深孔爆破设计方案
中深孔爆破设计方案
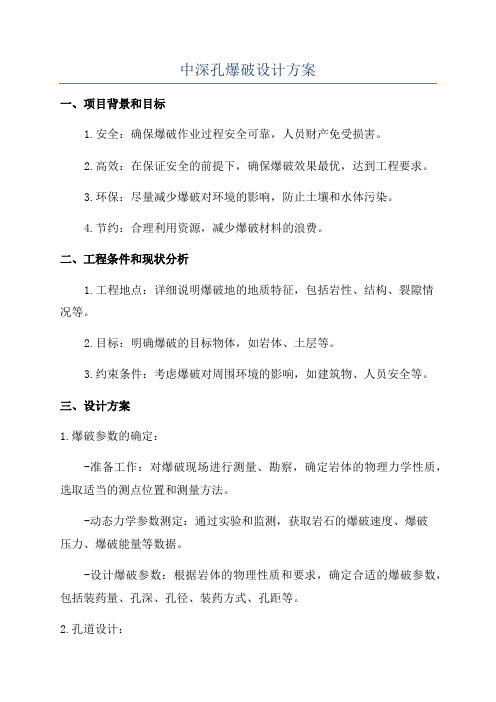
中深孔爆破设计方案一、项目背景和目标1.安全:确保爆破作业过程安全可靠,人员财产免受损害。
2.高效:在保证安全的前提下,确保爆破效果最优,达到工程要求。
3.环保:尽量减少爆破对环境的影响,防止土壤和水体污染。
4.节约:合理利用资源,减少爆破材料的浪费。
二、工程条件和现状分析1.工程地点:详细说明爆破地的地质特征,包括岩性、结构、裂隙情况等。
2.目标:明确爆破的目标物体,如岩体、土层等。
3.约束条件:考虑爆破对周围环境的影响,如建筑物、人员安全等。
三、设计方案1.爆破参数的确定:-准备工作:对爆破现场进行测量、勘察,确定岩体的物理力学性质,选取适当的测点位置和测量方法。
-动态力学参数测定:通过实验和监测,获取岩石的爆破速度、爆破压力、爆破能量等数据。
-设计爆破参数:根据岩体的物理性质和要求,确定合适的爆破参数,包括装药量、孔深、孔径、装药方式、孔距等。
2.孔道设计:-孔道位置:选择合适的爆破孔点,通过岩体的裂缝系统和结构特征,寻找最佳的孔道位置。
-孔道布置:根据爆破参数和孔道性质,合理布置爆破孔道,包括孔距、孔径、孔深等的确定。
-孔道钻探:采用合适的钻孔设备进行钻探,保证孔道的精度和质量。
3.装药设计:-装药方式:根据爆破参数和孔道布置,选择合适的装药方式,如直排、不等间距装药等。
-装药量控制:根据爆破需求和岩体的特性,确定合适的装药量,避免过度或不足的装药现象。
-装药材料:选择合适的装药材料,如炸药、起爆药、推进药等。
4.引爆方式:-爆破网路:根据孔道布置和爆破需求,设计合理的爆破网路系统,确保爆破的同时不引发安全事故。
-引爆方式:选择合适的引爆方式,如电雷管、导线、雷管串联等。
5.安全措施:-爆破现场的警戒和封锁:设置警戒线,限制人员和车辆进入爆破区域。
确保现场的安全封锁,避免事故发生。
-爆破作业人员的防护:爆破作业人员必须佩戴防护用品,如防护服、安全帽、防爆眼镜等。
-爆破作业的时间和天气限制:避免在恶劣的天气条件下进行爆破作业,如大风、雷雨等。
中深孔爆破设计方案

中深孔爆破设计方案在现代建筑和矿山工程中,爆破技术被广泛应用于石头、岩石和土壤的拆除和开采过程中。
其中,中深孔爆破设计方案在提高效率和保证安全方面起到了重要作用。
本文将探讨中深孔爆破设计方案的原理、方法及其对项目的影响。
一、中深孔爆破设计方案的原理中深孔爆破设计方案相对于传统一次性爆破方案具有更高的准确性和可控性。
其原理在于通过连续进行多次小规模爆破,逐渐破碎岩石或土壤,以达到最终的挖掘或爆破目标。
这种设计方案可以减少爆破过程中的冲击力和振动,最大程度地保护周围环境和结构物的安全。
二、中深孔爆破设计方案的方法1. 爆破孔的布置在中深孔爆破设计方案中,爆破孔的布置是关键一步。
爆破孔的位置、间距和角度需要根据工程项目的具体要求进行合理的规划。
一般来说,孔的间距应根据岩石或土壤的性质和强度来决定,孔的角度应使爆破效果最大化。
2. 炸药选择和装药方式在中深孔爆破设计方案中,炸药的选择和装药方式是至关重要的。
炸药的选择应根据岩石或土壤的性质、强度和颗粒大小来确定。
装药方式可以根据具体情况选择直排装药、无排装药或倒排装药等不同的方式。
3. 连续爆破的设计中深孔爆破设计方案中,连续爆破的设计是保证爆破效果的关键。
连续爆破的设计应根据岩石或土壤的性质、爆破孔的布置和装药方式来确定。
通过逐渐增加药量和爆破孔数目,以及控制爆破时间和间隔,可以使爆破过程更加平稳和可控。
三、中深孔爆破设计方案对项目的影响1. 提高工程效率中深孔爆破设计方案通过控制爆破过程,提高爆破效果和工程运输效率。
相对于传统一次性爆破,中深孔爆破设计方案能够更加准确地达到工程目标,减少不必要的爆破次数和材料浪费,从而提高整体工程效率。
2. 保证安全性中深孔爆破设计方案能够有效控制爆破过程中的冲击力和振动,降低对周围环境和结构物的破坏风险。
通过合理的爆破孔布置、炸药选择和装药方式,可以最大程度地保证施工过程的安全性。
3. 减少环境污染中深孔爆破设计方案相对于传统一次性爆破,减少了爆破过程中产生的噪音和颗粒物,对周围环境的污染更小。
各类中深孔爆破设计方案

各类中深孔爆破设计⽅案各类中深孔爆破设计⽅案2.1 矿区概述2.1.1 矿区地理和交通矿区地处⼭坡斜坡部位,所处地势总体为东部低,西部⾼;⼯作区内最低为矿区南西部冲沟⼝处,海拔标⾼1920⽶;最⾼为矿区北西部的⼭坡处,海拔标⾼2278⽶,相对⾼差358⽶,地形坡度⼀般15~40°之间。
属低中⼭浅切割地貌区。
隆阳区板桥镇秋⼭村宝⽯⼭⽯场位于保⼭市隆阳区(市区)42°⽅向,平距约19千⽶处。
矿区地理坐标(极值):东经99°15′28″~99°15′31″,北纬25°14′53″~25°15′01″。
矿区由四个拐点圈定(详见地形地质图),矿区⾯积0.019Km2,开采标⾼2060-2100⽶,矿区范围拐点坐标见表4-1。
⾏政区划⾪属隆阳区板桥镇秋⼭村宝⽯⼭村民⼩组管辖。
320国道经过矿区西部,有⼀条约6千⽶的简易矿⼭公路与西部国道相联通;矿区⾄隆阳区(保⼭市区)运距为23千⽶。
交通较为⽅便,详见交通图(图1)。
4.10凿岩爆破本采⽯场以机械开采为作业⽅式,台阶⾼度10m,凿岩采⽤VF-9/7型空压机驱动与之匹配的KQD-70型潜孔钻机,钻孔直径为70mm。
爆破采⽤中深孔微差爆破技术,炸药选⽤2#露天岩⽯炸药。
在爆破作业中需要做好各种防范措施,采点之间签订统⼀爆破协议,并派遣专⼈在300m爆破警戒范围上站岗放哨,发出明确的爆破信号和解除爆破信号。
4.10.1钻孔形式和炮孔布孔⽅式(1)、钻孔⽅式:采⽤中深孔潜孔钻机钻孔,多排炮孔时炮孔倾⾓取80°,最后⼀排炮孔取75°;采⽤单排炮孔时,倾⾓取75°。
(2)、布孔⽅式:⼀次爆破量较少时⽤单排孔,⼀次爆破量较⼤时,则采⽤V型孔布置⽅式。
4.10.2爆破参数的选择(1)、炮孔直径d炮孔直径取决于选定的钻机类型,采⽤KQD-70型潜孔钻机,钻孔直径取70mm。
(2)、底盘抵抗线Wp(a)、矿区内的台阶为斜坡⾯,其坡⾓在750。
爆破设计方案(深孔爆破)

黔江机场Ⅰ、Ⅲ标段深孔爆破设计方案一、概况1、工程简介:本次爆破范围为黔江机场Ⅰ、Ⅲ标段。
2、爆区地形地质情况:爆区岩体主要是灰岩和砾岩。
3、爆区环境:爆区周围的主要建筑物、构筑物、民房已根据工程要求拆迁,爆破环境较好。
二、爆破方案设计根据供料规格要求,采用深孔微差挤压爆破方式进行开采方案设计。
1、钻孔方式:主要采用潜孔钻作为穿孔设备,因垂直深孔容易操作且装药过程中不易堵孔,故采用垂直深孔方式钻孔。
2、孔形式:从爆破能量均匀分布和提高爆破效果考虑,设计采用梅花形孔布形式。
3、爆破参数设计根据穿孔设备及料场岩石的地质情况进行爆破参数设计如下:(1)阶高度H:6-10m(2)孔径φ:采用古河、阿特拉斯潜孔钻钻孔,其孔径为φ89mm。
(3)孔深L:根据爆区地形,采用8~12m孔深,其中超深1.5~2m。
(4)底盘抵抗线W:为了减少爆后根底、降低大块率,根据经验,W控制在2.5~3m。
(5)孔距a:根据经验一般取a=3.5~4.0m。
(6)排距b:根据经验一般取b=2.5~3.0m。
(7)单位炸药消耗量q:根据岩性及岩石结构情况,取q=0.55~0.6kg/ m3。
(8)单孔装药量:1)前排孔装药量Q:Q=qaHw。
2)第二排起每孔装药量Q′:Q′=kqabH 式中:k为岩阻系数取k=1.1。
(10)堵塞长度L2:根据经验L2=(20~40)d,设计取L2≥2m。
4、起爆方式:最大段药量根据爆区环境对爆破震动的要求来控制。
为了尽可能的降低大块率,孔内外采用微差复式网路起爆,微差间隔时间50~100ms。
正常情况下采用电雷管起爆网络。
5、工作平台宽度的确定平台宽度必须同时满足穿孔及装运设备安全作业的要求,根据料场将使用的潜孔钻、挖掘机、自卸汽车的运作情况,设计取工作平台宽度为30~35m。
6、深孔爆破施工(1)钻孔钻孔时,必须按设计要求布孔,保证孔的深度和方向符合设计。
钻孔前须清除孔周围的碎石及杂物,对钻好的孔用编织袋等将孔口封堵,以防杂物掉进孔内。
中深孔爆破施工设计方案

目录一、施工组织设计方案(一)说明书部分1.1 工程概况1.2 实施方案编制依据1.3 采场的地质概况1.4 采准工程1.5 回采方法1.6 采场各水平暴露面积及矿量:1.7 中深孔爆破设计(二)图纸部分2.1 爆破区环境平面图2.2 爆破区地形、地质图及爆破体结构图2.3 药包布置平面图和剖面图2.4 药室和导硐平面图、断面图2.5 装药和填塞结构图2.6 起爆网路敷设图2.7 爆破安全范围图2.8 防护工程设计图二、劳动组织及安全注意事项2.1 人员施工组织安排2.2工程责任人2.3 安全注意事项2.4 中深孔爆破安全技术措施三、安全警戒方案四、应急救援预案一、施工组织设计方案(一)说明书部分1.1 工程概况****矿房采场位于-430m水平4#矿体一盘区(1#盘间柱与2#盘间柱之间)。
该矿房采场落矿高度为70m(-430m~-360m),宽度12m,长度52m;矿量148680T。
相应各分层采准工程切割巷道已施工完毕。
-430m中段4#矿体设计采用垂直矿体走向布置盘间柱,盘间柱内布置运输主运巷与矿石溜井,垂直盘间柱布置运输巷,运输巷内布置出矿川脉。
4#矿体设计回采顺序是先回采矿柱,隔一采一,进行胶结充填,达到设计时间和强度后,再回采矿房。
****采场东临4344矿柱采场西邻4342矿柱采场,矿柱采场均已回采并采用全尾砂胶结充填施工结束。
采场全尾砂胶结充填的时间已达到三个月以上设计要求时间。
****采场的掏槽、拉槽、落矿均采用中深孔爆破施工,中深孔凿岩已施工完毕。
中深孔掏槽深孔凿岩,采用T-100型潜孔钻机施工完毕,孔径76mm,炮孔共布设51个;中深孔炮排深孔凿岩,采用YGN-90型凿岩机,孔径57mm,炮孔最小抵抗线1.5m,排间距1.4m。
采场底部出矿采用1.5m3电动铲运机出矿。
该采场采准工作已结束。
根据生产需要,经领导和技术人员研究决定,对****采场进行分层中深孔切割槽、回采施工。
完整版)☆露天中深孔爆破设计
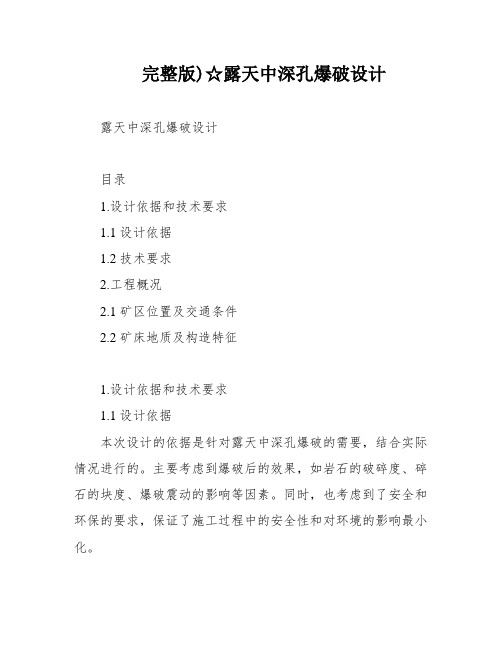
完整版)☆露天中深孔爆破设计露天中深孔爆破设计目录1.设计依据和技术要求1.1 设计依据1.2 技术要求2.工程概况2.1 矿区位置及交通条件2.2 矿床地质及构造特征1.设计依据和技术要求1.1 设计依据本次设计的依据是针对露天中深孔爆破的需要,结合实际情况进行的。
主要考虑到爆破后的效果,如岩石的破碎度、碎石的块度、爆破震动的影响等因素。
同时,也考虑到了安全和环保的要求,保证了施工过程中的安全性和对环境的影响最小化。
1.2 技术要求本次设计的技术要求主要包括爆破参数的确定、爆破方案的设计、爆破材料的选用、爆破震动的控制等方面。
其中,爆破参数的确定是关键,需要充分考虑到矿体的性质和周围环境的影响,以达到最佳的爆破效果。
2.工程概况2.1 矿区位置及交通条件本次工程位于XX矿区,交通较为便利,方便了材料和设备的运输。
同时,也需要考虑到施工期间的交通安全问题,保证人员和车辆的安全。
2.2 矿床地质及构造特征该矿床主要由XX岩和XX岩组成,具有一定的脆性和坚硬性。
同时,矿体的构造复杂,需要充分考虑到不同部位的爆破参数的不同,以达到最佳的爆破效果。
2.9 爆破施工环境在进行爆破施工前,需要对施工环境进行评估和分析,以确保施工的安全性和有效性。
评估的内容包括地质条件、水文地质条件、地下水位、周围建筑物等因素。
评估结果将直接影响到爆破方案的选择和参数计算。
3.1 露天采场构成要素及凿岩穿孔露天采场是指在地表开采矿石或矿砂的采矿场地。
其构成要素包括采场边坡、采场底部、采场顶部和采场道路等。
在进行露天采矿时,需要进行凿岩穿孔,以便进行爆破作业。
3.2 爆破方案选择在选择爆破方案时,需要综合考虑多种因素,如地质条件、爆破材料、爆破效果等。
合理的爆破方案能够提高爆破效率,减少对周围环境的影响。
3.3 爆破施工顺序爆破施工顺序应该根据采场的实际情况进行合理的安排。
一般来说,应该先进行边坡爆破,然后再进行底部和顶部的爆破。
城镇浅孔、复杂环境深孔石方爆破设计方案

城镇浅孔、复杂环境深孔石方爆破设计方案第一部分编制依据及原则一、编制依据1、《爆破安全规程》GB6722—2003;2、甲方提供的爆破申请书和工程合法性文件;3、甲方提供的部分地质勘探资料和工程现场勘察情况资料。
二、编制原则1、按照《爆破安全规程》GB6722—2003中所规定的设计容进行设计编制。
2、遵循工程文件设计规则,在工程文件设计文字中说明及图表中,尽量执行国家规和标准。
3、坚持“安全第一,预防为主”的原则,方案编制中始终把安全工作放在第一位,在此基础上力求做到多、快、好、省。
4、本工程爆破以松动爆破为主,在孔网参数、炸药单耗、装药量的设计与取值时均在此原则下取值。
5、坚持全员、全面、全过程的安全管理和质量控制,在每道工序施工中,严格按技术设计要求施工,并严格执行现场工程师的指令。
6、一切从实际出发,力求设计方案贴近实际,易于操作,真正成为指导工程施工的文件。
7、在爆破方案实施过程中,根据本公司施工能力、技术水平,做到坚持精心设计,精密组织,精细管理,精确操作,在确保安全的前提下高质量、高速度地完成工程任务。
第二部分爆破技术设计一、工程概况(一)工程环境该爆破工程位于xx市高新区舜华路以西,舜奥华府以南。
爆破作业区域边缘北面4米是人行道,道下面是地下管线,8米是工地围挡,围挡外是龙奥南路,路北是舜奥华府新建住宅楼(尚无人居住),距离爆破区域边缘40米;东面是施工围挡,围挡外5米是舜华南路;南面是xx施工现场;西面是存土场和施工临时设施。
表1 爆破区四邻距离表(二)交通条件本工程地处xx高新区,南有旅游路,东临舜华路,北有龙奥北路,所有机械设备可由这些道路进入施工现场,交通条件方便。
(三)施工任务与要求1、对工程设计爆破区域的岩石实施爆破;2、爆破后岩石粒径应满足机械破碎清运要求;3、爆破产生的飞石、震动、冲击波等有害效应不得损坏周围人员和被保护物;4、爆破、清运后地平标高应满足工程技术设计要求;5、爆破工程应在合同约定的时间完成。
露天深孔台阶爆破设计

露天深孔台阶爆破技术设计例题(终算)工程概况在某大型石灰岩露天矿山,石灰岩较坚硬(f=10),节理裂隙发育,台阶高度12米,台阶坡面角α=75°,爆破进尺10-15米,爆区长度50米。
矿山采用露天潜孔钻机(钻孔直径d=200毫米,最大钻孔深度20米)穿孔。
要求进行爆破方案技术设计。
一、爆破方案因矿山规模为大型,台阶高度为12米,故采用露天深孔台阶爆破方案。
二、技术设计1、钻孔形式因石灰岩较坚硬,节理裂隙发育,故采用垂直钻孔形式。
2、底盘最小抵抗线(W1)(1) 按钻机作业的安全条件W1=Hctgα+B=12ctg75°+(2.5~3)=5.7~6.2米。
(2)按台阶高度计算W1=(0.6~0.9)H=(0.6~0.9)×12=7.2~10.8米(3)按孔径计算W1=K1d=(30~35)×0.2=6~7米(4)按每孔装药条件W1=d[7.85·△·T/(q·m)]1/2=2 [7.85×0.9×0.75/(0.56×1.2)] 1/2=5.6米根据上述计算结果,取W1=6米3、孔距(a)a=m·W1=1.2×6=7.2米,取a=7米4、排距(b)采用矩形布孔,b=a/m=7/1.2=5.8米 ,取b=5.5米在爆破进尺范围内,可布设两排炮孔,爆破进尺11.5米。
每排50/7=7个炮孔,两排共14个炮孔.5、堵塞长度(L2)L2=0.7W1=0.7×6=4.2米。
L2=(20-30)d=(20-30)0.2=4-6米取4米。
6、超深(h)(1)按孔径:h=10d=10×0.2=2米(2)按抵抗线:h=0.3 W1=0.3×6=1.8米取h=2米7、孔深(L)L=H+h=12+2=14米8、炸药选择及装药结构为降低爆破成本,选择价廉的2号岩石炸药,采用连续装药结构。
- 1、下载文档前请自行甄别文档内容的完整性,平台不提供额外的编辑、内容补充、找答案等附加服务。
- 2、"仅部分预览"的文档,不可在线预览部分如存在完整性等问题,可反馈申请退款(可完整预览的文档不适用该条件!)。
- 3、如文档侵犯您的权益,请联系客服反馈,我们会尽快为您处理(人工客服工作时间:9:00-18:30)。
东平铁路DK5+00-Dk15+00段石方爆破方案和施工组织设计一.概况根据指挥部提供的该段路基的设计图,该路基出露岩石为石灰岩、砂岩、板岩。
此段内岩石开挖方量约55万立方米,最高挖深为16.3米。
路堑开挖断面为倒梯形,大部分为全路堑拉槽爆破开挖。
直线路基宽度约为15m,上口最大宽度约为57.16m,开挖断面为347.1m2(如图1)。
两侧边坡坡度均为1:1.5,按照设计要求,局部路段需实施光面爆破。
s=347.1 平方米图1典型开挖断面炮眼布置图二.爆破施工方案考虑到该段路堑地表地势比较平坦,爆破方量比较分散,为加快施工进度,经比较决定:采用全断面一次成型深孔爆破方案。
即在该段路堑全长范围内按爆破方案设计要求一次成孔,集中装药、一次起爆成型。
对于永久铁路边坡光面爆破,根据实际情况和设计要求在涮坡时实施或另行设计。
主要爆破区域的爆破穿孔采用瑞典阿特拉斯高风压钻机,钻孔直径为Ф120m m。
Ф90m m的钻机主要用于边坡光面爆破和零星小方量路段爆破。
三.爆破施工设计1.主体拉槽爆破参数设计根据现有施工设备,钻孔直径取φ120m m。
孔深由台阶高度和钻孔超深确定。
爆破台阶高度及路堑的开挖深度,该段路基的开挖深度为:H =6.2-16.3 m 。
钻孔超深可按以下经验公式确定:h = (0.15-0.35) W d : (1)其中:W d 为底盘抵抗线。
本设计中钻孔超深的取值为:h = 1.5 m 。
钻孔深度按:L =H +h 计算。
孔网参数按常规设计取值。
孔网参数不仅取决于钻孔直径,而且和梯段高度(即爆深)有关。
对于φ120 m m 的钻孔,当爆深H >15m 时,宜采用4×5 m 的孔网参数。
根据路基宽度的实际尺寸,并考虑到保护路肩的要求,炮眼间距a =4 m ,排距b =5m ;当爆深15m >H >10m 时,宜采用 3.5×4.5m 的孔网参数,炮眼间距a = 3.5 m ,排距b =4.5 m ;当爆深H <10m 时,可以考虑采用φ120 m m 的钻孔,其孔网参数应为4×3m , 炮眼间距a = 4.0 m ,排距b =3.0 m ;当爆深H <6.0 m 时,可以考虑采用φ90 m m 的钻孔和 2.5×3.0的孔网参数,炮眼间距a = 3.0 m ,排距b =2.5 m ;考虑到路基的设计尺寸和保护边坡的要求,为便于爆破网路联接的简单划一,取矩形布置。
为改善爆破效果,钻孔倾角取α=750° 钻孔长度按正下式计算:αsin h H l d += (2) 单孔装药量:Q =q a b H (3)式中:Q -单孔装药量,k g ;a b H = V :为单孔爆破岩石体积;其中a 为炮眼间距;b 为炮孔排距;H 为台阶高度,在此取炮眼深度,m 。
q -经验参数,即炸药单耗,根据爆破岩石性质,取q =0.40k g /m 3;钻孔布置见图2。
炮孔布置剖面示意图 置示意图各方案的孔网布置参数均可根据爆破效果设置,在不改变孔间距的基础上改变最小抵抗线和炮孔排距。
其钻孔装药参数不必更改。
从炸药能量合理利用考虑,炮孔布置采用正三角形的布置方式,见下图。
2.装药结构装药结构采用全长偶合装药。
为获得较好的爆破效果,炮孔下底部相当于 1.3W长度范围内的装药需捣实。
钻孔直径为φ120m m时,底部装药集中度应在10k g/m d左右,上部装药取自然装填密度即可,装药集中度应在8k g/m左右。
炮孔堵塞长度应大于或等于装药的最小抵抗W(或排距)。
主爆孔的装药结构见图3。
1.炮泥2.炸药3.引爆导爆雷管图3主爆孔的装药结构示意图3.光面爆破设计路基D K5+00~D K25+00段共2000m,路堑边坡开挖设计需要进行光面爆破,考虑充分利用路基拉槽爆破形成的侧向自由面,决定采用“预留光爆层”的光面爆破施工方案,其起爆顺序和时间可与路基主体爆破延后50m s一次起爆,也可以待主体爆破后再进行涮坡的方法进行光面爆破施工。
a.炮眼间距根据现有钻孔设备,路堑边坡光面爆破最好采用φ90m m的炮孔。
故:a=(12~16)d;(m m)式中:d -为钻孔直径,m m ;根据主爆孔的钻孔直径的不同,光面爆破孔的炮眼间距取:a =1.2~1.5mb. 光爆层厚度由 m = a /w = 0.8~1.0;式中:m – 钻孔密集系数;w – 最小抵抗线,这里即光爆层厚度。
故有:w g = a /m = 1.5~1.88;实际爆破取w g = 1.5~2.0m.c. 线装药密度光面爆破的线装药密度可参照预裂爆破装药量公式进行计算: a kd q l =;式中:l q - 光面爆破线装药密度,g /m 3;k – 岩石系数,坚硬岩石取:k = 0.6,其余同上。
将相关参数带入上式得:6611509.06.0=⨯⨯=l q g /m 3 = 0.66 k g /m 3;线装药密度还可按下式进行验算:g l qaw q =式中:q – 为炸药单耗,g /m 3;根据爆破岩石的性质及产出情况,取q = 450 g /m 3,其余同上。
故:13500.25.1450=⨯⨯=l q g /m 3 = 1.35 k g /m 3;实际操作时可视岩石出露情况和主爆破体所采用的钻孔直径,取=l q 0.75~1.0 k g /m 3。
d. 光面爆破孔的装药结构根据现场实际情况,光爆孔采用连续空气柱不偶合装药结构。
即将长20c m ,重150g 或200g 的炸药药卷按设计线装药密度用胶布均匀绑扎在导爆索上,而后将做好的导爆索串下放到光爆孔中即可。
装药不偶合系数:8.2~5.236~32900===d d ξ; 满足要求。
孔口炮泥的封堵长度取:='l 1.0~1.5m ,视主爆孔直径不同在此范围内取值。
光爆孔堵塞时,先用编织袋装少量沙土,用炮棍推压至设计堵塞起始位置,上部用钻屑充填至表地水平。
光爆孔装药结构如图4所示。
1.炮泥2.导爆索3.空气柱4.炸药卷图4光爆孔装药结构示意图3.起爆网路为简化起爆网路,降低爆破成本,该路堑爆破全部采用导爆管-导爆雷管爆网路。
为提高网路准爆的可靠性,亦采用孔内高段位,孔外高段位的导爆雷管微差爆破起爆网路,即孔内全部采用9~10段导爆雷管,孔外接力采用3段导爆雷管。
为确保室爆破网路准爆和爆破安全,建议一次起爆的钻孔数量不宜大于10排。
这样以保证前排首发装药起爆后,后面装药中的导爆雷管全部被引燃,确保整个爆破网路的安全起爆。
爆破网路示意图见图5。
四、爆破安全技术4.1个别飞石的安全距离梯段爆破总有个别飞石飞散较远,危险性大,个别飞石的分散距离与爆破参数、堵塞质量、地形和地质构造等因素有关,本设计按经验公式计算。
R F =15~16d式中R F ——个别飞石的安全距离,m ;d ––炮孔直径,c m 。
R F =225~240m 。
4.2爆破地震安全距离为了减少爆破地震危害,本次爆破采用毫秒微差爆破技术加以控制,减少单段爆破的药量,同时利用应力波相互干涉,以减弱爆破震动峰值和振速。
采用下式估算爆破振动安全距离:R d =(V K d )1/ 3Q =384 m 1.引爆导爆雷管 2. 接力导爆雷管 3. 连接块 4. 导爆管 5. 导爆索接力传爆雷管 6. 导爆索图5 起爆网路示意图式中R d——爆破地震波危险半径,(按地表建筑物安全确定);K d——岩石性质系数,K d=150;V-------允许地震速度,V=1.0c m/s;α——爆破性质系数,α=1.5;Q——最大单响装药量,Q=2400k g;R d=384m。
距离爆区的建筑物最近的在500m以上,爆破地震计算结果满足爆破安全要求。
5、爆破安全措施爆破施工安全技术和安全措施是保证工程顺利进行的重要环节。
因此,在进行爆破材料运输、装药、堵塞和起爆等关键工序中,必须严格遵守国家标准局发布的6722—86号《爆破安全规程》中有关的爆破安全规定要求。
本设计就相应措施做如下说明:(1)爆破材料运输必须有专职押运员、安全员负责押运;(2)人力搬运炸药每次不得超过一包;(3)装卸爆破材料要轻拿轻放。
按指定地点摆平放稳;(4)炸药雷管必须分区存储,存放距离按有关规定执行;(5)起爆体作业只允许爆破技术人员进行,其它人员不得接触(6)电雷管导通只允许用电雷管测试仪,网络检查应采用电爆网络测试仪进行;(7)装药堵塞时应注意保护起爆网络,并采用一定的保护措施;(8)起爆器应由专人看管,起爆器钥匙由起爆者随身携带,其它人员不得随意触碰起爆器和爆破网络;(9)起爆体安放与网络联接应严格按操作规程进行;(10)起爆前,除起爆人员留在掩体内外,所有人员必须撤离到警戒范围1000m以外;(11)爆破完毕后,由爆破技术人员首先进行爆破现场检查,确定各药室全部准确起爆后,方可解除警戒,其它人员才能进入爆破现场。
6、爆破施工组织设计6.1场地施工工在钻爆作业前,场地施工应当创造能够使钻眼台车运输、通行的条件。
6.2钻眼施工要求和安全技术措施(1)钻眼工作1)准备工作为了安全,钻眼前要检查并处理作业工作面,同时,要检修钻机,备齐钎子和钎头,并检查压风管是否有漏损现象,风压是否满足要求等。
2)钻眼注意事项钻眼工作必须严格按照爆破图表的要求,掌握好眼位、眼深及其角度。
此外,还应注意以下事项:a.开眼前,必须使钎头落在实岩上;b.绝对不允许在残眼内继续钻眼;c.工作面全部炮眼钻完后,要把工具清理好并撤至规定的存放地点,胶皮风管也要拖离工作面并保护好。
(2)爆破工作1)装药前的准备工作a.放炮线要妥善地铺设在地面,并要试一下放炮母线是否通电;b.检查炮眼布置是否符合爆破图表要求。
2)装药工作a.应严格按爆破设计进行,不得多装和少装;b.装药时,要细心将炸药送到眼底,避免炮孔中部堵塞;c,装药时,要注意保护导爆索;d.保证堵塞长度,没有封堵的炮眼,不准放炮。
3)联线工作a.联线时必须把雷管脚线的接头刮净并扭结牢固,以免联结不好而产生瞎炮;b.和放炮母线联接前,要先检查母线是否有电,如发现有电一定要查明原因,彻底排除杂散电流的干扰,然后再与脚线相联;c.联线时,无关人员应撤离工作面,以保证安全。
4)放炮工作a.放炮必须严格按照《爆破安全规程》的规定执行;b.放炮前,必须指定专人在可能进入放炮地点的通道上设置岗哨;c.放炮时,只准放炮员一个人进行工作,放炮器的钥匙必须由放炮员随身携带,不得转交别人;d.放炮员必须在有掩护的安全地点给电放炮;e.放炮后,放炮员离开掩护地点以前,必须先将放炮母线从电源上摘下,并将两股线芯扭结在一起,如通电后未爆炸,使用瞬发雷管要等5分钟、使用延期雷管要等15分钟,才能沿线路检查,找出不响的原因并进行处理;f.发现瞎炮要及时处理,如瞎炮系由于联线不良或错联所造成,则可重新联线再补爆。