压铸开题报告模板
罩壳压铸模 开题报告

国内外研究现状:
如今压铸已成为最先进的金属成型方法之一。近年来我国在压铸模设计、制造方面均有明显提高,能满足汽车行业部分需求及基本上满足摩托车、家电、电机、仪表、轻工等行业的需要。但是我国的压铸模存在使用寿命偏短,可靠性较差以及在压铸模的设计和制造方面进展较为缓慢,目前仍主要依靠设计人员的经验进行等缺陷。
3.按学校论文文本标准编写毕业设计说明书(8000字以上),翻译3000字以:表中一至六栏由学生填写
[5]赖华清主编.压铸工艺及模具.机械工业出版社,2005.
[6]械设计手册编写组.机械设计手册(1~5册).[M] 北京:机械工业出版社,1998.
七、指导教师意见:
1..按论文设计题目要求,查阅搜集、使用相关资料设计手册等,进行毕业设计;
2.绘制模具装配图、型芯及镶块等重要零件图,至少完成3张零号图的工作量;
发展趋势:
现代压铸模具的主要发展趋势是向精密、复杂、大型模具方向发展,缩短模具的制造周期,提高模具的加工质量,努力延长压铸模使用寿命,降低生产成本,提高产品竞争力。
三、本课题研究内容:
1、研究目标:
在指导老师的指导下,设计出一套结构简单、制造精度高的上盖压铸模具。
2、研究内容:
(1)、对压铸件进行工艺性分析,并绘制产品毛坯图。
(3)、根据有关模具的知识,设计模具总装图方案。
(4)、比较方案,最后确定方案。
(5)、绘制总装图和零件图。
(6)、成型零件的造型设计。
(7)、编制技术说明书。
五、主要特色及工作进度:
起止时间:2010 年 11 月 1 日至 2011 年 5 月 20 日
序号
工作内容
起止日期
备注
压铸模设计开题报告

压铸模设计开题报告压铸模设计开题报告一、引言压铸是一种常见的金属加工方法,通过将熔融金属注入压铸模中,使其在模具中凝固成型。
压铸模具的设计是压铸工艺中至关重要的一环,直接影响产品质量和生产效率。
本开题报告旨在探讨压铸模设计的关键问题和挑战,并提出解决方案。
二、研究背景随着工业技术的不断发展,压铸模具设计面临着新的挑战。
首先,客户对产品外观和尺寸的要求越来越高,要求产品表面光洁度高、无瑕疵。
其次,新材料的出现使得压铸模具需要适应更多种类的金属合金。
此外,快速生产和高效率也成为了压铸模设计的重要指标。
三、研究目标本研究的目标是设计一种高效、精确的压铸模具,以满足客户对产品质量和生产效率的要求。
具体目标如下:1. 提高产品表面质量,减少缺陷和瑕疵;2. 适应不同金属合金的压铸需求;3. 提高生产效率,缩短生产周期。
四、研究方法为了实现以上目标,本研究将采用以下方法:1. 基于CAD软件进行压铸模具的三维设计,通过仿真分析模具的流动性和充型性能,优化模具结构;2. 通过实验测试不同金属合金的熔点、流动性等物理特性,为模具设计提供准确的参数;3. 基于模具设计和物理特性的数据分析,提出改进方案和优化建议。
五、预期结果通过上述研究方法,我们预期可以达到以下结果:1. 设计出一种结构合理、流动性良好的压铸模具,提高产品表面质量;2. 提供针对不同金属合金的压铸模具设计方案,满足不同客户的需求;3. 通过优化模具结构和流动性,提高生产效率,降低生产成本。
六、研究意义压铸模具的设计对于提高产品质量和生产效率具有重要意义。
本研究的成果将为压铸模具设计提供新的思路和方法,为相关行业的发展做出贡献。
同时,研究过程中所积累的知识和经验也将为压铸模具设计的进一步研究提供参考。
七、研究计划本研究计划分为以下几个阶段:1. 文献调研阶段:对压铸模具设计的相关文献进行综述,了解当前研究状况和存在的问题;2. 数据收集阶段:通过实验测试和模具设计软件,收集相关的数据和参数;3. 模具设计阶段:基于收集到的数据和参数,进行压铸模具的三维设计;4. 仿真分析阶段:利用CAD软件进行模具的流动性和充型性能仿真分析;5. 优化改进阶段:根据仿真分析结果,对模具结构进行优化改进;6. 结果评估阶段:对优化后的模具进行实验测试,评估其性能和效果;7. 结果分析和总结阶段:对实验结果进行统计分析,总结研究成果并撰写论文。
铝合金压铸件压力铸造成形数值模拟研究的开题报告
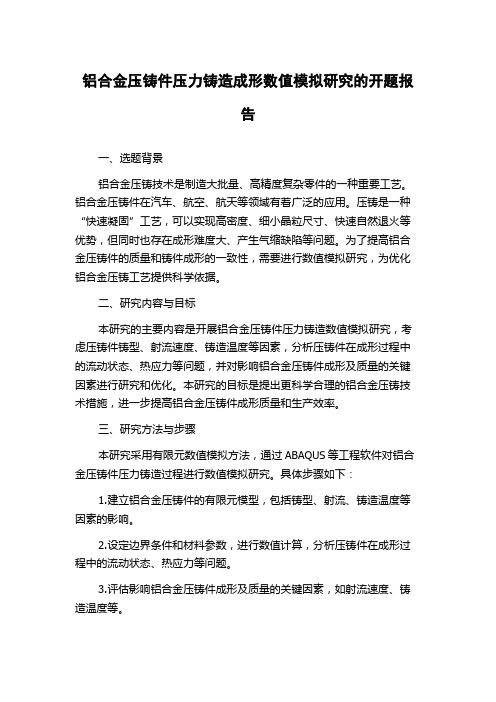
铝合金压铸件压力铸造成形数值模拟研究的开题报告一、选题背景铝合金压铸技术是制造大批量、高精度复杂零件的一种重要工艺。
铝合金压铸件在汽车、航空、航天等领域有着广泛的应用。
压铸是一种“快速凝固”工艺,可以实现高密度、细小晶粒尺寸、快速自然退火等优势,但同时也存在成形难度大、产生气缩缺陷等问题。
为了提高铝合金压铸件的质量和铸件成形的一致性,需要进行数值模拟研究,为优化铝合金压铸工艺提供科学依据。
二、研究内容与目标本研究的主要内容是开展铝合金压铸件压力铸造数值模拟研究,考虑压铸件铸型、射流速度、铸造温度等因素,分析压铸件在成形过程中的流动状态、热应力等问题,并对影响铝合金压铸件成形及质量的关键因素进行研究和优化。
本研究的目标是提出更科学合理的铝合金压铸技术措施,进一步提高铝合金压铸件成形质量和生产效率。
三、研究方法与步骤本研究采用有限元数值模拟方法,通过ABAQUS等工程软件对铝合金压铸件压力铸造过程进行数值模拟研究。
具体步骤如下:1.建立铝合金压铸件的有限元模型,包括铸型、射流、铸造温度等因素的影响。
2.设定边界条件和材料参数,进行数值计算,分析压铸件在成形过程中的流动状态、热应力等问题。
3.评估影响铝合金压铸件成形及质量的关键因素,如射流速度、铸造温度等。
4.通过调整关键因素,优化铝合金压铸技术措施,提高铸件质量和生产效率。
四、研究意义与预期结果本研究将对铝合金压铸件的生产提供科学的数值模拟方法和技术措施,有助于改进铝合金压铸工艺,进一步提高铝合金压铸件的成形质量和生产效率,推动铝合金压铸技术的发展。
预期结果为提出一些优化铝合金压铸工艺的方案和指导,以推动压铸业的均衡、可持续的发展。
压铸开题报告

压铸开题报告一、研究背景压铸是一种广泛应用于工业制造过程中的金属成形方法,其通过将熔融金属注入到预制模具中,等待其凝固后取出,从而得到所需的铸件。
由于其高效、精确和成本低等优点,压铸在各个行业中得到了广泛的应用。
然而,由于压铸过程中存在一些问题,如缺陷产生、模具磨损等,导致铸件质量无法达到预期的要求。
因此,本文将围绕压铸过程中存在的问题展开研究,并基于现有的技术手段,提出解决这些问题的方法和方案,旨在提高铸件质量和生产效率。
二、研究目的本文的主要研究目的如下:1.分析压铸过程中可能存在的问题和缺陷,如气孔、翘曲等;2.基于现有的技术手段,提出改善压铸质量的解决方案;3.设计和制作相应的实验模具,对改善效果进行验证;4.分析改善方案的可行性和经济性,为实际生产提供参考。
三、研究内容本文将按照以下步骤进行研究:1.调研分析:通过文献综述和实地调研,了解当前压铸过程中常见的问题和缺陷情况,如气孔、翘曲等;2.技术对比:对比不同的压铸技术,分析其优缺点,选择适合本研究的技术手段;3.解决方案设计:基于现有的技术手段,提出改善压铸质量的解决方案,如调整压铸参数、改进模具结构等;4.实验验证:设计和制作相应的实验模具,对改善方案进行实际验证,记录和分析实验数据;5.方案评估:分析改善方案的可行性和经济性,评估其对于提高铸件质量和生产效率的影响;6.结果总结:总结研究结果,对研究过程中的问题和不足进行讨论,并提出进一步的研究方向。
四、研究意义本文的研究成果对于改善压铸质量和提高生产效率具有重要意义。
通过深入分析压铸过程中的问题和缺陷,提出相应的解决方案,并进行实验验证和评估,将有助于优化生产流程,降低制造成本。
同时,本文的研究成果也可以为压铸技术的进一步发展提供理论和实践指导。
五、研究计划本文的研究计划如下:•第一阶段:调研和分析–完成对压铸相关文献的综述和分析,了解当前压铸过程中的问题和需求;–进行实地调研,了解实际生产中存在的压铸问题和改善方案;•第二阶段:技术对比和方案设计–对比不同的压铸技术,选择适合本研究的技术手段;–基于选择的技术手段,设计改善压铸质量的解决方案;•第三阶段:实验验证和结果分析–设计和制作实验模具,对改善方案进行实际验证;–记录和分析实验数据,评估改善方案的效果;•第四阶段:方案评估和总结–分析改善方案的可行性和经济性,评估其对生产效率的影响;–总结研究结果,讨论研究中的问题和不足,并提出进一步研究的方向。
镁合金压铸充型过程的计算机模拟及在工程上的应用的开题报告
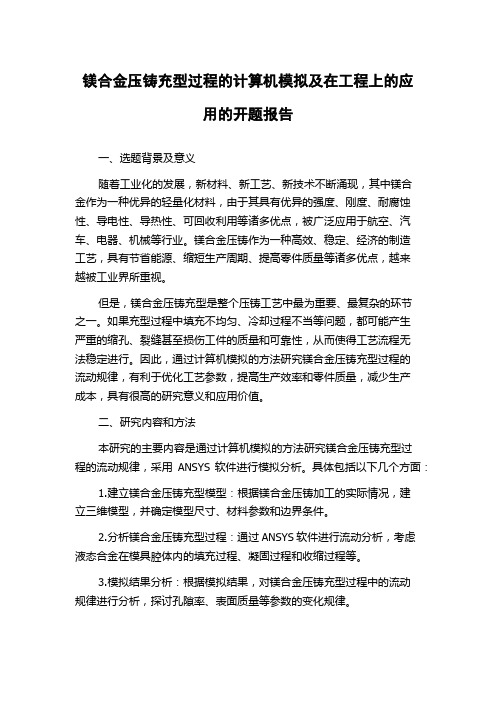
镁合金压铸充型过程的计算机模拟及在工程上的应用的开题报告一、选题背景及意义随着工业化的发展,新材料、新工艺、新技术不断涌现,其中镁合金作为一种优异的轻量化材料,由于其具有优异的强度、刚度、耐腐蚀性、导电性、导热性、可回收利用等诸多优点,被广泛应用于航空、汽车、电器、机械等行业。
镁合金压铸作为一种高效、稳定、经济的制造工艺,具有节省能源、缩短生产周期、提高零件质量等诸多优点,越来越被工业界所重视。
但是,镁合金压铸充型是整个压铸工艺中最为重要、最复杂的环节之一。
如果充型过程中填充不均匀、冷却过程不当等问题,都可能产生严重的缩孔、裂缝甚至损伤工件的质量和可靠性,从而使得工艺流程无法稳定进行。
因此,通过计算机模拟的方法研究镁合金压铸充型过程的流动规律,有利于优化工艺参数,提高生产效率和零件质量,减少生产成本,具有很高的研究意义和应用价值。
二、研究内容和方法本研究的主要内容是通过计算机模拟的方法研究镁合金压铸充型过程的流动规律,采用ANSYS软件进行模拟分析。
具体包括以下几个方面:1.建立镁合金压铸充型模型:根据镁合金压铸加工的实际情况,建立三维模型,并确定模型尺寸、材料参数和边界条件。
2.分析镁合金压铸充型过程:通过ANSYS软件进行流动分析,考虑液态合金在模具腔体内的填充过程、凝固过程和收缩过程等。
3.模拟结果分析:根据模拟结果,对镁合金压铸充型过程中的流动规律进行分析,探讨孔隙率、表面质量等参数的变化规律。
4.工程应用:根据模拟结果和分析,优化工艺参数,提高生产效率和零件质量,对于改善镁合金压铸工艺的稳定性和可靠性具有重要价值。
三、预期研究成果通过本研究,预期可以得到以下的成果:1.建立镁合金压铸充型过程的计算机模拟模型,得到流动规律在随时间、位置变化的情况下的空间分布,掌握流动规律的变化趋势。
2.采用模拟结果,研究充型过程对于镁合金零件内部缺陷的产生的影响, 包括孔隙率、毛刺、裂纹、收缩等。
3.通过模拟结果分析和工程应用,得出优化和改善镁合金压铸充型工艺的建议,避免在工程应用中的批量生产时出现缺陷,提高零件的可靠性和质量。
压铸开题报告

压铸开题报告压铸开题报告一、引言压铸是一种重要的金属加工方法,广泛应用于汽车、航空航天、电子、家电等行业。
本文旨在研究压铸技术的原理、应用和发展趋势,以期为相关行业提供参考和指导。
二、压铸技术的原理压铸是通过将熔融金属注入金属模具中,经过压力作用下形成所需形状的工艺过程。
其原理主要包括:1. 金属熔化:将金属材料加热至熔化点,使其变为液态。
2. 注射:将熔融金属注入金属模具中,填充整个模腔。
3. 压力保持:在注射完成后,保持一定的压力,以确保金属充分凝固。
4. 开模:待金属冷却凝固后,打开模具,取出成品。
三、压铸技术的应用压铸技术在各个行业有着广泛的应用,主要体现在以下几个方面:1. 汽车行业:压铸技术广泛应用于汽车零部件的制造,如发动机缸盖、曲轴箱等。
2. 电子行业:压铸技术用于生产电子产品的外壳,如手机、电视机等。
3. 家电行业:压铸技术在家电制造中起到了重要作用,如冰箱、洗衣机等。
4. 航空航天行业:压铸技术在航空航天领域中用于制造各种复杂形状的零部件。
四、压铸技术的发展趋势随着科技的进步和工业的发展,压铸技术也在不断演进和改进。
以下是压铸技术的一些发展趋势:1. 自动化程度提高:随着自动化技术的不断发展,压铸设备越来越多地实现了自动化操作,提高了生产效率和产品质量。
2. 材料的创新应用:新型材料的出现为压铸技术带来了新的发展机遇,如高强度铝合金、镁合金等。
3. 精密化和高效化:随着模具制造技术的进步,压铸件的尺寸精度和表面质量得到了显著提高,同时生产效率也得到了大幅度的提升。
4. 环保节能:压铸技术在材料利用率、能源消耗等方面的改进,使其更加环保节能,符合可持续发展的要求。
五、结论压铸技术作为一种重要的金属加工方法,在工业生产中具有广泛的应用前景。
通过对压铸技术的原理、应用和发展趋势的研究,我们可以更好地理解和应用这一技术,为相关行业的发展提供支持和指导。
随着科技的不断进步,压铸技术将不断创新和发展,为各个行业的发展带来更多的机遇和挑战。
XX—开题报告
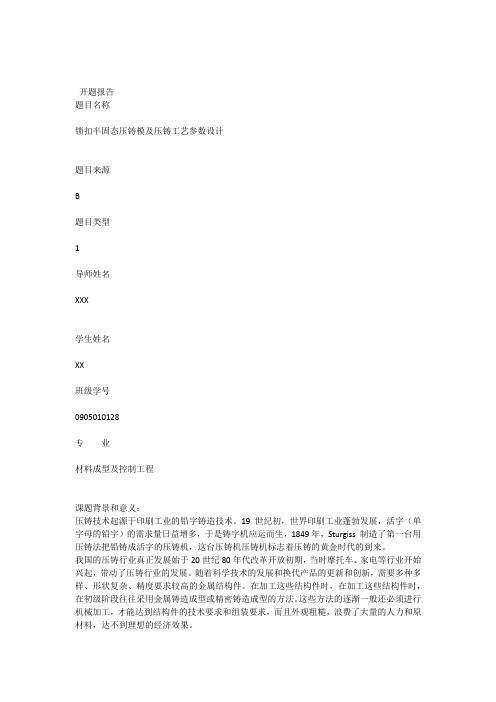
开题报告题目名称锁扣半固态压铸模及压铸工艺参数设计题目来源B题目类型1导师姓名XXX学生姓名XX班级学号0905010128专业材料成型及控制工程课题背景和意义:压铸技术起源于印刷工业的铅字铸造技术。
19世纪初,世界印刷工业蓬勃发展,活字(单字母的铅字)的需求量日益增多,于是铸字机应运而生,1849年,Sturgiss 制造了第一台用压铸法把铅铸成活字的压铸机,这台压铸机压铸机标志着压铸的黄金时代的到来。
我国的压铸行业真正发展始于20世纪80年代改革开放初期,当时摩托车、家电等行业开始兴起,带动了压铸行业的发展。
随着科学技术的发展和换代产品的更新和创新,需要多种多样、形状复杂、精度要求较高的金属结构件。
在加工这些结构件时,在加工这些结构件时,在初级阶段往往采用金属铸造成型或精密铸造成型的方法。
这些方法的逐渐一般还必须进行机械加工,才能达到结构件的技术要求和组装要求,而且外观粗糙,浪费了大量的人力和原材料,达不到理想的经济效果。
而压铸工艺具有以下优点:1.铸件的尺寸精度高,表面质量好;2.可以生产出形状复杂、轮廓清晰、深腔薄壁的压铸件;3.压铸件组织致密,具有较高的强度和硬度;4.才俩奥利用率高;5.生产效率高,以实现机械化和自动化生产;6.经济效益好。
由于金属压铸成型有不可比拟的突出优点,在工业技术快速发展的时代,必须得到越来越广泛的应用。
特别是在大批量的生产中,虽然模具成本高一些,但总的来说,其生产的综合成本却得到大幅度降低。
泵体类铝合金压铸件常出现表面质量差和模具寿命短等问题。
针对由于模具开裂引起铸件粗糙度超差,“粥样”花纹、“细小麻点”等铸件表面质量问题,若采取合理安排内浇道、增加倒角、调整自动喷涂机及更换脱模剂等解决措施,结果可以使铸造表面达到了密封面的粗糙度要求,免除了机加工,并且延长了模具使用寿命,降低了产品的生产成本。
国内、外研究现状:近几十年来,为了能生产出高强度、高密闭性、可焊接、可热处理、可扭曲等各种高要求的压铸件,在国外,除了真空压铸以外,有发展了挤压铸造和半固态压铸等闲的技术,并加以概括的称之为“高密实压铸法”,于是与之配套的新的压铸机机种也随即诞生。
压铸开题报告

2011.5.30~2011.6.10编写毕业设计论文,准备答辩。
参考文献:
[1]毛卫民.半固态金属成形技术.化学工业出版社.2004.(5)
[2]潘志勇.半固态铸造工艺简介.湖南工业职业技术学院学报.2006.6.(4)
[3]毛卫民,陈军.半固态合金流变铸造的研究进展.特种铸造及有色合金.2004.(2)
半固态金属铸造成形克服了传统铸造成形易产生的缩孔、缩松、气孔及尺寸偏差等缺点,具有成形温度低,延长模具寿命,节约能源,改善生产条件和环境,提高铸件质量 (减少气孔和凝固收缩),减少加工余量等许多优点[2]。半固态金属成形工艺将成为21世纪极具发展前途的近净成形技术之一[3]。本课题针对此问题,对壳体件的半固态压铸进行工艺以及工装设计。
课题研究方案:
明确毕业设计目的、意义及研究内容;查阅相关文献资料;完成开题报告;了解铸件结构特点进行工艺设计及计算;进行工装设计,绘制装配图及各个零件图。
日程安排:
2011.3.7~2011.4.1查阅相关资料、学习相关知识、明确毕业设计目的及内容;完成开题报告;
2011.4.4~2011.4.29读懂零件图,进行工艺设计及计算;
题目来源: A、自拟课题;B、民用科研课题;C、国防科研课题;(选A、B、C)。
开题报告内容使用宋体小四字号。(新工艺、新装置、新技术、新产品)
培训主题
培训地点
培训日期
课时
主办部门
主讲人
培训人数
培训主要内容
1.新工艺、新装置、新技术、新产品的特性;
2.工艺技术要求、注意事项;
3.存在的风险及防范措施;
4.工艺规程、设备、岗位安全操作规程及事故应急处理;
- 1、下载文档前请自行甄别文档内容的完整性,平台不提供额外的编辑、内容补充、找答案等附加服务。
- 2、"仅部分预览"的文档,不可在线预览部分如存在完整性等问题,可反馈申请退款(可完整预览的文档不适用该条件!)。
- 3、如文档侵犯您的权益,请联系客服反馈,我们会尽快为您处理(人工客服工作时间:9:00-18:30)。
[16]Masashi Uchida. Development of vacuum die-casting process[J]. China Foundry,2009,(02):137-144.
[17]. Opportunities and challenges of Chinese die-casting market[J]. China Foundry,2004,(01):23-27.
课题类型:
(1)A—工程实践型;B—理论研究型;C—科研装置研制型;D—计算机软件型;
E—综合应用型
(2)X—真实课题;Y—模拟课题;
(1)、(2)均要填,如AY、BX等。
2
1.查阅中英文资料,其中中文不少于15篇,英文不少于3篇。
2.翻译一篇相关的英文资料(不少于3000字符)。
3.计算机绘制铸件产品图,包括二维和三维图。
结合设计资料进行参数校核计算成型零部件尺寸,对模具的结构设计和计算,从而设计出整套压铸模具,并绘制模具总装图。
进度安排,共6周
第一周:分析零件结构工艺性,确定成型工艺和成型方案。
第二周:画出模具总装草图
第三周:选择压铸机并进行参数校核,对成型零部件尺寸进行计算。
第四周:模具结构计算
第五周:绘制模具总装图和零件图
模具生产是非常重要的工艺环节,其使用性能的好坏、寿命的高低,直接影响着一个企业产品的质量,更新换代的速度,以及经济效益和产品的市场竞争力。现代模具行业是技术、资金密集型的行业。近年来,我国模具行业结构调整步伐加快,主要表现为大型、精密、复杂长寿命模具和模具标准件发展速度高于行业的总体发展速度,塑料模和压铸模比例增大,面向市场的专业模具厂家数量及能力增加较快。随着经济体制改革的不断深入,“三资”及民营企业的发展很快。据国家统计局统计,截止2006年底,中国模具制造业规模以上企业1314家,从业人员244155人;全年完成总产值亿元,实现销售收入和利润分别为亿元、亿元;出口10亿美元,进口亿美元。如果加上未统计的小型模具企业,估计我国现有的模具生产厂超过20000家,总从业人员50万人左右。生产压铸模具的企业,一般兼做其他模具,但模具生产企业,不都生产压铸模。由于压铸模生产的复杂性,这些企业中只有一部分企业能生产压铸模。
[18]Lost Cores for High-Pressure Die. Jelínek Archives of Foundry Engineering 2014-2 De Gruyter期刊 afe-2014-0045
指导教师意见
指导教师签名:
年 月 日
开题报告(3)
如今,我国已经拥有世界上较为先进的压铸技术和装备,在我国也形成了一套比较完整的压铸原辅材料供应体系,以及能自主开发的压铸设备和工艺装备体系。主要压铸产品性能、质量和可靠性也跻身于当前国际一流行列。压铸件生产能满足国民经济发展和人民生活的需要,并有部分中高档铸件出口。
虽然我国压铸行业几十年了发展迅速,进步巨大,但毕竟起步较晚共生产压铸机1464台。国产压铸机系列(以合型力吨位计):冷室卧式压铸机从25t至1600t共23种;热室压铸机从至260t共11种;冷室立式压铸机有150t和250t两种;电机转子压铸机从25t至100t共4种。根据1992年统计,全国累计生产压铸机7619台,其中25t以下的为573台,占%;40~63t为691台,占%;80~160t为4554台,占%;180~300t为1421台,占%;400~630t为375台,占%;1000t以上的大型压铸机,为 数甚少。近年来,着重发展大型压铸机,相应地发展热室压铸机。国产900t、1250t和1600t大型压铸机于1992年至1993年研制成功,并投入生产。国内压铸机厂正致力于更大吨位的压铸设备的研制
20世纪80年代,中国实行改革开放模式下的市场经济模式。以深圳为试点的改革开放诸多举措的实施,以及港、台、日、韩等四小龙来华投资,促进了我国五金、摩托车、手表等产业的快速发展,给压铸生产企业带来了十分广阔的发展空间。此阶段我国压铸机生产企业猛增至50余家,是计划经济时代的八倍。其共有的特征是:以自行设计为主,仿型为辅;其已实现了批量生产,专业配套门类较全,具有独立的研发机构,开始注重自主知识产权。其中,力劲公司是典型的代表,该公司开发了多项国内领先的压铸机机型。近几年,国内压铸机制造厂家数量激增,约有100家,其中具有一定规模的约为有20家,多分布在沿海地区。
毕业设计(论文)学生开题报告
课题名称
阀体压铸模具设计
课题来源
课题类型
AY
指导教师
张友寿
学生姓名
学 号
专业班级
13铸造
本课题的研究现状、研究目的及意义
压铸设备最早起源于1838年,人们为了制造活字印刷的模具。在当时,压铸设备还是小型手动的,生产力十分低下,应用也很局限。后来,随着技术的进步和发展,压铸设备由字模制造扩展到了批量零部件制造方面,从此成了工业生产重要的一部分。
从技术和生产效率上看,我国的压铸产业同美,德,日等发达国家仍存在差距。尤其是在一些大型薄壁高精度的压铸件时,压铸模往往需要进口,同时还需要购买各种大型进口压铸机,无法做到完全的自给自足。在生产方面,同国外先进水平相比,主要存在着以下四个问题:一,模具寿命短 二,外观质量不甚理想 三,模具可靠性差 四是生产周期较长,生产效率较低。
第六周:撰写说明书.
开题报告(2)
已查阅的主要参考文献
[1]杨达康. 中国压铸行业发展历程及现状[EB/OL].2017(03)
[2]杨裕国.压铸工艺与模具设计[M].北京:机械工业出版社,1993.
[3]中国压铸业发展历程与进步[J]. 耿鑫明. 金属加工(热加工). 2010(19)
[4]邹剑佳. 压铸产业发展战略研究[J]. 特种铸造及有色合金,2012,(12):1107-1110.
我国的压铸应用技术以20世纪40年代中后期为起点。建国前夕,我国的压铸生产力几乎处于空白,仅有少数几家工厂有少量的小型压铸机,技术和生产力十分落后。
20世纪50年代,随着航空,汽车等工业的发展,中国压铸行业也随之得到了发展和兴起,呈现出了日新月异的局面。压铸在工业上的大量应用始于1958年,自此以后的数十年里,我国的压铸技术取得了极大的发展进步和成就,除掌握了常规压铸生产工艺外,还积极探讨研究各种新型工艺,扩大压铸件应用范围。
基于此,本课题以阀体压铸模研究为出发点,进行最基本的模具装配设计。虽然离真正的生产实践设计还有一定的距离,但希望通过这次的毕业设计,来检验自己平日所学,提高自己的动手能力,巩固自己的专业知识,在日后进入生产岗位,面临真正实际生产时不至于手足无措;也希望能提高自己的设计能力和动手能力,为今后进入压铸行业打下坚实基础,进而对中国压铸行业发展投入自己的一点力量,做出有积极意义的探讨和一点微小的贡献。
4.认真分析零件的结构工艺性、确定其成型工艺和成型方案,画出模具总装草图
5.选择合适的压铸机,进行相关参数校核,并对成型零部件尺寸进行计算。
6.模具结构设计与计算(包括抽芯机构、推出机构的设计与计算)
7.绘制模具总装图和零件图。
8.撰写设计说明书。
分析零件的结构工艺性,在合理的零件结构的条件下根据参考文献和设计原理,选择压铸机
[5]李荣德,于海朋,袁晓光. 压铸技术的发展与应用[J]. 铸造,2003,(08):597-601.
[6]提高压铸模具寿命的探讨[J]. 孔亚. 硅谷. 2012(07)
[7]压铸模具的验收[J]. 崔爱军. 铸造设备与工艺. 2012(06)
[8]耿鑫明. 我国压铸业的国际地位与发展前景[J]. 机械制造与自动化,2003,(01):8-11.
[9]《陈金城,彭余恭. 压铸机的发展[J]. 铸造,2005,(01):6-15.
[10]黄晓锋,谢锐,田载友,朱凯,曹喜娟. 压铸技术的发展现状与展望[J]. 新技术新工艺,2008,(07):50-55+3.
[11]宋才飞. 中国压铸市场分析与和谐发展[J]. 世界有色金属,2007,(05):42-44.
[12]周健波,田福祥. 压力铸造的现状与发展[J]. 铸造设备研究,2006,(02):48-51.
[13]唐玉林,苏仕方,徐爽,葛晨光. 世界压铸工业和市场的概况[J]. 铸造,2004,(12):951-957.
[14]缪良. 中国有色金属及特种铸造业概况[A]. 中国铸造协会(China Foundry Association).’98上海有色合金及特种铸造国际会议论文集[C].中国铸造协会(China Foundry Association):,1998:8.