课程设计说明书(瓶盖形状注塑设计)
瓶盖注塑模具设计说明

1 塑件成型分析1.1设计概述随着中国当前的经济形势的高速发展,在“实现中华民族的伟大复兴”口号的倡引下,中国的制造业也蓬勃发展;而模具技术已成为衡量一个国家制造业水平的重要标志之一,模具工业能促进工业产品生产的发展和质量提高,并能获得极大的经济效益,因而引起了各国的高度重视和赞赏。
在日本,模具被誉为“进入富裕的原动力”,德国则冠之为“金属加工业的帝王”,在罗马尼亚则更为直接:“模具就是黄金”。
可见模具工业在国民经济中重要地位。
我国对模具工业的发展也十分重视,早在1989年3月颁布的《关于当前国家产业政策要点的决定》中,就把模具技术的发展作为机械行业的首要任务。
近年来,塑料模具的产量和水平发展十分迅速,高效率、自动化、大型、长寿命、精密模具在模具产量中所战比例越来越大。
注塑成型模具就是将塑料先加在注塑机的加热料筒,塑料受热熔化后,在注塑机的螺杆或柱塞的推动下,经过喷嘴和模具的浇注系统进入模具型腔,塑料在其中固化成型。
本次课程设计的主要任务是塑料圆盖注塑模具的设计,也就是设计一副注塑模具来生产圆盖塑件产品,以实现自动化提高产量。
针对圆盖的具体结构,通过此次设计,使我对轮辐式浇口单分型面模具的设计有了较深刻的认识;同时,在设计过程中,通过查阅大量资料、手册、标准等,结合教材上的知识也对注塑模具的组成结构(成型零部件、浇注系统、导向部分、推出机构、侧抽机构、模温调节系统)有了系统的认识,拓宽了视野,丰富了知识,为将来独立完成模具设计积累了一定的经验。
1.2 塑件成型工艺性分析1.2.1 塑件分析塑件模型如图1-1所示(为计算需要仅标注几个重要尺寸本图见型中图)图1-1 塑料盖子1.2.2塑件的结构及成型工艺性分析结构分析:该塑件为瓶子罐盖子,其结构应尽可能的简单且维度和钢管应满足需要,塑件的顶部没有两个对称的孔,用于安装提手,部有简单的螺纹,用于和罐子连接紧密。
线性工艺性分析:1.精度等级:采用一班精度4级2.脱模斜度:改塑件件壁厚1.5mm,其脱模斜度查表得到塑件材料为聚丙烯pp ,其型腔脱横斜度为:25~45.其型蕊脱横斜度为:20~45.由于该塑件没有狭小部位,所以脱横斜度取1。
小瓶盖塑料注塑模具设计说明书
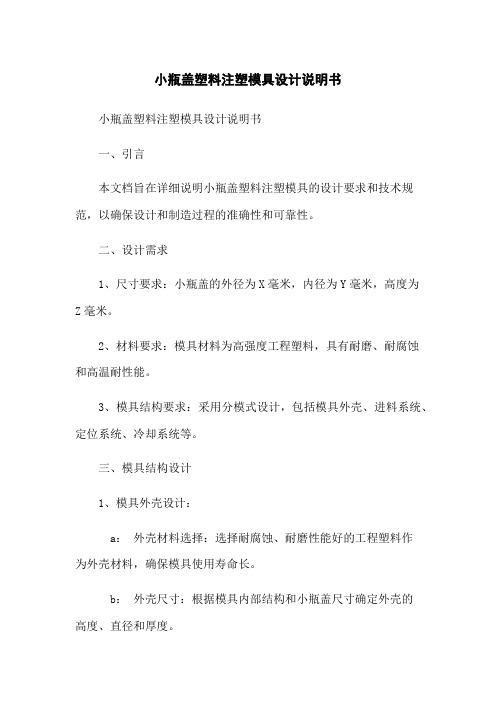
小瓶盖塑料注塑模具设计说明书小瓶盖塑料注塑模具设计说明书一、引言本文档旨在详细说明小瓶盖塑料注塑模具的设计要求和技术规范,以确保设计和制造过程的准确性和可靠性。
二、设计需求1、尺寸要求:小瓶盖的外径为X毫米,内径为Y毫米,高度为Z毫米。
2、材料要求:模具材料为高强度工程塑料,具有耐磨、耐腐蚀和高温耐性能。
3、模具结构要求:采用分模式设计,包括模具外壳、进料系统、定位系统、冷却系统等。
三、模具结构设计1、模具外壳设计:a:外壳材料选择:选择耐腐蚀、耐磨性能好的工程塑料作为外壳材料,确保模具使用寿命长。
b:外壳尺寸:根据模具内部结构和小瓶盖尺寸确定外壳的高度、直径和厚度。
c:模具外壳装配:确保外壳的装配牢固,能够承受注塑过程中的压力和冲击。
2、进料系统设计:a:进料口位置:进料口位于模具外壳上方,方便塑料材料的注入和冷却。
b:进料系统结构:进料系统包括进料管道、进料阀门和喷嘴等组成,确保塑料均匀流动。
3、定位系统设计:a:定位杆:在模具内部设置定位杆,以确保小瓶盖注塑时的位置准确性。
b:定位孔:在小瓶盖上开设定位孔,使得小瓶盖能够准确地套在定位杆上。
4、冷却系统设计:a:冷却通道:在模具内部设置冷却通道,以降低注塑过程中的温度,提高生产效率和产品质量。
b:冷却介质:选择高效的冷却介质,如冷水或冷气等,快速降低模具温度。
四、模具制造要求1、加工工艺:采用先进的数控加工设备和工艺,确保模具的加工精度和表面光洁度。
2、查漏测试:在模具制造过程中进行查漏测试,确保模具没有任何渗漏。
五、附录本文档涉及以下附件:1、小瓶盖的详细尺寸图纸。
2、模具的3D设计图纸。
六、法律名词及注释1、注塑模具:指用于塑料注塑成型的模具,可分为热流道模具和冷流道模具。
2、工程塑料:指具有高强度、耐磨、耐腐蚀和高温耐性能的塑料材料。
3、渗漏:指模具在注塑过程中出现塑料渗漏的现象,对产品质量产生负面影响。
冷水壶盖模具课程设计说明书

课程设计说明书题目:冷水壶盖模具课程设计学号:姓名:班级:专业:材料成型及控制工程指导教师:学院:机械工程学院题目如图所示:该塑件是一个冷水壶盖,材料为PE-HD,批量生产,塑件的原材料和各种工艺性分析如下所示。
目录1.塑件材料的选择和特性 (4)1.1基本特性 (4)1.2主要用途 (4)1.3成型特点 (4)2.塑件的工艺性分析 (5)2.1塑料的尺寸精度分析 (5)2.2塑件表面质量分析 (5)2.3塑件结构工艺性分析 (5)3.成型设备的选择与模具工艺参数的编制 (5)3.1计算塑件的体积 (5)3.2计算塑件的品质 (5)3.3选用注塑机 (6)4.模具结构方案的确定 (7)4.1分型面的选择 (7)4.2型腔数量的确定及型腔的排列 (7)4.3浇注系统的设计 (7)4.4推出方式的选择 (10)5.模具成型部件的设计计算 (10)5.1形芯型腔尺寸 (10)5.2侧向抽芯机构 (11)5.3镶块形腔 (12)6.装配图 (12)7.总结 (12)参考文献 (14)1.塑件材料的选择和特性根据产品的使用要求和性能要求,选择PE为塑件的材料。
1. 1基本特性聚乙烯塑料是塑料工业中产量最大的品种。
按聚合时采用的压力不同可分为高压、中压和低压三种。
低压聚乙烯的分子链上支链较少,相对分子质量、结晶度和密度较高,所以低压聚乙烯比较硬,耐磨、耐蚀、耐热及绝缘性较好。
高压聚乙烯分子带有许多支链,因而相对分子质量较小,结晶度和密度较低,且具有较好的柔软性、耐冲击性及透明性。
聚乙烯无毒、无味、呈乳白色。
密度为0.91-0.96g/cm3,为结晶型塑料。
聚乙烯有一定的机械强度,但与其他塑料相比其机械强度低,表面硬度差。
聚乙烯的绝缘性能优异,常温下聚乙烯不溶于任何一种已知的溶剂,并耐稀硫酸、稀硝酸和任何浓度的其他酸以及各种浓度的碱、盐溶液。
聚乙烯有高度的耐水性,长期接触水其性能保持不变。
聚乙烯透水气性能较差,而透氧气和二氧化碳以及许多有机物质蒸气的性能好。
杯盖注塑课程设计
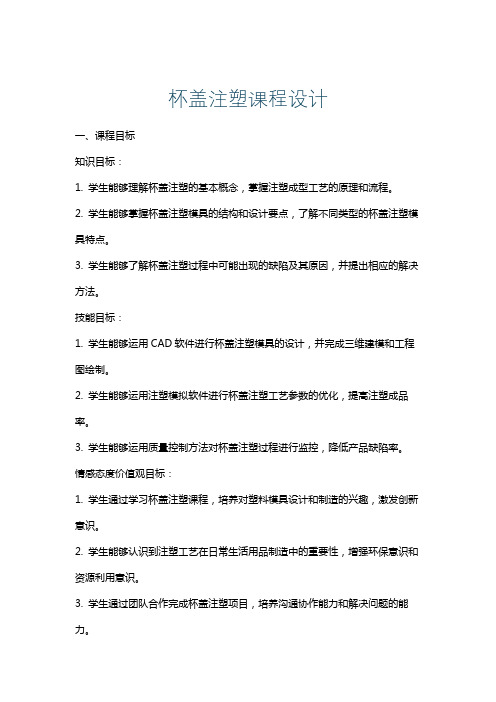
杯盖注塑课程设计一、课程目标知识目标:1. 学生能够理解杯盖注塑的基本概念,掌握注塑成型工艺的原理和流程。
2. 学生能够掌握杯盖注塑模具的结构和设计要点,了解不同类型的杯盖注塑模具特点。
3. 学生能够了解杯盖注塑过程中可能出现的缺陷及其原因,并提出相应的解决方法。
技能目标:1. 学生能够运用CAD软件进行杯盖注塑模具的设计,并完成三维建模和工程图绘制。
2. 学生能够运用注塑模拟软件进行杯盖注塑工艺参数的优化,提高注塑成品率。
3. 学生能够运用质量控制方法对杯盖注塑过程进行监控,降低产品缺陷率。
情感态度价值观目标:1. 学生通过学习杯盖注塑课程,培养对塑料模具设计和制造的兴趣,激发创新意识。
2. 学生能够认识到注塑工艺在日常生活用品制造中的重要性,增强环保意识和资源利用意识。
3. 学生通过团队合作完成杯盖注塑项目,培养沟通协作能力和解决问题的能力。
课程性质:本课程为专业技术实践课程,结合理论知识和实际操作,培养学生对杯盖注塑工艺的全面了解。
学生特点:学生具备一定的模具设计和制造基础知识,对注塑工艺有一定了解,但实际操作经验不足。
教学要求:结合课程性质和学生特点,注重理论与实践相结合,提高学生的实际操作能力和问题解决能力。
通过课程学习,使学生能够达到上述具体的学习成果。
二、教学内容1. 杯盖注塑工艺原理:讲解注塑成型原理,注塑机的类型及工作过程,使学生理解杯盖注塑的基本概念。
教材章节:《塑料模具设计》第二章 注塑成型工艺2. 杯盖注塑模具设计:介绍杯盖注塑模具的结构、设计要点及不同类型的杯盖模具特点。
教材章节:《塑料模具设计》第三章 注塑模具设计3. CAD软件应用:运用CAD软件进行杯盖注塑模具的三维建模、工程图绘制及模具零件的拆分。
教材章节:《CAD/CAM技术》第二章 CAD软件应用4. 注塑工艺参数优化:讲解注塑工艺参数对杯盖注塑质量的影响,运用注塑模拟软件进行工艺参数优化。
教材章节:《塑料模具设计》第四章 注塑工艺参数5. 质量控制方法:介绍杯盖注塑过程中常见的缺陷及其原因,讲解质量控制方法和措施。
塑料盖注射模具课程设计说明书
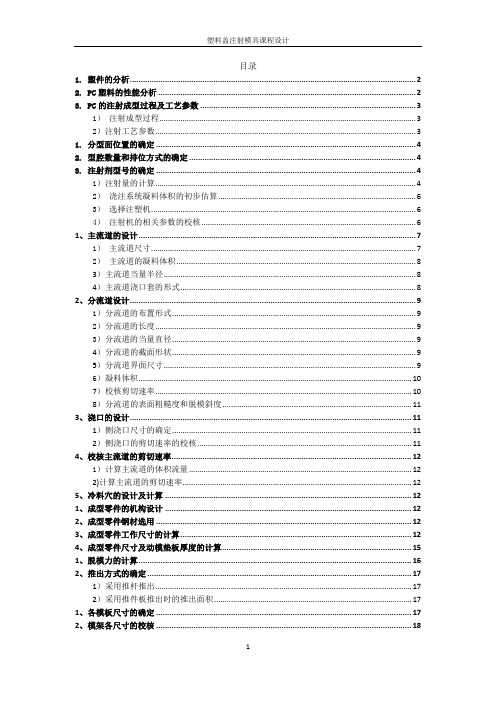
目录1. 塑件的分析 (2)2. PC塑料的性能分析 (2)3. PC的注射成型过程及工艺参数 (3)1)注射成型过程 (3)2)注射工艺参数 (3)1. 分型面位置的确定 (4)2. 型腔数量和排位方式的确定 (4)3. 注射剂型号的确定 (4)1)注射量的计算 (4)2)浇注系统凝料体积的初步估算 (6)3)选择注塑机 (6)4)注射机的相关参数的校核 (6)1、主流道的设计 (7)1)主流道尺寸 (7)2)主流道的凝料体积 (8)3)主流道当量半径 (8)4)主流道浇口套的形式 (8)2、分流道设计 (9)1)分流道的布置形式 (9)2)分流道的长度 (9)3)分流道的当量直径 (9)4)分流道的截面形状 (9)5)分流道界面尺寸 (9)6)凝料体积 (10)7)校核剪切速率 (10)8)分流道的表面粗糙度和脱模斜度 (11)3、浇口的设计 (11)1)侧浇口尺寸的确定 (11)2)侧浇口的剪切速率的校核 (11)4、校核主流道的剪切速率 (12)1)计算主流道的体积流量 (12)2)计算主流道的剪切速率 (12)5、冷料穴的设计及计算 (12)1、成型零件的机构设计 (12)2、成型零件钢材选用 (12)3、成型零件工作尺寸的计算 (12)4、成型零件尺寸及动模垫板厚度的计算 (15)1、脱模力的计算 (16)2、推出方式的确定 (17)1)采用推杆推出 (17)2)采用推件板推出时的推出面积 (17)1、各模板尺寸的确定 (17)2、模架各尺寸的校核 (18)1、冷却介质 (19)2、冷却系统的简单计算 (19)参考文献 (21)[1]伍先明,张蓉,杨军,周志冰. 塑料模具设计指导[M]. 国防工业出版社.2011. (21)[2]李德群,唐志玉. 塑料与橡胶模具设计[M]. 北京:电子工业出版社.2007. (21)[3]李建军,李德群. 模具设计基础及模具CAD[M]. 机械工业出版社.2005. (21)[4]叶久新,王群. 塑料成型工艺及模具设计[M]. 北京:机械工业出版社.2007. (21)一、塑料盖注射模设计本课程设计为一塑料盖,如图1所示。
高压瓶盖注塑模设计说明书

目录摘要 (1)关键词 (1)1前言 (2)2选题背景 (2)2.1选题的目的及意义 (2)2.2国内的现状及发展趋势 (2)2.2.1国内的现状 (2)2.2.2发展趋势 (3)2.3国外的现状 (4)3注射成型工艺规程的编制 (4)3.1塑件的工艺性分析 (4)3.1.1塑件的原材料分析 (4)3.1.2 塑件的结构和尺寸精度及表面质量分析 (4)3.2计算塑件的体积和重量 (5)3.3塑件注射工艺参数的确定 (6)3.4塑料成型设备参数 (6)3.4.1注射量的校核 (7)3.4.2注射压力的校核 (7)3.4.3锁模力的校核 (7)4注射模的结构设计 (8)4.1分型面的选择 (8)4.2确定型腔的数目及排列方式 (9)4.2.1按注射机的塑化能力确定型腔的数量 (9)4.2.2按注射机的最大注射量确定型腔的数量 (10)4.3浇注系统的设计 (9)4.3.1主流道的设计 (10)4.3.2分流道的设计 (11)4.3.3浇口的设计 (11)4.3.4冷料井和拉料杆的设计 (12)4.4排气系统的设计 (13)4.5成型零部件结构设计 (13)4.5.1凹模结构设计 (13)4.5.2型芯结构设计 (14)4.6合模导向机构设计 (15)4.6.1导柱设计 (15)4.6.2导套设计 (15)4.7推出机构设计 (16)4.7.1脱模力的计算 (16)4.7.2推杆尺寸的计算及机构设计 (18)4.7.3复位机构设计 (19)4.8侧抽芯机构设计 (19)4.8.1抽芯机构的选择 (20)4.8.2塑件左侧小孔的抽芯 (20)4.8.3塑件右侧小孔的抽芯 (21)4.8.4凸筋处的抽芯机构 (21)4.8.5斜导柱的结构设计 (22)4.8.6滑块 (23)4.8.7滑块的导槽 (24)4.9温度调节系统的设计 (24)4.9.1加热系统的设计 (24)4.9.2冷却系统的设计 (24)5模具零件的计算 (25)5.1型腔工作尺寸的计算 (25)5.1.1型腔径向尺寸计算 (25)5.1.2型腔深度尺寸计算 (26)5.2型芯工作尺寸计算 (26)5.2.1型芯径向尺寸计算 (26)5.2.2型芯高度尺寸计算 (27)5.3型腔侧壁厚度和底板厚度计算 (27)5.3.1型腔侧壁厚度计算 (28)5.3.2型腔底板厚度计算 (28)5.4冷却系统的有关计算 (29)5.4.1冷却水体积流量的计算 (29)5.4.2冷却水孔直径的确定 (30)5.4.3冷却管道总传热面积的计算 (30)5.4.4冷却水孔数目的计算 (30)5.4.5冷却水路的分布 (30)5.5斜导柱侧分型与抽芯的有关计算 (31)5.5.1抽拔力的计算 (31)5.5.2抽芯距的计算 (32)5.5.3斜导柱倾角 的确定 (32)5.5.4斜导柱的长度计算 (32)5.5.5斜导柱直径的计算 (33)5.5.6最小开模行程的计算 (33)6注射机有关参数的校核 (34)6.1模具闭合厚度校核 (34)6.2喷嘴尺寸校核 (34)6.3模具安装尺寸校核 (34)6.4开模行程的校核 (34)7模具的工作原理 (35)8结论和总结 (35)8.1结论 (35)8.2总结 (35)参考文献 (36)致谢 (37)高压瓶盖注塑模具设计摘要:本设计详细介绍了高压瓶盖注塑模具设计,选用了ABS作为塑件的材料能够满足高压瓶盖的使用性能及注射模具的成性特点。
盖的注塑模课程设计

盖的注塑模课程设计一、教学目标本课程旨在通过学习盖的注塑模相关知识,使学生掌握注塑模的基本概念、设计原则和制作流程。
在知识目标方面,学生应能够理解注塑模的组成部分、工作原理及其在塑料制品生产中的应用。
技能目标方面,学生应能够运用所学知识进行简单的注塑模设计和制作。
情感态度价值观目标方面,通过学习注塑模课程,培养学生对模具行业的兴趣和热情,提高学生对工程实践的认知。
二、教学内容教学内容主要包括注塑模的基本概念、设计原则、制作流程及应用。
具体包括以下几个方面:1.注塑模的基本概念:介绍注塑模的定义、分类及其在塑料制品生产中的作用。
2.注塑模的设计原则:讲解注塑模设计的基本原则,如模具结构、材料选择、尺寸精度等。
3.注塑模的制作流程:详细介绍注塑模的制作流程,包括模具设计、加工、装配及调试等环节。
4.注塑模的应用:分析注塑模在实际生产中的应用案例,让学生了解注塑模在各个行业的重要性。
三、教学方法为提高学生的学习兴趣和主动性,本课程采用多种教学方法相结合的方式,包括:1.讲授法:教师通过讲解注塑模的基本概念、设计原则和制作流程,使学生掌握相关理论知识。
2.案例分析法:分析实际生产中的注塑模应用案例,让学生了解注塑模在实际生产中的重要性。
3.实验法:学生进行注塑模的制作和调试实验,提高学生的动手能力和实践能力。
四、教学资源为实现教学目标,本课程需准备以下教学资源:1.教材:选用权威、实用的注塑模教材,为学生提供系统的理论知识。
2.参考书:提供相关领域的参考书籍,丰富学生的知识体系。
3.多媒体资料:制作精美的课件、视频等多媒体资料,提高学生的学习兴趣。
4.实验设备:配备完善的实验设备,确保学生能够进行实践活动。
五、教学评估为全面、客观地评估学生的学习成果,本课程采用多元化的评估方式,包括平时表现、作业、考试等。
具体评估方式如下:1.平时表现:通过观察学生在课堂上的参与程度、提问回答等情况,了解学生的学习态度和掌握程度。
塑料模具课程设计-饮料瓶瓶盖注射模设计
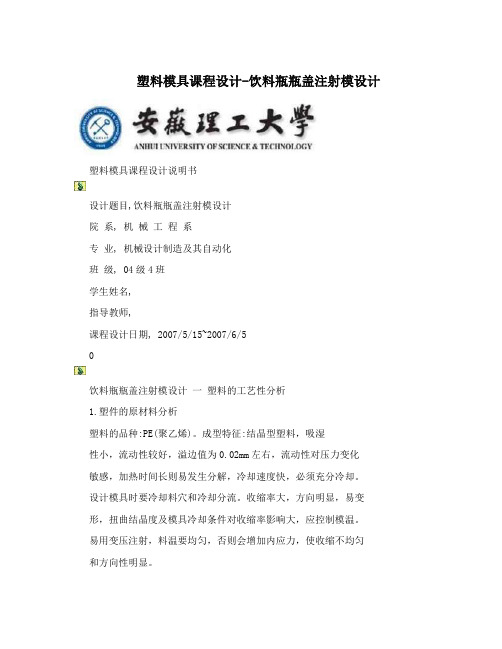
塑料模具课程设计-饮料瓶瓶盖注射模设计塑料模具课程设计说明书设计题目,饮料瓶瓶盖注射模设计院系, 机械工程系专业, 机械设计制造及其自动化班级, 04级4班学生姓名,指导教师,课程设计日期, 2007/5/15~2007/6/5饮料瓶瓶盖注射模设计一塑料的工艺性分析1.塑件的原材料分析塑料的品种:PE(聚乙烯)。
成型特征:结晶型塑料,吸湿性小,流动性较好,溢边值为0.02mm左右,流动性对压力变化敏感,加热时间长则易发生分解,冷却速度快,必须充分冷却。
设计模具时要冷却料穴和冷却分流。
收缩率大,方向明显,易变形,扭曲结晶度及模具冷却条件对收缩率影响大,应控制模温。
易用变压注射,料温要均匀,否则会增加内应力,使收缩不均匀和方向性明显。
2.塑料的尺寸精度分析影响塑料制品的尺寸精度的主要因素是材料的收缩和模具的制造误差。
查教材上表2-11得此材料的收缩率为1.5%~2%。
塑料制品的公差也可通过教材上表2-12查得,塑料的精度等级选择7级精度。
3.塑件的表面质量分析塑件外表面要求粗糙度较低,表面光滑,内表面要求低点。
4.塑件结构的工艺性分析结构简图如图所示1瓶盖主体外侧均匀分布120个增大摩擦力的防滑筋,瓶盖顶部有商标名称ZSM的字样。
瓶盖下部有一防伪圈与瓶盖主体通过8个直径为1mm高1mm的小圆柱相连,防伪圈内侧有8个均匀分布长为3mm直径为1.5mm的半圆形凸台。
瓶盖内部有螺呀为半圆形的螺纹及高为4mm截面直径为1mm的防伪圈与瓶子内径严密配合,而高为1mm,截面直径1mm的防伪圈与瓶子外径严密配合防止漏水。
综上所述可采用注射成型加工。
二确定成型设备选择与模塑工艺规程编制1.计算塑件体积和质量3cm V=3.05M=2.9g选择注射机为SZ-303 理论注射容积为37,实际注射质量为33g,螺杆直径 cm为26 mm,塑化能力3.6g/s,注射压力170MPa 螺杆转速210~160r/min,螺杆行程70 mm,锁模力为320KN,拉杆有效间距2300300,,模板行程110 mm,模具最小厚度80 mm,模具最mm2mm400400 ,大厚度110 mm,最大开距220 mm,模扳尺寸,顶出行程50 mm,喷嘴半径为12 mm,高为2 mm。
- 1、下载文档前请自行甄别文档内容的完整性,平台不提供额外的编辑、内容补充、找答案等附加服务。
- 2、"仅部分预览"的文档,不可在线预览部分如存在完整性等问题,可反馈申请退款(可完整预览的文档不适用该条件!)。
- 3、如文档侵犯您的权益,请联系客服反馈,我们会尽快为您处理(人工客服工作时间:9:00-18:30)。
目录0引言第1章塑件成型工艺分析 (1)1.1课程设计目的 (1)1.2塑料性能分析 (2)1.3尺寸精度分析 (2)第2章分型面的选择 (4)2.1分型面的选择原则 (4)2.2 确定型腔布局 (5)第3章注射机的型号和规格选择 (6)3.1注射机的选择 (6)3.2注射机的终选 (7)第4章浇注系统的设计 (8)4.1 浇注系统设计原则 (8)4.2 主流道设计 (8)4.3 分流道的设计 (9)4.4 浇口的设计 (9)第5章模具的结构分析与设计 (12)5.1确定模架 (12)第6章成型零件的设计 (14)6.1 成型零件的尺寸计算 (14)6.2 脱模机构的设计 (14)6.3 合模定位和导向机构设计 (16)6.4 温度调节系统设计(冷却系统) (17)6.5 排气系统的设计 (18)第7章成型设备的选择及校核 (19)7.1 模具闭合高度的校核 (19)第8章模具特点和工作原理 (21)8.1 模具的特点 (21)8.2 模具的工作过程 (21)第9章设计小结 (22)参考资料 (23)引言随着我国经济迅速发展,采用模具的生产技术越来越得到广泛应用,同时对模具的要求也越来越高。
在未来的模具市场中,塑料模具的发展速度将高于其他模具,在模具行业比重也逐步提高。
塑料模具制造的方法很多,例如:注射、挤出、传递、压缩、粉末冶金、铸造、热成型等等。
其中注射成型是当今市场最常用、最具有前景的塑料成型方法之一,因此塑料注射模作为塑料模具的一种,就具有了很大的市场需求量。
本说明书为塑料注射模具设计说明书,是根据塑料模具手册上的设计过程及相关工艺编写的。
本说明书的内容包括:目录、课程设计指导书、课程设计说明书、参考文献等。
编写本说明书时,力求符合设计步骤,详细说明了塑料注射模具设计方法,以及各种参数的具体计算方法,如塑件的成型工艺、塑料脱模机构的设计。
塑料模设计是“模具设计与制造”专业非常重要、也是对于学生进行的一次全面综合应用模具设计知识和CAD软件、PROE软件应用的实践性训练,对于学生的实践动手操作能力进行培养和提高,是模具设计等专业的一个重要环节。
通过模具结构设计,使学生在塑料制件工艺性分析、工艺方案论证、计算机设计、模具零件结构设计、塑料模标准件的应用、编写技术文件和查阅文献方面受到一次综合训练,增强学生的实际工作能力。
1、塑件成形工艺分析1.1塑料盖子塑件分析如图1.1所示。
塑件结构比较简单,塑件质量要求是不允许有裂纹、变形缺陷,脱模斜度30′-1°;材料要求为ABS,生产批量为大批量,塑件公差按模具设计要求进行转换。
(1)外形尺寸该塑件壁厚为2mm,塑件外形尺寸不大,塑料熔体流程不太长,塑件材料为热塑性塑料,流动性较好,适合于注射成型。
(2)精度等级塑件每个尺寸的公差不一样,任务书已给定尺寸公差,未注公差的尺寸取公差为MT5级。
(3)脱模斜度 ABS的成型性能良好,成型收缩率较小,表选择塑件上型芯和凹模的统一脱模斜度为0.7°。
图1.1 制品零件图1.2塑料性能分析{8}ABS 丙烯腈-丁二烯-苯乙烯共聚物化学和物理特性ABS是由丙烯腈、丁二烯和苯乙烯三种化学单体合成。
每种单体都具有不同特性:丙烯腈有高强度、热稳定性及化学稳定性;丁二烯具有坚韧性、抗冲击特性;苯乙烯具有易加工、高光洁度及高强度。
从形态上看,ABS是非结晶性材料。
三中单体的聚合产生了具有两相的三元共聚物,一个是苯乙烯-丙烯腈的连续相,另一个是聚丁二烯橡胶分散相。
ABS的特性主要取决于三种单体的比率以及两相中的分子结构。
这就可以在产品设计上具有很大的灵活性,并且由此产生了市场上百种不同品质的ABS材料。
这些不同品质的材料提供了不同的特性,例如从中等到高等的抗冲击性,从低到高的光洁度和高温扭曲特性等。
ABS材料具有超强的易加工性,外观特性,低蠕变性和优异的尺寸稳定性以及很高的抗冲击强度。
注塑模工艺条件干燥处理:ABS材料具有吸湿性,要求在加工之前进行干燥处理。
建议干燥条件为80~90C下最少干燥2小时。
材料温度应保证小于0.1%。
熔化温度:210~280C;建议温度:245C。
1.3尺寸精度分析1.3.1 塑件表面质量分析该塑件表面没有提出特殊要求,一般情况下外表面要求光洁,表面粗糙度可以取到。
没有特殊要求时,塑件内部表面粗糙度可取。
1.3.2塑件结构工艺性分析(1)壁厚分析:设计合理,壁厚相对均匀,且符合最小壁厚的一昂球。
(2)脱模斜度:为便于塑件从模腔中取出,塑件的内外壁需要足够的脱模斜度。
外形尺寸以大端为基准,斜度往小处取;内形尺寸以小端为基准,斜度往大处取。
根据ABS的性能和《模具设计与制造简明手册(第三版)》P433—表2-2-5:型芯脱模斜度为:0.7°,型腔脱模斜度为0.5°。
1.3.3 生产实际考虑该塑件的生产类型应该是大批量生产,因此在设计模具时,要提要塑件的生产效率,倾向于采用多型腔,以降低生产成本。
2、分型面的选择2.1分型面的选择原则如何确定分型面。
由于分型面受到塑件在模具中的成型位置、浇注系统设计、塑件的结构工艺性及精度、嵌件位置形状以及推出方法、模具的制造、排气、操作工艺等多种因素的影响,因此在选择分型面时应综合分析比较,从几种方案中优选出较为合理的方案。
选择分型面时一般应遵循以下几项原则:(1)分型面应选择在制品的最大截面处,无论塑件以何形式布置,都应将此作为首要原则;(2)便于塑件顺利脱模,尽量使塑件开模时留在动模一边。
(3)有利于保证塑件的精度要求。
(4)尽可能满足塑件的外观质量要求。
分型面上型腔壁面稍有间隙,就会产生飞边。
(5)便于模具加工制造,在选择非平面分型面时,应有利于型腔加工和制品的脱模方便。
(6)对成型面积的影响,尽量减少制品在合模方向上的投影面积,以减小所需锁模力。
(7)对排气效果的影响,尽可能有利于排气。
(8)对侧向抽芯的影响。
其中最重要的是第(2)和第(5)、第(8)点。
为了便于模具加工制造,应尽是选择平直分型面工易于加工的分型面。
图2.1 分型面示意图从图上来看,该产品必须要抽芯机构,也就是要垂直分型面,排除2分型面。
如果将图倒过来看,产品留在定模,不好取出,故排除3分型面,故我选择1分型面最合理。
2.2 确定型腔布局由考虑经济性实用性,经分析模具采用一模四腔,布局见零件图。
图2.2 型腔布局图3、注射机的型号和规格选择3.1注射机的选择3.1.1计算塑件的体积根据制件大概得塑件的体积为:V1=3.14*(100*10-81*8)=1105.28mm3。
3.1.2计算所需的体积浇注系统凝料按1:1取,故:V2= V1=1105.28mm3塑件和浇注系统凝料总体积为(按一模四腔算):V= 4(V1 +V2)=8842.24mm3 =8.84 cm3压实后的总体积为:S=S1+S2=8.84*1.8+(3.14*0.02*4.8+3.14*0.04*6)*1.8= 17.8cm3 其中S1为产品压实后所需的料,S2为流道压实后所需料。
3.1.3选用注射机根据总体积V=17800 mm3,初步选取SZ-60-400型螺杆式注射成型机。
SZ-60-400型螺杆式注射成型机主要参数如下表所示表3.1 SZ-60-400型注射机参数表3.2注射机的终选3.2.1注射量的校核公式是(0.8 ~ 0.85)式中——注射机的公称注射量,cm3——每模的塑料体积量,cm3如前所述,塑件及浇注系统的总体积为17.8cm3,远小于注射剂的理论注射量51 cm3,故满足要求。
4、浇注系统的设计4.1 浇注系统设计原则{3}(1)浇注系统与塑件一起在分型面上,应有压降,流量和温度的分布的均衡布置;(2)结合型腔布置考虑,尽可能采用平衡式分流道布置;(3)尽量缩短熔体的流程,以便降低压力损失、缩短充模时间;(4)浇口尺寸、位置和数量的选择十分关键,应有利于熔体流动、避免产生湍流、涡流、喷射和蛇形流动,有利于排气和补缩,且应设在塑件较厚的部位,以使熔料从后断面移入薄断面,以利于补料;(5)避免高压熔体对模具型芯和嵌件产生冲击,防止变形和位移的产生;(6)浇注系统凝料脱出应方便可靠,凝料应易于和制品分离或者易于切除和整修;(7)熔接痕部位与浇口尺寸、数量及位置有直接关系,设计浇注系统时要预先考虑到熔接痕的部位、形态,以及对制品质量的影响;(8)尽量减少因开设浇注系统而造成的塑料凝料用量;(9)浇注系统的模具工作表面应达到所需的硬度、精度和表面粗糙度,其中浇口应有IT8以上的精度要求;(10)设计浇注系统时应考虑储存冷料的措施;(11)尽可能使主流道中心与模板中心重合,若无法重合应使两者的偏离距离尽可能小。
4.2 主流道设计主流道通常位于模具中心塑料熔体的入口处,它将注射机喷射出的熔体导入分流道或型腔中。
主流道的形状为圆锥形,以便于熔体的流动和开模时主流道凝料的顺利拔出。
4.2.1 主流道尺寸(1)主流道小端直径d主流道小端直径d = 注射机喷嘴直径+0.5 ~ 1= 4 + 0.5~1取d = 5(mm)这样便于喷嘴和主流道能同轴对准,也能使的主流道凝料能顺利脱出。
(2)主流道球面半径主流道入口的凹坑球面半径R,应该大于注射机喷嘴球头半径的2~3mm。
反之,两者不能很好的贴合,会让塑件熔体反喷,出现溢边致使脱模困难.SR = 注射机喷嘴球头半径 + 2~3SR = 15 + 2~3取d = 18(mm)(3)主流道长度L一般按模板厚度确定,但为了减小充模时压力降和减少物料损耗,以短为好,小模具控制在50之内。
在出现过长流道时,可以将主流道衬套挖出深凹坑,让喷嘴伸入模具。
本设计中结合该模具的结构,取L=50(mm)(4)主流道大端直径D = d + 2 Ltgα(半锥角α:为1°~ 2°,取α=2°)≈ 124.2.2 主流道衬套形式及其固定主流道小端入口处与注射机喷嘴反复接触,属易损件,对材料要求较严,因而模具主流道部分常设计成可拆卸更换的主流道衬套形式,即浇口套。
本模具是三板模,因此需要尽量减少主流道长度。
方案一:用浇口套标准件,这样只需购买,但是主流道长度过大,在凝料脱模时会产生困难。
固定形式:用定位圈配合固定在模具的面板上。
定位圈也是标准件。
方案二:在定模座板上开设阶梯孔,将浇口套放入减小主流道长度。
浇口套自行设计。
在定模座板上在安装定位圈定位。
故选择方案一。
4.3 分流道的设计本模具的流道布置形式采用平衡式。
分流道的形状及尺寸与塑件的体积、壁厚、形状的复杂程度、注射速率等因素有关。
该塑件的体积不大而且形状不复杂,且壁厚均匀,可以考虑采用点进料的方式,有利于塑件的成型和外观质量的保证。