Edge joints with dowel type fasteners in cross laminated timber
ISO 21534-2007

Reference number ISO 21534:2007(E)INTERNATIONAL STANDARD ISO 21534Second edition 2007-10-01Non-active surgical implants — Joint replacement implants — Particular requirementsImplants chirurgicaux non actifs — Implants de remplacement d'articulation — Exigences particulières--`,,```,,,,````-`-`,,`,,`,`,,`---ISO 21534:2007(E)PDF disclaimerThis PDF file may contain embedded typefaces. In accordance with Adobe's licensing policy, this file may be printed or viewed but shall not be edited unless the typefaces which are embedded are licensed to and installed on the computer performing the editing. In downloading this file, parties accept therein the responsibility of not infringing Adobe's licensing policy. The ISO Central Secretariat accepts no liability in this area.Adobe is a trademark of Adobe Systems Incorporated.Details of the software products used to create this PDF file can be found in the General Info relative to the file; the PDF-creation parameters were optimized for printing. Every care has been taken to ensure that the file is suitable for use by ISO member bodies. In the unlikely event that a problem relating to it is found, please inform the Central Secretariat at the address given below.COPYRIGHT PROTECTED DOCUMENT© ISO 2007All rights reserved. Unless otherwise specified, no part of this publication may be reproduced or utilized in any form or by any means, electronic or mechanical, including photocopying and microfilm, without permission in writing from either ISO at the address below or ISO's member body in the country of the requester. ISO copyright officeCase postale 56 • CH-1211 Geneva 20 Tel. + 41 22 749 01 11 Fax + 41 22 749 09 47 E-mail copyright@ Web Published in Switzerland--`,,```,,,,````-`-`,,`,,`,`,,`---ISO 21534:2007(E)Contents PageForeword.............................................................................................................................................................v Introduction.......................................................................................................................................................vi 1 Scope.. (1)2 Normative references...........................................................................................................................13 Terms and definitions...........................................................................................................................24 Intended performance..........................................................................................................................25 Design attributes...................................................................................................................................3 5.1 General...................................................................................................................................................3 5.2 Surface finish of metallic or ceramic implants articulating on ultra-high-molecular-weightpolyethylene (UHMWPE)......................................................................................................................3 5.3 Surface finish of metallic or ceramic partial implants......................................................................3 5.4 Surfaces of convex, spherically-conforming metallic or ceramic implants articulating onUHMWPE................................................................................................................................................3 5.5 Surfaces of spherically-conforming metallic or ceramic partial implants......................................3 5.6 Surfaces of concave, spherically-conforming UHMWPE components...........................................3 6 Materials ................................................................................................................................................4 6.1 General...................................................................................................................................................4 6.2 Dissimilar metals or alloys ..................................................................................................................4 7 Design evaluation.................................................................................................................................4 7.1 General...................................................................................................................................................4 7.2 Preclinical evaluation...........................................................................................................................4 7.3 Clinical investigation............................................................................................................................5 7.4 Post market surveillance .....................................................................................................................5 8 Manufacture and inspection................................................................................................................5 8.1 General...................................................................................................................................................5 8.2 Metal surfaces.......................................................................................................................................5 8.3 Plastic surfaces.....................................................................................................................................5 8.4 Ceramic surfaces..................................................................................................................................5 9 Sterilization............................................................................................................................................6 9.1 General...................................................................................................................................................6 9.2 Expiry.....................................................................................................................................................6 10 Packaging..............................................................................................................................................6 11 Information supplied by the manufacturer ........................................................................................6 11.1 General...................................................................................................................................................6 11.2 Labelling of implants for use on one side of the body only.............................................................6 11.3 Instructions for orientation of implants..............................................................................................6 11.4 Markings for orientation of the implants............................................................................................6 11.5 Placing of markings on implants ........................................................................................................6 11.6 Restrictions on use...............................................................................................................................7 11.7 Re-sterilization of zirconia ceramics..................................................................................................7 11.8Labelling of implants for use with or without bone cement (7)Annex A (informative) List of International Standards for materials found acceptable for themanufacture of implants......................................................................................................................8 Annex B (informative) List of International Standards for materials found acceptable or notacceptable for articulating surfaces of implants (9)--`,,```,,,,````-`-`,,`,,`,`,,`---ISO 21534:2007(E)Annex C (informative) List of materials found acceptable or non-acceptable for metallic combinations for non-articulating contacting surfaces of implants (11)Bibliography (12)--`,,```,,,,````-`-`,,`,,`,`,,`---ISO 21534:2007(E)ForewordISO (the International Organization for Standardization) is a worldwide federation of national standards bodies (ISO member bodies). The work of preparing International Standards is normally carried out through ISO technical committees. Each member body interested in a subject for which a technical committee has been established has the right to be represented on that committee. International organizations, governmental and non-governmental, in liaison with ISO, also take part in the work. ISO collaborates closely with the International Electrotechnical Commission (IEC) on all matters of electrotechnical standardization.International Standards are drafted in accordance with the rules given in the ISO/IEC Directives, Part 2.The main task of technical committees is to prepare International Standards. Draft International Standards adopted by the technical committees are circulated to the member bodies for voting. Publication as an International Standard requires approval by at least 75 % of the member bodies casting a vote.Attention is drawn to the possibility that some of the elements of this document may be the subject of patent rights. ISO shall not be held responsible for identifying any or all such patent rights.--`,,```,,,,````-`-`,,`,,`,`,,`---ISO 21534 was prepared by Technical Committee ISO/TC 150, Implants for surgery, Subcommittee SC 4, Bone and joint replacements.This second edition cancels and replaces the first edition (ISO 21534:2002), which has been technically revised.ISO 21534:2007(E)IntroductionThere are three levels of International Standard dealing with non-active surgical implants. These are as follows, with level 1 being the highest:⎯level 1: general requirements for non-active surgical implants and instrumentation used in association with implants;--`,,```,,,,````-`-`,,`,,`,`,,`---⎯level 2: particular requirements for families of non-active surgical implants;⎯level 3: specific requirements for types of non-active surgical implant.This International Standard is a level 2 standard and contains requirements that apply to all non-active surgical implants in the family of joint replacement implants.The level 1 standard contains requirements that apply to all non-active surgical implants. It also indicates that there are additional requirements in the level 2 and level 3 standards. The level 1 standard has been published as ISO 14630.Level 3 standards apply to specific types of implants within a family, such as knee and hip joints. To address all requirements, it is recommended that a standard of the lowest available level be consulted first.INTERNATIONAL STANDARD ISO 21534:2007(E) Non-active surgical implants — Joint replacement implants — Particular requirements1 ScopeThis International Standard specifies particular requirements for total and partial joint replacement implants, artificial ligaments and bone cement, hereafter referred to as implants. For the purposes of this International Standard, artificial ligaments and their associated fixing devices are included in the term "implant".It specifies requirements for intended performance, design attributes, materials, design evaluation, manufacturing, sterilization, packaging and information to be supplied by the manufacturer.Some tests required to demonstrate conformance to this International Standard are contained in or referenced in level 3 standards.2 Normative referencesThe following referenced documents are indispensable for the application of this document. For dated references, only the edition cited applies. For undated references, the latest edition of the referenced document (including any amendments) applies.ISO 4287, Geometrical Product Specifications (GPS) — Surface texture: Profile method — Terms, definitions and surface texture parametersISO 7206-4, Implants for surgery — Partial and total hip joint prostheses — Part 4: Determination of endurance properties of stemmed femoral componentsISO 7206-8, Implants for surgery — Partial and total hip joint prostheses — Part 8: Methods of determining endurance performance of stemmed femoral componentsISO 14155-1, Clinical investigation of medical devices for human subjects — Part 1: General requirementsISO 14242-1, Implants for surgery — Wear of total hip-joint prostheses — Part 1: Loading and displacement parameters for wear-testing machines and corresponding environmental conditions for testsISO 14242-2, Implants for surgery — Wear of total hip joint prostheses — Part 2: Methods of measurementISO 14243-2, Implants for surgery — Wear of total knee-joint prostheses — Part 2: Methods of measurement ISO 14630:—1), Non-active surgical implants — General requirementsISO 14879-1, Implants for surgery — Total knee-joint prostheses — Part 1: Determination of endurance properties of knee tibial trays1) To be published. (Revision of ISO 14630:2005)--`,,```,,,,````-`-`,,`,,`,`,,`---ISO 21534:2007(E)3 Terms and definitionsFor the purposes of this document, the terms and definitions in ISO 14630 together with the following apply.3.1artificial ligamentdevice, including its necessary fixing devices, intended to augment or replace the natural ligament3.2joint replacement implantimplantable device, including ancillary implanted components and materials, intended to provide function similar to a natural joint and which is connected to the corresponding bones3.3mean centreposition within the spherical head for which the average of the distances to a set of points uniformly distributed over the surface of the sphere is minimum3.4radial separation valuedifference between the mean radius of the spherical surface and the radius to the point on the spherical surface furthest from the mean centreNOTE The units of the radial separation value are in micrometres.4 Intended performance--`,,```,,,,````-`-`,,`,,`,`,,`---For the purpose of this International Standard, the intended performance of implants shall conform to Clause 4 of ISO 14630:—, and the design input shall additionally address the following matters:a) intended minimum and maximum relative angular movement between the skeletal parts to which the jointreplacement implant is attached;b) expected maximum load actions (forces and moments) to be transmitted to the bony parts to which thejoint replacement implant is attached;c) dynamic response of the body to the shape/stiffness of the implants;d) expected wear of articulating surfaces;e) suitability of the dimensions and shape of the implant for the population for which it is intended;f) strength of the adhesion and durability of surface coatings or surface treatments.NOTE 1 The clinical indications and contra-indications for the use of a particular implant are complex and should be reviewed by the surgeons when they are selecting implants to be used for particular patients, relying upon their own personal judgment and experience.NOTE 2 The lifetime of an implant depends on the interaction of various factors; some are the responsibility of the manufacturer, some, such as the implantation technique, are the responsibility of the surgeon in conducting the operation, and some relate to the patient, for example, the biological and physiological response to the implant, the medical condition of the patient, the conduct of the patient in respect of increasing body weight, carriage of heavy loads and adopting a high level of physical activity.ISO 21534:2007(E)5 Design attributes5.1 GeneralThe development of the design attributes to meet the performance intended by the manufacturer shall conform to the requirements of Clause 5 of ISO 14630:—, and in addition, account shall be taken of the following points:a) the strength of adhesion and durability of surface coatings and surface treatments; b) the wear of the articulating and other surfaces;c) stability of the implant while allowing prescribed minimum and maximum relative movements between theskeletal parts; d) avoidance of cutting or abrading tissue during function other than insertion or removal; e) the creep resistance and rupture characteristics, particularly as they relate to ligaments.NOTE 1 Methods of assessment of the wear of articulating and other surfaces are prescribed in, e.g. ISO 14242-2 and ISO 14243-1, -2 and -3. NOTE 2More specific requirements, such as that for hip joint replacements, might appear in other standards.5.2 Surface finish of metallic or ceramic implants articulating on ultra-high-molecular-weight polyethylene (UHMWPE)The articulating surfaces of metallic or ceramic components of total joint replacements intended to articulate on UHMWPE shall have a surface roughness value Ra no greater than 0,1 µm (when measured in accordance with 7.2.2).5.3 Surface finish of metallic or ceramic partial implantsThe articulating surface of metallic or ceramic components of partial joint replacements shall have a surface roughness value Ra no greater than 0,5 µm (when measured in accordance with 7.2.2).5.4 Surfaces of convex, spherically-conforming metallic or ceramic implants articulating on UHMWPEThe articulating surface of convex spherically conforming metallic or ceramic components of total joint replacements intended to articulate on UHMWPE shall have a surface roughness Ra no greater than 0,05 µm and a radial separation value for sphericity no greater than 10 µm (when measured in accordance with 7.2.2 and 7.2.3).5.5 Surfaces of spherically-conforming metallic or ceramic partial implantsThe articulating surface of spherically conforming metallic or ceramic components of partial joint replacements shall have a surface roughness value Ra no greater than 0,5 µm and a radial separation value for sphericity no greater than 100 µm (when measured in accordance with 7.2.2 and 7.2.3).5.6 Surfaces of concave, spherically-conforming UHMWPE componentsThe articulating surface of concave, spherically-conforming UHMWPE components of total joint replacements shall have a surface roughness Ra no greater than 2 µm and a radial separation value for sphericity no greater than 200 µm (when measured in accordance with 7.2.2 and 7.2.3).--`,,```,,,,````-`-`,,`,,`,`,,`---ISO 21534:2007(E)6 Materials6.1 GeneralThe requirements of Clause 6 of ISO 14630:— apply together with the particular requirement of 6.2 of the present document.NOTE 1 Annex A gives a list of International Standards for materials found acceptable through proven use for the manufacture of implants or for use in association with implants.NOTE 2 Annex B gives lists of International Standards for pairs of materials found acceptable or not acceptable through proven use for articulating surfaces of implants.NOTE 3 Where 6.1 of ISO 14630:— states that the acceptability of materials may be demonstrated by selection from the materials found suitable by proven clinical use in similar applications, for the purposes of this International Standard, proven use should be demonstrated by records of implantation of at least 500 of the implants and recorded satisfactory clinical use over a period of not less than five years.6.2 Dissimilar metals or alloysFor applications in which two dissimilar metals or alloys or the same metals or alloys in different metallurgical states are in contact where articulation is not intended, combinations used shall not produce unacceptable galvanic effects.NOTE Annex C gives lists of International Standards for acceptable and unacceptable metallic combinations for use in non-articulating bearing surfaces of implants.7 Design evaluation7.1 GeneralJoint replacement implants shall be evaluated in order to demonstrate that the intended performance is achieved. This evaluation shall be in accordance with Clause 7 of ISO 14630:— together with the particular requirements of 7.2 to 7.4. This evaluation shall be undertaken using components fully representative of the final condition ready for implantation.7.2 Preclinical evaluation7.2.1 GeneralPreclinical evaluation shall consider:a) biocompatibility of any materials not previously used;b) mechanical loads and the related movements to which the implants can be subjected when functioning asprescribed by ISO 14630;c) fatigue testing of highly stressed parts in accordance with ISO 7206-4, ISO 7206-8 and ISO 14879-1;d) wear testing of articulating bearing surfaces in accordance with e.g. ISO 14242-1, ISO 14242-2 andISO 14243-1;e) the suitability of the dimensions and shape of the implant for the intended population;NOTE The suitability of the dimensions and shape of the implant for the intended population can be demonstrated by cadaver implantation, the use of imaging systems such as X-ray, CAT scan or magnetic resonance imaging, or by reference to corresponding implants of proven clinical use (see Note 3 of 6.1).f) adhesion and durability of coatings if present.7.2.2 Surface roughness measurementSurface roughness shall be measured according to one of the methods given in ISO 4287.7.2.3 Sphericity measurementRadial separation values for sphericity shall be measured according to a method demonstrated to be accurate and repeatable.NOTE A suitable method is described in the National Physical Laboratory (NPL) [30].7.3 Clinical investigationThe clinical investigation shall be conducted according to the general requirements of ISO 14155-1.7.4 Post market surveillance--`,,```,,,,````-`-`,,`,,`,`,,`---The post-market performance of joint replacement implants shall be determined.NOTE Suitable methodologies include survival analysis (with revision as the endpoint) and clinical assessment.Where it is available, relevant information from joint replacement registries are taken into account.8 Manufacture and inspection8.1 GeneralThe requirements of Clause 8 of ISO 14630:— apply together with the particular requirements of 8.2 to 8.4.8.2 Metal surfacesAll polishing operations on metallic components shall be performed using an iron-free material. Clean, degrease, rinse and dry all components and examine the articulating surfaces using normal or corrected vision. The surfaces shall be free of any imperfections that would impair their function and also be free from deposited finishing materials or other contaminants.NOTE Examples of imperfections which might impair function include scale, tool marks, nicks, scratches, cracks, cavities, burrs and other defects.8.3 Plastic surfacesArticulating surfaces of plastic components shall not be prepared using non-removable abrasive or polishing compounds. Clean, degrease (if necessary), rinse and dry the components and examine them using normal or corrected vision. The surfaces shall be free from particulate contamination.8.4 Ceramic surfacesCeramic components shall be cleaned, degreased, rinsed, dried and examined using normal or corrected vision. The articulating surfaces shall be free of any imperfections that would impair their function.NOTE Examples of imperfections which might impair function include particulate contamination, chemical discolouration (spots or larger areas), tool marks, nicks, chips, cavities and cracks.9 Sterilization9.1 GeneralThe requirements of Clause 9 of ISO 14630:— apply together with the following.The effects of the sterilization process shall not impair the intended performance of the implant [see Clause 4 and 7.2.1 c), d) and f)].Implants containing UHMWPE and sterilized by ionizing radiation, shall not be supplied for clinical use if an accumulated dose of radiation higher than 40 kGy has been received. This requirement does not apply if radiation intended to improve the mechanical characteristics of the material is combined with the radiation for sterilization purposes.9.2 ExpiryThe manufacturer shall conduct an investigation, and record the results, to ascertain the expiry date to be marked on the labelling for the implant.10 PackagingThe requirements of Clause 10 of ISO 14630:— shall apply. The expiry date (see 9.2) shall be marked on the label.11 Information supplied by the manufacturer11.1 GeneralThe requirements of Clause 11 of ISO 14630:— shall apply together with the requirements in 11.2 to 11.8.11.2 Labelling of implants for use on one side of the body onlyLabelling for implants designed for use on one side of the body only shall bear the symbol "LEFT'' or "L" for implants to be used on the left side or "RIGHT'' or "R" for implants to be used on the right side.11.3 Instructions for orientation of implantsThe instruction leaflet and/or manual shall, where necessary, indicate the required orientation of the implant relative to the body part. It shall also refer to the relevant marking(s) on the implant or the label (see 11.2 and 11.4).11.4 Markings for orientation of the implantsThe implant shall bear the symbol "ANT'' on the front and/or "POST'' on the back where this is necessary for interpretation of the instructions relating to the required orientation of the implant relative to the body given in the instruction leaflet and/or manual (see 11.3).11.5 Placing of markings on implantsMarkings shall be placed on the implant where they will not impair its intended function [see 7.2.1 c), d) and f)]. --` , , ` ` ` , , , , ` ` ` ` -` -` , , ` , , ` , ` , , ` ---11.6 Restrictions on useIf an implant is intended for a restricted population this shall be stated in the instructions for use or in themanual.11.7 Re-sterilization of zirconia ceramicsComponents manufactured from zirconia ceramics shall include an instruction advising users "Do not sterilizeusing moist heat”.11.8 Labelling of implants for use with or without bone cementLabelling for implants shall bear an appropriate legend as shown in Table 1.Table 1 — LabellingUsage LegendAlternativelegend Implants intended to be used withbone cementFOR USE WITH CEMENT CEMENTEDImplants intended to be usedwithout bone cementUNCEMENTED CEMENTLESSImplants intended to be used optionally USE WITH CEMENT ORUNCEMENTEDNO LEGEND--`,,```,,,,````-`-`,,`,,`,`,,`---Annex A(informative)List of International Standards for materials found acceptablefor the manufacture of implantsThe following International Standards deal with materials that have been found acceptable through proven use for the manufacture of implants. The inclusion of materials in this annex does not imply their satisfactory use in any particular application; neither does it relieve the manufacturer of the obligation to undertake a design evaluation such as prescribed in Clause 7.ISO 5832-1, Implants for surgery — Metallic materials — Part 1: Wrought stainless steelISO 5832-2, Implants for surgery — Metallic materials — Part 2: Unalloyed titaniumISO 5832-3, Implants for surgery — Metallic materials — Part 3: Wrought titanium 6-aluminium 4-vanadium alloyISO 5832-4, Implants for surgery — Metallic materials — Part 4: Cobalt-chromium-molybdenum casting alloy ISO 5832-5, Implants for surgery — Metallic materials — Part 5: Wrought cobalt-chromium-tungsten-nickel alloyISO 5832-6, Implants for surgery — Metallic materials — Part 6: Wrought cobalt-nickel-chromium-molybdenum alloyISO 5832-7, Implants for surgery — Metallic materials — Part 7: Forgeable and cold-formed cobalt-chromium-nickel-molybdenum-iron alloyISO 5832-8, Implants for surgery — Metallic materials — Part 8: Wrought cobalt-nickel-chromium-molybdenum-tungsten-iron alloyISO 5832-9, Implants for surgery — Metallic materials — Part 9: Wrought high nitrogen stainless steel --`,,```,,,,````-`-`,,`,,`,`,,`---ISO 5832-11, Implants for surgery — Metallic materials — Part 11: Wrought titanium 6-aluminium 7-niobium alloyISO 5832-12, Implants for surgery — Metallic materials — Part 12: Wrought cobalt-chromium-molybdenum alloyISO 5833, Implants for surgery — Acrylic resin cementsISO 5834-1, Implants for surgery — Ultra-high-molecular-weight polyethylene — Part 1: Powder formISO 5834-2, Implants for surgery — Ultra-high-molecular-weight polyethylene — Part 2: Moulded formsISO 6474, Implants for surgery — Ceramic materials based on high purity aluminaISO 13356, Implants for surgery — Ceramic materials based on yttria-stabilized tetragonal zirconia (Y-TZP) ISO 13779-1, Implants for surgery — Hydroxyapatite — Part 1: Ceramic hydroxyapatiteISO 13779-2, Implants for surgery — Hydroxyapatite — Part 2: Coatings of hydroxyapatiteISO 13779-4, Implants for surgery — Hydroxyapatite — Part 4: Determination of coating adhesion strength。
Akzo Nobel Coatings Inc. Resicoat R4-ES HJF42R 防腐蚀

Functional Powder CoatingsProduct Datasheet20, Culvert Street T+1 855-294-8934Nashville, TN 37210F+1 615-564-4181USAResicoat ®R4-ESfor Electrostatic Spray Application on Preheated Surfaces Code: HJF42RProduct DescriptionResicoat ® R4 is a high quality thermosetting epoxy powder coating for the corrosion protection of valves and fittings, manufactured from cast iron or steel. The powder coating is available to be applied in one layer on a preheated surface by electrostatic spray application. Typical film thickness achieved is in the range of 250 – 500 µm. The resultant thermoset epoxy has a high mechanical resistance with excellent electrical insulation properties. Drinking water approvals are available to confirm the coatings suitability, as a hygienic and environmental friendly coating. The outstanding adhesion of Resicoat ® R4epoxy powders to the metal substrate provides long term protection of the coated component. It ensures a reliable conservation to the function and value of the parts for the common water and gasdistribution network. The applicator of Resicoat ®R4 benefits from a modern and environmentallyfriendly process. It is possible to overcoat Resicoat ®R4 with polyester powder and liquid coatings to achieve UV protection.Typical valueMethod Powder PropertiesBinder System Epoxy resinDensity1.45 – 1.55 g/cm³ASTM D5965Gel time at 392° F (200° C )25 – 40 sec.ASTM D4217Particle size distribution D10 = 10 – 15 µm D90 = 135 – 160 µm Malvern ISO 8130-1Storage stability 6 months at ≤ 74 °F (23 °C)Safety precautionsSee Material Safety Datasheet (MSDS)Application DataPreheating temperature object 392 – 428 °F (200 – 220 °C) object temperaturePost cure conditions objectThe coating is self curing, if the wall thickness of the steel/cast iron is greater than 8 mm. If the wall thickness of the steel/cast iron is less than 8 mm, additional curing of 3 to 8 minutes at 392 °F (200 °C) object temperature is required.1. Pre-cleaning The surface must be free of oil, grease, salt, and other impurities.2. BlastingMolding sand, rust and sharp edges must be removed with angular steel grit. The graphite from the cast iron must beremoved from the blasting material according NACE No.2/ SSPC-10/Sa 2.5. Recommended anchor profile of ≥60 µm should be stored max. 4 hours before pre-heating (dust-free and dry).3. Pre-heating This form of heating produces a uniform, defined temperature in the component. Any oxidation should be avoided.4. Coating applicationImmediately after preheating, the coating process starts without loosing any object temperature. The coating is done in the shortest possible time in a single pass with no interruptionFunctional Powder Coatings20, Culvert Street T+1 855-294-8934Nashville, TN 37210F+1 615-564-4181USATypical valueMethodCoating Process5. Coating cureCuring is achieved by the heat contained in the object. If the heating capacity of the work piece is sufficient. To confirm fully curing, MIBK is dropped for 30 sec. on the film surface with no visible change.Material PropertiesColorblueRecommended film thickness 10 – 14 mils (250 – 350 µm)Flowsmooth Gloss at 90° angle 70 – 90 units DIN 67530Cross cut test Gt 0DIN EN ISO 2409Impact resistance> 5 Joule > 2.26 Joule > 18 JouleDIN 30677-2ASTM D279420 inchpoundASTM G14 modified1/8 in (3.2 mm) steel plate Abrasion resistance < 40 mg ASTM D4060CS-17, 1000 g, 1000 cycles Dielectric strength≥ 30 kV/mm IEC 60243-1Volume resistivity (DC voltage) 1.1 x 1015ASTM D257Elongation> 5 %DIN 30671Indentation resistance 48 h, 158 °F (70 °C)24 h, 140 °F (60 °C)< 30 %< 10 %DIN 30677-2/DIN EN 14901ASTM G17Compressive strength > 100 MPa ASTM D695Shear adhesion> 35 MPa ASTM D1002Heat aging in air (90 d), water fulfilled DIN EN 14901Thermal stability under heat aging pass AS/NZS 4158:2003Weathering (Xenon test), 100 d pass ASTM D2596-99HardnessF Pencil Strain polarization pass WIS 4-52-01Cathodic disbonding 30 d, 74 °F (23 °C)≤ 10 mm DIN 30677-2, GSK Hot water immersion 90 d, 158 °F (70 °C)pass AWWA C550-05Adhesion> 20 MPa ASTM D4541Adhesion after 7 d,194 °F (90°C)water≥ 16 MPaISO 4624, GSK Tensile strength approx. 500 kg/cm³ASTM D2370Penetration< 5 %ASTM G17Functional Powder Coatings20, Culvert Street T+1 855-294-8934Nashville, TN 37210F+1 615-564-4181USATypical valueMethodMaterial PropertiesDisinfectant resistanceaccording DVGW work sheet W 291(chlorine dioxide, sodium hypochlorite)no change of surface,no chalkingafter 10 test stages à 15 h The following migration test with demineralised water showed no defects of the film. The concentration of the examined parameters in the tested water were below the limits of the epoxy guideline for ancillaries for pipes DN > 300 mm (in main trunks).Water condensation test (Cleveland test), 21 d no changeASTM D4585Salt spray resistance, 2000 h no blistering, no loss of adhesionBS 3900:F4Salt spray test, 4000 hno under-rusting on the cut DIN EN ISO 9227(steel substrate)Water absorption, 100 d, 74 °F (23 °C)pass AS/NZS 3862Chemical resistance (pH 3–13, 23° C)fulfilledEN 598Conformities ·AWWA C116·AWWA C550-05·EN 14901·ISO 12944-2, table 1(standard does not include powder coating systems)It is assumed that Resicoat ® R4 is suitable to meet the high atmospheric corrosivity category C4 (typically in industrial areas and coastal areas with moderate salinity) and the very high atmospheric- corrosivity -categories C5-I (industrial) and C5-M (marine) if applied as a holiday-free coating at a film thickness> 400 µm. A sufficient film thickness is highly required to ensure good edge coverage. For gloss and color stability a UV-resistant polyester topcoat has to be applied.Drinking Water ApprovalsUS: ANSI/NSF 61 Drinking Water System Components – Health Effects, NSF DE: UBA-Coatings Guideline, Approval no.: C-138801-06, Hygiene InstitutDE: DVGW directive work sheet W 270, Approval no. W-211795-11, Hygiene Institut UK: BS 6920, Approval No. 1112500, WRASDate of issue:July 10, 2015Authorized by:GK Revision No.:3Disclaimer: This Product Data Sheet is based on the present state of our knowledge and on current laws. The data referring to Powder Properties, Application Data and Physical Tests is based on lab based samples. Factors such as quality or condition of the substrate may have an effect on the use and application of the product. It remains the responsibility of the user to test thoroughly if the product is applicable for the intended use. The use of the product beyond our recommendation releases us from our responsibility, unless we have recommended the specific use in writing. It is always the responsibility of the user to take all necessary steps to fulfil the demands set out in the local rules and legislation. We are not liable for any application-technological advice. The Product Data Sheet shall be updated from time to time. Please ensure you have the latest version before using the product. All products and Product Data Sheets are subject to our standard terms and conditions of sale (GCS). You can receive the latest copy of GCS via internet or our post address. Brand names mentioned in this Product Data Sheet are trademarks of or are licensed to the AkzoNobel group.Resistance against chemical substances of Resicoat ®R4 at room temperature20, Culvert Street T+1 855-294-8934Nashville, TN 37210F+1 615-564-4181USA Chemical resistanceAugust 01, 2014Page 1 of 3Acetic acid 10 % 2 years no change Ammonia 10 % 2 years no change Ammonia 36 % 1.5 years no change Antifrogen L 50 % 1 year no change Antifrogen N 50 %1 year no change Benzol 1 month no change Bore oil 1 year no change Butanol6 months no change Carbon tetra chloride 1 yearno change Caustic soda solution 10 % 2 years no change Caustic soda solution50 %2 years no change Chlorine cleanser and disinfectant 1.5 years no change Citric acid2 years no change Deicer Safeway KF HOT 1 year no change Deicer Safeway SF (solid) 1 year no change Deicer Safewing MP II 1951 1 yearno change Dichromatic potassium 10 % 1 year no change Diesel2 years no change Engine oil SAE 20 1 year no change Ethanol 1 year no change Ethyleneglycole 1 yearno change Formaldehyde 37 % 6 months no change Formic acid 5 % 2 years no change Formic acid 10 %1.5 years no change Glycerol 1 year no change Glysantin 1 yearno change Hydrochloric acid concentrated1 week no change Hydrochloric acid 10 %2 years no change Hydrochloric acid 25 % 1.5 yearsno change Hydrofluoric acid 1 % 1 day no change Hydrogen peroxide 3 % 1 year no change Hydrogen peroxide10 %1 yearfadedLactic acid10 % 1 week no changeMethanol 1 week no changeMethyl tert-butyl ether (MTBE)100% 6 months softeningNitric acid10 % 1.5 years no changeNitric acid25 % 1 year no changeOxalic acid 5 % 6 months no changePalm oil at 90° C7 days no changePetrol 2 years no changePetroleum 1 year no changePhosphoric acid10 % 2 years no changePhosphoric acid50 % 2 years no changePotassium hydroxide10 % 1 year no changePotassium hydroxide25 % 1 year no changePotassium hydroxide50 % 1 year no changePropanol 1 year no changeSea water 2 years no changeSodium acetate10 % 1 year no changeSodium carbonate20 % 1 year no changeSodium hypochlorite (15 % Cl2)10 weeks no changeSodium chloride 2 % 1 year no changeSodium chloride20 % 1 year no changeSodium formiate10 % 1 year no changeSuds 1 % 1 year no changeSulphuric acid 2 % 2 years no changeSulphuric acid20 % 2 years no changeSulphuric acid50 % 2 years no changeTartaric acid 5 % 1 year no changeToluol 1 year no changeTurpentine oil 1 year no changeUrea10 % 1 year no changeUrine 1 year no changeXylol 1 year no change 20, Culvert Street T+1 855-294-8934Nashville, TN 37210F+1 615-564-4181USA Chemical resistance August 01, 2014Page 2 of 3Our printed literature and technical information Sheets as well as our advisory services are offered to facilitate andsupport decision-making processes. All specifications provided reflect the state of our knowledge at the time of print. Anytechnical data and measured values supplied have been tested for compliance with current applicable standards, ifavailable. The information provided is not legally binding upon the party supplying such information.20, Culvert Street T+1 855-294-8934Nashville, TN 37210F+1 615-564-4181USA Chemical resistance August 01, 2014Page 3 of 3。
JBL Studio 260P 12英寸有力子woofer说明书

Bass that rises to any occasionNo self-respecting 9-piece series of loudspeakers would call itself unrivaled without packing unbeat-able bass. With the SUB 260P powered subwoofer as part of our new JBL® Studio 2 Series, it’s time we called it a day and claimed victory. Alongside its dynamic cousin, the 10" SUB 250P, the SUB 260P is engineered to add faultless, deep-penetrating bass into whatever music, movie, portable device, or game console you’re listening to at any given moment.With its 12" PolyPlas low-frequency transducer, its 300-watt Class D high-efficiency built-in amplifier, and its rear-firing Slipstream bass port that provides unyielding clarity, all that’s left for you to do is kick back, relax, and enjoy the final word in acoustics. Combine this with the SUB 260P’s sleek, clean design and you’ll be the first to admit - we’ve created a powered subwoofer that defines – and commands – its era.12" PolyPlas low-frequency transducer for tight, extended bass response300-watt Class-D high-efficiency amplifier features unobtrusive rear-mounted inputs and controls for easy set-up and system integrationInternal edge-to-edge bracing reduces cabinet wall flexing, there-by significantly improving bass response and lowering distortion Solid cabinet construction with soft-rounded edges and no visible fastenersGloss black top panel adds a touch of elegance to the sleek cabinet designSoft-touch paint covers driver trim ring for a clean, timeless look Rear-firing Slipstream bass port eliminates bass turbulence and audible distortionlifier features unobtrusive rear-mountedst century visual design features that can’t fail to seduce, we’ve made st century elegance – including a solid cabinet construction with no visible What’s in the box:JBL® Studio 2 Series 12" Powered Subwoofer Owner’s ManualLFE Cable x 1Carpet Spikes x 4Product specifications:Type: Studio 2 Series 12" Powered Subwoofer 12" (300mm) PolyPlas low-frequency transducer Braced enclosure with Slipstream rear-firing bass port Frequency response: 29Hz – 150Hz300W RMS built-in amplifier600W peak dynamic powerLine-level and LFE inputsContinuously adjustable low-pass crossover frequency control (50Hz – 150Hz; 24dB/octave)Phase switch, level control, bass boost and signal-sensing auto powerDimensions (H x W x D): 445mm x 381mm x 435mm (17-1/2" x 15" x 17-1/8")Weight: 17.2 kg (38 lb)HARMAN International Industries, Incorporated 8500 Balboa Boulevard, Northridge, CA 91329 USA © 2013 HARMAN International Industries, Incorporated. All rights reserved.JBL is a trademark of HARMAN International Industries, Incorporated, registered in the United States and/or other countries. The “Hear the truth” logo is a trademark of HARMAN International Industries, Incorporated. Features, specifications and appearance are subject to change without notice.。
翻译
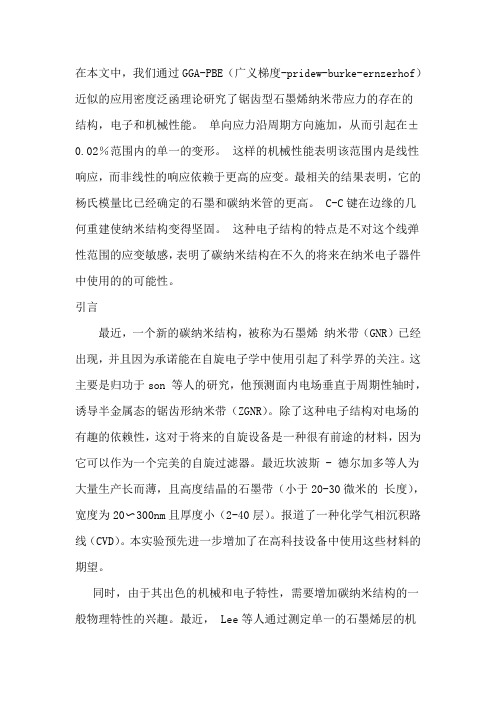
在本文中,我们通过GGA-PBE(广义梯度-pridew-burke-ernzerhof)近似的应用密度泛函理论研究了锯齿型石墨烯纳米带应力的存在的结构,电子和机械性能。
单向应力沿周期方向施加,从而引起在±0.02%范围内的单一的变形。
这样的机械性能表明该范围内是线性响应,而非线性的响应依赖于更高的应变。
最相关的结果表明,它的杨氏模量比已经确定的石墨和碳纳米管的更高。
C-C键在边缘的几何重建使纳米结构变得坚固。
这种电子结构的特点是不对这个线弹性范围的应变敏感,表明了碳纳米结构在不久的将来在纳米电子器件中使用的的可能性。
引言最近,一个新的碳纳米结构,被称为石墨烯纳米带(GNR)已经出现,并且因为承诺能在自旋电子学中使用引起了科学界的关注。
这主要是归功于son 等人的研究,他预测面内电场垂直于周期性轴时,诱导半金属态的锯齿形纳米带(ZGNR)。
除了这种电子结构对电场的有趣的依赖性,这对于将来的自旋设备是一种很有前途的材料,因为它可以作为一个完美的自旋过滤器。
最近坎波斯 - 德尔加多等人为大量生产长而薄,且高度结晶的石墨带(小于20-30微米的长度),宽度为20〜300nm且厚度小(2-40层)。
报道了一种化学气相沉积路线(CVD)。
本实验预先进一步增加了在高科技设备中使用这些材料的期望。
同时,由于其出色的机械和电子特性,需要增加碳纳米结构的一般物理特性的兴趣。
最近, Lee等人通过测定单一的石墨烯层的机械性能,表明了石墨烯是已知的最坚固的材料,因为它的弹性模量达到了1.0 TPA。
此外,更多的努力一直致力于研究石墨烯的电子特性,因为创造一个缺口就可能允许在场效应晶体管中使用石墨烯。
许多机制已经被提出来用于这一目的:纳米图案化,形成量子点,采用多层,共价功能化,掺杂如硫一样的杂原子和施加机械应力。
在最后这种情况下,线弹性理论中和紧束缚方法,佩雷拉等人发现,应变能产生大量的频谱差距。
但是这种差距是关键的,需要超过临界值20%,并且仅沿相对于所述底层优选的方向。
Bladegen和Turbogrid教程

新建选择“normal Axial”,如图选择“Ang/Thk”模式,如图修改如图参数,参数值如图所示单击“ok”后,如图所示将叶片与旋转轴角度设置为15,叶片数设置为13,Ang设置5,厚度设为3,如图所示点击“ok”,如图说一下,这四个框图表示的什么意思,如图单击“Model”,“Properties”,如图打开如图所示将“component type”改为“fan”,将“model units”改为“mm”,如图所示点击“ok”后,如图单击“blade”“properties”,如图所示打开后,如图所示,也就是打开叶片属性设置选择“LE/TE Ellipse”,如图将“TE Type”设置为“Ellipse”,如图单击“ok”,如图所示接上一篇,点击,如图所示点击后,如图所示点击这个全圆周显示,如图点击后,如图所示点击实体圆周显示,如图点击后,如图所示保存模型,注意:只能用英文或者数字名字,并保存在英文或者数字的目录下,名字及路径严禁用中文,否则会出错打开之后如图所示设置页顶间隙,双击“Geometry”“BladeSet”“Shroud Tip”如图所示出现如图所示打钩,选择“constant span”,然后“sapn”为0.95,如图单击“apply”,如图选择“Topology Set(suspended)”右键取消选择“suspended object updates”,如图去掉勾后,自动生成如图所示(此步,软件完成叶轮流道网格拓扑结构的划分同时,“Topology Set(Suspended)”变为“Topology Set”,如图所示双击“Topology set”,如图双击后,如图所示这里有两种拓扑优化方式“ATM Optimized”和“Traditional with control point”,此处选择“ATM Optimized”,如图点击“apply”,如图双击“mesh data“双击后,如图所示将方框拉大,便于查看,如图按照如图参数进行设置,如图同时勾选“inlet domain”和“outlet domain”如图单击“apply”,确定设置接上一篇《旋转机械TurboGrid网格划分教程(2/3)》,选择“3D mesh”,右键,选择“create mesh”,如图所示生成的“3d mesh”,如图所示双击“Mesh Analysis(Error)”,位置如图所示双击后,弹出“mesh statistics”对话框,如图所示在红色方框内有6个选项,其中有两个选项为红色,如图在两项红色指标中,发现“Maximum Element Volume Ratio”“Maximum Edge Length Ratio”项有少部分超过最低限定值,但由“Value”中数据可知,这项的最大值还算基本合理,同时可以双击参数,查看较差的网格情况,如图查看“Maximum Edge Length Ratio”项,如图关闭网格统计“mesh statics查看整个风机网格情况,点击,如图所示保存网格项目,准备进行CFX前处理,如图Love is not a maybe thing. You know when you love someone.。
钢纤维增强聚合物改性高强混凝土断裂韧性的试验研究
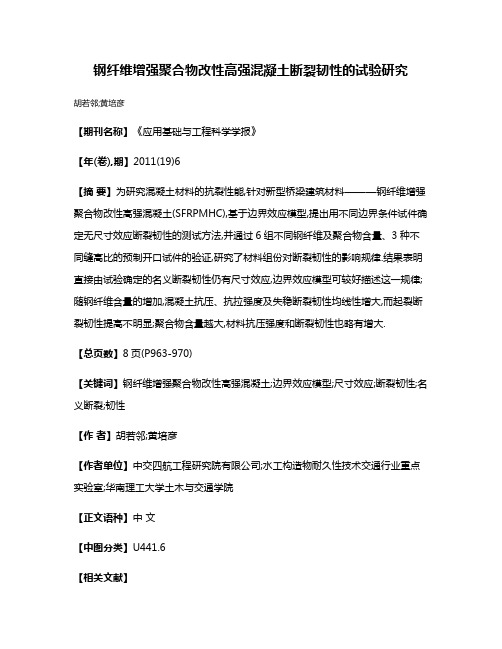
钢纤维增强聚合物改性高强混凝土断裂韧性的试验研究
胡若邻;黄培彦
【期刊名称】《应用基础与工程科学学报》
【年(卷),期】2011(19)6
【摘要】为研究混凝土材料的抗裂性能,针对新型桥梁建筑材料———钢纤维增强聚合物改性高强混凝土(SFRPMHC),基于边界效应模型,提出用不同边界条件试件确定无尺寸效应断裂韧性的测试方法,并通过6组不同钢纤维及聚合物含量、3种不同缝高比的预制开口试件的验证,研究了材料组份对断裂韧性的影响规律.结果表明直接由试验确定的名义断裂韧性仍有尺寸效应,边界效应模型可较好描述这一规律;随钢纤维含量的增加,混凝土抗压、抗拉强度及失稳断裂韧性均线性增大,而起裂断裂韧性提高不明显;聚合物含量越大,材料抗压强度和断裂韧性也略有增大.
【总页数】8页(P963-970)
【关键词】钢纤维增强聚合物改性高强混凝土;边界效应模型;尺寸效应;断裂韧性;名义断裂;韧性
【作者】胡若邻;黄培彦
【作者单位】中交四航工程研究院有限公司;水工构造物耐久性技术交通行业重点实验室;华南理工大学土木与交通学院
【正文语种】中文
【中图分类】U441.6
【相关文献】
1.钢纤维改性再生橡胶高强混凝土性能试验研究 [J], 朱江;陈传锋;朱志文;林凤兰
2.钢纤维增强聚合物改性混凝土的应用技术研究 [J], 黄灶盛;常浩
3.钢纤维增强聚合物改性混凝土力学性能的研究 [J], 刘亚东
4.钢纤维增强聚合物高强混凝土疲劳性能的试验研究 [J], 胡瀚
5.钢纤维增强高强钢筋混凝土梁柱节点抗震性能试验研究 [J], 张健新;张标;戎贤;丁传林
因版权原因,仅展示原文概要,查看原文内容请购买。
红木制作十二工艺流程

红木制作十二工艺流程英文回答:Redwood furniture is known for its exquisite craftsmanship and timeless beauty. The process of creating redwood furniture involves several intricate steps, each requiring skill and attention to detail. Let me take you through the twelve-step process of making redwood furniture.1. Design and Planning: The first step in creating redwood furniture is to come up with a design and plan.This involves considering the desired style, size, and functionality of the piece. For example, if I want to makea redwood dining table, I will sketch out the design and determine the dimensions.2. Material Selection: Once the design is finalized, I will carefully select the redwood lumber for the project. Redwood is prized for its durability and natural beauty. I will choose the best quality wood that is free from knots,cracks, or other imperfections.3. Cutting and Shaping: The selected redwood lumber is then cut and shaped according to the design. This step requires precision and expertise to ensure accurate measurements and smooth edges. I will use various toolssuch as a table saw, miter saw, and chisels to shape the wood.4. Joinery: Joinery is an important step in redwood furniture making, as it determines the strength andstability of the piece. Common joinery techniques include dovetail joints, mortise and tenon joints, and dowel joints.I will carefully select the appropriate joinery methodbased on the design and intended use of the furniture.5. Sanding: After the joinery is complete, thefurniture pieces are sanded to achieve a smooth andpolished surface. This step removes any rough edges or imperfections and prepares the wood for finishing. I will use different grits of sandpaper and sanding tools to achieve the desired smoothness.6. Assembly: Once all the individual components are sanded, they are assembled together using glue, screws, or other fasteners. This step requires careful alignment and attention to detail to ensure a sturdy and well-constructed piece of furniture.7. Finishing: The next step is to apply a finish to the redwood furniture. This can be a clear varnish, stain, or paint, depending on the desired look. The finish not only enhances the natural beauty of the wood but also provides protection against moisture, sunlight, and wear. I will apply multiple coats of finish, sanding between each coat for a smooth and flawless finish.8. Upholstery (if applicable): If the redwood furniture includes upholstery, such as cushions or fabric seats, this step involves attaching the upholstery securely to the furniture frame. This can be done using staples, screws, or upholstery nails. I will ensure that the upholstery is neatly attached and free from wrinkles or loose ends.9. Hardware Installation: If the redwood furniture includes any hardware, such as drawer pulls or hinges, this step involves installing them properly. I will carefully measure and mark the positions for the hardware and use appropriate tools to attach them securely.10. Quality Control: Before the redwood furniture is considered complete, it undergoes a thorough qualitycontrol check. I will inspect the piece for any defects, such as uneven surfaces, loose joints, or imperfections in the finish. Any issues found will be addressed and corrected.11. Packaging and Shipping: Once the redwood furniture passes the quality control check, it is carefully packaged to ensure safe transportation. This may involve wrapping the furniture in protective materials, such as bubble wrap or foam, and placing it in a sturdy box or crate. The furniture is then shipped to its destination, whether it be a retail store or directly to the customer.12. Customer Satisfaction: The final step in theredwood furniture-making process is ensuring customer satisfaction. I will follow up with the customer to ensure that they are happy with their purchase and address any concerns or issues they may have. Building strong relationships with customers is crucial for the success of my redwood furniture business.中文回答:红木制作工艺流程十分复杂,需要经过多个精细的步骤才能完成。
油井化学堵水效果评价方法及应用

技术应用/TechnologyApplication油井化学堵水效果评价方法及应用付亚荣刘泽姜春磊翟中杨杨亚娟吴泽美季保汐敬小龙唐光亮(中国石油华北油田公司)摘要:我国油田堵水调剖技术已经历60多年的发展历程,油井堵水、注水井调剖、调驱以及深部液流转向等技术经历了起源、试验、发展、成熟、更替的过程,取得了很好的增油效果。
大多学者重点关注堵水技术和方法的研究,堵水效果如何评估研究较少。
为此,将油井化学堵水波及油层分为内、外两区域,增加的原油产量在达西渗流线性系统中理论上无限叠加,以内区、外区、交界面等3个产出液流动控制方程为理论依据,基于Duhamdl 原理的反褶积算法,建立油井井口压力模型、有效渗透率模型、产油量计算模型等评价油井化学堵水效果。
在50多口油井应用后,评价符合率达到95%以上,消除了技术人员习惯直接利用堵水前后产油量的差值判断堵水效果所带来的不确定性,为油井化学堵水效果评价提供了一种新的方法。
关键词:油井;高含水;化学堵水;反褶积算法;评价符合率DOI :10.3969/j.issn.2095-1493.2024.03.001Evaluation method and application of chemical plugging effect in oil wellsFU Yarong,LIU Ze,JIANG Chunlei,ZHAI Zhongyang,YANG Yajuan,WU Zemei,JI Baoxi,JING Xiaolong,TANG Guangliang North China Oilfield Company,CNPCAbstract:China's oilfield water plugging and profile control technology has experienced more than 60years of development.The water plugging in oil wells,profile control in water injection wells,profile control and flooding,as well as deep fluid flow diversion and other technologies have gone through the process of origin,test,development,maturity and replacement,which achieved good oil increase effect.Most scholars mainly focus on the research of water plugging technology and methods,but there are few research on how to evaluate the water plugging effect.Hence,the oil well chemical water plugging wave and oil layer are divided into internal and external areas.The Darcy percolation linear system that was increased crude oil production is infinitely superposed in theory,and the three pro-duced fluid flow control equations of the inner zone,the outer zone and the interface are taken as the theoretical basis.Based on the anti-convolution algorithm of Duhamd l principle,the well head pres-sure model,effective permeability model and oil production calculation model are established to evalu-ate the effect of oil well chemical water plugging.After the application of more than 50oil wells,the coincidence rate of evaluation is more than 95%,which eliminates the uncertainty caused by technical personnel that are accustomed to directly judging the water plugging effect through using the difference in oil production before and after water plugging and provides a new method for evaluating the chemi-cal water plugging effect of oil wells.Keywords:oil well;high water content;chemical plugging;anti-convolution algorithm;coinci-dence rate of evaluation第一作者简介:付亚荣,教授级高级工程师,1987年毕业于重庆石油学校(油田应用化学专业),从事油气田开发技术研究与应用工作,引文:付亚荣,刘泽,姜春磊,等.油井化学堵水效果评价方法及应用[J].石油石化节能与计量,2024,14(3):1-5.FU Yarong,LIU Ze,JIANG Chunlei,et al.Evaluation method and application of chemical plugging effect in oil wells[J].Energy Conservation and Measurement in Petroleum &Petrochemical Industry,2024,14(3):1-5.付亚荣等:油井化学堵水效果评价方法及应用第14卷第3期(2024-03)陆相水驱开发油藏油层内部纵向非均质严重,油井出水是普通存在的问题。
- 1、下载文档前请自行甄别文档内容的完整性,平台不提供额外的编辑、内容补充、找答案等附加服务。
- 2、"仅部分预览"的文档,不可在线预览部分如存在完整性等问题,可反馈申请退款(可完整预览的文档不适用该条件!)。
- 3、如文档侵犯您的权益,请联系客服反馈,我们会尽快为您处理(人工客服工作时间:9:00-18:30)。
CIB-W18/40-7-2INTERNATIONAL COUNCIL FOR RESEARCH AND INNOVATIONIN BUILDING AND CONSTRUCTIONWORKING COMMISSION W18 - TIMBER STRUCTURESEDGE JOINTS WITH DOWEL TYPE FASTENERSIN CROSS LAMINATED TIMBERT UibelH J BlaßUniversität KarlsruheGermanyMEETING FORTYBLEDSLOVENIAEdge Joints with Dowel Type Fastenersin Cross Laminated TimberT. Uibel, H.J. BlaßLehrstuhl für Ingenieurholzbau und BaukonstruktionenUniversität Karlsruhe, Germany1 IntroductionDuring the 39th meeting of CIB-W18 the authors presented proposals for the calculation of the load carrying capacity of joints with dowel type fasteners positioned perpendicular to the plane of cross laminated timber (CLT) [4]. In continuation of the research project [1] the load carrying capacity of edge joints with dowels and screws in CLT was examined. To calculate the load carrying capacity of dowel-type fasteners according to Johansen’s yield theory [2], [3] the yield moment of the fasteners and the embedding strength are needed. The withdrawal strength is necessary to calculate the load carrying capacity of axially loaded screws. In addition, the withdrawal strength is important for estimating the rope effect of laterally loaded connections. In the narrow sides of CLT the fasteners can be positioned parallel to the grain direction. The embedment strength and the withdrawal strength are also influenced by gaps and grooves.Fig. 1: Opened connection with dowels in cross laminated timbernarrow side2Embedding strength2.1Test set-up and test materialThe embedment tests with dowels, screws and nails in CLT were carried out according to EN 383 [5]. To avoid splitting of test specimens tensile reinforcements were required in some cases. For this purpose stripes of plywood were glued onto the surface of the test specimen, as shown in Fig. 2. The stripes were placed in some distance to the fastener to exclude influences on the embedment strength and on the stress distribution within close range of the fastener.Fig. 2: Splitting failure of test specimen and tensile reinforcements to avoid splittingThe test programme includes tests with two different load directions as shown in Fig. 3 (direction A and B). In the narrow sides of CLT many positions of fasteners are possible. Fig. 4 shows five possible positions of fasteners with different diameters in relation to the thickness of the layers and in relation to the grain direction. The examined positions of fasteners in relation to gaps and grooves are displayed in Fig. 5. It was not possible to determine the relevant configuration before the tests. Thirteen different combinations of load direction and fastener positions were considered in the tests with dowels while in the tests with screws and nails seven combinations were included.For the tests CLT made of European spruce (Picea abies) from four different manufacturers with seven different build-ups were used. Table 1 gives some statistical information about the density of the test specimens.Fig. 3: Tested load directions, schematic sketch of a test specimen<<layerlayer>>layerlayerd t d t d t d t 1.) Fastener parallel to the grain 2.) Fastener perpendicular to the grain5.) Fastener between two layers3.) Fastener parallel to the grain4.) Fastener perpendicular to the grainFig. 4: Possible positions of fasteners in the narrow sides, schematic sketchG1.) Without gapsG2.) Over gapsG3.) In gapsFig. 5: Possible positions of the fasteners in relation to gaps, schematic sketch Table 1: Density of the specimens at normal climate, 20°C/65% RHDensityof the whole cross sectionDensityof the relevant layersManufacturer/ productnρmean kg/m³Coefficient of variationρ0,05 kg/m³ρmean kg/m³Coefficient of variationρ0,05 kg/m³1 184 474 5,76 % 434 481 9,54 % 412 2292 439 7,65 % 391 417 12,2 % 3453, 4 233 452 5,55 % 413 461 9,89 % 4012.2 Results for dowelsTo determine the embedding strength of cross laminated timber 390 tests with dowels were evaluated. For the tests dowels with 24, 16, 12, 8 and 6 mm in diameter were used. The test results in the different test configurations were analysed to reveal the relevant position. Fig. 6 shows the ratio f h,test /ρ over the diameter for the tested dowel positions. The test configurations are named after the combination of load direction (A, B as shown in Fig. 3) and the position of the fasteners (1 to 5 as shown in Fig. 4). The tests carried out in position A1 result in the lowest values for the embedment strength.0,000,010,020,030,040,050,060,070,080,090,100481216202428d in mmf h ,t e s t / ρ i n (N ·m ³)/(kg ·m m ²)0,000,010,020,030,040,050,060481216202428d in mmf h ,t e s t / ρ i n (N ·m ³)/(kg ·m m ²)Fig. 6: Ratio f h,test /ρ over diameter d for the different tested positions of dowelsFor dowels it was possible to develop the model for the embedment strength given in equation (1). It is based on a multiple regression analysis of 100 embedment tests carried out in the relevant test position A1. The embedment strength depends on the diameter d of the dowel and the density ρlayer of the layer or the layers in which the dowel is placed.0,91h,pred layerf 0,049(1-0,017d)ρr =0,63=⋅⋅⋅ in N/mm² (1)with ddiameter of the fastener ρlayer density of the relevant layer(s)A comparison of predicted values and test results is shown in Fig. 7. The correlation coefficient r is equal to 0,63. The diagram shows also the results for the non-relevant positions. By inserting the characteristic density of the relevant layer which complies with the density of the raw material (350 kg/m³ for C24) in equation (1) the characteristic embedment strength can be proposed as:()()0,91h,k layer,k f 0,04351-0,017d ρ9 1-0,017d =⋅⋅⋅=⋅⋅ in N/mm²(2)0510152025303540455005101520f h,pred in N/mm²f h ,t e s t i n N /m m ²56789f h,k in N/mm²Fig. 7: Comparison of test results and predicted values resp. characteristic values of theembedment strength, influence of the dowel position2.3 Results for screws and nailsAltogether 319 embedment tests with nails (d = 4,2 mm) and screws (d = 6, 8, 12 mm) in seven different combinations of load direction and fastener positions were carried out. On the basis of a regression analysis of 117 tests with screws and nails in the relevant test configuration A1 the embedment strength can be derived as:-0,460,56h,pred layer f =0,8622d ρr =0,68⋅⋅ in N/mm²(3)A comparison of predicted values and test results is shown in Fig. 8. The correlation coefficient was determined as r = 0,68. Having inserted the characteristic density of the layers (ρlayer,k = 350 kg/m³) in (3), simplified and adapted the equation the characteristic embedment strength can be proposed as:-0,50,56-0,5h,k layer,k f =0,862d ρ=20d⋅⋅⋅ in N/mm² (4)510152025303540455005101520f h,pred in N/mm²f h ,t e s t i n N /m m ²5678910f h,k in N/mm²Fig. 8: Comparison of test results and predicted or characteristic values (screws/nails) resp.3Withdrawal strength of self-tapping screws in CLT3.1Test set-up and test materialTo determine the withdrawal strength of self-tapping screws in CLT 119 tests with screws placed perpendicular to the plane of CLT and 268 tests with screws in the edges of CLT were carried out according to EN 1382 [6]. In the tests the positions of screws were varied, as shown in Fig. 9 and 10. In the plane side they were positioned in areas without gaps (position 1.1) and placed in gaps (position 1.2 to 1.4). Screws driven perpendicular (position C) and parallel (positions A, B) to the grain were considered in the edge withdrawal tests. Furthermore, tests with screws placed in gaps (positions B.1, B.2) were taken into consideration to derive the withdrawal capacity. Table 3 shows the statistical summary of the specimen density.Anordnung: 1.1 1.2 1.3 1.4 Fig. 9: Set-up for withdrawal tests with screws positioned perp. to the plane of CLTAnordnung:A B1B2CFig. 10: Set-up for edge withdrawal tests with screws in CLTTable 2: Density of the specimens at normal climate, 20°C/65% RHDensity of the specimen for withdrawal testsPlane side (hole cross section) Narrow side (relevant layers) Manufacturer/productnρmeankg/m³Coefficientof variationρ0,05kg/m³nρmeankg/m³Coefficientof variationρ0,05kg/m³1 24 454 4,48 % 423 57 448 8,21 % 3742 73 426 5,44 % 384 159 404 11,9 % 3353, 4 22 445 3,34 % 420 52 435 8,29 % 382 Position 1.1 1.2 1.3 1.4 Position A B.1 B.2 C3.2 Test resultsThe best correlation between test results and predicted values can be achieved if the withdrawal capacity of self-tapping screws in CLT is calculated according to the following expression:0,80,90,75ef ax,s,pred 0,44d ρR =1,25cos +sin r =0,91⋅⋅⋅⋅εεA in N(5)with d nominal or outer diameter of the screw in mm A efeffective pointside penetration length in mmε angle between screw axis and grain direction ρ for joints in the plane side of CLT: density of CLT (whole cross section) in kg/m³ for edge joints in CLT: density of the relevant layer(s) in kg/m³Fig. 11 (left) shows the test results vs. the predicted values. The correlation coefficient r is equal to 0,91. To simplify equation (5) the characteristic density of CLT is inserted and the denominator is increased up to 1,5. A further adaptation results in equation (6) for the characteristic withdrawal capacity. The right diagram in Fig. 11 shows the verification of the characteristic values.0,80,90,750,80,9ef ef ax,s,k22220,35d ρ31d R =1,5cos +sin 1,5cos +sin ⋅⋅⋅⋅⋅=⋅εε⋅εεA A in N (6)withε joints in the plane side of CLT: ε = 90°, edge joints: ε = 0° ρ characteristic density of CLT (400 kg/m³)The given equations are only valid for self-tapping screws, for which the characteristicwithdrawal strength in solid wood (C24) exceeds f ax,k = 80·k ρ2·10-6= 9,8 N/mm².0510152025510152025R ax,s,pred in kNR a x ,s ,t e s t i n k N051015202551015Rax,s,kin kNR a x ,s ,t e s t i n kNFig. 11: Withdrawal strength - test results over predicted or characteristic values resp.4Load carrying capacity of edge joints4.1Short-term testsIn order to confirm the calculation of the load carrying capacities of edge joints in CLT 49 tests with dowels and screws were carried out. The tests also provide a basis for determining the required spacing, edge and end distances for the fasteners, which are defined in Fig. 14. Table 3 shows the specimen parameters while table 4 shows the results of the tests. Connections with fasteners placed parallel to the grain (configuration B) and perpendicular to the grain (configuration A) were considered in the tests. Furthermore, joints with fasteners placed between two layers of different grain direction were tested in configuration C. Comparisons between test results and calculated load carrying capacities are given in Fig. 12 and Fig. 13.20406080100120140020406080100120140R pred in kNF t e s t i n k NF t e s t i n k N01020304050607080900102030405060708090R pred in kN F t e s t i n k N01020304050607080900102030405060708090R pred in kN F t e s t i n k NFig. 13: Test results for edge joints with screws vs. predicted load carrying capacitiesTable 3: Specimen parametersFastenersBuild-up of CLTSpecimenn test Conf.Typed mmM y Nm t 1mm t 2mm a 3,tmm a 1mm a 4,c mmsmnSide and middle members2-24-22_B1 1 B dowels 24 1224 96 1605⋅d 4⋅d 64 2 1 5 34-13-34-13-34 2-24-22_B1.F1 1 B dowels 24 122496 1605⋅d 4⋅d 64 2 1 4 34-13-34-13-34 2-24-22_C1 3 C dowels 24 1224 96 1605⋅d 4⋅d 89 2 1 3 34-22-34-22-34-22-34 (reduced to 178 mm) 2-24-22_B2 3 B dowels 24 1224 96 1605⋅d 4⋅d 1012 1 334-22-34-22-34-22-342-16-22_B1 3 B dowels 16 400 80 1605⋅d 4⋅d 30 2 1 3 19-22-19 2-16-22_A2 3 A dowels 16 400 80 1605⋅d 5⋅d 64 2 1 3 34-13-34-13-34 2-16-22_B2 4 B dowels 16400 80 1605⋅d 5⋅d64 2 1 3 34-13-34-13-34 2-12-22_A1.1 3 A screws 12 63,71)/100,82)12012012⋅d 10⋅d 64 1 1 2 34-13-34-13-34 2-12-22_B1.1 4 B screws 12 63,71)/100,82)60 12012⋅d4⋅d30 2 1 219-22-19 2-12-22_A1.2 2 A/B screws 12 63,71)/100,82)12012012⋅d 10⋅d 36,5 1 3 2 34-22-34-22-34 2-12-22_B1.2 2 B/A screws 12 63,71)/100,82)12012012⋅d 10⋅d 36,5 1 3 234-22-34-22-34 2-12-22_A2 3 A screws 12 63,71)/100,82)60 1207⋅d 4⋅d 64 2 1 2 34-13-34-13-34 2-12-22_B2 6 B screws 12 63,71)/100,82)60 1207⋅d 4⋅d 30 2 1 4 19-22-19 2-12-22_C2 3 C screws 12 63,71)/100,82)60 1207⋅d 4⋅d48 2 1 4 34-13-34-13-34 (reduced to 96 mm) 2-12-22_B3 2 B screws 12 63,71)/100,82)12012010⋅d 5⋅d 30 1 1 4 19-22-19 2-8-42_A1 3 A screws 8 24,1 12080 10⋅d7⋅d21 1 1 2 8,5-7,5-10-7,5-8,5 2-8-42_B1 3 B screws 8 24,1 80 1207⋅d 5⋅d21 1 1 28,5-7,5-10-7,5-8,5s: 1)Number of shear planes per fastener Yield moment of the thread of the screwm: 2)Number of fastener rowsYield moment of the shank of the screw n:Number of fasteners per rowTable 4: Results of the testsMean density ρlayer,m in kg/m³ SpecimenNumber of specimens n Side members Middle members Load carrying capacity per fastener and shear planeF u,mean in kNTypeof failure2-24-22_B1 1 408 410 9,35 1 x fa 2-24-22_B1.F1 1 405 355 11,1 1 x fa 2-24-22_C1 3 441 416 21,2 1 x fa, 2 x sp 2-24-22_B2 3 456 449 16,9 2 x d, 1 x sp+d2-16-22_B1 3 451 482 7,85 3 x sp 2-16-22_A2 3 438 391 13,9 2 x sp, 1 x t 2-16-22_B2 4 397 433 7,52 4 x d 2-12-22_A1.1 3 400 399 8,28 3 x d 2-12-22_B1.1 4 464 442 4,88 4 x d 2-12-22_A1.2 2 431 392 6,47 2 x d 2-12-22_B1.2 2 436 446 6,50 2 x d 2-12-22_A234303884,643 x sp2-12-22_B2 6 449 428 3,93 2 x sp, 2 x d 2 x sp+d2-12-22_C2 3 428 428 3,68 2 x sp, 1 x d 2-12-22_B3 2 439 439 5,65 2 x d 2-8-42_A1 3 474 492 8,15 3 x sp 2-8-42_B134775184,063 x spfa: failure at the force application point sp: splitting of the layers d: displacement v >15 mm t: tensile failureFor most of the test series with fasteners placed parallel to the grain (configuration B) the calculated loads and the test results correspond. In the other configurations the load carrying capacity is underestimated. The reason for this discrepancy is the conservatively assumed embedment strength, which also has to cover fasteners positioned parallel to the grain. Besides, differences between the calculated load carrying capacity and the test results are determined for connections with small spacings and end distances. In these tests splitting occurred. To avoid this failure the requirements given in Fig. 14 and Table 5 have to be fulfilled. For the design of multiple fastener joints it is suggested to consider the effective number of fasteners.a4,c a4,c a3,c a3,t F a1 a3,c F a3,t a4,c a4,cType of fastener Self-tapping screws a1 a2 a3,t a3,c 10 · d 3·d 12 · d 7·d 5·d Dowels 4·d 4·d 5·d 3·d 3·dti tCLTti tCLTa4,cFig. 14: Spacings, end distances and edge distances of fasteners in CLT Table 5: Requirements for the geometry of edge joints in CLT with dowel type fastenersType of fastener Self-tapping screws Dowels Minimum thickness of the relevant layer t i in mm d > 8 mm: 3 · d d ≤ 8 mm: 2 · d d Minimum thickness of CLT t CLT in mm 10 · d 6·d Minimum thickness/ minimum embedded length t1,req , t2,req in mm 10 · d 5·d4.2Long-term testsTo examine the influence of load duration and climate variation on the load carrying capacity of edge joints with screws in CLT long-term tests were set up. The test programme contains 48 tests with axially loaded self-tapping screws driven into the middle layer of the test specimens parallel to the grain. The long-term behaviour of laterally loaded edge joints with self-tapping screws is also examined. To this purpose, tests with single and double shear CLT-to-CLT-connections are included in the test programme. The test set-up is documented in Fig. 15. The environmental conditions comply with Service Class 2. The design resistance of the test specimens was determined from the characteristic values with the modification factor kmod = 0,8 and the partial factor γM = 1,3. The laterally loaded screws were loaded with the full design resistance while the axially loaded screws were loaded with 70 % of the design resistance. During the test duration the displacements 10are measured periodically and the climate is recorded. After three years the specimens will be unloaded and the remaining load carrying capacity will be determined in short-term tests.Fig. 15: Long term tests with screwed edge joints in CLT under lateral load and axial load5ConclusionsFor calculating the load carrying capacity of edge joints in CLT the parameters embedment strength and withdrawal capacity were examined. On the basis of statistical analysis of a multitude of test results it was possible to develop functions for predicted values of these parameters. Proposals for characteristic values are also given. The validity of the presented equations is limited to CLT with a characteristic density of 400 kg/m³ made of spruce. In tests with connections the required minimum edge and end distances and spacings of fasteners were determined. In addition the tests verify the calculation of the load carrying capacities. To determine the long-term behaviour of edge joints with self-tapping screws in CLT tests are performed.6[1]ReferencesBlaß, H. J.; Uibel, T.: Tragfähigkeit von stiftförmigen Verbindungsmitteln in Brettsperrholz, Karlsruher Berichte zum Ingenieurholzbau, Band 8, Lehrstuhl für Ingenieurholzbau und Baukonstruktionen (Ed.), Universität Karlsruhe (TH), 2007 Hilson, B. O. : Verbindungen mit stiftförmigen Verbindungsmitteln – Theorie. In: Blaß, H. J.; Görlacher, R.; Steck, G. (Ed.): Holzbauwerke STEP1 – Bemessung und Baustoffe, Fachverlag Holz, Düsseldorf, 1995 Johansen, K. W.: Theory of timber connections. International Association of bridge and structural Engineering, Bern, 1949, p. 249-262 Uibel, T.; Blaß, H. J.: Load carrying capacity of joints with dowel type fasteners in solid wood panels. In: Proceedings. CIB-W18 Meeting, Florence, Italy 2006, Paper 39-7-5 EN 383: 1993 - Timber structures; Test methods; Determination of embedding strength and foundation values for dowel type fasteners EN 1382: 1999 - Timber structures - Test methods - Withdrawal capacity of timber fasteners 11[2][3] [4][5] [6]。