精益改善案例提案改善报告
工厂精益改善提案案例

工厂精益改善提案案例
嘿,大家好呀!今天我要给你们讲讲咱工厂的精益改善提案案例,这可真的是超有意思呢!
还记得之前我们生产线上那堆零件总是乱七八糟地放着吗?就跟被调皮孩子弄乱的玩具一样!这多耽误事儿啊,找个零件都得老半天,那生产效率能高吗?不行,咱得想办法改善呀!于是呢,我们几个小伙伴就凑在一起商量,这不就是人多力量大嘛!我就说:“咱能不能弄个专门的架子把零件分类放好呀?”大家一听,觉得这主意不错。
说干就干,我们找来了材料,动手做起了架子。
嘿,你还别说,等架子做好一摆上,那场面,一下子就变得整洁有序多啦!就好像原本乱糟糟的房间被好好整理了一番,瞬间清爽了。
这之后找零件可轻松多了,生产效率那也是蹭蹭往上涨啊!
还有一次,我们发现有些工序之间衔接不畅,就像交通堵塞一样,这不就影响整体速度了嘛!我们就类比成跑步比赛,中间卡顿一下,那还怎么拿好成绩呀!于是,我们重新设计了流程,让各个工序像接力赛一样顺畅地交接。
结果呢,哇塞,那效果简直绝了!
工厂的精益改善真的能带来好多惊喜啊!这就像给工厂注入了新活力,让它能更好地运转起来。
所以呀,大家都要积极行动起来,一起为工厂的精益改善出谋划策,让我们的工厂越来越好!怎么样,是不是觉得很有意思呀?快来一起加入吧!。
精益现场改善提案工作总结
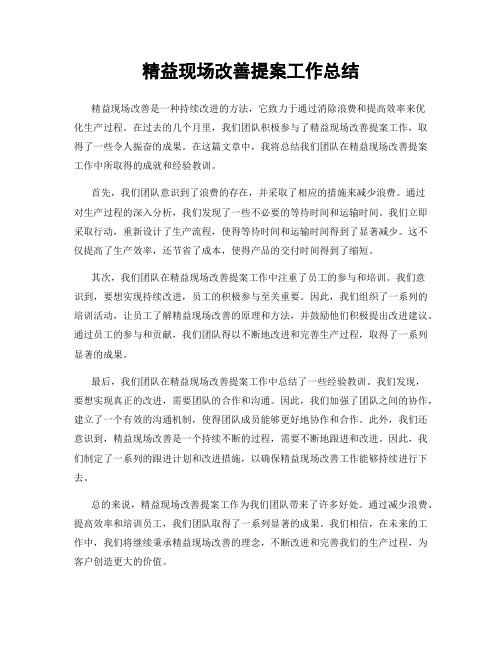
精益现场改善提案工作总结精益现场改善是一种持续改进的方法,它致力于通过消除浪费和提高效率来优化生产过程。
在过去的几个月里,我们团队积极参与了精益现场改善提案工作,取得了一些令人振奋的成果。
在这篇文章中,我将总结我们团队在精益现场改善提案工作中所取得的成就和经验教训。
首先,我们团队意识到了浪费的存在,并采取了相应的措施来减少浪费。
通过对生产过程的深入分析,我们发现了一些不必要的等待时间和运输时间。
我们立即采取行动,重新设计了生产流程,使得等待时间和运输时间得到了显著减少。
这不仅提高了生产效率,还节省了成本,使得产品的交付时间得到了缩短。
其次,我们团队在精益现场改善提案工作中注重了员工的参与和培训。
我们意识到,要想实现持续改进,员工的积极参与至关重要。
因此,我们组织了一系列的培训活动,让员工了解精益现场改善的原理和方法,并鼓励他们积极提出改进建议。
通过员工的参与和贡献,我们团队得以不断地改进和完善生产过程,取得了一系列显著的成果。
最后,我们团队在精益现场改善提案工作中总结了一些经验教训。
我们发现,要想实现真正的改进,需要团队的合作和沟通。
因此,我们加强了团队之间的协作,建立了一个有效的沟通机制,使得团队成员能够更好地协作和合作。
此外,我们还意识到,精益现场改善是一个持续不断的过程,需要不断地跟进和改进。
因此,我们制定了一系列的跟进计划和改进措施,以确保精益现场改善工作能够持续进行下去。
总的来说,精益现场改善提案工作为我们团队带来了许多好处。
通过减少浪费、提高效率和培训员工,我们团队取得了一系列显著的成果。
我们相信,在未来的工作中,我们将继续秉承精益现场改善的理念,不断改进和完善我们的生产过程,为客户创造更大的价值。
精益改善案例
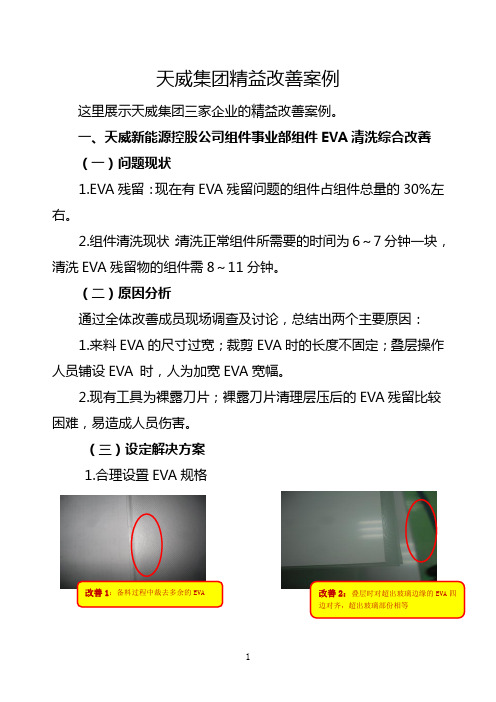
天威集团精益改善案例这里展示天威集团三家企业的精益改善案例。
一、天威新能源控股公司组件事业部组件EVA清洗综合改善(一)问题现状1.EVA残留:现在有EVA残留问题的组件占组件总量的30%左右。
2.组件清洗现状:清洗正常组件所需要的时间为6~7分钟一块,清洗EVA残留物的组件需8~11分钟。
(二)原因分析通过全体改善成员现场调查及讨论,总结出两个主要原因:1.来料EVA的尺寸过宽;裁剪EVA时的长度不固定;叠层操作人员铺设EVA 时,人为加宽EVA宽幅。
2.现有工具为裸露刀片;裸露刀片清理层压后的EVA残留比较困难,易造成人员伤害。
(三)设定解决方案1.合理设置EVA规格2.利用有效的EVA清除工具(四)改善效果通过实施改善:EVA残留率下降到3%以下。
改善前,EVA残留组件平均清洗时间为3分钟,改善后,EVA残留组件平均清洗时间仅为1分钟,下降率达67%。
(五)项目综合效益降低EVA残留组件比例达27%,同时节省了清洗小组清理EVA的时间。
若层压没有EVA残留组件流下去,则每清洗小组(俩人组)可节约0.7小时,6小组可节约4.2小时。
按人均60块/小时产量计算,4.2小时可多清洗252块组件。
按2小组班产量252块组件计算,可以减少4人。
按每人2400元/月工资计算,两组四人约2400*4=9600元/月,可节约成本115200元/年。
二、天威保变公司库房U型布局改善案例介绍天威保变根据本单位实际,把精益生产中U型工作线方式原则,灵活的运用到库房物流管理中去,改变横排多列的货架摆放方式;利用物料配套带来的托盘,采取单排货架加托盘的方式,可减少配套人员取货时的多次折返和物料寻找时间,也便于物料的清点,实现库房内部物料的可视化管理。
具体案例分析如下:(一)案例问题分析机电库内存放着公司内产品使用的大量物料。
包括变压器成品所需保护装置的仪器、仪表,蝶阀、球阀等进口(国产)重要物资。
配套工序涉及总装车间的一次装配、二次装配、冷却器装配、装齐件、备品备件等五、六道工序。
食堂精益改善提案案例
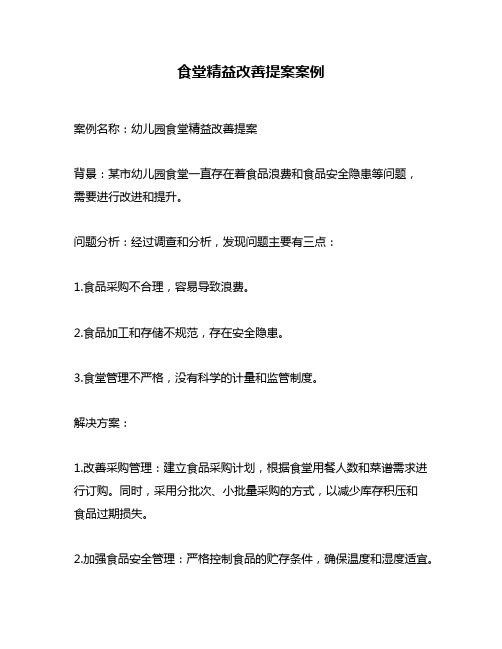
食堂精益改善提案案例案例名称:幼儿园食堂精益改善提案背景:某市幼儿园食堂一直存在着食品浪费和食品安全隐患等问题,需要进行改进和提升。
问题分析:经过调查和分析,发现问题主要有三点:1.食品采购不合理,容易导致浪费。
2.食品加工和存储不规范,存在安全隐患。
3.食堂管理不严格,没有科学的计量和监管制度。
解决方案:1.改善采购管理:建立食品采购计划,根据食堂用餐人数和菜谱需求进行订购。
同时,采用分批次、小批量采购的方式,以减少库存积压和食品过期损失。
2.加强食品安全管理:严格控制食品的贮存条件,确保温度和湿度适宜。
同时,要求食品加工人员进行培训和考核,以保证加工和烹饪的安全和卫生。
3.完善计量和监管制度:建立食品使用记录和库存盘点制度,规范食品使用和管理。
同时,设置食品损耗率的指标,对食品浪费情况进行监管和控制。
成果和效益:经过实施改善方案,幼儿园食堂取得了明显的成果和效益:1.食品浪费率明显降低:根据采购计划订购食品,加强食品管理,避免了食品浪费的情况。
2.食品安全得到了保障:规范食品加工和存储,有效避免了食品安全隐患。
3.食堂管理更加规范:建立计量和监管制度,实现了对食品使用情况的有效控制。
结论:幼儿园食堂精益改善提案的实施,有效地解决了食品浪费和食品安全隐患等问题,提高了食堂的管理水平和服务质量,受到了家长和幼儿的好评。
接着上面的内容,我们将根据提案中的三个重点问题进行分析和解决方案的提出。
## 问题一:餐具消毒不彻底为解决餐具消毒不彻底的问题,我们建议采取以下措施:1. 对餐具进行定期维护和清洁,包括消毒设备、清洗设备和餐具。
2. 定期更换消毒设备和餐具清洗设备中的滤网,并定期对设备进行保养和维修。
3. 建立日常检查和记录制度,记录餐具消毒情况和设备维护情况。
## 问题二:食材质量不过关为解决食材质量不过关的问题,我们建议采取以下措施:1. 与供应商建立稳定的合作关系,并要求供应商提供有关食材的相关证明文件。
精益改善案例

精益改善案例某公司生产线的产品存在质量问题,经过分析发现,主要原因是制程中存在一些不合理的环节和操作不规范的问题。
于是公司决定进行精益改善,以下是改善过程的案例。
首先,公司进行现场调查,了解每个环节的具体操作流程和问题所在。
通过观察和采访,发现生产线上存在很多浪费的环节,比如物料的搬运和存储浪费、操作流程不规范导致的错工错料等。
调查结果表明,这些问题严重影响了产品质量的稳定性和生产效率。
在调查的基础上,公司开始制定改善计划。
首先,对物料的存储和搬运进行优化。
通过调整仓库布局和材料的摆放顺序,缩短了从仓库到生产线的距离,减少了搬运时间和能量消耗。
同时,引入物料盘点管理系统,有效避免了物料的过期和损耗问题。
其次,对操作流程进行规范化。
通过标准化操作流程,减少人为因素对产品质量的影响。
采用可视化管理的方法,对员工进行培训和指导,确保操作规范的贯彻执行。
此外,通过控制生产环境的温湿度等因素,减少外界因素对产品质量的干扰。
再次,公司提供培训和技术支持,改善员工的技能水平和生产能力。
通过定期培训和知识分享会,提高员工的操作技能和质量意识。
此外,鼓励员工提供改善建议,并给予奖励以鼓励员工参与到精益改善中来。
最后,公司建立了一个持续改进的机制。
成立了质量改进小组,定期召开改进汇报会,评估改善效果并提出新的改进方案。
公司将改善思想和方法融入到企业文化中,鼓励每个员工积极参与到改善工作中。
经过以上的改进措施,公司生产线的产品质量得到了明显提升。
产品的不良率从10%下降到3%,生产效率也提高了20%。
公司的品牌形象得到了改善,客户满意度和市场份额也逐渐提升。
在这个案例中,公司通过精益改善的方法解决了生产线上存在的质量问题。
通过调查分析、制定改善计划、培训员工和建立持续改进机制,公司取得了显著的改进效果。
这个案例证明了精益思想和方法对企业的生产和管理是有积极作用的。
精益改善 优秀提案成果展示
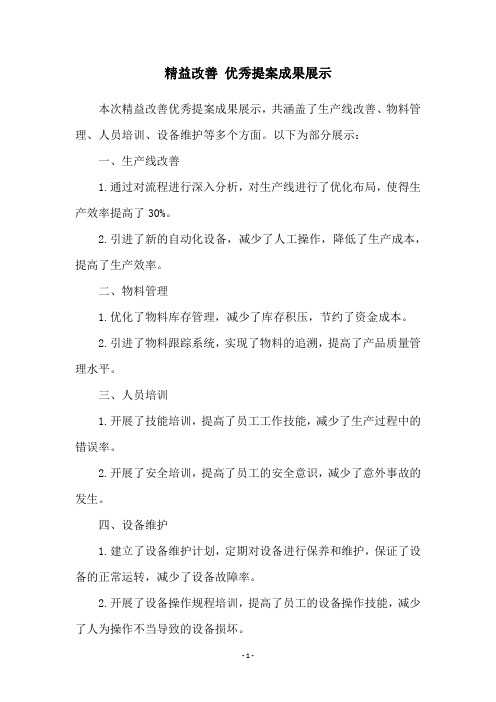
精益改善优秀提案成果展示
本次精益改善优秀提案成果展示,共涵盖了生产线改善、物料管理、人员培训、设备维护等多个方面。
以下为部分展示:
一、生产线改善
1.通过对流程进行深入分析,对生产线进行了优化布局,使得生产效率提高了30%。
2.引进了新的自动化设备,减少了人工操作,降低了生产成本,提高了生产效率。
二、物料管理
1.优化了物料库存管理,减少了库存积压,节约了资金成本。
2.引进了物料跟踪系统,实现了物料的追溯,提高了产品质量管理水平。
三、人员培训
1.开展了技能培训,提高了员工工作技能,减少了生产过程中的错误率。
2.开展了安全培训,提高了员工的安全意识,减少了意外事故的发生。
四、设备维护
1.建立了设备维护计划,定期对设备进行保养和维护,保证了设备的正常运转,减少了设备故障率。
2.开展了设备操作规程培训,提高了员工的设备操作技能,减少了人为操作不当导致的设备损坏。
以上是部分展示,我们将继续在精益改善的道路上前行,不断提升生产效率和产品质量,为客户提供更好的产品和服务。
精益改善 优秀提案成果展示
精益改善优秀提案成果展示介绍在当今竞争激烈的商业环境中,企业持续改进是取得成功的关键。
精益改善是一种管理理念和方法论,旨在通过减少浪费和提高效率来提高组织的绩效。
本文将展示一些优秀的精益改善提案成果,旨在为读者提供灵感和指导。
二级标题1:提案一三级标题1.1:问题识别在我们的生产流程中,我们发现每天浪费了大量的时间和资源在废品处理上。
这导致了不必要的成本和生产效率低下。
三级标题1.2:改进方法我们采取了一系列的措施来减少废品产生并提高生产效率。
首先,我们进行了流程分析,找出了造成废品的主要原因。
然后,我们通过改善工艺和培训员工的方式,减少了废品的数量。
最后,我们引入了一套全新的质量管理系统,以确保每个生产环节都符合高标准。
三级标题1.3:成果展示经过这些改进措施的实施,我们成功地减少了废品的数量,并提高了生产效率。
我们的废品率从每天10%降低到了每天2%。
此外,我们的生产周期也缩短了30%,使我们能够更快地响应客户需求。
二级标题2:提案二三级标题2.1:问题识别我们的供应链面临一些挑战,导致了交付延迟和库存积压的问题。
这严重影响了我们的客户满意度和利润。
三级标题2.2:改进方法我们采取了一系列的措施来改善供应链管理。
首先,我们与供应商建立了更紧密的合作关系,以确保及时交付。
其次,我们优化了物流和仓储管理,以减少库存积压。
最后,我们建立了一套供应链监控系统,及时发现并解决问题。
三级标题2.3:成果展示通过这些改进措施,我们成功地缩短了交付周期,并减少了库存积压。
我们的交付准时率提高了20%,库存周转率提高了15%。
这使我们能够更好地满足客户需求,同时降低了库存成本。
二级标题3:提案三三级标题3.1:问题识别我们的员工倦怠感越来越严重,导致生产力下降和员工离职率上升。
三级标题3.2:改进方法为了解决员工倦怠问题,我们采取了一系列的措施。
首先,我们改善了工作环境,提供更好的工作条件和设施。
其次,我们重视员工培训和发展,提供更多的学习机会和晋升渠道。
精益生产:公司生产效率提升改善项目报告
制作夹具,简化工艺 普通焊机改为储能式焊接机,减少后工序作业
人员 手动大螺丝改为自动打螺丝
月份
6月 6月 6月 6月 6月 6月 6月 6月
10
19系列天花灯固定器改善
螺丝加固定器改为半牙螺丝,取消固定器
6月
4.过程亮点展示
4.1、98,143系列压线扣工艺改善
1.压线扣单价0.03元 ,预计每年省1万元
54229.5
线外人员出勤
3298 457 488 1528 3595.5 9366.5
UPPH 151.98 35.15 39.78 76.96
2.70 345.67
数据分析 基准值 129.30 29.97 35.21 66.33
2.30
提升比率 17.54% 17.28% 12.98% 16.02% 17.56%
确认
2
953A 670 17 498 11 477 11 6 10.07%
3
9225N 650 19 535 13 483 13 6 8.52%
4
923N 650 19 535 13 479 13 6 7.63%
组装
5
9825 530 23 424 16 402 16 7 9.21%
6
983
530 23 424 16 419 16 7 11.02%
生物颗粒
优
高效,熔炼,安全 方便,灵活,节能 低碳,环保,恒温
4.过程亮点展示
4.7、异形插件机方案拟定
改善前视频
改善后方案视频
4.过程亮点展示
4.8、筒灯自动化生产线方案确认
筒灯自动化线视频
4.过程亮点展示
精益生产改善总结报告
精益生产改善总结报告精益生产改善总结报告精益生产是一种以提高价值流动为目标的系统性方法。
它的核心原则是消除浪费,并不断改进和优化生产过程,以提高生产效率和质量,降低成本。
在过去的一段时间里,我公司积极推行精益生产改善,通过实施一系列改进措施,取得了一定的成效。
一、改进项目1. 价值流分析:通过对生产过程进行价值流分析,我们发现了一些不必要的流程和活动,如物料运输和等待时间过长等。
我们采取了一些措施,如重新布局车间和优化运输方式,以减少运输距离和运输时间,提高物料流转速度。
2. 5S管理:我们实施了5S管理,即整理、整顿、清扫、清洁和素养。
通过对生产现场的整理和整顿,我们减少了时间浪费和活动浪费,并改善了工作环境和工作效率。
3. Kaizen活动:我们组织了一些Kaizen活动,即持续改进活动。
通过员工的参与和创新意识的激发,我们发现了一些问题和瓶颈,并提出了相应的解决方案。
我们采用了一些小改进,如改进工艺流程、更换设备和优化工作布局等,以提高生产效率和质量。
二、改进成果经过一段时间的改进工作,我们取得了以下一些成果:1. 生产效率提高:通过消除浪费和优化流程,我们的生产效率提高了20%。
生产时间缩短,生产速度提升,产量增加。
这使我们能够更好地满足客户需求,并提高竞争力。
2. 质量改善:通过改进工艺和优化设备,我们的产品质量得到了提高。
产品合格率提高了10%,不良品率降低了20%。
这不仅降低了生产成本,还增强了顾客对我们产品的信任和满意度。
3. 成本降低:通过消除浪费和减少不必要的活动,我们的生产成本得到了一定的降低。
这使我们能够更好地控制成本,并提高利润空间。
4. 员工参与度提高:通过推行精益生产改善活动,我们激发了员工的参与意愿和创新意识。
员工参与度提高了,他们对工作更加积极主动,提出了很多有价值的改进意见和建议。
三、改进方向虽然我们在精益生产改善方面取得了一些成果,但仍然存在一些问题和挑战。
精益现场改善提案表范文
精益现场改善提案表范文
内容:
尊敬的领导:
我代表部门,就现场改善提出以下提案。
一、存在问题
1. 物料堆放无序,查找不便
我们部门的物料堆放没有固定位置,员工需要花费时间去不同地方找料,降低了工作效率。
2. 器具使用无序,不易查找
部门共用器具放置混乱,使用后没有放回原位,导致频繁搜索器具的时间。
3. 作业区划分不清晰,容易发生混乱
作业区没有明确的标示与划分,不同作业区域混杂,导致人员频繁走动和工具搜索。
二、改善措施
1. 设立物料固定堆放区,贴标示,定期清点。
在部门空地处划定物料专区,分类堆放物料,并贴上标示,定期核查物料。
2. 设置公共器具存放处,使用后放回原位。
在显眼位置设置公共器具架,要求使用后放回原位。
3. 对作业区进行标示划分,人员就地作业。
用标示标出不同作业区域,人员就近当前区域作业,减少走动。
三、预期效果
1. 查找物料效率提高30%
2. 查找器具效率提高20%
3. 每人无效走动减少50%
改善这些问题,可以提高部门作业效率,创建更好的工作环境。
感谢领导的支持!
此致
礼!
部门全体员工
年月日。
- 1、下载文档前请自行甄别文档内容的完整性,平台不提供额外的编辑、内容补充、找答案等附加服务。
- 2、"仅部分预览"的文档,不可在线预览部分如存在完整性等问题,可反馈申请退款(可完整预览的文档不适用该条件!)。
- 3、如文档侵犯您的权益,请联系客服反馈,我们会尽快为您处理(人工客服工作时间:9:00-18:30)。
精益改善案例提案改善报告
一、背景
我们所处的公司是一家生产化妆品的企业,由于市场竞争激烈和内部管理不足等多种原因,导致生产效率低下,产品质量不稳定,在市场上的竞争力较弱。
为此,我们决定通过精益管理的方法来对生产过程进行改善,提高生产效率和产品质量,以增强企业的市场竞争力。
二、问题定义
通过对企业生产过程的分析,我们发现以下问题:
1. 生产过程中存在大量浪费,如原料浪费、等待时间浪费、生产线下停机时间浪费等,导致生产效率低下;
2. 生产线某些工站出现了制造不良品的情况,存在质量问题;
3. 生产过程中缺乏可视化管理,员工难以及时发现和解决问题。
三、改善方案
针对上述问题,我们提出以下改善方案:
1. 实施6S管理
6S管理是指整理、整顿、清洁、清点、标准化和维护的管理方法,通过对现场进行整理、清理、标识等操作,去除生产过程中的浪费,提高生产效率。
同时,开展6S培训,增强员工的职业素养和安全意识,营造整洁有序的工作环境,提高工作效率和生产质量。
2. 引入可视化管理
针对生产过程中缺乏可视化管理的问题,我们将引入可视化管理技术,将生产过程中的各项数据实时呈现在生产线上方的显示屏上,让员工随时了解生产状况,更好地发现和解决问题。
3. 实施质量管理和问题解决
在生产过程中,存在不良品生成的情况,我们将加强质量管理,对生产过程中的各项质量参数进行监控和检测,及时发现和解决问题。
同时,我们将建立定期例会和工作汇报机制,及时解决员工工作中遇到的问题,为员工提供更好的工作支持。
四、实施计划
通过培训,将6S管理理念传递至员工,开展整理、整顿、清洁等活动,打造整洁有序的生产环境,提高生产效率和产品质量。
引入并实施可视化管理系统,打造实时监控的全新生产模式,加强员工生产意识和工作效率,实现生产流程信息和数据的可视化和透明化。
五、效果预期
通过精益管理的方法,我们期望实现以下效果:
1. 生产效率提高:通过实施6S管理和改善流程,去除浪费,提高生产效率,降低生产成本。
2. 产品质量提升:通过加强质量管理,提高生产过程中产品的准确性和一致性,保障产品质量。
4. 员工工作效率提升:通过培训,营造整洁有序的工作环境,提高工作效率和生产质量,增加员工的职业素养和安全意识。
六、结论
本次改善方案的实施,将有效提高企业的生产效率、产品质量和员工工作效率,有利于企业加强市场竞争力,满足客户的需求和要求。
同时,这也是企业推行精益改善管理的必要性之一,希望通过不断地改进和提高,将企业的核心价值不断提升,使之成为业界的佼佼者。