光伏支架加工工艺标准
屋面分布式光伏支架的材料选择及加工工艺

屋面分布式光伏支架的材料选择及加工工艺随着可再生能源的发展和运用日益广泛,屋面分布式光伏发电系统成为一种受欢迎的选择。
光伏系统的核心组成部分之一,就是光伏支架。
本文将探讨屋面分布式光伏支架的材料选择及加工工艺,以帮助选择适合的材料和了解相关加工工艺。
一、材料选择屋面分布式光伏支架的主要功能是支撑光伏组件,并承受其产生的重量以及外部环境的风、雨、雪等作用力。
因此,在选择材料时,需要考虑以下几个方面:1. 强度和耐久性:支架需要具备足够的强度和耐久性,以承受光伏组件的重量和外部环境的作用力。
常用的材料有铝合金、镀锌钢等。
铝合金具有较好的强度和耐腐蚀性,适用于多种环境条件。
镀锌钢具有较高的强度和耐久性,适用于恶劣环境条件下的使用。
2. 轻量化:光伏支架安装在屋顶上,对屋面负荷有一定要求,因此轻量化也是材料选择的重要考虑因素之一。
铝合金由于密度较低,具有良好的轻量化特性,适用于屋面安装。
此外,还可以采用玻璃钢等材料,这些材料具有轻质化和高强度的特点。
3. 耐腐蚀性:屋面分布式光伏支架需要经受长期暴露在室外环境中的腐蚀,因此材料的耐腐蚀性也是需要考虑的重要因素。
铝合金具有优异的耐腐蚀性,镀锌钢则通过镀锌层提供了一定的防腐蚀性能。
二、加工工艺屋面分布式光伏支架的加工工艺需要满足以下几个要求:1. 精确度:支架需要与光伏组件精确匹配,以确保安装的稳定性和效率。
因此,加工工艺需要具备高精度的要求,可采用数控加工等技术来实现。
2. 搭建方式:屋面分布式光伏支架的搭建一般采用模块化设计,支架的加工工艺也应具备相应的模块化特点,以便于快速、高效的安装和维护。
3. 防水处理:屋面分布式光伏支架需要与屋面进行紧密连接,因此在加工工艺中还需要考虑防水处理的方法,以防止屋面漏水。
三、总结屋面分布式光伏支架的材料选择及加工工艺直接影响到系统的稳定性和效率。
在材料选择上,铝合金和镀锌钢是比较常见的两种选择,具有较好的强度、耐腐蚀性和轻量化特性。
光伏支架施工要求

光伏支架施工要求《光伏支架施工要求》篇一:光伏支架施工要求引言:嘿,咱为啥要聊聊光伏支架施工要求呢?你想啊,现在太阳能可是热门的清洁能源,光伏电站到处都在建。
而光伏支架就像是光伏板的“骨架”,要是这个“骨架”搭不好,那整个光伏系统都得“散架”。
咱的目标就是建出安全、高效、耐用的光伏电站,所以得好好讲讲光伏支架施工的要求。
主体要求:一、基础施工要求1. 定位准确性:基础的位置必须精确,误差不能超过±5厘米。
这就好比盖房子打地基,要是地基歪了,房子能稳吗?在施工前,得用专业的测量仪器,像全站仪之类的,仔仔细细地测量定位。
2. 深度和尺寸:基础坑的深度和尺寸得严格按照设计图纸来。
比如说,设计要求基础坑深1.5米,宽1米,那可不能偷工减料。
深度不够的话,支架在遇到大风等恶劣天气时就容易晃动。
这可不行,咱可不能让光伏支架成为“豆腐渣工程”的一部分。
3. 混凝土浇筑:混凝土的强度等级必须达到设计要求,一般来说,像C25这种强度等级比较常见。
在浇筑的时候,要振捣密实,不能有蜂窝麻面。
就像做蛋糕一样,得把面糊搅拌均匀,烤出来的蛋糕才好吃,混凝土振捣密实了,基础才结实。
二、支架安装要求1. 组件连接:支架的各个组件之间的连接必须牢固。
螺栓要拧紧,扭矩得达到规定数值,比如说M12的螺栓,扭矩要达到80 - 100N·m。
这就好比组装乐高积木,每个零件都得卡紧了,不然一晃动就散了。
连接部位还得做好防锈处理,刷上防锈漆,可不能让支架还没开始工作就先生锈了。
2. 平整度:支架安装完成后,整体的平整度要在允许范围内。
水平方向的误差不能超过±2厘米,垂直方向的误差不能超过±1厘米。
这要是不平,光伏板装上去也是歪的,影响发电效率不说,还不好看呢,就像一个人站得歪歪扭扭的,多别扭。
3. 朝向和角度:支架的朝向和角度得根据当地的经纬度和日照情况精确调整。
比如说,在北纬30度的地区,支架的倾斜角度可能在30 - 40度之间比较合适。
光伏支架生产工艺流程

光伏支架生产工艺流程
《光伏支架生产工艺流程》
光伏支架是太阳能光伏发电系统中的重要组成部分,它承载着太阳能板并将其固定在适当的位置,以保证太阳能板能够正常发电。
光伏支架的生产工艺流程包括多个环节,从原材料的选择到最终的组装安装都需要经过精细的工艺加工。
首先,光伏支架的生产过程从选材开始。
通常光伏支架的主要材料包括铝合金、不锈钢和镀锌钢等,这些材料需要经过严格的质量检验和选择,以确保支架最终的质量和稳定性。
接下来是材料的预处理。
在预处理阶段,材料通常需要经过切割、钻孔、焊接等加工工序,以便将加工成各段支架所需的形状和尺寸。
预处理工艺的质量直接影响着光伏支架的最终质量和使用寿命。
然后是表面处理。
表面处理是为了增加支架的耐腐蚀性能和美观度。
在这一阶段,通常会采用阳极氧化、喷涂、电镀等工艺,使支架具有更好的防腐蚀性和外观效果。
最后是组装和安装。
组装和安装是光伏支架生产工艺的最后一步,也是最关键的一步。
在这一阶段,需要严格按照设计要求进行组装和安装,确保支架的稳定性和安全性。
总的来说,光伏支架的生产工艺流程包括选材、预处理、表面处理和组装安装等多个环节。
每一个环节都需要经过严格的质
量控制和工艺加工,以确保最终产品的质量和稳定性。
光伏支架的生产工艺是一个复杂而精细的过程,只有经过严谨的操作和质量控制,才能生产出高质量的光伏支架产品。
光伏支架主要工艺技术指标
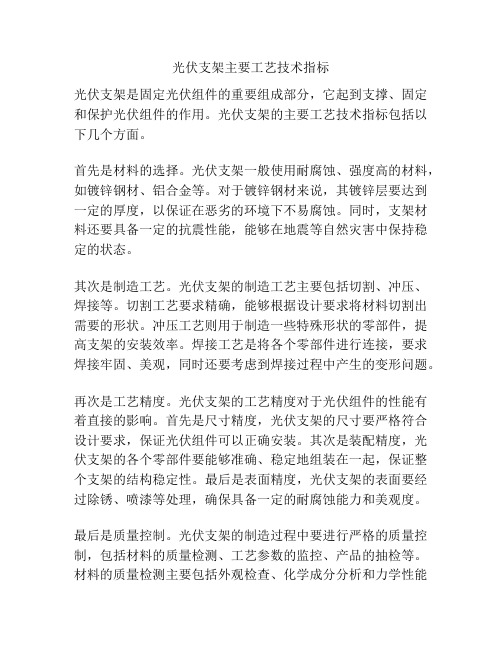
光伏支架主要工艺技术指标光伏支架是固定光伏组件的重要组成部分,它起到支撑、固定和保护光伏组件的作用。
光伏支架的主要工艺技术指标包括以下几个方面。
首先是材料的选择。
光伏支架一般使用耐腐蚀、强度高的材料,如镀锌钢材、铝合金等。
对于镀锌钢材来说,其镀锌层要达到一定的厚度,以保证在恶劣的环境下不易腐蚀。
同时,支架材料还要具备一定的抗震性能,能够在地震等自然灾害中保持稳定的状态。
其次是制造工艺。
光伏支架的制造工艺主要包括切割、冲压、焊接等。
切割工艺要求精确,能够根据设计要求将材料切割出需要的形状。
冲压工艺则用于制造一些特殊形状的零部件,提高支架的安装效率。
焊接工艺是将各个零部件进行连接,要求焊接牢固、美观,同时还要考虑到焊接过程中产生的变形问题。
再次是工艺精度。
光伏支架的工艺精度对于光伏组件的性能有着直接的影响。
首先是尺寸精度,光伏支架的尺寸要严格符合设计要求,保证光伏组件可以正确安装。
其次是装配精度,光伏支架的各个零部件要能够准确、稳定地组装在一起,保证整个支架的结构稳定性。
最后是表面精度,光伏支架的表面要经过除锈、喷漆等处理,确保具备一定的耐腐蚀能力和美观度。
最后是质量控制。
光伏支架的制造过程中要进行严格的质量控制,包括材料的质量检测、工艺参数的监控、产品的抽检等。
材料的质量检测主要包括外观检查、化学成分分析和力学性能测试等。
工艺参数的监控要通过合理的检测手段来确保工艺的可控性,如焊接接头的质量检测和冲压件的尺寸测量等。
产品的抽检则是对成品产品进行抽样检查,以保证产品的合格率。
综上所述,光伏支架的主要工艺技术指标包括材料的选择、制造工艺、工艺精度和质量控制等方面。
这些指标的优化和改进能够提高光伏支架的结构稳定性、耐腐蚀性能和装配效率,从而提高光伏组件的发电效率和使用寿命。
光伏支架制作工艺

光伏支架制作工艺
光伏支架制作工艺是一个复杂而精细的过程,涉及到多个环节和步骤。
以下是对光伏支架制作工艺的详细介绍:
1. 材料准备:首先需要准备制作支架所需的材料,包括钢材、铝合金、塑料等。
这些材料需要符合相关标准和规格,以确保支架的强度和稳定性。
2. 设计图纸:根据光伏电站的布局和安装要求,设计出支架的具体图纸。
图纸需要详细标注支架的尺寸、形状、材料等信息,以便后续的加工和安装。
3. 切割和打孔:根据设计图纸,使用切割机和钻床对钢材进行切割和打孔。
切割时要确保切口平整、无毛刺,打孔时要确保位置准确、孔径合适。
4. 焊接和组装:将切割好的钢材进行焊接和组装,形成完整的支架结构。
焊接时要确保焊缝平整、无气孔、无夹渣,组装时要确保各部件位置准确、连接牢固。
5. 表面处理:对支架进行表面处理,以增强其防腐性能和美观度。
常见的表面处理方法包括喷漆、镀锌等。
6. 检验和测试:对制作好的支架进行检验和测试,以确保其符合相关标准和要求。
检验内容包括尺寸、形状、材料等,测试内容包括承重能力、稳定性等。
7. 包装和运输:将检验合格的支架进行包装和运输,以防止其在运输过程中受到损坏。
包装要牢固、防水,运输要选择合适的交通工具和路线。
总之,光伏支架制作工艺是一个需要严格控制每个环节的精细过程,以确保最终产品的质量和稳定性。
光伏支架质量标准

光伏支架质量标准光伏支架作为太阳能发电系统中承载光伏组件的重要组成部分,其质量标准对于保障光伏发电系统的安全运行和持久使用具有至关重要的作用。
本文将从光伏支架的结构设计、材料选用、制造工艺以及安装要求等方面,详细介绍光伏支架质量标准的相关内容。
一、结构设计光伏支架的结构设计应满足以下要求:1. 结构稳定性:光伏支架应具有良好的承载能力和稳定性,能够经受特定的风载和雪载等外部荷载。
2. 防腐蚀性能:光伏支架应采用防腐蚀材料或采取有效的防腐蚀措施,以保证其在恶劣环境下的长期使用寿命。
3. 可调节性:光伏支架应设计成可调节的结构,可以适应不同地域的安装要求和光照角度。
二、材料选用光伏支架的材料应符合以下标准:1. 耐候性能:支架材料应具有良好的耐候性能,能够在户外恶劣环境下长期使用而不受损。
2. 质量稳定性:支架材料应具有稳定的质量和性能,不会因质量不合格而造成支架的失效。
3. 环保性:支架材料应符合环保要求,不含有有害物质,符合相关的环保标准。
三、制造工艺光伏支架的制造工艺应符合以下要求:1. 加工精度:支架的加工精度应符合设计要求,避免因尺寸偏差而影响支架的安装和使用。
2. 焊接质量:支架的焊接工艺应符合焊接标准,确保焊接接头的牢固性和密封性。
3. 表面处理:支架的表面处理应采取防腐蚀措施,确保支架在使用过程中不易生锈和腐蚀。
四、安装要求光伏支架的安装应遵循以下标准:1. 安装精度:支架的安装应符合设计要求,保证支架的水平度和垂直度符合要求。
2. 固定可靠性:支架的固定应采取可靠的固定措施,确保支架在风雨等恶劣气候下不易松动或脱落。
3. 安全防护:支架的安装应考虑周围环境和安全防护要求,避免因安装不当而引发事故。
光伏支架的质量标准是保障光伏发电系统安全稳定运行的重要保障,只有严格执行相关标准要求,才能有效确保光伏支架的质量和安全性。
希望今后在光伏支架的质量标准领域,能够有更多的行业标准和规范出台,为光伏行业的健康发展提供有力保障。
光伏支架制造工艺方案模板
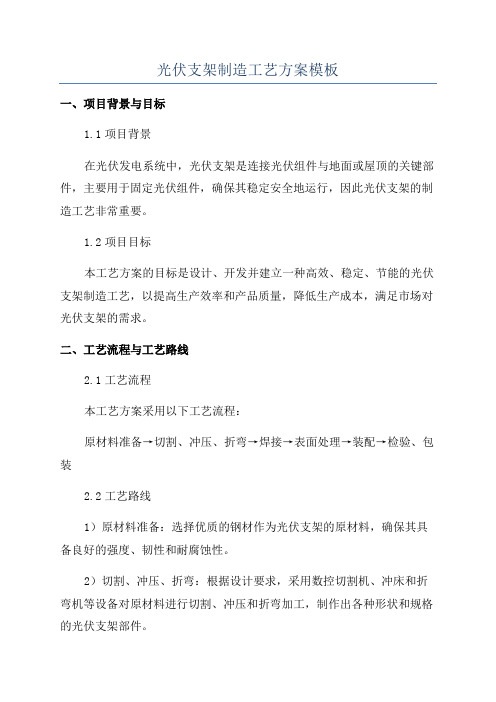
光伏支架制造工艺方案模板一、项目背景与目标1.1项目背景在光伏发电系统中,光伏支架是连接光伏组件与地面或屋顶的关键部件,主要用于固定光伏组件,确保其稳定安全地运行,因此光伏支架的制造工艺非常重要。
1.2项目目标本工艺方案的目标是设计、开发并建立一种高效、稳定、节能的光伏支架制造工艺,以提高生产效率和产品质量,降低生产成本,满足市场对光伏支架的需求。
二、工艺流程与工艺路线2.1工艺流程本工艺方案采用以下工艺流程:原材料准备→切割、冲压、折弯→焊接→表面处理→装配→检验、包装2.2工艺路线1)原材料准备:选择优质的钢材作为光伏支架的原材料,确保其具备良好的强度、韧性和耐腐蚀性。
2)切割、冲压、折弯:根据设计要求,采用数控切割机、冲床和折弯机等设备对原材料进行切割、冲压和折弯加工,制作出各种形状和规格的光伏支架部件。
3)焊接:采用自动焊接设备对光伏支架部件进行焊接,确保焊接接头的质量和强度,提高产品的使用寿命。
4)表面处理:利用喷涂或电镀等表面处理方法,提高光伏支架的耐腐蚀性和美观度。
5)装配:将焊接好的各个光伏支架部件进行装配,确保支架结构的完整性和稳定性。
6)检验、包装:对成品光伏支架进行质量检验,合格后进行包装,并进行质量追溯和记录。
三、关键工艺及设备选择3.1关键工艺3.1.1焊接工艺:采用自动焊接技术,确保焊接接头的质量和强度。
3.1.2表面处理工艺:选择合适的表面处理方法,如喷涂或电镀等,提高光伏支架的耐腐蚀性和美观度。
3.1.3检验工艺:建立一套完善的质量检验系统,确保产品的质量符合标准要求。
3.2设备选择3.2.1数控切割机:用于对原材料进行精准切割,保证光伏支架部件的尺寸准确。
3.2.2自动焊接设备:采用先进的自动焊接技术,提高焊接效率和焊接质量。
3.2.3表面处理设备:根据不同的表面处理方法选择相应的设备,如喷涂设备或电镀设备。
3.2.4检验设备:包括外观检查仪、拉力测试机、超声波无损检测仪等,用于对光伏支架进行质量检验。
光伏支架制造工艺方案
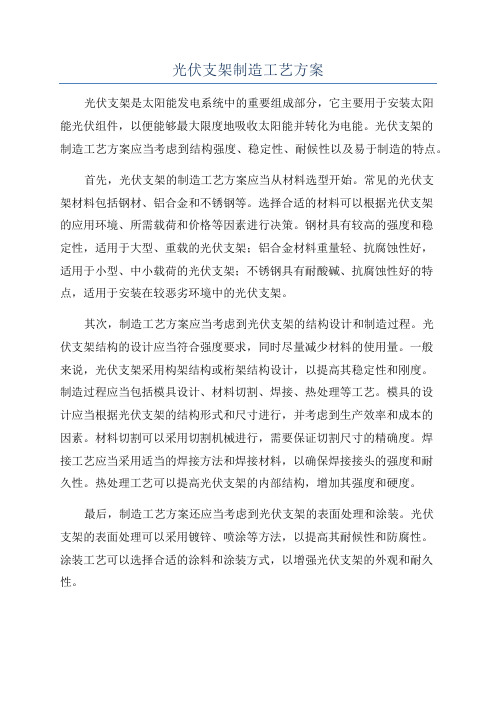
光伏支架制造工艺方案光伏支架是太阳能发电系统中的重要组成部分,它主要用于安装太阳能光伏组件,以便能够最大限度地吸收太阳能并转化为电能。
光伏支架的制造工艺方案应当考虑到结构强度、稳定性、耐候性以及易于制造的特点。
首先,光伏支架的制造工艺方案应当从材料选型开始。
常见的光伏支架材料包括钢材、铝合金和不锈钢等。
选择合适的材料可以根据光伏支架的应用环境、所需载荷和价格等因素进行决策。
钢材具有较高的强度和稳定性,适用于大型、重载的光伏支架;铝合金材料重量轻、抗腐蚀性好,适用于小型、中小载荷的光伏支架;不锈钢具有耐酸碱、抗腐蚀性好的特点,适用于安装在较恶劣环境中的光伏支架。
其次,制造工艺方案应当考虑到光伏支架的结构设计和制造过程。
光伏支架结构的设计应当符合强度要求,同时尽量减少材料的使用量。
一般来说,光伏支架采用构架结构或桁架结构设计,以提高其稳定性和刚度。
制造过程应当包括模具设计、材料切割、焊接、热处理等工艺。
模具的设计应当根据光伏支架的结构形式和尺寸进行,并考虑到生产效率和成本的因素。
材料切割可以采用切割机械进行,需要保证切割尺寸的精确度。
焊接工艺应当采用适当的焊接方法和焊接材料,以确保焊接接头的强度和耐久性。
热处理工艺可以提高光伏支架的内部结构,增加其强度和硬度。
最后,制造工艺方案还应当考虑到光伏支架的表面处理和涂装。
光伏支架的表面处理可以采用镀锌、喷涂等方法,以提高其耐候性和防腐性。
涂装工艺可以选择合适的涂料和涂装方式,以增强光伏支架的外观和耐久性。
综上所述,光伏支架制造工艺方案应当从材料选型、结构设计、制造过程、表面处理和涂装等方面进行考虑。
通过合理的工艺方案,可以制造出具有良好强度、稳定性和耐候性的光伏支架,以提高光伏发电系统的性能和寿命。
- 1、下载文档前请自行甄别文档内容的完整性,平台不提供额外的编辑、内容补充、找答案等附加服务。
- 2、"仅部分预览"的文档,不可在线预览部分如存在完整性等问题,可反馈申请退款(可完整预览的文档不适用该条件!)。
- 3、如文档侵犯您的权益,请联系客服反馈,我们会尽快为您处理(人工客服工作时间:9:00-18:30)。
光伏支架加工工艺
编制:刘超
审核:张亚军
批准:
安徽鸿路钢结构(集团)股份有限公司
二0一五年十月三十日
一材料选用与采购:
1 钢材
1.1制造所用主材,应严格按设计文件要求,并有合格的质量证明书。
应采用镇静钢,各元素化学成分均应符合国家标准,特别是S、P含量,越低越好;采购时材料供应商或钢厂、必须提供代表所采购加盖了红章的材料质量保证书原件、质量保证书上的炉批号必须与材料钢板标牌上的炉批号一致。
1.2 采购时,应选用质量信誉好的大钢厂的产品,以确保钢材的可靠性。
1.3 管材表面质量必须符合要求,不得有夹层、裂纹、非金属夹杂,也不得有气孔、结疤、折叠等缺陷。
锈蚀严重的管材不得使用。
2 焊接材料的选用:钢结构焊接材料的选用应与被焊母材等强性原则为准,质量应符合各相应标准的要求,采购时厂方应提供产品质量质保单。
2.1 焊接材料的选用:考虑到方管柱加工焊接的特点(构件截面小、构件板厚薄),为提高加工焊接效率,采用CO2气保焊方法进行加工焊接;由于产品材质为Q345B,因此选用的焊丝为ER50-6,直径为Ф1.0mm或Ф1.2mm配CO2气体纯度≥99.9%(体积),含水量<0.005%(重量)。
3 工程构件材料以及焊接材料等应按照工程设计说明要求或者按照钢结构工程施工质量验收规范,在工程加工前进行材料进场复验检查工作,合格方可使用。
二构件焊缝质量等级要求
钢柱加工技术说明:依据工程设计要求钢结构焊接规范(GB50661-2011),本工程的所
有焊缝均为角焊缝,除加劲板为双面角焊缝外,其余焊缝均为单面角焊缝。
三方管、零件板下料:
1 方管切割下料:采用锯床进行下料,严格保证下料后方管端头的精度。
首先依据加工详图尺寸对方管进行切割划线,测量长度尺寸放线前先对方管端头进行90°的校验,划出齐头线并进行齐头切割,之后再依齐头端进行测量,划出每节方管长度切割线,采用锯床切割时注意设置切割的角度,具体的切割角度见构件的详图。
首件切割后进行角度的测量,确保角度准确无误;后续相同的构件按照此角度进行切割。
如图3-1所示。
10mm左右
图3-1a:方管下料切割
图3-1:方管下料切割(采用锯床)
2 零件板切割下料:柱底板、托板及加劲板采用剪板机下料和冲孔,各零件板下料尺寸依据构件加工详图。
所有零件板下料尺寸误差±1.5mm,下料时应进行首件下料,并进行自检测下料误差,保证下料质量。
零部件下料完成后,若考虑预抛丸除锈,则先行送入抛丸机
进行抛丸除锈,除锈等级Sa2.5。
图3-2:缺少剪板机的照片
3 装配模板切割:采用编程数控切割
3.1 光伏支架装配侧模板切割尺寸见图3-3,模板底部90°角误差小于等于±0.5°。
光伏支架装配侧模板
图3-3:装配侧模板切割尺寸
3.2 光伏支架下模板见图3-4,模板高度误差≤1mm。
图3-4:装配下模板切割尺寸
四光伏支架的装配:
1装配平台胎模具的制作:为了提高装配精度及效率,也为了后续的机器人焊接提供必需的对口要求,方案采用制作装配胎模具进行。
1.1 工装要求整体轴线偏差≤0.5.mm(放大样线),胎模具平面度偏差≤1.mm,靠模具定位偏差≤0.5.mm,对角线尺寸偏差≤1mm。
1.2 柱底板装配采用模板装,模板垂直平台90°偏差≤0.5°,模板孔径偏差≤1mm。
孔距≤1mm。
2 装配
2.1 平台上放线:依据构件加工详图尺寸,首先在装配平台上放出十字线和构件大样线,
中心线为方管和底板中心线。
如图4-1所示。
边缘线+30mm
中心线
边缘线
柱底线
柱头大样线
(边缘线+30mm)
图4-1平台上放装配线
2.2 胎模具装配:将侧模板点焊固定于平台上,依据方管边线固定侧靠模板,方管另一侧边线+20mm 是用斜铁紧固方管靠模位置线,位置尺寸不予固定,以合适位置即可;下模板按照构件的大样线进行点焊固定。
如图4-2所示。
图4-2:平台上装靠模具
2.3 柱底板和管柱装配:将柱底板装配于底板位置固定胎模上,四周螺栓予以连接紧固,并用90°角尺测量其与平台垂直度,误差<0.5°,测量底板中心线与平台中心线的误差≤1mm ;依次将柱身以及柱头放入胎模具中,两侧和端头用楔铁进行顶紧,模板孔径偏差≤1mm ,孔距≤1mm 。
柱身之间应该贴严对其,其焊缝之间的装配间隙≤2mm ,柱身之间的角度偏差≤2°。
如图4-3所示。
装配柱底板
螺栓固定
图4-3:装配过程
2.4 点焊和完成装配:构件顶紧后进行点焊,点焊完成后将构件取出。
如图4-4所示。
装配柱底板
螺栓固定
图4-4:点焊后取出构件
2.5 装配托板:如图所示,将取出的构件翻转90°,使得需要装配托板的一侧斜向放置。
胎模板和上述的类似,只是多装配了侧向的托板安装靠模板;靠模板焊接在平台上,然后通过螺栓和托板连接紧密,装配时注意测量托板的偏差,角度偏差不应大于2°,尺寸偏差不应大于1mm;由于柱底板通过螺栓和模板连接,因此柱头不需要加固楔铁,只有B侧通过楔铁顶紧。
顶紧后对A侧的托板进行点固;完成后取出构件;由于两侧的托板为非对称设计,因此装配B侧托板时需使用另一个胎模板(和装配A侧托板的胎模板类似,只是装配托板模具位置的改变),B侧托板完成后取出构件。
如图4-5a、4-5b所示。
装配柱底板
螺栓固定
B 侧
A 侧
图4-5a :装配A 侧托板 装配柱底板
螺栓固定
B 侧
A 侧
图4-5b :装配B 侧托板
2.6 装配加劲板:柱体和托板装配完成后开始装配加劲板,首先画出加劲板位置的中心线,再由中心线向两边分出加劲板的边缘位置线。
最后手工操作,将加劲板放置于固定位置,并进行点焊。
如图4-6所示。
图4-6:装配加劲板
五 光伏支架的焊接:
1 工件由电动工具或人工搬运至机器人焊接工位,通过工装夹具对工件进行定位并夹紧,然后由机器人自动焊接。
为提高工作效率,采用双工位设计,机器人焊接和工人装卸工件可在不同工位同时工作,互不影响;机器人除了空程运动外,均处于焊接状态,提高了焊接机器人的利用率;焊接不同种类工件时只需更换工装夹具即可。
系统布置示意图如图5-1所示:
图5-1:机器人焊接系统布置示意图
5.2 首先工件由人工组对点焊完成后,通过工装板装夹至头尾架变位机之间(不同工件可更换对应工装板),然后机器人通过焊缝寻位功能找到焊缝,变位机可360°翻转以保证焊缝最佳位置。
见图5-2所示。
机器人控制器
机器人行
走导轨
按钮站
工件通过工装板
装夹于此处 焊接电源
清枪站
工位一
图5-2:焊接机器人系统三维布置示意图
配置的机器人工作范围为5000mm,为了保证机器人焊接时为最佳姿态,在工件长大于2.8m时,机器人需在机器人导轨上行走焊接,以达到最佳姿态,保证焊缝美观。
焊接工件焊缝周围30mm内应无油、锈及污渍,且满足工件图纸尺寸公差要求。
角接焊缝组对间隙超过3mm时先用手工打底补焊,考虑到待焊工件装配公差较大,为提高焊接自动化水平、减少焊缝位置偏差和操作人员的介入,该机器人焊接系统应配有焊缝寻位功能,能够在5-20mm之间实现自动寻找焊缝初始位置。
系统焊接工作流程如下:
1) 准备工序:焊接工件按图纸要求组对点焊。
2) 安装工件:操作工进入机器人工作区,将工件放置到待焊工位1,通过夹具将待焊
工件与工装连接在一起。
3) 机器人焊接:操作工回到安全位置,按下启动按钮,机器人从设定的位置开始实现
自动焊接。
此时操作工到工位2,将工件放置到工位2,通过夹具将待焊工件与工装连接在一起。
4) 工件卸装:工位1焊接结束后机器人转向工位2进行焊接,操作工进入机器人工作
区工位1,卸下工件。
5) 如此循环作业。
焊接完成后取出构件,送入下道工序。
六:镀锌、涂装、打包、发运
1 焊接完成后按照相关要求进行镀锌、涂装、打包和发运。