CA6140拨叉831002课程设计说明书
CA6140拨叉831002课程设计说明介绍模板之欧阳科创编

序言机械制造工艺学课程设计使我们学完了大学的全部基础课、技术基础课以及大部分专业课之后进行的.这是我们在进行毕业设计之前对所学各课程的一次深入的综合性的总复习,也是一次理论联系实际的训练,因此,它在我们四年的大学生活中占有重要的地位。
就我个人而言,我希望能通过这次课程设计对自己未来将从事的工作进行一次适应性训练,从中锻炼自己分析问题、解决问题的能力,为今后参加祖国的“四化”建设打下一个良好的基础。
一、零件的分析(一)零件的作用题目所给的零件是CA6140车床的拨叉。
它位于车床变速机构中,主要起换档,使主轴回转运动按照工作者的要求工作,获得所需的速度和扭矩的作用。
零件上方的φ25孔与操纵机构相连,二下方的φ60半孔则是用于与所控制齿轮所在的轴接触。
通过上方的力拨动下方的齿轮变速。
两件零件铸为一体,加工时分开。
(二)零件的工艺分析CA6140车床共有两处加工表面,其间有一定位置要求。
分述如下:1. 以φ25mm孔为中心的加工表面这一组加工表面包括:φ25H7mm的孔,以及φ42mm的圆柱两端面,其中主要加工表面为φ25H7mm通孔。
2. 以φ60mm孔为中心的加工表面这一组加工表面包括:φ60H12的孔,以及φ60H12的两个端面。
主要是φ60H12的孔。
3. 铣16H11的槽这一组加工表面包括:此槽的端面,16H11mm的槽的底面,16H11mm的槽两侧面。
4. 以M22×1.5螺纹孔为中心的加工表面。
这一组加工表面包括:M22×1.5的螺纹孔,长32mm的端面。
主要加工表面为M22×1.5螺纹孔。
这两组加工表面之间有着一定的位置要求,主要是:(1)φ60孔端面与φ25H7孔垂直度公差为0.1mm.。
(2)16H11mm的槽与φ25H7的孔垂直度公差为0.08mm。
由上面分析可知,加工时应先加工一组表面,再以这组加工后表面为基准加工另外一组。
二、工艺规程设计(一)确定毛坯的制造形式零件材料为HT200。
c6140拨叉831002说明书

8).M22×1.5 螺纹孔
由于该螺纹孔为未注公差尺寸, 根据 GB1800-79 规定其公差等级按 IT13, 同时表面粗糙的没 有要求,选择直接钻孔+攻螺纹。
9).铣断拨叉脚Φ60 圆孔
由于拨叉脚端面表面粗糙度为,故可选择直接铣断即可。
-5-
3.制订工艺路线
制订工艺路线的出发点,应当是零件的加工精度(尺寸精度、形状精度、位置精度)和表面 等技术要求能得到合理的保证。根据零件的几何形状、尺寸精度及位置精度等技术要求,以及加 工方法所能达到的经济精度,在生产纲领已确定的情况下 ,可以考虑采用万能性机床配以专用工 卡具,并尽量使工序集中来提高生产率。除此之外,还应当考虑经济效果,以便使生产成本尽量 下降。查《机械制造工艺设计简明手册》第 20 页表 1.4-6、1.4-7、1.4-8,选择零件的加工方法 及工艺路线方案如下:
三、确定毛坯的制造方法,初步确定毛坯的形状
零件材料为 HT200 (最低抗拉强度为 200MPa 的灰铸铁) 。 考虑零件在机床运行过程中所受冲 击不大,零件结构又比较简单,生产类型为中批量生产,故选择金属模机械砂型铸造毛坯。 零件形状并不复杂,因此毛坯形状可以与零件的形状尽量接近。考虑铸造应力,φ 25 的通孔 不必铸出。 毛坯尺寸通过确定加工余量后决定,然后再设计、绘制毛坯图。
1).φ42mm 圆柱的端面
由于该端面为未注公差尺寸,根据 GB1800-79 规定其公差等级按 IT13,尽管表面粗糙的没 有要求,但后续加工φ 25mm 的内孔要求很高,故选择进行粗加工+精加工。 (查表 1.4—6) 。
2).Φ25H7 通孔
由于其公差等级为 IT7,内表面粗糙度为,故选择进行钻+粗镗+精镗。 (查表 1.4—7)
CA6140拨叉831002课程设计说明介绍模板之欧阳家百创编
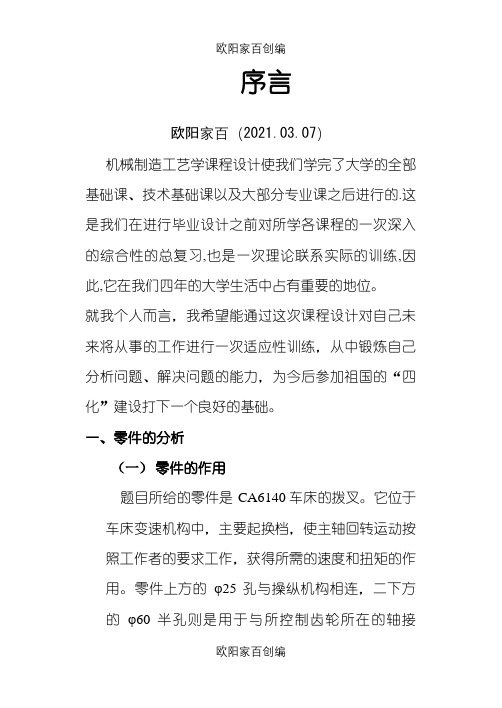
序言欧阳家百(2021.03.07)机械制造工艺学课程设计使我们学完了大学的全部基础课、技术基础课以及大部分专业课之后进行的.这是我们在进行毕业设计之前对所学各课程的一次深入的综合性的总复习,也是一次理论联系实际的训练,因此,它在我们四年的大学生活中占有重要的地位。
就我个人而言,我希望能通过这次课程设计对自己未来将从事的工作进行一次适应性训练,从中锻炼自己分析问题、解决问题的能力,为今后参加祖国的“四化”建设打下一个良好的基础。
一、零件的分析(一)零件的作用题目所给的零件是CA6140车床的拨叉。
它位于车床变速机构中,主要起换档,使主轴回转运动按照工作者的要求工作,获得所需的速度和扭矩的作用。
零件上方的φ25孔与操纵机构相连,二下方的φ60半孔则是用于与所控制齿轮所在的轴接触。
通过上方的力拨动下方的齿轮变速。
两件零件铸为一体,加工时分开。
(二)零件的工艺分析CA6140车床共有两处加工表面,其间有一定位置要求。
分述如下:1. 以φ25mm孔为中心的加工表面这一组加工表面包括:φ25H7mm的孔,以及φ42mm的圆柱两端面,其中主要加工表面为φ25H7mm通孔。
2. 以φ60mm孔为中心的加工表面这一组加工表面包括:φ60H12的孔,以及φ60H12的两个端面。
主要是φ60H12的孔。
3. 铣16H11的槽这一组加工表面包括:此槽的端面,16H11mm 的槽的底面,16H11mm的槽两侧面。
4. 以M22×1.5螺纹孔为中心的加工表面。
这一组加工表面包括:M22×1.5的螺纹孔,长32mm的端面。
主要加工表面为M22×1.5螺纹孔。
这两组加工表面之间有着一定的位置要求,主要是:(1)φ60孔端面与φ25H7孔垂直度公差为0.1mm.。
(2)16H11mm的槽与φ25H7的孔垂直度公差为0.08mm。
由上面分析可知,加工时应先加工一组表面,再以这组加工后表面为基准加工另外一组。
CA6140拨叉说明书

修改后的加工工艺路线见表§3-1。
序号
工序内容
定位基准
简要说明
铸造
时效
涂底漆
10
粗铣φ25H7孔两端面
φ25H7孔端面
先加工基准面
20
精铣φ25H7孔两端面
经上所述,按入体原则确定工序各工步的工序尺寸及公差,精铰φ25(+0.021/0)mm;粗铰φ24.94(+0.052/0)mm;扩孔φ24.8(+0.084/0)mm;钻孔φ23(+0.21/0)mm。
2.工序70(粗铣M22X1.5螺纹孔端面)
查表2.63,得粗加工余量Z为4mm。已知螺纹孔顶面的总余量ZN总为4mm。故精加工余量为0mm。
φ25H7孔端面和φ25H7孔内表面
70
粗铣M22X1.5螺纹孔端面
φ25H7孔左端面、内表面和φ60H12孔内表面
80
粗铣、半精铣槽所在的端面
φ25H7孔端面和φ25H7孔内表面
90
粗铣、半精铣16H11的槽
φ25H7孔端面和φ25H7孔内表面
100
精铣槽所在的端面
φ25H7孔端面和φ25H7孔内表面
精铣φ60H12孔两底面
φ25H7孔端面和φ25H7孔内表面
提高工艺基准精度
160
钻20.5垂直于φ25H7通孔
φ25H7孔端面和φ25H7孔内表面
工序分散,平衡节拍
170
攻M22×1.5螺纹
φ25H7孔端面和φ25H7孔内表面
次要表面在后面加工
CA6140车床拨叉[831002]机械加工工艺及精铣槽16H11夹具设计课程设计说明书
![CA6140车床拨叉[831002]机械加工工艺及精铣槽16H11夹具设计课程设计说明书](https://img.taocdn.com/s3/m/7f815cc3102de2bd960588e6.png)
题目:拨叉工艺(工装)设计目录任务书 (3)第1章. 零件分析 (5)1.1 零件的作用 (5)1.2 零件的工艺分析………………………………………5--61.3 零件的技术条件分析 (6)第2章. 选择毛坯、确定毛坯尺寸、设计毛坯图 (6)2.1 选择毛坯 (6)2.2 确定零件的加工余量 (6)2.3 设计毛坯图 (7)第3章. 机械加工工艺过程 (7)3.1 基准的选择 (7)3.2 表面加工方法的选择 (8)3.3 拟定机械加工工艺路线…............................................8--103.4 加工方案的比较与优化...................................10--11 第4章. 工序设计 (11)4.1 选择加工设备 (11)4.2 选择刀具、量具及夹具 (11)4.3 确定切削用量及基本工时………………………… ..11--134.4 确定工序尺寸...............................................13--14 第5章夹具设计.. (14)5.1 本工序的加工要求与应限制的自由度 (14)5.2 确定定位方案及定位误差的分析与计算……….14--155.3 夹紧方案确定及夹紧装置的选择设计…………15--185.4 确定夹具的对刀(或导向)装置………………18--195.5 夹具上其它装置的设计…………….……………19--215.6 夹具体的设计 (21)5.7 夹具技术条件的制定 (21)5.8 夹具的操作说明 (21)参考文献 (22)心得体会 (23)附录:1、机械加工工艺过程卡一套2、机械加工工序卡一张3、夹具总装图一张4、夹具体工作图一张课程设计任务书课程名称机械制造技术基础题目设计拨叉机械加工工艺工装第一章零件的分析1.1零件的作用题目所给的零件是CA6140车床的拨叉。
拨叉831002说明书

资料范本本资料为word版本,可以直接编辑和打印,感谢您的下载拨叉831002说明书地点:__________________时间:__________________说明:本资料适用于约定双方经过谈判,协商而共同承认,共同遵守的责任与义务,仅供参考,文档可直接下载或修改,不需要的部分可直接删除,使用时请详细阅读内容课程设计2012~2013学年第1学期课程设计任务书一、课程设计目的学生通过本课程设计,应在下述各方面得到锻炼:1、能熟练掌握和运用《机械制造工艺学》课程中的基本理论以及在生产实习中学到的实践知识,正确地解决一个零件在加工中的定位、夹紧以及工艺路线的安排、工序尺寸的确定等问题,保证零件的加工质量。
2、提高结构设计能力。
学生通过一副夹具的设计,应当获得根据被加工零件的加工要求,设计出高效、省力、既经济合理又能保证加工质量的夹具的能力。
3、掌握与本设计有关的各种资料的名称、出处,能做到熟练运用。
二、课程设计内容第一组: 设计CA6140车床后托架零件(831001)的机械加工工艺规程及加工及沉孔夹具。
第二组: 设计CA6140车床拨叉零件(831002)的机械加工工艺规程及加工夹具。
第三组: 设计CA6140车床拨叉零件(831003)的机械加工工艺规程及加工底孔两工位夹具。
第四组:设计CA6140车床法兰盘零件(831004)的机械加工工艺规程及加工透孔夹具。
第五组:设计CA6140车床拨叉零件(831005)的机械加工工艺规程及加工夹具。
第六组:设计CA6140拨叉零件(831006)的机械加工工艺规程及加工夹具。
第七组:设计CA6140车床拨叉零件(831007)的机械加工工艺规程及加工锥销孔(加工一半)夹具。
第八组: 设计CA6140车床拨叉零件(831008)的机械加工工艺规程及加工底孔夹具。
三、设计要求:1、被加工零件图一张2、机械加工工艺过程卡片一份(要求工序完整)3、机械加工工序卡片二张4、夹具装配总图一张5、夹具零件图一张6、课程设计说明书一份四、时间安排1、工艺分析、画被加工零件图。
CA6140车床拨叉课程设计说明书
题目:“CA6140车床拨叉〞零件的机械加工工艺
与铣槽夹具设计
一、序言................................2
二、设计题目............................2
三、设计内容............................2
四、工艺规程设计........................3
三、工序4——铣通槽
铸造时槽没铸出,得粗铣其槽边双边机加工余量2Z=2.0mm,槽深机加工余量为2.0mm其极限偏差:粗加工为 ,精加工为
粗铣两边工序尺寸为:18-2=16mm;
mm;
粗铣后毛坯最小尺寸为:16+0=16mm;
粗铣槽底工序尺寸为:33mm;
精铣两边工序尺寸为:180,已达到其加工要求:180。
R=F-2RAM-CT/2
〔3〕、确定加工零件通槽前槽的毛坯尺寸:
槽深:R=F-RAM-CT/2
=31-2-5/2
槽宽:R=F+2RAM+CT/2
〔4〕、确定加工零件上端面前的毛坯尺寸:
R=75mm
四、绘制拨叉锻造毛坯简图:
拟定拨叉工艺路线
一、定位基准的选择
定位基准有粗基准和精基准之分,通常先确定精基准,然后确定粗基准。
X51
面铣刀
游标卡尺
内花键孔和左端面
6
钻2×M8通孔并攻丝
Z525、SB408
扩孔钻、铰刀
卡尺、塞规
内花键孔和左端面
7
去毛刺
钳工台
8
中检
卡尺、塞规、百分表等
9
清洗
清洗机
平锉刀
10
终检
CA6140车床的拨叉831003--课程设计说明书(小批量)资料
CA6140车床拨叉831003(小批量)课程设计说明书学院:汽车与机械工程学院专业:机械设计制造及其自动化姓名:沈胜安学号:201421030503指导老师:李旭宇课程:机械制造技术基础2016.121.零件分析1.1零件的作用题目所给的零件是CA6140车床的拨叉。
它位于车床变速机构中,主要起换档,使主轴回转运动按照工作者的要求工作,获得所需的速度和扭矩的作用。
宽度为30mm的面寸精度要求很高,因为在拨叉拔动使滑移齿轮时如果槽的尺寸精度不高或间隙很大时,滑移齿轮得不到很高的位置精度。
所以,宽度为30mm 的面的槽和滑移齿轮的配合精度要求很高。
1.2零件材料零件的材料为HT200,灰铸铁生产工艺简单,铸造性能优良,考虑到零件需加工表面少,精度要求不高,有强肋,且工作条件不差,既无交变载荷,又属于间歇工作,故选用金属型铸件,以满足不加工表面的粗糙度要求及生产要求。
1.3零件的工艺分析分析零件图可知,该拨叉形状、结构比较简单,通过铸造毛坯可以得到基本形状,减少了加工工序,又节约了材料。
除了拨叉上表面外,其余表面加工精度较低,不需要高精度机床加工,通过铣削、钻床等车床的粗加工就可以达到加工要求;而主要工作表面----拨叉上表面虽然加工精度较高,但也可以在正常的生产条件下,采用经济的方法保质保量的加工出来。
由此可以见,该零件的工艺性较好。
1.4主要加工表面加工表面尺寸及偏差mm公差及精度等级表面粗糙度R am形位公差mm拨叉左端面80 3.2拨叉上表面30 3.2 ∥0.10 A花键小径φ22+00.021IT7花键大径φ25+00.021IT7 1.6通槽上底面35 6.3通槽内侧面18+00.11 3.2 ⊥0.08 A 通槽下底面352×M8通孔φ8φ5锥孔配件φ51.5确定生产类型经老师给定题目,确定为小批量生产。
2.确定毛坯、绘制毛坯简图2.1选择毛坯零件的材料为HT200,灰铸铁生产工艺简单,铸造性能优良,考虑到零件需加工表面少,精度要求不高,有强肋,且工作条件不差,既无交变载荷,又属于间歇工作,故选用木模手工砂型铸件,以满足不加工表面的粗糙度要求及生产要求。
拨叉(CA6140)831002课程设计任务书说明书及铣断夹具分析
3 工艺规程的设计
3.1 确定毛坯的制造形式
零件材料为 HT200。考虑零件在机床运行过程中所受冲击不大,零件结构又比较简单,故 选择铸件毛坯。
3.2 基准的选择 基面选择是工艺规程设计中的重要工作之一。 基面选择得正确与合理可以使 加工质量得到保证,生产率得以提高。否则,加工工艺过程中回问题百出,更有
本零件各加工表面的加工方法即加工工艺路线已经在前面根据有关资料确定本零件的各加工表面的各工序或工步的加工余量除粗加工工序或工步加工余量之外其余工序或工步加工余量可以根据现代制造工艺设计方法中的精半精加工余量建议值来确定粗加工工序或工步加工余量不是从表中查出确定而为加工余量毛坯余量减去其余后续工序或工步各加工余量之和
III
目录
设计任务书..................................................................................................................... Ⅰ 摘要 .................................................................................................................................................. Ⅱ Abstract ......................................................................................................................................... Ⅲ 1 设计内容 ..................................................................................................... 错误!未定义书签。 2 零件的分析 .................................................................................................................................. 2 2.1 零件的作用 ..................................................................................................................... 2 2.2 零件的工艺分析 ............................................................................................................ 2 3 工艺规程的设计 ......................................................................................................................... 2 3.1 确定毛坯的制造形式 ................................................................................................... 2 3.2 基准的选择 ..................................................................................................................... 2 3.3 制定工艺路线 .............................................................................. 错误!未定义书签。 3.4 机械加工余量、工序尺寸及毛坯尺寸的确定 ..................................................... 4 3.5 确定切削用量及基本工时.......................................................................................... 7 4 专用夹具设计............................................................................................................................ 18 参考文献 ......................................................................................................................................... 19 致谢 .................................................................................................................................................品零件图一份、生产纲领为中批生产、生产制造能力不限。
CA6140车床拨叉831002说明书
(四)机械加工余量、工序尺寸及毛皮尺寸的确定
”CA6140 车床拨叉”; 零件材料为 HT200, 硬度 190~210HB, 毛坯重量 1.45kg,生产类型为中批量,铸造毛坯。 据以上原始资料及加工路线,分别确定各家工表面的机械加工余 量、工序尺寸及毛坯尺寸如下: 1. 外圆表面(φ 42) 考虑其零件外圆表面为非加工表面, 所以外圆表面为铸造 毛坯, 没有粗糙度要求,因此直接铸造而成。 2. 外圆表面沿轴线方向长度方向的加工余量及公差(φ 25, φ 60 端面) 。 查《机械制造工艺设计简明手册》 (以下称《工艺手册》 ) 表 3.1~26,取 φ 25,φ 60 端面长度余量均为 2.5(均为双边 加工) 铣削加工余量为: 粗铣 2mm 半精铣 0.7mm 3. 内孔(φ 60 已铸成 φ 50 的孔) 查《工艺手册》表 2.2~2.5,为了节省材料,取 1.5 螺纹。 工序十 工序十一
空的精度达到 IT8。 以 φ 25 孔为精基准,铣螺纹孔端面。 以 φ 25 孔为精基准,钻 φ 20 孔(装配时钻铰锥 以 φ 25 孔为精基准,钻一个 φ 20 孔,攻 M22×
以 φ 25 孔为精基准,铣槽端面。 以 φ 25 孔为精基准,铣 16H11 的槽保证槽的侧 面相对孔的垂直度误差是 0.08。 工序十二 两件铣断 工序十三 检查。 虽然工序仍然是十三步,但是效率大大提高了。工序一和工 序二比起工艺路线方案二快了一倍(实际铣削只有两次,而且刀 具不用调整) 。多次加工 φ 60、φ 25 孔是精度要求所致。 以上工艺过程详见图 3。
一. 零件的分析
序言
机械制造工艺学课程设计使我们学完了大学的全部基础课、 技术基础课以及大部分专业课之后进行的 .这是我们在进行毕业 设计之前对所学各课程的一次深入的综合性的总复习 , 也是一次 理论联系实际的训练,因此,它在我们四年的大学生活中占有重要 的地位。 就我个人而言,我希望能通过这次课程设计对自己未来将从 事的工作进行一次适应性训练,从中锻炼自己分析问题、解决问 题的能力,为今后参加祖国的“四化”建设打下一个良好的基础。
- 1、下载文档前请自行甄别文档内容的完整性,平台不提供额外的编辑、内容补充、找答案等附加服务。
- 2、"仅部分预览"的文档,不可在线预览部分如存在完整性等问题,可反馈申请退款(可完整预览的文档不适用该条件!)。
- 3、如文档侵犯您的权益,请联系客服反馈,我们会尽快为您处理(人工客服工作时间:9:00-18:30)。
序言机械制造工艺学课程设计使我们学完了大学的全部基础课、技术基础课以及大部分专业课之后进行的.这是我们在进行毕业设计之前对所学各课程的一次深入的综合性的总复习,也是一次理论联系实际的训练,因此,它在我们四年的大学生活中占有重要的地位。
就我个人而言,我希望能通过这次课程设计对自己未来将从事的工作进行一次适应性训练,从中锻炼自己分析问题、解决问题的能力,为今后参加祖国的“四化”建设打下一个良好的基础。
一、零件的分析(一)零件的作用题目所给的零件是CA6140车床的拨叉。
它位于车床变速机构中,主要起换档,使主轴回转运动按照工作者的要求工作,获得所需的速度和扭矩的作用。
零件上方的φ25孔与操纵机构相连,二下方的φ60半孔则是用于与所控制齿轮所在的轴接触。
通过上方的力拨动下方的齿轮变速。
两件零件铸为一体,加工时分开。
(二)零件的工艺分析CA6140车床共有两处加工表面,其间有一定位置要求。
分述如下:1. 以φ25mm孔为中心的加工表面这一组加工表面包括:φ25H7mm的孔,以及φ42mm的圆柱两端面,其中主要加工表面为φ25H7mm通孔。
2. 以φ60mm孔为中心的加工表面这一组加工表面包括:φ60H12的孔,以及φ60H12的两个端面。
主要是φ60H12的孔。
3. 铣16H11的槽这一组加工表面包括:此槽的端面,16H11mm的槽的底面,16H11mm 的槽两侧面。
4. 以M22×1.5螺纹孔为中心的加工表面。
这一组加工表面包括:M22×1.5的螺纹孔,长32mm 的端面。
主要加工表面为M22×1.5螺纹孔。
这两组加工表面之间有着一定的位置要求,主要是:(1) φ60孔端面与φ25H7孔垂直度公差为0.1mm.。
(2) 16H11mm 的槽与φ25H7的孔垂直度公差为0.08mm 。
由上面分析可知,加工时应先加工一组表面,再以这组加工后表面为基准加工另外一组。
二、 工艺规程设计(一)确定毛坯的制造形式零件材料为HT200。
考虑零件在机床运行过程中所受冲击不大,零件结构又比较简单,故选择铸件毛坯。
(二)基面的选择基面选择是工艺规程设计中的重要工作之一。
基面选择得正确与合理可以使加工质量得到保证,生产率得以提高。
否则,加工工艺过程中回问题百出,更有甚者,还会造成零件的大批报废,是生产无法正常进行。
(1)粗基准的选择。
对于零件而言,尽可能选择不加工表面为粗基准。
而对有若干个不加工表面的工件,则应以与加工表面要求相对位置精度较高的不加工表面作粗基准。
根据这个基准选择原则,现选取φ25021.00 孔的不加工外轮廓表面作为粗基准,利用一组共两块V 形块支承这两个φ42作主要定位面,限制5个自由度,再以一个销钉限制最后1个自由度,达到完全定位,然后进行铣削。
(2)精基准的选择。
主要应该考虑基准重合的问题。
当设计基准与工序基准不重合时,应该进行尺寸换算,这在以后还要专门计算,此处不再重复。
(三)制定工艺路线制定工艺路线的出发点,应当是使零件的几何形状、尺寸精度及位置精度等技术要求能得到合理的保证,在生产纲领已确定的情况下,可以考虑采用万能性机床配以专用夹具,并尽量使工序集中来提高生产率。
除此之外,还应当考虑经济效果,以便使生产成本尽量下降。
1. 工艺路线方案一工序一粗、钻、扩、铰、精铰φ25、φ60孔工序二粗、精铣φ60、φ25孔下端面。
工序三粗、精铣φ25孔上端面工序四粗、精铣φ60孔上端面工序五切断。
工序六铣螺纹孔端面。
工序七钻φ22孔(装配时钻铰锥孔)。
工序八攻M22×1.5螺纹。
工序九粗铣半精铣精铣槽所在的端面工序十粗铣半精铣精铣16H11的槽。
工序十一检查。
上面的工序加工不太合理,因为由经验告诉我们大多数都应该先铣平面再加工孔,那样会更能容易满足零件的加工要求,效率不高,但同时钻两个孔,对设备有一定要求。
且看另一个方案。
2. 工艺路线方案二工序一粗、精铣φ25孔上端面。
工序二粗、精铣φ25孔下端面。
工序三钻、扩、铰、精铰φ25孔。
工序四钻、扩、铰、精铰φ60孔。
工序五粗、精铣φ60孔上端面工序六粗、精铣φ60孔下端面。
工序七切断。
工序八铣螺纹孔端面。
工序九钻φ22孔(装配时钻铰锥孔)。
工序十攻M22×1.5螺纹。
工序十一粗铣半精铣精铣槽所在的端面工序十二粗、半精铣精铣16H11的槽。
工序十三检查。
上面工序可以适合大多数生产,但是在全部工序中间的工序七把两件铣断,对以后的各工序的加工定位夹紧不方便,从而导致效率较低。
再看另一方案。
3. 工艺路线方案三工序一粗、精铣φ25孔上端面。
工序二粗、精铣φ25孔下端面。
工序三钻、扩、铰、精铰φ25孔。
工序四钻、扩、铰、精铰φ60孔。
工序五粗、精铣φ60孔上端面工序六粗、精铣φ60孔下端面。
工序七铣螺纹孔端面。
工序八钻φ22孔(装配时钻铰锥孔)。
工序九攻M22×1.5螺纹。
工序十粗铣半精铣精铣槽所在的端面。
工序十一粗、半精铣精铣16H11的槽。
工序十二切断。
工序十三检查。
此方案仍有先钻孔再铣平面的不足,所以这个方案仍不是最好的工艺路线综合考虑以上各方案的各不足因素,得到以下我的工艺路线。
4. 工艺路线方案四工序一以φ42外圆为粗基准,粗铣φ25孔下端面。
工序二精铣φ25孔上下端面。
工序三以φ25孔上端面为精基准,钻、扩、铰、精铰φ25孔,孔的精度达到IT7。
工序四以φ25孔为精基准,粗铣φ60孔上下端面。
工序五以φ25孔为精基准,精铣φ60孔上下端面,保证端面相对孔的垂直度误差不超过0.1。
工序六以φ25孔为精基准,钻、镗、铰φ60孔,保证空的精度达到IT8。
工序七以φ25孔为精基准,铣螺纹孔端面。
工序八以φ25孔为精基准,钻φ20孔(装配时钻铰锥孔)。
工序九以φ25孔为精基准,钻一个φ20孔,攻M22×1.5螺纹。
工序十以φ25孔为精基准,铣槽端面。
工序十一以φ25孔为精基准,铣16H11的槽保证槽的侧面相对孔的垂直度误差是0.08。
工序十二两件铣断工序十三检查。
虽然工序仍然是十三步,但是效率大大提高了。
工序一和工序二比起工艺路线方案二快了一倍(实际铣削只有两次,而且刀具不用调整)。
多次加工φ60、φ25孔是精度要求所致。
以上工艺过程详见图3。
(四)机械加工余量、工序尺寸及毛皮尺寸的确定”CA6140车床拨叉”;零件材料为HT200,硬度190~210HB,毛坯重量1.45kg,生产类型为中批量,铸造毛坯。
据以上原始资料及加工路线,分别确定各家工表面的机械加工余量、工序尺寸及毛坯尺寸如下:1.外圆表面(φ42)考虑其零件外圆表面为非加工表面,所以外圆表面为铸造毛坯,没有粗糙度要求,因此直接铸造而成。
2. 外圆表面沿轴线方向长度方向的加工余量及公差(φ25,φ60端面)。
查《机械制造工艺设计简明手册》(以下称《工艺手册》)表3.1~26,取φ25,φ60端面长度余量均为2.5(均为双边加工)铣削加工余量为:粗铣 2mm半精铣 0.7mm3. 内孔(φ60已铸成φ50的孔)查《工艺手册》表2.2~2.5,为了节省材料,取φ60孔已铸成孔长度余量为3,即铸成孔半径为50mm。
工序尺寸加工余量:钻孔 5mm扩孔0.5mm铰孔0.1mm精铰0mm同上,零件φ25的孔也已铸出φ15的孔。
工序尺寸加工余量:钻孔至φ23 余量为8mm扩孔钻 1.8 mm粗铰孔 0.14 mm精铰孔 0.06 mm4. 槽端面至中心线垂直中心线方向长度加工余量铸出槽端面至中心线47mm的距离,余量为3mm。
工序尺寸加工余量:粗铣端面 2.1 mm半精铣 0.7 mm精铣 0.2 mm5. 螺纹孔顶面加工余量铸出螺纹孔顶面至φ25孔轴线且垂直轴线方向40mm的距离,余量为4 mm工序尺寸加工余量:粗铣顶面 3.1 mm半精铣 0.7 mm精铣 0.2 mm6. 其他尺寸直接铸造得到由于本设计规定的零件为中批量生产,应该采用调整加工。
因此在计算最大、最小加工余量时应按调整法加工方式予以确认。
(五)确立切削用量及基本工时工序一以φ42外圆为粗基准,粗铣φ25孔上下端面。
1. 加工条件工件材料:HT200,σb =0.16GPa HB=200~241,铸造。
加工要求:粗铣φ25孔上下端面。
机床:X53立式铣床。
刀具:W18Cr4V硬质合金钢端铣刀,牌号YG6。
铣削宽度a e<=60,深度a p<=4,齿数z=10,故据《切削用量简明手册》(后简称《切削手册》)取刀具直径d o=80mm。
选择刀具前角γo=0°后角αo=15°,副后角αo’=10°,刀齿斜角λs=-15°,主刃Kr=60°,过渡刃Krε=30°,副刃Kr’=5°过渡刃宽bε=1.5mm。
2. 切削用量1)铣削深度因为切削量较小,故可以选择a p=1.3mm,一次走刀即可完成所需长度。
2)每齿进给量机床功率为10kw。
查《切削手册》f=0.08~0.15mm/z。
由于是对称铣,选较小量f=0.15 mm/z。
3)查后刀面最大磨损及寿命查《机械切削用量手册》表8,寿命T=180min4)计算切削速度按《2》表14,V=1.84n=7.32V=6.44f5)计算基本工时t m=L/ V f=(90+36)/6.44=6.99min。
工序二精铣φ25孔上下端面。
1. 加工条件工件材料:HT200,σb =0.16GPa HB=200~241,铸造。
加工要求:精铣φ25上下端面。
机床:X6140卧式铣床。
刀具:W18Cr4V硬质合金钢端铣刀,牌号YG6。
铣削宽度a e<=60,深度a p<=4,齿数z=10,故据《切削用量简明手册》(后简称《切削手册》)取刀具直径d o=80mm。
选择刀具前角γo=+5°后角αo=8°,副后角αo’=8°,刀齿斜角λs=-10°,主刃Kr=60°,过渡刃Krε=30°,副刃Kr’=5°过渡刃宽bε=1mm。
2. 切削用量1)铣削深度因为切削量较小,故可以选择a p=1.0mm,一次走刀即可完成所需长度。
2)每齿进给量机床功率为7.5kw。
查《切削手册》表5 f=0.14~0.24mm/z。
由于是对称铣,选较小量f=0.14 mm/z。
3)查后刀面最大磨损及寿命查《切削手册》表8,寿命T=180min4)计算切削速度按《切削手册》表14,查得V f=6.44mm/s,5)计算基本工时t m=L+18⨯2/ V f=(2+18⨯2)/6.44=5.9min。
工序三以φ25孔上端面为精基准,钻、扩、铰、精铰φ25孔,孔的精度达到IT7。
1. 选择钻床及钻头选择Z5125A钻床,选择高速钢麻花钻钻头,粗钻时d o=23mm,钻头采用双头刃磨法,2.选择切削用量(1)决定进给量由d o=23mm,查《2》表5按钻头r.0=~47mm.0f/57按机床强度查[1]表10.1-2选择r056=.08.1~mmf/最终决定选择机床已有的进给量r.0=f/48mm(2)耐用度查[2]表9T=4500s=75min(3)切削速度查《1》表10.1-2n=50-2000r/min 取n=1000r/min.3.计算工时m in 19.0100048.012801=⨯+==nf L t m 由于所有工步所用工时很短,所以使得切削用量一致,以减少辅助时间。