格力精益改善周成功案例
精益改善案例ppt课件

刀片夹板
绝缘胶带缠绕完成用刀片切断,刀片裸露,存在重大安全 隐患。
刀片内陷,减少安全隐患。
5
隔板循环使用
主体车的隔层垫板需循环利用,放置在架子上,占用场地。
在主体车上安装垫板托架,垫板放置方便,随车流动,方 便循环周转。
6
防止磁块漏装
客户反馈磁块多次漏安装。
从源头改善,制作工装,磁块单个弹出,方可用角铁拉杆铺设通道,货架 背靠背放置,减少铺设通道数量。
14
线路测试改善
手挡
欠 品
放置架
放置架 车附件
组装好线束需进行测试: 1、连接导线与线束都在桌面,凌乱。 2、寻找对应连接插座 3、车灯、手档未固定,操作不便。
插头
将连接线插座固定在桌面,并标明标识。 1、可以双手同时插插头。 2、减少寻找动作。 3、桌面整齐。
10
弯头安装
冷凝器需安装较多弯头,工作量大,在安装时参照图纸, 生产效率低,且有插错的品质不 良发生。
安装正确
安装错误 模板取不出
根据各品种制作简易对照模板,安装弯头前套入,免去安 装时对照图纸,提升作业效率。
在安装错误时,安装模板取不出,防止安装错误,保证产 品品质.
11
小物料拿取
垫片类物料拿取困难,效率低。
1
相互伤害
停车位区域划线
单线间隔,停车间距不好把握,开门易磕碰车身。
双线间隔,预留安全空隙,防止车门碰伤,促进和谐。 2
线体布局
横向走动作业,物流线路长。
流水线传送,由走动作业递减为转身作业。 3
夹具快速装卸
夹具装卸使用手拧螺丝。
螺丝上焊接把手,方便快捷。 或小气缸、快速夹。
4
刀片安全隐患
精益生产-改善项目案例

1、”三天不变”刚性计划; 2、当天作业实物配套率提升;
(重点为恰时供货物料改善) 3、作业尾数快速补货流程; 4、自制件在制品库存降低;
工作 思路
➢月度意向计划准确率提升; ➢规范各类订单下周频率、周期; ➢紧急订单关键资源评审机制;
➢月意向计划准确率 ➢月度订单下达次数 ➢月度订单接单率
➢建立长物料储备订单完成率监控 ➢长线物料当天作业配套率提升; ➢总装物料异常损失时间降低 ➢供方异常停产追溯;
原材料成本上升,铜等大宗材 料行情波动大,成本压力大
柜机产品市场表现不足
工厂生产效率提升优势显著!
3
项目章程
4
项目CTQ
根据2011年事业本部效率提升工作围绕月度总量与人员开展的要求,设定:
97.35套/人
70.37套/人
2010实际 2011目标
项目范围: 项目通过推进精益生产,减少生产制造全流程内的浪费,有效减少作业
最终达到制冷集团生产效率精益化管理,保持制造成本领先优势,持续满足客 户需求!!!
5
项目开展思路 工厂生产效率提升
Y1
生产组织模式变革:
1. 订单体系优化 2. 供应保障体系改善 3. 制造模式变革
Hale Waihona Puke Y2制造技术优化:
1. 减员: 管理优化 产品工艺优化 生产扶持
2、增效: 消除浪费
Y3
物流效率提升:
精益生产-改善项目案例
2020年7月17日星期五
项目背景 空调本部10年月人均产出实际达成情况
截止12月30日,各工厂月人均产出(标准台)与事业部11年提升30%考核目标相距甚远。 芜湖:70.35套/人(-38.38%);武汉:68.34台/人(-45.10%);广州:100.14台/人(-25.67%)
精益管理案例分享

精益管理案例分享【实用版】目录一、精益管理概述二、精益管理案例分享1.案例一:丰田汽车公司2.案例二:海尔集团3.案例三:阿里巴巴集团三、精益管理的启示和应用正文【一、精益管理概述】精益管理是一种源于日本的先进管理理念,它的核心思想是在生产和服务过程中,通过不断地去除浪费,降低成本,提高效率和质量,从而实现企业的可持续发展。
精益管理强调全员参与、全程管理、全面优化,追求“零浪费、零缺陷、零停滞”。
【二、精益管理案例分享】1.案例一:丰田汽车公司作为精益管理的典范,丰田汽车公司通过实施精益管理,成功降低了生产成本,提高了生产效率,从而在激烈的市场竞争中脱颖而出。
丰田公司采用准时生产制、持续改进流程、消除浪费等方法,全面推行精益管理,取得了显著的效果。
2.案例二:海尔集团海尔集团是我国实施精益管理的一个成功案例。
海尔通过引入精益管理理念,进行生产流程再造,优化供应链管理,提高了企业的竞争力。
此外,海尔还通过实施全员绩效管理,激发员工的积极性和创造力,为企业的发展注入了新的活力。
3.案例三:阿里巴巴集团阿里巴巴集团在实施精益管理方面也取得了显著的成绩。
阿里巴巴通过优化内部流程,提高工作效率,实现了快速响应客户需求的目标。
同时,阿里巴巴还运用大数据技术,进行精准营销,降低了成本,提高了企业的盈利能力。
【三、精益管理的启示和应用】精益管理的成功案例为我们提供了很多有益的启示。
首先,企业应该树立全员参与的理念,让每一个员工都参与到精益管理的实践中来。
其次,企业应该注重流程优化,通过去除浪费,提高工作效率。
最后,企业应该运用先进的管理工具和技术,如大数据、云计算等,实现精益管理的智能化。
格力数字化应用案例
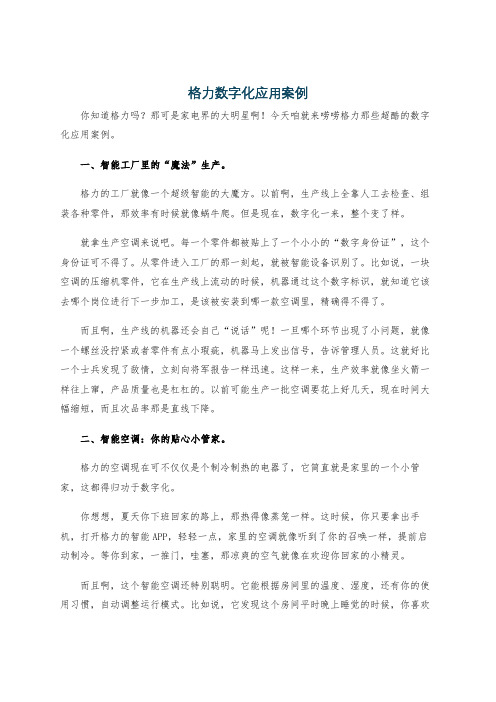
格力数字化应用案例你知道格力吗?那可是家电界的大明星啊!今天咱就来唠唠格力那些超酷的数字化应用案例。
一、智能工厂里的“魔法”生产。
格力的工厂就像一个超级智能的大魔方。
以前啊,生产线上全靠人工去检查、组装各种零件,那效率有时候就像蜗牛爬。
但是现在,数字化一来,整个变了样。
就拿生产空调来说吧。
每一个零件都被贴上了一个小小的“数字身份证”,这个身份证可不得了。
从零件进入工厂的那一刻起,就被智能设备识别了。
比如说,一块空调的压缩机零件,它在生产线上流动的时候,机器通过这个数字标识,就知道它该去哪个岗位进行下一步加工,是该被安装到哪一款空调里,精确得不得了。
而且啊,生产线的机器还会自己“说话”呢!一旦哪个环节出现了小问题,就像一个螺丝没拧紧或者零件有点小瑕疵,机器马上发出信号,告诉管理人员。
这就好比一个士兵发现了敌情,立刻向将军报告一样迅速。
这样一来,生产效率就像坐火箭一样往上窜,产品质量也是杠杠的。
以前可能生产一批空调要花上好几天,现在时间大幅缩短,而且次品率那是直线下降。
二、智能空调:你的贴心小管家。
格力的空调现在可不仅仅是个制冷制热的电器了,它简直就是家里的一个小管家,这都得归功于数字化。
你想想,夏天你下班回家的路上,那热得像蒸笼一样。
这时候,你只要拿出手机,打开格力的智能APP,轻轻一点,家里的空调就像听到了你的召唤一样,提前启动制冷。
等你到家,一推门,哇塞,那凉爽的空气就像在欢迎你回家的小精灵。
而且啊,这个智能空调还特别聪明。
它能根据房间里的温度、湿度,还有你的使用习惯,自动调整运行模式。
比如说,它发现这个房间平时晚上睡觉的时候,你喜欢温度稍微高一点,那到了晚上,它就会悄悄地把温度调整到你习惯的那个舒适区间。
这就像你有一个特别懂你的小助手,不用你操心,它就把一切都安排得妥妥当当的。
还有哦,如果空调的滤网该清洗了,它也会在APP上给你发个小提示,就像在说:“主人主人,我有点脏啦,该给我洗个澡啦。
”这多贴心啊。
知名企业文化理念案例

知名企业文化理念案例联想集团1、企业定位• 联想从事开发、制造及销售最可靠的、安全易用的技术产品。
• 我们的成功源自于不懈地帮助客户提高生产力,提升生活品质。
2、使命•为客户利益而努力创新• 创造世界最优秀、最具创新性的产品• 像对待技术创新一样致力于成本创新• 让更多的人获得更新、更好的技术• 最低的总体拥有成本(TCO),更高的工作效率3、核心价值观• 成就客户—我们致力于每位客户的满意和成功。
• 创业创新—我们追求对客户和公司都至关重要的创新,同时快速而高效地推动其实现。
• 诚信正直—我们秉持信任、诚实和富有责任感,无论是对内部还是外部。
• 多元共赢—我们倡导互相理解,珍视多元性,以全球视野看待我们的文化。
西门子公司1、价值观勇担责任致力于符合道德规范的、负责任的行为西门子努力满足一切法律和道德要求,并且,只要可能,我们还努力超越这些要求。
我们的责任是按照最高的职业和道德标准和惯例来开展业务:公司绝不容忍任何不合规的行为。
我们在“勇担责任”方面的原则堪称我们制定业务决策的指南针。
我们还必须鼓励我们的商业伙伴、供应商和其他利益相关者遵循同样高的道德标准。
追求卓越取得卓越的业绩和运营成果追求卓越,是我们在每个领域都将尽力实现的目标。
我们根据公司愿景制定这一远大目标,并在其指引下提供优异的质量及超越客户需求的解决方案。
一直如此。
追求卓越还意味着吸引市场上最优秀的人才。
我们将帮助这些人才掌握获得成功所需的各种技能,给他们提供发挥潜力的绝佳机会。
我们致力于营造一种高绩效企业文化。
追求卓越不仅仅关系到我们今天所做的一切,它还要求我们找到一条持续改善的道路。
这需要我们灵活、积极地迎接变革,从而确保我们能够牢牢把握新的机遇。
矢志创新敢于创新,创造可持续的价值创新就已成为西门子业务成功的基石。
研发是西门子发展战略的基本动力。
作为关键专利的持有者,无论是已经成熟的工艺,还是正在发展的技术,我们都是客户强有力的合作伙伴。
主机厂质量问题改善方案的成功案例与启示
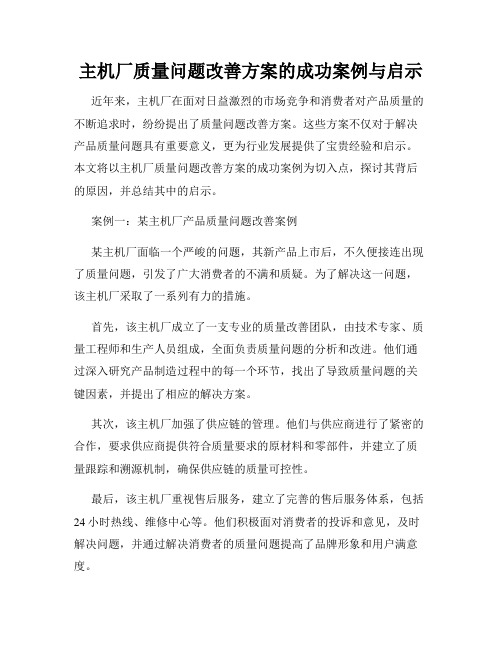
主机厂质量问题改善方案的成功案例与启示近年来,主机厂在面对日益激烈的市场竞争和消费者对产品质量的不断追求时,纷纷提出了质量问题改善方案。
这些方案不仅对于解决产品质量问题具有重要意义,更为行业发展提供了宝贵经验和启示。
本文将以主机厂质量问题改善方案的成功案例为切入点,探讨其背后的原因,并总结其中的启示。
案例一:某主机厂产品质量问题改善案例某主机厂面临一个严峻的问题,其新产品上市后,不久便接连出现了质量问题,引发了广大消费者的不满和质疑。
为了解决这一问题,该主机厂采取了一系列有力的措施。
首先,该主机厂成立了一支专业的质量改善团队,由技术专家、质量工程师和生产人员组成,全面负责质量问题的分析和改进。
他们通过深入研究产品制造过程中的每一个环节,找出了导致质量问题的关键因素,并提出了相应的解决方案。
其次,该主机厂加强了供应链的管理。
他们与供应商进行了紧密的合作,要求供应商提供符合质量要求的原材料和零部件,并建立了质量跟踪和溯源机制,确保供应链的质量可控性。
最后,该主机厂重视售后服务,建立了完善的售后服务体系,包括24小时热线、维修中心等。
他们积极面对消费者的投诉和意见,及时解决问题,并通过解决消费者的质量问题提高了品牌形象和用户满意度。
通过以上措施的实施,该主机厂成功地解决了产品质量问题,恢复了消费者的信任和市场竞争力。
从这一案例中,我们可以得到以下启示:一、建立质量改善团队是关键。
主机厂需要拥有一支专业的团队,负责从产品设计到生产制造的全过程质量控制,通过科学的数据分析和问题解决方法,找出质量问题的根源并提出改进策略。
二、加强供应链的管理是必要的。
供应链的每个环节都可能对产品质量造成潜在影响,主机厂应与供应商建立紧密的合作关系,确保原材料和零部件的质量可控,并建立质量跟踪和溯源机制。
三、注重售后服务的建设。
主机厂需要建立完善的售后服务体系,通过提供便捷的维修渠道和及时解决消费者的问题,提高品牌形象和用户满意度。
格力电器质量管理案例分析展示
质量管理成果
• 2013年售后故障率下降了25.2%,2014年售后故障率下降了27.8%。 • 格力电器凭借“T9全面质量控制模式的构建与实施”项目获得中 国质量协会质量技术奖一等奖。格力电器T9全面质量控制模式是 一种以用户需求为导向,以“检验触发”为核心,以追求零缺陷 完美质量为目标,结合6、TSQ工具的系统性运用,构建并实施的 创新质量控制模式。 • 先后获得“全国质量管理先进企业”、“全国质量奖”、“全国 质量工作先进集体”、“出口免检”等多项质量领域的顶级荣誉。
质量管理核心
一.创新质量管理体系 标准 管理 筛选 分厂 科技 部 质量 管理 试制 控制 部 中心 部
全员 质量 质量 厂长 制度 质量 制度 部长 制度
质量管理核心
二.高层领导,全员参与,从上而下培养质量意识。
总裁令
QC小组 质量月
。。。。
质量管理核心
三.动态更新质量技术标准 1995年开始推行ISO9000质量管理体系 1996年获得ISO9001质量管理体系认证证书。 2004年通过SGS国际认证服务公司认证审核。 2006年公司获得国家质监总局颁发的特种 设备制造许可证(压力容器)。 。。。。。。大赛
铜管焊接技能赛
《我的质量梦》主题演讲、质量征文(漫画)比赛、质量标兵评选、质量信得过班组评 选等;全员质量知识普及通过质量月主题活动的开展,激发了员工的工作热情,树立了 全员的质量意识,营造人人讲质量、重改善的良好氛围,提升了质量管理成熟度
强大的生产能力
• “好空调,格力造”一流的生产环境,一流的生产线,一流的生 产工艺。在不断地进取开拓中始终贯彻"一流"的原则,格力的生 产工艺将始终走在国际前列,为质量管理目标的实现奠定基础。
精益案例【79期】某乳业集团冷饮事业部产线快速清洗改善周总结
精益案例【79期】某乳业集团冷饮事业部产线快速清洗改善周总结该集团由液态奶、冷饮、奶粉、酸奶和原奶五大事业部组成,全国所属分公司及子公司130多个,在近50年的发展过程中,集团始终致力于生产100%安全、100%健康的乳制品,输出最适合中国人体制的营养和健康理念,并以世界最高的生产标准为消费者追求健康体魄和幸福生活服务。
集团冷饮事业部是目前国内最大、产品线最健全的冰激凌制造商,在全国多出设有生产基地,产品连续多年全国销量领先。
成都工厂作为集团冷饮事业部TPOS(Total Productive Optimization System,全员生产优化系统)精益推进体系的试点公司,在2012年-2013年进行了第一步精益管理尝试,2012年以专项改善为切入点,建立人员改善的意识,营造改善氛围,培养初级改善人才;2013年在维持2012年成果的基础上,尝试开展绩效提升项目,通过建立、完善标准作业并点检标准的建立与执行,促进绩效标准的提升,建立全员改善的文化,实现冷饮行业的精益生产系统。
一、改善周概要针对产品A生产线清洗时间长,限制生产产能问题,公司决定开展产品A线快速清洗改善周活动,期望降低清洗时间,提高产能。
在五天改善周过程中,改善团队基于快速换模SMED和团队作业甘特图这两个核心工具,按照区分清洗内外部作业、将内部清洗作业转换为外部清洗作业、压缩内外部清洗作业时间的工作思路,通过一些列的改善活动,取得了清洗时间降低30%的突破性改善成果。
二、改善周开展过程冷饮制造作为食品行业,由于工艺环境和卫生安全的特殊要求,每天开机生产前产线清洗是一项必要工作,这类似于生产线换产,因此对于降低清洗时间,快速换模SMED自然就成为了核心工具。
项目团队按照理论知识学习-现场诊断-对策制定-对策实施-标准作业的工作路线,首先是顾问老师培训SMED快速准备理论知识,让团队成员掌握内外部作业的概念以及快速准备的改善步骤,紧接着开始现场诊断,用团队作业表记录所有作业员的每一项作业内容和时间,同时基于产线布局图绘制作业意粉图,作为后续改善的依据,同时基于价值/浪费视角识别清洗作业中的所有问题点,汇总成改善新闻报,现场诊断后,输出现状清洗甘特图、岗位工具清单、改善新闻报、意粉图。
案例七 格力空调的专业化经营决策案例
案例七格力空调的专业化经营决策案例多元化经营在20世纪60年代风靡全球,认为多元化能分散风险,东方不亮西方亮。
然而,随着一个个公司的衰落,到了20世纪80年代,世界又回归到核心竞争的时代。
格力集团就是集中兵力,打拳头产品的家电企业。
在中国的家电产业里,格力集团是一个很有特色的企业。
第一,该公司从其成立之日起,就将空调作为主要经营业务,而且只限于做家用空调,不生产中央空调、汽车空调等。
第二,该公司进入空调时间较晚,当时春兰、华宝、美的等一批国内企业已经崛起,在市场份额与晶牌声誉等方面占有了很大优势。
第三,目前家电产业的许多公司出于分散风险、迅速扩张等原因,纷纷开展多元化经营,但格力集团仍然坚持专业化经营。
一、格力选择了专业化经营战略格力电器是中国惟一一家坚持专一化经营战略的大型家电企业。
长期以来,经济界、营销界、企业管理界有一些人对格力坚持专一化经营战略持否定态度。
但是,肯定也好,指责也罢,最近出版的著名国际财经杂志美国《财富》中文版揭晓的消息表明:作为我国空调行业的领跑企业,格力电器股份以7.959亿美元的营业收入、 0.33亿美元的净利润,以及6.461亿美元的市值等,再次荣登该排行榜第46位,入选《财富》“中国企业百强”。
成为少数连续两年进入该排行榜的家电企业之一。
不仅多项财务指标均位居家电企业前列,而且在2002年空调市场整体不景气的情形下,格力空调的销售实现了稳步增长,销量增幅达20%,销售额和净利润均有不同程度地提高,取得了良好的经济效益,充分显示了专一化经营的魅力。
(一)专业化战略是“一篮子鸡蛋”的战略吗?美国哈佛大学商学研究院著名教授,对于企业竞争战略理论做出了非常重要贡献的迈克尔·波特在他具有重要影响和贡献的《竞争战略》一书中明确地提出了三种适用的竞争战略,即:总成本领先战略、差异化战略和专一化战略。
专一化战略是一个重要的企业竞争战略。
波特认为:“这些战略类型的目标是使企业的经营在产业竞争中高人一筹”,尽管有时企业追逐的基本目标可能不止一个,但他认为:“这种情况实现的可能性是很小的。
品质改善分段控制案例
品质改善分段控制案例家电公司是一家专注于生产和销售电视机的企业,由于市场竞争激烈,品牌知名度较低,公司决定通过提升产品质量来赢得市场份额。
他们采取了品质改善分段控制的方法来逐步提高产品的品质和服务水平。
首先,公司对产品进行了全面的品质分析。
他们从产品设计、制造过程、原材料、配件等多个方面进行了详细的调研和分析,找出了当前产品存在的问题和不足之处。
通过品质分析,公司确定了需要改进和提高的关键指标,例如产品的分辨率、色彩还原度、屏幕亮度等。
接下来,公司制定了一套具体的品质改善控制计划。
他们根据产品分析结果,将品质改善目标分阶段确定。
在第一阶段,公司将集中精力改善产品外观和基本功能,以提高用户的第一印象。
在第二阶段,公司将着重改善产品的核心技术和性能,以提高产品的品质竞争力。
在第三阶段,公司将关注产品的细节和用户体验,以打造高品质的产品和服务。
在实施过程中,公司采取了一系列措施来控制品质改善的进程。
首先,他们加强了对供应商的管理和合作,选择优质的原材料和配件供应商,以确保产品的材料质量。
其次,公司加强了对生产过程的监控,采用先进的生产设备和技术,建立了一套严格的品质控制流程,确保产品的加工和制造过程符合标准。
此外,公司还加强了对产品的检测和测试,建立了一套完善的品质检测体系,确保产品的功能和性能符合预期。
最后,公司注重了对用户反馈和投诉的收集和分析,通过不断改善产品和服务,逐步提高用户满意度。
经过一段时间的努力,公司逐步实现了品质改善,并取得了显著的效果。
首先,产品的外观和基本功能得到了大幅改善,用户对产品的第一印象有了明显的提升,销量和市场份额逐步增加。
其次,产品的核心技术和性能也得到了大幅提升,产品在市场上与竞争对手的差距逐步缩小,用户满意度和品牌知名度不断提高。
最后,产品的细节和用户体验也得到了改善,用户反馈和投诉数量明显减少,公司形象得到了进一步塑造。
综上所述,品质改善分段控制是一种有效的管理方法,可以帮助企业逐步提高产品和服务的品质水平。