桥壳铸造工艺设计规范
铸钢车桥铸件技术规范

铸钢车桥铸件技术规范铸钢车桥铸件技术规范一、铸件第一次抛丸1、铸件经第一次抛丸,粘砂90%以上基本抛干净,允许拐角有不超过2毫米厚的粘砂。
2、浇冒口切割线的粘砂要彻底清除干净。
二、表面质量1、非加工面1.1表面粗糙度:连片和单个小刺高于基面1.5毫米要磨除1.2浇冒口痕迹、披缝、多肉、粘砂、氧化皮必须清除1.3冷隔凹陷的痕迹长小于40毫米,深小于1毫米不焊补。
长大于40毫米一律焊补。
1.4错箱值不大于2毫米。
1.5铸件弯曲变形量不影响整体机械加工。
1.6热处理后铸件焊补可不进行二次热处理2、加工面2.1浇口、冒口痕迹、披缝、多肉长度小于80毫米,凸出要小于3毫米;长度大于80毫米,凸出要小于5毫米。
2.2 凹陷不超过所在平面加工余量2/3.2.3 热处理后再焊补要进行二次低温热处理。
三、不允许存在的缺陷1、铸件不得有未经修补、影响使用寿命的裂纹、冷隔、缩松,夹砂等缺陷。
2、铸件不得有较大连片密集气孔、缩孔、砂眼和铁豆;3、铸件不得有危及与该铸件直接配合的零件寿命的任何铸造缺陷;4、铸件不得有不符合图样和技术要求的其他缺陷。
四、允许存在无须修补的缺陷1 在非加工面上:1.1单个缺陷(砂眼、气孔)小于5毫米,深度小于壁厚的1/4,在直径100毫米圆内小于5个,一般一个独立表面总数不多于12个,间距大于10毫米1.2 缩孔、缩松不大于该处热节圆1/42 在加工后存在的缺陷:2.1非主要工作面上孤立的圆滑的凹孔、非裂纹式沟槽,缺陷不大于5毫米。
深度小于该壁厚的1/4,数量在直径100毫米圆内小于4个,一个独立表面上不多于10个,间隙大于40毫米。
2.2 主要工作面上孤立的圆滑的凹孔、非裂纹式沟槽,缺陷不大于3毫米,深度小于3毫米,总面积不超出所在面的1%,间隔大于40毫米。
注:以上凹陷的缺陷,也可以用金属修补胶进行修补。
五、铸件尺寸公差应符合图纸的技术要求六、铸件重量公差±3%七、铸件化学成分和力学性能、金相组织、硬度7.1 化学成分(%)①残余元素总量不超过1%② ZG35Mn为广西方盛厂家专用的材质7.2 机械性能注:⑴ZG270—500,适用于厚度小于等于100mm的铸件,当铸件厚度超过100mm时,表中的σ0.2仅供设计使用。
508 桥壳总成工艺规程与镗夹具设计

摘要本文主要介绍了桥壳总成的相关知识,根据桥壳总成的结构和特点,在进行专门研究 的基础上制订出该部件的加工工艺路线,选择、计算各工序主要参数及选出加工设备,填 写加工工艺规程,设计针对该构件的专用夹具。
在确定了桥壳总成初步设计方案后,决定采用传统理论方法对桥壳总成的结构进行设 计、计算,并采用AutoCAD设计软件对桥壳总成、夹具、进总装图等行了工程绘图。
而后 又对桥壳总成的工艺规程进行了编排;在查阅了大量关于桥壳总成设计的书籍后,确定桥 壳总成的设计方案,绘制了桥壳总成夹具装配图,给出了桥壳总成工艺规程的说明书,并 对整个设计进行系统分析,得出整个设计切实可行。
关键词 桥壳总成;夹具;工艺规程AbstractThis paper describes the axle housing assembly of the relevant knowledge, according to Shell assembly of the bridge structure and characteristics in the field on the basis of the developed parts of the processing line, choose to calculate the main parameters of the processes and equipment, fill out the processing Of a point of order, designed for the dedicated members of the fixture. In determining the bridge shell assembly preliminary design options, decided to adopt the traditional theory of the bridge shell assembly and structure of the transmission system design, calculation, the intensity of checking and use of AutoCAD design software to bridge shell assembly, fixture, The General Armament Department plans to carry out the engineering drawings. Shell on the bridge and then the assembly of a scheduling order in check a large number of shell assembly on the bridge design books, determine the design of the bridge shell assembly programme, rendering the bridge shell assembly fixture assembly, are given Bridge shell assembly process of order brochures, and the design of systems analysis, that the whole design practical..Keywords Axle housing assembly Fixture Engineering procedure目 录1 绪论 (1)1.1 车桥发展概况 (1)1.1.1 车桥的技术进展 (1)1.2 车桥结构及其功能 (6)1.2.1 主要技术参数 (6)1.2.2 产品结构介绍 (6)2 桥壳总成加工工艺规程制订 (10)2.1 车桥制造 (11)2.1.1 车桥制造原材料 (11)2.1.2 用无缝钢管冲压桥壳 (11)2.1.3 桥壳毛坯的设计 (13)2.2 驱动桥壳工艺设计 (15)2.3 驱动桥壳强度计算 (17)2.4 驱动桥壳的焊接方案 (18)2.5 桥壳总成的工艺路线制订 (20)2.6 桥壳总成的工序卡片编制 (26)3 桥壳总成镗夹具设计 (28)3.1 镗大孔夹具工装设计 (28)3.1.1 定位基准的选择 (28)3.1.2 机床的选择 (28)3.1.3 夹具的设计 (31)结论 (34)致谢 (35)参考文献 (36)附录 (37)附录1 (37)附录2.................................................. 错误!未定义书签。
铸造工件设计标准要求有哪些
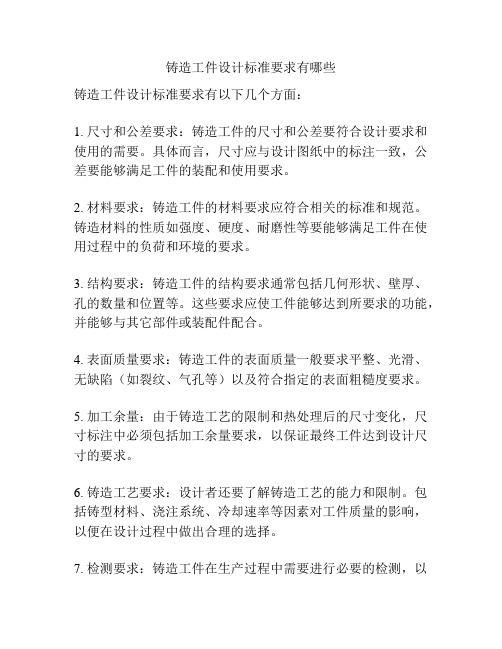
铸造工件设计标准要求有哪些
铸造工件设计标准要求有以下几个方面:
1. 尺寸和公差要求:铸造工件的尺寸和公差要符合设计要求和使用的需要。
具体而言,尺寸应与设计图纸中的标注一致,公差要能够满足工件的装配和使用要求。
2. 材料要求:铸造工件的材料要求应符合相关的标准和规范。
铸造材料的性质如强度、硬度、耐磨性等要能够满足工件在使用过程中的负荷和环境的要求。
3. 结构要求:铸造工件的结构要求通常包括几何形状、壁厚、孔的数量和位置等。
这些要求应使工件能够达到所要求的功能,并能够与其它部件或装配件配合。
4. 表面质量要求:铸造工件的表面质量一般要求平整、光滑、无缺陷(如裂纹、气孔等)以及符合指定的表面粗糙度要求。
5. 加工余量:由于铸造工艺的限制和热处理后的尺寸变化,尺寸标注中必须包括加工余量要求,以保证最终工件达到设计尺寸的要求。
6. 铸造工艺要求:设计者还要了解铸造工艺的能力和限制。
包括铸型材料、浇注系统、冷却速率等因素对工件质量的影响,以便在设计过程中做出合理的选择。
7. 检测要求:铸造工件在生产过程中需要进行必要的检测,以
确保工件的质量。
检测项目包括尺寸、化学成分、物理性质等。
检测方式应符合相关的标准和规范。
8. 标志和标记要求:铸造工件在生产过程中需要进行必要的标志和标记。
这些标志和标记应能够方便工件的使用、识别和追溯。
总之,铸造工件设计标准的要求涵盖了尺寸和公差、材料、结构、表面质量、加工余量、铸造工艺、检测、标志和标记等多个方面,以保证铸造工件的质量和性能符合设计和使用的要求。
桥壳总成工艺规程与钻夹具设计

摘要后桥是汽车的基本零件之一,后桥主要由主减速器、差速器、半轴、桥壳、轮毂制动鼓总成、制动器等组成,其功能是将万向传动装置传来的发动机扭矩传给驱动车轮。
输入的扭矩首先传给主减速器,在此增大扭矩并改变方向,然后经差速器分配给左、右半轴,最后通过半轴外端的法兰盘传给驱动车轮的轮毂。
后桥的加工质量直接影响后桥的装配质量,进而影响汽车的使用性能和寿命。
本课题进行汽车后桥钻孔专用夹具设计,主要步骤和内容分为:1)车桥的毛坯制定。
在分析了车桥的具体结构及其尺寸精度要求的基础上,绘制出毛坯图。
2)车桥总成工艺设计。
在毛坯图的基础上,根据桥壳总成零件图上各尺寸精度要求,详细制定了车桥加工工艺路线 (包括工件定位、夹紧、加工刀具的选择、切削用量的确定、切削力与切削功率的计算等)。
3)钻模夹具的设计。
根据被加工零件的结构特点、加工内容的尺寸和精度要求,确定钻模夹具的配置方案。
对钻模夹具进行总体设计,并绘制装配图。
4)气缸的选用。
根据弹簧选中选出合适的汽缸,绘制其零件图。
关键词:车桥;毛坯;工艺;钻模夹具;汽缸ABSTRACTThe bridge is one of the basic spare partses of car. The bridge is mainly from lord decelerate machine, the machine, half stalk, bridge hull, round drum system moving with drum total become, making to move machine's etc. to constitute. Its function is ten thousand to spread to move equip to spread of launch machine to twist to pass to drive car wheel.Importation of twist to pass a lord deceleration machine first, at this enlarge twist combine change direction, then through bad soon machine allotment give left and right half stalk, passing half stalk outside carry of the method orchid dish pass to drive a felloe round drum.Empress the bridge process quality direct influence behind bridge of assemble quality, then influence car of usage function and life span.This topic carry on empress the car bridge to drill a hole the design, main step and contents of the appropriation tongs to is divided into:1)the semi-finished product establishment of the car bridge.At analysis the concrete structure of the car bridge and the foundation of the its size accuracy request up, draw a semi-finished product diagram.2)the car bridge is total to become a technological design.On the foundation of semi-finished product diagram, according to bridge hull total become spare parts diagram up each size accuracy request, detailed establishment the car bridge process craft route.(include a work piece fixed position and clip tight, process knife of choice, slice to pare dosage really settle, slice to pare dint with slice to pare power of calculation etc.)3)drilling the design of mold tongs.According to is processed the structure characteristics of spare parts and process size and accuracy request of contents, assurance drill the allocation project of mold tongs.Carry on a total design towards drilling mold tongs, and draw to assemble diagram.4)the air cylinder choosing to use.Pick out cylinder of select the accommodation according to the spring coil, draw its spare parts diagram.Keyword:Car bridge mi-finished product aft;Drill mold tongs linder目录1绪论 (1)1.1车桥发展概况 (1)1.1.1车桥发展及其现状 (1)1.1.2本论文的主要工作 (3)2桥壳加工工艺规程制订 (4)2.1零件的功用 (4)2.1.1车桥结构及其功能 (4)2.1.2零件的工艺分析 (6)2.2工艺规程设计 (8)2.2.1确定零件生产类型 (8)2.2.2确定零件毛坯的种类及制造方法 (9)2.2.3定位基准的选择 (9)2.2.4零件各表面加工顺序的确定 (10)2.2.5拟定工艺路线 (10)2.2.6毛坯余量和工序间余量的确定 (13)2.2.7驱动桥壳的焊接方案 (13)2.2.8桥壳加工热处理工艺要求 (16)2.3切削用量和时间定额的确定 (18)2.3.1切削用量的选择原则 (18)2.3.2切削用量和时间定额 (18)3.指定工序夹具设计 (24)3.1钻攻大面夹具工装设计 (24)3.1.1机床的选择 (24)3.1.2钻模夹具的选择 (24)结论 (34)致谢 (35)参考文献 (36)附录....................................................... 错误!未定义书签。
铸造桥壳柔性生产线总体技术要求

铸造桥壳柔性生产线总体技术要求一、概述本设备主要用于车桥的加工。
设备要求高精度、高可靠性,结构合理,有足够的静态、动态、热态刚度,并能采用先进技术,保证系统具有良好的动态品质。
机床的使用、操作、维修方便,造型美观,售后服务优良。
本设备为交钥匙工程,工装夹具设计制作、刀具配置均由卖方完成。
二、产能说明3万件/年,300天6000小时,81%工作效率。
三、总体要求:1.生产线包含夹具及刀辅具,实行交钥匙工程,供应商对所供产品的适用性,正确性负责。
2.车桥加工长度兼容范围:1300∽1680mm3.全线共需配备CF、USB接口、配有以太网接口。
同时预留与机器人连接的IO电源模块及通讯接口。
4.方案制作时须体现工艺节拍,装夹时间(预估)与加工时间需分别体现。
四、设备使用环境:电源:电压:380伏±15%;频率:50赫兹±3%;压缩空气:压力:0.3-0.7Mpa,温度:-10℃-40℃;湿度:小于90%;五、加工零件图号、名称:SJ1080-025B.2 后桥壳体SJ1098-2401015F.1-DT 后桥壳体材料:QT450-10单边加工余量:不大于5mm六、夹具夹具设计、制造由供货方负责。
采用液压夹紧方式。
夹具方案设计完成后,须和订货方会签,获得订货方同意后方可投入制造,但供货方对夹具的正确性、可靠性、稳定性、适用性负责。
夹具经少量调整或更换定位元件便能完成多规格车桥不同的加工。
七、液压系统独立液压站,所有液压元件采用符合ISO标准的叠加阀,性能可靠,液压油箱中的油位可以从游标中观察,换油和放油非常方便;加油处有可靠的过滤装置;液压管应尽量做到横平竖直,安全美观可靠。
八、电气系统机床电器柜采用独立的全封闭结构,采用空中走线,保证密封性能可靠,防止粉尘进入。
用换气扇控制电器柜内的温度,保证各电器元件及系统工作时不因发热而产生故障。
整个电器系统符合国家标准,维修方便,连续运转稳定可靠。
铸造工件设计标准规范最新版

铸造工件设计标准规范最新版铸造工件设计标准规范最新版铸造是一种常见的制造工艺,用于制造各种工件和零件。
为了保证铸造工件的质量和性能,需要遵循一定的设计标准规范。
以下是最新版的铸造工件设计标准规范。
1. 材料选择铸造工件的材料选择应根据工件的使用条件和要求进行合理选择。
常用的有灰铁、球墨铸铁、合金铸铁、铝合金等。
在选择材料时要考虑其机械性能、耐磨性、耐蚀性和可加工性等因素。
2. 设计尺寸铸造工件的设计尺寸应符合工件的使用要求和制造工艺的要求。
设计尺寸时要考虑到热胀冷缩、砂芯融化收缩等因素,合理确定缩小量和公差。
3. 结构设计铸造工件的结构设计应具有合理的结构形式和几何形状,以保证工件的强度和刚度。
同时要尽量避免出现过于复杂和薄壁结构,以免影响铸造工艺和热处理工艺的实施。
4. 浇注系统设计铸造工件的浇注系统设计应合理确定浇注口、冲压头和灌注系统等部件的位置和形式。
浇注系统应保证流体金属能够顺利地填充整个铸模,避免产生砂眼、夹杂和缺陷等。
5. 管理设计铸造工件的管理设计应考虑到工件的加工性能和使用要求,合理确定表面粗糙度和加工余量。
同时要考虑到工件的热处理和表面处理等工艺要求。
6. 检测评定铸造工件的检测评定应根据工件的使用要求和质量标准进行。
常用的检测方法有目测检测、尺寸检测、化学成分分析、力学性能测试和无损检测等。
综上所述,最新版的铸造工件设计标准规范要求在材料选择、设计尺寸、结构设计、浇注系统设计、管理设计和检测评定等方面进行合理的设计和要求。
通过遵循这些标准规范,可以保证铸造工件的质量和性能,提高工件的使用寿命和安全性。
汽车桥壳的结构设计及制造工艺制定
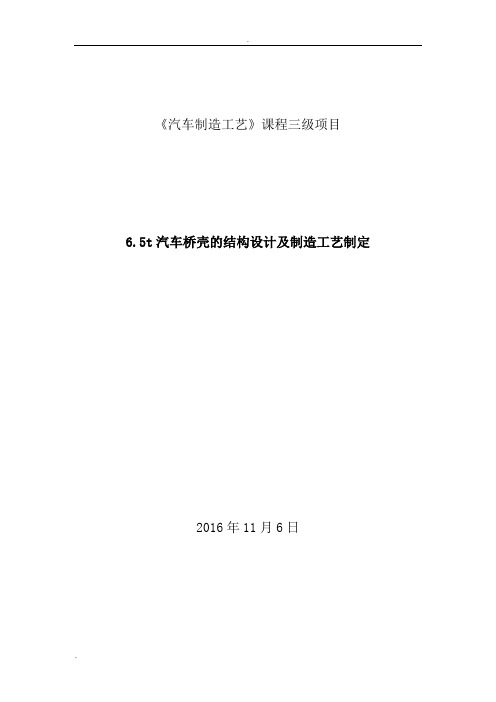
《汽车制造工艺》课程三级项目6.5t汽车桥壳的结构设计及制造工艺制定2016年11月6日目录一、汽车桥壳的功能及特征分析 (3)1.汽车桥壳的主要功能 (3)2.汽车桥壳的种类及特征 (3)二、汽车桥壳冲压焊接制造方法简述 (4)三、汽车桥壳冲压焊接工艺设计 (5)四、汽车桥壳冲压焊接工艺工序图的绘制 (7)五、材料利用率计算及成本预测 (8)1.材料利用率计算 (8)2.成本预测 (8)六、汽车桥壳的强度计算及校核 (8)七、汽车桥壳的结构设计 (11)八、项目心得体会 (12)九、参考资料 (12)一、汽车桥壳的功能及特征分析1.汽车桥壳的主要功能1、和从动桥一起承受汽车质量2、使左、右驱动车轮的轴向相对位置固定3、汽车行驶时,其作为行驶系的组成部分时功用主要是安装悬架或轮毂,支撑汽车悬架以上各部分重量,承受驱动轮传来的反力和力矩,并在驱动轮与悬架之间传力2.汽车桥壳的种类及特征1、铸造式桥壳整体铸造式桥壳是汽车发展史上最早采用的结构,整体铸造桥壳优缺点都较为明显。
整体铸造式桥壳可采用可锻铸铁、球墨铸铁以及铸钢铸造,为进一步提高整体铸造式桥壳的刚度和强度,还可以在整体铸造式桥壳两端压入较长的无缝钢管作为半轴套管,并用销钉固定。
整体铸造式桥壳的主要优点在于刚性好、塑性变形小、强度高、易铸成等强度梁,可根据各截面不同的强度要求设计铸造不一样的壁厚。
其缺点是弹性及韧变较冲焊桥壳差、铸造质量不易保证,且整体质量大、成本较高,不适合整车进行轻量化及降低成本设计。
2、冲压焊接式钢板冲压焊接式整体桥壳主要组成部分包括上下对焊的一对桥壳主件、两个突缘、四块三角钢板、两个半轴套管、加强圈、一个后盖以及两个钢板弹簧座,整体沿其间接缝组焊而成。
桥壳主件是由钢板冲压而成的上下两半桥壳,具体焊接方法可将桥壳主件(上、下半壳)与半轴套管间对焊,也可以将上、下桥壳主件两侧的半圆形端部与半轴套管内端的外圆对其贴紧,沿接缝焊一圈,伴以塞焊。
铸造工程施工规范标准

铸造工程施工规范标准第一章总则第一条为了规范铸造工程施工活动,保证工程质量,确保工程安全,提高工程效益,制定本规范。
第二条本规范适用于金属、非金属及合金的铸件,不适用于特种铸件的生产。
第三条本规范所称的铸造工程施工是指在既定的工艺、条件下,根据设计和技术要求用金属或非金属的熔融物质倒入砂型、金属型或其他型腔中,在凝固和冷却后获得所需的铸件的施工过程。
第四条铸造工程施工应符合设计规范的要求,按照技术标准和相关标准进行。
第五条铸造企业应当按照设计规范的要求,在设备、工艺和材料的选择上履行职责。
第六条铸造工程施工应当按照相应的施工组织设计,确保施工过程顺利进行。
第七条铸造工程施工应当严格遵守国家有关环保、安全和劳动保护法规,保护环境,保障人身和财产安全。
第八条铸造工程施工单位应当具有相应的职业资格,并有经验丰富的技术人员负责检查。
第二章施工组织和施工准备第九条铸造工程施工前,应编制施工组织设计,并报相关主管部门备案。
第十条铸造工程施工前,应制定详细的施工计划,并安排专人负责监督执行。
第十一条铸造工程施工前,应对施工现场进行勘察,确定有关设施和条件是否符合要求。
第十二条铸造工程施工前,应对所需的设备、材料和人员进行统一调配,确保施工顺利进行。
第十三条铸造工程施工前,应对施工现场进行安全检查,消除安全隐患,保障施工安全。
第十四条铸造工程施工单位应配备齐全的施工人员,确保施工过程能够按照计划进行。
第十五条铸造工程施工单位应当为施工人员提供必要的劳动防护用具,并进行相关安全教育。
第十六条铸造工程施工单位应当按照设计要求和施工计划准备好所需的砂型、金属型、熔炉等设备和材料。
第三章铸造工艺控制第十七条铸造工程施工应按照设计规范要求进行模具骨料的混合比例和制备。
第十八条铸造工程施工应根据不同的铸件要求选用不同的浇注方式和工艺。
第十九条铸造工程施工应严格控制熔铸温度和熔铸时间,确保熔铸物质的均匀稳定性。
第二十条铸造工程施工应按照设计规范要求进行浇注、冷却和清理。
- 1、下载文档前请自行甄别文档内容的完整性,平台不提供额外的编辑、内容补充、找答案等附加服务。
- 2、"仅部分预览"的文档,不可在线预览部分如存在完整性等问题,可反馈申请退款(可完整预览的文档不适用该条件!)。
- 3、如文档侵犯您的权益,请联系客服反馈,我们会尽快为您处理(人工客服工作时间:9:00-18:30)。
桥壳铸造工艺设计规范1适用范围本标准适用于铸钢桥壳工装、模具、检具等设计制图及铸造工艺设计工作规范。
2规范性引用文件下列文件中的条款通过本标准的引用而成为本标准的条款。
凡是注日期的引用文件,其随后所有的修改单(不包括戡误的内容)或修订版均不适用于本标准。
然而,鼓励根据本标准达成协议的各方研究是否可使用这些文件的最新版本。
凡是不注日期的引用文件,其最新版本适用于本标准。
GB/T 6414-1999 JB/T 5106-1991 《铸件尺寸公差与机械加工余量》《铸件模样型芯头基本尺寸》GB/T 11351-1989 《铸件重量公差》3术语和定义3.1铸件的最小壁厚:在一定的铸造条件下,铸造合金液能充满铸型的最小厚度。
3.2铸件的临界壁厚:当铸件的厚度超过了一定值后,铸件的力学性能并不按比例地随着铸件厚度的增大而增大,而是显著下降,存在一个临界厚度。
3.3铸钢件相对密度:浇注钢液重量与铸件三个方向最大尺寸的乘积之比。
因而往往小于铸件密度。
3.4吃砂量:模样与砂箱壁、箱顶(底)、和箱带之间的距离。
4铸造工艺设计原则4.1铸造工艺设计必须满足产品铸件质量和对环保的要求,有利于实现优质、高产、低耗,改善劳动条件,安全生产,提高生产标准化、通用化、系列化水平;4.2铸造工艺设计必须能够提供清晰、完整、正确、统一的资料输出:过程流程图、铸造材料清单、过程潜在失效模式及后果分析(PFME)、控制计划、铸造工艺图、铸造工艺卡、作业指导书等。
5铸造工艺设计程序 5.1铸件结构工艺和铸件的先期质量策划5.1.1铸造产品的设计阶段,应组成产品设计人员和铸造工艺设计人员的项目小组进行设计潜在失效模式及后果分析,分析的主要内容应包括铸件质量对产品结构的要求,铸造工艺对产品结构的要求及铸造工艺对环保的要求是否全部满足。
5.1.2铸件质量对产品结构的要求5.1.2.1 铸件的最小壁厚(见表1)表1砂型铸造铸钢件的最小壁厚注:为了避免铸件浇不到和冷隔等缺陷,应使铸件的设计壁厚不小于最小壁厚;铸件的最小壁厚还和最小壁厚处所具有的面积有关。
对于铸钢桥壳其处在桥壳上下法兰之间各处壁厚应不小于12mm后盖处顶面的壁厚应不小于15mm后盖侧面的壁厚局部可以12mm以上 5.122 铸件的临界壁厚(见表2)表2碳素钢铸件砂型铸造的临界壁厚注:砂型铸造各铸造合金铸件的临界壁厚也可按其最小壁厚的3倍来考虑。
5.1.2.3 铸件壁的过渡和连接5.1.2.3.1 一般情况下,铸件壁的断面尺寸不可能完全相同,同时铸壁有类型各异的接头, 铸壁的连接形式,按减小产生应力集中、裂纹、变形、缩孔、缩松等缺陷的原则,依次考虑采用L形、T形、V形、丫形和十字形。
5.1.2.4 铸造内圆角(见表3)表3铸造内圆角注:高碳钢和高锰铸件的R值需增大1.3-1.5倍5.1.2.5 铸造外圆角(见表4)表4铸造外圆角5.1.3铸造工艺对产品结构的要求5.131简化或减少分型面的铸件结构5.1.3.2 减少砂芯数量的铸件结构5.1.3.5方便起模的铸件结构5.1.3.4有利于砂芯的固定和排气的铸件结构5.1.3.5 需设置铸造工艺孔的铸件结构5.1.3.6 有利于铸件清理的铸件结构5.1.3.7有利于满足铸件尺寸公差的铸件结构5.1.4铸造工艺对环保的要求5.1.4.1降低熔炼能耗:合理设计工序流程;炉料入炉前进行预处理等5.1.4.2提高工艺出品率,以降低单位重量铸件在金属熔化过程中得能耗5.1.4.3 优化产品结构,以减少水玻璃废砂的产生5.1.4.4 原辅材料尽量使用,无有害气体产生的材料5.2浇注系统的设计5.2.1桥壳分型面设置在桥壳两端轴孔中线处,浇注系统采用中注半封闭式,即A直〈 A黄;A黄〉A内; A直〉A内,阻流断面设置在横浇道中,阻流断面之前封闭,其后开放。
5.2.2浇注系统总断面比为内浇道:横浇道:直浇道=1: (0.8-0.9 ) : (1.1-1.2 )5.2.3内浇道厚度应小于铸件壁厚的0.7倍以下,才不至于引起内浇道缩孔。
5.2.4浇注时间t= C G L;阻流断面面积或内浇道面积A阻=G L/tkS 'G L是浇注钢水的重量;K浇注比速;S’金属液流动系数,碳钢取1.0,高锰钢取0.8 ; t 浇注速度表5系数C、K值525桥壳浇注系统,由浇口杯、直浇道、横浇道、内浇道、集渣包、阻流块、冒口、缓流涡、出气孔组成。
526内浇口的设置位置在桥包过渡大R弧至上拖板之间的上箱,桥包偏心的桥壳一般设置在对应位置的长边。
5.3砂箱中铸件数量及排列的确定5.3.1按铸件重量确定最小吃砂量,见表 6 (单位mm表6A~ A532铸件在砂箱中的排列最好按对称排列方式。
5.4工艺参数确定5.4.1我司铸件尺寸公差按 CT10-12级执行,铸件的公差带一般应对称于铸件基本尺寸设置,即公差数值的一半取正值,一般取负值。
有特殊要求时,另外注明。
表7铸件尺寸公差等级542铸件的壁厚尺寸公差,可以比一般尺寸公差降一级执行。
543铸件错箱量必须保证在铸件尺寸公差等级数值范围内,有特殊要求时,另外注明表8错箱值544铸件重量公差5.441 铸件重量公差等级与铸件尺寸公差等级对应选取,一般情况下,铸件重量公差的上偏差与下偏差相同,要求较高时,下偏差等级可比上偏差等级小二级。
有特殊要求时,另外注明。
表9重量公差等级5.4.5机加工余量5.4.5.1 机械加工余量适用于整个毛坯铸件,且该值应根据最终机械加工后成品铸件的最大轮廓尺寸和相应的尺寸范围选取。
铸件的某一部位在铸态下的最大尺寸应不超过成品尺寸与要求的加工余量及铸造总公差之和。
当有斜度时,斜度值应另外考虑。
我司产品铸件机械加工余量等级按 E-H级执行。
铸件毛坯的基本尺寸=最终加工后的尺寸+n x要求的机械加工余量+铸件公差12表10要求的机械加工余量等级545.2铸件顶面的加工余量等级比铸件底面和底侧面的加工余量等级高1级546碳钢的线收缩率(固态收缩率)表11碳钢的线收缩率与碳的质量分数的关系(%实际生产中由于各种阻力的存在,实际收缩率会小于理论的线收缩率,对于结构复杂和精度要求高的铸件,其摸样尺寸必须经过多次尺寸定型试验来确定。
我司桥壳产品一般按2% 的实际收缩率执行。
5.4.7起模斜度(桥壳产品)5.4.7.1 V 法铸造工艺对外模的起模斜度要求较低,一般只要控制在0-1 °;表12起模斜度547.2 砂芯由于采用的水玻璃砂硬化成型,所以芯盒的起模斜度以增加铸件壁厚的方式控制在2-3 °。
5.4.8非加工壁厚的负余量548.1由于造型起模时往往会造成型腔的扩大,制芯时砂芯尺寸的减小,所有模样的尺寸往往小于图样的尺寸,所减少的尺寸称为非加工壁厚的负余量。
表13铸件非加工壁厚的负余量(单位:mm)5.4.9最小铸出孔和槽549.1当铸件上的孔和槽尺寸太小,覆膜困难,或铸件的壁厚较厚和金属液压力较高,反而会使铸件产生粘砂,造成清理和机械加工困难。
建议用机械加工方法做出这样的孔和槽;5.4.9.2当铸件上的孔和槽,需要采用复杂或难度较高的工艺措施才能铸出,建议采用机械加工方法做出;549.3 如孔径小于15mm或孔的长度与孔的直径之比大于 4时,则不便铸出,建议用机械加工方法做出;5.4.9.4 方形孔、菱形孔、气路孔等特殊形孔,不能加工做出的,原则上必须铸出;5.4.9.5 凹槽、台阶,当宽度w 20mm高度》10mn S寸,一般不予铸出;5.4.9.6 当孔和槽上放冒口且冒口盖住整个孔和槽时,应将孔和槽封死。
5.4.10 工艺肋5.4.10.1 铸件在凝固收缩时,由于受砂型和砂芯的阻碍,在受拉应力的壁上或在接头处容易产生热裂处应设收缩肋。
收缩肋厚度以最厚为15mm最小为4mn为原则;5.4.10.2 为防止半环形或U形铸件,冷却以后发生变形,常在影响变形最关键的部位设置拉肋。
5.4.11 工艺补正量5.4.11.1为防止铸件局部尺寸由于各种工艺因素,(如铸件线收缩率选用值和实际值不符、铸件变形、有规律的操作偏差等)的影响而超差,则应在铸件相应的部位调整金属层厚度。
5.5砂芯设计5.5.1桥壳砂芯按黏结剂分类,分为二氧化碳硬化水玻璃砂芯和二氧化碳硬化树脂砂芯,而桥壳二氧化碳硬化水玻璃砂芯采用组合式砂芯,即砂芯两端轴孔至板簧处表面砂芯成型采用覆膜砂热芯盒烤制的芯壳,其余采用水玻璃砂舂紧二氧化碳硬化。
5.5.2二氧化碳硬化水玻璃砂芯型砂与水玻璃的重量比为100:7,二氧化碳硬化树脂砂芯型砂与树脂的重量比为100:3.5 ;5.5.3砂芯的固定和定位可采用芯头、芯撑、钢丝、螺栓钩,芯头形状的设计一般应考虑砂芯在下芯时的方向和横纵向位移的防错形状。
5.5.4. V法造型的芯头间隙可略小以下参数表中得数值,芯头的尺寸也可根据铸件与砂箱的尺寸进行适当的调整。
5.5.4.1 水平芯头长度,可参照表14表14水平芯头长度/单位mm5.542 水平芯头间隙,可参照表15表15水平心头间隙/单位mm5.543 如需设置水平芯头斜度与斜面间隙,可参考JB/T 5106-1991.5.544 垂直芯头高度,可参照表16表16垂直芯头高度/单位mm5.5.4.5 垂直芯头斜度,可参照表17表17垂直芯头斜度5.5.4.6 垂直芯头间隙,可参照表18表18垂直芯头间隙/单位mm5.6芯撑5.6.1芯撑采用单光柱圆形或单光柱方形;5.6.2芯撑材质应与铸件材质相当。
表19单光柱圆形芯撑5.7通气孔设置原则5.7.1通气孔一般设置在铸件浇注位置的最高点,铸件高度方向上,充型金属液最后到达的部位,砂芯发气和蓄气较多的部位,型腔内气体难以排除的“死角”处。
5.7.2通气孔的设置位置应不破坏铸件的补缩条件,通常不宜设置在铸件的热节和厚壁处,以免因通气孔冷却导致铸件在该处产生收缩缺陷,如确实需要,可采用引出式出气孔。
5.7.3通气孔根部的厚度,一般按所在处铸件厚度的0.4-0.7倍计算,凝固体收缩大的合金取偏小值,防止形成接触热节导致铸件产生缩孔。
5.7.4暗冒口上也应设置较大的通气孔,一般认为,没有设置明冒口的铸件,通气孔根部总断面积最小应等于内浇道总断面积,以保证通气孔能顺畅地排出型腔中的气体。
5.8冷铁的设置原则5.8.1外冷铁最好采用高碳钢制作,其次是中低合金钢,最后才考虑采用铸铁,主要是防止外冷铁发生熔合,变形等。
5.8.2外冷铁的设置厚度应使被激冷厚度的0.5-1.0倍,外冷铁的长度为被激冷铸件厚度的2-4倍,外冷铁的宽度=外冷铁的长度,外冷铁之间的间隙为外冷铁长度的1/2-2/3。
5.8.3内冷铁熔合后需留在铸件内部的,内冷铁的材质采用与铸件相当的材质,如机加工部位的内冷铁熔合后,可被机加工去除的,则内冷铁的材质可采用碳钢或中低合金钢;5.8.4内冷铁的截面积和长度分别等于需被激冷部位截面积和深度的 0.7倍。