铸造工序标准
铸造的工艺流程
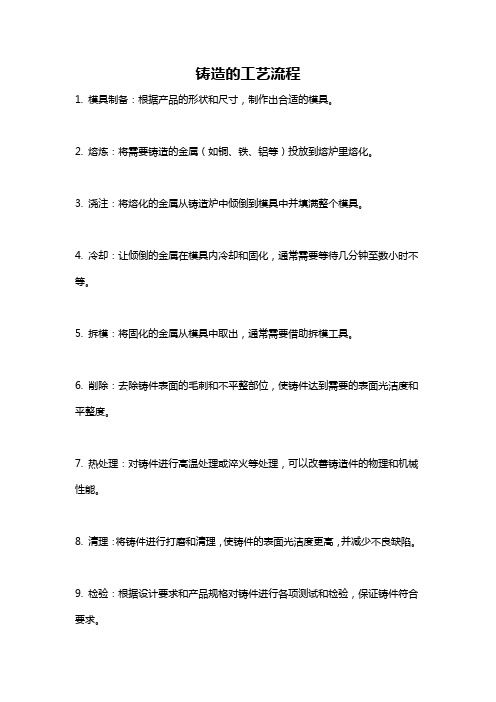
铸造的工艺流程
1. 模具制备:根据产品的形状和尺寸,制作出合适的模具。
2. 熔炼:将需要铸造的金属(如铜、铁、铝等)投放到熔炉里熔化。
3. 浇注:将熔化的金属从铸造炉中倾倒到模具中并填满整个模具。
4. 冷却:让倾倒的金属在模具内冷却和固化,通常需要等待几分钟至数小时不等。
5. 拆模:将固化的金属从模具中取出,通常需要借助拆模工具。
6. 削除:去除铸件表面的毛刺和不平整部位,使铸件达到需要的表面光洁度和平整度。
7. 热处理:对铸件进行高温处理或淬火等处理,可以改善铸造件的物理和机械性能。
8. 清理:将铸件进行打磨和清理,使铸件的表面光洁度更高,并减少不良缺陷。
9. 检验:根据设计要求和产品规格对铸件进行各项测试和检验,保证铸件符合要求。
10. 包装:根据产品的需求对铸造件进行包装和标识,方便后续处理和运输。
铸造生产的工艺流程
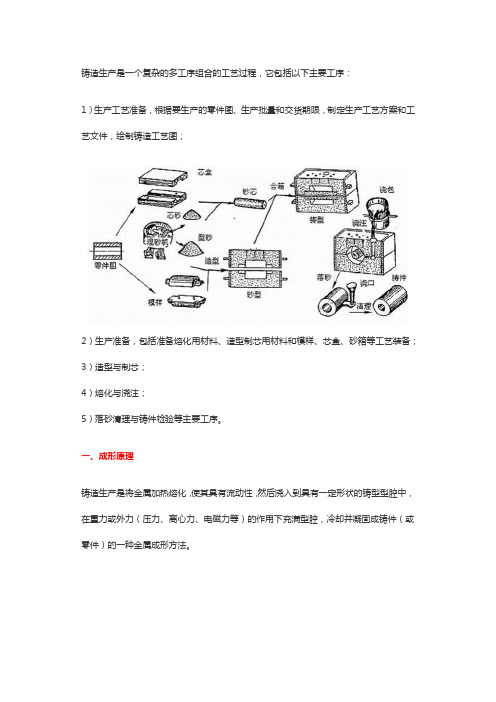
铸造生产是一个复杂的多工序组合的工艺过程,它包括以下主要工序:1)生产工艺准备,根据要生产的零件图、生产批量和交货期限,制定生产工艺方案和工艺文件,绘制铸造工艺图;2)生产准备,包括准备熔化用材料、造型制芯用材料和模样、芯盒、砂箱等工艺装备;3)造型与制芯;4)熔化与浇注;5)落砂清理与铸件检验等主要工序。
一、成形原理铸造生产是将金属加热熔化,使其具有流动性,然后浇入到具有一定形状的铸型型腔中,在重力或外力(压力、离心力、电磁力等)的作用下充满型腔,冷却并凝固成铸件(或零件)的一种金属成形方法。
图1 铸造成形过程铸件一般作为毛坯经切削加工成为零件。
但也有许多铸件无需切削加工就能满足零件的设计精度和表面粗糙度要求,直接作为零件使用。
二、型砂的性能及组成1、型砂的性能型砂(含芯砂)的主要性能要求有强度、透气性、耐火度、退让性、流动性、紧实率和溃散性等。
2、型砂的组成型砂由原砂、粘接剂和附加物组成。
铸造用原砂要求含泥量少、颗粒均匀、形状为圆形和多角形的海砂、河砂或山砂等。
铸造用粘接剂有粘土(普通粘土和膨润土)、水玻璃砂、树脂、合脂油和植物油等,分别称为粘土砂,水玻璃砂、树脂砂、合脂油砂和植物油砂等。
为了进一步提高型(芯)砂的某些性能,往往要在型(芯)砂中加入一些附加物,如煤粉、锯末、纸浆等。
型砂结构,如图2所示。
图2 型砂结构示意图三、工艺特点铸造是生产零件毛坯的主要方法之一,尤其对于有些脆性金属或合金材料(如各种铸铁件、有色合金铸件等)的零件毛坯,铸造几乎是唯一的加工方法。
与其它加工方法相比,铸造工艺具有以下特点:1)铸件可以不受金属材料、尺寸大小和重量的限制。
铸件材料可以是各种铸铁、铸钢、铝合金、铜合金、镁合金、钛合金、锌合金和各种特殊合金材料;铸件可以小至几克,大到数百吨;铸件壁厚可以从0.5毫米到1米左右;铸件长度可以从几毫米到十几米。
2)铸造可以生产各种形状复杂的毛坯,特别适用于生产具有复杂内腔的零件毛坯,如各种箱体、缸体、叶片、叶轮等。
精密铸造各工序操作规程及注意事项

精密铸造各工序操作规程及注意事项一一d49f2498-6eb9-llec-97c3-7cb59b590d7d压蜡工序工艺操作规程及注意事项一、工艺要求:室温:24±20,蜡缸温度:54±2团射蜡嘴温度:54±2回压射压力35-4.0mpa保压时间:根据蜡模尺寸和壁厚(一般为6-8秒)冷却水温度:≤2O0二.操作程序:L检查蜡机油压、保温温度、操作按钮是否正常,并按技术规定调整蜡机的注射压力力,射蜡嘴温度,保压时间,冷却时间等。
2.从培养箱中取出蜡筒,将其安装在蜡压机上,将上部混有空气的蜡挤出。
3.将模具放在压蜡机工作台面上,调整射蜡嘴使之与模具注蜡口高度一致,检查模具所有型芯和活动块的位置是否正确,模具的开启和关闭是否顺畅。
4.打开模具,喷洒一薄层脱模剂,关闭模具,对准蜡嘴。
5.双手按下工作按钮,按下蜡模。
6.抽出芯子,打开模具,小心取出蜡模,放在工作台一侧,合上模具开始压下一件,同时,在粗略检查零件无缺陷后,应按要求将其放入冷却水或储存板中冷却。
冷却时间为4小时。
注意:有以下缺陷的蜡模应报废:(1)蜡模的某些部位因模具材料中有空气而鼓包;(2)蜡模的任何部分有缺陷;(3)蜡模变形,不易修复;(4)尺寸不符合要求。
7.清除模具上残留的模料,注意只能用竹刀,不可用金属刀片清除残留模料,防止模具型腔及分型面受损,用压缩空气气嘴吹净模具分型面。
芯子上的蜡屑等,视模具结构及使用情况每2-10件喷一次分型剂。
8.及时从冷却水中轻轻取出蜡模,用压缩空气吹走蜡屑和水滴,并自检关闭。
把它放在储物盘里。
9.每班下班或模具使用完毕后,应用软布或棉棒清理模具,如发现模具有损伤或不正常,应立即报告领班,由领班处理。
并清扫压蜡机,工具及现场,做到清洁、整齐。
三、注意事项:1.压制蜡模时,首先必须进行检查,确认合格后,方可进行操作,压蜡模过在此过程中,冲压参数不易更改。
2.模具型腔不要喷过多的分型剂,并要均匀,必要时可用压缩空气气嘴辅助均匀地吹分离剂。
铸造工艺流程介绍

铸造生产的工艺流程铸造生产是一个复杂的多工序组合的工艺过程,它包括以下主要工序:1)生产工艺准备,根据要生产的零件图、生产批量和交货期限,制定生产工艺方案和工艺文件,绘制铸造工艺图;2)生产准备,包括准备熔化用材料、造型制芯用材料和模样、芯盒、砂箱等工艺装备;3)造型与制芯;4)熔化与浇注;5)落砂清理与铸件检验等主要工序。
成形原理铸造生产是将金属加热熔化,使其具有流动性,然后浇入到具有一定形状的铸型型腔中,在重力或外力(压力、离心力、电磁力等)的作用下充满型腔,冷却并凝固成铸件(或零件)的一种金属成形方法。
图1 铸造成形过程铸件一般作为毛坯经切削加工成为零件。
但也有许多铸件无需切削加工就能满足零件的设计精度和表面粗糙度要求,直接作为零件使用。
型砂的性能及组成1、型砂的性能型砂(含芯砂)的主要性能要求有强度、透气性、耐火度、退让性、流动性、紧实率和溃散性等。
2、型砂的组成型砂由原砂、粘接剂和附加物组成。
铸造用原砂要求含泥量少、颗粒均匀、形状为圆形和多角形的海砂、河砂或山砂等。
铸造用粘接剂有粘土(普通粘土和膨润土)、水玻璃砂、树脂、合脂油和植物油等,分别称为粘土砂,水玻璃砂、树脂砂、合脂油砂和植物油砂等。
为了进一步提高型(芯)砂的某些性能,往往要在型(芯)砂中加入一些附加物,如煤份、锯末、纸浆等。
型砂结构,如图2所示。
图2 型砂结构示意图工艺特点铸造是生产零件毛坯的主要方法之一,尤其对于有些脆性金属或合金材料(如各种铸铁件、有色合金铸件等)的零件毛坯,铸造几乎是唯一的加工方法。
与其它加工方法相比,铸造工艺具有以下特点:1)铸件可以不受金属材料、尺寸大小和重量的限制。
铸件材料可以是各种铸铁、铸钢、铝合金、铜合金、镁合金、钛合金、锌合金和各种特殊合金材料;铸件可以小至几克,大到数百吨;铸件壁厚可以从0.5毫米到1米左右;铸件长度可以从几毫米到十几米。
2)铸造可以生产各种形状复杂的毛坯,特别适用于生产具有复杂内腔的零件毛坯,如各种箱体、缸体、叶片、叶轮等。
铸造工序产品标准
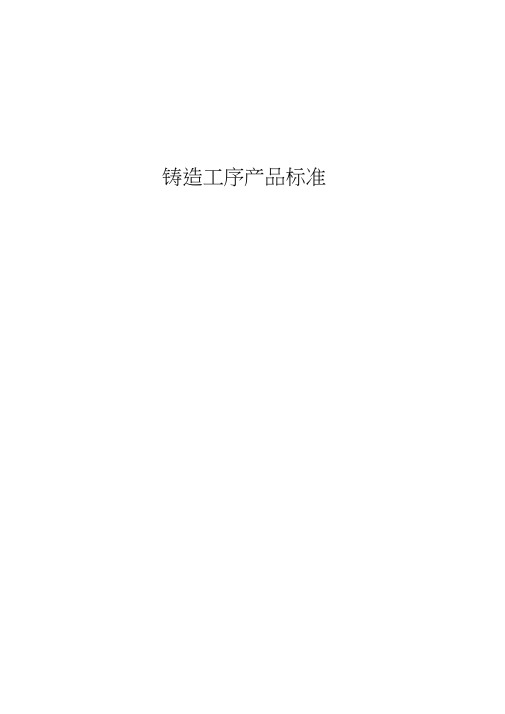
铸造工序产品标准铝及铝合金铸锭工序标准本标准规定了铝及铝合金铸锭的化学成分、尺寸偏差、表面质量、锯切、铳边和晶粒度的要求,适用于熔铸工序转热轧工序时铸锭的检查和验收。
铸锭尺寸及允许长度偏差应符合表2。
3. 表面质量3.1 GY/DY铸锭表面质量应符合表34. 内部质量铸锭做组织分析时(低倍、高倍例行检验),不得有影响使用的严重冶金缺陷存在。
铸锭内部缺陷类别见附录5. 氢含量要求对工艺文件无特殊说明的产品一般要求氢含量w 0.12ml/100gAI检测位置:过滤盆出口检测频次:正常生产时,每10天必须测一次氢,热轧反馈气泡出现时随时监测。
6. 锯切6.1工艺文件要求锯切头尾的,根据计划要求切成主料6.2铸锭头尾有严重缺陷的,一般以锯掉缺陷为准。
6.3斜切度:w 5mm6.4铸锭锯切完后应清扫表面残存的锯屑,并保持铸锭表面清洁,不得因锯切造成铸锭表面二次污染7. 铸锭组织7.1铸锭组织符合表48. 检测方法8.1铸锭内部质量检查为例行抽样检验,不做日常验收项目。
8.2其它项目作日常检验。
外观检测以目测为主,可借助卷尺测量缺陷大小。
铸锭弯曲程度拉线后用钢尺测量弯曲值。
8.3高压切片组织每月取样一次,每次取样4片,取样位置在头600mm处;有重大工艺调整时每次取样4片,取样位置在头600mm处;后工序反馈质量问题时随时检测。
9. 验收9.1铸锭在熔铸车间的验收属一次外观和化学成分的合格判定,若铸锭在后工序使用中发现问题且经技术中心分析属铸锭内部质量问题,做二次不合格判定。
9.2 按验收标准对铸锭进行验收,对不符合要求的做出及时的处理意见。
9.3 铸造车间对铸锭验收完毕后,在其头部钢印号下面贴检验合格标签9.4 铸锭上必须有高压、低压标识、批号标识,特殊专用的要有相应代号标识。
9.5 验收有异议时,由技术中心仲裁。
铸造工序常见产品缺陷。
铸造生产有哪些主要工序

铸造生产有哪些主要工序铸造是一种工业制造方法,通过将熔化的金属或其他材料注入模具中,待冷却凝固后得到所需形状的零件或构件的过程。
在铸造过程中,主要包括铸型制备、熔炼浇注、冷却凝固、去除浇口、整形修磨等一系列工序。
以下将详细介绍铸造生产的主要工序及其作用。
铸型制备铸型是用来容纳熔化金属或其他材料并使其凝固成型的模具,铸型制备是铸造生产中的第一步。
在铸型制备阶段,首先根据产品的形状和尺寸设计制作模具,然后根据模具制作出砂型或金属型,以便后续浇注熔化金属。
熔炼浇注熔炼浇注是指将金属或其他材料加热至熔化状态后,通过设备或工具将熔化物质倒入铸型中的过程。
在熔炼浇注阶段,需要控制好熔炼温度和浇注速度,确保熔化物质填充铸型并保持稳定的流动性,以得到理想的铸件形态。
冷却凝固在熔炼浇注后,熔化金属或其他材料会逐渐冷却凝固成型。
冷却凝固阶段的时间取决于铸件的厚度和材料的性质,一般较厚的铸件需要更长的冷却时间。
冷却凝固是铸造过程中至关重要的一步,直接影响着最终铸件的质量和性能。
去除浇口铸造完成后,铸件上会留有与浇口相连的余料,需要进行去除浇口处理。
去除浇口的主要目的是让铸件表面更加平整,减少后续修磨工序的难度,并且通过去除浇口可以避免影响铸件美观度和功能性。
整形修磨整形修磨是指根据设计要求对铸件表面进行加工处理,以消除可能存在的缺陷或不规则形状,使铸件达到精度要求。
这一工序通常包括车削、磨削、抛光等加工方式,旨在提高铸件的表面质量和精度,并确保其符合规范要求。
综上所述,铸造生产的主要工序包括铸型制备、熔炼浇注、冷却凝固、去除浇口、整形修磨等环节。
每个工序都起着至关重要的作用,互相配合,共同完成铸造生产过程,最终得到高质量、符合要求的铸件产品。
在实际生产中,各个工序需要密切配合,确保每个环节的质量和效率,从而提高铸造产品的生产效率和竞争力。
铸造企业工艺流程简介(带环保工程)

生产工艺简介1、生产工艺流程图本项目以生铁、废钢、孕育剂、球化丝、混配土、砂子、塑粉等为主要原料,生产发动机配件、外贸阀门件、农机配件。
/膜砂制芯生快'ft 电炉融化喂纥球化浇注或里落矽消砂"舞, 机加工喷堡固化成品铁、或恻桢掇M砂、煤机混砂造型砂处理彩洞上图2.6-1生产工艺流程图工艺流程简述(1)混砂造型:将型砂(包含落砂工序产生的旧砂)、煤粉、膨润土等按一定比例,用混砂机混合搅拌。
将模具放置在造型台上,设置好砂箱,通过混砂机将砂子冲入砂箱模具中,开启震实台震动,形成砂型。
部分产品内部需放置芯体,需先将覆膜砂投放到制芯机料仓,将其制成芯体,再利用成型的芯体完成砂体的造型。
(2)电炉熔炼:将生铁等原料按比例配好料后放进中频电炉熔炼,在熔炼成铁水状态时添加球化剂进行球化处理(有效地提高了铸铁的机械性能,特别是提高了塑性和韧性,从而得到比碳钢还高的强度)。
(3)浇注:将中频电炉熔炼好的铁水浇注到砂型内。
在浇注的过程中放入孕育剂(铁水经球化处理后容易出现白口,难以产生石墨核心。
因此,球化处理的同时,必须进行孕育处理。
孕育剂是一种可促进石墨化,减少白口倾向,改善石墨形态和分布状况,增加共晶团数量,细化基体组织,从而显著改善了球铁的机械性能)。
(6)落砂清砂:浇注后清理模具、将铸件表面的铸造砂等通过落砂滚筒将其清理干净,落下来的旧砂重新返回砂处理流水线混砂工序,重新造型使用。
(7)抛丸打磨:利用高速旋转的叶轮把钢丸抛掷出去,高速撞击零件表面,达到表面处理的要求。
(8)检验:对不合格产品重新返工制作;合格的产品进行下一道工序机加工。
(9)机加工:根据铸件要求,进行机械加工,加工完成后部分铸件进行检验包装,入库待售。
3)废气治理工艺流程描述:(1)活性炭吸附脱附催化燃烧装置(RCO)原理活性炭脱附:当吸附床吸附饱和后,切换脱附风阀和吸附风阀,启动脱附风机对该吸附床脱附。
脱附新鲜空气首先通过新风入口的换热器和点加热室进行加热,将新空气加热到120°C左右进入活性炭床,炭床受热后,活性炭吸附的溶剂挥发出来。
铸造工序标准

铝及铝合金铸锭工序标准本标准规定了铝及铝合金铸锭的化学成分、尺寸偏差、表面质量、锯切、铣边和晶粒度的要求,适用于熔铸工序转热轧工序时铸锭的检查和验收。
1. 表1 单位:ppm2. 尺寸及允许偏差铸锭尺寸及允许长度偏差应符合表2。
表2单位:mm3. 表面质量3.1GY/DY铸锭表面质量应符合表3表33.2高低压铸锭:重点控制表面鱼鳞的大小和冷隔的深度4. 内部质量铸锭做组织分析时(低倍、高倍例行检验),不得有影响使用的严重冶金缺陷存在。
铸锭内部缺陷类别见附录5. 氢含量要求对工艺文件无特殊说明的产品一般要求氢含量≤0.12ml/100gAl检测位置:深床出口检测频次:正常生产时,每10天测一次氢,热轧反馈气泡出现时随时监测。
6. 锯切6.1工艺文件要求锯切头尾的,根据计划要求切成主料6.2铸锭头尾有严重缺陷的,一般以锯掉缺陷为准。
6.3斜切度:≤5mm6.4 铸锭锯切完后应清扫表面残存的锯屑,并保持铸锭表面清洁,不得因锯切造成铸锭表面二次污染7. 铸锭组织7.1铸锭组织符合表4表48. 检测方法8.1铸锭内部质量检查为每批例行抽样检验,不做日常验收项目。
8.2其它项目作日常检验。
外观检测以目测为主,可借助卷尺测量缺陷大小。
铸锭弯曲程度拉线后用钢尺测量弯曲值。
9. 验收9.1 铸锭在熔铸车间的验收属一次外观和化学成分的合格判定,若铸锭在后工序使用中发现问题且评审分析属铸锭内部质量问题,做二次不合格判定。
9.2按验收标准对铸锭进行验收,对不符合要求的做出及时的处理意见。
9.3铸锭上必须有高压、低压标识、批号标识,特殊专用的要有相应代号标识。
9.4验收有异议时,由品管部仲裁。
铸造工序常见产品缺陷45。
- 1、下载文档前请自行甄别文档内容的完整性,平台不提供额外的编辑、内容补充、找答案等附加服务。
- 2、"仅部分预览"的文档,不可在线预览部分如存在完整性等问题,可反馈申请退款(可完整预览的文档不适用该条件!)。
- 3、如文档侵犯您的权益,请联系客服反馈,我们会尽快为您处理(人工客服工作时间:9:00-18:30)。
铝及铝合金铸锭工序标准
本标准规定了铝及铝合金铸锭的化学成分、尺寸偏差、表面质量、锯切、铳边和晶粒度的要求,适用于熔铸工序转热轧工序时铸锭的检查和验收。
2.尺寸及允许偏差
铸锭尺寸及允许长度偏差应符合表2。
表2
3.
3.1 GY/DY铸锭表面质量应符合表3
4. 内部质量
铸锭做组织分析时(低倍、高倍例行检验),不得有影响使用的严重冶金缺陷存在。
铸
锭内部缺陷类别见附录
5. 氢含量要求
对工艺文件无特殊说明的产品一般要求氢含量w 0.12ml/100gAI
检测位置:深床出口
检测频次:正常生产时,每10天测一次氢,热轧反馈气泡出现时随时监测。
6. 锯切
6.1工艺文件要求锯切头尾的,根据计划要求切成主料
6.2铸锭头尾有严重缺陷的,一般以锯掉缺陷为准。
6.3斜切度:w 5mm
6.4铸锭锯切完后应清扫表面残存的锯屑,并保持铸锭表面清洁,不得因锯切造成铸锭表面
二次污染
7. 铸锭组织
7.1铸锭组织符合表4
8. 检测方法
8.1铸锭内部质量检查为每批例行抽样检验,不做日常验收项目。
8.2其它项目作日常检验。
外观检测以目测为主,可借助卷尺测量缺陷大小。
铸锭弯曲程度拉线后用钢尺测量弯曲值。
9. 验收
9.1铸锭在熔铸车间的验收属一次外观和化学成分的合格判定,若铸锭在后工序使用中发现问题且评审分析属铸锭内部质量问题,做二次不合格判定。
9.2按验收标准对铸锭进行验收,对不符合要求的做出及时的处理意见。
9.3 铸锭上必须有高压、低压标识、批号标识,特殊专用的要有相应代号标识。
9.4 验收有异议时,由品管部仲裁。