拉延模设计
拉延模具毕业设计

拉延模具毕业设计拉延模具毕业设计在现代工业生产中,模具被广泛应用于各个领域,其中拉延模具是一种常见且重要的模具类型。
本文将探讨拉延模具的设计和应用,以及其在毕业设计中的潜在价值。
一、拉延模具的概述拉延模具是一种用于金属材料成型的工具,其主要功能是通过拉伸和挤压金属材料,使其形成所需的形状和尺寸。
拉延模具通常由上模和下模组成,上模和下模之间的空间形状决定了最终产品的形状。
拉延模具的设计需要考虑材料的性质、形状的复杂程度以及生产效率等因素。
二、拉延模具的设计要点1. 材料选择:在拉延模具的设计中,材料的选择至关重要。
模具需要具备足够的硬度和强度,以承受拉伸和挤压过程中的高压力和摩擦力。
常见的模具材料包括工具钢、硬质合金等。
2. 模具结构:拉延模具的结构设计应考虑到产品的形状和尺寸,以及生产效率的要求。
模具的结构应合理布局,以便于操作和维护。
同时,模具的结构还需要考虑到产品的材料流动性,以确保产品成型的质量和精度。
3. 润滑和冷却系统:在拉延模具的设计中,润滑和冷却系统的设置是非常重要的。
润滑系统可以减少模具与金属材料之间的摩擦力,提高产品的表面质量。
冷却系统则可以有效地降低模具的温度,延长模具的使用寿命。
三、拉延模具在毕业设计中的应用拉延模具在毕业设计中具有广泛的应用价值。
一方面,通过设计和制造拉延模具,可以提高学生对模具设计和制造的理论和实践能力的培养。
学生可以通过研究和分析不同材料的性质,选择合适的材料,并进行模具结构的设计和优化。
此外,学生还可以通过实际操作,了解模具制造的流程和技术要点。
另一方面,通过毕业设计中的拉延模具应用,学生可以将所学的理论知识应用于实际生产中。
他们可以通过与企业合作,了解实际生产的需求和挑战,并在设计和制造过程中解决实际问题。
这种实践经验将为学生的职业发展提供宝贵的资本,并增强他们在工业界的竞争力。
四、拉延模具设计的挑战和前景虽然拉延模具设计具有广泛的应用前景,但也面临一些挑战。
拉延模的设计

拉延模的设计第一章、综述第一节、拉延模的概念拉延模是在压床的作用下,通过凸模、压边圈、凹模的联合作用使平板状坯料经过塑性变形获得稳定的空间形状的一种工艺装备第二节、拉延模的种类根据使用设备的不同,拉延模可分为单动拉延模和双动拉延模;单动拉延模:(两种类型的图形上下模都反了)单动拉延模是利用机床的气垫机构进行压料,靠凸模和凹模进行成形。
其特点是结构较简单,模具安装较方便。
双动拉延模:双动拉延模是利用机床外滑块机构压料,靠凸模和凹模进行成形。
其特点是四角的压料力可分别调整,但模具安装、调整较费时间,现采用较少。
以下仅对单动拉延模结构加以介绍单动拉延模可分为以下多种形式:1、按下模铸造结构特点分:分体,整体;2、按压边圈与凸模的导向形式特点分:内导向,外导向;3、按制件形状特点分:沿形,不沿形;(何时出现?如很少见可不介绍。
)4、按凸模轮廓线封闭与否分:开口,闭口;详见拉延模设计规范第三节、拉延模的设计要点一、根据制件的大小、形状、受力情况确定采用哪种形式的结构二、确定数模中心、压床中心、模具中心三者之间的关系,尽量使三心重合三、确定压边圈的行程四、确定气垫顶杆的数量、位置以及长度1、充分分析工艺要求,了解制件的产品部分和工艺补充部分,确定拉延是否必须镦实,以及冲压方向、送料方向、料厚及方向等。
2、建立模具中心、数模中心、压床中心之间的关系,尽量使三心重合。
3、分析拉延所需行程,确定压边圈工作行程。
4、气垫顶杆布置。
5、其它结构设计。
第二章、单动拉延模的设计第一节、单动拉延模的基本结构基本结构简图第二节、单动拉延模的行程计算一、压料行程1、定义:当压料面为曲面时,从凹模接触板料到被凹模与压边圈固定住,上模在垂直方向运动的距离。
(当制件比较大或者拉延深度较深时)当压料面起伏较大时(如行李箱盖板),压料过程中如果不对板料加以约束,将会影响坯料定位。
(压料行程的确定对于板料的定位有着决定性作用。
)2、计算方法:根据模具的实际情况,按照理想状态估计压料行程再加上5-10的余量即可(加10〜20较好,对行李箱盖还应在挡料机构上对坯料约束如对坯料运动过程分析后,将挡料板做斜度,或做摆动结构等)二、拉延工作行程1、定义:从压边圈与凹模压住板料开始直至拉延工序完成,上模在垂直方向运动的距离。
拉延模设计顺序标准
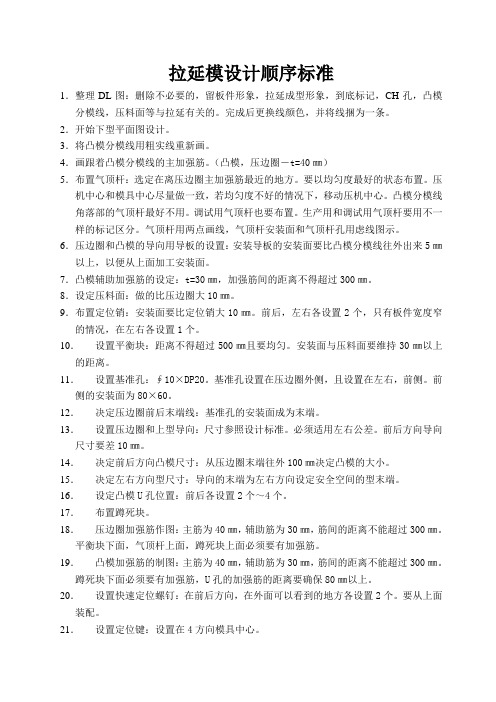
拉延模设计顺序标准1.整理DL图:删除不必要的,留板件形象,拉延成型形象,到底标记,CH孔,凸模分模线,压料面等与拉延有关的。
完成后更换线颜色,并将线捆为一条。
2.开始下型平面图设计。
3.将凸模分模线用粗实线重新画。
4.画跟着凸模分模线的主加强筋。
(凸模,压边圈-t=40㎜)5.布置气顶杆:选定在离压边圈主加强筋最近的地方。
要以均匀度最好的状态布置。
压机中心和模具中心尽量做一致,若均匀度不好的情况下,移动压机中心。
凸模分模线角落部的气顶杆最好不用。
调试用气顶杆也要布置。
生产用和调试用气顶杆要用不一样的标记区分。
气顶杆用两点画线,气顶杆安装面和气顶杆孔用虑线图示。
6.压边圈和凸模的导向用导板的设置:安装导板的安装面要比凸模分模线往外出来5㎜以上,以便从上面加工安装面。
7.凸模辅助加强筋的设定:t=30㎜,加强筋间的距离不得超过300㎜。
8.设定压料面:做的比压边圈大10㎜。
9.布置定位销:安装面要比定位销大10㎜。
前后,左右各设置2个,只有板件宽度窄的情况,在左右各设置1个。
10.设置平衡块:距离不得超过500㎜且要均匀。
安装面与压料面要维持30㎜以上的距离。
11.设置基准孔:∮10×DP20。
基准孔设置在压边圈外侧,且设置在左右,前侧。
前侧的安装面为80×60。
12.决定压边圈前后末端线:基准孔的安装面成为末端。
13.设置压边圈和上型导向:尺寸参照设计标准。
必须适用左右公差。
前后方向导向尺寸要差10㎜。
14.决定前后方向凸模尺寸:从压边圈末端往外100㎜决定凸模的大小。
15.决定左右方向型尺寸:导向的末端为左右方向设定安全空间的型末端。
16.设定凸模U孔位置:前后各设置2个~4个。
17.布置蹲死块。
18.压边圈加强筋作图:主筋为40㎜,辅助筋为30㎜,筋间的距离不能超过300㎜。
平衡块下面,气顶杆上面,蹲死块上面必须要有加强筋。
19.凸模加强筋的制图:主筋为40㎜,辅助筋为30㎜,筋间的距离不能超过300㎜。
拉延模设计手册

拉延模设计手册一、拉延模的分类拉延模分双动拉延模与单动拉延模两类1、双动拉延模是在专用的双动压力机上生产的拉延模,通常上模为凸模,下模为凹模,压边圈安装在压机的外滑块上,其结构如下图,此种结构拉延模压边力较为稳定,但由于需要专用的压机,安装较为烦琐,且结构尺寸较大,现在已经运用的越来越少。
2、单动拉延模是在单动压机上生产的拉延模,通常上模是凹模,下模是凸模,压边圈由下气垫或其它压力源(例于氮气弹簧)提供压料力,其结构如下图,由于模具通用性好,现大部分拉延模为此种结构。
工作台下模上模压边圈上模垫板内滑块外滑块下模上模工作台压边圈上滑块二、拉延模的主要零件(主要为单动拉延模)拉延模一般有上模、下模、压边圈三大部件组成(根据结构的不同要求,可能增加一此部件,例于局部的小压料板),以及安装这三大部件上的其它功能零件,主要有以下零件:1、导向零件:耐磨板、导向腿,导柱;2、限位调压零件:平衡块、到底块;3、坯料定位零件:定位具、气动定位具;4、安全装置:卸料螺钉(等向套筒,也起锁付的作有)、安全护板;5、拉延功能零件:到底印记、弹顶销、通气管、CH孔合件;6、取送料辅助零件:辅助送出料杆、打料装置。
三、单动拉延模的设计(一)模具中心的确认与顶杆的分布模具中心的确认通常依据顶杆的布置的需要设定。
一般在工艺设计时,会按钣件的中心确定一个数模中心。
顶杆的分布需尽量靠近分模线,并均匀布,通常两根顶杆之间最多空一个顶杆位,顶杆数量要尽可能多。
在模具设计时首先以数模中心与压机工作台中心重合,如顶杆分布满足上述要求,则以数模中心做为模具中心。
如无法满足上述要求,侧在需要更改的方向上移动(最大1/2顶杆间距),确认一个最优化的方案,同时以工作台的中心做为模具的中心。
(注:在试模压力机与工作压力机顶杆孔不致时,需设置试模顶杆,并在优先保证生产顶杆的要求下,优化顶杆部置)模具中心与数模中心重合如厂家要求使用顶杆以外的压力源,例于氮气弹簧等,则一般直接以数模中心做为模具中心,压力源沿分模线均匀分布,并需确认压力源的大小是否足够。
第四章 拉延模设计3-导向

凸模—压边圈 (导板) 0.05±0.022 凹模—压边圈 (导板) 0.05±0.02 注单动和双动拉 延同此要求;含 切角工序内容时, 按剪切类标准。
拉延模导向
端头结构设计
中间导向腿
中小型模具
A B 135 135 155 B′ 180 180 180 C 150 150 200 D 100 100 100 D1 110 110 110 E 100 100 125 J 50 50 50 K 40 40 40 M 60 60 60 d 50 50 50
类别 Ⅳ Ⅴ Ⅵ Ⅶ Ⅷ
A 450 700 1000 1200 1500
拉延模导向
端头结构设计
角部导向腿
拉延模导向
端头结构设计
角部导向腿
拉延模导向
端头结构设计
类别 Ⅰ Ⅱ Ⅲ Ⅳ Ⅴ Ⅵ Ⅶ Ⅷ
角部导向腿
R 55 55 55 60 60 70 70 70 B 135 135 135 160 160 185 185 185 B′ 195 195 195 205 205 225 225 225 C 100 100 100 125 125 150 150 150 D 120 120 120 140 140 180 180 180 D1 110 110 110 120 120 140 140 140 E 100 100 100 125 125 150 150 150 J 50 50 50 50 50 60 60 60 K 40 40 40 40 40 50 50 50 M 60 60 60 70 70 90 90 90 d 50 50 50 60 60 80 80 80
拉延模设计讲解
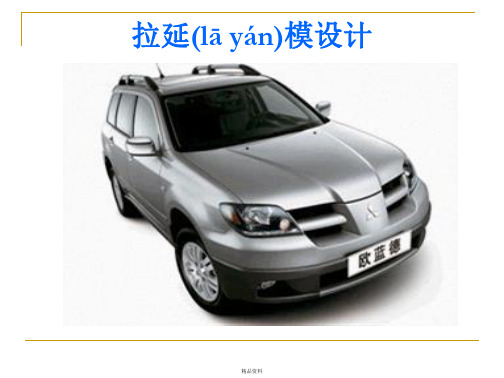
精品资料
4.下模座 (一)肋条 根据模仁肋条、贴模垫块以及顶杆逃孔来适当地分布肋条。 (二)U沟 U沟为模具安装在压力机上的部位(bùwèi)。铸件结构的U沟 设计尺寸为: 图中L1=40mm,L2=50mm。
选取。当采用铸入式吊耳时,应注意吊耳高度不能太低,以便于装卸吊索。吊耳 周围的肉厚也不应太少,否则强度不够。
精品资料
(四)快速定位 快速定位为模具在压力机上定位而设,其位置(wèi zhi)要根据机台
(上模)、压料板三个主要(zhǔyào)工作部分组成。
精品资料
拉延模的各部分因材质(cái zhì)及热处理等要求不同其结构可分为以下几种 形式(常用)
一.整体式
整体式常用于 小型模具(mújù),将 下横仁与下模 座做成一体, 使模具(mújù)加工制 造方便。
二.组合式
组合式常用于
大中型模具, 将下模仁与下 模座分开,降 低模具的材料
拉延(lā yán)模设计
精品资料
一.基本知识
1.汽车覆盖件的特点 汽车覆盖件钣金模具是指生产汽车钣金覆盖件用的冷冲压模
具. 汽车覆盖件按其材质的不同,所处部件及功能的不同,可以进
行以下(yǐxià)区分 :
精品资料
覆盖件和一般冲压件相比较,具有材料薄、形状复杂、多为空间曲面、结构尺寸大和 表面质量高等特点。
精品资料
(六)2D面逃料 如左下图所示,该面需要进行跑2D加工,因
此需要对其进行逃料处理(chǔlǐ)。如右下图所示 结构,一般取①=50mm,②=10mm。
-拉延模设计
(如图一)
(2)切口处形面低于周围形面,但高度差小于提前切入量 时,下模块形面高出安装处形面,但不应高于周围形面, 上模切口模块也高出形面并保证提前切入量。 (如图二)
上模与压边圈的导向设计
• 上模座与压边圈是通过导腿导向的,只
是用来导正压边圈与上模的,与压边圈 和凸模的导向无直接的联系。
•在导板的高度选取上要参 考模具的压料行程,一般导 板要先模具压料前导入 50mm。
•导板安装在导腿和压边圈 上时,要考虑加工刀具的大 小、安装面是否能加工。
七、拉延模各辅助结构部件的设计
• 安全区的设计: 一般情况下,安全区都 设计在下模座和上模座 上,这时压边圈就需要 做出相应的避让,一般 每边10mm;但有些时候, 下安全区设计在压边圈 上,分布在压边圈的四 角,尺寸为150x150mm, 在模具闭合时与上安全 区的距离为110mm。
2.下模座的完善
• 压板槽、快速定位的
设计 依据机床平面图确定 压板槽和快速定位顶 杆的具体位置,具体 见《模具设计规范》
• 起吊、翻转的设计
• 一般在下模座的前后方向(相对送料方向)各设计2
处标准起重棒,规格根据下模座的重量确定;如有特 殊要求,起重棒也可设计在下模座的左右2端。无论 是哪种情况,下模座的翻转均可通过所设计的起重棒 来实现。
注意:下模座的起重装置要按可以承载3套模具的规格来 选取。
• 定位键槽,V形中心线的设计
• 并考虑调整垫块、定位板、卸料螺钉、气垫顶
杆等都合理的布置完成后
• 合理的减轻:为了节约成本、提高强度、美观模具,
需要对压边圈进行合理的减轻,使之成为一个协调、 牢固的框架结构,减轻原则如下:
2.拉延模设计规范
目录1 拉延模的类型....................................................22 下平面图标注内容................................................43 上平面图 ....................................................174 剖视图........................................................255 尺寸标注与标准件选用规范........................................266 铸件结构.....................................................267 拉延筋 ......................................................298 拉延凸模轮廓的确定............................................319 拉延件坯料尺寸的确定...........................................3210 拉延工艺缺口...................................................3311 拉延模的材料....................................................3512 拉延件对拉延模的特殊要求........................................361 拉延模的类型拉延模送料面线的高度及结构形式,是根据冲压设备情况由用户提出的。
拉延模的闭合高度一般取650-1000mm。
送料面线的高度一般取500-700mm,必须保证压边圈有足够的强度,使操作者能够方便的进行上下料操作,所以送料面高度取在闭合高度中心偏上100-200mm。
第四章 拉延模设计2-结构
n
单动拉延模
典型结构
第十一章 拉延模设计
11-1 拉延模典型结构
1.
n
单动拉延模
典型结构
4-5 拉延模结构
n
双动拉延模典型结构
1一凸模固定板 2一压边圈 3一防磨板 4一凸模 5一凹模 6一隐 式定位器 7一毛坯导向装置 8一送料用辊式滑槽 9 一前定位装 置 10一提升器
第十一章 拉延模设计
共通要素
n
研模用基准孔结构(CH孔)
是拉延时在拉延件废料处冲出的孔,因为拉延时或
多或少会产生型面回弹,或者圆角打大的情况。这 样下序就可以用拉延时冲出的孔作基准对修边或其 它后序模具进行型面打磨,以使拉延件与模具贴合。 这些孔在模具打配完成后要去掉的。即拔掉拉延时 CH的冲头。
4-5 拉延模结构
凹模结构
n
装配式凹模
4-5 拉延模结构
凹模结构
n
装配式凹模
4-5 拉延模结构
凹模结构
n
镶拼式凹模(窄而深的拉延)
4-5 拉延模结构
凸模结构
第十一章 拉延模设计
11-2 拉延模工作零件 导向板
4-5 拉延模结构
n
共通要素
凹模入口圆角一般取R凹=(6-10)×t。
4-5 拉延模结构
4-5拉延模结构
n
共通要素
调压垫布置
调压垫的许用承压力:φ60-(20吨);φ80-(40吨)。 承压力一般为80吨-400吨。 调压垫一般每400mm-500mm一块,调压垫的对应位置应 有立筋。 若手工取件,调压垫上平面应低于压料面。
第十一章 拉延模设计
《拉延模结构设计》PPT课件
(2)还要考虑下模的整体强度及
起重装置(吊耳,起重棒等)
18
的空间
可整理ppt
气顶接柱接触面积〉 3/4(接柱整园面积)即可
19
可整理ppt
6.确定压料芯限程及坯料送料定位装置
确定压料芯限程 (1)一般采用退料螺钉限程, 外导向盒式导向模具多用限程板。 (2)限程距离=压料芯行程 +(10mm-20mm) (3)一般选用4个布在受力平衡的四角
流水孔一般为直径40的圆孔,设在模具型腔底部,并要保证 液体能流到模具外侧。
检查干涉,做出躲空。
25
可整理ppt
实体设计完成
26
可整理ppt
工艺更改可能对拉延模结构造成的影响
分模线更改 影响气顶的布置,凸模及压边圈支撑筋的位置,镦死垫的位置, 凸模及压边圈导板的大小及位置等
坯料线更改 影响压边圈及凹模压料面的大小,制件定位位置,调压垫的位置
(2)用坯料线外偏10-20MM确定压边圈 工作部分的轮廓(同凹模做法)
(3)确定刃口高度
刃口高度
50
压料面为二维曲面是高度一般为50MM
压料面为三维曲面是高度一般为60MM
(4)做出受力筋
11
可整理ppt
压边圈工作 部分
12
可整理ppt
3.布置调整垫块及镦死垫块
调整垫块布置(压边圈) (1)300MM-400MM均布 (2)调整垫块安装台的位置 距离压料面至少30MM (3)手动线时尽量保证垫块 的上表面在坯料面以下
拉延模压边圈行程〉制件拉延后最大落差+10mm
气顶数量=压边力/单个气顶所受力(3T-4T)+安全个数(0-4)
气顶位置的布置 (1)保证气顶均布在分模线外侧并尽量接近分模线 (2)尽量保证300MM均布 (3)尽量保证受力平衡
- 1、下载文档前请自行甄别文档内容的完整性,平台不提供额外的编辑、内容补充、找答案等附加服务。
- 2、"仅部分预览"的文档,不可在线预览部分如存在完整性等问题,可反馈申请退款(可完整预览的文档不适用该条件!)。
- 3、如文档侵犯您的权益,请联系客服反馈,我们会尽快为您处理(人工客服工作时间:9:00-18:30)。
5.上模座
(一)模面 如同压板模面,将素材线往外偏20mm得到模面。 (二)肋条 根据分模线、平衡块来布主肋、副肋。 (三)漏水孔与窥视孔 漏水孔作用为:清洗模具时,使上模能方便的排水。如左下图所 示。窥视孔为当采用箱跟导引时,为了方便测量箱跟导引与耐磨板间 的间隙,在耐磨板上方开个孔以方便测量。该孔尺寸为40X50。
外部工艺补充——压料面
压料面是指板料在凹模圆角以外的法兰部分,工件本体部分或工 艺补充部分组成,其应是平面或曲率较小的曲面,不允许有大的起伏 或拐点在拉延成型过程中,压料面的材料被逐渐拉入凹模型腔内,转 化为覆盖件形状。压料面与凸模形状保持一定几何关系,保证在拉延 过程中板料处于张紧状态,并能平稳地包拢凸模,防止起皱破裂。
3.模仁
(一)2D面 如同压板,模仁的2D面也需要逃料,其尺寸为: ①=50mm,②=10mm。
(二)肋条 分模线内偏10mm布主肋,再布副肋,并保证型面肉厚有60mm。
(三)定位元件 当模仁采用组合式时,模仁需要准确的定位在模座上。一般采用 键定位。键一般设置 3处,键的长度为60mm,宽度视模仁大小而定。 (四)锁付 模仁的锁付有正锁和反锁两种。中小模仁锁付用正锁,大模仁用 反锁。正锁为螺栓锁付承面在模仁外侧,螺纹孔打在下模座上,螺栓 由下模座的正面锁入。反锁则相反,锁付承面在模仁内侧,螺纹孔打 在模仁的锁付面上,螺栓由下模座的底面锁入。采用正锁时,应注意 锁付承面的打螺丝空间,承面不能太小,一般为分模线往外偏70mm 左右。 (五)起吊、翻转 模仁设计时应考虑到起吊与翻转的操作。一般起吊孔可以在螺 栓锁付承面上打出。翻转可在模仁侧壁上补上四个平台,以打翻转螺 丝孔,或在模仁侧壁上装铸入螺母,翻转应在同一水平面上。
2.对覆盖件的要求
覆盖件表面不允许波纹、皱纹、凹痕、边缘拉痕、擦伤以及其他 破坏表面完美的缺陷。覆盖件上的装饰棱线、装饰筋条要求清晰、平 滑、左右对称以及过渡均匀。覆盖件之间的装饰棱线衔接外应吻合, 不允许参差不齐。表面上一些微小缺陷都会在涂漆后引起光的漫反射 而损坏外观。 覆盖件一般需要经过落料、拉延、冲孔修边、翻边、整形等多道 工序才能完成。覆盖件的工艺性关键在于拉延的可能性和可靠性,即 拉延的工艺性。覆盖件一般都是一道工序拉延。为了实现拉延或造成 良好的拉延条件,将翻展开,窗口补满再加添工艺补充部分构成一个 拉延件。工艺补充是拉延件不可缺少的组成部分,是指为了顺利拉延 成型出合格的制件,而在冲压件的基础上所添加的那部分材料,用以 满足拉延、压料面和修边等工序的要求。这部分材料仅仅是冲压成型 需要而不是零件所需要的,故在拉延成型后的修边工序中需将工艺补 充切除掉。 工艺补充部分有两大类:外部工艺补充、内部工艺补充。
(六)2D面逃料 如左下图所示,该面需要进行跑2D加工,因此需要对其进行逃 料处理。如右下图所示结构,一般取①=50mm,②=10mm。
2D面
(七)布肋条 分模线往外偏10mm布主肋,根据平衡块,顶杆的位置布副肋。 肋条间距以250-300mm为佳。周肋肋厚为50mm。 (八)吊耳 压板的起吊、翻转装置一般采用铸入式吊耳。如左下图所示结 构。吊耳的大小根据模具的重量来决定,模具重量初估可根据公式: W=长(mm)X宽(mm)X高(mm)X7.8(g/cm3)X0.4 在根据设计标准来选择相应的大小。
C/H销
到底标记
6.其他部位设计
(一)修模孔 修模孔是作为模具加工的基准孔。在下模座、压板、上模座都应做出, 各设置3处(1处在F侧),一般放置于床台中心,如果无法在床台中 心做出,应放置在与床台中心距离成50mm的倍数的位置上。如下图 所示,其台面大小40X80,孔径φ16×20mm深。
进料支架 退料支架
素材定位器是为了使钣料能准确的定位在模具上,素材定位器的 布置也应该视钣件的大小来分布,一般当钣件的侧边较长时,该边应 分布2个且间距应尽量大点,同时定位器的顶面应在同一平面上。为 方便现场调试定位器,定位器承面应超过素材线3-5mm。同时在上 模应做出定位逃孔,以免干涉。
素材定位器
上模与压板的导向方式有箱跟导板导向和外导板导向。箱跟导板 导向形式如下图:
当拉延模需要装突破刀,且突破形式为剪切突破时,因有切边, 要求有更高的导向精度,因此需要使用导柱与导套来导向,此时上模 与压板的导向形式为导板+导柱导向,如下图:
当上模与压板导向采用外导板导向时,其形式如下左图,此时应 做出假导柱(如下右图),加工时以假导柱为基准,再加工导向面。 设计时,假导柱应用透明色组入。
三. 拉延模设计
1.拉延模的导向形式
பைடு நூலகம்拉延模的导向根据不同的分模线形状、模具的功能、拉延的行程、 模具的大小等,可进行不同的选择。 下模与压板的导向方式根据分模线形式,拉延的行程,模具的大 小可分为内导和外导:
两种导引方式的选用及优缺点: 1.一般拉延行程比较大或模具比较大的时候会选用外导方式,行程 比较小的时候会选用内导方式。 2.外导方式的模具平稳性比较好,但是模具会比较大。 3.内导方式的模具比较小.但是平稳性不是很好。
二.拉延模介绍
1.拉延变形过程
拉延质量
拉延过程中的主要缺陷是起皱和拉裂。起皱是拉深时由于较大的 切向压应力使板料失稳造成的,起皱是拉深工艺产生废品的主要原因 之一,正常的拉深工艺中是不允许的。常采用压边圈(压料板)压住 周边凸缘部分材料来防止起皱。 拉裂一般出现在直壁与底部的过渡圆角处。拉深时材料各部分厚 度都发生变化,而且变化是不均匀的。而直壁与底部过渡圆角部分材 料在整个拉深中一直受到拉应力作用,造成此处变薄最大,当拉应力 超过材料的抗拉强度时,此处将被拉裂。
①
②
③ 耐磨板组立尺寸
(四)分布顶杆 压板顶杆应根据压力机的顶杆位置来布置,顶杆应尽可能设计 于形状面之下方(靠近P/F线)且必须有肋支撑,顶杆之相邻间距约以 300最佳,顶杆设置位置应考虑压板作动时之整体平衡性。 (五)分布平衡块 凡拉延或成型之模具必须设计平衡块,两平衡块相邻之间距以小 于500为最佳,一般300-500之间。平衡块之位置必须有肋支撑,使 成型压力能与上模、压板,下模间透过肋传至生产设备之床台上。平 衡块下方必须设计贴模垫块,以利合模作业及试模与生产之调整,厚 度、大小与平衡块一致。原则上平衡块设计组立于压板上,且高度低 于压板型面10mm以上,以利于生产作业性。平衡块应量靠近模面 (30-40mm)。为了模具的生产调试,平衡块下应垫0.5mm的垫片。
一.整体式 整体式常用于 小型模具,将 下横仁与下模 座做成一体, 使模具加工制 造方便。
二.组合式 组合式常用于 大中型模具, 将下模仁与下 模座分开,降 低模具的材料 成本。
三.镶钢块情况 当钣件的厚度t≥1.2,或钣件为高强度板,或者钣件拉延深度 大(段差大于100)时,为了防止钣件起皱或拉裂,应对模具上模、 压板或模仁进行局部或全局地镶钢块处理(视具体情况而定)。其示 例图如下:
(四)快速定位 快速定位为模具在压力机上定位而设,其位置要根据机台上的 压力销而定,我厂的快速定位标准为: 注:1.设置位置以各工程 生产用机械之压力销孔位 置为准。 2.制作形式参照左图所示。 3.设置尽量于明显处,方 便模具安装。 4.仅设置于下模机械后侧。 5.R值及D值均以压力梢直 径为准。 6.若客户有提供设计标准, 以客户要求为准。
3.汽车钣金模具分类
按模具的功能不同主要可分为
翻边模
4.工程名称
名称 (中文) 下料 拉延 剪边 切边 分离 冲孔 折边 整形 成形 翻边孔 包边压平 凸点 剪缝 印记 斜楔 工程定义及性质 将材料与毛料分离,得到平的零件或用于后加工 将材料施以抽制加工,其边缘以压边压住 制品之边缘废料作剪切加工 将材料非成型部分切除加工 将平的、弯的或空心的毛料分成两部分或数部分 制品之冲孔加工 制品边缘作加工 将前工程之拉伸或成形件再作出正确尺寸加工 材料在上模与下模间施以形状凹凸的加工 通过连续材料拉伸,将在材料上折成凸缘 在零件折边后再折边加工 改变零件厚度,在表面上得到凹凸纹路 材料非成品部分切开加工 将前工程之形状再次加工打印 用于材料的侧冲也,侧修,侧整等 工作简图 名称(英文) BIANKING DRAW TRIM CUT SEPARATE PIERCE FLANGE RESTRIKE FORM BUURING HEMMING EHBOSS SLIT MARK CAM 略记号 BL DR TR CUT SEP PRC(PI) FL RST FO BUR HEM EHB SLIT MAK CAM
拉延模设计
一.基本知识
1.汽车覆盖件的特点
汽车覆盖件钣金模具是指生产汽车钣金覆盖件用的冷冲压模具. 汽车覆盖件按其材质的不同,所处部件及功能的不同,可以进行以 下区分 :
覆盖件和一般冲压件相比较,具有材料薄、形状复杂、多为空间 曲面、结构尺寸大和表面质量高等特点。 覆盖件按作用和要求可分为三类:外覆盖件、内覆盖件和骨架件。
假导 柱
2.压板
(一)压板高度的确定 当压板与下模的导引方式为外导向时,可根据给定的模高,均匀 分布压板、上下模的高度。 当压板与下模的导引方式为内导向时,压板高度的计算公式为:
压板行程: 压板行程应保证压板在随顶杆顶高时,板料放在压板面上 时不能与模仁型面有所接触,应留有10mm左右的空间。 (二)确定模具大小 将素材线往外偏20确定模面大小,再往外偏110得到压板大小。 (三)分布导引耐磨板
2.拉延模类型
拉延模按动作类型可分为:单动拉延模和双动拉延模
单动拉延 模
双动拉延模
3.拉延模的结构
由于我司拉延模大多采用单动拉延,因此这里主要介绍单动拉 延模的结构。 拉延模的主要结构是由凸模(下模)、凹模(上模)、压料板
三个主要工作部分组成。
拉延模的各部分因材质及热处理等要求不同其结构可分为以下几 种形式(常用)
(四)到底标记与C/H销 到底标记是为了验证一些成形类模具,如拉伸、成形、整形类模 具是否达到成形所需要的深度而设定的。一般在凹模上,在板件最终 接触点(凹部)组装。C/H销是为了了解在试模过程中模具的定位情 况而设立的,设计时根据工法图所给的位置来布置。C/H销装在上模, 相对应的在模仁上应开C/H孔(孔径φ8×20mm深)。