铸造工艺守则
铸造工艺操作守则

铸造工艺守则目录3…………………………………………总则4…………………………………………混砂4…………………………………………造型6…………………………………………泥芯8…………………………………………烘型9…………………………………………配箱10………………………………………浇注11………………………………………清砂11………………………………………切割11………………………………………焊补12………………………………………整理13………………………………………脱蜡13………………………………………焙烧14………………………………………热处理15………………………………………熔炼总则本守则适用于铸钢件一般性工艺生产,根据本公司实际情况编制,它有利于铸钢件在生产过程中质量稳定的控制,也为操作工.车间主任和检验员在工作中起重要的依据。
在生产过程中除严格遵守本守则外,还要按照工艺卡规定进行操作,如本守则与工艺卡要求有冲突时,则按工艺卡进行操作。
由于实践经验不足,在执行过程中多提宝贵意见,以便进一步修改完整。
混砂工艺守则一.混砂前的准备1.机械设备运转不正常不得混拌。
2.原砂不干,水玻璃浓度不附,不得混拌。
二.操作要点.1.严格遵守各种原材料的配比和混拌时间.未经技术科同意不得更改。
2.拌不同类的砂,必须将拌砂机内残余的砂清除干净。
3.拌好的新砂必须按车序依次堆放,水玻璃石英砂应在回性二小时后方可使用。
每只盛砂桶上要盖好湿麻袋,麻袋不宜过湿。
三.型砂配方及混拌顺序.造型工艺守则一.造型前的准备.1.造型前应先熟悉工艺卡,并按工艺卡规定检查型板是否平整.冒口.补贴.浇道等附件是否齐全。
模型及型板部分定位是否有松动和偏移.发现问题应即时提出检修。
2.造型使用的冷铁.耐火管.底砖等都必须保持干燥,冷铁表面需平整。
不得有氧化物或油污,并涂银粉漆。
二.造型.1.填砂前应把模型和型板刷擦干净,摆好底砖,耐火管口上应塞上工具,防止堵塞,做好相应准备后方可填砂。
铸造工艺规范

总则为做到对铸造生产过程的有效控制现对我公司电炉熔化,砂子混制,制芯、造型(机器造型、手工造型)、浇注、清整,6个工序,特制定工艺规范。
(一)电炉熔化工艺规范1.修炉衬1.1炉底打结1.1.1先在紧靠感应圈内壁及炉底处围铺上石棉布,形成绝缘层。
1.1.2把石英砂倒入炉底,每层厚度不超过50mm,用捣固棒捣实,再用平锤打结实。
逐步打结直至把炉底打结到高度。
1.1.3校正中心,安放好坩埚膜。
在坩埚内放入一些重铁块,防止打结时坩埚膜松动。
1.2打结坩埚壁1.2.1在坩埚底与坩埚壁交界处,打结时要特别细心。
1.2.2后每层打结紧实高度为50-60mm,打结时间不少于20分钟。
当坩埚壁打结好后,在修筑炉口之前,要用平锤打实打平。
1.2.3加料时,不许石英砂落入石棉板和云母片(石棉布)等隔热绝缘层中。
1.2.4为使紧实度均匀,应由两人或两人以上站在对称位置转圈打结。
1.2.5在整个打结过程中,要严防杂物掉入硅砂中。
1.3修筑炉口和炉嘴1.3.1用水玻璃做粘结剂,快速成形。
用适量的硼酸水和水玻璃与打结料相混合,待用手一捏基本成团即可。
1.3.2在打好的炉口上涂上适量水玻璃,然后填筑混合料并用小锤打实。
1.3.3炉口和炉嘴修成内低外高的斜面。
1.4 烘炉和烧结1.4.1烘炉前要对冷却水系统、倾炉系统、控制回路及仪表等进行检查。
1.4.2烘炉时应加入一定数量的炉料,以保持温度升降的均匀性。
1.4.3烘炉要按低功率慢升温及材料厂提供的烧结工艺进行。
1.4.4炉衬温度达到1000度以上时,改用功率供电,使坩埚膜和炉料缓慢升温,慢慢熔化以减轻冲刷作用。
1.4.5熔化第一炉时尽量用洁净无锈和杂质的炉料。
1.4.6熔化完第一炉时铁液温度不要超过1550度,保温1-2小时,使炉衬均匀烧结。
1.4.7第一炉铁液化得满一些,使炉口烧结好一些。
整个坩埚由上到下均匀密实烧结。
1.4.8熔化第一炉后,坩埚的烧结层很薄,应连续熔化2-4炉后才能完成烧结过程。
铸造工艺操作规程范本

铸造工艺操作规程范本第一章总则第一条为加强铸造工艺操作,确保铸造质量,保障生产安全,制定本操作规程。
第二条本规程适用于铸造工艺的操作和管理,所有参与铸造工艺的人员必须遵守本规程。
第三条铸造工艺操作人员应具备相关的铸造知识和技能,严格遵守操作规程和工艺要求。
第二章工艺准备第四条铸造工艺操作前,必须进行工艺准备,包括准备材料、设备和工具等,确保顺利进行。
第五条铸造工艺操作人员应对所用的铸造材料进行检验,确保其质量符合要求。
第六条铸造工艺操作人员应检查设备及工具的完好程度,确保其能够正常使用。
第三章环境与安全第七条铸造工艺操作时,必须确保操作环境清洁、整齐,并保证通风良好。
第八条铸造工艺操作人员必须佩戴符合安全要求的个人防护装备,包括安全帽、防护眼镜、耳塞等。
第九条铸造工艺操作人员应熟悉和遵守相关的安全操作规程,严禁违章操作。
第四章操作程序第十条铸造工艺操作必须按照规定的操作程序进行,不得随意更改和省略。
第十一条铸造工艺操作人员应仔细阅读工艺文件和要求,了解工艺流程和工序要求。
第十二条铸造工艺操作必须严格按照标准要求进行操作,确保产品质量。
第十三条铸造工艺操作人员应注意操作和设备的安全,发现异常情况及时报告。
第十四条铸造工艺操作人员应做好记录工作,包括工艺参数、设备运行状态等。
第五章现场管理第十五条铸造工艺操作现场必须保持整洁,杂物要及时清理、整理。
第十六条铸造工艺操作人员应按照工艺要求组织、协调好相关工作。
第十七条铸造工艺操作现场必须禁止吸烟、明火和乱堆乱放。
第六章故障处理第十八条铸造工艺操作中出现设备故障、异常情况时,操作人员应立即停机,通知相关人员进行处理。
第十九条铸造工艺操作人员应熟悉常见故障现象和处理方法,能够迅速排除故障。
第二十条铸造工艺操作人员应及时向领导层报告故障处理情况,并提出改进意见。
第七章质量控制第二十一条铸造工艺操作人员必须按照工艺要求进行质量控制,确保产品合格。
第二十二条铸造工艺操作人员应认真填写相应的质量记录,确保质量数据准确完整。
铸造工艺规范
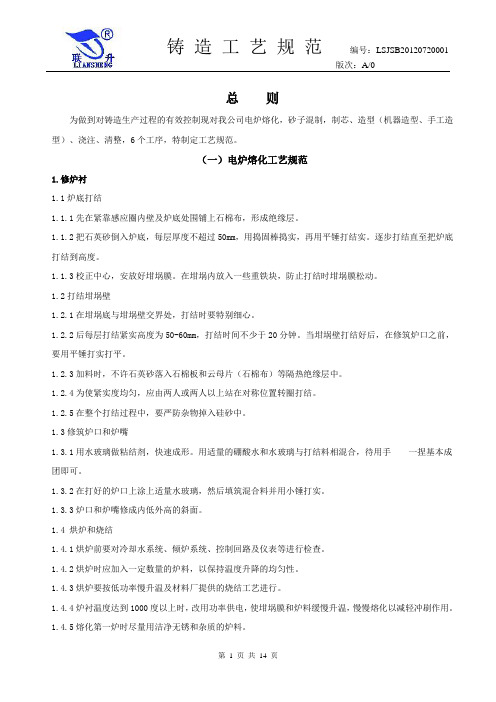
总则为做到对铸造生产过程的有效控制现对我公司电炉熔化,砂子混制,制芯、造型(机器造型、手工造型)、浇注、清整,6个工序,特制定工艺规范。
(一)电炉熔化工艺规范1.修炉衬1.1炉底打结1.1.1先在紧靠感应圈内壁及炉底处围铺上石棉布,形成绝缘层。
1.1.2把石英砂倒入炉底,每层厚度不超过50mm,用捣固棒捣实,再用平锤打结实。
逐步打结直至把炉底打结到高度。
1.1.3校正中心,安放好坩埚膜。
在坩埚内放入一些重铁块,防止打结时坩埚膜松动。
1.2打结坩埚壁1.2.1在坩埚底与坩埚壁交界处,打结时要特别细心。
1.2.2后每层打结紧实高度为50-60mm,打结时间不少于20分钟。
当坩埚壁打结好后,在修筑炉口之前,要用平锤打实打平。
1.2.3加料时,不许石英砂落入石棉板和云母片(石棉布)等隔热绝缘层中。
1.2.4为使紧实度均匀,应由两人或两人以上站在对称位置转圈打结。
1.2.5在整个打结过程中,要严防杂物掉入硅砂中。
1.3修筑炉口和炉嘴1.3.1用水玻璃做粘结剂,快速成形。
用适量的硼酸水和水玻璃与打结料相混合,待用手一捏基本成团即可。
1.3.2在打好的炉口上涂上适量水玻璃,然后填筑混合料并用小锤打实。
1.3.3炉口和炉嘴修成内低外高的斜面。
1.4 烘炉和烧结1.4.1烘炉前要对冷却水系统、倾炉系统、控制回路及仪表等进行检查。
1.4.2烘炉时应加入一定数量的炉料,以保持温度升降的均匀性。
1.4.3烘炉要按低功率慢升温及材料厂提供的烧结工艺进行。
1.4.4炉衬温度达到1000度以上时,改用功率供电,使坩埚膜和炉料缓慢升温,慢慢熔化以减轻冲刷作用。
1.4.5熔化第一炉时尽量用洁净无锈和杂质的炉料。
1.4.6熔化完第一炉时铁液温度不要超过1550度,保温1-2小时,使炉衬均匀烧结。
1.4.7第一炉铁液化得满一些,使炉口烧结好一些。
整个坩埚由上到下均匀密实烧结。
1.4.8熔化第一炉后,坩埚的烧结层很薄,应连续熔化2-4炉后才能完成烧结过程。
锻造工艺守则
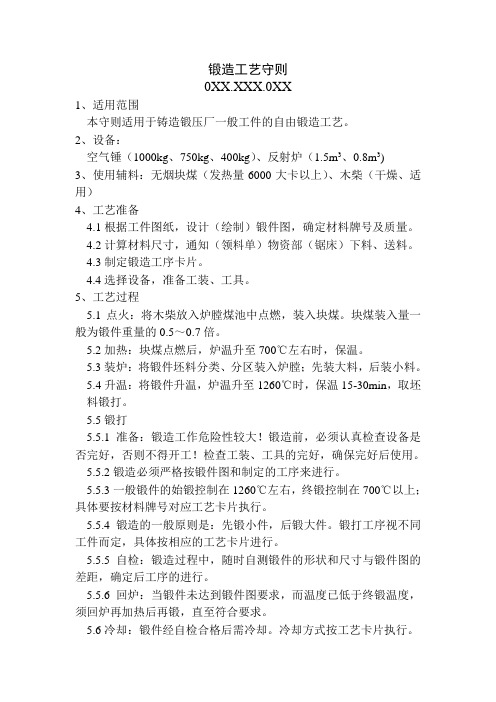
锻造工艺守则0XX.XXX.0XX1、适用范围本守则适用于铸造锻压厂一般工件的自由锻造工艺。
2、设备:空气锤(1000kg、750kg、400kg)、反射炉(1.5m3、0.8m3)3、使用辅料:无烟块煤(发热量6000大卡以上)、木柴(干燥、适用)4、工艺准备4.1根据工件图纸,设计(绘制)锻件图,确定材料牌号及质量。
4.2计算材料尺寸,通知(领料单)物资部(锯床)下料、送料。
4.3制定锻造工序卡片。
4.4选择设备,准备工装、工具。
5、工艺过程5.1点火:将木柴放入炉膛煤池中点燃,装入块煤。
块煤装入量一般为锻件重量的0.5~0.7倍。
5.2加热:块煤点燃后,炉温升至700℃左右时,保温。
5.3装炉:将锻件坯料分类、分区装入炉膛;先装大料,后装小料。
5.4升温:将锻件升温,炉温升至1260℃时,保温15-30min,取坯料锻打。
5.5锻打5.5.1准备:锻造工作危险性较大!锻造前,必须认真检查设备是否完好,否则不得开工!检查工装、工具的完好,确保完好后使用。
5.5.2锻造必须严格按锻件图和制定的工序来进行。
5.5.3一般锻件的始锻控制在1260℃左右,终锻控制在700℃以上;具体要按材料牌号对应工艺卡片执行。
5.5.4锻造的一般原则是:先锻小件,后锻大件。
锻打工序视不同工件而定,具体按相应的工艺卡片进行。
5.5.5自检:锻造过程中,随时自测锻件的形状和尺寸与锻件图的差距,确定后工序的进行。
5.5.6回炉:当锻件未达到锻件图要求,而温度已低于终锻温度,须回炉再加热后再锻,直至符合要求。
5.6冷却:锻件经自检合格后需冷却。
冷却方式按工艺卡片执行。
5.7检查:冷却后,须经质量检查人员检查合格,方可填写入库单,转入下道工序。
6 注意事项6.1 严格按《安全技术操作规程》中“锻工部分”的要求进行。
6.2 开炉前要全面检查设备、工装工具等完好。
6.3 严格控制始锻温度与终锻温度。
铸锻件调质工艺守则

铸锻件调质工艺守则1范围本标准规定了碳素钢及合金钢铸锻件调质处理的技术要求及操作规程。
本标准适用于材料为碳素钢、合金钢,截面小于800mm,硬度HB≤320的一般机器零件(如:轴、齿轮、圆盘等锻件及形状比较简单的铸件)的调质处理。
2规范性引用文件GB231-1984 金属布氏硬度试验方法GB/T699-1999 优质碳素结构钢GB/T3077-1999 合金结构钢GB/T6402-1991 钢锻件超声波检验方法GB7232-1999 金属热处理工艺术语GB7233-1987 铸钢件超声波探伤及质量评级GB8539-1987 齿轮材料及热处理检验的一般规定GB9452-1988 热处理炉有效加热区测定方法GB11352-1989 一般工程用铸造碳素钢件GB/T16923-1997 钢的正火与退火处理GB/T17394-1998 金属里氏硬度试验方法JB3877-1985 钢的淬火回火处理3名词术语3.1淬火将钢件加热到AC3或AC1点以上某一温度,保持一定时间,然后以适当速度冷却获得马氏体或贝氏体组织的热处理工艺。
3.2回火钢件淬硬后,再加热到AC1点以下某一温度,保温一定时间,然后冷却到室温的热处理工艺。
3.3调质钢件淬火后高温回火的复合热处理工艺。
3.4待调质件凡要求进行调质处理的钢材、零件坯料等统称待调质件。
3.5调质件经过调质处理的钢材或零件坯料。
4待调质件的有关规定4.1待调质件的钢种牌号适用于调质的部分钢种牌号列于表1。
表1钢组及标准号钢种牌号(1)结构钢大型碳素结构钢锻件普通含锰钢大型合金结构钢锻件35,45,55,60硅锰钢硅锰钼钒钢铬钢铬钼钢铬钼铝钢铬锰钼钢铬镍钢铬镍钼钢铬锰硅钢重型机械用弹簧钢轴承钢35SiMn,50SiMn37 SiMn2MoV40Cr, 50Cr35CrMo, 42CrMo,50 CrMo38CrMoAl40CrMnMo40CrNi, 45 CrNi34CrNiMo, 40CrNiMo30CrMnSi, 35 CrMnSi65Mn, 60Si2Mn, 50CrVAGCr15, GCr15SiMn(2) 工具钢大型锻件用碳素工具钢大型锻件用合金工具钢T7、T8、T10、T129CrSi,9Cr2,9 Cr2Mo,5 CrMnMo,5 CrNiMo,60 CrMnMo(3)特殊钢大型不锈、耐酸耐热钢锻件1 Cr13,2 Cr13,3 Cr13,4 Cr13,(4)铸钢一般工程用铸造碳钢件大型低合金钢铸件ZG270-500,ZG310-570,ZG340-640ZG40Mn2,ZG50Mn2,ZG35CrMnSi, ZG35SiMn, ZG34CrNiMo4.2 调质件的原始资料a、一般零件必须提供:钢号、预先热处理方法等。
2023年铸造工艺操作规程
2023年铸造工艺操作规程第一章总则第一条为规范和规范化2023年铸造工艺的操作流程,提高生产效率,确保产品质量,制定本操作规程。
第二条本规程适用于所有从事铸造工艺操作的工作人员。
第三条所有从事铸造工艺操作的工作人员必须遵守本规程,严格按照操作流程进行操作。
第四条铸造工艺操作应遵循安全第一、质量第一的原则,确保操作人员的身体安全和生产环境的安全。
第五条铸造工艺操作应遵守相关的法律法规和政策规定,保护环境和资源。
第二章岗位职责第六条所有从事铸造工艺操作的工作人员应具备相关的岗位职责,按照工艺操作流程完成工作任务。
第七条铸造工艺操作的岗位职责包括但不限于以下几个方面:1.准备工作:包括准备材料、检查设备、调整设备参数等。
2.操作工作:包括开机、调试、加工等操作工作。
3.检测工作:包括对产品进行质量检测和检验,保证产品符合要求。
4.维护工作:包括设备维护、保养等工作,确保设备正常运行。
5.安全工作:包括安全检查、消防设备检查等工作,确保工作场所的安全。
第三章操作流程第八条铸造工艺操作应按照以下流程进行:1.准备工作:包括准备材料、检查设备、调整设备参数等。
2.操作工作:按照工艺流程进行操作,确保产品质量。
3.检测工作:对产品进行质量检测和检验,保证产品符合要求。
4.维护工作:对设备进行维护、保养等工作,确保设备正常运行。
5.安全工作:进行安全检查、消防设备检查等工作,确保工作场所的安全。
第九条操作前,应制定具体的操作计划和操作指导,明确操作程序和注意事项。
第四章操作规范第十条所有从事铸造工艺操作的工作人员应遵循以下操作规范:1.严格遵守操作流程,不得随意改变工艺流程。
2.熟悉设备功能和操作方法,严禁未经培训或未获得许可使用设备。
3.严格遵守操作规程,保持操作规范,不得违规操作。
4.严格按照操作规程进行质量检测和检验,不得随意抽检或漏检。
5.认真维护设备,按时进行保养和维修,确保设备正常运行。
第五章安全防护第十一条铸造工艺操作应加强安全防护,确保操作人员的身体安全。
铸造工艺守则
浙江万丰科技开发有限公司铸模车间铸造工艺守则编制:审核:批准:日期:日期:日期:总则本守则适用于铸铝件一般性工艺生产,根据本公司实际情况编制,它有利于铸件在生产过程中质量稳定的控制,也为操作工.车间主任和检验员在工作中起重要的依据。
在生产过程中除严格遵守本守则外,还要按照工艺卡规定进行操作,如本守则与工艺卡要求有冲突时,则按工艺卡进行操作。
由于实践经验不足,在执行过程中多提宝贵意见,以便进一步修改完整。
1目录一、铸造概念 (03)二、铝液熔化工艺守则 (06)三、低压铸造工艺 (13)四、热处理工艺守则 (28)五、模具保养工艺 (34)六、重力和低压铸造涂料的开发和应用 (36)七、打磨工艺 (42)八、气密性实验工艺 (43)九、割冒口工艺 (43)十、抛丸工艺 (44)十一、清洗工艺 (45)十二、安装管接头工艺 (46)十三、包装工艺 (46)十四、加工中心工艺 (47)2一、铸造概念铸造工艺:应用铸造有关理论和系统知识生产铸件的技术和方法。
包括造型材料准备、造型、制芯、金属熔炼、浇注和凝固控制等。
铸造还可以按金属液的浇注工艺分为重力铸造和压力铸造。
重力铸造是指金属液在地球重力作用下注入铸型的工艺,也称浇铸。
广义的重力铸造包括砂型浇铸、金属型浇铸、熔模铸造,泥模铸造等;窄义的重力铸造专指金属型浇铸。
压力铸造是指金属液在其他外力(不含重力)的作用下注入铸型的工艺。
广义的压力铸造包括压铸机的压力铸造和真空铸造、低压铸造、离心铸造等;窄义的压力铸造专指压铸机的金属型压力铸造,简称压铸。
这几种铸造工艺是目前有色金属铸造中最常用的、也是相对价格最低的。
砂型铸造是一种以砂作为主要造型材料,制作铸型的传统铸造工艺。
3砂型一般采用重力铸造,有特殊要求时也可采用低压铸造、离心铸造等工艺。
砂型铸造的适应性很广,小件、大件,简单件、复杂件,单件、大批量都可采用。
砂型铸造用的模具,以前多用木材制作,通称木模。
木模缺点是易变形、易损坏;除单件生产的砂型铸件外,可以使用尺寸精度较高,并且使用寿命较长的铝合金模具或树脂模具。
水玻璃铸造工艺守则
水玻璃铸造工艺守则引言水玻璃铸造是一种常用于制作精密铸件的工艺。
它利用水溶性玻璃作为粘结剂,将石粉、天然矿石、氧化物等材料与玻璃粉混合,形成糊状物质,然后通过模具铸造成型。
本文档旨在介绍水玻璃铸造工艺的守则,以确保制作出高质量的铸件。
材料准备在水玻璃铸造过程中,正确的材料准备是确保质量的关键之一。
以下是几个重要的守则:1.准确称量:使用精确的称量设备,确保材料的比例准确无误。
不同材料的比例对于最终的铸件性能影响很大,因此必须精确控制。
2.材料筛选:选择合适的石粉、矿石和氧化物材料,以及适量的玻璃粉。
这些材料的质量和粒度分布对铸件的密度和强度有重要影响。
3.材料混合:将材料充分混合,确保材料的均匀性。
不同材料的颗粒大小和密度可能会导致颗粒分层,因此混合过程非常关键。
模具设计和制作模具是水玻璃铸造中至关重要的部分,它决定了最终铸件的形状和尺寸。
以下是一些模具设计和制作的守则:1.准确测量:在设计模具前,应仔细测量铸件的尺寸和形状。
尺寸的准确度对于最终产品的质量至关重要。
2.模具材料选择:根据铸件的材料和形状,选择合适的模具材料。
一些常用的模具材料包括石膏、金属、橡胶等。
确保模具材料具有足够的耐火性和精细度。
3.模具制作:制作模具时,需要确保模具的平整度和合理的引水系统。
模具的平整度直接影响到铸件的表面质量,引水系统有助于铸件内部的液态玻璃流动。
铸造工艺控制水玻璃铸造的工艺控制对成品的质量至关重要。
以下是几个工艺控制的守则:1.浇注温度控制:控制玻璃溶液的浇注温度,避免过高或过低的温度对铸件性能的影响。
过高的温度会导致铸件开裂或失真,过低的温度会使铸件表面粗糙。
2.浇注速度控制:控制玻璃溶液的浇注速度,以保持合适的流动性和注入压力。
过慢的浇注速度可能导致玻璃凝固太早,过快的速度可能导致玻璃渗透到模具墙壁中。
3.硬化时间控制:控制铸件在模具中的硬化时间,确保铸件充分硬化和成型。
硬化时间不足会导致铸件强度不够,硬化时间过长可能导致铸件变形。
铸造工艺规范
总则为做到对铸造生产过程的有效控制现对我公司电炉熔化,砂子混制,制芯、造型(机器造型、手工造型)、浇注、清整,6个工序,特制定工艺规范。
(一)电炉熔化工艺规范1.修炉衬1.1炉底打结1.1.1先在紧靠感应圈内壁及炉底处围铺上石棉布,形成绝缘层。
1.1.2把石英砂倒入炉底,每层厚度不超过50mm,用捣固棒捣实,再用平锤打结实。
逐步打结直至把炉底打结到高度。
1.1.3校正中心,安放好坩埚膜。
在坩埚内放入一些重铁块,防止打结时坩埚膜松动。
1.2打结坩埚壁1.2.1在坩埚底与坩埚壁交界处,打结时要特别细心。
1.2.2后每层打结紧实高度为50-60mm,打结时间不少于20分钟。
当坩埚壁打结好后,在修筑炉口之前,要用平锤打实打平。
1.2.3加料时,不许石英砂落入石棉板和云母片(石棉布)等隔热绝缘层中。
1.2.4为使紧实度均匀,应由两人或两人以上站在对称位置转圈打结。
1.2.5在整个打结过程中,要严防杂物掉入硅砂中。
1.3修筑炉口和炉嘴1.3.1用水玻璃做粘结剂,快速成形。
用适量的硼酸水和水玻璃与打结料相混合,待用手一捏基本成团即可。
1.3.2在打好的炉口上涂上适量水玻璃,然后填筑混合料并用小锤打实。
1.3.3炉口和炉嘴修成内低外高的斜面。
1.4 烘炉和烧结1.4.1烘炉前要对冷却水系统、倾炉系统、控制回路及仪表等进行检查。
1.4.2烘炉时应加入一定数量的炉料,以保持温度升降的均匀性。
1.4.3烘炉要按低功率慢升温及材料厂提供的烧结工艺进行。
1.4.4炉衬温度达到1000度以上时,改用功率供电,使坩埚膜和炉料缓慢升温,慢慢熔化以减轻冲刷作用。
1.4.5熔化第一炉时尽量用洁净无锈和杂质的炉料。
1.4.6熔化完第一炉时铁液温度不要超过1550度,保温1-2小时,使炉衬均匀烧结。
1.4.7第一炉铁液化得满一些,使炉口烧结好一些。
整个坩埚由上到下均匀密实烧结。
1.4.8熔化第一炉后,坩埚的烧结层很薄,应连续熔化2-4炉后才能完成烧结过程。
- 1、下载文档前请自行甄别文档内容的完整性,平台不提供额外的编辑、内容补充、找答案等附加服务。
- 2、"仅部分预览"的文档,不可在线预览部分如存在完整性等问题,可反馈申请退款(可完整预览的文档不适用该条件!)。
- 3、如文档侵犯您的权益,请联系客服反馈,我们会尽快为您处理(人工客服工作时间:9:00-18:30)。
铸造工艺守则XX阀门有限公司2007年编制目录总则SZ01…………………………………………混砂SZ02…………………………………………造型SZ03…………………………………………泥芯SZ04…………………………………………烘型SZ05…………………………………………配箱SJ/Z06………………………………………浇注SJ/Z07………………………………………熔炼SJ/Z08………………………………………清砂SJ/Z09………………………………………切割S/JZ10………………………………………焊补S/JZ11………………………………………热处理S/JZ12………………………………………整理JZ01…………………………………………制型JZ02…………………………………………修接JZ03…………………………………………制壳JZ04…………………………………………脱蜡JZ05/6………………………………………焙烧总则本守则适用于铸钢件一般性工艺生产,根据本公司实际情况编制,它有利于铸钢件在生产过程中质量稳定的控制,也为操作工.车间主任和检验员在工作中起重要的依据。
在生产过程中除严格遵守本守则外,还要按照工艺卡规定进行操作,如本守则与工艺卡要求有冲突时,则按工艺卡进行操作。
由于实践经验不足,在执行过程中多提宝贵意见,以便进一步修改完整。
XX有限公司2007年编制混砂工艺守则HLSZ01-07一.混砂前的准备1.机械设备运转不正常不得混拌。
2.原砂不干,水玻璃浓度不附,不得混拌。
二.操作要点.1.严格遵守各种原材料的配比和混拌时间.未经技术科同意不得更改。
2.拌不同类的砂,必须将拌砂机内残余的砂清除干净。
3.拌好的新砂必须按车序依次堆放,水玻璃石英砂应在回性二小时后方可使用。
每只盛砂桶上要盖好湿麻袋,麻袋不宜过湿。
三.型砂配方及混拌顺序.造型工艺守则HLSZ02-07一.造型前的准备.1.造型前应先熟悉工艺卡,并按工艺卡规定检查型板是否平整.冒口.补贴.浇道等附件是否齐全。
模型及型板部分定位是否有松动和偏移.发现问题应即时提出检修。
2.造型使用的冷铁.耐火管.底砖等都必须保持干燥,冷铁表面需平整。
不得有氧化物或油污,并涂银粉漆。
二.造型.1.填砂前应把模型和型板刷擦干净,摆好底砖,耐火管口上应塞上工具,防止堵塞,做好相应准备后方可填砂。
2.面砂厚度或模型浇冒口与箱边的距离应符合下列规定。
铸件重量(公斤) 面砂厚度(毫米)50-10025-30101-25031-40251-50041-503.砂型面砂要捣硬,坚实度要均匀.在椿砂时应先把面砂捂实泠铁摆好后方可填背砂。
每次填入的型砂不可过多.应控制在300mm以内(指椿砂时的高度)。
4.椿砂时要注意爱护模型,避免椿头直接碰到模型,防止模型贴边.冒口.冷铁.浇道等位置变动。
5.砂型椿实后,底盖箱上的型砂都要铲平,并严禁砂型低于箱面,防止跌箱,一切做好后方可通二氧化碳硬化。
6.盛砂桶内用剩的面砂必须用湿麻袋盖好,麻袋不宜过湿(以手按不出水为准)以防风干硬化。
三.起模和修型.1.起模前应检查砂型松硬,局部松软的地方应修正修好。
起模时要平稳,保持砂型的完整。
2.模型取出后,检查砂型松紧程度。
模型贴边.浇道.冒口.冷铁等位置是否移动或遗漏,局部松软或损坏应修好保证牢固。
3.修型时,必须修到位,并符合模型原来的几何形状。
冒口根部,浇口与砂型接触处以及其它铸造圆角要均匀倒好,按工艺卡规定打好气眼,保证砂型的排气畅通。
4.刷涂料时必须涂刷均匀到位,不得在型腔内堆积。
涂料的悬浮度控制在81-83`。
编制:审核:批准:泥芯工艺守则HLSZ03-07一.造芯前的准备1.造芯前应先熟悉工艺卡,并按工艺卡规定检查芯盒是否变形,表面是否光滑和平整,活动部分附件是否齐全或损坏,发现问题应及提出检修。
2.造芯使用的冷铁和芯骨等都必须保持干燥。
冷铁表面需平整,不得有氧化物或油污,并涂银粉漆。
二.造芯1.填砂前应把芯盒刷擦干净。
冷铁一定要符合工艺卡的要求摆放,泥芯骨要放正,属于铸型处的泥芯骨不得露出。
2.较大泥芯在椿砂时必须采取逐层加砂逐层椿实的方法.每次加砂量不超过150mm.3.应尽量采取中间掏空的方法,空的大小可根椐泥芯的大小决定,原则上不影响砂芯强度。
4.泥芯椿实后,在泥芯头处必须开好排气槽,打通出气孔,确保气体顺利排除,一切做好后方可通二氧化碳硬化。
手工硬化时,开始二氧化碳不能过大,防止冲坏泥芯。
5.在拆卸或取出时,敲击不宜过重,以免造成损坏,还要检查泠铁摆放是否正确,有无移位或遗漏,若损坏的必须修复后再硬化。
6.造芯结束后,要将泥芯配套分类堆放。
盛砂桶内用剩的砂需立即用湿麻袋盖好,以防风干硬化。
7.刷涂料时,需注意的是刷的均匀到位不得有堆积。
涂料悬浮度控制在81-83`。
烘型工艺守则HLSZ04-07一.烘箱.1.一般铸钢件的铸型用煤气烘干时间3-5分钟,重要铸件(特殊材质)按工艺卡规定操作。
2.烘干的砂型放置时间不得超过2小时,超过规定时间要重新进行烘干。
3.炉子烘箱的时间与湿度1.烘干湿度及保温时间2.操作要点1).严格执行烘干温度和时间,以泥芯干燥不烧枯为原则。
2).升温速度控制在100-120℃/小时,经保温后缓慢冷却。
3).在泥芯进炉时,大泥芯应摆在近火口处。
4).泥芯返潮后,必须重新进炉子烘干。
配箱工艺守则HLSZ05-07一.配箱前准备1.查看泥芯,浇口杯等附件是否齐全。
2.检查场地是否平整,以确保底箱的平整防止砂型损坏。
二.配箱1.严格按生产计划,工艺要求进行操作。
发现砂型损坏,及时用原砂予以修复,修复后进行干燥后方可合箱,做到浇一炉配一炉。
凡配好箱超过3小时未浇注的,必须开箱重新烘过再配箱。
2.合箱前应吹清砂型内的砂杂物,粘结的砂块必须用手或刷子清除干净,特别要注意浇道和冒口内的粘砂,浇道和气眼一定要畅通。
盖箱上平面有松散的砂层必须在合箱前铲落处理干净以免砂落入型腔造成铸件缺陷。
3.按工艺卡要求落好泥芯,泥芯要求落正.稳因.塞紧。
泥芯头处要引出气槽,保证气体的顺利排出。
4.泥芯头要采用石棉线包好,原则上应保证浇注时不发生漏钢水现象。
5.定位销的数量应根椐砂箱的要求安放,绝不可以少放或不放。
6.凡泥芯需压牢的砂型必须经过两次合箱,以观察其泥芯是否压牢或型腔内壁是否被压塌。
三.配箱后的工作.1.检查直浇口与横浇口是否对直,上下箱接触处是否密缝,如不密封,需用石棉线摆好以防射箱。
2.浇口杯周围要捂上新砂,以防浇注时浇口杯开裂。
3.合箱后应检查视线是否对准,直浇口和冒口内是否有散落杂物,泥芯是否有偏斜。
4.浇配人员浇注后,气眼及浇口处溢出钢水应及时撬除,以利开箱。
编制:审核:批准:浇注工艺守则HLSZ06-071.浇注前先了解铸件钢号,重量和形状,根据钢号,按铸件重量先重后轻。
复杂件和试棒应在炉钢重量中间浇注。
2.熟悉工艺卡,按工艺要求进行浇注。
根据钢水温度高低,铸件形状简单与复杂确定浇注速度快慢。
3.浇注过程必须做到“两头慢中间快”的要求,中途不得停顿。
冒口高度必须浇足,根椐工艺要求进行回冲钢水,以利补缩。
注:钢水注满冒口时,稍待片刻,再续浇一下,经利冒口补缩铸件。
浇注过程中必须要引火,以便气体顺利排出。
4.浇注工要做到,低温钢不浇,浇口低于冒口不浇,严重抬箱不浇。
发生泻箱时一方面采取措施堵住,一方面要细流慢浇不得停顿。
5.浇注普通铸件要在20钟后才能起吊,2小时后方可开箱,特殊铸件按工艺卡操作。
编制:审核:批准:清砂工艺守则HLS/JZ08-071.清砂时,不得因清理不当而有损铸件质量。
对薄壁或小件,不应用大锤敲击,以免裂纹或变形。
2.应仔细地尽可能地清除铸件内外腔的残砂、芯骨、冷铁。
芯骨、冷铁按规定位置堆放,复杂件的内腔型砂尽量设法清理干净。
3.浇冒口与铸件连接部位的型砂必须清除干净。
如有铁夹砂则用凿子打出割缝。
4.清砂完毕后应把场地清理干净,铁锤、铁棍、凿子应收好管好,水管下班时要圈好挂好。
编制:审核:批准:切割工艺守则HLS/JZ09-071.操作前应熟悉工艺卡的要求,然后才能进行切割。
2.在切割过程中,如遇回火应立即关闭纯氧阀,再关闭慢风阀。
3.铸件切割中,尽量把冒口割的平整,达到美观效果。
4.切割冒口时,应把大的或厚的披锋,毛刺同时割去。
5.切割前铸件不得有积水,切割后不得浇水。
6.特殊铸件需要热割,由工艺卡规定操作。
编制:审核:批准:焊补工艺守则HLS/JZ10-071.缺陷的修补范围。
1).凡铸件加工面上的夹渣、砂眼等缺陷。
若用磨光机全部能清理,其深度不超过机械加工余量的,可不焊补。
2).在铸件非加工面上,夹杂、砂眼、气孔及针孔等缺陷,都要补焊。
2.焊补工艺。
1).铸件上需焊补的缺陷,焊补前都应把非金属夹杂物彻底清除,方可焊补。
2).当铸件有较多缺陷时,大缺陷小缺陷应交替焊补,避免过热。
每层焊补后应敲去熔渣,才能继续焊补。
并要随时检查是否有焊补缺陷,如发现要挖净后再继续焊补。
3.特殊材质,按工艺卡规定操作。
编制:审核:批准:整理工艺守则HLS/JZ12-07一.抛丸.1.铸件按产品要求,表面做到无氧化物.无粘砂.无打磨痕迹等颜色要均匀。
2.做到三抛。
1).清砂后,必须把表面氧化壳残砂抛干净,有利与焊补。
2).焊补打磨后,必须把打磨和焊补痕迹处理干净,有利与再次焊补。
3).热处理后,必须把氧化物彻底抛干净,达到美观效果。
二.打磨.1.熟悉产品要求,按工艺卡规定操作。
2.铸件非加工面要符合原来形状,做到无毛刺批锋.凹坑.皱纹和焊疤等缺陷,使外表自然美观。
3.铸件加工面上不能留有焊疤和批锋。
三.防锈及摆放.1.铸件非加工面上必须全部刷上防锈油,不得遗漏。
加工面上可以不上油。
特殊铸件按工艺卡操作。
2.铸件要按指定位置堆放,产品名称规格型号要分类清楚,摆放有整齐。
编制:审核:批准:脱蜡工艺守则HLJZ04-071.清理浇口。
脱蜡前要将浇口杯顶部的浮砂及涂料清除刮净,以免在脱蜡过程中落入型腔内。
2.加入补充硬化剂。
在脱蜡水中加入工业盐酸w=1%使型壳脱蜡进补充硬化,也有利于旧蜡回收再用。
3.水温控制。
热水脱蜡的水温度控制在95-98℃,避免沸腾。
型壳脱蜡时间控制在40min,不宜超过60 min。
4.型壳冲洗。
型壳脱蜡后,用热水冲洗干净。
脱蜡后的型壳可代倒置存放。
5.槽液换新及清理。
应定期更换脱蜡水,同时清理槽底砂粒及脏物。
编制:审核:批准:型壳焙烧与浇注工艺守则HLJZ05/6-071.焙烧温度控制在850℃±10℃,保温0.5-2h。
出炉时表面呈白色或浅色,不冒黑烟。
若表面颜色较深或呈深灰色,应重新焙烧,不得浇注。
2.浇注前型壳一定要摆平,凡重量超过30kg的铸件应放在砂箱内,浇口处盖好挡砂工具后才可填砂。