精密与特种加工
精密与特种加工精密与特种加工
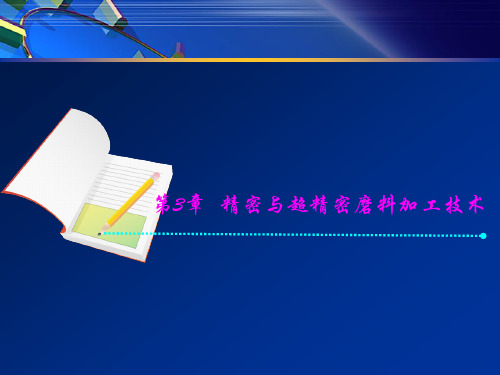
3 砂轮修整
车削法 磨削法
用单点、聚晶金刚石笔,修整片等车 削金刚石砂轮达到修整目的。
用普通磨料砂轮或砂块与超硬磨料砂轮对磨进行 修整,普通磨料磨粒被破碎,切削超硬磨料砂轮 上的树脂、陶瓷、金属结合剂,致使超硬磨粒就 会脱落。目前最为广泛采用的修整法。
3 砂轮修整 软钢磨削整形法
单滚轮法
双滚轮法
31 概述
3. 精密与超精密磨料加工的磨具按其形状和特征又可以分为固 结磨具、涂覆磨具和研磨剂三类。
将一定粒度的磨粒或微粉与结合剂黏结在一起,形成一定形 状并具有一定强度,再采用烧结、黏结、涂敷等方法即形成砂轮、 砂条、油石、砂带等磨具。其中用烧结方法形成砂轮、砂条、油 石等称为固结磨具,其性能评价指标主要有磨粒、粒度、结合剂、 组织与浓度、硬度、强度等方面。用涂敷方法形成砂带,称为涂 覆磨具或涂敷磨具,常用的涂覆磨有砂纸、砂布、砂带、砂盘和 砂布套等。
连续磨削
3 砂轮修整
1. 砂轮修整的必要性 修正几何精度;修锐磨粒;清理容屑空间
2. 修整通常包括整形和修锐两个过程,修整是整形和修锐的总称。 整形是使砂轮达到一定的精度要求的几何形状;修锐是去除磨
粒间的结合剂,使磨粒突出结合剂一定高度(一般是磨粒尺寸的 1/3左右),形成足够的切削刃和足够的容屑空间。前者是为了获 得理想的砂轮几何形状,后者是为了提高磨削锋利度。普通砂轮 的整形和修锐一般是合二为一进行的,超硬磨料砂轮的整形和修 锐一般分开。
(5)计算机数控
5 砂带磨削
1.砂带磨削方式、特点和应用
砂带磨削方式
闭式砂带磨 削
采用无接头或有接头的环形砂带,通过张紧轮撑 紧,由电动机通过接触轮带动砂带高速回转,工 件回转,砂带头架或工作台纵向及横向进给运动, 从而对工件进行磨削。
精密与特种加工

精密与超精密加工1什么是精密与超精密加工?目前在工业发达国家中,一般工厂能稳定掌握的加工精度是1微米。
与此相应,通常将加工精度在0.1~1微米、加工表面粗糙度Ra 在0.02~0.1微米之间的加工方法称为精密加工;而将加工精度高于0.1微米、加工表面粗糙度Ra 小于0.01微米的加工方法称为超精密加工。
2积屑瘤对切削力的影响规律;能够画出积屑瘤的模型;会解释积屑瘤产生规律的原因 规律:积屑瘤高时切削力大,积屑瘤小时切削力也小,和普通切削钢时的规律正好相反。
普通切削切钢时,积屑瘤可增加刀具的前角,故积屑瘤增大可使切削力下降,但是超精密切削时积屑瘤增大反而使切削力增大; 模型如图;产生原因:1)积屑瘤前端R 大约2~3μm ,实际切削力由积屑瘤刃口半径R 起作用,切削力明显增加 。
2)积屑瘤与切削层和已加工表面间的摩擦力增大,切削力增大。
3)实际切削厚度超过名义值,切削厚度增加 ,切削力增加。
3会画金刚石晶体三个面的原子分布图、面网距、面网密度的计算。
100晶面 110晶面 111晶面面积=面积=面积=原子数4x1/4+1=2 原子数 4x1/4+2x1/2+2=4 原子数3x1/6+3x1/2=2 面网密度 面网密度 面网密度面网距 面网距 面网距22D 2D 2/32D 2/2D 22/4D 223/4)2/3/(2D D4理解掌握我国采用哪个晶面作为前后刀面;为什么?应考虑因素:刀具耐磨性好;刀刃微观强度高,不易产生微观崩刃;刀具和被加工材料间摩擦系数低,使切削变形小,加工表面质量高;制造研磨容易。
选用(100)晶面的原因:(111)不适合作前后面。
推荐采用(100)晶面作金刚石刀具的前后面,理由如下:1)(100)晶面的耐磨性高于(110)晶面;2 )(100)晶面的微观破损强度高于(110)晶面,(100)晶面受载荷时的破损机率比(110)晶面低很多;3 ) (100)晶面和有色金属之间的摩擦系数要低于(110)晶面的摩擦系数。
精密加工和特种加工简介

精密加工和特种加工简介
13
的工艺技术,适应加工范围广。
一、电火花加工 1.基本原理 电火花加工是基于脉冲放电蚀除原理产生的,故又称 放电加工或电蚀加工。 电火花加工原理图,由脉冲电源、自动进给调节装置、 工作液循环系统、工具电极等组成。 加工时,脉冲电源的一极接工具电极,另一极接工 件电极。两极均浸入具有一定绝缘度的液体介质(常用 煤油或矿物油)中。
精密加工和特种加工简介
2
工件精度和减少表面粗糙度值为目的的加工方法,如研磨、 珩磨等。
光整加工是指不切除或从工件上切除极薄材料层, 以降低表面粗糙度为目的的加工方法,如超精加工、抛 光等。
一、研磨 1.加工原理
研磨是用研磨工具和研磨剂,从工件上研去一层极 薄表面层的精加工方法。
精密加工和特种加工简介
精密加工和特种加工简介
9
超精加工可在普通车床、外圆磨床上进行,对于批 量较大的生产则宜在专用机床上进行。工作时应充分地 加润滑油,以便形成油膜和清洗极细地磨屑。
超 精 加 工 后 地 工 件 表 面 粗 糙 度 Ra 值 约 在 0.1~0.006μm之间。
四、抛光
抛光是利用机械、化学或电化学地作用,使工件获 的光亮、平整表面的加工方法
精密加工和特种加工简介
5
经研磨后的工件表面,尺寸精度可达IT4~IT1级; 表面粗糙度值可减小到0.1~0.006μm。形状精度 相应提高。
亦可
2)生产效率低,加工余量小。 3) 研磨剂易飞溅,污染环境。
在现代制造业中研磨应用很广,许多精密量块、 量规、齿轮、钢球、喷油嘴、石英晶体、陶瓷元件、光 学镜头及棱镜等零件均需研磨。
3
采用不同的研磨工具(如研磨心棒、研磨套、研磨平板等) 可对内圆、外圆和平面等进行研磨。
精密加工和特种加工简介

14
四、激光加工
工件的激光加工由激光加工机完成。 激光加工机通常由激光器、电源、光学系统 和机械系统等组成。激光器(常用的有固体激 光器和气体激光器)把电能转变为光能,产生 所需的激光束,经光学系统聚焦后,照射在 工件上进行加工。工件固定在三坐标精密工 作台上,由数控系统控制和驱动,完成加工 所需的进给运动。
9
特点及应用范围
①加工硬、脆、韧、软和高熔点的导电材料; ②加工半导体材料及非导电材料; ③加工各种型孔、曲线孔和微小孔; ④加工各种立体曲面型腔,如锻模、压铸模、 塑料模的模膛; ⑤用来进行切断、切割以及进行表面强化、刻 写、打印铭牌和标记等。
10
二、电解加工
电解加工是利用金属在电解液中产生阳极溶 解的电化学原理对工件进行成形加工的一种 方法。 工件接直流电源正极,工具接负极,两极之 间保持狭小间隙(0.1mm-0.8mm)。具有一 定压力(0.5MPa-2.5MPa)的电解液从两极 间的间隙中高速15m/s-60m/s)流过。当工 具阴极向工件不断进给时,在面对阴极的工 件表面上,金属材料按阴极型面的形状不断 溶解,电解产物被高速电解液带走,于是工 具型面的形状就相应地“复印”在工件上。11
12
三、超声波加工
超声波加工是利用超声频(16KHz-25KHz) 振动的工具端面冲击工作液中的悬浮磨料, 由磨粒对工件表面撞击抛磨来实现对工件 加工的一种方法。
13
特点及应用范围
在加工难切削材料时,常将超声振动与其它 加工方法配合进行复合加工,如超声车削、 超声磨削、超声电解加工、超声线切割等。 这些复合加工方法把两种甚至多种加工方法 结合在一起,能起到取长补短的作用,使加 工效率、加工精度及工件的表面质量显著提 高。
精密加工和特种加工简介

电火花线切割加工 电火花线切割加工是用线状电极(钼丝或铜
丝)靠火花放电对工件进行切割,故称为电 火花线切割,有时简称线切割。其应用广泛, 占电加工机床旳60%以上。
二、电解加工
1、加工旳基本原理
电解加工(电化学加工)是利用金属 在电解液中产生阳极溶解旳电化学反应原 理,对金属材料进行成形加工旳一种措施。
不产生宏观应力和变形 加工材料范围很广 电子束能量密度高,生产率很高 加工过程能够自动化 污染少,加工表面不氧化 需要一整套专用设备和真空系统,价格较贵,
应用有一定旳不足
➢电子束加工旳应用
按其功率密度和能量注入时间旳不同,可用于打 孔、切割、蚀刻、焊接、热处理和光刻加工等
➢高速打孔
最小直径可达0.003 mm左右 电子束还能加工小深孔(深径比>10:1) 可加工玻璃、陶瓷、宝石等脆性材料
3、电解加工旳特点及应用
(1)能以简朴旳进给运动一次加工出形状复杂旳型 面或型腔,如锻模、叶片等。
(2)可加工高硬度、高强度和高韧性等难切削旳金 属材料。
(3)加工中无机械切削力或切削热,适合于易变形 或薄壁零件旳加工。
(4)加工后零件表面无剩余应力和毛刺。
(5)工具阴极不损耗。
(6)因为影响电解加工旳原因较多难于实现高精度 旳稳定加工。
焦点上到达很高旳能量密度,靠光热效应来加 工多种材料旳。
激光加工旳特点: 功率密度高达108~1010W/cm2,几乎可加工任何材
料 激光光斑可聚焦到微米级,输出功率可调整,可
用于精密微细加工 所用工具为激光束,是非接触加工,所经没有明
显旳机械力,没有工具损耗;加工速度快,热影 响区小 打孔和切割旳激光深度受限
机械制造1_第6章 精密加工和特种加工

6.2 特种加工方法
1.电火花加工 (1)加工原理。
图6-6 电火花加工原理示意图 a)电火花加工机床结构示意图 b)原理示意图 1—床身 2—立柱 3—工作台 4—工件电极 5—工具电极 6—进给结构及间隙调节器
7—工作液 8—脉冲电源 9—工作液箱
6.2 特种加工方法
图6-7 电火花加工时工件表面形成过程
6.2 特种加工方法
6.2.1 特种加工的概念 特种加工主要是利用电能、光能、声能、热能和化学能
来去除金属和非金属材料的非传统性加工方法。 (1)力学加工。 (2)电物理加工。 (3)电化学加工。 (4)激光加工。 (5)化学加工。 (6)复合加工。 6.2.2 特种加工的特点及应用范围
6.2 特种加工方法
6.1 精密和超精密加工
图6-1 盒式超精密立式车床
6.1 精密和超精密加工
6.与测量技术配套 精密测量是精密加工和超精密加工的 必要条件,有时要采用在线检测、在位检测以及在线补偿 等技术,以保证加工精度要求。 6.1.3 精密与超精密加工方法
根据加工方法的机理和特点,精密和超精密加工方法可 以分为刀具切削加工、磨料加工、特种加工和复合加工4 类。
6.1 精密和超精密加工
(3)超净。 3.切削性能 精密加工和超精密加工必须能均匀地去除不 大于工件加工精度要求的极薄的金属层,这是精密加工和 超精密加工的重要特点之一。 4.加工设备 精密加工和超精密加工的实施必须依靠高精 密加工设备。 (1)机床主轴应具有极高的回转精度及很高的刚性和热稳定 性。 (2)机床的进给系统应能提供超精确的匀速直线运动,保证 在超低速条件下进给均匀,不发生爬行。
图6-2
6.1 精密和超精密加工
(1)金刚石刀具精密切削机理。 (2)影响金刚石刀具精密切削的因素。 1)金刚石刀具材料的材质、几何角度设计、晶面选择、刃 磨质量及对刀。 2)金刚石刀具精密切削机床的精度、刚度、稳定性、抗振 性和数控功能。 3)被加工材料的均匀性和微观缺陷。 4)工件的定位和夹紧。 5)工作环境。
精密加工与特种加工教学大纲5篇
精密加工与特种加工教学大纲5篇第一篇:精密加工与特种加工教学大纲《精密加工与特种加工》教学大纲精密和超精密加工技术部分第一章精密和超精密加工技术及其发展展望(一)课程内容本章主要介绍了发展精密和超精密加工技术的重要性以及超精密加工的现状。
(二)考核知识点和考核要求1、识记:精密加工和超精密加工概念、领域,金刚石刀具两个重要问题,超精密加工中检测内容。
第二章超精密切削与金刚石刀具(一)课程内容本章主要介绍了超精密切削的切削速度选择;超精密切削时刀具的磨损和耐用度;超精密切削时积屑瘤的生成规律;切削参数变化对加工表面质量的影响;刀刃锋锐度对切削变形和表面质量的影响;超精密切削时最小切削厚度;金刚石刀具晶面选择对切削变形和加工表面质量的影响;超精密切削对刀具的要求及金刚石的性能和晶体结构;金刚石晶体各晶面的耐磨性和好磨难磨方向;单晶金刚石刀具的破损机理;金刚石晶体的定向;金刚石刀具的设计与制造。
(二)考核知识点和考核要求1、识记:超精密切削的切削速度选择,金刚石刀具破损或磨损的标志,积屑瘤的生成规律、影响因素及其对加工过程的影响。
刀刃锋锐度对切削过程的影响,金刚石各晶面的好磨难磨方向,金刚石晶体的定向。
2、领会:切削参数对加工表面质量的影响,金刚石的性能特点及晶体结构,单晶金刚石刀具的破损机理,金刚石刀具的设计。
第三章精密磨削和超精密磨削(一)课程内容本章主要介绍了精密和超精密磨削;精密磨削;超硬磨料砂轮磨削;超精密磨削;精密和超精密砂带磨削。
(二)考核知识点和考核要求1、识记:精密和超精密磨料加工方法分类,精密和超精密磨削的特点及其应用,精密和超精密磨削工艺,砂带磨削方式、特点、应用范围及其机理。
2、领会:精密磨削机理,精密磨削与超硬磨料砂轮的修整,超精密磨削机理及其特点。
第四章精密和超精密加工的机床设备(一)课程内容本章主要介绍了精密主轴部件;床身和精密导轨部件;进给驱动系统;微量进给装置;机床的稳定性和减振隔振;减少热变形和恒温控制。
第四章精密与特种加工
(1) 设备简单,操作方便;(2) 加工余量极小; (3) 生产率较高;(4) 表面质量好;(5)仅能提高
工件的表面质量,不能提高尺寸和形位精度。 超级光磨的应用也很广泛,如汽车和内燃
机零件、轴承、精密量具等小粗糙度表面的光 整加工。它不仅能加工轴类零件的外圆柱面, 而且还能加工圆锥面、孔、平面和球面等。
磨膏—由磨料(氧化铬、氧化铁等) 和油酸、软脂等配制而成。
A
抛光
A
抛光机
A
抛光轮 (具有一定弹性的软轮)
组成
毛毡 橡胶 皮革
棉制品 (压制纸板)
A
抛光膏
磨料 (氧化铬、氧化铁等)
油酸
软脂
A
工作原理
抛光时,将零件压于高速旋转的抛光 轮上,在抛光膏介质的作用下,金属表面 产生的一层极薄的软膜,可以用比零件材 料软的磨料切除,而不会在零件表面留下 划痕。加之高速摩擦,使零件表面出现高 温,表层材料被挤压而发生塑性流动,这 样可填平表面原来的微观不平,获得很光 亮的表面(呈镜面状)。
从所用工具和设备来看,抛光最简单,研磨 和超级光磨稍复杂,而珩磨则较为复杂。
A
超精密加工 指加工的尺寸精度以微米计的加工方 法的统称。是指加工精度和表面质量达到 极高精度的加工工艺。
根据所用的工具不同,超精密加工可以 分为超精密切削、超精密磨削和超精密研 磨等。
A
加工原理
零件旋转,磨具以恒力轻压于零件表面, 作轴向进给的同时作轴向微小振动,从而对 零件微观不平的表面进行光磨。
A
加工原理
油石 油膜 零件
超精加工
超精加工
加工过程中,在油石和零件之间注入光磨液 (一般为煤油加锭子油),一方面为了冷却、润滑 及清除切屑等,另一方面为了形成油膜,以便自 动终止切削作用。
04精密加工和特种加工
抛光特点:
①方法简便、经济,不用特殊设备;
②容易对曲面进行加工;
③只能提高粗糙度,不能改变零件的尺寸精度、形状精度或位置精度;
④劳动条件差。
抛光应用: 抛光主要用于零件表面的装饰加工,或者利用抛光方法去除前道工序的加工
痕迹,提高零件的疲劳强度。
抛光零件表面的形状可以是平面、外圆、孔、以及各种成形表面等。 五、各种精密加工方法的比较:
用装有细磨粒、低硬度的油石磨头,在一定压力下 对工件表面进行光整加工的方法称为超级光磨 。
• 加工时工件旋转,油石以恒力轻压于工件表面, 在作轴向进给的同时作轴向微小振动,从而达到 对工件微观不平的表面进行光磨的效果。
超级光磨的特点 : ①加工余量极少,一般为3 ~ 10μm; ②生产率较高,一般加工时间只需30~60秒; ③表面质量好,Ra<0.012μm; ④设备简单,操作方便。 但是,超级光磨只能提高表面质量,不能提高尺寸精度和形位精度。
第二节 特种加工
特种加工是相对于传统的切削加工而言,传统的切削加工是用刀具靠机械 能去除工件表面的多余材料。当工件材料的强度、硬度、脆性、韧性过高, 或零件的结构过于复杂,或尺寸太小,或零件的刚度较差时,传统的切削加 工方法就难于实现。特种加工就是为解决这些难题而发展起来的一种新的加 工方法.
特种加工是直接利用电能、光能、声能、热能、化学能或多种能量复合形 式进行加工的方法。常用的特种加工有电火花加工、电解加工、超声波加工、 激光加工、电子束加工和离子束加工等。
精度为3~O.3 μm,粗糙度为O.3~O·03μm的叫精密加工;
精度为0.3~0.03 μm,粗糙度为0.03~0.005 μm的叫超精密加工,或亚微米 加工;
精度为0.03 μm(30纳米),粗糙度优于0.005 μm以上的则称为纳米(nm)加工。
精密加工与特种加工
一、名词解释1、杂散腐蚀:电解加工时,由于系统中杂散电流的存在而对零件产生的腐蚀。
杂散腐蚀是衡量电解液加工精度高低的指标。
2、空气静压轴承:是利用气体作为润滑剂的滑动轴承。
具有很高的回转精度,但刚度较低,只能承载较小的载荷。
3、激光束模式:激光束的断面能量分布称为模式,用TEM表示,是指横截面上的电磁能分布。
4、多电极更换法:采用多个电极依次更换加工同一个型腔,每个电极加工时必须把上一标准的放电痕迹去掉。
5、解理面:矿物晶体在外力作用下严格沿着一定结晶方向破裂,所裂出的光滑平面称为解理面。
6、电化学当量:在一个电极反应中,相当于1摩尔电子参与反应的发应物的质量。
7、浓度超电压:电解加工时,为减轻浓度极化现象保持一定电化学电流和加工速度而外加的一个电压。
8、精密研磨:属于游离磨粒切削加工,是在刚性研具上注入磨料,在一定压力下,通过研具与工件的相对运动,借助磨粒的微切削作用,除去微量的工件材料,以达到高级几何精度和优良表面粗糙度的加工方法。
9、分解电极法:根据型腔的具体问题将型腔形状分解成几个部分,分别制作不同的电极工具,再分别进行型腔的电火花加工。
是单电极平动加工法和多电极更换加工法的综合应用。
10、面网密度:面网上单位面积内结点的数目。
11、极性效应:在电火花加工过程中,两电极的电蚀量不同的现象。
12、电极电位:任何一种金属插入含该金属离子的水溶液中,在金属或溶液界面上形成的电位差。
二、计算电解加工三、简答1、研磨与抛光的差异。
答:(1)基本原理不同:研磨是通过介于工件与研具之间的磨料或研磨液的流动产生机械摩擦或化学作用去除微量加工余量。
抛光是指采用无纺布等软质材料,具有一定研磨性质地获得光滑表面的加工方法。
(2)磨具不同:研磨用磨具包括铸铁盘、沥青盘、锡盘等硬质材料(刚性材料);抛光采用无纺布、平绒布等软质材料(柔性材料)。
(3)作用不同:抛光只能提高工件表面的光亮度,不改变零件表面的粗糙度;研磨不但可以减小零件的粗糙度,还能在一定程度上提高零件的尺寸和形状精度。
- 1、下载文档前请自行甄别文档内容的完整性,平台不提供额外的编辑、内容补充、找答案等附加服务。
- 2、"仅部分预览"的文档,不可在线预览部分如存在完整性等问题,可反馈申请退款(可完整预览的文档不适用该条件!)。
- 3、如文档侵犯您的权益,请联系客服反馈,我们会尽快为您处理(人工客服工作时间:9:00-18:30)。
精密与超精密加工1什么是精密与超精密加工?目前在工业发达国家中,一般工厂能稳定掌握的加工精度是1微米。
与此相应,通常将加工精度在0.1~1微米、加工表面粗糙度Ra 在0.02~0.1微米之间的加工方法称为精密加工;而将加工精度高于0.1微米、加工表面粗糙度Ra 小于0.01微米的加工方法称为超精密加工。
2积屑瘤对切削力的影响规律;能够画出积屑瘤的模型;会解释积屑瘤产生规律的原因 规律:积屑瘤高时切削力大,积屑瘤小时切削力也小,和普通切削钢时的规律正好相反。
普通切削切钢时,积屑瘤可增加刀具的前角,故积屑瘤增大可使切削力下降,但是超精密切削时积屑瘤增大反而使切削力增大; 模型如图;产生原因:1)积屑瘤前端R 大约2~3μm ,实际切削力由积屑瘤刃口半径R 起作用,切削力明显增加 。
2)积屑瘤与切削层和已加工表面间的摩擦力增大,切削力增大。
3)实际切削厚度超过名义值,切削厚度增加 ,切削力增加。
3会画金刚石晶体三个面的原子分布图、面网距、面网密度的计算。
100晶面 110晶面 111晶面面积= 面积=面积=原子数4x1/4+1=2 原子数 4x1/4+2x1/2+2=4 原子数3x1/6+3x1/2=2 面网密度 面网密度 面网密度面网距 面网距 面网距22D 2D 2/32D 2/2D22/4D223/4)2/3/(2D D4理解掌握我国采用哪个晶面作为前后刀面;为什么?应考虑因素:刀具耐磨性好;刀刃微观强度高,不易产生微观崩刃;刀具和被加工材料间摩擦系数低,使切削变形小,加工表面质量高;制造研磨容易。
选用(100)晶面的原因:(111)不适合作前后面。
推荐采用(100)晶面作金刚石刀具的前后面,理由如下:1)(100)晶面的耐磨性高于(110)晶面;2 )(100)晶面的微观破损强度高于(110)晶面,(100)晶面受载荷时的破损机率比(110)晶面低很多;3 ) (100)晶面和有色金属之间的摩擦系数要低于(110)晶面的摩擦系数。
5理解晶体的解理现象;金刚石哪个晶面容易产生解理现象,为什么?解理现象:是某些晶体特有的现象,晶体受到定向的机械力作用时,沿平行于某个平面平整的劈开的现象;原因:(111)面的宽的面间距(0.154nm)是金刚石晶体中所有晶面间距中的最大的一个,并且其中的连接共价键数最少,只需击破一个价键就可使其劈开,故劈开比较容易。
金刚石内部的解理劈开,在绝大多数情况下是与(111)面网平行,在两个相邻的加强(111)面网之间。
在解理劈开时,可以得到很平的劈开平面。
6精密磨削加工机理;精密磨削砂轮如何选择?精密磨削主要是靠砂轮的精细修整,使磨粒具有微刃性和等高性,磨削后被加工表面留下大量极微细的磨削痕迹,残留高度极小,加上无火花磨削阶段的作用,获得高精度和小表面粗糙度表面,因此精密磨削机理可以归纳为以下几点:a微刃的微切削作用;b微刃的等高切削作用;c微刃的滑挤、摩擦、抛光作用。
精密磨削使所用砂轮的选择以易产生和保持微刃及其等高性为原则。
包括砂轮的粒度选择,砂轮结合剂的选择。
7超精密磨削加工机理(会画图解释单颗粒的磨削过程)(1)超微量切除精密和超精密磨削是一种极薄切削,切屑厚度极小,磨削深度可能小于晶粒的大小,磨削就在晶粒内进行,因此磨削力一定要超过晶体内部非常大的原子、分子结合力,从而磨粒上所承受的切应力就急速地增加并变得非常大,可能接近被磨削材料的剪切强度的极限。
同时,磨粒切削刃处受到高温和高压作用,要求磨粒材料有很高的高温强度和高温硬度。
对于普通磨,在这种高温、高压和高剪切力的作用下,磨粒将会很快磨损或崩裂,以随机方式不断形成新切削刃,虽然使连续磨损成为可能,但得不到高精度、低表面粗糙度值的磨削质量。
因此,在超精密磨削时般多采用人造金刚石、立方氮化硼等超硬磨料砂轮。
(2)单颗粒磨削加工过程砂轮中的磨粒分布是随机的,磨削时磨粒与工件的接触也是无规律的,为研究方便起见,对单颗粒的磨削加工过程进行分析。
1)磨粒是一颗具有弹性支承(结合剂)的和大负前角切削刃的弹性体。
2)磨粒切削刃的切入深度是从零开始逐渐增加,到达最大值再逐渐减少,最后到零。
3)磨粒磨削时在工件中,开始是弹性区,继而塑性区、切削区、塑性区,最后是弹性区。
4)超精密磨削时有微切削作用、塑性流动和弹性破坏作用,同时还有滑擦作用。
磨削加工是无数磨粒的连续磨削。
加工的实质是工件被磨削的表层,在无数磨粒瞬间的挤压,摩擦作用下产生变形,而后转为磨屑,并形成光洁表面的过程。
(3)连续磨削加工过程磨削加工是无数磨粒的连续磨削。
加工的实质是工件被磨削的表层,在无数磨粒瞬间的挤压,摩擦作用下产生变形,而后转为磨屑,并形成光洁表面的过程。
8理解掌握砂带磨削方式,特点(加以描述)及应用范围。
方式:闭式砂带磨削和开式砂带磨削;(1)闭式砂带磨削采用无接头或有接头的环形砂带,通过张紧轮撑紧,由电动机通过接触论带动砂带高速回转,并有工件回转,砂带头架或工作台作纵向及横向进给运动,从而对工件进行磨削。
这种方式效率高、但噪声大、容易发热,可用于粗、半精和精加工。
(2)开式砂带磨削采用成卷砂带,由电动机经减速机构通过卷带轮带动砂带作极缓慢的移动,砂带绕过接触论并以一定的工作压力与工件被加工表面接触,并有工件回转,砂带头架或工作台作纵向及横向进给,从而对工件进行磨削。
由于砂带在磨削过程中的连续缓慢移动,磨削区域不断出现新砂粒,退出旧砂粒,切削比较稳定,因此磨削质量高,磨削效果好,但效率不如闭式砂带磨削,多用于精密和超精密磨削中。
砂带磨削按砂带与工件接触形式来分又可分为接触轮式、支撑板(轮)式、自由浮动接触式和自由接触式。
按加工表面类型来分,砂带磨削又可分为外圆、内圆、平面、成形表面等磨削方式。
特点及应用范围:1)砂带磨削时,砂带本身具有弹性,接触轮外缘表面有橡胶层或软塑料层,砂带与工件是柔性接触,磨粒载荷小而均匀,具有较好的抛光作用,同时又能减振,因此工件的表面质量高,表面粗糙度可达Ra0.05~0.01um。
砂带磨削又有“弹性”磨削之称。
2)砂带制作时,用静电植砂法易于使磨粒有方向性,同时磨粒的切削刃间隔长,摩擦生热少,散热时间长,切屑不易堵塞,力、热作用小,有较好的切削性,有效的减少了工件的变形和表面烧伤。
3)砂带磨削效率高,可以与铣削和砂轮磨削媲美,强力砂带磨削的效率可为铣削的10倍、普通砂轮磨削的5倍。
砂带磨削无需修整,磨削比(切除工件重量与磨料磨损重量之比)可高达300:1甚至400:1,而砂轮磨削一般只有30:1.砂带磨削方法早已有之,由于基底材料强度和磨粒与基底的粘结强度有了极大地提高,才使得砂带磨削焕发新生,因此有“高效”磨削之称。
4)砂带制作比砂轮简单方便,无烧结、动平衡等问题,价格也比砂轮便宜。
砂带磨削设备结构简单,可制作砂带磨床或砂带磨削头架,后者可安装在各种普通机床上进行砂带磨削工作,使用方便,制造成本低廉,又有“廉价”磨削之称。
5)砂带磨削有广阔的工艺性和应用范围,可加工外圆、内圆、平面和成形表面。
砂带磨削头架可安装在卧式车床、立式车床、龙门刨床等普通机床上进行磨削加工。
因此有很强的适应性,砂带不仅可加工各种金属材料,材料,而且可加工木材、塑料、石材、水泥制品、橡胶等非金属材料以及单晶硅、陶瓷和宝石等硬脆材料。
开式砂带磨削加工铜、铝等软材料表面效果良好,独具特色,因此又有“万能”磨削之称。
缺点:砂带磨削不能加工窄退刀槽的阶梯轴、阶梯孔、盲孔、小孔、齿轮等,对形状和位置精度要求高的也不如精密砂轮磨削。
9减少机床热变形的措施?1)尽量减少机床中的热源;2)采用热膨胀系数小的材料制造机床部件;3)结构合理化使在同样的温度变化条件下,机床的热变形最小;4)使机床长期处在热平衡状态,使热变形量成为恒定;5)使用大量恒温液体浇淋,形成机床附近局部地区小环境的精密恒温。
10理解怎样减少外界振动对机床的影响?(会举例)提高机床结构的抗振性和消除减少机床内的振动:(1)各运动部件都经过精密动平衡,消灭或减少机床内部的振源。
(2)提高机床结构的抗振性。
(3)在机床结构的易振动部分,人为的加入阻尼,减小振动。
(4)使用振动衰减能力强的材料制造机床的结构件。
隔离振源,使用隔振沟、隔振墙和空气隔振垫以减少外界振动的影响:(1)超精密机床应尽量远离振源;LODTM大型超精密车床为避免恒温水的水泵的振动的影响,水泵将恒温水打到水箱中,恒温水靠自重从水箱流到超精密机床的各个部件。
(2)超精密机床采用单独地基,隔振沟、隔振墙等;LODTM车床除用带隔振沟的地基外,还将机床放置在带隔振墙的房间。
(3)使用空气隔振垫Moore公司的M-18AG车床、Pneumo公司的MSG-325车床、DTM-3机床和LODTM 车床用空气隔振垫支承,高位支承将使机床的抗振性提高,增加机床的稳定性。
11什么是在线检测?及其特点。
在线检测:工件在加工过程中同时进行检测,称之为在线检测。
特点:(1)能够连续检测加工过程的变化,了解在加工过程中误差分布和发展,从而为实时误差补偿、预报误差补偿和控制创造了条件;(2)检测结果能够反映实际加工情况;(3)在线检测由于是在加工过程中进行,会受到加工过程中一些条件的限制,在线检测的难度一般较大;(4)在线检测大都用非接触传感器,对传感器的性能要求较高;(5)在线检测一般是自动运行,形成在线检测系统,包括误差信号的采集、处理和输出、与误差补偿控制系统的连接。
因此它往往不是一种单纯的检测方法。
12什么样的机床稳定性好?怎样提高机床的稳定性?1)各部件的尺寸稳定性好(1)采用尺寸稳定性好的材料制造机床部件,如用陶瓷、花岗岩、尺寸稳定性好的钢材、合金铸铁等;(2)各部件经过消除应力使部件有高度的尺寸稳定性。
2)结构钢性高,变形小(1)当机床运动部件位置改变,工件装卸或负载变化,受力作用变化等,均将造成变形。
要求结构刚度高、变形量极小,基本不影响加工精度。
(2)各接触面和连接面的接触良好,接触刚度高,变性极小。
13理解空气静压轴承主轴的工作原理(1)圆柱径向轴承和端面止推空气静压轴承:径向轴承的轴套制成外面鼓形,能自动调整定心。
轴套的外表面做凸形球面,与轴承盖及轴承座上的凹形球面相配合。
当轴变形时,轴套可以自动调整位置,从而保证轴颈与轴鼓为面接触。
用多孔石墨的轴衬代替小节流孔。
(2)双半球空气轴承主轴:前后轴承均采用半球状,既是径向轴承又是轴向轴承。
由于轴承的气浮面是球面,有自动调心作用,可提高前后轴承的同心度,提高主轴的回转精度。
(3)前部用球形后部用圆柱径向空气轴承的主轴、立式空气轴承14切削刃钝圆半径与最小切削厚度的关系?分析最小厚度与哪些因素有关?15超精密切削刀具常采用哪些材料以及材料特点。