铸造工艺规范
铸造工艺规范
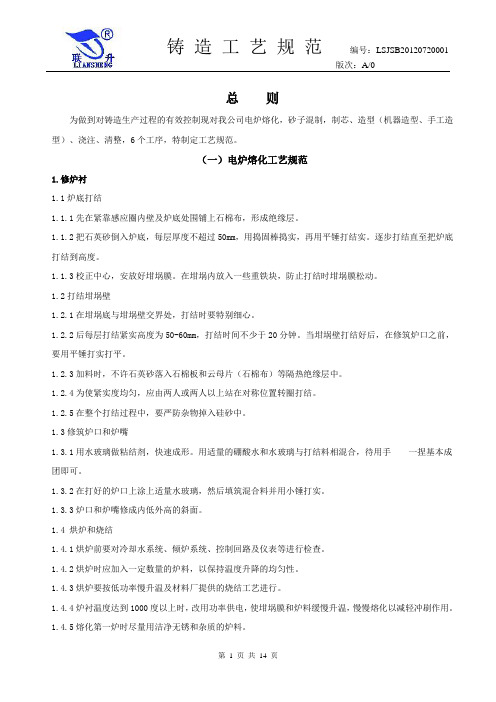
总则为做到对铸造生产过程的有效控制现对我公司电炉熔化,砂子混制,制芯、造型(机器造型、手工造型)、浇注、清整,6个工序,特制定工艺规范。
(一)电炉熔化工艺规范1.修炉衬1.1炉底打结1.1.1先在紧靠感应圈内壁及炉底处围铺上石棉布,形成绝缘层。
1.1.2把石英砂倒入炉底,每层厚度不超过50mm,用捣固棒捣实,再用平锤打结实。
逐步打结直至把炉底打结到高度。
1.1.3校正中心,安放好坩埚膜。
在坩埚内放入一些重铁块,防止打结时坩埚膜松动。
1.2打结坩埚壁1.2.1在坩埚底与坩埚壁交界处,打结时要特别细心。
1.2.2后每层打结紧实高度为50-60mm,打结时间不少于20分钟。
当坩埚壁打结好后,在修筑炉口之前,要用平锤打实打平。
1.2.3加料时,不许石英砂落入石棉板和云母片(石棉布)等隔热绝缘层中。
1.2.4为使紧实度均匀,应由两人或两人以上站在对称位置转圈打结。
1.2.5在整个打结过程中,要严防杂物掉入硅砂中。
1.3修筑炉口和炉嘴1.3.1用水玻璃做粘结剂,快速成形。
用适量的硼酸水和水玻璃与打结料相混合,待用手一捏基本成团即可。
1.3.2在打好的炉口上涂上适量水玻璃,然后填筑混合料并用小锤打实。
1.3.3炉口和炉嘴修成内低外高的斜面。
1.4 烘炉和烧结1.4.1烘炉前要对冷却水系统、倾炉系统、控制回路及仪表等进行检查。
1.4.2烘炉时应加入一定数量的炉料,以保持温度升降的均匀性。
1.4.3烘炉要按低功率慢升温及材料厂提供的烧结工艺进行。
1.4.4炉衬温度达到1000度以上时,改用功率供电,使坩埚膜和炉料缓慢升温,慢慢熔化以减轻冲刷作用。
1.4.5熔化第一炉时尽量用洁净无锈和杂质的炉料。
1.4.6熔化完第一炉时铁液温度不要超过1550度,保温1-2小时,使炉衬均匀烧结。
1.4.7第一炉铁液化得满一些,使炉口烧结好一些。
整个坩埚由上到下均匀密实烧结。
1.4.8熔化第一炉后,坩埚的烧结层很薄,应连续熔化2-4炉后才能完成烧结过程。
铸造生产的工艺操作规范
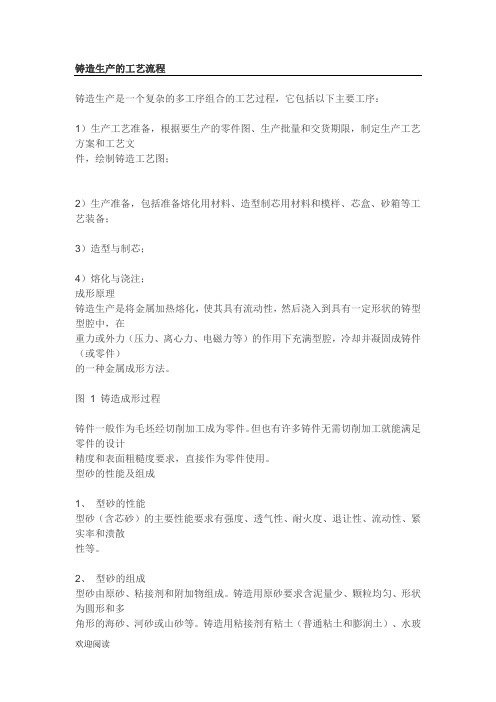
铸造生产的工艺流程铸造生产是一个复杂的多工序组合的工艺过程,它包括以下主要工序:1)生产工艺准备,根据要生产的零件图、生产批量和交货期限,制定生产工艺方案和工艺文件,绘制铸造工艺图;2)生产准备,包括准备熔化用材料、造型制芯用材料和模样、芯盒、砂箱等工艺装备;3)造型与制芯;4)熔化与浇注;成形原理铸造生产是将金属加热熔化,使其具有流动性,然后浇入到具有一定形状的铸型型腔中,在重力或外力(压力、离心力、电磁力等)的作用下充满型腔,冷却并凝固成铸件(或零件)的一种金属成形方法。
图1 铸造成形过程铸件一般作为毛坯经切削加工成为零件。
但也有许多铸件无需切削加工就能满足零件的设计精度和表面粗糙度要求,直接作为零件使用。
型砂的性能及组成1、型砂的性能型砂(含芯砂)的主要性能要求有强度、透气性、耐火度、退让性、流动性、紧实率和溃散性等。
2、型砂的组成型砂由原砂、粘接剂和附加物组成。
铸造用原砂要求含泥量少、颗粒均匀、形状为圆形和多角形的海砂、河砂或山砂等。
铸造用粘接剂有粘土(普通粘土和膨润土)、水玻璃砂、树脂、合脂油和植物油等,分别称为粘土砂,水玻璃砂、树脂砂、合脂油砂和植物油砂等。
为了进一步提高型(芯)砂的某些性能,往往要在型(芯)砂中加入一些附加物,如煤份、锯末、纸浆等。
型砂结构,如图 2 所示。
图2 型砂结构示意图工艺特点铸造是生产零件毛坯的主要方法之一,尤其对于有些脆性金属或合金材料(如各种铸铁件、有色合金铸件等)的零件毛坯,铸造几乎是唯一的加工方法。
与其它加工方法相比,铸造工艺具有以下特点:1)铸件可以不受金属材料、尺寸大小和重量的限制。
铸件材料可以是各种铸铁、铸钢、铝合金、铜合金、镁合金、钛合金、锌合金和各种特殊合金材料;铸件可以小至几克,大到数百吨;铸件壁厚可以从0.5 毫米到1 米左右;铸件长度可以从几毫米到十几米。
2)铸造可以生产各种形状复杂的毛坯,特别适用于生产具有复杂内腔的零件毛坯,如各种箱体、缸体、叶片、叶轮等。
刹车盘铸造工艺规程

刹车盘铸造⼯艺规程
刹车盘铸造⼯艺规程
1 ⽬的
规范刹车盘铸造⽣产过程,确保铸造产品符合质量要求。
2 适⽤范围
适⽤于公司刹车盘铸造⽣产过程。
3 ⽣产⼯艺规程
3.1刹车盘铸造⼯艺流程:
3.2 芯砂配制及制芯烘⼲
3.2.1 制芯设备与⽅法:芯⼦采⽤合脂油砂,⼿⼯制芯,⾦属芯盒。
3.2.2 刹车盘主要砂芯⽰意图:见图4。
3.2.3 制芯:
3.2.3.1 车间按有关⼿续到模具库领⽤合格的芯盒,⽤完后应清洗⼲净及时送回。
3.2.3.2 油砂混制时,严格按⽐例混制(芯砂与合脂油按100:3⽐例混制)。
使⽤过程中出现争议时,取样送实验室测试其强度和透⽓性。
3.2.3.3 打芯时,芯盒的筋⽚不得有刮砂、粘砂现象。
3.2.3.4 刹车盘砂芯上的字要清晰完整,刮出⾯要⽤⼯具刮了压光。
3.2.3.5 砂芯应尽量轻轻在专⽤⼯作台上均匀敲出或磕出芯盒。
3.1.3.6 芯头⽤Φ8mm⽓孔锥扎透。
(芯盒带有透⽓锥的除外)
3.1.3.7 检验砂芯,⼤平⾯度不得⼤于0.3mm,厚度尺⼨不⼩于芯盒磨损极限尺⼨。
3.1.4 砂芯质量要求:
尺⼨准确、形状完整、紧实光洁、⽆有松动、⽓眼要畅、砂芯不得有掉砂、粘砂、裂纹的现象。
3.1.5 烘⼲(烤芯)
3.1.5.1 严格控制芯窑温度和时间。
(芯窑温度和时间的控制温度见下图)
T(
降温
50 50。
桥壳铸造工艺设计规范

桥壳铸造工艺设计规范1 适用范围本标准适用于铸钢桥壳工装、模具、检具等设计制图及铸造工艺设计工作规范。
2 规范性引用文件下列文件中的条款通过本标准的引用而成为本标准的条款。
凡是注日期的引用文件,其随后所有的修改单(不包括戡误的内容)或修订版均不适用于本标准。
然而,鼓励根据本标准达成协议的各方研究是否可使用这些文件的最新版本。
凡是不注日期的引用文件,其最新版本适用于本标准。
GB/T 6414-1999 《铸件尺寸公差与机械加工余量》JB/T 5106-1991 《铸件模样型芯头基本尺寸》GB/T 11351-1989 《铸件重量公差》3术语和定义3.1铸件的最小壁厚:在一定的铸造条件下,铸造合金液能充满铸型的最小厚度。
3.2铸件的临界壁厚:当铸件的厚度超过了一定值后,铸件的力学性能并不按比例地随着铸件厚度的增大而增大,而是显著下降,存在一个临界厚度。
3.3铸钢件相对密度:浇注钢液重量与铸件三个方向最大尺寸的乘积之比。
因而往往小于铸件密度。
3.4吃砂量:模样与砂箱壁、箱顶(底)、和箱带之间的距离。
4铸造工艺设计原则4.1铸造工艺设计必须满足产品铸件质量和对环保的要求,有利于实现优质、高产、低耗,改善劳动条件,安全生产,提高生产标准化、通用化、系列化水平;4.2铸造工艺设计必须能够提供清晰、完整、正确、统一的资料输出:过程流程图、铸造材料清单、过程潜在失效模式及后果分析(PFMEA)、控制计划、铸造工艺图、铸造工艺卡、作业指导书等。
5铸造工艺设计程序5.1铸件结构工艺和铸件的先期质量策划5.1.1 铸造产品的设计阶段,应组成产品设计人员和铸造工艺设计人员的项目小组进行设计潜在失效模式及后果分析,分析的主要内容应包括铸件质量对产品结构的要求,铸造工艺对产品结构的要求及铸造工艺对环保的要求是否全部满足。
5.1.2 铸件质量对产品结构的要求5.1.2.1 铸件的最小壁厚(见表1)注:为了避免铸件浇不到和冷隔等缺陷,应使铸件的设计壁厚不小于最小壁厚;铸件的最小壁厚还和最小壁厚处所具有的面积有关。
DB32T 3850-2020 有色金属深井铸造工艺安全技术规范
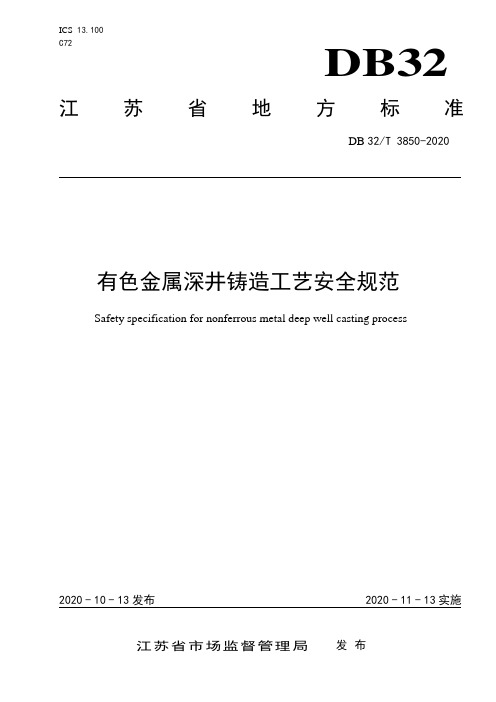
ICS13.100C72 DB32 江苏省地方标准DB 32/T 3850-2020有色金属深井铸造工艺安全规范Safety specification for nonferrous metal deep well casting process2020-10-13发布2020-11-13实施目次前言 (II)1 范围 (1)2 规范性引用文件 (1)3 术语和定义 (2)4 一般(总体)要求 (3)5 厂址选择与工厂总平面布置 (4)6 厂房建筑和作业环境 (5)7 主要生产设备设施 (6)8 应急设施 (9)9 应急管理 (10)前言本标准按照GB/T 1.1-2009 给出的规则起草。
本标准由江苏省应急管理厅提出。
本标准由江苏省安全生产标准化技术委员会归口。
本标准起草单位:江苏省安全生产科学研究院。
本标准主要起草人:匡蕾、胡根林、孙颢、荣铁渝、刘赫、蒋俊、丁锦宣、周应泉、许国兵、吴德军、葛蔚、苏学。
有色金属深井铸造工艺安全规范1 范围本标准规定了涉及有色金属深井铸造工艺生产企业的厂址选择与工厂总平面布置、厂房建筑和作业环境、主要生产设备设施、应急设施、应急管理等通用安全技术要求。
本标准适用于冶金、有色、机械行业涉及深井铸造工艺的有色金属生产企业。
2 规范性引用文件下列文件对于本文件的应用是必不可少的。
凡是注日期的引用文件,仅注日期的版本适用于本文件。
凡是不注日期的引用文件,其最新版本(包括所有的修改单)适用于本文件。
GB 2893 安全色GB 2894 安全标志及其使用导则GB 3095 环境空气质量标准GB 3096 声环境质量标准GB 4387 工业企业厂内铁路、道路运输安全规程GB 5083 生产设备安全卫生设计总则GB/T 5611 铸造术语GB 5768.1 道路交通标志和标线第1部分:总则GB 5768.2 道路交通标志和标线第2部分:道路交通标志GB 5768.3 道路交通标志和标线第3部分:道路交通标线GB 5768.4 道路交通标志和标线第4部分:作业区GB 5768.5 道路交通标志和标线第5部分: 限制速度GB 5768.6 道路交通标志和标线第6部分: 铁路道口GB/T 5976 钢丝绳夹GB 6222 工业企业煤气安全规程GB 7231 工业管道的基本识别色、识别符号和安全标识GB/T 11651 个体防护装备选用规范GB 13495.1 消防安全标志GB 15630 消防安全标志设置要求GB 15763 建筑用安全玻璃GB 17945 消防应急照明和疏散指示系统GB/T 18664 呼吸防护用品的选择、使用与维护GB/T 20801 压力管道规范工业管道GB/T 20801.5 压力管道规范工业管道第5部分:检验与试验GB/T 20801.6 压力管道规范工业管道第6部分:安全防护GB/T 25894 疏散平面图设计原则与要求GB/T 29639 生产经营单位生产安全事故应急预案编制导则GB 30078 变形铝及铝合金铸锭安全生产规范GB/T 30081 反射炉精炼安全生产规范GB/T 33000 企业安全生产标准化基本规范GB/T 33942 特种设备事故应急预案编制导则GB/T 34529 起重机和葫芦钢丝绳、卷筒和滑轮的选择GB/T 38315 社会单位灭火和应急疏散预案编制及实施导则GB 50016 建筑设计防火规范GB 50028 城镇燃气设计规范GB/T 50033 建筑采光设计标准GB 50034 建筑照明设计标准GB 50140 建筑灭火器配置设计规范GB 50187 工业企业平面设计规范GB 50207 屋面工程质量验收规范GB 50482 铝加工厂工艺设计规范GB/T 50493 石油化工可燃气体和有毒气体检测报警设计标准GB 50544 有色金属企业总图运输设计规范GB 50630 有色金属工程设计防火规范GBZ 1 工业企业设计卫生标准GBZ 2.1 工作场所有害因素职业接触限值第1部分:化学有害因素GBZ 2.2 工作场所有害因素职业接触限值第2部分:物理因素AQ/T 7009 机械制造企业安全生产标准化规范AQ/T 9007 生产安全事故应急演练指南AQ/T 9009 生产安全事故应急演练评估规范AQ/T 9011 生产经营单位生产安全事故应急预案评估指南YS/T 12 铝及铝合金火焰熔炼炉、保温炉技术条件DB32/T 3614 工贸企业安全风险管控基本规范3 术语和定义GB/T 5611 界定的以及下列术语和定义适用于本文件。
砂型铸造通用技术规范最新版

砂型铸造通用技术规范最新版砂型铸造是一种常见的铸造工艺,通过在模具中填充砂子并将其固化,然后在固化的砂型中倒入熔融金属,待金属冷却凝固后取出,得到所需产品。
为了确保砂型铸造的质量和效率,制定了一系列的砂型铸造通用技术规范。
一、砂型铸造材料规范1. 砂型铸造用砂应选用合适的砂子,具有良好的耐热性和粘结性,保证铸件的表面质量和尺寸精度;2. 砂型铸造砂子的组成和比例应符合工艺要求,避免因过多的添加剂对铸件质量造成不良影响;3. 砂型铸造砂子的处理要求,如筛选、干燥等,保证砂子的质量和适用性。
二、砂型铸造模具设计规范1. 砂型铸造模型应根据铸件的形状、尺寸和结构特点合理设计,保证铸件的准确度和外观质量;2. 砂型铸造模具应采用适当的材料,具有足够的强度和刚度,可靠地承受铸造过程中的挤压力和热应力;3. 砂型铸造模具的结构应合理,易于脱模,减少破损和报废率。
三、砂型铸造工艺规范1. 砂型铸造工艺中,要控制铸造温度、浇注速度和金属的液态时长,保证铸件的质量和性能;2. 砂型铸造时,要注意金属液流动的方向和填充的均匀性,避免产生气孔、缩松等缺陷;3. 砂型铸造后,要进行适当的铸件清理和修整工作,如修边、抛光等,使其达到要求的外观质量。
四、砂型铸造检测规范1. 砂型铸造铸件的检测主要包括外观检验、尺寸测量和性能试验等;2. 外观检验要求铸件表面光滑,无缺陷和毛刺;3. 尺寸测量要求按照设计要求进行,对于特殊要求的铸件要进行形状测量;4. 砂型铸造铸件的性能试验包括强度、硬度、耐磨性等试验,保证铸件的使用性能。
以上为砂型铸造通用技术规范的主要内容,对于砂型铸造工艺的实施具有指导作用。
不同的铸造企业可以根据自身的实际情况进行相应的调整和补充,以确保铸造的质量和效率。
1.4410铸造标准

1.4410铸造标准本标准旨在规定1.4410铸造的各个方面,包括范围、规范性引用文件、术语和定义、化学成分、铸造工艺、检验规则、试验方法、质量证明文件、包装、标记和存储等。
1.范围本标准适用于1.4410铸造的质量控制和检验。
2.规范性引用文件下列文件对于本文件的应用是必不可少的。
凡是注日期的引用文件,仅注日期的版本适用于本文件。
凡是不注日期的引用文件,其最新版本(包括所有的修改单)适用于本文件。
3.术语和定义3.1 铸造:通过将金属熔炼成液态,倒入模具中,待其冷却凝固后形成铸件的过程。
3.2 铸件:经过铸造工艺得到的具有一定形状和尺寸的金属零件。
4.化学成分1.4410铸造的化学成分应符合相关标准的规定。
具体可参考有关标准或咨询专业人士。
5.铸造工艺5.1 模具设计:根据铸件的要求,设计合理的模具结构。
5.2 熔炼:将金属材料熔炼成液态。
5.3 浇注:将熔炼后的金属液体倒入模具中。
5.4 冷却:使铸件在模具中冷却凝固。
5.5 脱模:从模具中取出铸件。
6.检验规则6.1 外观质量:铸件外观应平整、光滑,无气孔、砂眼、裂纹等缺陷。
6.2 尺寸精度:铸件的尺寸应符合设计要求,允许偏差应在规定范围内。
6.3 化学成分:铸件的化学成分应符合要求,可通过光谱分析等方法进行检测。
6.4 力学性能:铸件的力学性能应符合相关标准的规定,可通过拉伸、冲击、硬度等试验进行检测。
7.试验方法7.1 外观质量:采用目视或放大镜等方法进行检测。
7.2 尺寸精度:采用卡尺、千分尺等测量工具进行检测。
铸造工件设计标准要求有哪些
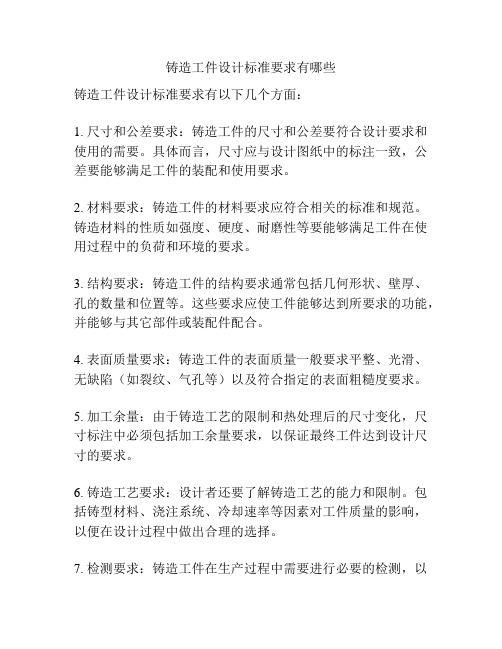
铸造工件设计标准要求有哪些
铸造工件设计标准要求有以下几个方面:
1. 尺寸和公差要求:铸造工件的尺寸和公差要符合设计要求和使用的需要。
具体而言,尺寸应与设计图纸中的标注一致,公差要能够满足工件的装配和使用要求。
2. 材料要求:铸造工件的材料要求应符合相关的标准和规范。
铸造材料的性质如强度、硬度、耐磨性等要能够满足工件在使用过程中的负荷和环境的要求。
3. 结构要求:铸造工件的结构要求通常包括几何形状、壁厚、孔的数量和位置等。
这些要求应使工件能够达到所要求的功能,并能够与其它部件或装配件配合。
4. 表面质量要求:铸造工件的表面质量一般要求平整、光滑、无缺陷(如裂纹、气孔等)以及符合指定的表面粗糙度要求。
5. 加工余量:由于铸造工艺的限制和热处理后的尺寸变化,尺寸标注中必须包括加工余量要求,以保证最终工件达到设计尺寸的要求。
6. 铸造工艺要求:设计者还要了解铸造工艺的能力和限制。
包括铸型材料、浇注系统、冷却速率等因素对工件质量的影响,以便在设计过程中做出合理的选择。
7. 检测要求:铸造工件在生产过程中需要进行必要的检测,以
确保工件的质量。
检测项目包括尺寸、化学成分、物理性质等。
检测方式应符合相关的标准和规范。
8. 标志和标记要求:铸造工件在生产过程中需要进行必要的标志和标记。
这些标志和标记应能够方便工件的使用、识别和追溯。
总之,铸造工件设计标准的要求涵盖了尺寸和公差、材料、结构、表面质量、加工余量、铸造工艺、检测、标志和标记等多个方面,以保证铸造工件的质量和性能符合设计和使用的要求。
- 1、下载文档前请自行甄别文档内容的完整性,平台不提供额外的编辑、内容补充、找答案等附加服务。
- 2、"仅部分预览"的文档,不可在线预览部分如存在完整性等问题,可反馈申请退款(可完整预览的文档不适用该条件!)。
- 3、如文档侵犯您的权益,请联系客服反馈,我们会尽快为您处理(人工客服工作时间:9:00-18:30)。
总则为做到对铸造生产过程的有效控制现对我公司电炉熔化,砂子混制,制芯、造型(机器造型、手工造型)、浇注、清整,6个工序,特制定工艺规范。
(一)电炉熔化工艺规范1.修炉衬1.1炉底打结1.1.1先在紧靠感应圈内壁及炉底处围铺上石棉布,形成绝缘层。
1.1.2把石英砂倒入炉底,每层厚度不超过50mm,用捣固棒捣实,再用平锤打结实。
逐步打结直至把炉底打结到高度。
1.1.3校正中心,安放好坩埚膜。
在坩埚内放入一些重铁块,防止打结时坩埚膜松动。
1.2打结坩埚壁1.2.1在坩埚底与坩埚壁交界处,打结时要特别细心。
1.2.2后每层打结紧实高度为50-60mm,打结时间不少于20分钟。
当坩埚壁打结好后,在修筑炉口之前,要用平锤打实打平。
1.2.3加料时,不许石英砂落入石棉板和云母片(石棉布)等隔热绝缘层中。
1.2.4为使紧实度均匀,应由两人或两人以上站在对称位置转圈打结。
1.2.5在整个打结过程中,要严防杂物掉入硅砂中。
1.3修筑炉口和炉嘴1.3.1用水玻璃做粘结剂,快速成形。
用适量的硼酸水和水玻璃与打结料相混合,待用手一捏基本成团即可。
1.3.2在打好的炉口上涂上适量水玻璃,然后填筑混合料并用小锤打实。
1.3.3炉口和炉嘴修成内低外高的斜面。
1.4 烘炉和烧结1.4.1烘炉前要对冷却水系统、倾炉系统、控制回路及仪表等进行检查。
1.4.2烘炉时应加入一定数量的炉料,以保持温度升降的均匀性。
1.4.3烘炉要按低功率慢升温及材料厂提供的烧结工艺进行。
1.4.4炉衬温度达到1000度以上时,改用功率供电,使坩埚膜和炉料缓慢升温,慢慢熔化以减轻冲刷作用。
1.4.5熔化第一炉时尽量用洁净无锈和杂质的炉料。
1.4.6熔化完第一炉时铁液温度不要超过1550度,保温1-2小时,使炉衬均匀烧结。
1.4.7第一炉铁液化得满一些,使炉口烧结好一些。
整个坩埚由上到下均匀密实烧结。
1.4.8熔化第一炉后,坩埚的烧结层很薄,应连续熔化2-4炉后才能完成烧结过程。
1.4.9烘烧炉时必须按规范进行。
2.修处理包2.1 新包用耐火砖砌筑后用耐火砂打结,然后表面敷上一层焦粉和耐火泥混合料,最后刷一层涂料(铅粉)。
2.2 球化处理包修补时,首先检查浇包的转动机构是否完好,将包内的残渣、余铁及松动包衬清理干净,刷上泥浆水。
需要修补的地方用耐火材料用力搪紧实并刮平,然后再搪一层焦粉和耐火泥混合料并刷上涂料。
包嘴处修补时应搪牢固、光滑。
2.3 球化处理包修补好后要按规定尺寸进行检查,避免容量发生波动。
处理包修理尺寸见下表:浇包容量内径深度堤坝高度3.电炉操作和维修3.1检查炉衬磨损情况,及有无裂缝。
3.2确保冷却水畅通、控制柜线路无异常。
3.3按配料单称料。
3.4禁止加入带有铁锈其他合金或潮湿的料,以防在炉内爆炸和侵炉。
3.5加入少量炉料后接通电源。
熔化第一炉时应先低功率进行加热,以后逐步提高功率加热。
3.6第二炉可以直接调至最高功率加热熔化。
3.7在熔化过程中应经常检查水路是否畅通,出水温是否低于55度,上水温度不得超过30度。
3.8经常观察控制柜的功率表并根据功率大小及熔化情况加料。
由于晶闸管过载能力低,故不允许过载使用。
3.9不管炉料如何,都要在前次投入的料没有熔化完之前投入下一次炉料。
3.10熔炼过程中不允许机内带电体或炉子感应圈有接地或短路现象发生。
3.11当炉内铁水熔化满后,先清渣后保温升温。
3.12在升温期间,应用热电偶测温和用CE表测定铁水的C、Si值。
3.13当铁水温度和成分均合格后即可出炉。
3.14每一班次的最后一炉应将炉内铁水出尽,关闭控制柜电源。
但电炉循环水不能停,继续运转40分钟,待炉内温度达到恒温后方可关闭。
3.15如果在熔化过程中突然停电,应及时清除炉内铁水和炉料并立即将备用水管节门打开以保证感应线圈内有循环水。
3.16平时要经常检查炉壁、炉口、炉嘴的损坏情况,及时进行维修。
3.17熔化过程中,应防止炉内棚料,用钎子直接去捅料,让其自然下行熔化。
3.18每月检查一次电路、水路,清除机内尘土灰垢,发现腐蚀松动现象应修整后再使用。
3.19要保持控制室干净、明亮、整洁。
4.铁水成分控制及球化处理4.1原铁水成分控制的目标值为4.2当铁水温度达到1450℃以上时,通过CE表测定原铁水的碳硅值,若超出规定范围,应进行成分调整并进一步测定碳硅值,直至符合目标值为止。
4.3将球化剂、孕育剂和覆盖剂依次放入球化包的反应堤坝内,并依次用捣锤捣实。
4.4当铁水成分和温度均达到要求时,将400公斤铁水倒入球化包中,但应避免铁水直接冲向球化剂(应冲入对面的堤坝里),同时将孕育剂随流均匀加入,进行孕育处理。
必须保证400KG铁水出到位后,包内球化剂才开始起爆反映;若铁水到位后20秒内没有起爆,应用铁钎对准球化剂用力扎两下引诱起爆。
用铁板将反应包盖住进行球化反应。
4.5球化反应时间应在40-80秒之间。
4.6反应处理结束后,用珍珠岩扒渣3-4次,将渣扒净后,再将铁水表面覆盖上一层后珍珠岩(加入量大概是每次扒渣时加入量的两倍),然后浇注。
在浇注过程中若珍珠岩层破裂,应不断加入珍珠岩使结成新膜。
应在8分钟内将全部铁水浇完。
在熔化过程中,操作者必须将有关数据填入《电炉熔解日报》(LSA-013)(二)浇注工艺规范1 准备工作1.1 每天浇注前检查浇包是否烘干,浇口嘴是否圆滑,平整。
1.2 集渣剂是否备齐,扒渣工具是否准备好。
1.3 需加冷铁的产品是否备齐,用废的铸件代替冷铁。
1.4 压铁卡子、套箱准备齐全。
2 浇注2.1 出炉的第一包铁水用于浇注不重要铸件。
2.2 浇注工要熟知所要浇注产品的重量,浇注温度,浇注速度。
2.3每接一浇包铁水后都要均匀撒满集渣剂,并用扒渣机在浇嘴处扒净。
2.4 浇注温度按产品工艺要求严格控制。
2.5 包嘴离浇口杯的高度,一般控制在150—200MM之间。
2.6 浇注时浇口杯应保持常满,正常情况下浇注不应中断。
浇注时浇口杯内不得产生旋涡、飞溅和外溢。
2.7 两个浇包同时浇一个铸件时,开始浇注时间、浇注速度和温度等应尽量相同,浇注后应同时收包。
2.8 壁厚大的和有特殊要求的铸件,在浇满后应进行充分的补浇,或根据工艺要求从冒口补浇。
2.9 浇包应经常保持清洁完整,如损坏或结渣太多应修好和清理干净后继续使用。
浇注后剩余的铁水或温度太低不能浇成的铁水倒回推包,由推包推到低温铁砂模处浇成铁锭作压铁使用。
2.10 浇注后不得小于30分钟开箱,特殊件可再长一些。
2.11 浇注后如有跑铁水现象立即用砂将跑铁水处堵住和将由铁水引燃的托板压灭。
2.12 浇注完毕后,将浇注工具集中保管,压铁、套箱、卡子整齐码放到固定地点,以备下次再用。
2.13 浇注完毕后将浇包内包衬砸掉、清净,从新修好、烘干,待明日再用。
3 生产安全3.1 工作前应穿戴好劳动保护用品。
3.2 浇包要安全可靠。
3.3 浇包接铁水时不要盛得太满。
3.4 浇注过程精力集中不要窥视冒口。
3.5 搬压铁倒箱时,小心谨慎,轻拿轻放。
3.6 浇注结束后清理现场。
4 岗位职责4.1 浇注工必须全面熟悉浇注铸件的工艺文件和工艺守则。
4.2 清除浇注通道的不安全因素。
4.3 备好集渣剂、扒渣工具等。
4.4 浇注时按铸造守则规定各项认真执行。
4.5 浇注完毕全面检查,清理场地,熄灭火源。
4.6 浇注发现异常现象立即通知工段长,提出解决措施。
4.7 发生成批不合格只要认真分析,由浇注所造成的废品原因,提出纠正和预防措施。
(三)造型工艺规范1. 造型机造型工艺守则1.1 准备工作1.1.1 造型前应熟悉该产品的生产注意事项和各项要求。
1.1.2 使用固定铁砂箱前要用试棒、卡尺检查砂箱销眼,销眼(Ф20±0.05),销子(Ф19.9±0.05)有无超差1.1.3 使用活脱箱和可拆箱的工装时检查销母和导销是否已磨损严重,有异常现象需调整销母,防止错箱。
上下二扇接缝是否平整,不平整需修理。
有异常现象需调整销母,防止错箱。
1.1.4 检查设备震实、压实、起模机构是否正常。
使用148C,145带起模装置的造型机时还要检查起模是否平稳、垂直。
1.1.5模板翅曲量不得大于1mm,木质模板与砂箱接触面磨损量不得大于1mm。
1.1.6 检查型板模样有无破损、缺残、裂纹、变形。
1.2 造型1.2.1使用铁砂箱造型时,将砂箱用定位销定位平稳放到模板上,千万不要碰模板和定位销。
1.2.2 造型时必须用筛子筛靠模砂再向砂箱内填加,震实3次用砂冲扁头将模样周围舂实,再填背砂震实5—6次后压实,对于特殊产品必要时用风动捣固器,震捣砂子,如不需用砂冲舂实可将砂子铺匀,震动10次左右后压实,保证砂型硬度。
1.2.3 有活块的型板填砂前先将活块周围用砂塞实,吃砂量过大或深凹棱角处要放砂钩或钉子加固。
1.2.4 对于箱带下面的型砂不易舂实,填砂后用两手将箱带下面的砂型按紧。
1.2.5 扎气眼每100X100平方毫米不少于两个,气眼针直径Ф4—8mm,扎入深度应离模样表面15—30 mm,暗冒口顶部应扎气眼。
1.2.6 起模不能扒箱,如有扒箱严重,弃掉从新造型,轻微要修型,修型要求面平、线直、孔圆、角方,轮廓清晰,尺寸符合要求。
1.2.7 放型地面铺上一层10—20mm厚砂子,用刮砂齿板刮匀,将下扇平整放上,用皮老虎将表面浮砂吹净后平稳合箱。
1.2.8 使用活脱箱和可拆箱造型时,除和用铁砂箱造型共同之处遵守上述要求外,注意以下几点:a) 合箱前每扇都用气嘴吹掉型面和水口浮砂。
b) 每炉要检查砂箱销子和销母是否错位,以防错箱。
c) 下芯之前要认真检查芯子,下芯后用气再吹一下。
d) 脱箱时要轻砸砂箱,防止错箱和掉砂。
如砂箱不易脱掉,适当在砂箱内壁薄薄涂一层脱膜剂。
e) 脱板要平整,砂型要码放整齐准备浇注。
2 手工造型工艺守则2.1准备工作2.1.1 造型前要熟悉该产品的生产注意事项。
2.1.2 模样应齐全完整,地势板应和模样配合紧凑。
2.1.3 检查模样的起模、敲模装置是否齐备,分模定位装置是否合适精确。
2.1.4 检查砂箱尺寸及吃砂量是否符合工艺要求,配置好适宜的砂箱。
2.1.5 检查造型底板是否平直、坚固,尺寸是否符合工艺要求。
2.1.6 检查型砂、面砂是否符合工艺要求,有疑问时,委托型砂试验室试验。
2.2 造型2.2.1 造型底板应放平稳和清理干净并擦净模样上粘砂。
2.2.2 砂型吃砂量较大或容易脱落的地方,应下铁钉。
2.2.3 使用面砂厚度约为铸件壁厚的1—1.5倍,或根据工艺要求。
2.2.4 对浇冒口处用手工适当捣实,拔出浇口模样后用手拍实防止浇注冲砂。
2.2.5 不准填入干湿不均匀的或热的型砂,手工舂实度要均匀合适,一般控制在70—85硬度单位。
2.2.6 需要放置芯撑的砂型,应在造型前考虑好放的位置,以防砂型磕崩。