高压直流电机7712说明书
直流电动机使用维护

滑动轴承电机的转子应放置于机械中心。 应特别注意在某些情况下 ,被驱动设备的轴有热膨胀,如果这一膨胀引起电机在正常运行下转子 轴向位置的偏移,在室温下安装电动机时应将定子向远离被驱动设备的 方向移一小段距离,其数值等于被驱动设备的轴在额定运行温度与安装 时的室温之间的膨胀。 安装滚动轴承电机时,考虑被驱动设备的轴有热膨胀,这一膨胀会 引起电动机在正常运行下转子轴向位置的偏移,在室温下安装电动机时 应将电动机向远离被驱动设备的方向移一段小距离,其数值等于被驱动 设备的轴在额定运行与安装时的室温之间膨胀,应由被驱动设备的制造 厂提供此数值。 当电机的定位已满足轴向游动的要求时,则装上并拧紧底脚螺栓。
机械连接
当采用管道通风方式时,电机上设有连接法兰与管道连接,其具体位 置及连接尺寸见随机提供的外形图。 当采用空水冷却方式时,空水冷却器的进、出水法兰的位置及尺寸见 电机外形图。水管和法兰密封连接后检查是否有泄漏,冷却水应符合水质 要求。 。 电机滑动轴承若采用强制润滑方式供油,应尽可能将稀油站安装在靠 近电机的地方,一般情况下,与电机轴承的出油口相接的管道希望是一个 从轴承略向下(至少15°)的管道,要求电机轴承的出油口位置至少比稀 油站的回油管高300毫米,以避免轴承油位过高,且可保证回油畅通。将 管道连接到轴承之前,要注入清洁油,检查供油系统,然后取下滤油器, 清理干净。在稀油站与滑动轴承间应装有油量调节装置。 稀油站运行前,先在稀油站和滑动轴承中加入规定牌号(见电机外形 图或轴承铭牌)的润滑油,打开稀油站,观察油路是否存在泄漏现象,观 察轴承内油的位置,正常油位应在轴承油位观察孔1/2至2/3的位置,否则 应及时处理。供油系统试运行48小时左右,再次取下滤油器,确认润滑油 系统是否清洁,并清理干净。 安装振动传感器的电机,其安装螺孔一般在轴承座上。
海拔199122电机反转启动器说明书
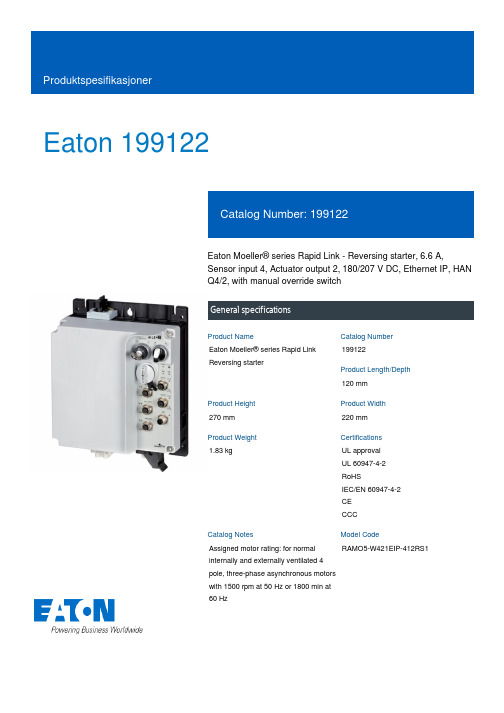
Eaton 199122Eaton Moeller® series Rapid Link - Reversing starter, 6.6 A,Sensor input 4, Actuator output 2, 180/207 V DC, Ethernet IP, HANQ4/2, with manual override switchGeneral specificationsEaton Moeller® series Rapid LinkReversing starter199122120 mm270 mm220 mm1.83 kg UL approvalUL 60947-4-2RoHSIEC/EN 60947-4-2CECCCAssigned motor rating: for normal internally and externally ventilated 4 pole, three-phase asynchronous motors with 1500 rpm at 50 Hz or 1800 min at 60 Hz RAMO5-W421EIP-412RS1Product Name Catalog NumberProduct Length/Depth Product Height Product Width Product Weight CertificationsCatalog Notes Model CodeIs the panel builder's responsibility. The specifications for the switchgear must be observed.3 kW6.6 A (at 150 % Overload)480 V AC, 3-phase400 V AC, 3-phase10000 A0 VMeets the product standard's requirements.Is the panel builder's responsibility. The specifications for the switchgear must be observed.Does not apply, since the entire switchgear needs to be evaluated.0 kW2.238 kWMeets the product standard's requirements.0 V-40 °CTwo sensor inputs through M12 sockets (max. 150 mA) for quick stop and interlocked manual operation2 Actuator outputsKey switch position OFF/RESET Generation Change RASP4 to RASP5Generation change from RA-SP to RASP 4.0Generation Change RA-SP to RASP5Generation change from RA-MO to RAMO 4.0Configuration to Rockwell PLC for Rapid LinkGeneration change RAMO4 to RAMO5Rapid Link 5 - brochureDA-SW-drivesConnect - installation helpDA-SW-Driver DX-CBL-PC-3M0DA-SW-drivesConnectDA-SW-USB Driver DX-COM-STICK3-KITDA-SW-USB Driver PC Cable DX-CBL-PC-1M5DA-SW-drivesConnect - InstallationshilfeMaterial handling applications - airports, warehouses and intra-logistics ETN.RAMO5-W421EIP-412RS1.edzIL034092ZUramo5_v14.dwgramo5_v14.stpDA-DC-00004525.pdfDA-DC-00003964.pdfDA-DC-00004184.pdfDA-DC-00004523.pdfeaton-bus-adapter-rapidlink-speed-controller-dimensions-002.eps eaton-bus-adapter-rapidlink-speed-controller-dimensions-003.eps eaton-bus-adapter-rapidlink-reversing-starter-dimensions-003.eps eaton-bus-adapter-rapidlink-reversing-starter-dimensions-002.eps10.11 Short-circuit ratingRated operational power at AC-3, 380/400 V, 50 HzInput currentRated operational voltageRated conditional short-circuit current, type 1, 480 Y/277 V Rated control supply voltage (Us) at AC, 50 Hz - min10.4 Clearances and creepage distances10.12 Electromagnetic compatibility10.2.5 LiftingRated power at 575 V, 60 Hz, 3-phaseRated power at 460 V, 60 Hz, 3-phase10.2.3.1 Verification of thermal stability of enclosures Rated control supply voltage (Us) at DC - minAmbient storage temperature - minFitted with:Applikasjonsmerknader BrosjyrereCAD model Installeringsinstruksjoner mCAD model SertifiseringsrapporterTegningerManual override switchKey switch position AUTOThermistor monitoring PTCKey switch position HANDThermo-clickElectronic motor protectionShort-circuit releaseOverload cycleAC-53aNumber of pilot lightsRated control supply voltage (Us) at AC, 50 Hz - max0 VSystem configuration typePhase-earthed AC supply systems are not permitted.AC voltageCenter-point earthed star network (TN-S network)10.8 Connections for external conductorsIs the panel builder's responsibility.Coordination class (IEC 60947-4-3)Class 1Rated conditional short-circuit current, type 1, 600 Y/347 V0 ARated conditional short-circuit current (Iq)10 kABraking voltage180/215 V DC -15 % / +10 %, Actuator for external motor brakeAmbient operating temperature - max55 °CRated operational power at AC-3, 220/230 V, 50 Hz0 kWClimatic proofing< 95 %, no condensationIn accordance with IEC/EN 50178FeaturesParameterization: drivesConnectParameterization: drivesConnect mobile (App) Parameterization: KeypadParameterization: FieldbusLifespan, electrical10,000,000 Operations (at AC-3)Number of command positions2Electrical connection type of main circuitPlug-in connectionElectrical connection type for auxiliary- and control-current circuit Plug-in connectionRated control supply voltage (Us) at DC - max0 V10.9.3 Impulse withstand voltageIs the panel builder's responsibility.Braking current≤ 0.6 A (max. 6 A for 120 ms), Actuator for external motor brakeAmbient operating temperature - min-10 °C10.6 Incorporation of switching devices and componentsDoes not apply, since the entire switchgear needs to be evaluated.Current limitation0.3 - 6.6 A, motor, main circuitAdjustable, motor, main circuitCable length10 m, Radio interference level, maximum motor cable length10.5 Protection against electric shockDoes not apply, since the entire switchgear needs to be evaluated.Mounting positionVerticalMains switch-on frequencyMaximum of one time every 60 secondsClassCLASS 10 A10.13 Mechanical functionThe device meets the requirements, provided the information in the instruction leaflet (IL) is observed.10.2.6 Mechanical impactDoes not apply, since the entire switchgear needs to beevaluated.10.9.4 Testing of enclosures made of insulating materialIs the panel builder's responsibility.10.3 Degree of protection of assembliesDoes not apply, since the entire switchgear needs to be evaluated.Electromagnetic compatibilityClass AVoltage typeDCProduct categoryMotor starterOverload release current setting - min0.3 ARated control voltage (Uc)24 V DC (-15 %/+20 %, external via AS-Interface® plug)180/207 V DC (external brake 50/60 Hz)Rated operational current (Ie)6.6 AAssigned motor power at 460/480 V, 60 Hz, 3-phase3 HPRated frequency - min47 HzNumber of auxiliary contacts (normally closed contacts)Rated conditional short-circuit current (Iq), type 2, 380 V, 400 V, 415 V0 APower consumption8 W10.2.3.2 Verification of resistance of insulating materials to normal heatMeets the product standard's requirements.10.2.3.3 Resist. of insul. mat. to abnormal heat/fire by internal elect. effectsMeets the product standard's requirements.On-delay20 - 35 msLifespan, mechanical10,000,000 Operations (at AC-3)Rated operational current (Ie) at 150% overload6.6 AProtocolEtherNet/IPOverload release current setting - max6.6 A10.9.2 Power-frequency electric strengthIs the panel builder's responsibility.Overvoltage categoryIIIDegree of protectionNEMA 12IP65Rated frequency - max63 HzVibrationResistance: 10 - 150 Hz, Oscillation frequency Resistance: 57 Hz, Amplitude transition frequency on accelerationResistance: 6 Hz, Amplitude 0.15 mmResistance: According to IEC/EN 60068-2-6Rated operational power at 380/400 V, 50 Hz - max3 kWAmbient storage temperature - max70 °CShort-circuit protection (external output circuits)Type 1 coordination via the power bus' feeder unit, Main circuitRated control supply voltage (Us) at AC, 60 Hz - min0 V10.7 Internal electrical circuits and connectionsIs the panel builder's responsibility.Rated impulse withstand voltage (Uimp)4000 VConnectionConnections pluggable in power sectionOff-delay20 - 35 ms10.10 Temperature riseThe panel builder is responsible for the temperature rise calculation. Eaton will provide heat dissipation data for the devices.FunctionsFor actuation of motors with mechanical brakeExternal reset possibleTemperature compensated overload protectionOutput frequency50/60 HzMains voltage tolerance380 - 480 V (-15 %/+10 %, at 50/60 Hz)Rated conditional short-circuit current (Iq), type 2, 230 V0 ATypeReversing starter10.2.2 Corrosion resistanceMeets the product standard's requirements.Supply frequency50/60 Hz, fLN, Main circuit10.2.4 Resistance to ultra-violet (UV) radiationMeets the product standard's requirements.10.2.7 InscriptionsMeets the product standard's requirements.Rated control supply voltage (Us) at AC, 60 Hz - max0 VRated operational current (Ie) at AC-3, 380 V, 400 V, 415 V6.6 ARated operational power at 380/400 V, 50 Hz - min0.09 kWModelReversing starterNumber of auxiliary contacts (normally open contacts)2Shock resistance15 g, Mechanical, According to IEC/EN 60068-2-27, 11 ms, Half-sinusoidal shock 11 ms, 1000 shocks per shaftAltitudeEaton Corporation plc Eaton House30 Pembroke Road Dublin 4, Ireland © 2023 Eaton. Med enerett. Eaton is a registered trademark.All other trademarks areproperty of their respectiveowners./socialmediaMax. 2000 mMax. 1000 mAbove 1000 m with 1 % performance reduction per 100 m。
(完整word版)科蒂斯控制器1207A说明书(中)

1207A型直流电机控制器使用手册1概述CURTIS PMC 1207A可编程电机速度控制器为各种小型电动车辆提供了高效和易于安装的的控制系统,典型的应用对象为行走式叉车/堆垛车,小型载客车和清洁车等,以微控制器为核心的逻辑部分,配以可靠的MOSFET功率单元,为封装简洁紧凑的1207A控制器提供了大功率输出和先进的性能,可选用手持式编程器使用户能进行快捷、方便地完成参数设定,指导调试及获取故障诊断信息。
同所有CURTIS PMC 电机速度控制器一样,1207A型控制器为车辆的电机驱动速度提供了优异的运动控制,1207A控制器的主要性能包括:◆无级变速和反相制动控制◆大功率MOSFET设计提供高效(减少电机和电池损耗)和无噪声操作◆纯铜功率母线,配以经极化处理接线器传输能量◆采用铝制安装板和注模外壳,具有坚固而保护良好的结构◆过电压和欠电压保护可有效。
◆温度保护和补偿电路提供了低温消减,恒定电流限幅及高温线性回落功能一因而在任何温度条件下都不会发生突然性功率输出中断。
◆智能型手持编程器(选用件)提供了一套完整的参数设定和功能设定◆控制器及其它系统部件的诊断与测试信息,既能够通过车辆上的控制器获得,也可通过编程器获得◆硬件电路和软件对调速器电路, MOSFET驱动电路,MOSFET晶体管,接触器驱动器和接触器进行故障检测---确保控制器满足欧洲经济共同体(EEC)所规定的故障检测要求。
◆输入顺序选择包括空档起动和SRO◆微处理器控制的接触器动作顺序提供了真正的无电弧接触器开闭◆平滑的, 可控的反相制动—可变方式(与调速器位置相关)或固定的反相电流限幅方式◆空挡制动功能。
◆双模式运行可使车辆在不同环境下有不同的运行特性。
◆单信号输入方式的紧急反向功能(凸键开关)◆防后滑功能提供了满功率斜坡起动◆简洁的接触器和开关接线,带有短路和开路监测的线圈驱动器确保了安全操作。
◆灵活的调速器电路能够适应各种类型的调速器:5000-0欧姆,0-5000欧姆,0-5伏,3线电位器和各种电子调速器熟悉CURTIS PMC控制器会帮助您正确地安装和使用它。
同步发电机使用说明书(中文)
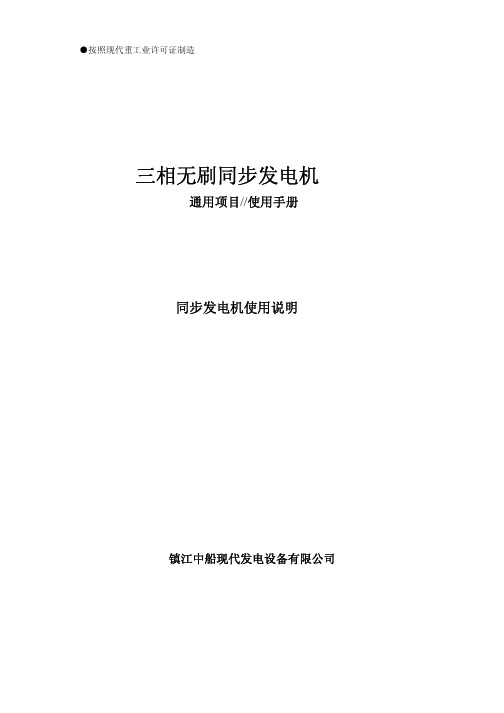
在传输元件装好之前不要移开轴承座。 如果传输元件装好不得不再运输电机时,必须配 置其它适当尺寸的轴承座。
如果电机到达后不立即使用,应贮藏在干燥 没有振动的室内。
贮藏地点必须干燥且干净。防止热气侵入电 机绕组。
机器加工面(联接部位、底脚部位等)涂上 防锈油。
!DANGER 危险 危险电压 将导致死亡、严重伤害、电死或设备损坏 设备检查之前断开所有电源
使用之前和长期存放后或备机时必须用直 流电测量绕组对机座的绝缘。在尚未显示出最终 的绝缘电阻之前,不要停止通电测量工作(对于 高压电机来说,这种过程可能要持续一分钟) 最小绝缘电阻和临界绝缘电阻的极限值(在绕组 温度为 25℃时测量)和测量电压的极限值可根据 电机的额定电压而从下表中得出。
力矩传给发电机。 轴承端允许的振动强度如下:
<10HZ
振幅
S≤0.40mm-峰值
10-100HZ
振速 Veff≤18mm/s-rms
>100HZ
加速度 b≤1.6g
如需要更高的振动要求,请咨询。
10)运输
!WARING 警告 不适当的操作会导致人身伤害或财产损失。 起吊发电机时: 1、 仅在指定的地点起吊。 2、 使用机器起吊。 3、 起吊绳索缓缓地拉紧。 4、 不要猛拉或突然移动发电机。 5、 不要使用盖子手柄起吊。
5
5
发电机安装场所必须是冷却空气进口 和出口都畅通无阻。
排出的热废气不能再重新吸入。
百叶窗开口应朝下以确保防护等级。 移开轴承座(适宜的时候)。 遵照附在轴伸端或接线盒上的说明。 在轴伸嵌入的半个导向键以使转子达到动 态平衡。 将电机仔细地进行对中,对轴上的部件 精确地进行平衡校验,以确保能平稳无振动 地运行。
双电机调速技术说明书

双电机调速技术说明书小组成员:XXX XXX XXX XXX随着现代化步伐的加快,人们生活水平的不断提高,对自动化的需求也越来越高,直流电机和步进电机的应用领域也不断扩大。
本设计的功能比直流电机强大,我们既可以把此设计用于教学也可作为需要同步的两个物体的底层设计。
工作原理:本设计主要是实现直流电机和步进电机同步调速,就是将步进电机的速度设为参照,然后执行利用直流电机调速,通过PID控制算法使得直流电机跟着步进电机同步随动。
一、工作原理电路图(一)系统总体设计图图1 调速系统总体设计框(二)本设计选用STC公司89C52单片机作为主控制器模块。
单片机的最小系统模块如下图所示。
图2 单片机的最小系统(三)本设计采用目前市场上较容易买到的L298直流或步进电机驱动芯片,它采用单片集成塑装,是一个高电压、大电流全双桥驱动器,由标准的TTL电平控制。
直流驱动模块电路如图所示。
图3 直流驱动模块电路表1 L298对直流电机控制的逻辑真值表输入输出Ven=H Ven=H Ven=H C=H;D=L 正转C=L;D=H 反转C=D 制动Ven=L C,D不确定没有输出,电机不工作(四)本设计中步进电机驱动部分采用专用电机驱动芯片TB6560对电机进行驱动。
步进电机的驱动模块如下图所示:图4 步进电机的驱动模块表2 转矩设定输入TQ1和转矩设定输入TQ2工作电流选择TQ2 TQ2 电流值L L 100%L H 75%H L 50%H H 20%表3 细分方式的选择M2 M10 0 整步0 1 二分之一细分1 0 十六分之一细分1 1 八分之一细分表4 衰减方式PFD2 PFD10 0 快衰减0 1 百分之二十快衰减1 0 百分一五十快衰减1 1 慢衰减(五)1602显示电路设计中显示模块采用LCD1602液晶同时显示步进电机和直流电机的速度,以及步进电机的脉冲光和直流电机的PWM。
其硬件电路实现如图所示:图5 1602显示电路(五)设计中的键盘模块有四个弹性按键,采用高电平输入方式进行信号的输入,按键控制电路如图所示:图6 按键控制电路(六)转速检测电路如图所示:图7 转速检测电路二、电路板的制作工艺(一)电路板的制作过程1.根据电路功能需要设计原理图。
调节系统说明书Z771{08}01_PLM2
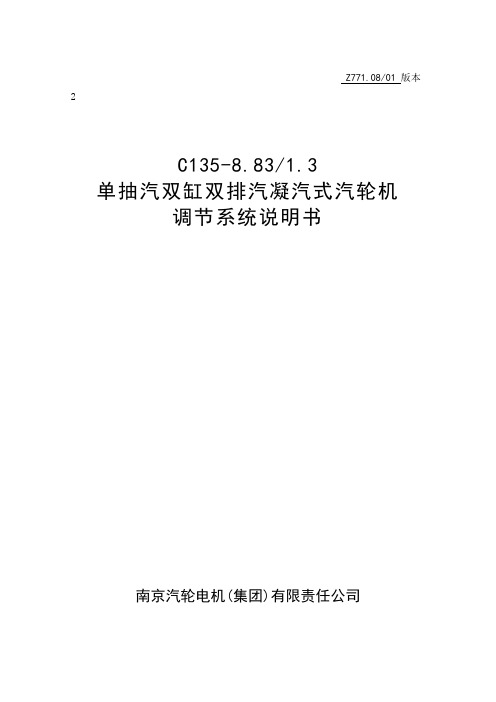
Z771.08/01 版本2C135-8.83/1.3单抽汽双缸双排汽凝汽式汽轮机调节系统说明书南京汽轮电机(集团)有限责任公司编制张琦2008.4 校对汤继星2008.4 审核张静2008.4 会签标准审查郝思军2008.4 审定马艳增2008.4 批准目次1 引言 .................................................. 错误!未定义书签。
2 调节保安系统的主要技术规范 ............................ 错误!未定义书签。
3 供油系统 .............................................. 错误!未定义书签。
4 保安系统 .............................................. 错误!未定义书签。
5 保安系统的调整与试验 .................................. 错误!未定义书签。
1 引言本说明书为C135-8.83/1.3型100MW单抽汽双缸双排汽凝汽式汽轮机调节保安系统的安装,调试以及日后的使用维护和检修提供必要的依据。
本说明书分别列出了调节(控制)、保安、供油及热工系统的主要技术规范。
在使用说明书时,还需要随时参考本机组的其它有关文件和图纸,特别是与调节系统有关的系统总图及相关部套图纸。
2 调节保安系统的主要技术规范3 供油系统润滑油系统的作用是向机组各轴承提供润滑油和向保安系统提供压力油,同时还向盘车装置和顶轴装置供油。
油系统采用的工质为L-TSA46或L-TSA32透平油,透平油质量必须符合GB/T7596-2000《电厂用运行中汽轮机油质量标准》的要求。
本系统采用传统的汽轮机转子直接驱动的主油泵------注油器供油线,主油泵出口的压力油驱动注油器投入工作,润滑油系统主要用于向汽轮发电机组各轴承提供润滑油,向调节保安部套提供压力油,向顶轴装置中的油泵提供充足的油源。
RoboClaw 2x7A 双通道电机控制器数据手册说明书

RoboClaw 2x7A, 34VDC Dual Channel Brushed DC Motor ControllerData Sheet Version 2.3Feature Overview:• 7.5 Amps Continuous Per Channel• 15 Amps Peak Per Channel• Channel Bridging Supported• Dual Quadrature Decoding• 9.8 million PPS Decoding• Multimode Interface• TTL Serial• USB Port• Analog Interface• R/C Input Control• Limit, Home and E-Stops• Up to 34VDC Operation• Air Cooled• 3.3v Compliant Control Outputs• 5v Tolerant Control Inputs• Programmable Current Limiting• Programmable Voltage Clamping• Closed and Open Loop Operation• Auto Tuning PID Feature• Mixed Control Modes• Data Logging• Diagnostic LEDs• Field Firmware Updates• Regulated 5VDC, 1A User Available Output• Over Voltage and Under Voltage Protection• Easy Tuning, Monitor and Setup with PC utilityDevice OverviewThe RoboClaw is an intelligent, high performance motor controller designed to control dual brushed DC motors. It can be controlled from USB, RC radio, PWM, TTL serial, analog and microcontrollers such as an Arduino or Raspberry Pi.RoboClaw automatically supports 3.3V or 5V logic levels, travel limit switches, home switches, emergency stop switches, power supplies, braking systems and contactors. A built-in switching mode BEC supplies 5VDC at up to 1 Amp for powering user devices. In addition power supplies can be utilized by enabling the built in voltage clamping control feature.A wide variety of feedback sensors are supported. This includes quadrature encoders, potentiometers and absoluteencoders which can be easily configured using the available auto tune function. With sensors, two brushed DCmotors can be controlled in closed loop mode allowing precise control over position and speed. With the ability to use potentiometers, servo systems can be created and controlled from any of RoboClaw’s interface modes.For greater control, built-in commands are available for controlling acceleration, deceleration, distance, speed, current sense, voltage limits and more. In addition, RC and analog modes can be configured by user defined settings to control acceleration and deceleration rates.RoboClaw incorporates multiple protection features including temperature, current, over voltage and under voltage limits.The protection features are self monitoring and protect RoboClaw from damage in any operating condition. User definable settings such as maximum current limit, maximum and minimum battery voltages are provided for more refined control.RoboClaw’s regenerative capabilities will charge a supply battery during slow down or breaking. It’s advance circuitry can change direction during full throttle without damage! RoboClaw also incorporates a LiPo cutoff mode to prevent battery damage.Multimode InterfaceRoboClaw’s I/O are voltage protected and can handle up to 5VDC. The I/O only output a high of 3.3V. This allows RoboClaw to be interfaced to 5V or 3V logic easily with no translation circuits required. RoboClaw can be connected directly to a Raspberry Pi or Arduino. All of RoboClaw’s inputs are internally pulled-up to prevent false triggers. Inputs can also be configured using the Motion Studio application.User Regulated Power OutputRoboClaw provides regulated power (BEC) for user devices. A high efficiency switching regulator supplies 5VDC at up to1 Amp. This voltage can be used to power external sensors, encoders, MCUs and other electronics. The regulated userpower is automatically current limited and thermally protected.Main BatteryThe peak operational input voltage depending on the model can be up to 34VDC, 60VDC or 80VDC. The modelsmaximum input voltage can not be exceeded. If the maximum voltage is exceed the motors will be disabled. Fully charged batteries maximum voltage must be taken into account when in use. RoboClaw is a regenerative motor controller. During regeneration, voltages can peak over the maximum rated voltage in which RoboClaw is designed to handle these over voltage spikes by braking the motors.Logic BatteryRoboClaw accepts a logic battery. The logic battery is also known as a backup battery. The user regulated power output (BEC) is by default powered from the main battery, unless a logic battery is detected. The logic battery source is coupled to the main battery through an on board automatic switch. If the main battery voltage drops below the logic battery input level, the logic circuit and user regulated power output will be drawn from the logic battery.SoftwareRoboClaw can be easily configured using the Motion Studio software tool. The Windows based application enables users to quickly configure RoboClaw. The software can be used during run time to monitor and control several operational parameters. Motion studio is available from the website. It can also be found in the Downloads section of the Basicmicro website or listed under the Download tabs on the production page.User ManualThis data sheet only covers model specific information and basic wiring. To properly setup and use RoboClaw refer to the RoboClaw User Manual available for download from .CoolingRoboClaw will generate heat. The maximum current ratings can only be achieved and maintained with adequate heat dissipation. The motor controller should be mounted so that sufficient airflow is provided. Which will dissipate the heat away from the motor controller during operation. Some models of RoboClaw include a built-in automatic cooling fan controller, which can be used to help maintain continuous currents under extreme conditions.Emergency StopThe motor controller should be wired using an external contactor, relay or high amperage mechanical switch to control the main power input. A second power source should be used to power the logic section in situations where the main power will be under heavy load. Voltage drops can occur from constant full load or high speed direction changes. Voltage drop can cause logic brown outs if only a main battery is used without a logic battery.USBThe motor controllers USB port should be used for configuration and debugging. The USB protocol is not designed for electrically noisy environments. The USB port will likely disconnect and not automatically recover during operation in electrically noisy environments. To recover from a dropped USB port, the motor controllers USB cable may require being unplugged and re-plugged in. The TTL serial control should be the preferred method of control in electrically noisy environments.Firmware UpdatesFirmware updates will be made available to add new features or resolve any technical issue. Before using RoboClaw for the first time it is recommended to update to the latest firmware. Download and install Motion Studio. Refer to the RoboClaw User Manual or Application Notes for additional information on updating the RoboClaw firmware.Hardware Overview:Control InterfaceThe RoboClaw uses standard male pin headers with 0.100” (2.54mm) spacing. The pin headers are ideal for use withstandard servo cables and other popular interface connectors. The table below list the pins and their respective functions. All pins are 5V tolerant and output 3.3V for compatibility with processor such as Raspberry Pi and Arduino. R/C pulse input, Analog and TTL can be generated from any microcontroller such as a Arduino or Raspberry Pi. The R/C Pulse input pins can also be driven by any standard R/C radio receiver . There are several user configurable options available. Toconfigure RoboClaw, install Motion Studio and connect it to an available USB port.Logic Battery (LB IN)The logic circuit of RoboClaw can be powered from a secondary battery wired to LB IN. A logic battery will prevent brownouts when the main battery is low or under heavy load. The positive (+) terminal is located at the board edge and ground (-) is the inside pin closest to the heatsink.Encoder Power (+ / -)The pins labeled + and - are the source power pins for encoders. The positive (+) is located at the board edge and supplies +5VDC. The ground (-) pin is near the heatsink. On RoboClaws with screw terminals, power for the encoders can be supplied by the 5VDC and GND on the main screw terminal.Encoder Inputs (1A / 1B / 2A / 2B)The encoders inputs are labeled EN1 and EN2. EN1 is for encoder 1 and EN2 is for encoder 2 which also correspond to motor channel 1 and motor channel 2. Quadrature encoder inputs are typically labeled 1A, 1B, 2A and 2B. ChannelA of both EN1 and EN2 are located at the board edge on the pin header. ChannelB pins are located near the heatsinkon the pin header. Quadrature encoders are directional. When connecting encoders make sure the leading channel for the direction of rotation is connected to A. If one encoder is backwards to the other you will have one internal counter counting up and the other counting down. Use Motion Studio to determine the encoders direction relative to the motors rotation. Encoder channels A and B can be swapped in software using Motion Studio to avoid re-wiring the encoder or motor.Control Inputs (S1 / S2 / S3 / S4 /S5)S1, S2, S3, S4 and S5 are configured for standard servo style headers I/O (except on ST models), +5V and GND. S1 and S2 are the control inputs for serial, analog and RC modes. S3 can be used as a flip switch input, when in RC or Analog modes. In serial mode S3, S4 and S5 can be used as emergency stops inputs or as voltage clamping control outputs.When configured as E-Stop inputs, they are active when pulled low. All I/O have internal pull-ups to prevent accidental triggers when left floating. S4 and S5 can be configured as home switch and limit switch inputs. The pins closest to the board edge are the I/0s, center pin is the +5V and the inside pins are ground. Some RC receivers have their own supply and will conflict with the RoboClaw’s 5v logic supply. It may be necessary to remove the +5V pin from the RC receivers cable in those situations.Cooling Fan ControlThe cooling fan control will automatically turn on and off a fan based on RoboClaws temperature. The fan will turn on when the board temperature reaches 45°C and will automatically turn off when the board temperature falls below 35°C.The fan control circuit can power a 5VDC fan at up to 230mA. A wide range of fans can be used. The CFM rating of the fan will determine how effective the fan is at cooling. A tested fan is available from DigiKey under part number:259-1577-ND. However any fan can be used provided it meets the electrical specifications outlined above.Main Battery Screw TerminalsThe main power input can be from 6VDC to 34VDC on a standard RoboClaw and 10.5VDC to 60VDC or 80VDC on an HV (High Voltage) RoboClaw. The connections are marked + and - on the main screw terminal. The plus (+) symbol marks the positive terminal and the negative (-) marks the negative terminal. The main battery wires should be as short as possible.Do not reverse main battery wires or damage will occur.DisconnectThe main battery should include a quick disconnect in case of a run away situation and power needs to be cut. The switch must be rated to handle the maximum current and voltage from the battery. Total current will vary depending on the type of motors used. A common solution would be an inexpensive contactor which can be sourced from sites like Ebay.A power diode rated for approximately 2 to 10 Amps should be placed across the switch/contactor to provide a return tothe battery when power is disconnected. The diode will provide the regenerative power a place to go even if the switch is open.Motor Screw TerminalsThe motor screw terminals are marked with M1A / M1B for channel 1 and M2A / M2B for channel 2. For a typical differential drive robot the wiring of one motor should be reversed from the other. The motor and battery wires should be as short as possible. Long wires can increase the inductance and therefore increase potentially harmful voltage spikes.Control ModesRoboClaw has 4 main functional control modes explained below. Each mode has several configuration options. The modes can be configured using Motion Studio or the built-in buttons. Refer to the RoboClaw User Manual for installation and setup instructions.RCUsing RC mode RoboClaw can be controlled from any hobby RC radio system. RC input mode also allows low powered microcontrollers such as a Basic Stamp to control RoboClaw. Servo pulse inputs are used to control the direction and speed. Very similar to how a regular servo is controlled. Encoders are supported in RC mode, refer to the RoboClaw user manual for setup instructions.AnalogAnalog mode uses an analog signal from 0V to 2V to control the speed and direction of each motor. RoboClaw can be controlled using a potentiometer or filtered PWM from a microcontroller. Analog mode is ideal for interfacing RoboClaw with joystick positioning systems or other non microcontroller interfacing hardware. Encoders are supported in Analog mode, refer to the RoboClaw user manual for setup instructions.Simple SerialIn simple serial mode RoboClaw expects TTL level RS-232 serial data to control direction and speed of each motor.Simple serial is typically used to control RoboClaw from a microcontroller or PC. If using a PC, a MAX232 or an equivalent level converter circuit must be used since RoboClaw only works with TTL level inputs. Simple serial includes a slave select mode which allows multiple RoboClaws to be controlled from a signal RS-232 port (PC or microcontroller). Simple serial is a one way format, RoboClaw can only receive data. Encoders are not supported in Simple Serial mode.Packet SerialIn packet serial mode RoboClaw expects TTL level RS-232 serial data to control direction and speed of each motor. Packet serial is typically used to control RoboClaw from a microcontroller or PC. If using a PC a MAX232 or an equivalent level converter circuit must be used since RoboClaw only works with TTL level input. In packet serial mode each RoboClaw is assigned a unique address. There are 8 addresses available. This means up to 8 RoboClaws can be on the same serial port. Encoders are supported in Packet Serial mode, refer to the RoboClaw user manual for setup instructions.USB ControlUSB can be used in any mode. When RoboClaw is in packet serial mode and another device, such as an Arduino, is connected commands from the USB and Arduino will be executed and can potentially override one another. However if RoboClaw is not in packet serial mode, motor movement commands will be overiden by Analog or RC pulse input. USB packet serial commands can then only be used to read status information and set configuration settings.There are several wiring configurations for RoboClaw. Each configuration will have unique wiring requirements to ensure safe and reliable operation. The diagram below illustrates a very basic wiring configuration used in a small motor system where safety concerns are minimal. This is the most basic wiring configuration possible. All uses of RoboClaw should include some kind of main battery shut off switch, even when safety concerns are minimal. Never underestimate a system with movement when an uncontrolled situation arises.In addition, RoboClaw is a regenerative motor controller. If the motors are moved when the system is off, it could cause potential erratic behavior due to the regenerative voltages powering the system. The regenerative voltages can cause problems if a power supply is used for main power. A voltage clamping circuit is recommended to dump the excessive voltages. See the RoboClaw user manual or Application Notes for voltage clamping setup and wiring diagrams.R/C ModeThe below wiring diagram is very basic and for use with R/C mode. R/C mode can be used when pairing RoboClaw with a standard R/C receiver. R/C mode can also be used with a microcontroller and using servo pulses to control RoboClaw. The RoboClaw supplies power to the R/C system. If the R/C receiver used, has its own power the 5V pin on the 3 pin header must be remove otherwise it will interfere with RoboClaw’s BEC.In all system with movement, safety is a concern. This concern is amplified when dealing with higher voltages. The wiring diagram below illustrates a properly wired system. An external main power cut off is required (SW1). The external cut off can consist of a high amperage mechanical switch or a contactor.When the RoboClaw is switched off or a fuse is blown, a high current diode (D1) is required to create a return path to the battery for potential regenerative voltages. In addition a pre-charge resistor (R1) is required to reduce the high inrush currents to charge the on board capacitors. A pre-charge resistor (R1) should be around 1K, 1/2Watt for a 60VDC motor controller which will give a pre-charge time of about 15 seconds. A lower resistances can be used with lower voltages to decrease the pre-charge time.Closed Loop ModeA wide range of sensors are supported for closed loop operation. RoboClaw supports dual quadrature encoders (up to9.8 million PPS), absolute encoders, potentiometers and hall effect sensors. The wiring diagram below is an exampleof closed loop mode using quadrature encoders. Quadrature encoders are directional. RoboClaw’s internal counters will increment for clockwise rotation (CW) and decrement for counter clockwise rotation (CCW). When wiring encoders A andB channels it is important they are wired to match the direction of the motor. If the encoder is wired in reverse it cancause a run away condition. All motor and encoder combinations will need to be tuned (see the RoboClaw user manual).Logic BatteryAn optional logic battery is supported. Under heavy loads the main power can suffer voltage drops, causing potential logic brown outs which may result in uncontrolled behavior . A separate power source for the motor controllers logic circuit, will remedy potential problems from main power voltage drops. The logic battery maximum input voltage is34VDC with a minimum input voltage of 6VDC. The 5V regulated user output is supplied by the secondary logic battery if supplied. The mAh of the logic battery should be determined based on the load of attached devices powered by the regulated 5V user output.Logic Battery JumperThe configuration below utilizes a logic battery. Older models of RoboClaw have a logic battery jumper . On models where the LB-MB header is present the jumper must be removed when using a separate logic battery. If the header for LB-MB is not present, then the RoboClaw will automatically set the logic battery power source.R1D1Bridging ChannelsRoboClaws dual channels can be bridge to run as one channel, effectively doubling its current capability for one motor.Damage will result if RoboClaw is not set to bridged channel mode before wiring. Download and install Motion Studio.Connect the motor controller to the computer using an available USB port. Run Motion Studio and in general settings check the option to combine channels. Then click “Write Settings” in the device menu. When operating in bridged mode the total peak current output is combined from both channels. Each channel will indicate the amount of current being drawn for that channel. The peak current run time is dependant on heat build up. Adequate cooling must be maintained.For more information see the RoboClaw user manual.Bridged Channel WiringWhen bridged channel mode is active the internal driver scheme for the output stage is modified. The output leads must be wired correctly or damage will result. One side of the motor is connected to M1A and M2B. The other side of the motor is then connected to M1B and to M2A.DimensionsNotes:1. Peak current is automatically reduced to the typical current limit as temperature approaches 85°C.2. Current is limited by maximum temperature. Starting at 85°C, the current limit is reduced on a slope with a maximumtemperature of 100°C, which will reduce the current to 0 amps. Current ratings are based on ambient temperature of 25°C.3. RS232 format is 8Bit, No Parity and 1 Stop bit.4. Condensing humidity will damage the motor controller.WarrantyBasicmicro warranties its products against defects in material and workmanship for a period of 1 year. If a defect is discovered, Basicmicro will, at our sole discretion, repair, replace, or refund the purchase price of the product in question.*******************************.Noreturnswillbeacceptedwithouttheproperauthorization.Copyrights and TrademarksCopyright© 2015 by Basicmicro, Inc. All rights reserved. All referenced trademarks mentioned are registered trademarks of their respective holders.DisclaimerBasicmicro cannot be held responsible for any incidental or consequential damages resulting from use of products manufactured or sold by Basicmicro or its distributors. No products from Basicmicro should be used in any medical devices and/or medical situations. No product should be used in any life support situations.ContactsEmail:********************Techsupport:**********************Web: Discussion ListA web based discussion board is maintained at Technical Support*******************************************************************,byopeningasupportticketontheIon Motion Control website or by calling 800-535-9161 during normal operating hours. All email will be answered within 48 hours.。
70系列直流无刷电机

70系列直流无刷电机Version版权所有不得翻印【利用前请认真阅读本手册,以避免损坏电机】地址:东莞市万江区新和工业区瑞联振兴工业园B栋4楼70系列直流无刷电机利用手册70系列直流无刷电机一、产品简介概述70系列直流无刷电机,相较于市场中现有的产品,因东莞市一能机电技术设计革新使70无刷电机具有噪音更低,振动更小和工作寿命更长的优势。
产品能够普遍应用与工业自动化、泵阀、太阳能设备等。
产品特点驱动电压:DC48V基座号:70方形功率:320W调速范围:≤3500rpm适配驱动器:BLD300B参数规格型号输出功率(W)电机电压(VDC)转速(RPM)额定扭矩(Nm)机身长度(mm)重量(kg)70BLF-3230LBB 320 48 3000 120机械尺寸驱动器连接方式网址:70系列直流无刷电机利用手册力矩曲线图注意事项一不可拎着电机引线去拿70系列直流无刷电机二在70系列直流无刷电机通电的状态下不可插拨插头三请不要使70无刷电机落地,和碰撞电机,有此类情形发生的话,即便那时能够利用但70无刷电机的质量将不能取得保证四请顾客方对70直流无刷电机在实际装配的状态进行确认,验证明际利历时的适用性五 70直流无刷电机对过电压、过热、逆转、外部噪音等没有爱惜装置利历时请注意六70直流无刷电机分解后不可在组装利用七本公司对70直流无刷电机在实际利用中、关于利用方式所涉及的专利问题不负任何责任配套产品网址:70系列直流无刷电机利用手册产品保修条款一、一年保修期本公司对该产品的元器件和生产进程进行严格治理,从发货日起为客户提供一年的质保。
在保修期内本公司为有缺点的产品提供免费维修效劳。
二、不属保修之列1、不适当的接线,如电源正负极接反和带电拨插2、未经许可擅自更改内部器件,或撕掉易碎QC凭条的;3、超电器参数要求利用;4、极为特殊的应用环境,如极高温度或极度潮湿的环境等。
三、维修流程如需维修产品,将按下述流程处置:1、发货前请致电本公司窗口效劳人员获取返修许可号码2、随货周围寄书面说明,说明返修驱动器的故障现象;故障发生时所利用的电压、电流和利用环境等情形,联系人姓名、号及邮寄地址信息。