塑钢门窗出厂检验表格
塑料门窗安装工程检验批质量验收记录通用表格

1
10)
门、窗扇与框搭接量
2
11) 推拉门扇与竖框平行度
2
12) 组合门窗平面度、横竖缝直线度
2.5
实测值(mm)
专业工长(施工员)
施工班组长
施工单位检 查评定结果
项目专业质量检查员:
年月日
监理(建设) 单位验收结论
监理工程师 (建设单位项目专业技术负责人):
年月日
工程检验批质量验收记录通用表格 DB11/T 1087—2014
般
2) 门窗框槽口对角线 ≤2000mm
5
长度差
>2000mm
允许偏差
(mm) 2 3
2.5 3
项 塑 3) 门窗框(含拼樘料)正侧面垂直度
3
料 4) 门窗框(含拼樘料)水平度
3
目 门 5)
门窗下横框标高
5
窗 6)
门窗竖向偏离中心
5
安 7)
双层窗内外框间距
4
装 8) 同樘平开门窗相邻扇高度差
2
9) 平开门窗铰链部位配合间隙
施工质量验收规范的规定
施工单位检查评定记录
监理(建设) ห้องสมุดไป่ตู้位验收记录
1
塑料门窗的物理性能
主
2
塑料门窗的品种、规格、尺寸、性能 、开启方式及型材壁厚
第5.3.1条 第5.3.2条
控3
塑料门窗窗框和副框的安装
项
4
塑料门窗及拼樘料内衬增强型钢的处 理
5
塑料门窗扇的安装
目
6
塑料门窗配件的型号、规格、数量及 安装质量
工程1
塑料门窗安装工程检验批 质量验收记录(最新)
公共建筑装饰工程质量验收标准(DB11/T 1087-2014)
塑料门窗产品检验记录表
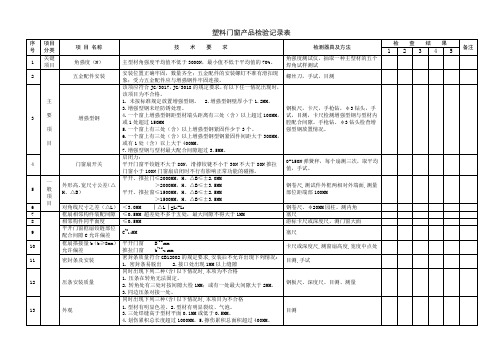
序号
项目分类
项目名称
技术要求
检测器具及方法
检查结果
备注
1
2
3
4
5
1
关键
项目
角强度(N)
主型材角强度平均值不低于3000N,最小值不低于平均值的70%。
角强度测试仪,抽取一种主型材的五个焊角试样测试
2
主
要
项
目
五金配件安装
安装位置正确牢固,数量齐全;五金配件的安装螺钉不准有滑扣现象;受力五金配件应与增强钢件牢固连接。
0-150N弹簧秤,每个扇测三次,取平均值,手试。
5
一
般
项
目
外形高、宽尺寸公差(△H、△B)
平开、推拉门≤2000MM,H、△B≤±2.0MM
>2000MM,H、△B≤±3.5MM
平开、推拉窗≤1500MM,H、△B≤±2.5MM
>1500MM,H、△B≤±3.5MM
钢卷尺,测试件外框两相对外端面,测量部位距端部100MM
2.转角处有三处对按间隙大检1MM;或有一处最大间隙大于2MM。
3.同边压条对接一处。
钢板尺、深度尺、目测、测量
13
外观
同时出现下列三种(含)以下情况时,本项目为不合格
1.型材有明显色差。2.型材有明显裂纹、气泡。
3.三处焊缝高于型材平面0.1MM或低于0.5MM。
4.划伤累积总长度超过1000MM。5.擦伤累积总面积超过400MM。
6
对角线尺寸之差(△L)
<3.0MM│△L│=L1-L2
钢卷尺、φ20MM园柱。测内角
7
框扇相邻构件装配间隙
≤0.5MM超差处不多于五处,最大间隙不得大于1MM
门窗质检表

DB21/1234-录
表Q.2.6 工程名称 施工单位 施工执行标准名称及编号 分包单位 序号 1 2 主 控 项 目 3 4 5 6 1 主 控 项 目 2 3 玻璃的品种 玻璃裁割尺寸正确 玻璃安装方法 木压条 密封条与玻璃 带密封条的玻璃压条 玻璃表面洁净 门窗玻璃不应直接接触型材 腻子填抹 符合要求 符合要求 项 目 分项工程名称 专业工长 门窗玻璃安装 验收部位 项目经理 19、20、21层
分项工程质量验收记录
结构类型 项目经理 分包单位负责人 施工单位检查评定结果 符合要求 符合要求 符合要求 符合要求 符合要求 符合要求 符合要求 剪力墙 检验批数 项目技术负责人 分包项目经理 监理(建设)单位验收结论 7
监理工程师: (建设单位项目专业技术负责人) 年 月 日
DB21/1234-2003
塑料门窗安装工程检验批质量验收记录
表Q.2.4 工程名称 施工单位 施工执行标准名称及编号 分包单位 序号 1 主 控 项 目 2 3 4 5 6 1 2 3 4 5 序号 项 品种、类型、规格 框、副框的扇安装必须牢固 拼樘料内衬增强型钢 开启灵活、关闭严密 门窗配件的型号、规格、数量 框与墙体间缝隙 门窗表面洁净、平整 密封条 开关力 玻璃密封条与玻璃 排水孔 项 门槽口宽度 、高度 对角线长度 差 正侧垂直度 横框的水平度 横框的标高 竖向偏离中心 内外框间距 相邻扇高度 铰链间隙 扇、竖框搭接量 推拉门窗与竖框平行度 目 ≤1500mm >1500mm ≤2000mm >2000mm 目 分项工程名称 专业工长 塑料门窗安装 验收部位 项目经理 15、16层
建筑装饰装修工程施工质量验收规范 GB50210-2001 分包项目经理 施工单位检查评定记录 符合要求 符合要求 符合要求 符合要求 符合要求 符合要求 施工班组长 合格率 % 监理建设单位 验收记录
塑钢门窗安装检验批
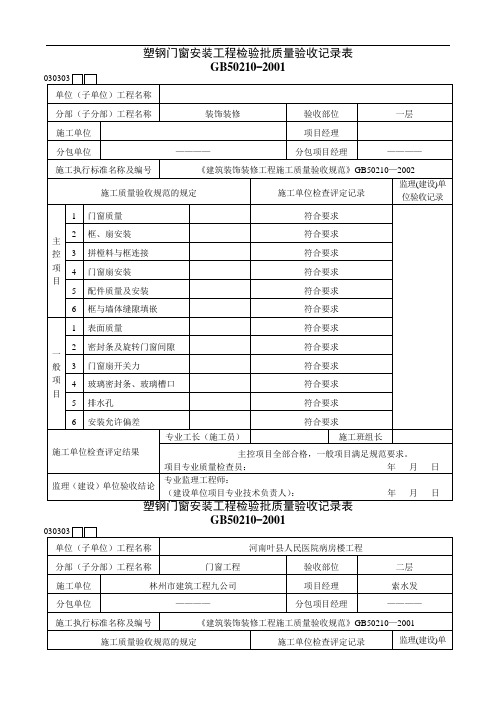
符合要求 符合要求 符合要求
5 排水孔
符合要求
6 安装允许偏差
专业工长(施工员)
符合要求
王鹏
施工班组长
卢明旭
施工单位检查评定结果
主控项目全部合格,一般项目满足规范要求。
项目专业质量检查员:
年月日
专业监理工程师: 监理(建设)单位验收结论
(建设单位项目专业技术负责人):
年月日
塑钢门窗安装工程检验批质量验收记录表
GB50210-2001
030303
单位(子单位)工程名称
河南叶县人民医院病房楼工程
分部(子分部)工程名称
门窗工程
验收部位
设备夹层
施工单位
林州市建筑工程九公司
项目经理
索水发
分包单位
————
分包项目经理
————
施工执行标准名称及编号
《建筑装饰装修工程施工质量验收规范》GB50210—2001
施工质量验收规范的规定
监理(建设)单 位验收记录
1 门窗质量
符合要求
主 2 框、扇安装 控 3 拼樘料与框连接
项 4 门窗扇安装 目
5 配件质量及安装
符合要求 符合要求 符合要求 符合要求
6 框与墙体缝隙填嵌
符合要求
1 表面质量
符合要求
一 2 密封条及旋转门窗间隙 般 3 门窗扇开关力
项 4 玻璃密封条、玻璃槽口 目
5 排水孔
施工单位检查评定记录
监理(建设)单 位验收记录
1 门窗质量
符合要求
主 2 框、扇安装 控 3 拼樘料与框连接
项 4 门窗扇安装 目
5 配件质量及安装
符合要求 符合要求 符合要求 符合要求
门窗质量检查表
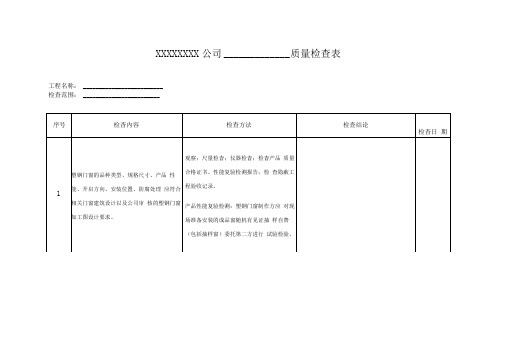
检查人签字:
(根据规范要求实施)
C)型材、增强型钢、玻璃、密封材料
及五金配件等的产品合格证书、性 能检测报告、材料申报审批表、进 场验收记录及复验报告;
d)结构胶相容性试验合格报告;
e)门窗框与洞口连接固定、防腐、缝 隙及密封处理等隐蔽工程项目验
收记录;
f)门窗产品质量合格证书,工厂检查 验收记录;
g)门窗安装施工自检记录。
产品性能复验检测:塑钢门窗制作方应 对现场准备安装的成品窗随机有见证抽 样自费(包括抽样窗)委托第二方进行 试验检验。
2
PVC型材、增强型钢、玻璃的品种、 规格、颜色及附件质量应求。
观察;仪器检查;检查进场验收记录、 性能检测报告和复验检查报告。
1)门窗扇安装完毕、竣工验收前经历暴 雨。
2)水压2kg,每樘门窗全面喷水5分钟。
3)屋顶女儿墙处设置穿孔水管,淋水
24小时。
淋水试验经建设和监理公司检验。
6
塑钢门窗工程移交验收时应检查下列
文件和记录:
a)门窗工程设计文件及竣工图;
b)门窗工程的抗风压性能、水密性
能、气密性能(在寒冷及严寒地区 必须同时进行隔热保温性能验收。
XXXXXXXX
工程名称:
检查范围:
序号
检杳内容
检查方法
检查结论
检杳日 期
1
塑钢门窗的品种类型、规格尺寸、产品 性能、开启方向、安装位置、防腐处理 应符合相关门窗建筑设计以及公司审 核的塑钢门窗加工图设计要求。
观察;尺量检杳;仪器检杳;检杳产品 质量合格证书、性能复验检测报告;检 查隐蔽工程验收记录。
3
门窗框安装必须牢固,预埋件及锚固件 的数量、位置、与框连接方式必须符合 公司审批的加工图和本标准的规定。
PVCU塑料门窗检验等表格
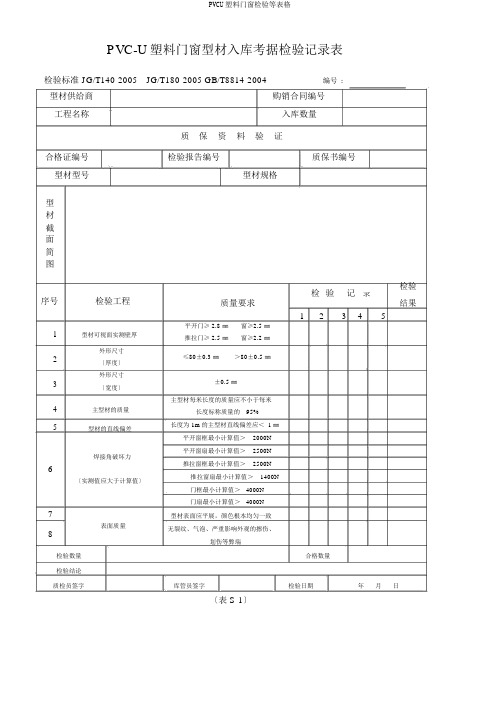
PVCU塑料门窗检验等表格PVC-U塑料门窗型材入库考据检验记录表检验标准 JG/T140-2005 JG/T180-2005 GB/T8814-2004编号:型材供给商购销合同编号工程名称入库数量合格证编号型材型号型材截面简图序号检验工程1型材可视面实测壁厚2外形尺寸〔厚度〕3外形尺寸〔宽度〕4主型材的质量5型材的直线偏差焊接角破坏力6〔实测值应大于计算值〕7表面质量8质保资料验证检验报告编号质保书编号型材规格检验记检验质量要求录结果12345平开门≥ 2.8 ㎜窗≥2.5 ㎜推拉门≥ 2.5 ㎜窗≥2.2 ㎜≤80±0.3 ㎜>80±0.5 ㎜±0.5 ㎜主型材每米长度的质量应不小于每米长度标称质量的95%长度为 1m的主型材直线偏差应< 1㎜平开窗框最小计算值>2000N平开窗扇最小计算值>2500N推拉窗框最小计算值>2500N推拉窗扇最小计算值>1400N门框最小计算值>4000N门扇最小计算值>4000N型材表面应平展,颜色根本均匀一致无裂纹、气泡、严重影响外观的擦伤、划伤等弊端检验数量合格数量检验结论质检员签字库管员签字检验日期年月日〔表 S-1〕PVC-U塑料门窗增强型钢入库考据检验记录表检验标准 JG/T131-2000型材供给商购销合同编号工程名称进货数量入库日期质保资料验证合格证编号检验报告编号质保书编号配用门窗增强型厚度㎜门≥2窗≥型钢断面尺寸宽:型钢断面尺寸高:内外~㎜-0.1 ~㎜序号表面型材型号钢规格123123123分层检12验34结56果789注:入库抽检数量应按标准要求。
必要时对型钢应进行直线度、扭拧度、角度偏差检验。
〔一检验支型钢的厚度、断面宽度、高度检验结论质检员签字库管员签字检验日期〔表 S-2〕PVC-U塑料门窗焊接〔角强度〕试验记录表检验标准 JG/T140-2005 JG/T180-2005编型材供给商品牌/ 颜色购销合同编号工程名称加工单编号型号规格型材生产厂家供给的焊接角最小破坏力计算值或依据型材生产厂家供给的有关参数自行计算得出的焊接角的最小平开框料N平开扇料 N推拉框料 N推拉扇料 N门框料N焊接角最小破坏力计算值:平开窗框>2000N平开窗扇 >2500N推拉窗框 >2500N推拉窗扇 >1400N门框 >3大于计算值。
塑料门窗检验批表格

施工单位检查 监理单位验收 评定记录 记录
施工班组长
主控项目全部合格,一般项目满足规范规定要求 项目质量员: 检查情况: 年 月 日
监理单位 验收结论 专业监理工程师:
同意验收 年 月 日
塑料门窗安装
单位工程名称 分部工程名称 分项工程名称 施工单位 分包单位 /
检验批施工质量验收记录
编号:
验收部位 项目经理 项目负责人 /
门窗槽口对角线长度差
符合
合格
符合 符合
合格 合格
允许偏差 (mm) 2 3 3 5
实测值(mm)
>2000
塑料门窗安装
单位工程名称 分部工程名称 分项工程名称
检验批施工质量验收记录
编号:
验收部位 项目经理 项目负责人 /
施工单位 一 般 分包单位 / 项 《招标文件技术规范》及《建筑装饰装修工程施工质量验收规范》 目 (GB50210-2001) 3 6 4 5 6 7 8 9 10 11 门窗框的正、侧面垂直度 门窗框的水平度 门窗横框标高 门窗竖向偏离中心 双层门窗内外框间距 同樘平开门窗相邻扇高度差 平开门窗铰链部位配合间隙 推拉门窗扇与框搭接量 推拉门窗扇与竖框平行度 施工员 施工单位检查 评定结果 检查情况: 3 3 5 5 4 2 +2,-1 +1.5,-2.5 2
施工单位检查 监理单位验收 评定记录 记录 材料及施工方 法符合要求 窗扇安装牢 固,连接方式 符合设计要求 合格
2
合格
、。
主 控 项 目
3
/ 窗扇开关灵活 、关闭严密, 无倒翘 符合 配件的型号、 规格、数量符 合要求 符合 符合
/
4
合格
5
合格
门窗成品检验记录表
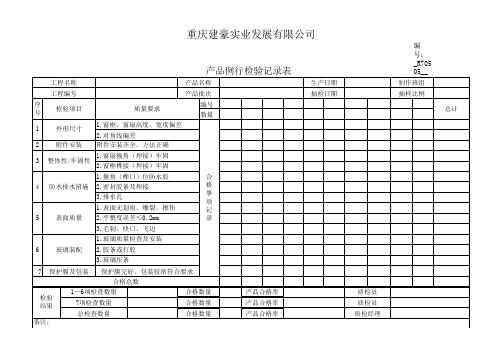
产品例行检验记录表
工程名称 工程编号 序 号 1 2 3 检验项目 外形尺寸 附件安装 整体性/牢固性 质量要求 1.窗框、窗扇高度、宽度偏差 2.对角线偏差 附件安装齐全,方法正确 1.窗扇撞角(焊接)牢固 2.窗框榫接(焊接)牢固 1.撞角(榫口)位防水胶 4 防水排水措施 2.密封胶条及焊接 3.排水孔 1.表面无划痕、爆裂、擦伤 5 表面质量 2.平整度误差≤0.2mm 3.毛刺、快口、飞边 1.玻璃质量检查及安装 6 7 玻璃装配 保护膜及包装 2.胶条或打胶 3.玻璃压条 保护膜完好、包装胶纸符合要求 合格总数 合格数量 合格数量 合格数量 产品合格率 产品合格率 产品合格率 质检员 质检员 质检经理 合 格 事 项 记 录 产品名称 产品批次 编号 数量 生产日期 抽检日期
编号:_R70505__
制作班组 抽样比例 总计
检验 结果 备注:
Байду номын сангаас
1—6项检查数量 7项检查数量 总检查数量
注:产品合格事项,即在上述记录栏中划“正”字标记,未检测事项划“/”标记
- 1、下载文档前请自行甄别文档内容的完整性,平台不提供额外的编辑、内容补充、找答案等附加服务。
- 2、"仅部分预览"的文档,不可在线预览部分如存在完整性等问题,可反馈申请退款(可完整预览的文档不适用该条件!)。
- 3、如文档侵犯您的权益,请联系客服反馈,我们会尽快为您处理(人工客服工作时间:9:00-18:30)。
8检验规则
产品出厂检验和型式检验。
8.1出厂检验
应在型式检验合格后的有效期内进行出厂检验。
8.1.1出厂检验项目应符合表11的规定。
不合格的产品不允许出厂。
8.1.2产品出厂前,抽样方法应按每一批次、品种、规格分别随机抽取5%且不得少于3
樘。
表11 出厂检验与型式检验项目
8.1.3产品出厂检验判定规则应根据表11规定的出厂检验项目进行检验。
当其中某项不合格时,应加倍抽样。
对不合格的项目进行复检,如该项仍不合格,则判定该批产品为不合格。
若全部检测项目符合本标准规定的要求,则判定该批产品为合格。
8.1.4塑料窗的物理性能和力学性能应符合订货合同中的要求,且不应低于本标准规定的最低值。
8.2 型式检验
8.2.1 有下列情况之一时应进行型式检验:
a) 新产品或老产品转厂生产的试制定型鉴定;
b)正式生产后,当结构、材料、工艺有较大改变而可能影响产品性能时;
c)正常生产时,每两年检测一次;
d)产品长期停产后,恢复生产时;
e)出厂检验结果与上次型式检验有较大差异时;
f)国家质量监督机构提出进行型式检验要求时。
8.2.2 型式检验项目见表11。
8.2.3 批量生产时,抽样方法为每二年从出厂检验合格产品中随机抽取三樘进行型式检验。
8.2.4 判定规则应根据表11规定的型式检验项目进行检验。
当其中某项不合格时,应加倍抽
样。
对不合格的项目进行复检,如该项仍不合格,则判定该批产品为不合格品。
若检测项目符合本标准规定的要求,则判定该批产品为合格品。
9 标志、包装、运输、贮存
9.1 标志
9.1.1 在产品的明显部位应注明产品标志,标志内容包括:
a) 制造厂名称;
b) 产品标记;
c) 产品执行标准;
d) 制造日期。
9.1.2 产品检验合格后应有合格证。
合格证应符合GB/T 14436的规定。
9.2 包装
9.2.1 产品表面应有保护措施,宜用无腐蚀性的软质材料包装。
9.2.2 包装应牢固,并有防潮措施。
9.2.3 产品出厂时应附有产品清单及产品检验合格证。
9.36 运输
9.3.1 装运产品的运输工具,应有防雨措施并保持清洁。
9.3.2 在运输、装卸时,应保证产品不变形、不损伤、表面完好。
9.4 贮存
9.4.1 产品应放置在通风、防雨、干燥、清洁、平整的地方。
严禁与腐蚀性物质接触。
9.4.2 产品贮存环境温度应低于50℃,距离热源不应小于1米。
9.4.3 产品不应直接接触地面,底部应垫高不小于100㎜。
产品应立放,立放角不应小于70°,并有防倾倒措施。
附录A
(规范性附录)
未增塑聚氯乙烯(PVC-U)新旧料共挤型材、未增塑聚氯乙烯(PVC-U)与聚甲基丙烯酸甲酯(PMMA)共挤型材、表面涂层型材、覆膜型材的补充要求
A.1 PVC-U新旧料共挤型材
A.1.1 新料应覆盖全部旧料,且厚度不应小于0.5㎜。
型材表面不得有杂质、裂纹、气泡或其他缺陷。
A.1.2 旧料不应含有增塑剂和其他杂质。
维卡软化点不小于71℃;弹性模量不小于2000N/㎜²。
A.1.3 按GB/T 8814—2004规定的试验方法对型材进行老化试验,老化后的冲击强度保留率应符合GB/T 8814—2004的要求。
A.1.4 老化前后试样颜色的变化,△E*不大于5、△b*不大于3。
A1.5 老化后型材外层与芯部旧料之间不得出现分离。
A.2 PVC-U与PMMA共挤型材
A.2.1 PMMA共挤层厚度不小于0.3㎜,共挤层应覆盖全部外可视面,颜色应均匀一致。
A.2.2 PMMA共挤层的维卡软化点不小于90℃,粘数为68㎝³/g—78㎝³/g。
A.2.3 按GB/T8814—2004规定的试验方法向不带共挤层的主型可视面做落锤冲击试验,型材可视面破裂的试样数应符合GB/T8814—2004的要求。
A.2.4按GB/T8814—2004规定的试验方法向聚甲基丙烯酸甲酯(PMMA)层主型材可视面做落锤冲击试验,,即使发生破碎,聚甲基丙烯酸甲酯(PMMA)层也不应与型材分离。
A.2.5 按GB/T8814—2004规定的150℃加热后状态试验方法进行试验,试样不应出现气泡、裂纹和分层,共挤层不应出现分离。
A.2.6 按GB/T8814—2004规定的试验方法对型材共挤层外可视面做6000小时老化试验,老化后冲击强度保留率应符合GB/T8814—2004的要求。
A.2.7 老化前后试样共挤层可视面颜色变化,△E*不大于5。
A.2.8老化前后试样共挤层可视面不得出现斑点、条纹、气泡、裂纹、分离等明显缺陷。
A.3 表面涂层型材
A.3.1 涂层应覆盖型材全部外可视面,厚度不应小于10微米。
涂层表面不得有杂质、裂纹、气泡或其他缺陷。
A.3.2 按GB/T8814—2004规定的150℃加热后状态试验方法进行试验,试样不应出现气泡、、斑点、裂纹、分层和脱落的现象。
A.3.3 按GB/T8814—2004规定的试验方法向不带涂层的主型材可视面做落锤冲击试验,型材可视面破裂的试样数应符合GB/T8814—2004的要求。
A.3.4
按GB/T8814—2004规定的试验方法向带涂层的主型材可视面做落锤冲击试验,即使发生破碎,涂层也不应与型材发生分离。
A.3.5 按GB/T8814—2004规定的方法做涂层附着力的试验,试验结果分级不应大于一级。
A.3.6 按GB/T8814—2004规定的试验方法对型材涂层外可视面做6000小时、涂层内可视面做4000小时老化试验,老化后冲击强度保留率应符合GB/T8814—2004的要求。
A.3.7 老化前后试样带涂层可视面颜色变化,△E*不大于5。
A.3.8 老化后试样带涂层可视面不得出现斑点、条纹、气泡、裂纹、溶化、分离等明显缺陷。
注:试样应在涂装48小时后从型材上截取。
A.4 覆膜型材
A.4.1 基膜上层应有厚度不小于50微米聚丙烯酸酯保护层。
膜不应有杂质、裂纹、气泡或其他缺陷。
膜应覆盖主型材全部外可视面。
A.4.2按GB/T8814—2004规定的150℃加热后状态试验方法进行试验,,试样覆膜层不得有分层、气泡、裂纹、脱落现象。
A.4.3 按GB/T8814—2004规定的试验方法向未覆膜的主型材可视面做落锤冲击试验,型材可视面破裂的试样数应符合GB/T8814—2004的要求。
A.4.4按GB/T8814—2004规定的试验方法未主型材覆膜的可视面做落锤冲击试验,即使发生破碎,膜与型材、基膜与丙烯酸酯层也不应出现肉眼可见的分离。
A.4.5 覆膜层的附着力试验应在覆膜72小时后进行。
取宽度为(20±1)㎜、长度为100㎜的四个试样,采用剥落试验法进行测试,以10㎜/min的剥落速度至20㎜时中止,同时记录剥落的力和行程,每个试件的力不应小于2.5N/㎜(相当于20㎜试验宽度时剥落力为50N)。
A.4.6 按GB/T8814—2004规定的试验方法对型材外可视面覆膜做6000小时、内可视面覆膜做4000小时老化试验,老化后冲击强度保留率应符合GB/T8814—2004的要求。
A.4.7 老化前后试样膜色变化,△E*不大于5。
A.4.8 老化后试样覆膜层的附着力,每个试样均不应小于2.0N/㎜。
A.4.9 老化后试样覆膜可视面不得出现斑点、条纹、=气泡、裂纹、分离、脱落等明显缺陷。