阀门铸造工艺
《阀体铸造工艺》课件
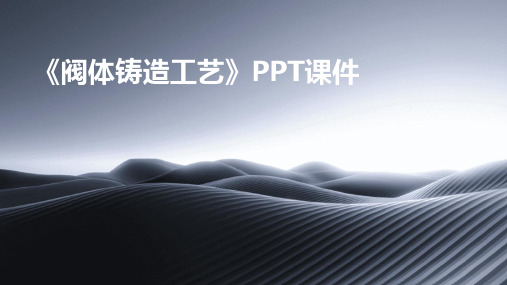
的装置,以及优化浇注系统。
02
夹渣
夹杂在铸件内部的非金属夹杂物,通常是因为熔炼过程中杂质进入金属
液或浇注过程中卷入杂质。预防措施包括控制原材料的纯净度,优化熔
炼和浇注条件。
03
缩孔
铸件冷却过程中,由于金属液的收缩而形成的孔洞。预防措施包括控制
金属液的冷却速度和浇注温度,以及优化铸件的结构设计。
铸造质量的检测方法
外观检测
通过目视或简单的工具对铸件表面进行检测,检查是否存在明显的 缺陷。
无损检测
利用X射线、超声波、磁粉等手段对铸件内部进行检测,以发现潜 在的缺陷。
力学性能检测
对铸件进行拉伸、冲击、硬度等力学性能试验,以评估其机械性能是 否满足要求。
提高铸造质量的措施
优化铸造工艺
通过试验和改进,不断优化铸造工艺参数,以提 高铸件的质量。
模具制造的材料选择
钢材
选用高强度、耐磨、耐腐蚀的钢 材,如合金钢、不锈钢等,确保 模具的长期稳定性和使用寿命。
铸铁
适用于对精度要求不高的模具,成 本相对较低,但需注意其易锈蚀的 特性。
塑料
在特定情况下,如简易模具或原型 制造,可使用塑料作为替代材料。
模具制造的工艺流程
粗加工
对模具毛坯进行初步加工,形 成大致的形状和尺寸。
组装与调试
将各部分组合在一起,进行必 要的调整和测试,确保模具正 常工作。
准备图纸和材料
根据设计图纸准备所需材料, 确保规格和质量符合要求。
精加工
按照图纸要求进行精细加工, 确保模具的精度和表面质量。
后期处理
进行防锈、涂装等处理,以提 高模具的耐久性和美观度。
04
阀体铸造的生产工艺
阀门铸造工艺流程

阀门铸造工艺流程
《阀门铸造工艺流程》
阀门是工业设备中常用的一种控制装置,其铸造工艺流程关乎产品质量和性能。
下面是阀门铸造工艺流程的简要介绍:
1. 原料准备:阀门的主要原料是铸铁、铸钢、不锈钢等金属材料。
在铸造工艺流程开始之前,需要对原料进行精细的筛选和混合,保证其质量和化学成分符合要求。
2. 模具制作:根据阀门的设计图纸,制作相应的铸造模具。
模具通常分为上、下两部分,用以塑造产品的外形和内部空腔。
模具制作需要考虑到材料的热胀冷缩和流动性,以保证成品的精度和表面光洁度。
3. 熔炼金属:将已准备好的原料放入熔炼炉中,加热至一定温度,然后进行搅拌和除气处理,得到符合要求的熔融金属溶液。
4. 浇注成型:将熔融的金属通过浇口注入模具中,根据阀门的设计需求冷却并凝固,在模具内形成产品的外形和内部空腔。
5. 取模清理:待成品冷却后,拆卸模具,清理产品表面上的余渣和砂粒,做到干净整洁。
6. 精密加工:对铸造成品进行精密加工,包括修整外形、加工内部腔体、打磨表面等步骤,以达到阀门的使用要求。
7. 表面处理:产品经过精密加工后,需要进行表面的防腐、喷涂或者镀层处理,以提高产品的使用寿命和外观质量。
以上就是阀门铸造工艺流程的简要介绍。
通过严格的工艺流程和质量控制,可以生产出质量稳定、性能可靠的阀门产品,满足不同行业的需求。
阀门铸造工艺分类
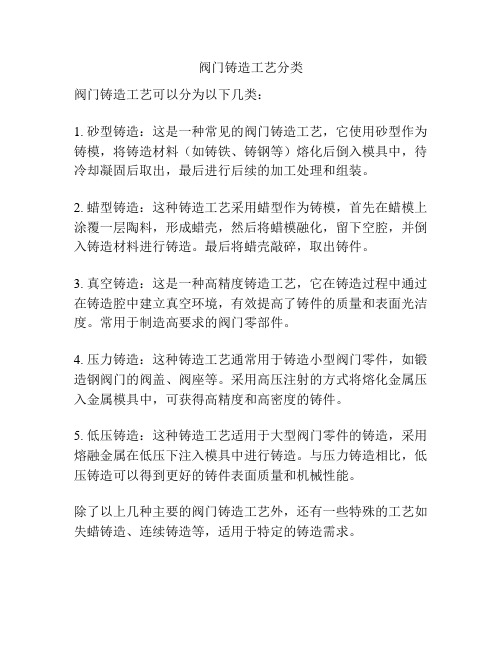
阀门铸造工艺分类
阀门铸造工艺可以分为以下几类:
1. 砂型铸造:这是一种常见的阀门铸造工艺,它使用砂型作为铸模,将铸造材料(如铸铁、铸钢等)熔化后倒入模具中,待冷却凝固后取出,最后进行后续的加工处理和组装。
2. 蜡型铸造:这种铸造工艺采用蜡型作为铸模,首先在蜡模上涂覆一层陶料,形成蜡壳,然后将蜡模融化,留下空腔,并倒入铸造材料进行铸造。
最后将蜡壳敲碎,取出铸件。
3. 真空铸造:这是一种高精度铸造工艺,它在铸造过程中通过在铸造腔中建立真空环境,有效提高了铸件的质量和表面光洁度。
常用于制造高要求的阀门零部件。
4. 压力铸造:这种铸造工艺通常用于铸造小型阀门零件,如锻造钢阀门的阀盖、阀座等。
采用高压注射的方式将熔化金属压入金属模具中,可获得高精度和高密度的铸件。
5. 低压铸造:这种铸造工艺适用于大型阀门零件的铸造,采用熔融金属在低压下注入模具中进行铸造。
与压力铸造相比,低压铸造可以得到更好的铸件表面质量和机械性能。
除了以上几种主要的阀门铸造工艺外,还有一些特殊的工艺如失蜡铸造、连续铸造等,适用于特定的铸造需求。
阀门的铸造工艺
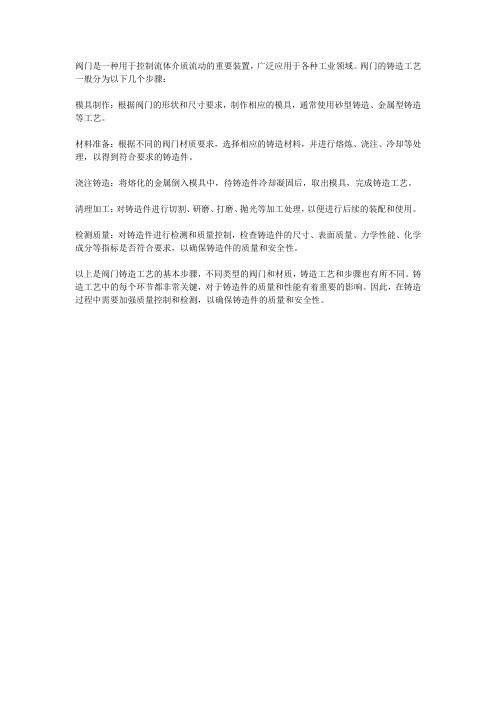
阀门是一种用于控制流体介质流动的重要装置,广泛应用于各种工业领域。
阀门的铸造工艺一般分为以下几个步骤:
模具制作:根据阀门的形状和尺寸要求,制作相应的模具,通常使用砂型铸造、金属型铸造等工艺。
材料准备:根据不同的阀门材质要求,选择相应的铸造材料,并进行熔炼、浇注、冷却等处理,以得到符合要求的铸造件。
浇注铸造:将熔化的金属倒入模具中,待铸造件冷却凝固后,取出模具,完成铸造工艺。
清理加工:对铸造件进行切割、研磨、打磨、抛光等加工处理,以便进行后续的装配和使用。
检测质量:对铸造件进行检测和质量控制,检查铸造件的尺寸、表面质量、力学性能、化学成分等指标是否符合要求,以确保铸造件的质量和安全性。
以上是阀门铸造工艺的基本步骤,不同类型的阀门和材质,铸造工艺和步骤也有所不同。
铸造工艺中的每个环节都非常关键,对于铸造件的质量和性能有着重要的影响。
因此,在铸造过程中需要加强质量控制和检测,以确保铸造件的质量和安全性。
阀体铸件缺陷及工艺介绍
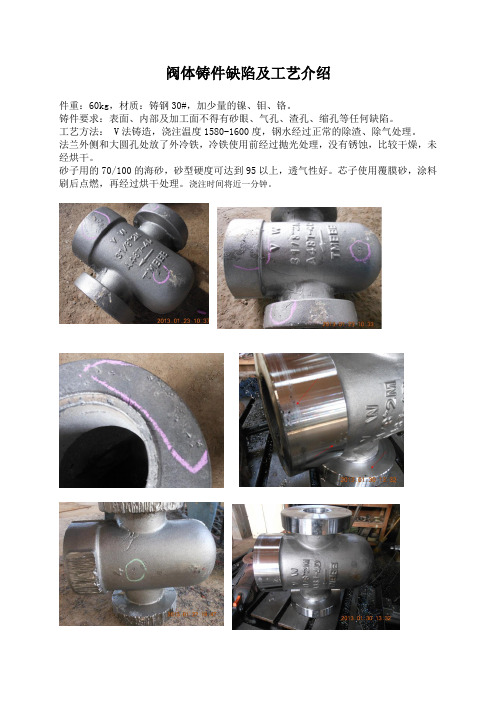
阀体铸件缺陷及工艺介绍
件重:60kg,材质:铸钢30#,加少量的镍、钼、铬。
铸件要求:表面、内部及加工面不得有砂眼、气孔、渣孔、缩孔等任何缺陷。
工艺方法: V法铸造,浇注温度1580-1600度,钢水经过正常的除渣、除气处理。
法兰外侧和大圆孔处放了外冷铁,冷铁使用前经过抛光处理,没有锈蚀,比较干燥,未经烘干。
砂子用的70/100的海砂,砂型硬度可达到95以上,透气性好。
芯子使用覆膜砂,涂料刷后点燃,再经过烘干处理。
浇注时间将近一分钟。
以下是型板布置图
请问以上除气孔外还有什么缺陷?如何改善?。
大件铸造阀门铸造工艺流程
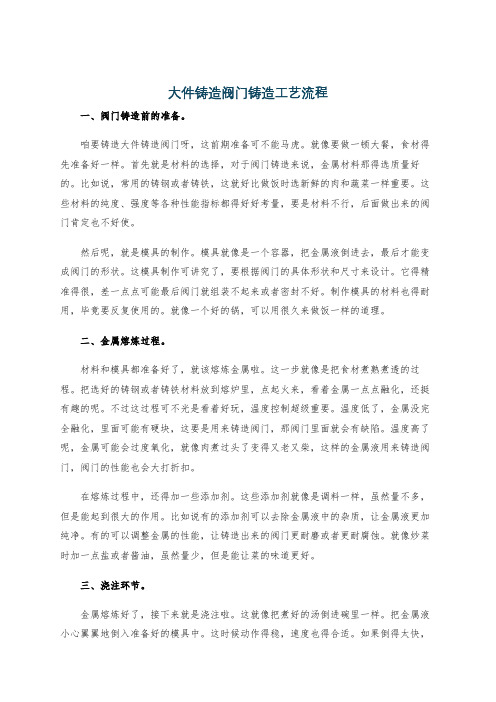
大件铸造阀门铸造工艺流程一、阀门铸造前的准备。
咱要铸造大件铸造阀门呀,这前期准备可不能马虎。
就像要做一顿大餐,食材得先准备好一样。
首先就是材料的选择,对于阀门铸造来说,金属材料那得选质量好的。
比如说,常用的铸钢或者铸铁,这就好比做饭时选新鲜的肉和蔬菜一样重要。
这些材料的纯度、强度等各种性能指标都得好好考量,要是材料不行,后面做出来的阀门肯定也不好使。
然后呢,就是模具的制作。
模具就像是一个容器,把金属液倒进去,最后才能变成阀门的形状。
这模具制作可讲究了,要根据阀门的具体形状和尺寸来设计。
它得精准得很,差一点点可能最后阀门就组装不起来或者密封不好。
制作模具的材料也得耐用,毕竟要反复使用的。
就像一个好的锅,可以用很久来做饭一样的道理。
二、金属熔炼过程。
材料和模具都准备好了,就该熔炼金属啦。
这一步就像是把食材煮熟煮透的过程。
把选好的铸钢或者铸铁材料放到熔炉里,点起火来,看着金属一点点融化,还挺有趣的呢。
不过这过程可不光是看着好玩,温度控制超级重要。
温度低了,金属没完全融化,里面可能有硬块,这要是用来铸造阀门,那阀门里面就会有缺陷。
温度高了呢,金属可能会过度氧化,就像肉煮过头了变得又老又柴,这样的金属液用来铸造阀门,阀门的性能也会大打折扣。
在熔炼过程中,还得加一些添加剂。
这些添加剂就像是调料一样,虽然量不多,但是能起到很大的作用。
比如说有的添加剂可以去除金属液中的杂质,让金属液更加纯净。
有的可以调整金属的性能,让铸造出来的阀门更耐磨或者更耐腐蚀。
就像炒菜时加一点盐或者酱油,虽然量少,但是能让菜的味道更好。
三、浇注环节。
金属熔炼好了,接下来就是浇注啦。
这就像把煮好的汤倒进碗里一样。
把金属液小心翼翼地倒入准备好的模具中。
这时候动作得稳,速度也得合适。
如果倒得太快,金属液可能会溅出来,造成浪费不说,还可能在模具里形成气泡。
要是倒得太慢呢,金属液可能在浇注过程中就开始凝固了,这样阀门就会有残缺。
在浇注的时候,还得注意浇注的高度和角度。
阀门的一般铸造工艺
阀门的一般铸造工艺阀门是工业自控系统中的重要元件,用于控制流体的流通或停止。
阀门的制造工艺主要包括铸造、加工和装配。
阀门的铸造工艺主要有砂型铸造、金属型铸造和石膏型铸造等。
以下详细介绍阀门的一般铸造工艺。
1. 铸造材料的选择阀门一般使用铸铁、铸钢、不锈钢、铜合金或铝合金等材料。
根据阀门的用途和工作条件选择合适的铸造材料。
2. 铸型制备根据阀门的形状和尺寸,制作阀门的铸型。
常用的铸型有砂型、金属型和石膏型。
砂型是最常用的铸型,制作砂型需要用到砂子、骨料、黏结剂和水等材料。
首先根据阀门的外形尺寸制作型板,然后将型板埋入砂箱中,将砂子、骨料和黏结剂混合均匀后倒入砂箱中,再用另一块砂板压实,使砂子紧密连接起来,在型板上加以震动,使砂子填满型腔,并在砂子上留下阀门的外形。
待砂子凝固后,将砂箱翻转,取出型板,即可得到阀门的砂型。
金属型铸造是高精度铸造的一种方法,适用于制造要求较高的阀门。
金属型一般由铝合金、青铜或钢等材料制成,耐高温、耐磨损。
石膏型铸造是用石膏作为铸型材料的一种铸造方法,适用于制造复杂形状的阀门。
制作石膏型的方法是将阀门的模特浸入石膏浆中,待石膏干固后,取出模特,即可得到阀门的石膏型。
3. 熔炼和浇铸在铸造过程中,首先需要熔炼原材料,将铸材加热至熔点,并保持一定的熔化状态。
随后将熔融的铸材倒入铸型中,待铸材冷却凝固后,取出铸件,即可得到阀门的铸件。
4. 铸件修整铸件取出后,常常会有一些缺陷,如气孔、夹渣等。
需要对铸件进行修整和清理,去除表面的氧化皮和铸造缺陷,使其表面光滑。
5. 热处理对于某些铸件,需要进行热处理,以提高其性能。
常见的热处理方法有淬火、回火和正火等。
6. 加工经过铸造和热处理的阀门铸件需要进行加工,以达到设计要求。
加工一般包括切割、钻孔、镗孔、铰孔、攻螺纹、铣削和磨削等工序。
7. 装配加工完成后,将各个零部件组装到一起,形成完整的阀门。
装配时需注意零部件的配合精度和密封性。
同时要对阀门进行严格的检验和试验,确保其性能和质量。
第4章 阀门铸造工艺.
第四章:阀门铸造工艺第一节、 铸造的特点将液体金属浇到具有与零件形状相适应的铸型空腔中,待其凝固后,以获得一定形状尺寸和表面质量的零件和毛坯的方法,称为铸造。
铸造方法中,最常用的方法是砂型铸造。
目前来讲,用砂型浇铸的铸件约占铸件产量的90%以上,除此之外还有其他多种铸造方法,如:金属型铸造、熔模铸造、压力铸造,离心铸造、壳型铸造、真空铸造等。
一、铸造生产优、缺点:1、用铸造方法可制成形状复杂,特别是具有复杂内腔的毛坯,象:箱体、气缸体、机座、机床床身等。
2、铸造的适应性很广,灵活性很大。
工业中常用的多种金属材料都可用于铸造。
如:碳钢、合金钢、铸铁、青铜、黄铜、铝等特别是用得最多的铸铁,只能用铸造来生产毛坯。
铸件重量可小到只有几克,重达几百吨,壁厚可由1mm到1m左右。
生产大件,铸造优势尤为明显。
3、铸造所用的原材料大都来源广,价格低廉,如:切削、废钢、报废的机件,冲皮等。
4、铸件形状与零件相似,减少了切削加工的工作量,节约金属。
二、但铸造也存在着一些问题:1、机械性能不如锻件高,使得铸件显得相当笨重。
2、铸造工序较多,且一些工艺过程无法清确控制,这就造成铸件质量不够稳定,废品率较高。
3、此外,劳动条件差,强度高。
第二节 铸造的工艺过程一、砂型铸造工艺1、型砂型(芯)砂质量对铸件质量有很大的影响,如:砂眼、气孔、夹砂、裂纹等缺陷的产生常是由于型砂质量不合格所致。
型砂性能对铸件质量的影响:型砂应具备如下性能:(1)强度 在外力作用下,其不易被破坏的性能称为强度。
这种性能在铸型制造、搬运以及液体金属冲击和压力作用下,不发生变形、损坏是非常重要的,否则会造成塌箱、冲砂和砂眼等缺陷。
(2)透气性 型砂由于各砂粒间存在空隙,具有能使气体透过的能力称为透气性。
(3)耐火度 型砂在高温金属液作用下不软化、熔化的性能。
当耐火度不足时,砂粒将烧融而粘在铸件表面形成一层硬皮,使切削时加快刀具磨损。
因此粘砂严重时,也会使铸件报废,为弥补型砂耐火度不足,在铸型型腔表面刷一层涂料。
阀门 铸造工艺
阀门铸造工艺
阀门铸造工艺是指将金属材料通过铸造工艺,制作成阀门的加工过程。
铸造工艺是一种制造工艺,其优点是生产周期短、生产效率高、生产成本低、能够生产较大型号的产品等特点。
阀门铸造工艺包括模型制作、模具制作、熔炼和浇注等环节。
首先需要根据阀门的形状和尺寸,制作出相应的模型。
然后,依照模型制作出相应的模具,模具通常采用砂型、金属型等不同类型。
熔炼过程需要按照所需的材料比例,将金属材料加入到炉中进行熔化。
最后,熔融状态的金属材料通过浇注进入模具中,待金属材料冷却后,就可以取出铸造好的阀门。
阀门铸造工艺需要注意的问题包括铸造工艺参数的设置、铸造材料的选择、浇注过程的控制等。
不同的阀门类型需要采用不同的铸造工艺,以满足阀门的性能和使用要求。
总之,阀门铸造工艺是一项关键的制造过程,对于阀门的性能和质量具有重大的影响。
因此,在铸造过程中应该严格按照工艺要求进行操作,以保证阀门的质量和使用寿命。
- 1 -。
第4章 阀门铸造工艺
第四章:阀门铸造工艺第一节、 铸造的特点将液体金属浇到具有与零件形状相适应的铸型空腔中,待其凝固后,以获得一定形状尺寸和表面质量的零件和毛坯的方法,称为铸造。
铸造方法中,最常用的方法是砂型铸造。
目前来讲,用砂型浇铸的铸件约占铸件产量的90%以上,除此之外还有其他多种铸造方法,如:金属型铸造、熔模铸造、压力铸造,离心铸造、壳型铸造、真空铸造等。
一、铸造生产优、缺点:1、用铸造方法可制成形状复杂,特别是具有复杂内腔的毛坯,象:箱体、气缸体、机座、机床床身等。
2、铸造的适应性很广,灵活性很大。
工业中常用的多种金属材料都可用于铸造。
如:碳钢、合金钢、铸铁、青铜、黄铜、铝等特别是用得最多的铸铁,只能用铸造来生产毛坯。
铸件重量可小到只有几克,重达几百吨,壁厚可由1mm到1m左右。
生产大件,铸造优势尤为明显。
3、铸造所用的原材料大都来源广,价格低廉,如:切削、废钢、报废的机件,冲皮等。
4、铸件形状与零件相似,减少了切削加工的工作量,节约金属。
二、但铸造也存在着一些问题:1、机械性能不如锻件高,使得铸件显得相当笨重。
2、铸造工序较多,且一些工艺过程无法清确控制,这就造成铸件质量不够稳定,废品率较高。
3、此外,劳动条件差,强度高。
第二节 铸造的工艺过程一、砂型铸造工艺1、型砂型(芯)砂质量对铸件质量有很大的影响,如:砂眼、气孔、夹砂、裂纹等缺陷的产生常是由于型砂质量不合格所致。
型砂性能对铸件质量的影响:型砂应具备如下性能:(1)强度 在外力作用下,其不易被破坏的性能称为强度。
这种性能在铸型制造、搬运以及液体金属冲击和压力作用下,不发生变形、损坏是非常重要的,否则会造成塌箱、冲砂和砂眼等缺陷。
(2)透气性 型砂由于各砂粒间存在空隙,具有能使气体透过的能力称为透气性。
(3)耐火度 型砂在高温金属液作用下不软化、熔化的性能。
当耐火度不足时,砂粒将烧融而粘在铸件表面形成一层硬皮,使切削时加快刀具磨损。
因此粘砂严重时,也会使铸件报废,为弥补型砂耐火度不足,在铸型型腔表面刷一层涂料。
- 1、下载文档前请自行甄别文档内容的完整性,平台不提供额外的编辑、内容补充、找答案等附加服务。
- 2、"仅部分预览"的文档,不可在线预览部分如存在完整性等问题,可反馈申请退款(可完整预览的文档不适用该条件!)。
- 3、如文档侵犯您的权益,请联系客服反馈,我们会尽快为您处理(人工客服工作时间:9:00-18:30)。
阀门铸造工艺介绍阀门铸造工艺*第一节铸造的概述及特点一、何为铸造:将液体金属浇到具有与零件形状相适应的铸型空腔中,待其凝固后,以获得一定形状尺寸和表面质量的零件的产品,称之为铸造。
二、铸造概述:铸造具有悠久的历史,约在公元前三千年,人类已铸出多种精美的青铜器。
但几千年来是靠手工用粘土、砂等天然材料制造的。
铸件的产量很小,随着工业革命的发展,机械化的增加,铸件需求量的提高,在20世纪30年代开始使用气动机器和人工合成造型的粘土砂工艺生产。
随着时代的发展,各类造型方法应运而生。
例如:1933年出现水泥砂型,1967年出现水泥流态砂型;1944年出现冷却覆膜树脂砂壳型;1955年出现热法覆膜树脂砂壳型,1958年出现咲喃树脂自硬砂型;1947年出现CO2硬化水玻璃砂型,1968年出现了有机硬化剂的水玻璃(有机脂水玻璃)工艺等。
近年来,用物理手段制造铸型的新方法,如:磁丸造型,真空密封造型法,失膜造型等。
铸造由于可选用多样成分、性能的铸造合金,加工基本建设投资小,工艺灵活性大,生产周期短等优点,被广泛用于机械制造、矿山冶金、交通运输、石化通用设备、农业机械、能源动力、轻工纺织、土建工程、电力电子、航天航空、国际军工等国民经济各部门,是现代大机械工业的基础。
铸造在中国已有漫长的历史,但铸造技术长期处于停滞状态,改革开放以来,我国的铸造技术有了很大的发展,突出的表现在三个方面:造型、造芯的机械化、自动化程度明显提高;自硬性化学型砂取代干型粘土砂和油砂;铸造工艺技术由凭经验走向科学化,如:计算机模拟设计。
这一系列的改革对提高生产效率,降低劳动强度,改善生产环境,提高铸件内在质量和外观质量,节约原材料和能源起了重大的作用。
三、铸造特点:1、铸造的适应性很广,灵活性很大,产品要求及所处各种工况,可制造多种金属材料的产品,如:铁、碳素钢、低合金钢、铜、铜合金、铝、铝合金、钛合金等等。
与其他成型方式相比,铸造不受零件的重量、尺寸和形状限制。
重量可从几克到几百吨,壁厚由0.3mm到1m,形状只要在铸造工艺性范围内,是十分复杂的,还是机械加工困难的,甚至难以制得的零件,都可通过铸造的方式获得。
22、铸造所用的原材料大多来源广,价格低廉,如废钢、砂等。
但由于近期国内铸造和钢铁业大量兴起,这些原材料价格出现上涨。
3、铸件可通过先进的铸造工艺方法,提高铸件的尺寸精度和表面质量,使零件做到少切割和无切割。
对产品制造达到省工省料的效果,节约总体的制作成本。
3四、铸造存在问题:1、我国大多数铸造企业,其铸造工艺落后,机械化程度低,从而使铸件的尺2、寸精度低、表面质量差、能源和原材料消耗高、生产效率低、劳动强度大、环境污染严重、企业效益差。
3、铸造是一个高危行业,同时又是一个苦、脏、累的工作,行业效益差,留不往人。
不论技术人员还是具体的操作者都很难寻,后继无人的现象十分突出。
4、铸造工序较多,流程长,对产品质量难以控制、废品率较高,近期合金价格和人工费上涨,铸件成本大幅上升。
第二节核电阀铸造工艺核电阀门铸造零件考虑其使用的特殊性和使用要求,为稳定铸件的工艺质量,所以对铸件的铸造工艺流程、材料、工艺、质量控制有严格的规定。
核电阀铸造工艺流程*浇 铸***冒口切粗清整 * —打磨— ***补焊〜 射线探伤渗透或磁粉探伤热处理_______ 渗透或磁粉探伤**喷丸(喷砂) f 不锈钢酸洗钝化J J*入库・铸造工艺方案根据产品结构、大小及技术要求制定铸造方式。
制造方式通常分为两种:砂铸和精铸。
****冶炼J成分控制型砂试验 铸造工艺设计 造型 温度控制 配模砂铸:有粘土砂、树脂砂(咲喃、碱性酚醛、聚尿烷)、水玻璃砂〔C02*法硬化法、VRHC真空CO2置换太热空气硬化法(脱水硬化)、硅酸二钙和赤泥等粉状硬化剂的自硬砂、有机酯硬化〕。
精铸:又称之为特种铸造。
有熔膜铸造(失蜡铸造)、陶瓷型铸造、金属型铸造、压力铸造、离心铸造、真空吸铸、磁性铸造、壳型铸造、实型铸造(消失膜铸造)等约12种。
根据企业所具备的生产条件确定铸造方式。
三.砂铸铸造工艺1、型砂型(芯)砂质量对铸件质量有很大的影响,如:砂眼、气孔、夹砂、裂纹等缺陷的产生常是由于型砂质量不合格所致。
型砂性能对铸件质量的影响:型砂应具备如下性能:(1)强度在外力作用下,其不易被破坏的性能称为强度。
这种性能在铸型制造、搬运以及液体金属冲击和压力作用下,不发生变形、损坏是非常重要的,否则会造成塌箱、冲砂和砂眼等缺陷。
(2)透气性型砂由于各砂粒间存在空隙,具有能使气体透过的能力称为透气性。
(3)耐火度型砂在高温金属液作用下不软化、熔化的性能。
当耐火度不足时,砂粒将烧融而粘在铸件表面形成一层硬皮,使切削时加快刀具磨损。
因此粘砂严重时,也会使铸件报废,为弥补型砂耐火度不足,在铸型型腔表面刷一层涂料。
(4)退让性型(芯)砂具有随着铸件的冷却收缩而被压缩其体积的性能,浇注后,型砂高温强度愈低,退让性愈好,铸件所受机械阻力也小。
铸件内应力减小;反之收缩受阻,内应力大,甚至产生裂纹。
6除此之外,还有回用性、发气量,对于树脂砂还有微粉、烧减量、碱性树脂的残碱量等等。
2、型砂的分类:按照粘结剂的不同,型砂可分为:(1)粘土砂(2)水玻璃砂(3)树脂砂(4)油砂及合脂砂。
树脂砂工艺是铸造工艺上的一次大变革,它采用“树脂”作为粘洁剂,使铸造工艺在各个方面都上了一个台阶。
树脂砂工艺的种类很多如壳芯,热芯盒、冷芯盒,自硬砂等等。
我们采用的是“咲喃树脂自硬砂工艺”。
咲喃树脂自硬砂工艺不仅适用大批量的机械化生产,同时也适用于单件、多品种、小批量生产,它同传统粘士砂比较它具有如下优点:生产铸件尺寸精度高,表面粗糙度低,节省能源,提高劳动生产率,改善工人劳动条件,旧砂回用率高,对环境污染小等等。
该工艺自八十年引入中国,尤其是生产线投入,相关技术原材料问题的解决。
在我国发展很快,尤其在机床、造船、重机、电工等行业,所使用都取得较好的成果。
但其也有本身的局限性,在浇注碳钢薄壁铸件时,因其高温强度较高,故极易产生裂纹缺陷。
这一点对于核电阀门来讲是绝对不和行,同时也有一个铸件表面渗碳问题,对生产超低碳不锈钢最好不要米用该工艺3、造型方法:造型方法分为手工造型和机器造型:手工造型适用于单件,小批量生产。
7按砂箱特征可分为:两箱、三箱、地坑、脱箱几种。
按模型特征可分为:整模、挖砂、假箱、活块、分模、车板等。
四.铸造工艺图的制定:铸造生产的第一步,是根据零件的结构特点、技术要求、生产批量及生产条件等,来确定其铸造工艺方案,并绘制铸造工艺图。
铸造工艺图是利用各种工艺符号和颜色,把制造模型和铸型所需的资料直接绘在零件图上的图样。
图中应有:铸件的浇注位置,分型面,型芯的数量形状、尺寸及其固定方法、机械加工余量、拔模斜度和收缩率,浇口、冒口、冷铁的尺寸和位置等。
1.浇注位置的选择原则:铸件的浇注位置是指浇注时铸件在铸型中所处的位置,这个位置对铸件质量有很大影响,选择浇注位置应考虑如下原则:把铸件的重要部位和易产生缺陷的部位放在最有利的位置。
(1)铸件的重要加工面或主要工作面应朝下或朝侧面,因为铸件上表面的缺陷(如砂眼、气孔、夹渣等)通常比下部多,组织也不如下面致密。
如果这些平面难以做到朝下,则尽力使其位于侧面。
当铸件的重要加工面有数个时,则应将较大的面朝下,并对朝上的表面采用加大加工余量的办法来保证铸件质量。
89图3-1为阀体铸件的浇注位置方案。
由于法兰面、密封面是关键表面,不允许有任何表面缺陷,而且要求组织均匀致密,因此,最理想是将这些面朝下浇注,但针 对阀体又不可能,故只得采用如图的方案,将其放置于侧面图3-2法兰浇注位置方案图3-2是法兰的浇注位置方案。
因为法兰圆周表面的质量要求比较高,不允 许有铸造缺陷。
如果采用卧浇,虽然便于采用二箱造型,且合箱方便,但上部*圆周表面的质量难以保证。
若采用图中所示的立浇方案,虽然造型、合箱的工 作量加大,但法兰的全部圆周表面均处于侧面,其质量均匀一致,易于获得合格 铸件。
(2) 铸件的大平面应朝下。
这是由于在浇柱过程中,高温的液态金属对型腔上表面有强烈的热幅射,有时型腔上表面型砂因急剧地热膨胀而拱起或 开裂,使铸件表面产生夹砂缺陷。
很明显,呈水平位置的平面愈厚大,上表面愈易产生夹砂。
为此,对于平板类铸件,要使大平面朝下(图 3-3)。
SOOG/D9/LI 1525?图3-1阀体的浇注位置10多,液体金属易于填满铸型。
(4) 铸件易形成缩孔的的热节部位,浇注位置将其设置在分型面附近的上部或 侧面,这样便于在铸件厚处直接安置冒口,使之自下而上的顺序凝固、进行补 缩,以防止缩孔。
如上述法兰铸件(图 3-2 ),厚端放在上部是合理的;反之, 若厚端在下部,则难以补缩。
(5) 应能减少型芯的数量,便于型芯的固定和排气。
2、铸型分型面的选择原则铸型分型面的选择也是铸造的工艺是否合理的重要关键之一。
如果选择不当,铸件质量难以保证,并使制模、造型、制芯、合箱,甚至切削加工等工序 复杂化。
因此,分型面的选择要在保证铸件质量的前提下,尽量简化工艺,节 省人力物力。
实践证明,分型面的选择应考虑如下原则:(1)应使铸型有最少的分型面,并尽可能为整形造型或分一个分型面。
因为多一个分型面,铸型就多增加一些误差,使铸件的精确度降低。
如果铸件只有一图3-4薄件的浇注位置件上大面积薄壁部分产生生浇不足或冷隔缺陷,应尽量将大面的J:壁部分放在铸型的下部或垂直、倾斜,这对于流动性差的合金尤为重要。
图3-4J 珈油盘类铸件的合理浇注方案 ____ u__- .■- ____ ______ a . ___ ita — J L g ■得此时, 平面处液体金属的压力比平面在上部(3)为个分型面,就可采用工艺简便的两箱造型方法。
图3-5为阀盖铸件,在大批量生产时,为能在造型、合箱过程中方便操作,采用图中I的分型方式,只有一个分型面。
图3-5 阀盖铸件的分型面必须指出,实际选定分型面时要从实际出发,对一些大而复杂或具有特殊要求的铸件,有时采用二个以上的分型面,反而有利于保证铸件质量和简化工艺。
(2)分型面的选择应尽量使型芯和活块数量少,以使制模、造型和合箱等工序简化。
(3)应尽量使铸件全部或大放在同一砂箱内,这样易于保证铸件精度。
若铸件的加工面多,也应尽量使其加工基准面与大部分加工面在同一砂箱内。
图3-6为一阀瓣铸件的两种分型方案。
图中方案使铸件整个位于一个砂箱中,有利于保证相互位置,有利于保证上下同心图3-6 阀瓣铸件(4)为便于造型、下芯、合箱及检验铸件壁厚,应尽量使型腔及主要型芯位于下箱。
但下箱型腔也不宜过深,并力求避免使用吊芯和大的吊砂。
(5)分型面尽量采用平直面,以简化模具制造及造型工艺。