压力铸造工艺介绍
压力铸造工艺流程

压力铸造工艺流程压力铸造是一种常见的金属件生产工艺,通过在高压下将熔融金属注入模具中,使其在模具中凝固成型。
这种工艺可以生产复杂形状的零件,并且具有较高的生产效率和良好的表面质量。
下面将详细介绍压力铸造的工艺流程。
1. 模具设计与制造首先,需要进行零件的模具设计与制造。
模具设计需要根据零件的形状和尺寸来确定模具的结构和尺寸,同时考虑到金属的液态流动特性和凝固收缩规律。
模具制造一般采用铝合金或钢材料,需要具有一定的强度和耐磨性。
2. 熔炼金属在进行压力铸造之前,需要先将金属材料进行熔炼。
常见的压力铸造金属包括铝合金、锌合金、镁合金等。
熔炼金属需要控制好熔炼温度和熔炼时间,以保证金属的纯净度和流动性。
3. 模具预热在进行压力铸造之前,需要对模具进行预热。
模具预热的目的是为了提高金属的流动性和凝固速度,同时减少金属与模具之间的热应力,防止模具变形或损坏。
4. 注射当模具预热完成后,将熔融金属通过注射系统注入模具中。
注射系统一般由注射机、注射活塞和喷嘴组成,通过控制注射压力和速度来实现金属的注入。
5. 压力保持在金属注入模具后,需要保持一定的压力以确保金属充填模具内部的每一个角落。
这一步需要根据金属的凝固特性和模具的结构来确定压力的大小和保持时间。
6. 凝固与冷却当金属充填模具后,开始凝固和冷却过程。
凝固和冷却的速度需要根据金属的类型和零件的厚度来确定,以保证零件的内部组织和表面质量。
7. 模具开启当零件凝固和冷却完成后,模具打开,取出成型的零件。
在取出零件之前,需要等待一定的时间以确保零件完全凝固。
8. 修整与处理取出零件后,需要进行修整和处理。
修整包括去除浇口、余料和表面氧化层,同时可以进行热处理或表面处理以提高零件的性能和表面质量。
以上就是压力铸造的工艺流程,通过这一流程可以生产出复杂形状的金属零件,并且具有较高的生产效率和良好的表面质量。
压力铸造在汽车、航空航天、电子等领域有着广泛的应用,是一种重要的金属件生产工艺。
压力铸造分类

压力铸造分类压力铸造是一种常见的铸造工艺,根据不同的压力源,可以将其分为普通压铸和低压铸造。
下面将对两种压力铸造进行详细介绍。
普通压铸是一种铸造工艺,它利用高压将熔化的金属通过模具中的喷口注入模腔中,然后在模具中冷却凝固。
这种工艺适用于生产中小型铸件,如汽车发动机罩、传动箱等。
普通压铸的优点是生产效率高,能够快速生产大量的铸件,且铸件质量高,表面光滑,尺寸精度高,线条流畅,不易变形。
缺点是模具成本高,需要定期维护和更换。
低压铸造是一种新兴的铸造工艺,它的原理是将金属熔化后注入模具中,在注入金属的同时,通过低压将金属推入模腔中,然后在模具中冷却凝固。
这种工艺适用于生产大型铸件,如风电叶片、船舶舵轮等。
低压铸造的优点是可生产大型铸件,且铸件质量高,表面光滑,尺寸精度高,线条流畅,不易变形。
缺点是生产效率较低,成本较高。
除了普通压铸和低压铸造外,还有其他的压力铸造工艺,如高压铸造和挤压铸造。
高压铸造是一种利用高压将金属熔化后注入模具中的铸造工艺。
它适用于生产高强度、高精度的铸件,如航空发动机叶轮、火箭发动机涡轮等。
高压铸造的优点是能够生产高强度、高精度的铸件,缺点是成本高、生产效率低。
挤压铸造是一种利用挤压力将金属压入模腔中的铸造工艺,它适用于生产大尺寸、复杂形状的铸件。
挤压铸造的优点是能够生产大尺寸、复杂形状的铸件,缺点是模具成本高。
总的来说,压力铸造是一种高效、高质量的铸造工艺,适用于生产各种尺寸、形状的金属铸件。
不同的压力源对应不同的压力铸造工艺,每种工艺都有其适用范围和优缺点。
在选择铸造工艺时,需要根据铸件的尺寸、形状和材料等因素综合考虑,选择最适合的铸造工艺。
压铸工艺详解
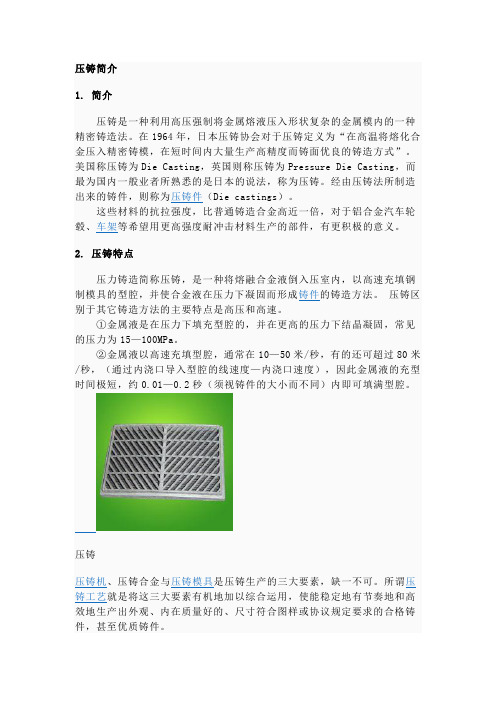
压铸简介1. 简介压铸是一种利用高压强制将金属熔液压入形状复杂的金属模内的一种精密铸造法。
在1964年,日本压铸协会对于压铸定义为“在高温将熔化合金压入精密铸模,在短时间内大量生产高精度而铸面优良的铸造方式”。
美国称压铸为Die Casting,英国则称压铸为Pressure Die Casting,而最为国内一般业者所熟悉的是日本的说法,称为压铸。
经由压铸法所制造出来的铸件,则称为压铸件(Die castings)。
这些材料的抗拉强度,比普通铸造合金高近一倍,对于铝合金汽车轮毂、车架等希望用更高强度耐冲击材料生产的部件,有更积极的意义。
2. 压铸特点压力铸造简称压铸,是一种将熔融合金液倒入压室内,以高速充填钢制模具的型腔,并使合金液在压力下凝固而形成铸件的铸造方法。
压铸区别于其它铸造方法的主要特点是高压和高速。
①金属液是在压力下填充型腔的,并在更高的压力下结晶凝固,常见的压力为15—100MPa。
②金属液以高速充填型腔,通常在10—50米/秒,有的还可超过80米/秒,(通过内浇口导入型腔的线速度—内浇口速度),因此金属液的充型时间极短,约0.01—0.2秒(须视铸件的大小而不同)内即可填满型腔。
压铸压铸机、压铸合金与压铸模具是压铸生产的三大要素,缺一不可。
所谓压铸工艺就是将这三大要素有机地加以综合运用,使能稳定地有节奏地和高效地生产出外观、内在质量好的、尺寸符合图样或协议规定要求的合格铸件,甚至优质铸件。
压铸是一种精密的铸造方法,经由压铸而铸成的压铸件之尺寸公差甚小,表面精度甚高,在大多数的情况下,压铸件不需再车削加工即可装配应用,有螺纹的零件亦可直接铸出。
从一般的照相机件、打字机件、电子计算器件及装饰品等小零件,以及汽车、机车、飞机等交通工具的复杂零件大多是利用压铸法制造的。
压铸法也有下列缺点:· (1)压铸合金受限制目前的压铸合金只有锌、锡、铅、铜、镁、铝等六种,其中以铜合金的熔点最高、铝合金压铸应用广泛。
压铸工艺
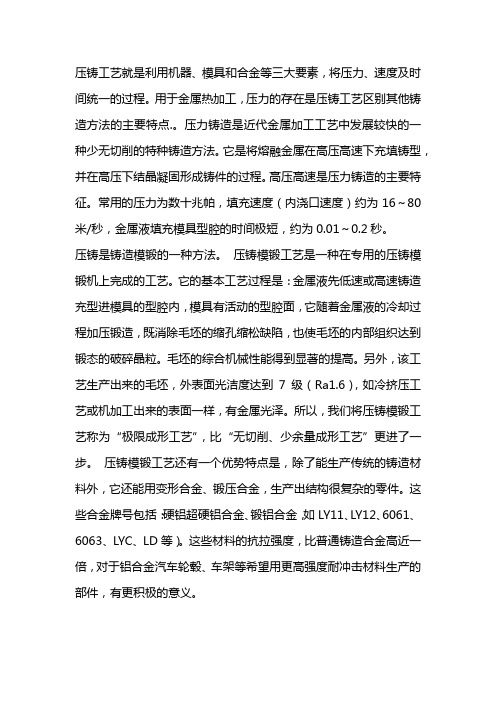
压铸工艺就是利用机器、模具和合金等三大要素,将压力、速度及时间统一的过程。
用于金属热加工,压力的存在是压铸工艺区别其他铸造方法的主要特点.。
压力铸造是近代金属加工工艺中发展较快的一种少无切削的特种铸造方法。
它是将熔融金属在高压高速下充填铸型,并在高压下结晶凝固形成铸件的过程。
高压高速是压力铸造的主要特征。
常用的压力为数十兆帕,填充速度(内浇口速度)约为16~80米/秒,金属液填充模具型腔的时间极短,约为0.01~0.2秒。
压铸是铸造模锻的一种方法。
压铸模锻工艺是一种在专用的压铸模锻机上完成的工艺。
它的基本工艺过程是:金属液先低速或高速铸造充型进模具的型腔内,模具有活动的型腔面,它随着金属液的冷却过程加压锻造,既消除毛坯的缩孔缩松缺陷,也使毛坯的内部组织达到锻态的破碎晶粒。
毛坯的综合机械性能得到显著的提高。
另外,该工艺生产出来的毛坯,外表面光洁度达到7级(Ra1.6),如冷挤压工艺或机加工出来的表面一样,有金属光泽。
所以,我们将压铸模锻工艺称为“极限成形工艺”,比“无切削、少余量成形工艺”更进了一步。
压铸模锻工艺还有一个优势特点是,除了能生产传统的铸造材料外,它还能用变形合金、锻压合金,生产出结构很复杂的零件。
这些合金牌号包括:硬铝超硬铝合金、锻铝合金,如LY11、LY12、6061、6063、LYC、LD等)。
这些材料的抗拉强度,比普通铸造合金高近一倍,对于铝合金汽车轮毂、车架等希望用更高强度耐冲击材料生产的部件,有更积极的意义。
压铸工艺详细介绍
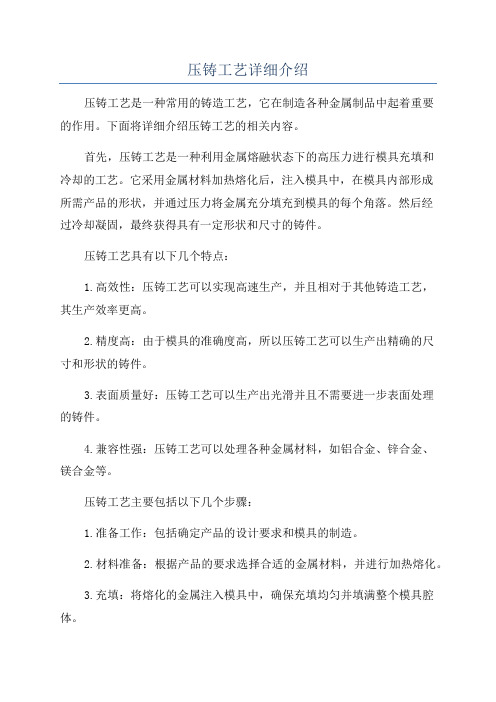
压铸工艺详细介绍压铸工艺是一种常用的铸造工艺,它在制造各种金属制品中起着重要的作用。
下面将详细介绍压铸工艺的相关内容。
首先,压铸工艺是一种利用金属熔融状态下的高压力进行模具充填和冷却的工艺。
它采用金属材料加热熔化后,注入模具中,在模具内部形成所需产品的形状,并通过压力将金属充分填充到模具的每个角落。
然后经过冷却凝固,最终获得具有一定形状和尺寸的铸件。
压铸工艺具有以下几个特点:1.高效性:压铸工艺可以实现高速生产,并且相对于其他铸造工艺,其生产效率更高。
2.精度高:由于模具的准确度高,所以压铸工艺可以生产出精确的尺寸和形状的铸件。
3.表面质量好:压铸工艺可以生产出光滑并且不需要进一步表面处理的铸件。
4.兼容性强:压铸工艺可以处理各种金属材料,如铝合金、锌合金、镁合金等。
压铸工艺主要包括以下几个步骤:1.准备工作:包括确定产品的设计要求和模具的制造。
2.材料准备:根据产品的要求选择合适的金属材料,并进行加热熔化。
3.充填:将熔化的金属注入模具中,确保充填均匀并填满整个模具腔体。
4.冷却:待金属充填完成后,模具会进行冷却以凝固金属,并保持所需形状。
5.脱模:冷却后,打开模具并取出铸件。
6.修整:对铸件进行必要的修整和整形,以满足产品的要求。
7.表面处理:根据产品的要求进行表面处理,如喷漆、电镀等。
8.检验和包装:对铸件进行质量检验,并进行包装。
在压铸工艺中,模具是一个关键的部分。
模具的制造需要对产品的设计要求有一定的了解,并采用精密的制造工艺,以保证模具的精确度和耐用性。
压铸工艺在各个领域都有广泛的应用,特别是在汽车行业、家电行业和机械制造行业中更为常见。
通过压铸工艺,可以生产出各种复杂形状的铸件,并且可以实现大规模、高效率的生产。
总之,压铸工艺是一种非常重要的铸造工艺,它具有高效性、精度高、表面质量好等特点,并在各个领域都有广泛应用。
压铸工艺的成功实施需要准备工作、材料准备、充填、冷却、脱模、修整、表面处理、检验和包装等多个步骤的协调配合。
压力铸造工艺流程
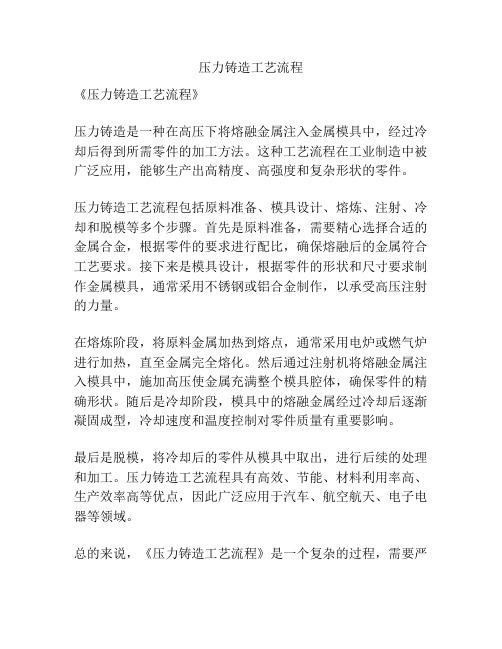
压力铸造工艺流程
《压力铸造工艺流程》
压力铸造是一种在高压下将熔融金属注入金属模具中,经过冷却后得到所需零件的加工方法。
这种工艺流程在工业制造中被广泛应用,能够生产出高精度、高强度和复杂形状的零件。
压力铸造工艺流程包括原料准备、模具设计、熔炼、注射、冷却和脱模等多个步骤。
首先是原料准备,需要精心选择合适的金属合金,根据零件的要求进行配比,确保熔融后的金属符合工艺要求。
接下来是模具设计,根据零件的形状和尺寸要求制作金属模具,通常采用不锈钢或铝合金制作,以承受高压注射的力量。
在熔炼阶段,将原料金属加热到熔点,通常采用电炉或燃气炉进行加热,直至金属完全熔化。
然后通过注射机将熔融金属注入模具中,施加高压使金属充满整个模具腔体,确保零件的精确形状。
随后是冷却阶段,模具中的熔融金属经过冷却后逐渐凝固成型,冷却速度和温度控制对零件质量有重要影响。
最后是脱模,将冷却后的零件从模具中取出,进行后续的处理和加工。
压力铸造工艺流程具有高效、节能、材料利用率高、生产效率高等优点,因此广泛应用于汽车、航空航天、电子电器等领域。
总的来说,《压力铸造工艺流程》是一个复杂的过程,需要严
格控制各个环节,确保零件质量和生产效率。
随着工艺技术的不断进步,压力铸造将会在制造业中发挥越来越重要的作用。
压力铸造及工艺特点
压力铸造及工艺特点同学们,今天咱们来了解一下压力铸造以及它的工艺特点。
这可是个很有趣的知识呢!先来说说什么是压力铸造。
想象一下,有一个大大的机器,就像一个大力士,用力地把融化的金属液体压进一个模具里,然后等金属冷却凝固,就变成了我们想要的形状,这就是压力铸造啦。
那压力铸造有什么工艺特点呢?它的生产效率超级高。
这个大力士工作起来速度可快了,一下子就能做出好多零件。
比如说,要是制造一些小型的铝合金零件,用压力铸造的方法,短时间内就能做出一大堆,这可比其他方法快多啦。
压力铸造出来的铸件尺寸精度特别高。
这就意味着做出来的东西大小、形状都非常准确,误差很小很小。
就好像我们用尺子画直线,能画得笔直笔直的。
所以很多对精度要求高的零件,都喜欢用压力铸造来做。
还有哦,压力铸造的表面质量也很棒。
做出来的铸件表面光滑平整,就像镜子一样。
比如说,一些汽车的零部件,用压力铸造做出来,表面又好看又光滑,质量杠杠的。
但是呢,压力铸造也有一些小缺点。
因为压力很大,模具很容易磨损,所以模具的成本就比较高啦。
而且,不是所有的金属都适合用压力铸造的方法,只有那些能在压力下快速凝固的金属才行。
压力铸造的时候,因为金属液是在高压下快速填充模具的,所以铸件内部容易产生气孔。
这就像我们吹气球,如果吹得太快太猛,气球里可能就会有一些小气泡。
在很多领域都发挥着重要的作用。
比如说,在航空航天领域,那些精密的零件很多都是通过压力铸造做出来的;在电子行业,像手机的外壳、电脑的配件,也经常用到压力铸造。
同学们,现在你们对压力铸造和它的工艺特点是不是有了更清楚的了解啦?希望大家以后在生活中看到相关的产品,能想到今天学到的知识哦!。
压力铸造工艺介绍
压力铸造工艺介绍压力铸造是一种将熔融金属通过压力注入模具中形成所需零件的工艺。
它通常用于生产具有复杂几何形状的零部件,比如汽车发动机缸体、航空航天部件和电子设备外壳等。
本文将介绍压力铸造的工艺流程、设备和应用。
压力铸造的工艺流程包括准备工作、注射、凝固和取模四个主要步骤。
首先,需要准备好模具,并在其内表面涂上涂料或涂腻子,以防止金属液渗透。
然后,将金属锭放入熔炉中进行熔化。
一旦金属达到所需温度,就可以开始注射。
注射是指将熔融金属通过高压注射机注入预先准备好的模具中。
在注射期间,金属会快速充满整个模腔,并且根据模具的形状形成所需零件。
完成注射后,金属将开始凝固。
在凝固过程中,金属会从熔融态变为固态,并逐渐获得足够的强度。
最后,完成凝固后,可以取出铸件,并进行进一步的处理和加工。
为了实现高质量的压力铸造,必须使用特定的设备。
注射机是压力铸造的核心设备。
它通常由注射缸、注射橡胶、压力缸和压力橡胶组成。
注射缸和压力缸之间通过活塞连接,活塞由液压系统提供动力。
注射缸的功能是将金属注射到模具中,而压力缸则用于施加额外的压力,以确保金属充实整个模具。
此外,还需要一些辅助设备,如熔炉、模具加热系统和模具翻转装置等。
压力铸造具有许多优点,使其成为制造业中广泛应用的一种工艺。
首先,由于金属在高压下被迫充实整个模具,因此可以得到高密度、无缺陷的铸件。
其次,压力铸造可以生产具有复杂几何形状的零件,这是其他铸造工艺无法达到的。
此外,压力铸造具有较高的生产效率和较短的周期时间,适用于大规模生产。
最后,压力铸造能够使用各种金属材料,如铝合金、镁合金、铜合金和锌合金等。
在汽车制造、航空航天和电子行业,压力铸造被广泛应用于生产各种零件。
在汽车制造领域,凭借其高度精密的加工能力,压力铸造可以生产出轻型、高强度的发动机缸体、曲轴壳体和转向器等零件。
在航空航天领域,压力铸造可以制造出复杂的涡轮叶片、喷气发动机零件和飞机外壳等关键部件。
压铸及精密铸造介绍
压铸及精密铸造介绍压铸及精密铸造介绍1.铸造种类很多,按造型方法习惯上分为:①普通砂型铸造,包括湿砂型、干砂型和化学硬化砂型3类。
②特种铸造,按造型材料又可分为以天然矿产砂石为主要造型材料的特种铸造(如熔模铸造、泥型铸造、铸造车间壳型铸造、负压铸造、实型铸造、陶瓷型铸造等)和以金属为主要铸型材料的特种铸造(如金属型铸造、压力铸造、连续铸造、低压铸造、离心铸造等)两类。
通过以上,可以看出,精密铸造是特殊铸造的一类.压铸:压力铸造的简称,是一种将熔融合金液倒入压室内,以高速充填钢制模具的型腔,并使合金液在压力下凝固而形成铸件的铸造方法。
压铸区别于其它铸造方法的主要特点是高压和高速。
精铸:精密铸造,属特种铸造。
用此方法获得的零件一般不需再进行机加工。
如熔模铸造、压力铸造等。
精密铸造是相对于传统的铸造工艺而言的一种铸造方法。
它能获得相对准确地形状和较高的铸造精度。
较普遍的做法是:首先根据产品要求设计制作(可留余量非常小或者不留余量)的模具,用浇铸的方法铸蜡,获得原始的蜡模;在蜡模上重复涂料与撒砂工序,硬化型壳及干燥;再将内部的蜡模溶化掉,是为脱蜡,获得型腔;焙烧型壳以获得足够的强度;浇注所需要的金属材料;脱壳后清沙,从而获得高精度的成品。
根据产品需要或进行热处理与冷加工。
蜡铸:即失蜡浇铸方法,最早出现于春秋时期,整个制造过程均为手工操作。
它的工艺过程是:将蜡制成所要制作的型器样式,后将耐高温细泥浆淋至蜡型表面,并撒细纱在泥浆表层,反复多次,使之形成完整的型壳,干燥后加温使蜡质熔出,形成型腔,用以浇铸铜液(即:紫铜加铅、锌、锡等金属元素的溶液)。
完成浇铸后,经去壳、打磨、做旧,一件精美绝伦的仿古青铜器就展现在您的面前。
失蜡法精密铸造现称熔模精密精密铸造,是一种少切削或无切削的精密铸造工艺,是精密铸造行业中的一项优异的工艺技术,其应用非常广泛。
它不仅适用于各种类型、各种合金的精密铸造,而且生产出的铸件尺寸精度、表面质量比其它精密铸造方法要高,甚至其它精密铸造方法难于铸得的复杂、耐高温、不易于加工的铸件,均可采用熔模精密精密铸造铸得。
压力铸造
2.3 压铸应用范围和注意点 ① 压铸是实现少无切削加工的精密铸造技术,在汽车、 航空、仪表、 国防等工业部门广泛用于非铁金属的小型、 薄壁、形状复杂件的大批量生产。 ② 铸件壁厚均匀,以3-4mm的壁厚为宜,最大壁厚应小 于8mm,以防止缩孔、缩松等缺陷。 ③ 铸件不宜进行热处理或在高温下工作,以免铸件内气 孔中的气体膨胀而导致铸件变形或断裂。 ④ 由于内部疏松,铸件塑性和韧性差,故它不适合于制 造受冲击的零件。 ⑤ 铸件应尽量避免机械加工,以防内部孔洞外漏。
(2)外观质量不理想。国产压铸件往往线条不清晰,水 流纹不理想,表面粗糙度差。与进口压铸件对比,差距明显。 (3)模具可靠性较差。传统的压铸模设计方法设计的模 具可靠性较差,一般需经反复调试才能正式投入使用。 (4)生产率低。由于国产模具使用可靠性不稳定,生产 中故障多,返修量大,班产量不如进口模具高。 (5)国产压铸机大都存在漏油的现象,主要原因是密封 件质量差和加工质量问题。 (6)我国在压铸模的设计和制造方面,进展较为缓慢。 在压铸模设计中,目前仍主要依靠设计人员的经验。
第Ⅳ阶织致密;这时压射冲头只做小 位移移动
图3-2 压铸不同阶段压射冲头的压力与运动速度的变化
卧式冷室压铸广泛用于铝合金的压铸。其压铸过程示意图如图3-3。
图3-3 卧室压铸机压铸过程示意图 1— 浇道;2—型腔;3—金属液浇入口;4—金属液;5—压射冲 头;6—动模;7—定模;8—顶杆;9—铸件及涂料
图3-4立式压铸机压铸过程示意图 1-压射冲头;2-压室;3-金属液;4-定模;5-动模;6-喷嘴;7-型腔; 8-返料冲头;9-余料
3.2.1 立式压铸优点: ①有余料切断、顶出功能; ②空气不易随金属进入压室; ③金属液进入型腔经过转折,压力消耗大。 3.3热室压铸 热室压铸的工作过程如图3-5所示。当压射冲头3上升 时,金属液1通过进口5进入压室4,随着压射冲头下压,液 体金属沿着通道6经喷嘴7填充铸型8;冷却后压射冲头回 升,多余的液体金属回流至压室中,然后打开铸型取出铸 件。
- 1、下载文档前请自行甄别文档内容的完整性,平台不提供额外的编辑、内容补充、找答案等附加服务。
- 2、"仅部分预览"的文档,不可在线预览部分如存在完整性等问题,可反馈申请退款(可完整预览的文档不适用该条件!)。
- 3、如文档侵犯您的权益,请联系客服反馈,我们会尽快为您处理(人工客服工作时间:9:00-18:30)。
卧式压铸机
热压室压铸机
3.压铸工艺三大要素 3.2.1 卧式压铸机工作原理
3.压铸工艺三大要素 3.2.2 立式压铸机工作原理
640~680℃
200℃左右 900~980℃
1. 密度低,比强度高 2. 流动性好 3. 减震性、磁屏蔽性能好
1.熔点低,流动性好,收缩小 2.可塑性好 3.铸件表面光滑,易做各种表面处理
因熔点高,模具寿命低,应减少使用
3.2 压铸机 3.压铸工艺三大要素
压铸机一般分为冷压室压铸机和热压室压铸机两大类。 冷压室压铸机按其压室结构和布置方式分为卧式压铸机和立式压铸机两种。
3.1 压铸合金
压铸合金应具备的特性: 易于压铸:流动性、收缩性、出模性等尽可能满足压铸的要求。 机械性能:强度、延伸性、脆性等满足产品的设计要求。 机械加工性:易于加工及加工表面的质量能达到产品设计的要求。 表面处理性:抛光、电镀、喷漆、氧化等要求能达到产品设计的要求。 抗腐蚀性:产品在最终的使用环境下具有一定的抗腐蚀性。
4.1 压铸各阶段4.压铸工艺的工艺参数
t1:金属液在压室中未承受压力的时间 t2:金属液于压室中在压射冲头的作用下,通过内 浇口充填型腔的时间 t3:充填刚刚结束时的瞬间 t4.压铸工艺的工艺参数
4.2 工艺参数的选4择.压铸工艺的工艺参数
影响充型的主要因素包括:压力、速度、温度、时间,而各个因素是相互影响和制约的。调整某一 因素,其他因素也会随之变化,因此需对这些工艺参数进行正确选择和调整才能保证生产。
2.1 定义
2.压力铸造
压力铸造:熔融金属在高压下高速充型,并在压力下凝固的铸造方法
2.2 特点
金属液是在压力下填充型腔并结晶凝固 金属液以高速(10~100 m/s)填充型腔,金属液充型时间极短(0.1~0.2 s)
2.3 优缺点
优点
生产效率高,适合大批量生产 铸件尺寸精度高,表面光洁 铸件强度高,比普通铸件强度提高25%~30% 金属利用率高,后续加工量小
铸件结构对各参数选择的影响如下表所示:
铸件结构
速度
厚而简单
低速
薄而复杂
高速
压力 高压 高压
温度 低温 高温
时间 长 短
主要压铸合金 铝合金
锌合金
镁合金 铅锡合金 铜合金
3浇.铸压温度 铸工艺三大特点要及性能素
650~680℃
1. 密度低,可生产要求减轻质量的零部件 2. 强度高,塑性好 3. 抗氧化腐蚀性能好
420~440℃
1. 良好的压铸特性:容易压铸形状复杂,尺寸精度高的产品 2. 抗拉强度高和硬度高,冲击韧性和伸长率较好 3. 良好的加工性能:产品表面,容易做各种表面处理 4. 生产高效
3.压铸工艺三大要素 3.2.3 热压室压铸机工作原理
3.压铸工艺三大要素 3.2.4 各压铸的压铸特点
卧式压铸: ①结构简单,操作程序少,生产效率高,易实现自动化 ②金属消耗少; ③能量损失少,使用更为广泛。 立式压铸: ①有余料切断、顶出功能; ②空气不易随金属进入压室; ③金属液进入型腔经过转折,压力消耗大~缺点 热压室压铸: ①生产工序简单、生产效率高、易实现自动化 ②金属消耗少、工艺稳定、无氧化杂物、铸件质量好; ③压室和冲头长时间浸泡在高温金属液中,影响使用寿命,常用 于锌合金压铸。
缺点
液态金属充型速度高,流态不稳定,铸件易产生气孔 设备费用昂贵,压铸机、熔化炉、保温炉、压铸模等费用都很昂贵 高熔点合金(铜、铁等),压铸模寿命短
3.压铸工艺三大要素
压铸工艺的三大要素分别是:压铸合金;压铸机;压铸模 压铸工艺则是将三大要素作有机的组合并加以运用的过程,使各种工艺参数满足压铸生产的需要。
压力铸造工艺简介
1. 铸造简介
1.1 定义
材料成型工艺:焊接、铸造、压力加工(锻造和冲压) 铸造:熔炼金属,制造铸型,并将熔融金属浇入铸型,凝固后获得具有一定形状、尺寸和性能金属零件毛坯的成型方法
1.2 铸造分类
按造型分类:① 砂型铸造;② 特种铸造——金属模铸造;脱蜡铸造 按成型工艺分类:① 重力浇铸;② 压力铸造