扭簧的设计
扭转弹簧的设计知识
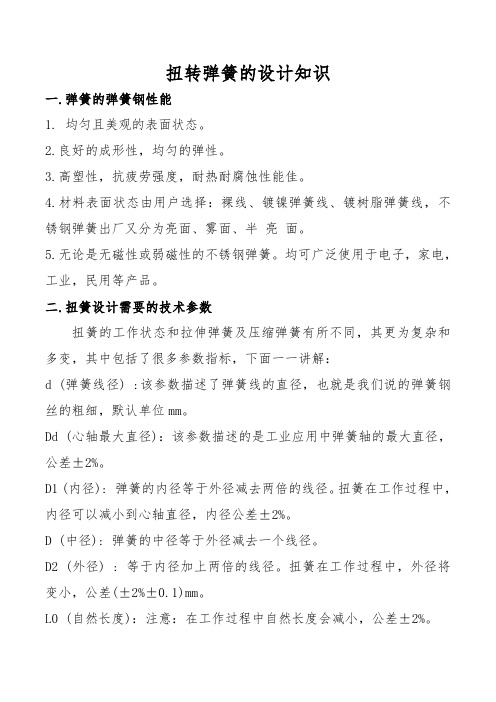
扭转弹簧的设计知识一.弹簧的弹簧钢性能1. 均匀且美观的表面状态。
2.良好的成形性,均匀的弹性。
3.高塑性,抗疲劳强度,耐热耐腐蚀性能佳。
4.材料表面状态由用户选择:裸线、镀镍弹簧线、镀树脂弹簧线,不锈钢弹簧出厂又分为亮面、雾面、半亮面。
5.无论是无磁性或弱磁性的不锈钢弹簧。
均可广泛使用于电子,家电,工业,民用等产品。
二.扭簧设计需要的技术参数扭簧的工作状态和拉伸弹簧及压缩弹簧有所不同,其更为复杂和多变,其中包括了很多参数指标,下面一一讲解:d (弹簧线径) :该参数描述了弹簧线的直径,也就是我们说的弹簧钢丝的粗细,默认单位mm。
Dd (心轴最大直径):该参数描述的是工业应用中弹簧轴的最大直径,公差±2%。
D1 (内径): 弹簧的内径等于外径减去两倍的线径。
扭簧在工作过程中,内径可以减小到心轴直径,内径公差±2%。
D (中径): 弹簧的中径等于外径减去一个线径。
D2 (外径) : 等于内径加上两倍的线径。
扭簧在工作过程中,外径将变小,公差(±2%±0.1)mm。
L0 (自然长度):注意:在工作过程中自然长度会减小,公差±2%。
Tum (扭转圈数):弹簧绕制的圈数,圈数的不同直接影响扭簧的性能。
扭簧的圈数越多扭力越小。
deg (原始角度):扭簧的两个扭脚之间的原始角度。
上图的原始角度为180°。
X1 (支承长度): 这是从弹簧圈身中轴到弹簧支承的长度,一般工作中是固定不动的,也就是我们所说的固定力臂,公差±2%。
X2 (施力长度):这是从弹簧圈身中轴到弹簧施力点的长度,一般工作中是转动的,也就是我们所说的施力力臂,公差±2%。
A1 (工作扭转角度):扭转弹簧的在工作中扭转的角度。
An (最大扭转角度):扭转弹簧的最大扭转角度。
F1 (工作负荷):扭簧在工作角度A1时作用在扭转弹簧支承上的作用力。
Fn (最大负荷):允许作用在扭转弹簧支承上的最大力,对应的是An 最大扭转角度时所需的作用力。
扭簧设计实例
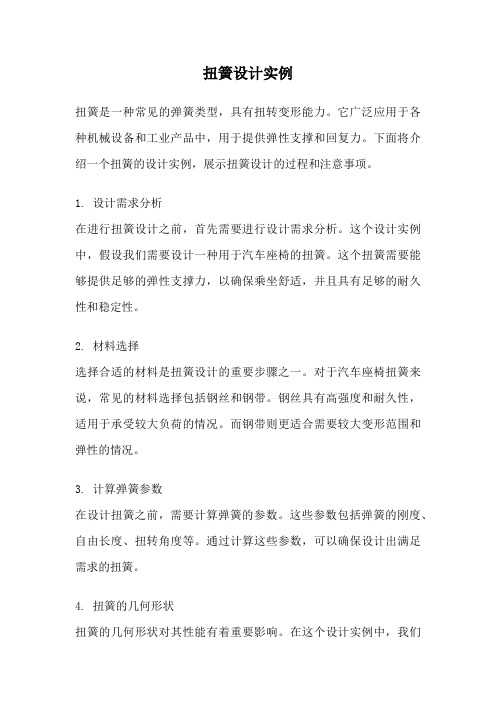
扭簧设计实例扭簧是一种常见的弹簧类型,具有扭转变形能力。
它广泛应用于各种机械设备和工业产品中,用于提供弹性支撑和回复力。
下面将介绍一个扭簧的设计实例,展示扭簧设计的过程和注意事项。
1. 设计需求分析在进行扭簧设计之前,首先需要进行设计需求分析。
这个设计实例中,假设我们需要设计一种用于汽车座椅的扭簧。
这个扭簧需要能够提供足够的弹性支撑力,以确保乘坐舒适,并且具有足够的耐久性和稳定性。
2. 材料选择选择合适的材料是扭簧设计的重要步骤之一。
对于汽车座椅扭簧来说,常见的材料选择包括钢丝和钢带。
钢丝具有高强度和耐久性,适用于承受较大负荷的情况。
而钢带则更适合需要较大变形范围和弹性的情况。
3. 计算弹簧参数在设计扭簧之前,需要计算弹簧的参数。
这些参数包括弹簧的刚度、自由长度、扭转角度等。
通过计算这些参数,可以确保设计出满足需求的扭簧。
4. 扭簧的几何形状扭簧的几何形状对其性能有着重要影响。
在这个设计实例中,我们可以选择一种常见的扭簧形状,如圆柱形。
通过选择合适的弹簧直径、线径和螺距,可以满足设计要求。
5. 弹簧的预压和预扭预压和预扭是扭簧设计中的重要步骤。
预压是指在安装扭簧时,给予其一定的压缩力,使其在工作时能够保持一定的压缩状态。
预扭是指在安装扭簧时,给予其一定的扭转角度,使其在工作时能够有足够的弹性支撑力。
通过合理的预压和预扭设计,可以确保扭簧在工作时具有稳定的性能。
6. 弹簧的制造和检测完成扭簧设计之后,需要进行制造和检测。
制造过程中需要选择合适的加工工艺和设备,确保扭簧的精度和质量。
检测过程中需要使用合适的检测设备和方法,对扭簧进行强度、刚度和变形等性能的测试。
7. 扭簧的应用和优化设计完成的扭簧可以应用于汽车座椅中。
在实际使用过程中,可以进行优化和改进,以提高扭簧的性能和寿命。
例如,可以通过调整扭簧的材料、几何形状和预压预扭等参数,来满足不同座椅的需求。
总结:以上是一个扭簧设计实例的介绍。
通过对扭簧的设计需求分析、材料选择、参数计算、几何形状设计、预压预扭设计、制造和检测等步骤的介绍,可以对扭簧设计的过程有一个清晰的了解。
扭簧设计文档

扭簧设计1. 简介扭簧是一种常见的机械弹性元件,广泛应用于各种机械装置中。
它具有弹性变形能力,能够承受旋转或回转运动时的扭矩,常用于提供力矩或恢复力的作用。
本文将介绍扭簧的设计原理、计算方法和注意事项。
2. 设计原理扭簧的设计需要考虑以下几个关键因素:2.1 材料选择扭簧通常使用优质的弹簧钢材料,如65MN、60SI2MN等。
这些材料具有良好的弹性和硬度,能够确保扭簧的稳定性和耐久性。
2.2 弹性系数扭簧的弹性系数是一项重要的设计参数,用于描述扭簧的刚度。
弹性系数决定了扭簧所能承受的最大扭力和变形程度。
在设计过程中,需要合理选择弹性系数,使得扭簧在工作条件下能够满足所需的扭矩和回弹力。
2.3 螺旋方向扭簧的螺旋方向分为左旋和右旋,具体选择取决于应用需求。
在实际应用中,需要根据装置的运动方式和力矩要求来确定扭簧的螺旋方向,以确保扭簧可以提供所需的扭矩和回弹力。
3. 计算方法扭簧的设计计算需要考虑以下几个方面:3.1 扭矩计算根据应用需求和工作条件,可以通过扭矩计算公式来确定扭簧的设计参数。
一般情况下,扭矩计算公式为:T = K * φ * G式中,T表示扭矩,K表示弹簧的弹性系数,φ表示扭簧的角度变形,G表示扭簧的几何形状参数。
3.2 变形计算扭簧的变形计算需要考虑弹簧材料的弹性模量和几何参数。
一般情况下,变形计算公式为:φ = (T * L) / (G * d^4)式中,φ表示扭簧的角度变形,T表示扭矩,L表示扭簧的长度,G表示扭簧的剪切模量,d表示扭簧的直径。
3.3 弹性系数计算扭簧的弹性系数计算需要考虑弹簧材料的切变模量和几何参数。
一般情况下,弹性系数计算公式为:K = (G * d^4) / (8 * D^3 * n)式中,K表示弹性系数,G表示扭簧的剪切模量,d表示扭簧的直径,D表示扭簧的平均直径,n表示扭簧的总匝数。
4. 注意事项在扭簧设计过程中,需要注意以下几点:•根据应用需求选择合适的弹簧钢材料,确保扭簧的强度和耐久性;•合理选择扭簧的弹性系数,以满足所需的扭矩和回弹力;•在设计过程中考虑扭簧的螺旋方向,以适应装置的运动方式和力矩要求;•使用合适的计算方法,准确计算扭簧的扭矩、变形和弹性系数;•定期检查和维护扭簧,确保其正常工作。
汽车扭簧扭力公差设计参照标准

汽车扭簧扭力公差设计参照标准
汽车扭簧扭力公差设计通常参照以下标准:
1. ISO 2088: 这是国际标准化组织(ISO)发布的标准,涉及弹簧的一般要求和试验方法。
其中包括了关于扭簧扭力公差的设计指南。
2. SAE J543: 这是美国汽车工程师学会(SAE)发布的标准,用于弹簧的设计原则和测试要求。
该标准提供了有关扭簧的公差范围和设计建议。
3. DIN 2095: 这是德国标准化协会(DIN)发布的标准,涵盖了扭簧的规格和试验方法。
其中包括了有关扭簧扭力公差的指导。
这些标准提供了关于扭簧扭力公差的设计参考值,以确保扭簧在使用中的性能和可靠性符合要求。
请注意,具体的设计参考值可能因不同应用和制造商而有所不同,因此最好根据相关标准和制造商的要求进行具体设计。
扭簧设计计算范文

扭簧设计计算范文第一步:确定应力和变形在扭簧设计中,首先需要确定扭簧所需要承受的应力和变形。
应力是指扭簧在受力时所承受的力。
变形是指扭簧在受力时所发生的弯曲程度。
这两个参数都是根据具体的应用和需求来确定的。
第二步:确定扭簧材料扭簧的材料选择对于扭簧的设计至关重要。
一般来说,扭簧通常采用高强度的弹簧钢或不锈钢。
根据扭簧所需要的弹性模量、屈服强度和延伸率等参数来选择合适的材料。
第三步:计算扭簧的参数在确定了应力和变形以及材料之后,需要计算扭簧的具体参数。
主要包括弹簧常数、扭矩、螺旋角、扭转角等。
这些参数的计算需要使用相关的数学公式和物理原理。
第四步:确定扭簧的尺寸根据扭簧的参数,确定扭簧的具体尺寸。
包括弹簧直径、圈数、绕制直径等。
在确定尺寸时,需要考虑到扭簧的受力情况,合理地安排扭簧的空间,以保证扭簧能够正常工作。
第五步:进行强度校验通过计算和确定尺寸之后,需要对扭簧进行强度校验。
主要是对扭簧的材料强度和设计参数进行评估,确保扭簧在受力的情况下不会发生断裂或损坏。
第六步:确定扭簧的工艺参数根据扭簧的设计和需求,确定扭簧的工艺参数。
这包括绕制工艺、热处理工艺和表面处理工艺等。
根据不同的工艺要求,选择合适的工艺参数,并进行相应的加工和处理。
第七步:进行性能测试完成扭簧的设计和加工之后,需要进行性能测试。
主要是对扭簧进行强度和变形的测试,以确保扭簧能够满足设计和使用要求。
总结:扭簧设计计算是一项复杂的工作,需要考虑到多个参数和因素。
通过合理地确定应力和变形、选择合适的材料、计算扭簧的参数和尺寸、进行强度校验、确定工艺参数以及进行性能测试,可以设计出性能优良、质量可靠的扭簧产品。
扭簧弹簧的设计和计算
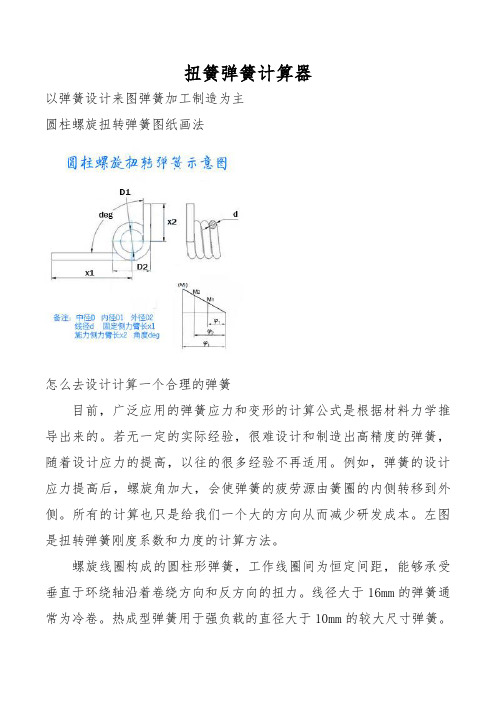
扭簧弹簧计算器以弹簧设计来图弹簧加工制造为主圆柱螺旋扭转弹簧图纸画法怎么去设计计算一个合理的弹簧目前,广泛应用的弹簧应力和变形的计算公式是根据材料力学推导出来的。
若无一定的实际经验,很难设计和制造出高精度的弹簧,随着设计应力的提高,以往的很多经验不再适用。
例如,弹簧的设计应力提高后,螺旋角加大,会使弹簧的疲劳源由簧圈的内侧转移到外侧。
所有的计算也只是给我们一个大的方向从而减少研发成本。
左图是扭转弹簧刚度系数和力度的计算方法。
螺旋线圈构成的圆柱形弹簧,工作线圈间为恒定间距,能够承受垂直于环绕轴沿着卷绕方向和反方向的扭力。
线径大于16mm的弹簧通常为冷卷。
热成型弹簧用于强负载的直径大于10mm的较大尺寸弹簧。
备注:该计算设计用于线圈卷绕方向的扭转负载,不计入弹簧内部或外部导向零件的支撑效果。
也不计入出现的摩擦效果。
线圈之间的可能的摩擦也不计入在内。
扭簧的常见形式··外臂扭转弹簧···内臂扭转弹簧···中心臂扭转弹簧···平列双扭弹簧·弹簧力度设计扭簧按两种基本设计制造:紧和松(线圈间隙)。
如果是静态负载,紧凑的线圈为推荐选项。
但是,工作线圈之间出现摩擦,这将导致弹簧寿命减少。
另外,线圈的过于接近的间隙阻止弹簧完美喷丸。
由于弹簧端部的节构形状,弹簧与导杆的摩擦等均影响弹簧的特性,所以无特殊需要时,不规定特性要求。
如规定弹簧的特性要求时,应采用簧圈间有间隙的弹簧,用指定扭转变形角时的扭力进行考核。
扭转弹簧的类型如上图,前三类为普通形式扭转弹簧,第4种为平列式双扭转弹簧。
平列双扭转弹簧,是用一根弹簧材料在同一芯轴上,向相反方向缠绕所得的两个圈数相同的弹簧。
其中每一个弹簧的扭转度,相当于以此两个弹簧的总长作为一单个弹簧使用时的2倍。
平列双扭弹簧的刚度为其单个弹簧的4倍,变形量则为单个弹簧的1/4.因此,这种平列双扭转弹簧效率高。
扭簧结构设计
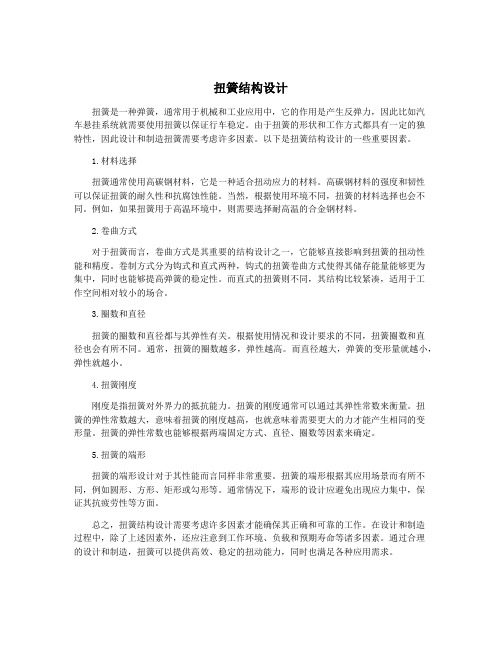
扭簧结构设计扭簧是一种弹簧,通常用于机械和工业应用中,它的作用是产生反弹力,因此比如汽车悬挂系统就需要使用扭簧以保证行车稳定。
由于扭簧的形状和工作方式都具有一定的独特性,因此设计和制造扭簧需要考虑许多因素。
以下是扭簧结构设计的一些重要因素。
1.材料选择扭簧通常使用高碳钢材料,它是一种适合扭动应力的材料。
高碳钢材料的强度和韧性可以保证扭簧的耐久性和抗腐蚀性能。
当然,根据使用环境不同,扭簧的材料选择也会不同。
例如,如果扭簧用于高温环境中,则需要选择耐高温的合金钢材料。
2.卷曲方式对于扭簧而言,卷曲方式是其重要的结构设计之一,它能够直接影响到扭簧的扭动性能和精度。
卷制方式分为钩式和直式两种,钩式的扭簧卷曲方式使得其储存能量能够更为集中,同时也能够提高弹簧的稳定性。
而直式的扭簧则不同,其结构比较紧凑,适用于工作空间相对较小的场合。
3.圈数和直径扭簧的圈数和直径都与其弹性有关。
根据使用情况和设计要求的不同,扭簧圈数和直径也会有所不同。
通常,扭簧的圈数越多,弹性越高。
而直径越大,弹簧的变形量就越小,弹性就越小。
4.扭簧刚度刚度是指扭簧对外界力的抵抗能力。
扭簧的刚度通常可以通过其弹性常数来衡量。
扭簧的弹性常数越大,意味着扭簧的刚度越高,也就意味着需要更大的力才能产生相同的变形量。
扭簧的弹性常数也能够根据两端固定方式、直径、圈数等因素来确定。
5.扭簧的端形扭簧的端形设计对于其性能而言同样非常重要。
扭簧的端形根据其应用场景而有所不同,例如圆形、方形、矩形或勾形等。
通常情况下,端形的设计应避免出现应力集中,保证其抗疲劳性等方面。
总之,扭簧结构设计需要考虑许多因素才能确保其正确和可靠的工作。
在设计和制造过程中,除了上述因素外,还应注意到工作环境、负载和预期寿命等诸多因素。
通过合理的设计和制造,扭簧可以提供高效、稳定的扭动能力,同时也满足各种应用需求。
扭簧设计计算表格

弹簧弹性模量
弹簧材料 不锈钢A组 不锈钢B组 不锈钢C组 琴钢丝E组 琴钢丝F组 琴钢丝G组
弹性模量 试验弯曲
E(MPa)
应力系数
185000 0.75
195000 0.75
195000 0.75
206000 0.78
206000 0.78
206000 0.78
受力侧力臂l2(mm)
7
负荷类型
静负荷
扭簧材料选择
不锈钢A组
以下为自动计算
项目
公式
弹簧弹性模量
Hale Waihona Puke 系统查表扭簧内径D1(mm)
D1=D-d
扭转变形角φ(°)
φ=φ2-φ1
内径减小量△D
△D=φ2*D/(360*n)
请输入 请输入 请输入 请输入 请选择 请选择
计算结果 185000
11 80 0.36
设计计算 强度校核
0.68 1400 952 790.58 158.12
上限应力系数
σmax/Rm
0.565
下限应力系数
σmin/Rm
0.11
循环特征系数γ
γ=σmin/σmax
0.2
强度校核要求:从上述计算中取坐标点(下限应力系数,上限应
力系数),若该点在γ=σmin/σmax与要求达到的寿命次数斜线
的交点以下,则说明此扭簧的疲劳寿命N大于寿命次数,符合寿命
扭矩T2 (N.mm)
T2=T´*φ2
620.92
曲度系数Kb
顺向扭转时为1
1
弯曲应力系数K1´ 材料抗拉强度Rm
(N/mm²) 许用弯曲应力σ