + H2O+CO = H2+CO2
0 400 500 600 700 800 900 1000 1200 0C
度随温度升高而降低,即温度升高,
CO的利用率提高,是吸热反应,
2.温度对反应的影响: 曲线3是FeO+CO=Fe+CO2的平衡 气相成分线,向上倾斜,与曲线2 正好相反,是放热反应,升温对反
应不利.
曲线4是Fe3O4+4CO=Fe+4CO2的 平衡气相成分线,向上倾斜,它在
%CO
Fe
利用高炉炼铁的原理是
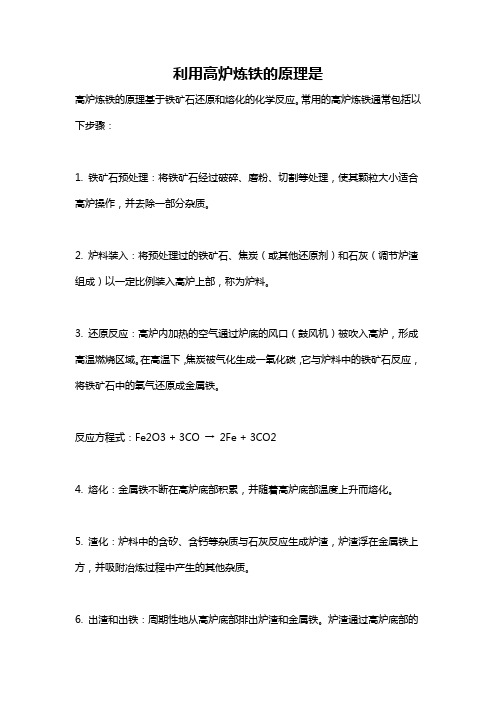
利用高炉炼铁的原理是
高炉炼铁的原理基于铁矿石还原和熔化的化学反应。
常用的高炉炼铁通常包括以下步骤:
1. 铁矿石预处理:将铁矿石经过破碎、磨粉、切割等处理,使其颗粒大小适合高炉操作,并去除一部分杂质。
2. 炉料装入:将预处理过的铁矿石、焦炭(或其他还原剂)和石灰(调节炉渣组成)以一定比例装入高炉上部,称为炉料。
3. 还原反应:高炉内加热的空气通过炉底的风口(鼓风机)被吹入高炉,形成高温燃烧区域。
在高温下,焦炭被气化生成一氧化碳,它与炉料中的铁矿石反应,将铁矿石中的氧气还原成金属铁。
反应方程式:Fe2O3 + 3CO →2Fe + 3CO2
4. 熔化:金属铁不断在高炉底部积累,并随着高炉底部温度上升而熔化。
5. 渣化:炉料中的含矽、含钙等杂质与石灰反应生成炉渣,炉渣浮在金属铁上方,并吸附冶炼过程中产生的其他杂质。
6. 出渣和出铁:周期性地从高炉底部排出炉渣和金属铁。
炉渣通过高炉底部的
渣口排出,金属铁通过铁口流出。
通过上述步骤,高炉炼铁能够将铁矿石中的金属铁提取出来,并形成可用的铁水。
高炉炼铁
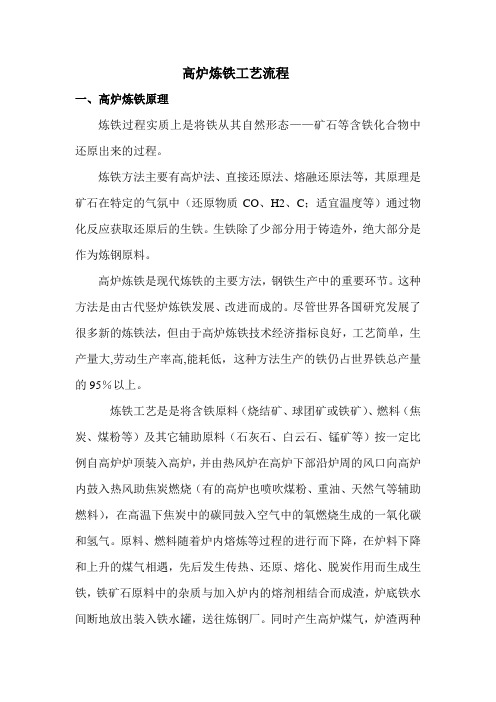
高炉炼铁工艺流程一、高炉炼铁原理炼铁过程实质上是将铁从其自然形态——矿石等含铁化合物中还原出来的过程。
炼铁方法主要有高炉法、直接还原法、熔融还原法等,其原理是矿石在特定的气氛中(还原物质CO、H2、C;适宜温度等)通过物化反应获取还原后的生铁。
生铁除了少部分用于铸造外,绝大部分是作为炼钢原料。
高炉炼铁是现代炼铁的主要方法,钢铁生产中的重要环节。
这种方法是由古代竖炉炼铁发展、改进而成的。
尽管世界各国研究发展了很多新的炼铁法,但由于高炉炼铁技术经济指标良好,工艺简单,生产量大,劳动生产率高,能耗低,这种方法生产的铁仍占世界铁总产量的95%以上。
炼铁工艺是是将含铁原料(烧结矿、球团矿或铁矿)、燃料(焦炭、煤粉等)及其它辅助原料(石灰石、白云石、锰矿等)按一定比例自高炉炉顶装入高炉,并由热风炉在高炉下部沿炉周的风口向高炉内鼓入热风助焦炭燃烧(有的高炉也喷吹煤粉、重油、天然气等辅助燃料),在高温下焦炭中的碳同鼓入空气中的氧燃烧生成的一氧化碳和氢气。
原料、燃料随着炉内熔炼等过程的进行而下降,在炉料下降和上升的煤气相遇,先后发生传热、还原、熔化、脱炭作用而生成生铁,铁矿石原料中的杂质与加入炉内的熔剂相结合而成渣,炉底铁水间断地放出装入铁水罐,送往炼钢厂。
同时产生高炉煤气,炉渣两种副产品,高炉渣铁主要矿石中不还原的杂质和石灰石等熔剂结合生成,自渣口排出后,经水淬处理后全部作为水泥生产原料;产生的煤气从炉顶导出,经除尘后,作为热风炉、加热炉、焦炉、锅炉等的燃料。
二、高炉冶炼主要工艺设备简介高护炼铁设备组成有:①高炉本体;②供料设备;③送风设备;④喷吹设备;⑤煤气处理设备;⑥渣铁处理设备。
通常,辅助系统的建设投资是高炉本体的4~5倍。
生产中,各个系统互相配合、互相制约,形成一个连续的、大规模的高温生产过程。
高炉开炉之后,整个系统必须日以继夜地连续生产,除了计划检修和特殊事故暂时休风外,一般要到一代寿命终了时才停炉。
钢铁的冶炼原理及生产工艺流程

炼铁方法主要有高炉法、直接还原法、熔融还原法等,其原理是矿石在特定的气氛中(还原物质CO、H2、C;适宜温度等)通过物化反应获取还原后的生铁。
生铁除了少部分用于铸造外,绝大部分是作为炼钢原料。
1、高炉炼铁的冶炼原理(应用最多的)
1)炼铁的原理:用还原剂将铁矿石中的铁氧化物还原成金属铁。
铁氧化物(Fe2O3、Fe3O4、FeO)+还原剂(C、CO、H2)铁(Fe)
2) 炼铁的方法
(1)直接还原法(非高炉炼铁法)
(2)高炉炼铁法(主要方法)
3)高炉炼铁的原料及其作用
(1)铁矿石:(烧结矿、球团矿)提供铁元素。
(2)焦碳:提供热量;提供还原剂;作料柱的骨架。
(3)熔剂:(石灰石、白云石、萤石)
使炉渣熔化为液体;去除有害元素硫(S)。
(4)空气:为焦碳燃烧提供氧。
2、工艺流程
生铁的冶炼虽原理相同,但由于方法不同、冶炼设备不同,所以工艺流程也不同。
下面分别简单予以介绍。
高炉生产是连续进行的
从炉顶(一般炉顶是由料种与料斗组成,现代化高炉是钟阀炉顶和无料钟炉顶)不断地装入铁矿石、焦炭、熔剂,从高炉下部的风口吹进热风(1000~1300摄氏度),喷入油、煤或天然气等燃料。
装入高炉中的铁矿石,主要是铁和氧的化合物。
在高温下,焦炭中和喷吹物中的碳及碳燃烧生成的一氧化碳将铁矿石中的氧夺取出来,得到铁,。
高炉炼铁的原理

高炉炼铁的原理
简介
高炉炼铁是一种重要的冶炼工艺,通过高炉将铁矿石和焦炭等原料还原为铁。
高炉通常是一个巨大的金属容器,内部通过高温反应实现铁的冶炼。
原料
铁矿石是高炉炼铁的主要原料之一,常见的铁矿石包括赤铁矿、磷铁矿等。
此外,焦炭、石灰石等原料也是高炉炼铁中必不可少的。
原理
1.燃烧过程: 高炉中焦炭等燃料在燃烧时产生高温,燃气通过矿石料床
加热矿石,并在还原区域发生还原反应。
2.还原反应: 在高炉内,煤气经过还原区域与铁矿石中的氧化铁发生反
应,将氧还原为气态二氧化碳,释放出铁。
3.融化过程: 上述反应产生的铁在高温下融化,并通过热对流从上向下
移动到高炉的熔融区域。
4.炉渣形成: 高炉中产生的碳酸化合物和石灰石在高温下融化形成炉渣,
在铁水表面形成保护膜,防止铁的再氧化。
冶炼过程
高炉炼铁过程通常会经历炉料下料、补料、冶炼、出铁等阶段。
整个过程需要
严格调控高炉的温度、气氛、矿石的质量等参数,以确保炼铁效果。
结论
高炉炼铁是一项复杂的冶炼过程,通过高炉的高温还原反应,将铁矿石转化为铁。
高炉炼铁工艺的改进和提高效率对于保障铁铸造业的发展至关重要,进一步
提高炼铁效率和降低成本是未来的发展方向。
高炉炼铁

3.用固体C还原
高炉冶炼特点
1.高炉冶炼是在炉料与煤气流的逆向运动 过程中完成各种复杂的化学反应和物理变 化,反应气氛是还原性气氛; 2.高炉是一个密闭容器,除了装料、出铁、 出渣以及煤气以外,操作人员都无法直接 观察到反应过程的状况,只能凭借仪器间 接观察; 3.高炉生产过程是连续的,大规模的高温 生产过程,机械化和自动化水平较高。
燃料燃烧反应 铁矿石还原反应(铁氧化物) 非铁元素还原(Si,Mn,等) 造渣过程 生铁生成
A、燃烧反应
放热 燃烧 产生高温还原气体CO 在高炉下部形成空间, 保证炉料持续下降 直接还原(参与化学还原) 溶入生铁(铁水中含有一定量C)
焦炭 (主要燃料)
燃料的燃烧是高炉的热能和化学能的发源 地,决定了炉内煤气流,温度和热量的初始 分布,对高炉生产起着至关重要的作用!
1.钢筋混凝土 2.耐火砖 3.冷却壁 4.水冷管
5.炉壳
冷却设备
支梁式水箱 A—铸管式 B—隔板式
扁水箱 (铸钢)
炉腹、炉腰、炉身下部:冷却壁
炉缸和炉底周围:光板式冷却壁(紫铜冷却壁)
风口:冷却套
1.风口 2.风口二套 3.风口大套 4.直吹管 5.弯管 6.固 定弯管 7.围管 8.短管 9.带有窥视孔的弯管 10.拉杆 11.炉壳
B、还原反应
铁氧化物的还原
1.铁氧化物的还原条件 还原反应通式: MeO+B=Me+BO B:还原剂 Me:某种金属 要使反应能够进行,则: Me O B
还原剂B与O的化学亲和力 > Me与O的化学亲和力 在高炉冶炼过程中,满足条件的还原剂是CO和C,还 有少量的H2也参与还原
二.铁氧化物的还原顺序
焦炭在风口发生燃烧反应: C+O2 =CO2 +33356kJ/kg + C+CO2 =2CO -13794kJ/kg 2C+O2 =2CO +9781kJ/kg
炼铁原理解析高炉冶炼过程中的矿石还原与炉渣形成机制
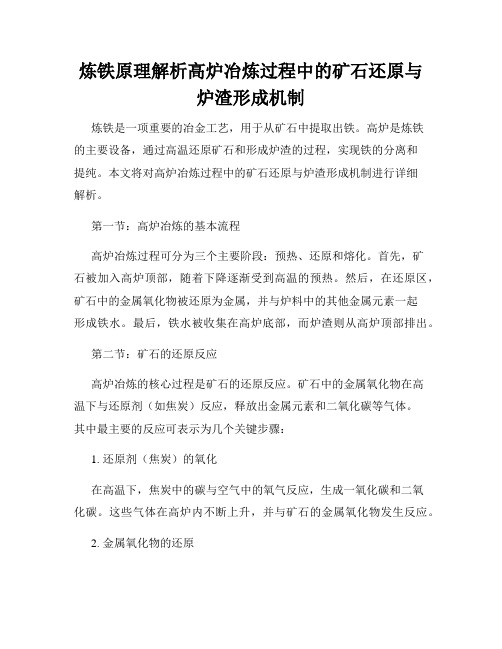
炼铁原理解析高炉冶炼过程中的矿石还原与炉渣形成机制炼铁是一项重要的冶金工艺,用于从矿石中提取出铁。
高炉是炼铁的主要设备,通过高温还原矿石和形成炉渣的过程,实现铁的分离和提纯。
本文将对高炉冶炼过程中的矿石还原与炉渣形成机制进行详细解析。
第一节:高炉冶炼的基本流程高炉冶炼过程可分为三个主要阶段:预热、还原和熔化。
首先,矿石被加入高炉顶部,随着下降逐渐受到高温的预热。
然后,在还原区,矿石中的金属氧化物被还原为金属,并与炉料中的其他金属元素一起形成铁水。
最后,铁水被收集在高炉底部,而炉渣则从高炉顶部排出。
第二节:矿石的还原反应高炉冶炼的核心过程是矿石的还原反应。
矿石中的金属氧化物在高温下与还原剂(如焦炭)反应,释放出金属元素和二氧化碳等气体。
其中最主要的反应可表示为几个关键步骤:1. 还原剂(焦炭)的氧化在高温下,焦炭中的碳与空气中的氧气反应,生成一氧化碳和二氧化碳。
这些气体在高炉内不断上升,并与矿石的金属氧化物发生反应。
2. 金属氧化物的还原金属氧化物与一氧化碳发生反应,还原成金属元素和二氧化碳。
这个还原反应是炉内主要的化学反应之一。
不同金属氧化物的还原程度和速率有所不同,这取决于各自的化学性质及温度条件。
3. 金属元素的迁移还原后的金属元素在高温下与其他金属元素结合,形成熔化的铁水。
这些金属元素在高炉内上升,直至达到悬浮于铁水上方的炉渣层。
第三节:炉渣的形成机制炉渣是高炉冶炼过程中的重要产物,它具有多种功能,如吸附杂质、稀释硫和磷等。
在高炉冶炼过程中,炉渣的形成主要经历以下几个步骤:1. 矿石中杂质的熔化矿石中的杂质(如硅、铝、钙等)在高温下被熔化,并分散于铁水和炉渣中。
这种熔化是高炉冶炼过程中的一个重要步骤,它有助于将杂质从铁水中分离出来。
2. 杂质的反应和吸附杂质在铁水和炉渣中发生各种化学反应,如与炉渣中的主要成分形成化合物或吸附于炉渣颗粒表面。
通过这些反应和吸附作用,炉渣能够有效地吸附和脱除铁水中的杂质。
高炉炼铁的原理
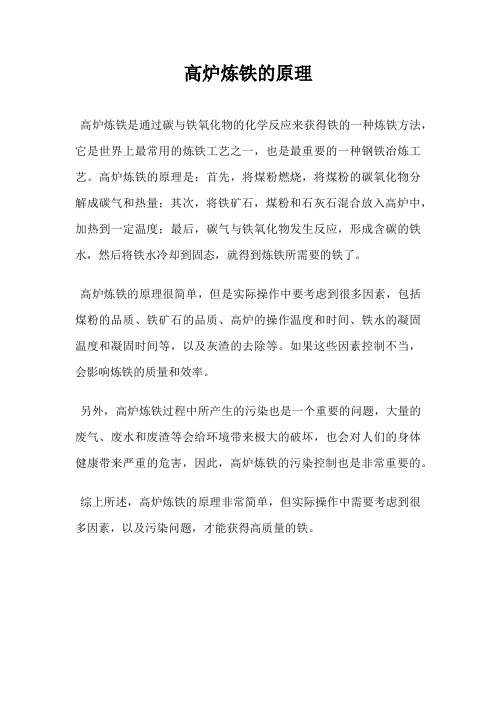
高炉炼铁的原理
高炉炼铁是通过碳与铁氧化物的化学反应来获得铁的一种炼铁方法,它是世界上最常用的炼铁工艺之一,也是最重要的一种钢铁冶炼工艺。
高炉炼铁的原理是:首先,将煤粉燃烧,将煤粉的碳氧化物分解成碳气和热量;其次,将铁矿石,煤粉和石灰石混合放入高炉中,加热到一定温度;最后,碳气与铁氧化物发生反应,形成含碳的铁水,然后将铁水冷却到固态,就得到炼铁所需要的铁了。
高炉炼铁的原理很简单,但是实际操作中要考虑到很多因素,包括煤粉的品质、铁矿石的品质、高炉的操作温度和时间、铁水的凝固温度和凝固时间等,以及灰渣的去除等。
如果这些因素控制不当,会影响炼铁的质量和效率。
另外,高炉炼铁过程中所产生的污染也是一个重要的问题,大量的废气、废水和废渣等会给环境带来极大的破坏,也会对人们的身体健康带来严重的危害,因此,高炉炼铁的污染控制也是非常重要的。
综上所述,高炉炼铁的原理非常简单,但实际操作中需要考虑到很多因素,以及污染问题,才能获得高质量的铁。
- 1、下载文档前请自行甄别文档内容的完整性,平台不提供额外的编辑、内容补充、找答案等附加服务。
- 2、"仅部分预览"的文档,不可在线预览部分如存在完整性等问题,可反馈申请退款(可完整预览的文档不适用该条件!)。
- 3、如文档侵犯您的权益,请联系客服反馈,我们会尽快为您处理(人工客服工作时间:9:00-18:30)。
高炉炼铁原理
高炉气体力学
P炉料的下降力=炉料自身重力 —炉料间及炉料与炉墙摩擦力 —煤气浮力 >0
220kpa
如P=0,意味着炉料停止下降
料柱
炉
1
料
下
3 降煤
气
2
上
8升
4
69 57
鼓风、喷吹燃料
10
液态渣铁
出铁、出渣
高炉中的反应
高炉炼铁原理
预热区 间 接 还 原
热储备区 区
Fe2O3+CO→Fe3O4+CO2 Fe3O4+1.25CO →FeO+0.25CO+CO2 游离水蒸发、化合水分解 碳的沉积 2CO →CO2+C
FeO+3.3CO ↔ Fe+2.3CO+CO2
炼铁
2012年9月
高炉炼铁原理
Байду номын сангаас
高炉炉内炉料状况及反应
高炉炼铁原理
•高炉炼铁过程实质是一个铁氧化物的还原过程
这个过程极为复杂,存在一系列的化学反应。这些反应发生在炉料下 降和煤气上升的逆流运动中:还原顺序为Fe2O3→Fe3O4→FeO→Fe 高炉内由上到下大致分为五个区域,即块状带、软熔带、滴落带、焦 炭回旋区和渣铁区。
综上所述,高炉的基本功能是将铁矿石加热、还原、造渣、脱硫、融 化、渗碳得到铁水。
矿石、焦炭、熔剂装入
煤气排出炉外净化后并入管网
3、高炉内的主要反应有:
1、吸附水蒸发
2、结晶水分解 3、矿石间接还原 4、矿石间接还原和直接还原 5、矿石直接还原 6、含铁元素还原和渗C 7、脱S反应 8、石灰石分解 91、0、炉碳渣的生燃成烧槽下称量、配料
此反应在900℃达到平衡时,CO的 气相成分为70%,即ηco=30%
直 接 还 原 区
0
熔化区 1000℃
FeO+CO→Fe+CO2 C+CO2→2CO 各种元素的还原
铁的渗碳
2000℃
FeO+C→Fe+CO
高炉炼铁原理
高炉气体力学
高炉可以认为是个逆流式热交换器。
炉料存在空隙,使得煤气得以上升。煤气的机械运动取决于 它上升过程中遇到的阻力,而其热能和化学能的利用则取决 于与炉料接触的时间、紧密程度及其分布的均匀性。
高炉炼铁原理
炉料在下降过程中,经预热、脱水、间接还原 、直接还原而转化成金 属铁,并不断升温和被焦炭渗碳而形成液态铁水。
焦炭堆密度小,在高炉中其体积占高炉总体积的35~50%。在风口区以 上地区,始终处于固体状态,而在高炉炉料中部铁矿石软化、熔融,在料 柱下部,金属铁和炉渣已形成液态铁水和熔渣,故焦炭对上部炉料起支承 作用,并成为煤气上升和铁水、熔渣下降所必不可少的高温疏松骨架。
煤气穿过料柱上升,就会遇到 阻力,阻力的大小与多种因素 有关。
380kpa