煤热值差
煤的发热量误差范围国标

煤的发热量误差范围国标在煤炭产品质量国家标准中,对煤的发热量有了明确规定,即不大于3500大卡/千克。
对实际测定结果允许负偏差,按规定以平均值±2%表示,一般都控制在±5%左右。
也就是说,用高热值煤或低热值煤进行掺配时,如发热量误差超过10%,则高热值煤或低热值煤所占比例越多,混合后煤的平均发热量相对值越低。
这样,以其他煤种进行混配时,高热值煤和低热值煤的比例可提高到50%。
( 1)煤炭的发热量误差范围指从小于某一发热量时开始计算,至被测煤的实际发热量与该发热量的平均值±2%表示;在煤炭的发热量相对值(测定的煤的平均发热量与其真实发热量之比)上允许负偏差,即允许实际煤的发热量±5%;混合煤的发热量由于存在掺配问题,故其相对值允许负偏差更小,即在混合后的煤的平均发热量相对值允许负偏差为±5%,而不论它们的原煤的发热量误差程度。
( 2)我国对高低热值煤的具体要求是:热值在2900~3500卡的为低热值煤, 4000~5000卡的为中热值煤, 5000~6000卡的为高热值煤。
其最小发热量应当符合国家标准要求,发热量在3500卡以下的低热值煤应不得混入高热值煤,发热量在5500卡以下的高热值煤应不得混入低热值煤。
( 3)我国对高低热值煤的具体要求是:热值在2900~3500卡的为低热值煤, 4000~5000卡的为中热值煤,5000~6000卡的为高热值煤。
而对于普通煤和次烟煤等类型的煤炭没有作出具体的规定,由企业自行掌握。
如果按煤炭的发热量算,每一吨煤可掺配1200大卡煤或1800大卡煤或2000大卡煤或2500大卡煤或3000大卡煤,按照普通煤配置每吨可掺混1000大卡煤或1200大卡煤或700大卡煤或500大卡煤或300大卡煤,按照次烟煤等类型的煤炭配置可掺混400大卡煤或200大卡煤或100大卡煤或50大卡煤或20大卡煤或10大卡煤。
通常情况下,各类型煤的混合可掺混25~40%,但最高不宜超过50%。
火电企业入厂入炉煤热值差的分析和对策

火电企业入厂入炉煤热值差的分析和对策摘要火电企业作为我国主要的能源消耗行业之一,煤炭作为其主要燃料,煤热值差的问题直接影响到火电企业的经济效益和环境污染。
本文分析了火电企业入厂入炉煤热值差的原因,并提出了相应的对策,从而提高火电企业的能源利用效率和减少环境污染。
1. 引言火电企业是我国能源消耗最大的行业之一,长期以来主要依赖煤炭作为燃料。
然而,煤炭资源的有限性和煤热值差问题给火电企业带来了许多困扰。
煤热值差指的是煤炭入厂和入炉之间的热值差异,其主要原因包括煤炭质量不均一和煤炭储存、运输过程中的能量损失等。
本文将对火电企业入厂入炉煤热值差的原因进行分析,并提出相应的对策。
2. 煤热值差的原因分析2.1 煤炭质量不均一煤炭的质量与其出产地、储存时间等因素有关,不同的煤炭质量对应不同的热值。
而火电企业采购的煤炭往往来源广泛,因此煤炭质量的不均一性导致了煤热值差的存在。
2.2 煤炭储存、运输过程中的能量损失煤炭在储存和运输过程中会存在能量损失的问题。
首先,煤炭在长时间堆放过程中容易受潮,导致煤炭的热值降低。
其次,在煤炭运输过程中,由于装卸、堆放等环节的能量损失,也会造成煤热值的下降。
3. 煤热值差的对策3.1 加强煤炭质量检测和管理为了降低煤热值差带来的影响,火电企业应加强对煤炭质量的检测和管理。
可以采用先进的煤质分析技术,进行煤质指标的测定,选择热值较高的煤炭进行采购,并建立完善的供应链管理体系。
3.2 优化煤炭储存和运输过程为了减少煤炭储存和运输过程中的能量损失,火电企业应采取有效的措施。
例如,加强煤炭的防潮处理,选择合适的储存方式,减少能量损失;在煤炭运输过程中,优化运输方案,减少装卸环节的时间和能量损失。
3.3 提高燃烧效率火电企业在燃煤过程中,可以通过改进燃烧技术,提高燃烧效率,从而减少煤热值差的影响。
例如,采用先进的燃烧设备,优化运行参数,提高煤炭的利用率,降低煤炭的热值损失,并减少环境排放。
火电企业入厂入炉煤热值差的分析和对策
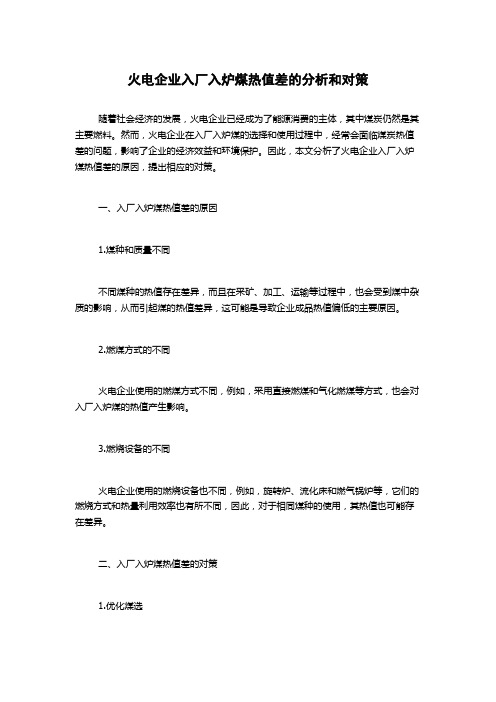
火电企业入厂入炉煤热值差的分析和对策
随着社会经济的发展,火电企业已经成为了能源消费的主体,其中煤炭仍然是其主要燃料。
然而,火电企业在入厂入炉煤的选择和使用过程中,经常会面临煤炭热值差的问题,影响了企业的经济效益和环境保护。
因此,本文分析了火电企业入厂入炉煤热值差的原因,提出相应的对策。
一、入厂入炉煤热值差的原因
1.煤种和质量不同
不同煤种的热值存在差异,而且在采矿、加工、运输等过程中,也会受到煤中杂质的影响,从而引起煤的热值差异,这可能是导致企业成品热值偏低的主要原因。
2.燃煤方式的不同
火电企业使用的燃煤方式不同,例如,采用直接燃煤和气化燃煤等方式,也会对入厂入炉煤的热值产生影响。
3.燃烧设备的不同
火电企业使用的燃烧设备也不同,例如,旋转炉、流化床和燃气锅炉等,它们的燃烧方式和热量利用效率也有所不同,因此,对于相同煤种的使用,其热值也可能存在差异。
二、入厂入炉煤热值差的对策
1.优化煤选
火电企业应该选择高质量煤炭,并且根据其热值、燃烧特性和企业燃烧设备的特点进行综合考虑,确保煤炭的质量符合要求,最大化热能的利用效率。
2.升级燃烧设备
可以通过对燃烧设备进行技术改进和升级,提高燃烧效率、减少能源损失,从而降低成品热值差的可能性。
3.加强烟气处理和减排
对烟气中的污染物进行有效处理和减排,减少能源消耗和资源浪费,发挥煤炭作为清洁能源的优势,保护环境和人民健康。
综上所述,火电企业入厂入炉煤热值差是一个需要引起重视的问题。
通过优化煤选、升级燃烧设备和加强烟气处理和减排等措施,可以最大程度地减少煤的热值差,提高产能利用率,提高企业经济效益,缩小资源浪费和环境污染。
入厂煤、入炉煤热值差的原因分析及解决措施

的数据。只有按机采设备性能试验给出的结论来运行机采设备 ,采 ( 1 ) 在 制 样过 程 中 ,由于 制 样设 备 或 工具 不 合格 ,或 制样 操 样 偏差 、制样 偏差才 能得 到有 效 的控制 。 2 . 规 范采 制化操 作 作 不 规 范 ,特 别 是 不 按煤 的最 大 粒 度 与 最小 保 留量 之 间 的关 系 留 样 。舍弃 部分 甚 至全部 予 以保 留的难破 碎 的样 品 ,导致 制样偏 差 。 ( 1 )由对 采制 化 流 程 熟悉 、标 准熟 悉 且 有 一 定技 术 的 人来 监
的采样 、制 样 、化验 工作 ,不 让入 厂煤 、人 炉煤 热值差 超 过考 核指 3 6 . 4 5 %,灰分 最 大 为6 0 . 8 9 % ,极 差为 2 4 . 4 4 %,煤 质非 常不 均 匀 。 标 。不 要有 了 问题再 去解 决 ,而是 防患 未然 。第 二如 果发 生 了入厂 对 于 这种 情 况 ,如 果 按 常 规采 样 而 不 增 加子 样 个 数 ,采 样 代 表 性 煤 、人 炉煤 热量 差 大的情 况 ,那就 要全 面 、系统 地 找出造 成热 值差 就差 。 大的根 本原 因 。 3 . 煤 长时 间存放 氧化 的影 响
来煤 在 车厢 底部 装约 3 0 c m 高左 右 的矸石 或劣 质煤 ,然 后再 在上 面装 质量 好 的煤 ,致使 采样 机所 采煤 样发 热量 偏高 。
7 . 入 炉煤 采样 设备 方 式的 影响
( 2)定期 检 查 破碎 机 的 出 料粒 度 ,定期 检 查 采样 头 和 缩 分器
二 、采制化偏差
要 从 ~批 煤 中采 取 少 量煤 样 ,经 过 制 样 程 序制 成 数 量 较 少 ,
据 资 料 统 计 ,无 烟 煤筒 仓存 放 半 年 热 量 损 失 1 % ,若 5 0 0 0 大
造成煤热值差原因及解决办法

造成煤热值差原因及解决办法一、前言发电厂入厂煤、入炉煤热量差是经济性评价及燃煤管理的重要指标,将其热量差控制在一定范围内可以体现出燃料管理和采制化工作的水平。
入厂煤、入炉煤热值差考核指标为502J/g。
在目前市场这种情况下,要完成这一指标,从管理和技术上难度都很大。
对均匀单一的煤种完成这一指标相对容易一些;对煤源复杂、煤量大,要完成这一指标有一定技术难度,必须从管理和技术上下很大功夫。
产生较大热量差的原因有多种因素,不一定是入厂煤或入炉煤的某一单方面的问题,也就是说可能是入厂煤的问题也可能是入炉煤的问题,或两方面都存在问题。
可以肯定是采样、制样、化验工作未做好,另外就是产生较大热量差时分析原因不到位。
为什么认为分析原因不到位呢?一般在分析原因时大多从煤样的采制和化验的规范性操作检查入手,检查这些操作环节方面固然重要,但往往只是分析了一些常规的、表面上的东西,缺乏对采制化工作操作细节、仪器设备性能方面的深层次的分析,其结果是热量差降低效果不明显或未起到作用。
解决发电厂入厂煤、入炉煤热量差,我们应从两方面来做这个工作。
第一重点放在预防上,通过平时扎实地做好入厂煤、入炉煤的采样、制样、化验工作,不让入厂煤、入炉煤热值差超过考核指标。
不要有了问题再去解决,而是防患未然。
第二如果发生了入厂煤、入炉煤热量差大的情况,那就要全面、系统地找出造成热值差大的根本原因。
二、采样、制样和化验偏差组成要从一批煤中(几千吨或上万吨)采取少量煤样(几百公斤),经过制样程序制成数量较少,仅约100克,粒度<0.2mm的试样,供化验使用,即用少量煤样(单次测定仅为1克左右的样)的分析结果去推断一批燃煤的质量和特性,就必然会存在偏差,这些偏差由采样偏差、制样偏差和分析偏差构成。
在此条件下,若用方差来表示总偏差,则有如下表达式:2总S=2采S+2制S+2分S。
其中采样偏差最大,占总偏差80%,制样偏差16%,分析偏差4%。
从以上分析结果可以看出,分析结果的可靠性,在很大程度上取决于样本的代表性,因此在煤质检测中,首先要做好采样工作,这说明不但要有科学的采样方法,而且还要有受过严格训练的、能认真执行采样方法的采样人员。
火力发电厂入厂入炉煤热值差计算及应用
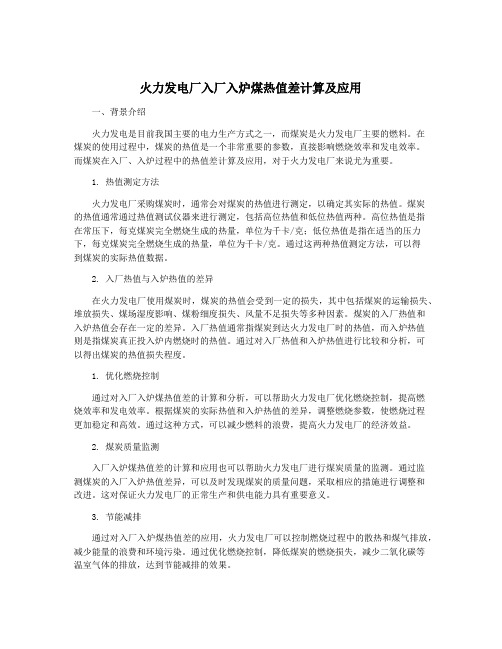
火力发电厂入厂入炉煤热值差计算及应用一、背景介绍火力发电是目前我国主要的电力生产方式之一,而煤炭是火力发电厂主要的燃料。
在煤炭的使用过程中,煤炭的热值是一个非常重要的参数,直接影响燃烧效率和发电效率。
而煤炭在入厂、入炉过程中的热值差计算及应用,对于火力发电厂来说尤为重要。
1. 热值测定方法火力发电厂采购煤炭时,通常会对煤炭的热值进行测定,以确定其实际的热值。
煤炭的热值通常通过热值测试仪器来进行测定,包括高位热值和低位热值两种。
高位热值是指在常压下,每克煤炭完全燃烧生成的热量,单位为千卡/克;低位热值是指在适当的压力下,每克煤炭完全燃烧生成的热量,单位为千卡/克。
通过这两种热值测定方法,可以得到煤炭的实际热值数据。
2. 入厂热值与入炉热值的差异在火力发电厂使用煤炭时,煤炭的热值会受到一定的损失,其中包括煤炭的运输损失、堆放损失、煤场湿度影响、煤粉细度损失、风量不足损失等多种因素。
煤炭的入厂热值和入炉热值会存在一定的差异。
入厂热值通常指煤炭到达火力发电厂时的热值,而入炉热值则是指煤炭真正投入炉内燃烧时的热值。
通过对入厂热值和入炉热值进行比较和分析,可以得出煤炭的热值损失程度。
1. 优化燃烧控制通过对入厂入炉煤热值差的计算和分析,可以帮助火力发电厂优化燃烧控制,提高燃烧效率和发电效率。
根据煤炭的实际热值和入炉热值的差异,调整燃烧参数,使燃烧过程更加稳定和高效。
通过这种方式,可以减少燃料的浪费,提高火力发电厂的经济效益。
2. 煤炭质量监测入厂入炉煤热值差的计算和应用也可以帮助火力发电厂进行煤炭质量的监测。
通过监测煤炭的入厂入炉热值差异,可以及时发现煤炭的质量问题,采取相应的措施进行调整和改进。
这对保证火力发电厂的正常生产和供电能力具有重要意义。
3. 节能减排通过对入厂入炉煤热值差的应用,火力发电厂可以控制燃烧过程中的散热和煤气排放,减少能量的浪费和环境污染。
通过优化燃烧控制,降低煤炭的燃烧损失,减少二氧化碳等温室气体的排放,达到节能减排的效果。
火电企业入厂煤与入炉煤热值差偏大的原因浅析
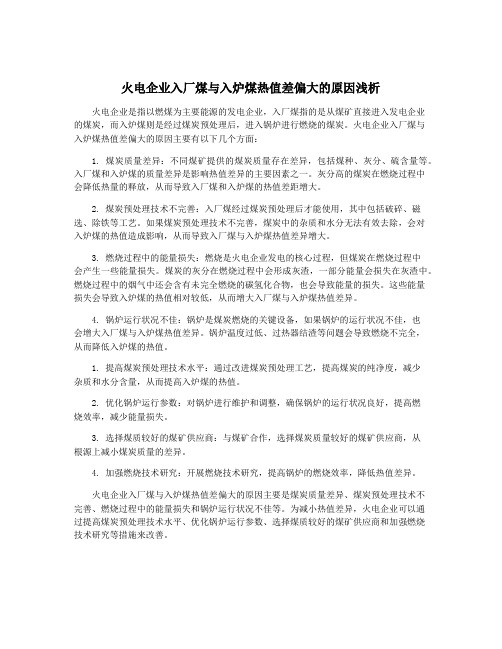
火电企业入厂煤与入炉煤热值差偏大的原因浅析火电企业是指以燃煤为主要能源的发电企业,入厂煤指的是从煤矿直接进入发电企业的煤炭,而入炉煤则是经过煤炭预处理后,进入锅炉进行燃烧的煤炭。
火电企业入厂煤与入炉煤热值差偏大的原因主要有以下几个方面:1. 煤炭质量差异:不同煤矿提供的煤炭质量存在差异,包括煤种、灰分、硫含量等。
入厂煤和入炉煤的质量差异是影响热值差异的主要因素之一。
灰分高的煤炭在燃烧过程中会降低热量的释放,从而导致入厂煤和入炉煤的热值差距增大。
2. 煤炭预处理技术不完善:入厂煤经过煤炭预处理后才能使用,其中包括破碎、磁选、除铁等工艺。
如果煤炭预处理技术不完善,煤炭中的杂质和水分无法有效去除,会对入炉煤的热值造成影响,从而导致入厂煤与入炉煤热值差异增大。
3. 燃烧过程中的能量损失:燃烧是火电企业发电的核心过程,但煤炭在燃烧过程中会产生一些能量损失。
煤炭的灰分在燃烧过程中会形成灰渣,一部分能量会损失在灰渣中。
燃烧过程中的烟气中还会含有未完全燃烧的碳氢化合物,也会导致能量的损失。
这些能量损失会导致入炉煤的热值相对较低,从而增大入厂煤与入炉煤热值差异。
4. 锅炉运行状况不佳:锅炉是煤炭燃烧的关键设备,如果锅炉的运行状况不佳,也会增大入厂煤与入炉煤热值差异。
锅炉温度过低、过热器结渣等问题会导致燃烧不完全,从而降低入炉煤的热值。
1. 提高煤炭预处理技术水平:通过改进煤炭预处理工艺,提高煤炭的纯净度,减少杂质和水分含量,从而提高入炉煤的热值。
2. 优化锅炉运行参数:对锅炉进行维护和调整,确保锅炉的运行状况良好,提高燃烧效率,减少能量损失。
3. 选择煤质较好的煤矿供应商:与煤矿合作,选择煤炭质量较好的煤矿供应商,从根源上减小煤炭质量的差异。
4. 加强燃烧技术研究:开展燃烧技术研究,提高锅炉的燃烧效率,降低热值差异。
火电企业入厂煤与入炉煤热值差偏大的原因主要是煤炭质量差异、煤炭预处理技术不完善、燃烧过程中的能量损失和锅炉运行状况不佳等。
入厂煤入炉煤热值差原因及分析方法
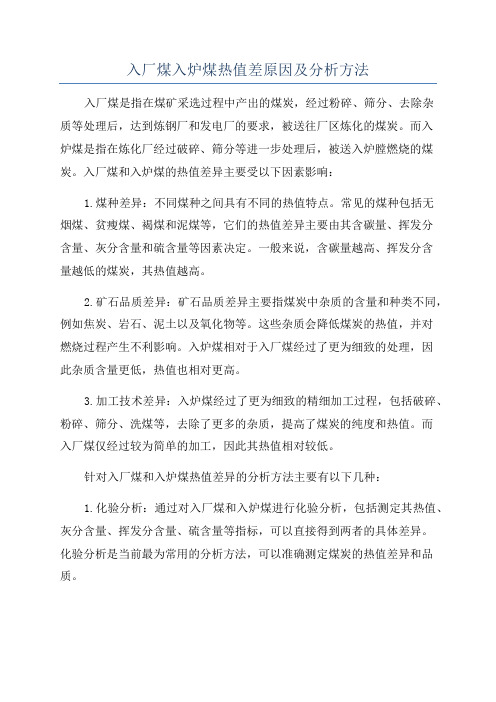
入厂煤入炉煤热值差原因及分析方法入厂煤是指在煤矿采选过程中产出的煤炭,经过粉碎、筛分、去除杂质等处理后,达到炼钢厂和发电厂的要求,被送往厂区炼化的煤炭。
而入炉煤是指在炼化厂经过破碎、筛分等进一步处理后,被送入炉膛燃烧的煤炭。
入厂煤和入炉煤的热值差异主要受以下因素影响:1.煤种差异:不同煤种之间具有不同的热值特点。
常见的煤种包括无烟煤、贫瘦煤、褐煤和泥煤等,它们的热值差异主要由其含碳量、挥发分含量、灰分含量和硫含量等因素决定。
一般来说,含碳量越高、挥发分含量越低的煤炭,其热值越高。
2.矿石品质差异:矿石品质差异主要指煤炭中杂质的含量和种类不同,例如焦炭、岩石、泥土以及氧化物等。
这些杂质会降低煤炭的热值,并对燃烧过程产生不利影响。
入炉煤相对于入厂煤经过了更为细致的处理,因此杂质含量更低,热值也相对更高。
3.加工技术差异:入炉煤经过了更为细致的精细加工过程,包括破碎、粉碎、筛分、洗煤等,去除了更多的杂质,提高了煤炭的纯度和热值。
而入厂煤仅经过较为简单的加工,因此其热值相对较低。
针对入厂煤和入炉煤热值差异的分析方法主要有以下几种:1.化验分析:通过对入厂煤和入炉煤进行化验分析,包括测定其热值、灰分含量、挥发分含量、硫含量等指标,可以直接得到两者的具体差异。
化验分析是当前最为常用的分析方法,可以准确测定煤炭的热值差异和品质。
2.燃烧试验:通过对入厂煤和入炉煤进行燃烧试验,观察其燃烧特性和产生的热量,可以间接得出两者的热值差异。
燃烧试验可以模拟真实的燃烧情况,对于研究煤炭的燃烧特性和性能差异有着重要意义。
3.化学分析:通过对入厂煤和入炉煤的化学成分进行分析,包括各种元素含量和化学组成,可以推测其热值差异的原因。
化学分析可以深入了解煤炭的组成和结构,从而进一步分析煤炭的燃烧特性和性能。
综上所述,入厂煤和入炉煤的热值差异主要由煤种差异、矿石品质差异和加工技术差异等因素决定。
通过化验分析、燃烧试验和化学分析等方法,可以对两者的热值差异进行分析和比较,为炼钢厂和发电厂选择适合的煤炭提供科学依据。
- 1、下载文档前请自行甄别文档内容的完整性,平台不提供额外的编辑、内容补充、找答案等附加服务。
- 2、"仅部分预览"的文档,不可在线预览部分如存在完整性等问题,可反馈申请退款(可完整预览的文档不适用该条件!)。
- 3、如文档侵犯您的权益,请联系客服反馈,我们会尽快为您处理(人工客服工作时间:9:00-18:30)。
案例:厂煤、入炉煤热值差统计分析入厂煤与入炉煤热值差是火电厂十分关注的问题之一,它是发电集团或者电厂管理部门实施燃料考核的重要指标。
将其热量差控制在一定范围内可以体现出燃料管理和采制化工作的水平。
由于各种因素影响,造成某些电厂人炉煤的发热量比人厂煤偏低较多,因此有必要对造成人厂煤与人炉煤发热量差异偏大的原因进行分析,提出解决问题办法。
1、关于入厂煤、入炉煤热值差概念1)、所谓入厂煤、入炉煤热值差是指针对同一煤源对象,在一段时期内,入厂煤和入炉煤的收到基低位发热量在同一全水分下的差值。
2)、目前,各大发电集团执行的入厂煤与入炉煤热值差考核指标一般为502J/g(0.50MJ/kg,120卡/克,再现性300j/g,72cal/g))以内。
在目前市场情况下,要完成这一指标,无论从管理和技术上难度都很大。
3)、产生较大热值差的原因有多方面,可能是入厂煤的问题,也可能是入炉煤的问题,或两方面都存在问题。
可以肯定是采样、制样、化验工作未做好,另外就是产生较大热量差时分析原因不到位。
4)、解决电厂入厂煤、入炉煤热量差,应从两方面做起:一方面重点放在预防上,通过平时扎实地做好入厂煤、入炉煤的采制化工作管理,要防患于未然,不要等有了问题再去解决,;第二如果发现了热值差超标,那就要全面、系统地找出超标原因。
2、关于热值差计算下面以年度为核算单位计算入厂煤与入炉煤的热值差。
某电厂2008年入厂煤与入炉煤质量统计表3、计算热值差将入炉煤收到基低位发热量折算到入厂煤全水分下的热值4、产生入厂煤、入炉煤热值差的原因引起入厂煤与入炉煤热值差的原因很多,下面分别加以讨论。
1)入厂煤与入炉煤燃用不同步计算对象不一致性产生热值差2) 煤长时间存放产生的热值差各种煤存放6个月后发热量的下降见下表。
3)煤炭的不均匀性易产生的热值差4).采制化人员不规范操作带来的热值差5)、入厂煤与入炉煤采样方法等不同造成的的代表性不同产生的热值差6)、计算与统计方法的不合理性产生的热值差入厂煤与入炉煤的热值差以收到基低位发热量表示。
实验室实测的弹筒发热量,首先转换成高位发热量,再进一步换算成低位发热量。
其计算公式如下:例如,某电厂入厂煤煤样如果煤样全水分取11.2%,其它常数都不变,那么其低位热值为关于热值差统计与考核方法,建议以月度、季度为统计单位,考核以半年、全年为考核期限,这样更能反映实际的煤场管理水平。
4、降低热值差应采取的措施和对策1 )制定衡量入厂煤与入炉煤热值差的标准。
该标准包括以下内容:(1)明确一个固定的、时间较长的热值差比较周期:(2)研究不同煤种、不同存储时间热值损失与修正公式:(3)制定适合可行的比较试验操作规程。
2).加强煤场管理。
减少存煤热值损失。
这是降低入厂煤与入炉煤热值差的主要措施之一。
3 )制定有效的入厂煤验收管理办法,防止对掺杂掺假,以次充好的煤入厂.减小入厂煤检验误差。
4)规范人工取制样的标准和方法,强化人工取样工作制度.减少人为因素影响,确保煤质化验的真实可靠。
特别是煤质不稳定的电厂,采样尤为重要。
煤样越不均匀,采样越重要。
应先从规范入炉煤采制样工作开始。
如果将入炉煤采制样工作先规范化,以其为基准来比较热量差,就容易查出问题所在。
例某厂化验室的化验的数据如下:同一煤样入厂煤、入炉煤分别制样并化验的结果。
由第三方制样,然后缩分出两份煤粉样,分别由入厂、入炉煤化验室化验。
入厂煤化验室热量测定值比实际高930J,入炉煤化验室热量测定值比实际值低185J。
看出,入厂、入炉煤化验室化验第三方制样的煤样热量结果非常接近,对标准煤样发热量测定结果也在标准值的允许范围内,证明两化验室化验的数据是可靠的。
但入厂煤化验室测定自己制样的煤样发热量偏离实际值较大,说明入厂煤制样存在问题。
5、入厂煤、入炉煤热值差分析方法分析时应由浅入深、由易到难、逐一排除,最后找出问题所在。
对于较大的热量差,可以肯定不是化验为主要问题,应先从制样开始分析,然后再分析采样问题1热量计准确度、热量检验当热量差稍微超规定值时,应首先排除化验方面是否有问题。
热量计准确度检查可以使用在有效期内的标准煤样,不推荐使用标准苯甲酸。
热量计的标定记录及反标记录检查主要是了解设备性能及系统偏差情况。
2、人工制样偏倚检查分析人工制样如果不按标准操作也可产生较大的误差。
熟悉采制化标准的技术人员,可通过对制样人员的现场实际操作,检查制样人员规范操作的程度。
3.采样偏倚检查分析对于人工采样首先应澄清一个认识问题,不是人工采样不准或代表性差的问题,而是一方面采样人员没按照规范操作,另外一方面入厂来煤存在掺假或分层装车现象,此条件下人工采不到车底部的煤,从而造成人工采样代表。
4采样、化验设备偏倚检查1、入厂煤、入炉煤热值差*所谓入厂煤、入炉煤热值差是指针对同一煤源对象,在一段时期内,入厂煤和入炉煤的收到基低位发热量在同一全水分下的差值。
2、产生入厂煤、入炉煤热值差的原因*。
1)入厂煤与入炉煤燃用不同步计算对象不一致性产生热值差。
2) 煤长时间存放产生热值差。
3)煤炭的不均匀性易产生热值差。
4)采制化人员不规范操作带来的热值差。
5)入厂煤与入炉煤采样方法等不同造成的的代表性不同产生的热值差。
6)计算与统计方法的不合理性产生的热值差。
A发电公司能耗专项评估分析报告一、问题2005年1-5月供电煤耗指标大幅度上升。
1-5月公司累计完成供电煤耗424.22g/kWh,同比上升38.57g/kWh。
二、煤耗大幅度上升的主要原因1、今年因发电量较同期少发23370万千瓦时,综合厂用电率同比上升0.61%,使供电煤耗上升 5.54g/kWh,多耗用原煤 2.23万吨。
2、非生产耗能今年1-5月累计扣除供热因素影响耗煤21636吨,去年同期仅扣除8269吨,今年较去年同期多扣除1.34万吨。
3、评估组反平衡计算2004年1-5月供电煤耗累计值为399g/kWh,评估组认为该煤耗水平基本符合机组实际情况。
而公司2004年1-5月份统计上报供电煤耗累计值385.65g/kWh,存在人为压低现象,影响煤耗上升13.35g/kWh,以致帐面存量增加,引起煤场亏损5.37万吨,煤场亏损对今年煤耗大幅度升高有较大影响。
4 、燃料管理影响供电煤耗上升19.68g/kwh,多耗用原煤7.92万吨供电煤耗大幅度上升原因具体分析1、运行指标影响供电煤耗上升5.54g/kWh对公司05年1-5月份与04年同期的20项小指标进行了对比分析(汽轮机指标、厂用电率采用耗差分析法)结果如下:2、燃料管理对供电煤耗的影响煤耗上升19.68g/kwh燃料管理影响供电煤耗上升19.68g/kwh,多耗用原煤7.92万吨,是05年1-5月供电煤耗上升幅度较大的主要原因。
表现为:(1)2004年末,财务帐面存煤126924吨,而燃管中心帐存煤为60335吨,煤场亏损66589吨,至今未作处理,因此煤场继续出现亏损的可能性存在。
(2入厂煤的热值存在虚高现象,从而影响煤耗升高。
(见下表)来分析:锅炉燃烧工况一致,影响锅炉效率一致,相同的热值、相同的煤量应发出相同的电量,但05年2月实际发电量较去年同期下降很多,而耗用煤量反而增加,由此05年入厂煤热值有虚高现象。
05年2月入厂煤热值较同期入厂煤热值高81kcal/kg,而入厂煤直上量今年2月较去年同期多29427吨,但发电量比去年同期减少11033万kwh。
附表:三、结论综上引起能耗大幅度上升的主要原因:1、领导对能耗管理不够重视表现在:一是对集团公司下达的能耗考核指标:供电煤耗383g/kWh、综合厂用电率8.8%没有按计划分解,分月控制,也没有具体的保证措施;二是对目前供电煤耗和厂用电远远高于集团公司下达的考核指标,没有及时组织综合分析,找出影响能耗大幅度升高的真实原因,更没有具体的解决措施;三是能耗管理上职能部门界面不清晰,责任不明确,分析不及时,措施不具体,考核不到位等。
2、整体能耗管理水平低下,个别环节问题比较突出燃料管理只注重煤耗和入厂、入炉煤热值差两个指标,忽视全过程管理;数据统计人为调整,煤耗计算不准确,以致出现入厂、入炉煤热值差和供电煤耗值大起大落,根本不能反映机组的实际煤耗水平;非生产用能计量装置不全,无法核实真实的供热、供电负荷;运行指标管理粗放,很多经济指标长期偏离设计值和规定值,没有组织研究解决,使得机组运行经济性较差。
四、有待改进的地方及建议建议一事实依据:煤耗计算数据混乱,不能反映机组真实煤耗水平1、煤耗计算原始数据采用混乱计算煤耗数据源有三个,分别是燃管中心月统计耗煤量、皮带秤月累计用煤量、生产早报累计上煤量。
2005年1月采用皮带秤计量耗煤量379976吨,2005年2月采用燃管中心上报耗煤量309429吨,2005年5月采用生产早报累计上煤量329538吨。
2、计算入炉煤量人为调整2004年7月燃管中心上报耗煤量为335710吨,而计算煤耗所用入炉煤量为319710吨,人为调整16000吨;2004年8月燃管中心上报耗煤量为373934吨,而计算煤耗所用入炉煤量为328934吨,人为调整45000吨;2004年11月燃管中心上报耗煤量为393592吨,而计算煤耗所用入炉煤量为377592吨,人为调整16000吨;2005年5月生产早报耗煤量为329538吨,而计算煤耗所用入炉煤量为319538吨,人为调整10000吨。
3、入炉煤热值不是实际检测值,而是按照入厂煤热值减去人为调整数确定入炉煤热值2004年1~2月在入厂煤热值上减去120kcal/kg,3~6月在入厂煤热值上减去110kcal/kg,10月在入厂煤热值上减去410kcal/kg, 2005年2月在入厂煤热值上减去318kcal/kg,3~5月在入厂煤热值上减去120kcal/kg。
原因分析:1、煤耗指标管理概念不清,只关注煤耗指标的最终数据,不重视对影响煤耗各个环节的过程管理。
对集团公司燃料管理制度执行不力,对煤耗管理没有明确一个职能部门归口负责,煤耗管理的相关部门职责不清,当煤耗出现不正常波动时,没有管理部门和责任人进行全面分析,查找原因,制定相应的整改和防范措施,而是随意调整数据。
2、入炉煤没有采样装置,无法对入炉煤质量进行检验,造成了入炉煤热值人为调整确定,同时也不能对入厂煤质量进行核对监督。
3、对皮带秤管理长期不重视,以致于皮带秤1995年安装,至今不能正常运行,无法对入炉煤量用计量装置进行统计。
改进建议:1、公司领导应从思想上高度重视能耗的过程管理,严格执行集团公司燃料管理的有关规定。
建立完善的入炉煤计量及采、制、化管理制度,明确煤耗归口管理部门及相关部门职责,建立煤耗分析管理制度,定期进行发、供电煤耗的正、反平衡验证,对不正常的煤耗波动保持高度的警觉,及时组织分析、查找原因,限期制定措施、加以解决,确保入厂煤和入炉煤热值差的真实性。