钻削加工钻头的磨制办法
磨钻头的方法和技巧口诀
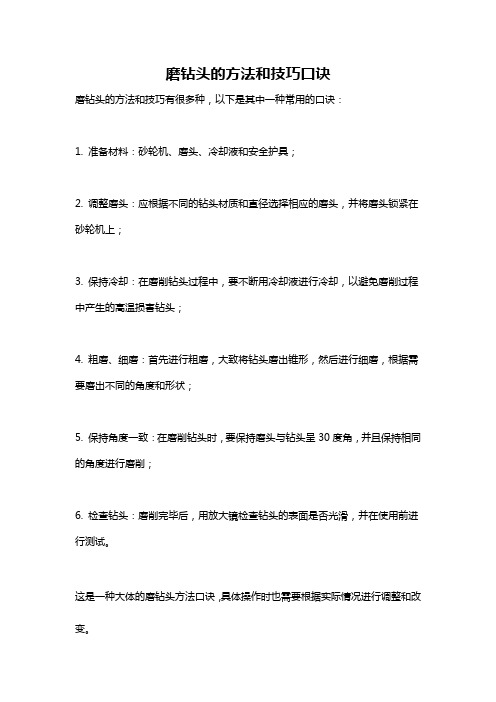
磨钻头的方法和技巧口诀
磨钻头的方法和技巧有很多种,以下是其中一种常用的口诀:
1. 准备材料:砂轮机、磨头、冷却液和安全护具;
2. 调整磨头:应根据不同的钻头材质和直径选择相应的磨头,并将磨头锁紧在砂轮机上;
3. 保持冷却:在磨削钻头过程中,要不断用冷却液进行冷却,以避免磨削过程中产生的高温损害钻头;
4. 粗磨、细磨:首先进行粗磨,大致将钻头磨出锥形,然后进行细磨,根据需要磨出不同的角度和形状;
5. 保持角度一致:在磨削钻头时,要保持磨头与钻头呈30度角,并且保持相同的角度进行磨削;
6. 检查钻头:磨削完毕后,用放大镜检查钻头的表面是否光滑,并在使用前进行测试。
这是一种大体的磨钻头方法口诀,具体操作时也需要根据实际情况进行调整和改变。
手工磨钻头的方法和技巧

手工磨钻头的方法和技巧手工磨钻头的方法和技巧作为一个手艺人,从钻头的选择到磨制细节,每一步都需要认真对待。
精心磨制的钻头可以加快工作效率并提高观感。
下面是手工磨钻头的方法和技巧,希望对你有所帮助。
选择正确的钻头选择正确的钻头是成功磨制的第一步。
不同的材料和工作需要不同形状和大小的钻头。
一般而言,较大的钻头适用于粗加工,较小的钻头适用于细加工。
准备工作在磨制钻头前,我们需要先准备好工具和材料。
在磨制钻头时,需要使用磨片和多种研磨材料。
准备好的材料需分别按磨具的不同材质和不同磨头尺寸进行分类,便于使用。
磨头角度选择正确的磨头角度可以让你的钻头切入材料时更加顺畅。
较小的角度可进一步提高精度,但是也会降低切削深度。
最好的角度范围在118~135度之间。
使用磨头当你正在磨钻头时,需要小心地使用磨头。
切记不要迫使磨头向着过于极端的角度进行移动,否则将会失去磨削达到想要的效果。
应该慢慢打圆而不是直接进行切削。
同时,需要确保保持钻头杆平直避免磨坏几何形状。
使用适当的磨具使用适当的磨具可以让你更快速地磨制钻头,但同时也可能损害锋利的钻头。
一般使用小型钻床会更加可靠和稳定,而手工磨削过程中考虑到个人能力问题可以随心所欲的控制切割面,但不建议太多力量加在它上面。
清洁与保养在完成磨制后,需要使用清洁剂或其他磨削剂来清洁钻头并确保其质量。
同时,在使用时,要避免过多插入或者在安装时摆弄钻头,以免磨损破坏。
切记,正确使用和存放孔钻将会让它们保持锋利并且持久不衰。
总结手工磨制钻头需要认真对待,注意细节,并选择正确的钻头和磨具。
如果你按照以上方法进行操作并保持良好的清洁和保养习惯,你将可以获得持久锋利和高质量的钻头,帮助你在工作中取得更好的效果。
钻头磨削的技巧

钻头磨削的技巧钻头磨削是一项重要的技巧,它对于钻头的使用寿命和钻孔质量至关重要。
下面将介绍一些钻头磨削的技巧,以便能够更有效地使用钻头。
首先,要选择合适的磨削工具和磨削材料。
常见的磨削工具有手持磨削机、砂轮和磨石等。
砂轮有两种类型,硅炭化研磨头适用于高速钻头的磨削,硼氮化合金砂轮适用于硬质和脆性的钻头。
磨石可以用来修复已经磨削过的钻头。
其次,需要选择合适的磨削角度。
对于一般的钻头,应该选择30度的磨削角度。
对于硬质材料和脆性材料,可以选择更小的磨削角度,如25度或20度。
这样可以减小钻头的磨损和断裂的风险。
在磨削过程中,要保持磨削的稳定和均匀。
首先,要避免过度磨削。
磨削时要用足够的力量,但不宜过大。
过度磨削会导致钻头过热,从而损坏钻头的钢质,并降低钻头的硬度和韧性。
其次,要保持磨削的均匀。
磨削时要注意磨削的力度和速度要均匀,以免造成钻头的不均匀磨损。
此外,还要定期修复已磨削过的钻头。
钻头使用一段时间后,钻片会变钝并磨损,影响其使用效果。
定期修复可以延长钻头的寿命。
修复钻头时,可以使用砂轮或磨石将钻头的前端修复成合适的尺寸和形状。
修复钻头时要注意保持修复的平整和光滑,以保证钻头的使用效果。
此外,要定期清理和润滑钻头。
在钻孔过程中,钻头会受到金属屑和灰尘的侵蚀,导致钻头的磨损加剧。
因此,要定期清理钻头,可以使用软刷将金属屑和灰尘清除,并使用适量的润滑油涂抹钻头,减小钻头与工件的摩擦力并保护钻头。
最后,要选择适当的钻头材质。
不同的钻头材质适用于不同的材料和应用场景。
例如,硬质合金钻头适用于钢材和铁材的加工,而高速钢钻头适用于铝材和塑料材料的加工。
总结起来,钻头磨削的技巧包括选择合适的磨削工具和材料、选择合适的磨削角度、保持磨削的稳定和均匀、定期修复钻头、清理和润滑钻头以及选择适当的钻头材质。
通过掌握这些技巧,可以更有效地使用和管理钻头,延长钻头的寿命并提高钻孔质量。
(完整版)钻削加工,钻头的磨制方法

1 钻小孔的精孔钻钻削直径在(2~16)mm的内孔时,可将钻头修磨成图7-1所示的几何形状,使其具有较长的修光刃和较大的后角,刃口十分锋利,类似铰刀的刃口和较大的容屑槽,可进行钻孔和扩孔,使孔获得较高的加工精度和表面质量。
钻孔或扩孔时,进给要均匀。
对钻削碳钢时加工精度可达IT(6~8),表面粗糙度可达Ra(3.2~1.6)μm。
采用的切削用量:Vc =(2~10)m/min,f=(0.08~0.2)mm/r。
冷却润滑液为乳化液或植物油。
2 半孔钻工件上原来就有圆孔,要扩成腰形孔,这就需要钻半孔了。
若采用一般的钻头进行钻削,会产生严重的偏斜现象,甚至无法钻削加工。
这时可将钻头的钻心修整成凹形,如图7-2所示,突出两个外刃尖,以低速手动进给,即可钻削。
实际钻削时,还会遇到超过半孔和不超过半孔的情况,由于两者的切削分力情况不同,必须对半孔钻的几何参数作必要的修正,若条件可能的话,使用相应的钻套,就更好了。
3 平底孔钻平底又分平底解体4通孔和平底盲孔,如图7-5(b)、(c)所示。
这时,可把麻花钻磨成两刃平直且十分对称的切削刃,并把前角修磨成3°~8°,后角为2°~3°特别是后角不能大,大了以后不仅引起“扎刀”,而且孔底面呈波浪形,重则会造成钻头折断事故。
若钻削盲孔时,应把钻心磨成如图7-5(c)所示的凸形钻心,以便钻头定心,使钻削平稳。
4 薄板钻在(0.1~1.5)mm厚的薄钢板、马口铁皮、薄铝板、黄铜皮和紫铜皮上钻孔,不能用普通钻头,否则钻出的孔就会出现不圆、成多角形、孔口飞边、毛刺很大,甚至薄板扭曲变形,孔被撕破。
大的薄板很难固定在机床上,若用手握住薄板钻孔,当用普通麻花钻的钻尖刚钻透时,钻头失去定心的能力,工件发生抖动,刀刃突然多切,扎入薄板,切削力急增,易使钻头折断或手扶不住,造成事故。
图7-6所示的薄板钻,钻时钻尖先切人工件,起定心作用,两个风力的外尖迅速把中间切离,得到所要求的孔用它钻薄板的干净利落,安全可靠。
标准钻头磨法
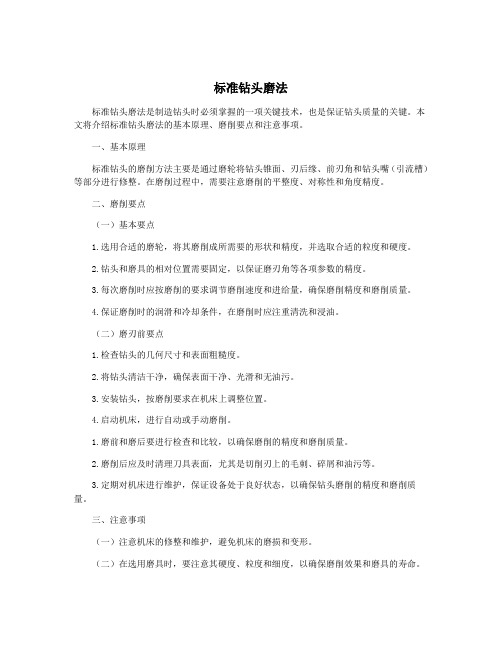
标准钻头磨法
标准钻头磨法是制造钻头时必须掌握的一项关键技术,也是保证钻头质量的关键。
本文将介绍标准钻头磨法的基本原理、磨削要点和注意事项。
一、基本原理
标准钻头的磨削方法主要是通过磨轮将钻头锥面、刃后缘、前刃角和钻头嘴(引流槽)等部分进行修整。
在磨削过程中,需要注意磨削的平整度、对称性和角度精度。
二、磨削要点
(一)基本要点
1.选用合适的磨轮,将其磨削成所需要的形状和精度,并选取合适的粒度和硬度。
2.钻头和磨具的相对位置需要固定,以保证磨刃角等各项参数的精度。
3.每次磨削时应按磨削的要求调节磨削速度和进给量,确保磨削精度和磨削质量。
4.保证磨削时的润滑和冷却条件,在磨削时应注重清洗和浸油。
(二)磨刃前要点
1.检查钻头的几何尺寸和表面粗糙度。
2.将钻头清洁干净,确保表面干净、光滑和无油污。
3.安装钻头,按磨削要求在机床上调整位置。
4.启动机床,进行自动或手动磨削。
1.磨前和磨后要进行检查和比较,以确保磨削的精度和磨削质量。
2.磨削后应及时清理刀具表面,尤其是切削刃上的毛刺、碎屑和油污等。
3.定期对机床进行维护,保证设备处于良好状态,以确保钻头磨削的精度和磨削质量。
三、注意事项
(一)注意机床的修整和维护,避免机床的磨损和变形。
(二)在选用磨具时,要注意其硬度、粒度和细度,以确保磨削效果和磨具的寿命。
(三)在磨削过程中,要坚持与操作规程相符合,不要随意调整进给量和转速等参数。
(四)磨削时应注意质量控制,磨削出来的钻头应经过检查合格后方可使用。
不同用途钻头的刃磨方法

不同用途钻头的刃磨方法有:
1.磨钻头前,先要将钻头的主切削刃与砂轮面放置在一个水平面
上,保证刃口接触砂轮面时,整个刃都要磨到。
这是钻头与砂轮相对位置的步,位置摆好再慢慢往砂轮面上靠。
2.钻头轴线要与砂轮面斜出60°的角度。
这个角度是钻头的锋角,
此时的角度不对,将直接影响钻头顶角的大小及主切削刃的形状和横刃斜角。
这里是指钻头轴心线与砂轮表面之间的位置关系,取60行,这个角度一般比较能看得准。
3.由刃口往后磨后面。
刃口接触砂轮后,要从主切削刃往后面磨,
也就是从钻头的刃口先开始接触砂轮,而后沿着整个后刀面缓慢往下磨,这样便于散热和刃磨。
钻头切入时可轻轻接触砂轮,先进行较少量的刃磨,并注意观察火花的均匀性,及时调整手上压力大小,还要注意钻头的及时冷却,不能磨过火,造成刃口变色。
C17钻头的基本磨制作业指导书
鑽頭的基本磨制方法一﹑鑽頭的分類﹕麻花鑽﹑中心鑽﹑扁鑽﹑深孔鑽﹑直柄鑽。
1.中心鑽﹕加工軸類零件用﹔分為中心鑽﹑復合中心鑽和鑽三類。
2.麻花鑽﹕直柄(Φ13㎜以下)﹐Φ13㎜以上一般做成錐柄。
錐柄的好處﹕傳遞較大的轉矩﹐裝夾時的定位精度較高。
麻花鑽的七個組成部分(見圖7-3)A前面﹕起排屑作用B主切削刃﹕起切屑作用C橫刃﹕起修光孔臂和導向作用D后面﹕起定心作用﹐產生軸向抗力E主切削刃F副切削刃(棱刃)G副后面(棱邊)二﹑磨削鑽頭時應注意的3個角度1.頂角(鋒角)﹐即圖7-3的2Φ應為118°誤差為正負2°頂角的大小影響主切削刃上切削力的大小﹐在相同的切削條件下﹐頂角越小在鑽削時軸向抗力越小﹐刀尖端角隨之越大﹐則切削溫度下降﹐鑽頭使用壽命延長﹐僻端鑽尖瘦弱﹐強度降低。
一般在硬材料上鑽孔。
頂角稍大些﹐反之頂角可小些。
2.后角﹐通過主切削刃上某一選定點(Y)所作以鑽頭軸線為軸心的圓柱面的切平面上﹐后面與切削平面的夾角﹐外徑邊緣處的事角為8°-14°﹐近橫刃處紙20°-26°3.橫刃斜角﹐鑽頭端面投影上﹐橫刃與中剖面間的夾角標准麻花鑽的橫刃斜角一般為50°-55°.三﹑標准鑽頭的刃磨1.操作者站在砂輪的左側﹐右手握住鑽頭工作部分﹐食指晝量靠近切削部分作鑽頭擺動支點﹐將主切削刃與砂輪中心面放置在同一水平面內(見圖7-21)﹐且使鑽頭的軸線與砂輪圓柱面母線在水平面內的夾角為Φ(56°-60°)﹐右手操縱鑽頭繞自身軸線轉動﹐磨削到整個后刀面﹐左手握住鑽柄作上下擺動﹐磨出不同的后角﹐兩手的動作必須穩定﹐協調一致﹐轉動的目的上下擺動﹐磨好一個主切削刃﹐翻轉180°磨另一個主切削刃。
2.注意事項﹕左手擺動鑽柄時不得高出水平面﹐以免磨出負后角﹐粗磨時﹐一般后面的下部先接觸砂輪﹐左手上擺進行刃磨﹐精磨時﹐一般主切削刃先接觸砂輪﹐左手下擺進行刃磨﹐且磨削量要小﹐刃磨時面要短﹐整個刃磨過程中﹐鑽頭應經常浸水冷卻以免退火。
磨钻头的方法
磨钻头的方法磨钻头是一项重要的工艺,它可以提高钻头的使用寿命和钻孔效果。
下面将介绍几种常用的磨钻头的方法。
一、手工磨削法手工磨削法是最常见的磨钻头的方法之一。
首先,需要准备磨具,如磨石、砂轮等。
然后,将钻头夹紧在钻头夹具上,用手持磨具对钻头进行磨削。
在磨削的过程中,要注意保持磨具与钻头的接触面积,保持一定的磨削压力,并使磨削均匀。
同时,要时刻观察钻头的磨削情况,确保磨削的效果达到要求。
二、机械磨削法机械磨削法是使用机械设备对钻头进行磨削的方法。
常见的机械设备有磨床、磨削机等。
首先,将钻头夹紧在机械磨削设备上,调整设备的磨削参数,如转速、磨削压力等。
然后,启动设备,让钻头与磨具接触,进行磨削。
在磨削的过程中,要注意设备的运行状态,确保磨削的效果良好。
三、电火花磨削法电火花磨削法是利用电火花放电原理对钻头进行磨削的方法。
首先,需要准备电火花磨削设备,如电火花磨床。
然后,将钻头夹紧在电火花磨削设备上,调整设备的放电参数,如电流、脉冲宽度等。
接下来,启动设备,让钻头与电极接触,进行磨削。
在磨削的过程中,要注意设备的运行状态,确保磨削的效果达到要求。
四、化学磨削法化学磨削法是利用化学溶解原理对钻头进行磨削的方法。
常见的化学磨削方法有酸洗法、电解法等。
首先,需要准备相应的化学磨削液,如酸溶液、电解液等。
然后,将钻头浸泡在化学磨削液中,进行磨削。
在磨削的过程中,要注意控制化学磨削液的浓度和温度,确保磨削的效果良好。
以上是几种常见的磨钻头的方法,每种方法都有其适用的场景和优缺点。
在使用这些方法进行磨削时,要根据具体的情况选择合适的方法,并注意操作的安全性和磨削的效果。
同时,还要定期对钻头进行磨削,以保证其良好的工作状态和使用寿命。
磨钻头是一项需要技巧和经验的工艺,只有掌握了正确的方法和技巧,才能达到预期的效果。
磨钻头的方法和技巧
磨钻头的方法和技巧
磨钻头是一项需要技巧和耐心的工作,正确的磨削可以延长钻头的使用寿命,
提高工作效率。
下面我将介绍一些磨钻头的方法和技巧,希望能对大家有所帮助。
首先,选择合适的磨削工具非常重要。
通常情况下,我们可以选择磨刀石、砂
轮或者专业的钻头磨削机来进行磨削。
不同的工具适用于不同类型的钻头,因此在选择工具时需要根据钻头的材质和形状来进行合理的选择。
其次,正确的磨削角度也是非常重要的。
通常情况下,钻头的磨削角度应该根
据具体的使用要求来确定。
一般来说,木工钻头的磨削角度应该在25°到30°之间,金属工艺钻头的磨削角度则应该在135°到150°之间。
因此,在进行磨削之前,需要先确定好钻头的使用对象,然后再进行磨削角度的调整。
此外,磨削过程中需要注意保持稳定的力度和速度。
磨削时,需要用手稳定住
钻头,并且保持适当的力度和速度,避免过快或者过慢的磨削速度,以免损坏钻头或者磨削效果不佳。
最后,磨削后需要进行合理的抛光和清洁工作。
磨削完成后,需要用砂纸或者
砂轮对钻头进行适当的抛光,以确保钻头表面光滑,减少使用时的摩擦阻力。
同时,还需要用清洁剂对钻头进行清洁,去除磨削产生的金属屑和污垢,以保持钻头的清洁和锋利度。
总的来说,磨钻头是一项需要技巧和耐心的工作,正确的磨削可以延长钻头的
使用寿命,提高工作效率。
选择合适的磨削工具,正确的磨削角度,稳定的力度和速度,以及合理的抛光和清洁工作,都是磨钻头时需要注意的关键点。
希望以上方法和技巧能够帮助大家更好地进行钻头的磨削工作。
磨转头的正确方法与技巧
磨钻头是一项需要技巧和耐心的任务,正确的磨钻方法不仅可以提高工作效率,还能保证钻孔质量。
下面将详细介绍磨转头的正确方法和技巧,以帮助您更好地完成这一工作。
一、准备工作1. 工具准备:准备磨钻头所需的工具,包括钻头、砂轮、夹具、磨石等。
确保工具齐全且完好无损。
2. 安全防护:佩戴好安全眼镜、口罩等防护用品,确保工作过程中的安全。
3. 钻头选择:根据需要磨削的钻头材质、尺寸和形状选择合适的磨削工具和磨石。
二、磨削技巧1. 保持平衡:在磨削钻头时,要保持手腕的平衡,避免用力过度或不均导致钻头损坏。
2. 调整角度:根据需要磨削的钻头角度,调整磨石与钻头的角度,一般保持在15-20度左右。
3. 控制速度:磨削时速度不宜过快,应该以均匀的速度进行,避免热量集中导致钻头损坏。
4. 观察火花:在磨削过程中要时刻观察火花情况,如果火花颜色为暗红色,说明磨削已经完成。
5. 冷却液:在磨削过程中要使用冷却液,保持钻头冷却,避免因过热导致钻头损坏。
三、注意事项1. 不要在砂轮侧面磨削钻头,以免损坏砂轮。
2. 磨削时要避免将手放在钻头前方,防止意外伤害。
3. 不要将钻头对着他人或自己,防止意外伤害。
4. 在磨削过程中要时刻观察钻头的磨损情况,如果磨损严重应及时更换。
5. 磨削完成后要清洗干净钻头,并妥善保管,避免受潮和污染。
通过掌握正确的磨转方法和技巧,可以有效地提高工作效率和钻孔质量。
在操作过程中,一定要注意安全问题,遵循操作规程,确保工作顺利完成。
同时,对于不同的材料和加工需求,需要采用不同的钻头和磨削参数,因此在实际操作中要根据具体情况进行调整。
- 1、下载文档前请自行甄别文档内容的完整性,平台不提供额外的编辑、内容补充、找答案等附加服务。
- 2、"仅部分预览"的文档,不可在线预览部分如存在完整性等问题,可反馈申请退款(可完整预览的文档不适用该条件!)。
- 3、如文档侵犯您的权益,请联系客服反馈,我们会尽快为您处理(人工客服工作时间:9:00-18:30)。
精心整理1 钻小孔的精孔钻
钻削直径在(2~16)mm的内孔时,可将钻头修磨成图7-1所示的几何形状,使其具有较长的修光刃和较大的后角,刃口十分锋利,类似铰刀的刃口和较大的容屑槽,可进行钻孔和扩孔,使孔获得较高的加工精度和表面质量。
钻孔或扩孔时,进给要均匀。
对钻削碳钢时加工精度可达IT(6~8),表面粗糙度可达Ra(3.2~1.6)μm。
采用的切削用量:Vc =(2~10)m/min,f=(0.08~0.2)mm/r。
冷却润滑液为乳化液或植物油。
2 半孔钻
工件上原来就有圆孔,要扩成腰形孔,这就需要钻半孔了。
若采用一般的钻头进行钻削,会产生严重的偏斜现象,甚至无法钻削加工。
这时可将钻头的钻心修整成凹形,如图7-2所示,突出两个外刃尖,以低速手动进给,即可钻削。
实际钻削时,还会遇到超过半孔和不超过半孔的情况,由于两者的切削分力情况不同,必须对半孔钻的几何参数作必要的修正,若条件可能的话,使用相应的钻套,就更好了。
3 平底孔钻
平底又分平底解体4通孔和平底盲孔,如图7-5(b)、(c)所示。
这时,可把麻花钻磨成两刃平直且十分对称的切削刃,并把前角修磨成3°~8°,后角为2°~3°特别是后角不能大,大了以后不仅引起“扎刀”,而且孔底面呈波浪形,重则会造成钻头折断事故。
若钻削盲孔时,应把钻心磨成如图7-5(c)所示的凸形钻心,以便钻头定心,使钻削平稳。
4 薄板钻
在(0.1~1.5)mm厚的薄钢板、马口铁皮、薄铝板、黄铜皮和紫铜皮上钻孔,不能用普通钻头,否则钻出的孔就会出现不圆、成多角形、孔口飞边、毛刺很大,甚至薄板扭曲变形,孔被撕破。
大的薄板很难固定在机床上,
若用手握住薄板钻孔,当用普通麻花钻的钻尖刚钻透时,钻头失去定心的能力,工件发生抖动,刀刃突然多切,扎入薄板,切削力急增,易使钻头折断或手扶不住,造成事故。
图7-6所示的薄板钻,钻时钻尖先切人工件,起定心作用,两个风力的外尖迅速把中间切离,得到所要求的孔用它钻薄板的干净利落,安全可靠。
当钻削较厚的板料时,应将外缘刃尖磨成短平刃,以增强外缘刃尖的强度和改善散热条件。
钻黄铜皮时,外缘刃刀尖处的前角为0°。
5 在平板玻璃上钻孔
利用研磨的原理,在平板玻璃上钻孔。
将研磨剂涂敷在研磨头和玻璃表面,研磨头安装在钻床或电钻上,使研磨头旋转,在适当的压力下,研磨剂中的磨粒对玻璃起切削作用,从而在玻璃上研磨出一个和研磨头外圆一样大的圆孔。
研磨头如图7-10所示,材质为45钢,L大于玻璃2倍厚度,d0为玻璃孔径,并在端面开槽,以便使磨料进入磨削区。
磨料为碳化硅,粒度为150#~180#,用煤油调成糊状,研磨时涂抹在研磨头和玻璃之间。
研磨时,玻璃必须安放平,并在它的底下垫上较软的东西。
被加工的孔快要通时,进给压力要减小,也可翻转180°再研。
厚度为3mm的玻璃加工一个孔,只需要2min,而且加工出来的孔,轮廓整齐无细微脆裂,粗糙度也好。
6 前排屑扩孔钻头
在普通钻床或车床上由普通麻花钻孔时,切屑总是沿着钻头的螺旋形容屑槽向后排出。
这样,它对钻削过程产生以下不利影响:切屑向后排出,随着扩孔深度的增加,切屑不断增长,随钻头一起旋转甩出,危及操作者的安全;切屑向后排,影响冷却液的进入,使切削温度增高,钻头的耐用度下降,同时切屑划伤已加工表面,使表面粗糙度增大。
为了解决扩孔中的排屑问题,刃磨了如图7-12所示的前排屑钻头,克服了上述的问题,获得了良好的效果。
前排屑钻头采用锋角2Φ为100°~120°,去掉横刃,外刃磨出15°~30°的刃倾角,控制切屑流向。
外刃长度为(1~1.5)倍切削深度。
切削时,切削速度选择为(2~8)m/min,进给量为0.2mm/r左右。
在正的刃倾角的作用下,切屑排向待加工表面。
冷却液从钻头的螺旋槽流入,没有切屑的干扰,很容易流入切削区,冷却效果好。
这种前排屑扩孔钻,不仅用于精扩,而且可用于毛坯孔的扩孔,纠正毛坯孔的歪斜。
采用前排屑扩孔钻,可以提高产品质量,提高钻头的使用寿命30%,降低表面粗糙度。
刃磨时,要求外刃刃磨对称,否则形成单刃切削,引起孔径扩大。
还要根据工件材料的不同,硬度高低选择不同的刃倾角。
7 精孔扩孔钻头
钻孔一般只作为粗加工工序,对孔的精度和孔的表面粗糙度要求不高。
但在特殊的情况下,也可用钻头来加工精度较高、粗糙度较低的孔。
为了钻出精度较高的孔,就必须采取措施,减少棱边与孔壁的摩擦、刮伤和避免切屑对孔壁的擦伤,避免切削过程中定心不稳和振动和切屑瘤的产生,改善切削层的变形,减小残留面积高度,注意钻头本身的精度和切削运动中的位置精度。
图7-14 所示的是钢料精孔钻的几何参数。
一般在钢料上要钻出精孔,应采用扩孔的方法。
在外刃上磨出大于1 5°的正刃倾角,以控制切屑向待加工表面排出,并将外刃与棱边处修圆。
在扩钢料孔时,切削速度为(2~8)m/ min,进给量为(0.14~0.2)mm/r,单边加工余量为(0.5~0.8)mm,孔的表面粗糙度可达到Rα(3.2~1.6)μm,如果进一步避免刀瘤,提高钻头与工件的相对运动精度,仔细修磨棱边,孔壁表面粗糙度可达Ra(1.6~0.8)。
8 钻削难切材料时应注意的问题
难切削材料的切削的加工特点主要是切削力和切削热大,切削表面硬化现象严重,切屑难于控制和刀具磨损严重。
要在难切削材料上钻孔,比其它切削加工更为困难。
(1)钻削硬度高、强度高的材料时,产生的切削力大和切削热也多,为了提高刀具耐用度,首先应选用硬质合金钻头,如整体和镶片的硬质合金钻头,如选高速钢麻花钻,应使外刃前角减小,以增加刃口强度和改善散热条件。
钻削时应选用合理的切削速度,保证钻头有一定的耐用度。
(2)钻削硬化严重的不锈钢、高温合金、高锰钢等材料时,这些材料切削加工硬化程度可达100%~200%,深度可达0.1mm以上。
钻削时要求钻头刃口锋利,以减小挤压和使硬化加剧。
钻头用钝后要及时刃磨,特别是在进给的过程中,不要随意停止进给,使钻头在切削表面摩擦,造成切削表面严重硬化,给下一步切削造成困难,所以进刀和退刀要果断。
选择切削用量时,切削深度和进给量不宜太小,应避免在硬化层上切削,加速刀具磨损。
(3)要选择合理的钻头几何参数和切削用量。
群钻的出现,为改变钻头几何参数和适应不同材料的钻孔,提供了宝贵经验,特别是对难切削材料更为重要。
通过长期实践证明,改变钻头的几何参数与形状,是提高钻削效率、保证钻孔质量、提高钻头耐用度的有效途径。
钻削难切削材料时,要选择较低的切削速度,较大的进给量为好,有利于提高钻头耐用度。
(4)选用以冷却性能好的切削液。
切削难切削材料的切削温度比切削45钢在相同条件下高100℃~300℃。
为了降低钻削温度,钻孔时必需使用切削液。
9 在台钻上钻小孔时用肥皂润滑
在台钻上钻孔时,若采用液体润滑液,液体润滑液在钻头旋转离心力的作用下,不仅污染环境,而且还会弄脏操作者的衣服。
为此,工人采用肥皂做固体润滑,效果十分好。
方法是在钻孔时,将肥皂涂在旋转的钻头上。
进几次刀,再涂抹一次。
窗体底端。